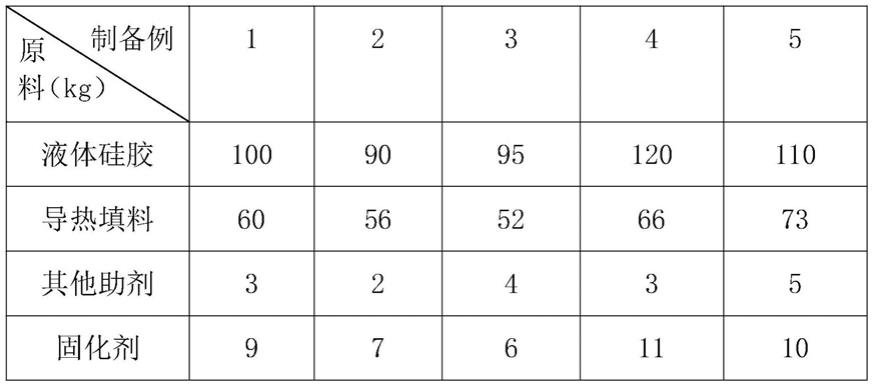
1.本技术涉及硅胶技术领域,更具体地说,它涉及一种高导热硅胶、硅胶套、高导热硅胶压花辊筒及其制备方法。
背景技术:2.硅胶是一种高活性吸附材料,包括无机硅胶和有机硅胶,其中有机硅胶因其具有绝缘、耐候和稳定的特性,在航空、军事、建筑、电子电气、纺织、汽车、机械、皮革造纸、化工轻工和医药医疗领域均有较好的应用。
3.同时硅胶可以应用在压花辊上进行压花,且相较于辊筒压花效果更佳。另外可以根据产品所需灵活更换硅胶,达到便捷改变压花花纹的效果;且相较于更换辊筒,操作更为便捷,成本更低。
4.但是由于硅胶的导热效果较差,基本导热率都在0.15w/mk左右。这种普通的硅胶辊压出的花纹纹理较为粗糙,且在压花过程中硅胶材料自身的热量较高,容易导致使用寿命较短。随着客户对外观要求的不断提升,普通硅胶辊较难满足需求。
技术实现要素:5.为了制备一种导热性能好且使用寿命长的硅胶压花辊筒,本技术提供一种高导热硅胶、硅胶套、高导热硅胶压花辊筒及其制备方法。
6.第一方面,本技术提供一种高导热硅胶,采用如下的技术方案:一种高导热硅胶,包括以下质量份的原料:液体硅胶90~120份、导热填料52~73份、固化剂6~11份、其他助剂2~5份,其中所述液体硅胶为rtv室温硫化硅橡胶。
7.通过采用上述技术方案,以rtv室温硫化硅橡胶作为液体硅胶,并在其内部填充导热填料,从而有助于提高其导热性能,并且导热填料填充后rtv室温硫化硅橡胶的强度有所改善。由于rtv室温硫化硅橡胶在室温条件下就能够固化的特性,使得制备工艺操作较为简便,且工艺控制性较好。另外rtv室温硫化硅橡胶与导热填料的结合效果较好,导热填料在其内部的分散效果较好,因此有助于提高制得高导热硅胶导热的均匀性。
8.作为优选,所述导热填料为金刚石微粉和氧化铝微粉按照质量比1:1组成的混合物。
9.通过采用上述技术方案,以金刚石微粉和氧化铝微粉作为导热填料,其中金刚石微粉是指粒度细于54微米的金刚石颗粒,氧化铝微粉同样是指微米级的氧化铝颗粒。两者在体系中的分散性较好,不易发生团聚现象,且导热性能较为优异,同时两者与rtv室温硫化硅橡胶的相容性均较好。另外两者复配使用有助于进一步提高体系的导热效果。
10.作为优选,所述金刚石微粉的粒径为5~10μm,所述氧化铝微粉的粒径为30~50μm。
11.通过采用上述技术方案,粒径为5~10μm金刚石微粉和粒径为30~50μm的氧化铝微粉均可以较好地分散在体系中,且更小粒径的金刚石微粉可以存在于氧化铝微粉之间的
间隙内,即导热填料可以更紧密地堆积,导热填料之间可以形成更多的有效接触,使得导热连续性更好,有助于进一步提高体系的导热效果。
12.作为优选,所述金刚石微粉为金刚石微粉原料经硅烷偶联剂和聚乙烯酮改性处理后得到,所述氧化铝微粉为氧化铝微粉原料经硅烷偶联剂和聚丙烯酰胺改性处理后得到。
