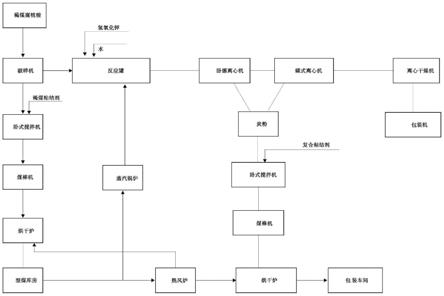
1.本发明属于煤化工产品生产技术领域,特别涉及一种利用褐煤腐植酸生产腐植酸钾的方法。
背景技术:2.传统方法生产腐植酸钾,多用小分子,游离酸含量高、易提取腐植酸钾的风化煤,但风化煤多储存于烟煤表层,资源有限。而褐煤腐植资源丰富,大规模矿采。但是褐煤腐植酸大分子,化学反应中的钙镁离子对可溶性腐植酸提取率产生影响,加之采用传统方法存在能耗高,生产成本高等问题,导致褐煤腐植酸生产腐植酸钾困难重重。
3.目前国内很多用褐煤腐植酸生产有机复合肥,多采用褐煤腐植酸和家禽粪便、农作物桔杆混合堆呕发酵的方法生产腐植酸有机肥,这种方法提取的肥料植物可吸收利用的可溶性腐植酸含量低,不利于高效利用褐煤腐植酸资源。
技术实现要素:4.本发明的目的是为了解决现有技术的不足,而提供一种与传统生产方法完全不同的利用褐煤腐植酸生产腐植酸钾的方法,该利用褐煤腐植酸生产腐植酸钾的方法采用水加氢氧化钾、亚硫酸钠与褐煤腐植酸粉进行化学反应,避免钙镁等离子对提取水溶性腐植酸的影响;该利用褐煤腐植酸生产腐植酸钾的方法提取腐植钾后的炭粉不含挥发物,加复合粘结剂可生产附加值高的洁净炭燃料,进一步降低生产成本;该利用褐煤腐植酸生产腐植酸钾的方法采用褐煤腐植酸粉末成型生产低成本型煤燃料技术,降低燃料成本69%,进一步降低生产成本;该利用褐煤腐植酸生产腐植酸钾的方法突破了传统方法生产腐植酸钾成本高的问题,大大提高了褐煤腐植酸钾产品的市场竞争能力。
5.本发明采用的技术方案为:一种利用褐煤腐植酸生产腐植酸钾的方法,该利用褐煤腐植酸生产腐植酸钾的方法包括以下步骤:步骤一,制取褐煤腐植酸粉,将褐煤腐植酸原料送破碎机破碎到30-60目,得到褐煤腐植酸粉;步骤二,制取腐植酸钾半成品,在反应罐中加水,升温加热到50℃-60℃,再加入氢氧化钾,接着加入褐煤腐植酸粉,边加边搅拌,反应温度为60℃-80℃,反应时间为60—70min;最后加入亚硫酸钠进而二次反应,反应温度为60℃,反应时间为60min,得到腐植酸钾半成品;步骤三,除去炭粉,将腐植酸钾半成品通过管道送臥螺式离心分离机,进行一级提纯,除去腐植酸钾半成品中95%—97%炭粉;步骤四,除去杂质,将除去炭粉后的腐植酸钾半成品送入蝶式离心机,进行二级分离提纯,除去少量杂质,得到杂质≤1%的高纯度腐植酸钾液体肥;步骤五,干燥脱水,将高纯度腐植酸钾液体肥通过管道送入高速离心干燥机,进行
干燥脱水,制成高纯度腐植酸钾粉状产品。
6.进一步,步骤一中,褐煤腐植酸原料是水分含量为45%-50%、灰分含量为8%-12%、腐植酸干基含量为45%—60%的褐煤腐植酸原料。
7.进一步,步骤二中,水的比例为腐植酸的3-4倍,氢氧钾的加入量为褐煤腐植酸的3%-6%,亚硫酸钠加入量为褐煤腐植酸的0.8%-1.5%,氢氧化钾纯度和亚硫酸钠纯度含量为96%-98%。
8.一种粉状高纯度腐植酸钾,该粉状高纯度腐植酸钾通过上述的利用褐煤腐植酸生产腐植酸钾的方法制取获得。
9.一种利用炭粉制备洁净炭棒的方法,包括以下步骤:制取粘性好的混合料,将上述步骤三中除去的炭粉经输送带送搅拌机,并向搅拌机内加入复合粘结剂,复合粘结剂的加入量为炭粉的4%-5%,混合搅拌8—10分钟,得到粘性好的混合物料;制取洁净炭棒,将粘性好的混合物料通过输送带送煤棒机,挤压成型,得到洁净炭棒;烘干脱水,将含水的洁净炭棒通过输送带送烘干炉,烘干脱水。
10.一种烘干脱水的洁净炭棒,该烘干脱水的洁净炭棒通过上述的利用炭粉制备洁净炭棒的方法制取获得。
