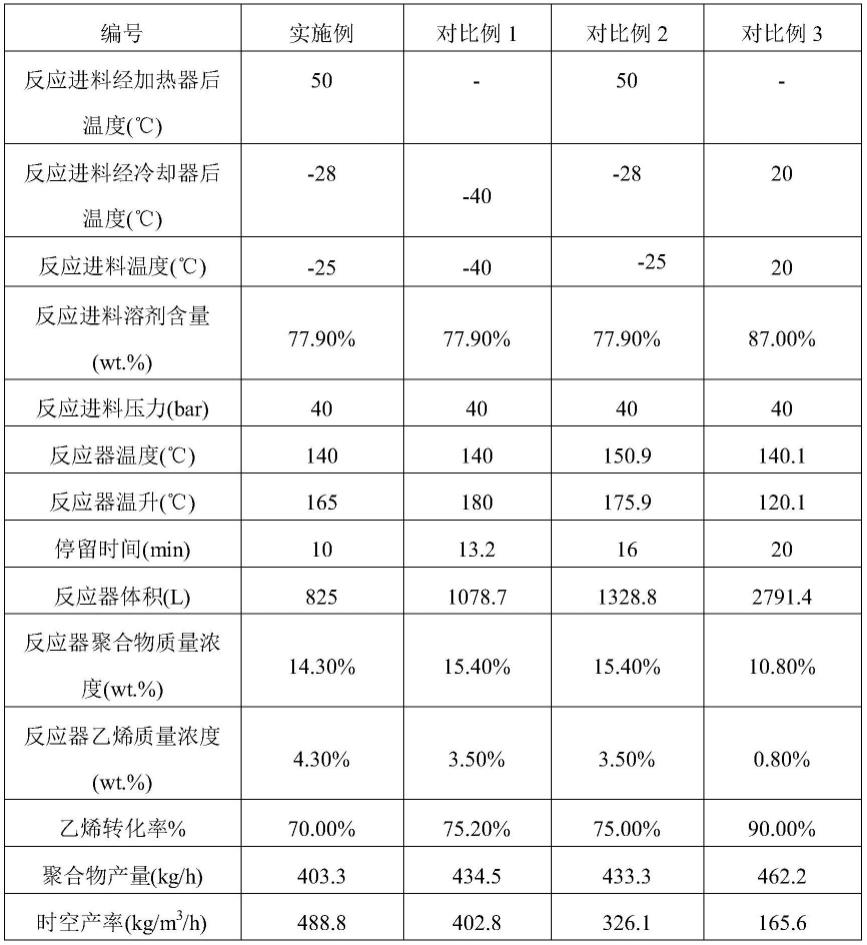
一种乙烯和
α-烯烃的溶液聚合方法
技术领域
1.本发明属于聚烯烃领域,具体涉及乙烯和α-烯烃溶液聚合领域,更具体涉及一种提高溶液聚合反应时空产率的方法。
背景技术:2.乙烯聚合是一个强放热反应,为了提高反应效率,通常要求以较高的速率移除反应热,以确保催化剂反应活性。气相法聚合工艺可通过加入冷凝剂调节反应温度,如专利cn 110023346 b提供了一种方法使用丙烷和异丁烷为冷凝剂的气相烯烃聚合方法,该方法包括使一种或多种单体、至少一种催化剂体系和冷凝剂在聚合条件下接触以得到聚合物,冷凝剂包含至少25mol%丙烯和至少20ml%异丁烷。淤浆法聚合工艺通过溶剂气化、夹套移热或外循环的方式控制反应器温度,如专利cn 110918018 a发明一种淤浆釜式聚乙烯反应器组合撤热方法,将淤浆外循环、溶剂蒸发和反应釜夹套三种撤热方法进行组合并同时运用,以强化撤热效果。
3.溶液法聚合工艺反应速率快,停留时间较短,且聚合物溶液粘度高,传热系数小,反应器夹套移热的效率较低。此外,溶液法聚乙烯工艺需维持较高温度,以降低聚合物溶液的粘度。因此,溶液法聚烯烃工艺通常采用绝热反应器。绝热反应器是指不与外界进行热交换的反应器。溶液法聚合是指将聚合物溶解在液体聚合体系中的聚合过程,所述液体聚合体系如惰性溶剂和单体。选择合适的溶液聚合的温度和压力以确保反应器中的单一均匀聚合相。如,专利cn 103880999 b描述了一种乙烯和α-烯烃在混合有机溶剂中的溶液聚合方法,聚合温度和压力高于混合溶剂中超临界流体的超临界温度和压力,从而降低了聚合物体系粘度。
4.绝热反应器的特征在于,聚合反应热将转化为进料和出料的温升。反应程度越大,即乙烯单体转化率越高,其聚合物溶液的温升就越大。对于乙烯和α-烯烃聚合反应而言,其反应温度同时还受催化剂活性范围的约束,过高的反应温度可能导致催化剂失活,所以溶液法聚合通常要求低温进料,以控制反应温度。cn 107614541 b描述一种连续溶液聚合方法,用冷冻机将进料冷却低至50~-15℃,聚合热使温度升高到约85~150℃,出口聚合物浓度范围在8wt.%~15wt.%。
5.反应进料的温度、组成以及反应器的停留时间,共同影响反应器的时空产率,同时也决定了进料单元和分离及回收单元的能耗。时空产率是指单位时间内可生产的聚合物量与反应设备体积之间的比值,是衡量生产效率的重要指标。
6.提高时空产率是提高烯烃聚合工艺生产能力的关键。上述专利cn 110023346 b提出一种使用丙烷和异丁烷为冷凝剂的气相乙烯聚合工艺,生产率比使异戊烷为冷凝剂的相同方法高至少5%,时空产率大于224kg/m3/h。专利cn 109996818b也发明一种使用至少两种冷凝剂的气相烯烃聚合方法,冷凝剂的最佳蒸汽压由如下公式614
–
716*d+2.338*p+3.603*ln(mi)确定,其中d为聚合物密度,p为聚合压力,mi为聚合物熔体指数,该方法时空产率大于250kg/m3/h。专利cn 103328518 b提出一种在具有至少250m3的第一体积的垂直流
化床反应器中连续气相烯烃聚合的方法,其冷凝率高于15%,在催化剂存在和在不小于120kg/m3/h的时空产率下操作。
7.针对聚烯烃溶液聚合工艺,也有相关专利提出提高生产效率的方法,如cn1283204a描述了一种在烯烃溶液聚合反应工艺中用于反应器出口流股聚合物含量的方法,该方法至少一个反应器中、在足够量的溶剂中聚合生产聚合物含量为3-24wt.%的聚合物溶液,聚合温度为150-260℃,其采用的反应器为“沸腾反应器”,是一种可以闪蒸反应器内聚合物反应溶液的反应器,即反应器内同时存在液相和气相,部分单体和溶剂通过蒸汽化离开反应器,可以去除部分反应热。但是,尚未有相关专利对如何提高溶液法聚乙烯工艺的时空产率做明确说明。
