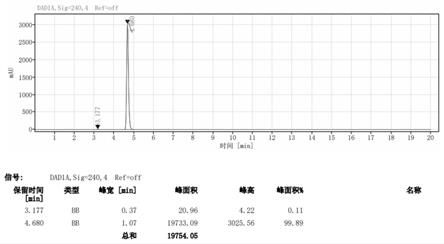
固体酸催化合成4,4
´‑
二氯二苯砜的方法
技术领域
1.本发明涉及苯砜技术领域,具体涉及一种固体酸催化合成4,4
´‑
二氯二苯砜的方法。
背景技术:2.4,4
´‑
二氯二苯砜作为一种重要的化工原料,广泛用于工程塑料、医药、染料及农药等领域,随着工程塑料聚砜的用量与日俱增,其单体4,4
´‑
二氯二苯砜的用量也随之增加,并且对4,4
´‑
二氯二苯砜的纯度、色度等指标有严苛的要求。
3.cn 106349126a采用浓硫酸作催化剂,1,2-二氯丙烷和冰醋酸为溶剂,氧化4,4
´‑
二氯二苯亚砜制备4,4
´‑
二氯二苯砜;cn107540581a采用冰醋酸为溶剂,过氧化氢与冰醋酸生成过氧乙酸氧化剂制备4,4
´‑
二氯二苯砜;cn 105732447a采用磷钨杂多酸季铵盐为催化剂,过氧化氢为氧化剂制备4,4
´‑
二氯二苯砜;cn 112608258a采用4,4
´‑
二氯二苯亚砜、1,2-二氯丙烷、水、相转移催化剂,滴加双氧水氧化得到4,4
´‑
二氯二苯砜。
4.以上专利都公开了制备4,4
´‑
二氯二苯砜的方法,采用小分子羧酸、浓硫酸、金属盐配合物或相转移剂作为氧化反应的催化剂,都存在易溶于水的缺点而难以分离回收,加入浓硫酸还可能生成芳烃磺酸,影响产品品质,强酸还存在腐蚀设备、污染环境等问题;金属盐形成的杂多酸催化剂,通常需要匹配特定的相转移剂或溶剂,因此存在制备工艺复杂、价格昂贵、适用范围小的问题。
技术实现要素:5.本发明要解决的技术问题是:克服现有技术的不足,提供一种固体酸催化合成4,4
´‑
二氯二苯砜的方法,其设计科学合理,采用的催化剂的单体来源广泛,适用于多种溶剂体系,易于从反应体系分离回用,反应后的溶剂可回收使用,对环境无污染,对设备无腐蚀,目标产物的纯度高、收率高。
6.本发明所述的固体酸催化合成4,4
´‑
二氯二苯砜的方法,是将4,4
´‑
二氯二苯亚砜、固体酸催化剂和溶剂混合升温,然后滴加过氧化氢,反应完全后,分离,将反应液进行后处理,得到所述的4,4
´‑
二氯二苯砜和水油两相混合液。
7.所述固体酸催化剂为含羧酸、磺酸、硒酸或膦酸中的至少一种官能基团的有机酸,其可以与过氧化氢作用生成过氧酸的一大类聚合物及其改性聚合物。
8.优选的,固体酸催化剂加入量为4,4
´‑
二氯二苯亚砜质量的0.5%~10%。
9.优选的,溶剂为苯、甲苯、二甲苯、氯苯、1,2-二氯丙烷或二氯乙烷中的一种或多种。
10.优选的,溶剂的加入量为4,4
´‑
二氯二苯亚砜质量的2~10倍。
11.优选的,4,4
´‑
二氯二苯亚砜与过氧化氢的摩尔比为1:1.1~3。
12.优选的,反应温度为50~80℃。
13.优选的,分离时采用过滤方法,过滤得到的催化剂放入乙醇水溶液洗涤,烘干备
用。
14.优选的,后处理包括向反应液中加入活性炭除杂脱色,过滤,滤液冷却结晶,再次过滤。
15.优选的,活性炭的加入量为4,4
´‑
二氯二苯亚砜质量的0.3%~3%。
16.所述两相混合液进行静置分液处理,分离水相,溶剂可供下一轮次反应直接使用。
17.优选的,一种固体酸催化合成4,4
´‑
二氯二苯砜的方法,包括以下步骤:(1)将4,4
´‑
二氯二苯亚砜、氯苯、固体酸催化剂投到反应釜中,搅拌并升温混合,使4,4
´‑
二氯二苯亚砜全溶于溶剂;(2)将过氧化氢逐滴加入到含4,4
´‑
二氯二苯亚砜的混合液中,氯苯的加入量为4,4
´‑