11.一种利用褐煤腐植酸粉制备煤棒的方法,包括以下步骤:制粘性好的混合料,将上述步骤一中部分褐煤腐植酸粉末经输送带送搅拌机,并向搅拌机内按比例加入褐煤粘结剂,混合搅拌8—10分钟,得到粘性好的混合物料;制取煤棒,将粘性好的混合料通过输送带送煤棒机,挤压成型,得到煤棒;烘干脱水,将含水的煤棒通过输送带送入烘干炉,烘干脱水。
12.进一步,所述烘干脱水后的煤棒作为热风炉和蒸汽锅炉的燃料;热风炉产生的热风供给烘干炉,蒸汽锅炉生产的蒸汽供给反应罐制取腐植酸钾半成品。
13.一种烘干脱水的煤棒,该烘干脱水的煤棒通过上述的利用褐煤腐植酸粉制备煤棒的方法制取获得。
14.本发明的有益效果是:一套生产技装置技术可生产三种产品:一是腐植酸钾高附加值产品;二是低价褐煤腐植酸生产型煤燃料产品。传统方法市场采购1800元/吨型煤燃料生产腐植酸钾,燃料成本高。该发明自产褐煤腐植酸型煤燃料,生产成本约550元/吨,与传统方法相比,可节约燃料成本69%;三是洁净型炭燃料产品,该产品是用提纯腐植酸钾附产的炭粉生产的。该发明将褐煤腐植酸提质利用技术提高到国内外先进水平。获取好的经济效益和社会效益。
附图说明
15.为了更清楚地说明本发明实施例的技术方案,下面将对实施例中所需要使用的附图作简单地介绍,应当理解,以下附图仅示出了本发明的某些实施例,因此不应被看作是对范围的限定,对于本领域普通技术人员来讲,在不付出创造性劳动的前提下,还可以根据这些附图获得其他相关的附图。
16.图1为该生产腐植酸钾方法的生产工艺流程图。
具体实施方式
17.下面将结合本发明实施例中附图,对本发明实施例中的技术方案进行清楚、完整地描述,显然,所描述的实施例仅仅是本发明一部分实施例,而不是全部的实施例。通常在此处附图中描述和示出的本发明实施例的组件可以以各种不同的配置来布置和设计。因此,以下对在附图中提供的本发明的实施例的详细描述并非旨在限制要求保护的本发明的范围,而是仅仅表示本发明的选定实施例。基于本发明的实施例,本领域技术人员在没有做出创造性劳动的前提下所获得的所有其他实施例,都属于本发明保护的范围。
18.实施例一:(一)利用褐煤腐植酸生产腐植酸钾的方法原料选择:褐煤腐植酸原料指标要求:水分含量为45%,灰分含量为9%,腐植酸干基含量为45%。
19.如图1所示;步骤一,制取褐煤腐植酸粉末,将褐煤腐植酸原料送破碎机破碎到30-60目,得到褐煤腐植酸粉。
20.步骤二,制取腐植酸钾半成品,在反应罐中加水,水的加入量为腐植酸粉末的3倍,升温加热到50℃-60℃,再加入纯度含量为96%的氢氧化钾,氢氧化钾加入量为褐煤腐植酸的3%,最后加入褐煤腐植酸粉末,边加边搅拌,反应温度为70℃-80℃,反应时间为70min,接着加入纯度含量为96%的亚硫酸钠,亚硫酸钠加入量为褐煤腐植酸的0.8%,反应温度为60℃,反应时间为60min,得到腐植酸钾半成品,该腐植酸钾半成品为液体。
21.步骤三,除去炭粉,将腐植酸钾半成品通过管道送臥螺式离心分离机,进行一级提纯,除去腐植酸钾半成品中95%—97%炭粉。
22.步骤四,除去杂质,将除去炭粉后的腐植酸钾半成品送入蝶式离心机,进行二级分离提纯,除去少量杂质,得到杂质≤1%的高纯度腐植酸钾液体肥;步骤五,干燥脱水,将高纯度腐植酸钾液体肥通过管道送入高速离心干燥机,进行干燥脱水,制成高纯度腐植酸钾粉状产品。
23.从高速离心干燥机出来的高纯度腐植酸钾粉状产品其质量符合国家农用腐植酸钾质量标准,通过输送带送入包装机,即可包装入库。
24.(二)通过中间产物炭粉制备洁净炭棒制取粘性好的混合料;将生产腐植酸钾的方法步骤三中的炭粉经输送带送搅拌机,并向搅拌机内加入复合粘结剂,复合粘结剂的加入量为炭粉的4%,混合搅拌10分钟,得到粘性好的混合物料。