8.对于溶液聚合,降低进料流股的温度,反应溶液温升可以吸收更多的反应热,即反应转化率可以更高。然而,高转化率会导致反应速率较低,进而导致时空产率较低。此外,工业生产过程中,流股冷却温度受冷公用工程的制约,过低的进料温度导致生产成本增大。针对难以实现乙烯和α-烯烃溶液聚合的高时空产率和低工艺能耗的难题,需要寻找一种新的方法,能够兼顾工艺能耗和时空产率。
9.定义:
[0010]“α-烯烃”是指双键在分子链端部的单烯烃,如1-丁烯、1-己烯、1-辛烯。
[0011]“聚合物”是乙烯与α-烯烃共聚单体的聚合物。
[0012]“连续”是指没有间断地运行的系统。如,连续将反应物引入一个或多个反应器,并连续取出聚合物产物。
[0013]“换热器”是用来使热量从热流体传递到冷流体以满足规定的工艺要求的装置。在化工、石油、动力、食品及其它许多工业生产中占有重要地位,尤其是在化工生产中换热器可作为加热器、冷却器、冷凝器、蒸发器和再沸器等,应用广泛。
[0014]“分离系统”是一个包括多步分离和回收操作的系统,其目的通常是将聚合反应所得的聚合物从聚合物溶液中分离出,并获得可循环回用的单体、共聚单体、溶剂组分,和/或去除杂质组分。烯烃聚合生产工艺的分离系统通常包含多级闪蒸、脱挥、循环、挤出等过程。
[0015]“闪蒸分离”表示通过压力降低导致相分离的分离步骤。
[0016]“反应速率”是指化学反应中反应物转变为生成物(也成为产物)的速度,反应速率通常表达为单位时间和单位反应器体积内反应物转变为生成物的摩尔量,如mol/(l
·
s)、mol/(l
·
min)等。
技术实现要素:[0017]
为了克服现有技术中的问题,本发明提供一种乙烯与α-烯烃共聚的溶液聚合方法,所述方法包含:乙烯、α-烯烃和溶剂经进料单元(1)混合和调节温度后得到反应进料流股,将该流股送入反应单元(2)中,在催化剂作用下得到包含乙烯和α-烯烃的聚合物的溶液,将所述反应单元(2)的聚合物溶液出料到分离和回收单元(3)中,得到包含未反应乙烯、α-烯烃和溶剂的循环物流以及聚合物产品。
[0018]
其特征在于,控制反应器温升为130~180℃,即出料流股和进料流股温度差为130~180℃,反应进料流股中溶剂的质量浓度为70~85wt.%,反应单元的停留时间为5~15min。
[0019]
根据本发明方法,通过反应操作条件的控制,使乙烯转化率在70%以上,和/或反应单元出口聚合物溶液的聚合物质量浓度为10~20wt.%,和/或时空产率在450kg乙烯和α-烯烃共聚物每立方米反应体积每小时(kg/m3/h)以上。
[0020]
根据本发明方法,其中所述反应进料流股温度为-30~0℃,优选-30~-18℃。
[0021]
根据本发明方法,其中所述反应进料流股温度由一个加热器和一个冷却器并联控制,从而温度控制更精准,时空产率始终在最高值运行。
[0022]
根据本发明方法,其中所述溶剂选自c4~c12的链状烷烃或环烷烃、c6~c9的芳香烃或其混合溶剂,优选c5~c8链状烷烃或环烷烃。
[0023]
根据本发明方法,所述反应单元(2)包含至少一个绝热溶液聚合反应器。
[0024]
根据本发明方法,其中所述α-烯烃为c3~c12的烯烃,优选c4~c8的α-烯烃。
[0025]
根据本发明方法,所述反应单元的反应器压力在30~200bar,优选35~50bar。