13.通过采用上述技术方案,利用硅烷偶联剂和聚乙烯酮对金刚石微粉进行改性处理,硅烷偶联剂可以在金刚石微粉表面接枝有机链段,提高其表面活性,有助于提高金刚石微粉在体系中的分散效果;并且硅烷偶联剂可以作为聚乙烯酮和金刚石微粉之间的中间分子桥,使得聚乙烯酮较为稳定地交联在金刚石微粉表面。同时利用硅烷偶联剂和聚丙烯酰胺对氧化铝微粉进行改性处理,硅烷偶联剂可以在氧化铝微粉表面接枝有机链段,提高其表面活性,有助于提高金刚石微粉在体系中的分散效果;并且硅烷偶联剂可以作为聚丙烯酰胺和氧化铝微粉之间的中间分子桥,使得聚丙烯酰胺较为稳定地交联在金刚石微粉表面。由于聚乙烯酮结构中含有较多的羰基基团,而聚丙烯酰胺结构中含有较多的胺基基团,两种基团接触后可以相互作用并连接在一起。因此改性后的金刚石微粉和改性后的氧化铝微粉在填充过程中,有效接触更多,且接触的稳定性更佳;同时更小粒径的金刚石微粉可以更好地位于氧化铝微粉之间,使得填充的导热填料在体系中更趋向于形成与热流方向平行的导热网状链,从而使得体系的导热效果更佳。
14.第二方面,本技术提供一种高导热硅胶的制备方法,采用如下的技术方案:一种高导热硅胶的制备方法,包括以下步骤:称料混合:按配方称量原料并混合均匀,得到混合料;研磨处理:研磨混合料,制得复合型液体硅胶;模具定型:将复合型液体硅胶均匀涂抹在模具上,室温固化22~25h后制得高导热硅胶。
15.通过采用上述技术方案,对混合料进行研磨处理,使得各组分的混合效果更好,且有利于导热填料较为均匀地分散在体系中,均匀分散的导热填料对提高体系导热效果具有积极意义。由于选用rtv室温硫化硅橡胶,可在室温下进行固化,制备工艺较为简便,实用性较强。
16.第三方面,本技术提供一种硅胶套,采用如下的技术方案:一种硅胶套,由上述高导热硅胶的制备方法制备得到。
17.第四方面,本技术提供一种高导热硅胶压花辊筒,采用如下的技术方案:一种高导热硅胶压花辊筒,包括钢芯、硅胶层和粘合层,所述硅胶层为硅胶套套设在钢芯上形成的层,所述粘合层位于钢芯和硅胶层之间,且所述粘合层为钢芯上涂抹粘合剂形成的层。
18.通过采用上述技术方案,整个压花辊筒结构简单,组装方便,且稳定性较好。同时利用导热性优异的硅胶套作为压花媒介,有助于提高压花质量,同时可以及时传导出自身所积蓄的热量,有助于延长硅胶套的使用寿命。
19.作为优选,所述硅胶层的厚度为1.8~2.3mm。
20.通过采用上述技术方案,硅胶层的厚度为1.8~2.3mm,该厚度范围内的硅胶层不仅可以满足压花自身所需,而且导热效果更佳。
21.作为优选,所述粘合层为单组分室温固化胶涂抹在钢芯周壁上形成的层,且所述
粘合层的厚度为0.15~0.24mm。
22.通过采用上述技术方案,单组分室温固化胶暴露在空气中可以进行初始固化,同时在隔绝空气的条件下也可以通过加热实现固化,契合压花辊的制备工艺条件,且粘接强度较高,使得硅胶层可以较为稳定的套设在钢芯上。另外将粘合层的厚度控制在0.15~0.24mm,与硅胶层的厚度较为匹配。
23.第五方面,本技术提供一种高导热硅胶压花辊筒的制备方法,采用如下的技术方案:一种高导热硅胶压花辊筒的制备方法,包括以下步骤:粘合组装:在钢芯表面涂抹粘合剂,然后将硅胶套套设在钢芯上,得到硅胶套的纹理面朝外的粗产品;干燥成型:在80℃~90℃的温度下加热干燥粗产品,5.5~7h后制得成品高导热硅胶压花辊筒。
24.通过采用上述技术方案,整个压花辊筒的制备工艺较为简单,规模化生产前景较好。
25.综上所述,本技术具有以下有益效果:1、本技术通过在液态硅胶中填充导热填料,且液态硅胶选用rtv室温硫化硅橡胶,体系中导热填料的分散性较好,且对rtv室温硫化硅橡胶自身的性能具有一定的增益效果,从而制备得到的导热硅胶导热性能较为优异,且强度及韧性方面也较好。