二氯二苯亚砜质量的2~6倍,升温至50~80℃,反应2~10小时;(3)反应结束后,趁热过滤出催化剂,催化剂放入乙醇水中洗涤、烘干备用;(4)向滤液中加入质量为4,4
´‑
二氯二苯亚砜质量0.3%~3%的活性炭除杂、脱色,趁热过滤出活性炭,将所得滤液冷却,再次过滤,得到滤饼和两相混合液,将滤饼真空干燥,得到高纯度4,4
´‑
二氯二苯砜;(5)将步骤(4)得到的两相混合液进行静置分液处理,溶剂相可直接用于下一轮反应。
18.本发明采用的固体酸催化剂是一类拥有多支化、网状结构的碳链聚合物,其聚合物分子链同时含羧酸基团和磺酸基团的特殊结构,通过羧酸基团和磺酸基团在溶液中电离出质子,形成的酸性环境既增强了过氧化氢的稳定性,又促进了羧酸基团与过氧化氢的结合能力,生成氧化性更强的过氧酸基团,提高4,4
´‑
二氯二苯亚砜氧化反应速率,而固体酸上过氧羧酸在氧化4,4
´‑
二氯二苯亚砜后,又重新被还原成羧酸,然后又可以继续结合过氧化氢重复上述反应过程。
19.固体酸催化剂不溶于多种有机溶剂,可在80℃长时间浸泡,简单过滤即可实现分离,并且能重复使用,很好地解决了小分子催化剂溶于水难分离回收的问题;固体酸催化剂避免了金属盐类催化剂引入的金属离子水体污染问题,避免了硫酸、乙酸带来的设备腐蚀等问题,符合绿色环保的要求。与其他催化剂相比,以高分子作为骨架的固体酸催化剂,分子结构可灵活设计,单体来源广泛,制备工艺成熟;固体酸催化剂合成的产物无异构体或其他副产物,因此产物纯度、收率都很高。
20.综上所述,固体酸催化剂可以更好的替代小分子催化剂用于4,4
´‑
二氯二苯砜合成。
21.本发明所用的过氧化氢是一种极弱的酸,其分解过程如下:,故酸性环境有利于过氧化氢稳定存在。
22.羧酸类有机物在酸性条件下,生成过氧乙酸过程: 。
23.固体酸催化剂参与4,4
´‑
二氯二苯亚砜氧化过程如下:
。
24.与现有技术相比,本发明具有以下有益效果:(1)本发明采用固体酸催化剂,其分子结构可根据需求灵活设计,单体来源广泛,对环境无污染,对设备无腐蚀,易于从反应体系分离,可重复使用,适用于多种溶剂体系,产品收率高、纯度高;(2)本发明对产生的油水两相混合溶液处理方法简单,成本低,处理后的溶剂可直接用于下一轮反应使用,利用率高,节约成本。
附图说明
25.图1为实施例3制备的4,4
´‑
二氯二苯砜的hplc图;图2为实施例4制备的4,4
´‑
二氯二苯砜的hplc图;图3为对比例1制备的4,4
´‑
二氯二苯砜的hplc图;图4为对比例2制备的4,4
´‑
二氯二苯砜的hplc图。
具体实施方式
26.以下结合实施例对本发明做进一步说明。
27.固体酸催化剂市售或者自行合成均可。
28.实施例中所用其他原料除均为市售。
29.本发明提供一种固体酸催化剂的合成方法,为本领域技术人员公知方法,具体包括以下步骤:第一步、单酯化合物的制备:称取28.01g 3-羟基丙磺酸、23.20g富马酸溶于400.00g乙酸乙酯,50℃搅拌6小时,蒸馏除去乙酸乙酯,得到含烯烃、羧酸基、磺酸基的单酯化合物。反应方程式如下:
ꢀ
。
30.第二步、合成固体酸催化剂:取23.80g单酯化合物溶于300.00g乙醇,加入0.15g过氧化苯甲酰,升温至70℃搅拌2小时形成低聚物,再加13.02g二乙烯基苯、56.00g1-辛烯、0.35g过氧化苯甲酰、20.00g甲苯(制孔剂)、2.00g十二烷基硫酸钠(分散剂),升温80℃搅拌5小时,过滤,100℃真空干燥12小时,60目和100目过筛,得到多孔微球固体酸催化剂。