[0026]
根据本发明方法,所述反应单元的反应器温度在100~220℃,优选120~180℃。
[0027]
本发明的目的在于克服现有技术的不足,提供一种通过调节进料温度及组成、反应停留时间,控制乙烯转化率,使其时空产率在较优范围,在450kg乙烯和α-烯烃共聚物每立方米反应体积每小时(kg/m3/h)以上。
[0028]
与现有技术相比,本发明具有以下优势:1)通过低温进料实现较高的聚合物溶液的聚合物含量;2)多个牌号的低温进料需求均可通过丙烯制冷实现,降低冷公用工程系统投资;3)控制反应停留时间,兼顾单体转化率和反应速率;4)时空产率高。
附图说明
[0029]
图1是本发明整体结构示意图。
[0030]
图中,1-进料单元;2-反应单元;3-分离和回收单元;4-乙烯;5-α-烯烃;6-溶剂;7-催化剂;8-反应进料流股;9-聚合物溶液;10-循环流股;11-聚合物产品。
具体实施方式
[0031]
下面结合具体实施方式对本发明做进一步阐述和说明。所述实施例仅是本公开内容的示范且不圈定限制范围。本发明中各个实施方式的技术特征在没有相互冲突的前提下,均可进行相应组合。
[0032]
如图1所示,乙烯4、α-烯烃5和溶剂6经进料单元1混合和调节温度后得到反应进料流股8,将该反应进料流股8送入反应单元2中,在催化剂7作用下得到包含乙烯和α-烯烃的聚合物溶液9,将所述反应单元2的聚合物溶液9出料到分离和回收单元3中,得到包含未反应乙烯、α-烯烃和溶剂的循环流股10以及聚合物产品11。本发明主要进料包括乙烯单体、α-烯烃共聚单体和溶剂,如本领域已知,乙烯和α-烯烃共聚合是生产具有不同密度、分子量等性质的方法,如乙烯和1-辛烯生产线性低密度聚乙烯(lldpe)。溶剂在不同聚合工艺中所起的作用不完全相同,如本领域已知,溶液聚合需要大量的溶剂,维持乙烯单体、α-烯烃共聚单体、催化剂、分子量调节剂以及聚合物产品在反应器处于单一相态。溶剂需对催化剂体系和反应物而言呈惰性,且在反应过程中保持稳定,正己烷是一种本领域已知,并广泛采用的一种。
[0033]
如本领域已知,乙烯和α-烯烃聚合需在催化剂作用下进料,催化剂可以是本领域
已知的能将乙烯与α-烯烃共聚单体共聚的任何催化剂,包括z-n催化剂和茂金属催化剂,如主催化剂为限定几何构型催化剂(cgc),助催化剂为甲基铝氧烷(mao)。
[0034]
如本领域已知,常通过添加少量链转移常数大的物质用以降低聚合物分子量,即分子量调节剂,合适的链转移剂有多种,常用的如氢气。图1中虽未展示氢气的进料管线,但是本方法可以包含使用氢气以控制共聚物分子量的方法,氢气的加入方式取决于氢气的条件,既可以通过进料单元,混合后进料,也可以单独进料至反应单元。
[0035]
聚合物溶液离开反应器,进入分离阶段前需先终止反应,即使催化剂失活,以未反应单体和共聚单体在分离阶段继续反应,导致分子量过大或放热难以控制,使催化剂失活的物质(失活剂)有许多,如本领域已知,可以加入水使催化剂失活。
[0036]
聚合物溶液进入分离系统之前通常还需进行升温,以获得更好的气液分离效果,脱除聚合物溶液中的挥发性组分。如本领域已知,换热器是用来将热量从热流体传递到冷流体以满足工艺要求的设备。在本方法中,换热器用于控制离开反应单元的聚合溶液温度,使到达分离系统指定温度。
[0037]
如本领域已知,聚合物分离系统是一个包括多步分离、回收操作的系统,通常包含多个闪蒸、精馏、循环、挤出等过程,当仅考虑两闪蒸时,将来自换热器出口的加热聚合物溶液进料到闪蒸罐进行分离,将顶部气相流股输送至热量回收单元,部分输送至进料单元循环到反应单元,剩余流股输送至下游精馏操作,底部液相流股送入第二级闪蒸罐中继续进行分离,送入第二级闪蒸单元之前根据要求调节温度。