26.2、本技术导热填料选用金刚石微粉和氧化铝微粉,且金刚石微粉的粒径为5~10μm,氧化铝微粉的粒径为30~50μm,两者均能够较好地分散在体系中;同时较小粒径的金刚石微粉可以进入相邻氧化铝微粉之间的间隙处,有利于导热填料更紧密地堆积,增加有效接触,从而有助于进一步提高体系的导热效果。
27.3、本技术利用硅烷偶联剂和聚乙烯酮对金刚石微粉进行改性,并利用硅烷偶联剂和聚丙烯酰胺对氧化铝微粉进行改性,使得金刚石微粉和氧化铝微粉的表面活性更高,且两者分别交联的聚乙烯酮和聚丙烯酰胺中的羰基基团和胺基基团可以发生相互作用,使得金刚石微粉和氧化铝微粉相互连接,形成导热网状链,从而有助于进一步提高体系的导热效果。
28.4、本技术的制备工艺简便,操作简单,规模化生产前景较好。
具体实施方式
29.本技术制备例及实施例中所用的原料均可通过市售获得,其中单组分室温固化胶产自东莞市汇瑞胶业有限公司,型号为瑞汇hr-323t;聚乙烯酮产自江苏新素新材料有限公司,货号为9003-39-8;聚丙烯酰胺产自任丘市江海化工产品有限公司,货号为9003-05-8。
30.以下结合制备例和实施例对本技术作进一步详细说明。
31.高导热硅胶的制备例制备例1~5的区别之处在于各原料的添加量不同。
32.以下以制备例1为例进行说明。
33.制备例1
一种高导热硅胶,包括以下质量的原料:液体硅胶100kg、导热填料60kg、其他助剂3kg、固化剂9kg;其中液体硅胶为rtv室温硫化硅橡胶;导热填料为金刚石微粉和氧化铝微粉按照质量比1:1组成的混合物,且金刚石微粉的粒径为5~10μm,氧化铝微粉的粒径为30~50μm;其他助剂为色料;固化剂为cat-1600。
34.该高导热硅胶的制备方法包括以下步骤:s1导热填料改性:将金刚石微粉加入硅烷偶联剂kh-550及聚乙烯酮的混合物中,混合搅拌后静置20min,得到改性金刚石微粉备用;将氧化铝微粉加入硅烷偶联剂kh-550及聚丙烯酰胺的混合物中,混合搅拌后静置20min,得到改性氧化铝微粉备用;s2称料混合:按配方称量原料并混合均匀,得到混合料;s3研磨处理:研磨混合料,其中研磨轮为:φ200mm*200mm*200mm,研磨厚度为1mm,制得复合型液体硅胶;s4模具定型:将复合型液体硅胶均匀涂抹在带有花纹的模具上,室温固化24h后制得厚度为2mm的高导热硅胶。表1高导热硅胶原料组分表
35.制备例6本制备例与制备例1的区别之处在于,导热填料为金刚石微粉,且s1导热填料改性步骤为:将金刚石微粉加入硅烷偶联剂kh-550及聚乙烯酮的混合物中,混合搅拌后静置20min,得到改性金刚石微粉备用。
36.制备例7本制备例与制备例1的区别之处在于,导热填料为氧化铝微粉,且s1导热填料改性步骤为:将氧化铝微粉加入硅烷偶联剂kh-550及聚乙烯酮的混合物中,混合搅拌后静置20min,得到改性氧化铝微粉备用。
37.制备例8本制备例与制备例1的区别之处在于,导热填料为金刚石微粉和氧化铝微粉按照质量比2:1组成的混合物。
38.制备例9本制备例与制备例1的区别之处在于,导热填料为金刚石微粉和氧化铝微粉按照质量比1:2组成的混合物。
39.制备例10本制备例与制备例1的区别之处在于,金刚石微粉的粒径为30~50μm。