31.所制得的固体酸催化剂酸强度为2.07mmol/g[h
+
],堆积密度0.80g/ml,骨架密度1.22g/ml,平均孔径35nm,比表面积40m2/g,孔容0.25ml/g,粒度为0.10~0.30mm占95%。
[0032]
实施例1将135.58g(0.5mol)4,4
´‑
二氯二苯亚砜、271.50g氯苯、制备的1.00g催化剂投到反应釜中,搅拌并升温至50℃,使4,4
´‑
二氯二苯亚砜全溶于溶剂,将65.00g 30%过氧化氢逐滴加入到含4,4
´‑
二氯二苯亚砜的混合液中;tlc薄层色谱法监测反应进程,待反应结束后,趁热过滤出催化剂,将催化剂浸入乙醇水溶液中洗涤,真空干燥备用;向滤液中加入0.5g活性炭除杂、脱色,趁热过滤出活性炭,将所得滤液冷却至5℃,冷却结晶2小时,再次过滤,得到湿产品和水油两相混合液,将湿产品在100℃真空干燥12小时得到4,4
´‑
二氯二苯砜;得到的两相混合液进行静置分液处理,溶剂相直接用于下一轮反应。
[0033]
实施例2将135.58g(0.5mol)4,4
´‑
二氯二苯亚砜、401.50g氯苯、制备的2.50g催化剂投到反应釜中,搅拌并升温至50℃,使4,4
´‑
二氯二苯亚砜全溶于溶剂,将78.00g 30%过氧化氢逐滴加入到含4,4
´‑
二氯二苯亚砜的混合液中;tlc薄层色谱法监测反应进程,待反应结束后,趁热过滤出催化剂,将催化剂浸入乙醇水溶液中洗涤,真空干燥备用;向滤液中加入0.80g活性炭除杂、脱色,趁热过滤出活性炭,将所得滤液冷却至5℃,冷却结晶2小时,再次过滤,得到湿产品和水油两相混合液,将湿产品在100℃真空干燥12小时得到4,4
´‑
二氯二苯砜;得到的两相混合液进行静置分液处理,溶剂相直接用于下一轮反应。
[0034]
实施例3将135.58g(0.5mol)4,4
´‑
二氯二苯亚砜、531.50g 1,2-二氯丙烷、制备的4.00g催化剂投到反应釜中,搅拌并升温至55℃,使4,4
´‑
二氯二苯亚砜全溶于溶剂,将91.00g30%过氧化氢逐滴加入到含4,4
´‑
二氯二苯亚砜的混合液中;tlc薄层色谱法监测反应进程,待反应结束后,趁热过滤出催化剂,将催化剂浸入乙醇水溶液中洗涤,真空干燥备用;向滤液中加入1.10g活性炭除杂、脱色,趁热过滤出活性炭,将所得滤液冷却至5℃,冷却结晶2小时,再次过滤,得到湿产品和水油两相混合液,将湿产品在100℃真空干燥12小时得到4,4
´‑
二氯二苯砜;得到的两相混合液进行静置分液处理,溶剂相直接用于下一轮反应。
[0035]
实施例4将135.58g(0.5mol)4,4
´‑
二氯二苯亚砜、661.50g 1,2-二氯丙烷、制备的5.50g催化剂投到反应釜中,搅拌并升温至60℃,使4,4
´‑
二氯二苯亚砜全溶于溶剂,将104.00g30%过氧化氢逐滴加入到含4,4
´‑
二氯二苯亚砜的混合液中;tlc薄层色谱法监测反应进程,待反应结束后,趁热过滤出催化剂,将催化剂浸入乙醇水溶液中洗涤,真空干燥备用;向滤液中加入1.40g活性炭除杂、脱色,趁热过滤出活性炭,将所得滤液冷却至5℃,冷却结晶2小
时,再次过滤,得到湿产品和水油两相混合液,将湿产品在100℃真空干燥12小时得到4,4
´‑
二氯二苯砜;得到的两相混合液进行静置分液处理,溶剂相直接用于下一轮反应。
[0036]
实施例5将135.58g(0.5mol)4,4
´‑
二氯二苯亚砜、791.50g 1,2-二氯丙烷、制备的7.00g催化剂投到反应釜中,搅拌并升温至60℃,使4,4
´‑