[0038]
下面结合实施例和对比例(详细结果见表1)进一步描述本发明方法,需申明此处实施例仅用于解释本发明,并不用限定本发明。
[0039]
实施例,按本发明所述方法进行,进料包括乙烯单体,流量400kg/h,共聚单体为1-辛烯,流量225kg/h,溶剂为正己烷,进料2200kg/h。单体、共聚单体和溶剂混合后,调节温度至-25℃,进入反应釜。进料流股通过分流为两条流股,一条流股(2726.125kg/h)经冷却器调节温度至-28℃,另一条流股(98.875kg/h)经加热器调节温度至50℃,混合后进料流股达到制定的-25℃。主催化剂为cgc,助催化剂为mao,将0.02kg/h主催化剂和0.2kg/h的助催化剂溶于2kg/h的正己烷溶剂,注入反应器。分子量调节剂选用氢气,通入0.2kg/h。反应器采用绝热釜式反应器,内设搅拌部件,反应压力40bar,停留时间为10min。分离系统采用三级闪蒸方式,第一级为中压闪蒸,压力为15bar,温度为200℃;第二级为低压闪蒸i,压力为3bar,温度为190℃。第三级为低压闪蒸ii,压力为1bar,温度为190℃。三级闪蒸之后,聚合物溶液进入挤出机,得到聚合物。
[0040]
在实施例的反应条件下,反应器温度为140℃,出口聚合物溶液含聚合物403.3kg/h,时空产率为488.8kg/m3/h。
[0041]
对比例1,该对比例与实施例使用类似的方法进行烯烃聚合,区别在于进料温度更低,为-40℃,即聚合物溶液可以吸收更多反应热,增加停留时间至13.2min,乙烯的转化率更高,反应器温度也为140℃,出口聚合物溶液含聚合物434.5kg/h,时空产率为402.8kg/m3/h。对比例1中进料温度仅通过一个冷却器实现。
[0042]
实施例与对比例1相比,时空产率更高。对比例1通过降低反应进料温度,使乙烯的转化率更高,但是停留时间的增长,故时空产率较低,即对比例1反应器设备投资所带来收益小;且对比例1进料冷却温度低至-40℃,公用工程费用更高。
[0043]
对比例2,该对比例与实施例和对比例1使用类似的方法进行烯烃聚合,区别在于保持-25℃反应进料温度的情况下,增加停留时间至16min,乙烯的转化率比实施例更高,反应器温度达150.9℃,出口聚合物溶液含聚合物433.3kg/h,时空产率为326.1kg/m3/h。
[0044]
实施例与对比例2相比,时空产率更高。对比例2通过增加反应停留时间,使乙烯的转化率更高,即聚合物产量更大,但是其时空产率较低。
[0045]
对比例3,该对比例与实施例使用类似的方法进行烯烃聚合,区别在于增加反应进料流股的溶剂流量至4200kg/h,反应进料温度为20℃,停留时间至20min。反应器温度为140.1℃,乙烯的转化率达90%,出口聚合物溶液含聚合物462.2kg/h,但时空产率仅为165.6kg/m3/h。对比例3中进料温度仅通过一个冷却器实现。
[0046]
实施例与对比例3相比,时空产率更高。对比例3通过增加反应进料流股的溶剂含量,以提高反应进料流股的冷却温度,并增加反应停留时间以提高乙烯转化率,但是其时空产率较低。
[0047]
表1
[0048]
[0049]
以上所述实施例仅表达了本发明的几种实施方式,其描述较为具体和详细,但并不能因此而理解为对本发明专利范围的限制。对于本领域的普通技术人员来说,在不脱离本发明构思的前提下,还可以做出若干变形和改进,这些都属于本发明的保护范围。