25.制取洁净炭棒;将粘性好的混合物料通过输送带送煤棒机,挤压成型,得到洁净炭棒,该洁净炭棒具有较好的粘性。
26.烘干脱水;将含水的洁净炭棒通过输送带送烘干炉,烘干脱水。
27.包装;将烘干脱水后的洁净炭棒通过输送带带送包装车间包装入库。这种洁净型炭,冷态抗压强度好,热稳定性好。燃点温度334℃,可作烧烤炭和民用洁净燃料。
28.(三)通过褐煤腐植酸粉制备煤棒制取粘性好的混合料;将生产腐植酸钾的方法步骤一中部分褐煤腐植酸粉末经输送带送搅拌机,并向搅拌机内按比例加入褐煤粘结剂,褐煤粘结剂的加入量为褐煤腐植酸
粉末的7%,混合搅拌8分钟,得到粘性好的混合物料。
29.制取煤棒;将粘性好的混合料通过输送带送煤棒机,挤压成型,得到煤棒,该煤棒具有较好的粘性。
30.烘干脱水;将含水的煤棒通过输送带送入烘干炉,烘干脱水。
31.入库;将干脱水后的煤棒通过输送带送型煤库房。
32.为生产腐植酸钾提供燃料;将型煤库房的煤棒送热风炉和蒸汽锅炉作燃料;热风炉产生的热风供给制备煤棒和制备洁净炭棒的烘干炉;蒸汽锅炉生产的蒸汽供给生产腐植酸钾的反应罐制取腐植酸钾半成品。
33.实施例二:(一)利用褐煤腐植酸生产腐植酸钾的方法原料选择:褐煤腐植酸原料指标要求:水分含量为50%,灰分含量为8%,腐植酸干基含量为58%。
34.步骤一,制取褐煤腐植酸粉,将褐煤腐植酸原料送破碎机破碎到30-60目,得到褐煤腐植酸粉。
35.步骤二,制取腐植酸钾半成品,在反应罐中加软水,水的加入量为腐植酸粉末的4倍,升温加热到50℃-60℃,再加入纯度含量为97%的氢氧化钾,氢氧化钾加入量为褐煤腐植酸的4.8%,最后加入褐煤腐植酸粉末,边加边搅拌,反应温度为60℃-80℃,反应时间为60min,时间到加入纯度含量为97%的亚硫酸钠,亚硫酸钠加入量为煤腐植酸的1%,反应温度60℃,反应时间为60min,接得到腐植酸钾半成品,该腐植酸钾半成品为液体.步骤三,除去炭粉,将腐植酸钾半成品通过管道送臥螺式离心分离机,进行一级提纯,除去腐植酸钾半成品中95%—97%炭粉。
36.步骤四,除去杂质,将除去炭粉后的腐植酸钾半成品送入蝶式离心机,进行二级分离提纯,除去少量杂质,得到杂质≤1%的高纯度腐植酸钾液体肥;步骤五,干燥脱水,将高纯度腐植酸钾液体肥通过管道送入高速离心干燥机,进行干燥脱水,制成高纯度腐植酸钾粉状产品。
37.从高速离心干燥机出来的高纯度腐植酸钾粉状产品其质量符合国家农用腐植酸钾质量标准,通过输送带送入包装机,即可包装入库。
38.(二)通过中间产物炭粉制备洁净炭棒制取粘性好的混合料;将生产腐植酸钾的方法步骤三中的炭粉经输送带送搅拌机,并向搅拌机内加入复合粘结剂,复合粘结剂的加入量为炭粉的4%,混合搅拌9分钟,得到粘性好的混合物料。
39.制取洁净炭棒;将粘性好的混合物料通过输送带送煤棒机,挤压成型,得到洁净炭棒,该洁净炭棒具有较好的粘性。
40.烘干脱水;将含水的洁净炭棒通过输送带送烘干炉,烘干脱水。
41.包装;将烘干脱水后的洁净炭棒通过输送带带送包装车间包装入库。这种洁净型炭,冷态抗压强度好,热稳定性好。燃点温度334℃,可作烧烤炭和民用洁净燃料。
42.(三)通过褐煤腐植酸粉末制备煤棒制取粘性好的混合料;将生产腐植酸钾的方法步骤一中部分褐煤腐植酸粉末经输送带送搅拌机,并向搅拌机内按比例加入褐煤粘结剂,褐煤粘结剂的加入量为褐煤腐植酸
粉末的7%,混合搅拌9分钟,得到粘性好的混合物料。
43.制取煤棒;将粘性好的混合料通过输送带送煤棒机,挤压成型,得到煤棒,该煤棒具有较好的粘性。
44.烘干脱水;将含水的煤棒通过输送带送入烘干炉,烘干脱水。
45.入库;将干脱水后的煤棒通过输送带送型煤库房。