40.制备例11本制备例与制备例1的区别之处在于,不对金刚石微粉和氧化铝微粉进行改性处理,即不进行s1导热填料改性步骤。
41.制备例12本制备例与制备例1的区别之处在于,s1导热填料改性步骤中,将金刚石微粉加入硅烷偶联剂kh-550中,混合搅拌后静置20min,得到改性金刚石微粉备用;将氧化铝微粉加入硅烷偶联剂kh-550中,混合搅拌后静置20min,得到改性氧化铝微粉备用。
42.制备例13本制备例与制备例1的区别之处在于,s1导热填料改性步骤中,将金刚石微粉加入硅烷偶联剂kh-550和聚乙烯酮中,混合搅拌后静置20min,得到改性金刚石微粉备用;将氧化铝微粉加入硅烷偶联剂kh-550中,混合搅拌后静置20min,得到改性氧化铝微粉备用。
43.制备例14本制备例与制备例1的区别之处在于,s1导热填料改性步骤中,将金刚石微粉加入硅烷偶联剂kh-550中,混合搅拌后静置20min,得到改性金刚石微粉备用;将氧化铝微粉加入硅烷偶联剂kh-550和聚丙烯酰胺中,混合搅拌后静置20min,得到改性氧化铝微粉备用。
44.制备例15本制备例与制备例1的区别之处在于,s1导热填料改性步骤中,将金刚石微粉加入聚乙烯酮中,混合搅拌后静置20min,得到改性金刚石微粉备用;将氧化铝微粉加入聚丙烯酰胺中,混合搅拌后静置20min,得到改性氧化铝微粉备用。
45.制备例16本制备例与制备例1的区别之处在于,s4模具定型步骤中,制得高导热硅胶的厚度为1mm。
46.制备例17本制备例与制备例1的区别之处在于,s4模具定型步骤中,制得高导热硅胶的厚度为3mm。
47.对比制备例对比制备例1本对比制备例与制备例1的区别之处在于,不加入导热填料,且不进行s1导热填料改性步骤。
48.对比制备例2本对比制备例与制备例1的区别之处在于,导热填料的添加量为100kg,且制备方法不变。
49.对比制备例3本对比制备例与制备例1的区别之处在于,不进行s2研磨处理步骤,即制备方法包
括以下步骤:1)导热填料改性:将金刚石微粉加入硅烷偶联剂kh-550及聚乙烯酮的混合物中,混合搅拌后静置20min,得到改性金刚石微粉备用;将氧化铝微粉加入硅烷偶联剂kh-550及聚丙烯酰胺的混合物中,混合搅拌后静置20min,得到改性氧化铝微粉备用;2)称料混合:按配方称量原料并混合均匀,得到混合料;3)模具定型:将混合料均匀涂抹在带有花纹的模具上,室温固化24h后制得厚度为2mm的高导热硅胶。
50.对比制备例4本对比制备例与制备例1的区别之处在于,液体硅胶为高温硫化硅橡胶,且s4模具定型步骤中,将复合型液体硅胶均匀涂抹在带有花纹的模具上,在加热加压条件下固化24h后制得厚度为2mm的高导热硅胶。实施例
51.实施例1一种高导热硅胶压花辊筒,包括钢芯、硅胶层和粘合层,粘合层位于钢芯和硅胶层之间;其中硅胶层为硅胶套套设在钢芯上形成的层,硅胶套为制备例1中制备得到;粘合层为钢芯上涂抹粘合剂形成的层,粘合剂为单组分室温固化,具体为汇瑞hr-323t,粘合层厚度为0.2mm;钢芯为经喷砂处理后的铁质圆筒,且表面处理层的壁厚为10-15mm,且钢芯为双套夹层八水道钢芯。