二氯二苯亚砜全溶于溶剂,将117.00g30%过氧化氢逐滴加入到含4,4
´‑
二氯二苯亚砜的混合液中;tlc薄层色谱法监测反应进程,待反应结束后,趁热过滤出催化剂,将催化剂浸入乙醇水溶液中洗涤,真空干燥备用;向滤液中加入1.70g活性炭除杂、脱色,趁热过滤出活性炭,将所得滤液冷却至5℃,冷却结晶2小时,再次过滤,得到湿产品和水油两相混合液,将湿产品在100℃真空干燥12小时得到4,4
´‑
二氯二苯砜;得到的两相混合液进行静置分液处理,溶剂相直接用于下一轮反应。
[0037]
实施例6将135.58g(0.5mol)4,4
´‑
二氯二苯亚砜、921.50g 1,2-二氯丙烷、制备的8.50g催化剂投到反应釜中,搅拌并升温至75℃,使4,4
´‑
二氯二苯亚砜全溶于溶剂,将130.00g 30%过氧化氢逐滴加入到含4,4
´‑
二氯二苯亚砜的混合液中;tlc薄层色谱法监测反应进程,待反应结束后,趁热过滤出催化剂,将催化剂浸入乙醇水溶液中洗涤,真空干燥备用;向滤液中加入2.00g活性炭除杂、脱色,趁热过滤出活性炭,将所得滤液冷却至5℃,冷却结晶2小时,再次过滤,得到湿产品和水油两相混合液,将湿产品在100℃真空干燥12小时得到4,4
´‑
二氯二苯砜;得到的两相混合液进行静置分液处理,溶剂相直接用于下一轮反应。
[0038]
实施例7将135.58g(0.5mol)4,4
´‑
二氯二苯亚砜、921.50g 1,2-二氯丙烷、制备的10.00g催化剂投到反应釜中,搅拌并升温至75℃,使4,4
´‑
二氯二苯亚砜全溶于溶剂,将130.00g 30%过氧化氢逐滴加入到含4,4
´‑
二氯二苯亚砜的混合液中;tlc薄层色谱法监测反应进程,待反应结束后,趁热过滤出催化剂,将催化剂浸入乙醇水溶液中洗涤,真空干燥备用;向滤液中加入2.00g活性炭除杂、脱色,趁热过滤出活性炭,将所得滤液冷却至5℃,冷却结晶2小时,再次过滤,得到湿产品和水油两相混合液,将湿产品在100℃真空干燥12小时得到4,4
´‑
二氯二苯砜;得到的两相混合液进行静置分液处理,溶剂相直接用于下一轮反应。
[0039]
实施例8将135.58g(0.5mol)4,4
´‑
二氯二苯亚砜、921.50g 1,2-二氯丙烷、制备的12.00g催化剂投到反应釜中,搅拌并升温至75℃,使4,4
´‑
二氯二苯亚砜全溶于溶剂,将130.00g 30%过氧化氢逐滴加入到含4,4
´‑
二氯二苯亚砜的混合液中;tlc薄层色谱法监测反应进程,待反应结束后,趁热过滤出催化剂,将催化剂浸入乙醇水溶液中洗涤,真空干燥备用;向滤液中加入2.00g活性炭除杂、脱色,趁热过滤出活性炭,将所得滤液冷却至5℃,冷却结晶2小时,再次过滤,得到湿产品和水油两相混合液,将湿产品在100℃真空干燥12小时得到4,4
´‑
二氯二苯砜;得到的两相混合液进行静置分液处理,溶剂相直接用于下一轮反应。
[0040]
实施例9将135.58g(0.5mol)4,4
´‑
二氯二苯亚砜、1311.50g 1,2-二氯丙烷、制备的13.50g催化剂投到反应釜中,搅拌并升温至80℃,使4,4
´‑
二氯二苯亚砜全溶于溶剂,将169.00g30%过氧化氢逐滴加入到含4,4
´‑
二氯二苯亚砜的混合液中;tlc薄层色谱法监测反应进程,待反应结束后,趁热过滤出催化剂,将催化剂浸入乙醇水溶液中洗涤,真空干燥备
用;向滤液中加入2.90g活性炭除杂、脱色,趁热过滤出活性炭,将所得滤液冷却至5℃,冷却结晶2小时,再次过滤,得到湿产品和水油两相混合液,将湿产品在100℃真空干燥12小时得到4,4