46.为生产腐植酸钾提供燃料;将型煤库房的煤棒送热风炉和蒸汽锅炉作燃料;热风炉产生的热风供给制备煤棒和制备洁净炭棒的烘干炉;蒸汽锅炉生产的蒸汽供给生产腐植酸钾的反应罐制取腐植酸钾半成品。
47.实施例三:(一)利用褐煤腐植酸生产腐植酸钾的方法原料选择:褐煤腐植酸原料指标要求:水分含量为50%,灰分含量为12%,腐植酸干基含量为60%。
48.步骤一,制取褐煤腐植酸粉,将褐煤腐植酸原料送破碎机破碎到30-60目,得到褐煤腐植酸粉。
49.步骤二,制取腐植酸钾半成品,在反应罐中加水,水的加入量为腐植酸粉末的4倍,升温加热到50℃-60℃,再加入纯度含量为98%的氢氧化钾,氢氧化钾加入量为褐煤腐植酸的6%,最后加入褐煤腐植酸粉末,边加边搅拌,反应温度为60℃-80℃,反应时间为60min,时间到加入纯度含量为98%的亚硫酸钠,亚硫酸钠加入量为褐煤腐植酸的1.5%,反应温度60℃,反应时间60min。得到腐植酸钾半成品,该腐植酸钾半成品为液体。
50.步骤三,除去炭粉,将腐植酸钾半成品通过管道送臥螺式离心分离机,进行一级提纯,除去腐植酸钾半成品中95%—97%炭粉。
51.步骤四,除去杂质,将除去炭粉后的腐植酸钾半成品送入蝶式离心机,进行二级分离提纯,除去少量杂质,得到杂质≤1%的高纯度腐植酸钾液体肥;步骤五,干燥脱水,将高纯度腐植酸钾液体肥通过管道送入高速离心干燥机,进行干燥脱水,制成高纯度腐植酸钾粉状产品。
52.从高速离心干燥机出来的高纯度腐植酸钾粉状产品其质量符合国家农用腐植酸钾质量标准,通过输送带送入包装机,即可包装入库。
53.(二)通过中间产物炭粉制备洁净炭棒制取粘性好的混合料;将生产腐植酸钾的方法步骤三中的炭粉经输送带送搅拌机,并向搅拌机内加入复合粘结剂,复合粘结剂的加入量为炭粉的5%,混合搅拌8分钟,得到粘性好的混合物料。
54.制取洁净炭棒;将粘性好的混合物料通过输送带送煤棒机,挤压成型,得到洁净炭棒,该洁净炭棒具有较好的粘性。
55.烘干脱水;将含水的洁净炭棒通过输送带送烘干炉,烘干脱水。
56.包装;将烘干脱水后的洁净炭棒通过输送带带送包装车间包装入库。这种洁净型炭,冷态抗压强度好,热稳定性好。燃点温度334℃,可作烧烤炭和民用洁净燃料。
57.(三)通过褐煤腐植酸粉末制备煤棒取粘性好的混合料;将生产腐植酸钾的方法步骤一中部分褐煤腐植酸粉末经输送带送搅拌机,并向搅拌机内按比例加入褐煤粘结剂,褐煤粘结剂的加入量为褐煤腐植酸粉
的7%,混合搅拌10分钟,得到粘性好的混合物料。
58.制取煤棒;将粘性好的混合料通过输送带送煤棒机,挤压成型,得到煤棒,该煤棒具有较好的粘性。
59.烘干脱水;将含水的煤棒通过输送带送入烘干炉,烘干脱水。
60.入库;将干脱水后的煤棒通过输送带送型煤库房。
61.为生产腐植酸钾提供燃料;将型煤库房的煤棒送热风炉和蒸汽锅炉作燃料;热风炉产生的热风供给制备煤棒和制备洁净炭棒的烘干炉;蒸汽锅炉生产的蒸汽供给生产腐植酸钾的反应罐制取腐植酸钾半成品。
62.需要说明的是,本发明中所使用的褐煤腐植酸粉原料、氢氧化钾、亚硫酸钠、水、复合粘结剂、褐煤粘结剂等产品可通过市购获得,同时图1中所使用的生产设备也可通过市购获得。
63.该利用褐煤腐植酸生产腐植酸钾的方法可生产三种产品:一是腐植酸钾高附加值产品;二是低价褐煤腐植酸生产型煤燃料产品,型煤燃料产品主要作生产腐植酸钾的供热燃料,生产成本约550元/吨,与传统方法市场采购价1800元/吨型煤相比,可节约燃料成本69%;三是洁净型炭燃料产品,炭燃料产品是用提纯腐植酸钾附产的炭粉生产的。
64.综上所述,该发明将褐煤腐植酸提质利用技术提高到国内外先进水平。获取好的经济效益和社会效益。