52.该高导热硅溶胶压花辊筒的制备方法包括以下步骤:a1粘合组装:调整涂刀和钢芯之间的距离,在钢芯表面涂抹粘合剂,控制涂料量使得粘合层的厚度为0.2mm;然后将硅胶套翻转过来,使其有纹理的面朝内,将粘合面朝外对准涂有粘合剂的钢芯进行套装,得到粗产品;a2干燥成型:使用介质为水的模温机在80℃的温度下加热干燥粗产品,6h后制得成品高导热硅胶压花辊筒。
53.实施例2~17与实施例1的区别之处在于,各实施例中的硅胶套由不同的制备例制得。
54.表2实施例中硅胶套与制备例的对应关系表表2实施例中硅胶套与制备例的对应关系表对比例对比例1本对比例与实施例1的区别之处在于,硅胶层为硅胶套套设在钢芯上形成的层,硅胶套为对比制备例1中制备得到。
55.对比例2本对比例与实施例1的区别之处在于,硅胶层为硅胶套套设在钢芯上形成的层,硅
胶套为对比制备例2中制备得到。
56.对比例3本对比例与实施例1的区别之处在于,硅胶层为硅胶套套设在钢芯上形成的层,硅胶套为对比制备例3中制备得到。
57.对比例4本对比例与实施例1的区别之处在于,硅胶层为硅胶套套设在钢芯上形成的层,硅胶套为对比制备例4中制备得到。
58.性能检测试验检测方法/试验方法导热性能检测:参照astm-d5470《导热系数检测》中的相关检测检测方法对实施例1~17和对比例1~4中的硅胶套的导热系数进行检测。
59.拉伸性能检测:参照gb/t528-2009《硫化橡胶或热塑性橡胶拉伸应力应变性能的测定》中拉伸强度的检测方法对实施例1~17和对比例1~4中的硅胶套的导热系数进行检测。
60.压花质量评价:分别使用实施例1~17和对比例1~4中制备得到的压花辊筒进行压花,保持压花工艺操作一致,根据压印花纹纹理细节的质量进行评价。
61.表3检测数据表
结合实施例1和对比例1的检测数据可知,本技术制备得到的压花辊筒的硅胶层具有优异的导热性能,且拉伸强度较好,且应用该压花辊筒进行压花纹理细节清晰,压花质量较高。可以看出在液态硅胶内填充导热填料可以有效改善其导热性能,且合适量的导热填料对硅胶层自身的拉伸强度还具备一定的积极意义。同时选用rtv室温硫化硅橡胶使得制备工艺较为简单,对加热加压工艺条件的需求较小,有助于提高生产效率。
62.结合实施例1和实施例11的检测数据可知,预先利用硅烷偶联剂和聚乙烯酮对金
刚石微粉改性,利用硅烷偶联剂和聚丙烯酰胺对氧化铝微粉进行改性,可以有效改善金刚石微粉和氧化铝微粉在体系中的分散效果。同时改性后的金刚石微粉和氧化铝微粉可以在其表面羰基和胺基的相互作用下连接在一起,使得导热填料整体在体系中趋向于呈导热网状链的结构堆积,使得导热性能更佳。
63.结合实施例1和实施例6~7的检测数据可知,金刚石微粉和氧化铝微粉复配使用对导热性能的改善效果更佳,因两者粒径相差较大,粒径较小的金刚石微粉可以进入相邻氧化铝微粉之间的间隙中,从而增加导热填料间的有效接触,形成较为连续的热传导通道,使得导热性能更佳。
64.结合实施例1和实施例12~15的检测结果可知,金刚石微粉和氧化铝微粉的改性具有协同效果,即单独改性其中一个对导热性能的改善效果不明显,说明并不是聚乙烯酮、聚丙烯酰胺和硅烷偶联剂中的单独一个具有明显的改善效果,而是在发生交联和基团作用的情况下,而使得导热填料趋向于形成导热网状链结构。
65.本具体实施例仅仅是对本技术的解释,其并不是对本技术的限制,本领域技术人员在阅读完本说明书后可以根据需要对本实施例做出没有创造性贡献的修改,但只要在本技术的权利要求范围内都受到专利法的保护。