´‑
二氯二苯砜;得到的两相混合液进行静置分液处理,溶剂相直接用于下一轮反应。
[0041]
实施例10-14所述的固体酸催化剂制备4,4
´‑
二氯二苯砜方法,按照实施例3相同的合成条件,对实施例3处理后的备用固体酸催化剂进行循环使用,依次为实施例10、实施例11、实施例12、实施例13、实施例14,用hplc检测产品,计算产品收率和催化剂收率。
[0042]
将实施例1-14所合成的4,4
´‑
二氯二苯砜的收率和纯度以及对应的催化剂的收率进行计算与检测,其结果如表1所示。
[0043]
表1对比例1将135.58g(0.5mol)4,4
´‑
二氯二苯亚砜、531.50g 1,2-二氯丙烷、35.00g乙酸投到反应釜中,搅拌并升温至55℃,使4,4
´‑
二氯二苯亚砜全溶于溶剂,将91.00g 30%过氧化氢逐滴加入到含4,4
´‑
二氯二苯亚砜的混合液中;tlc薄层色谱法监测反应进程,待反应结束后,向滤液中加入1.10g活性炭除杂、脱色,趁热过滤出活性炭,将所得滤液冷却至5℃,冷却结晶2小时,再次过滤,得到湿产品和水油两相混合液,将湿产品在100℃真空干燥12小时,得到4,4
´‑
二氯二苯砜纯度为:99.21%,收率为95.62%。
[0044]
两相混合液静置分液,水相包括乙酸和水,油相包括1,2-二氯丙烷和乙酸,通过真空蒸馏水相和油相,难以得到质量分数大于70%的乙酸。
[0045]
对比例2
将135.58g(0.5mol)4,4
´‑
二氯二苯亚砜、531.50g 1,2-二氯丙烷、35.00g乙酸、8.25g浓硫酸投到反应釜中,搅拌并升温至55℃,使4,4
´‑
二氯二苯亚砜全溶于溶剂,将91.00g30%过氧化氢逐滴加入到含4,4
´‑
二氯二苯亚砜的混合液中;tlc薄层色谱法监测反应进程,待反应结束后,向滤液中加入1.10g活性炭除杂、脱色,趁热过滤出活性炭,将所得滤液冷却至5℃,冷却结晶2小时,再次过滤,得到湿产品和水油两相混合液,将湿产品在100℃真空干燥12小时,得到4,4
´‑
二氯二苯砜纯度为:99.63%,收率为96.84%。
[0046]
两相混合液静置分液,水相包括乙酸、硫酸和水,油相包括1,2-二氯丙烷和乙酸,通过真空蒸馏水相和油相,难以得到质量分数大于70%的乙酸。
[0047]
根据实施例3的纯度、收率数据可知,固体酸催化剂对4,4
´‑
二氯二苯砜的合成体现出非常好的催化活性,所得产品最高能够达到99.89%的纯度,并且对回收的催化剂进行套用,循环5次后,4,4
´‑
二氯二苯砜的纯度仍能达到99.81%,实施例6、7、8改变催化剂用量,纯度和收率几乎不变,证明催化剂的用量已经达到饱和。对比使用乙酸作为催化剂,得到的4,4
´‑
二氯二苯砜纯度为99.21%,对比例2在乙酸的基础上加入浓硫酸催化,谱图出现了杂质峰,该杂质极性较强很有可能是生成了芳基磺酸化合物,影响产品品质,并且反应结束后硫酸和乙酸、水、有机溶剂组成的混合液,成份复杂难以分离,产生的废酸污染环境,腐蚀设备。而本发明使用的固体酸催化剂,只需通过过滤即可实现回收,解决了小分子催化剂难分离的问题,减少了废水废液的产生,节约了成本,催化选择性高、易分离回收、能够循环利用,是一种绿色环保型催化剂。
[0048]
上述内容仅为本发明的较佳实施例,不能被认为用于限定对本发明的实施例范围。本发明也并不仅限于上述举例,本技术领域的普通技术人员在本发明的实质范围内所做出的均等变化与改进等,均应归属于本发明的专利涵盖范围内。