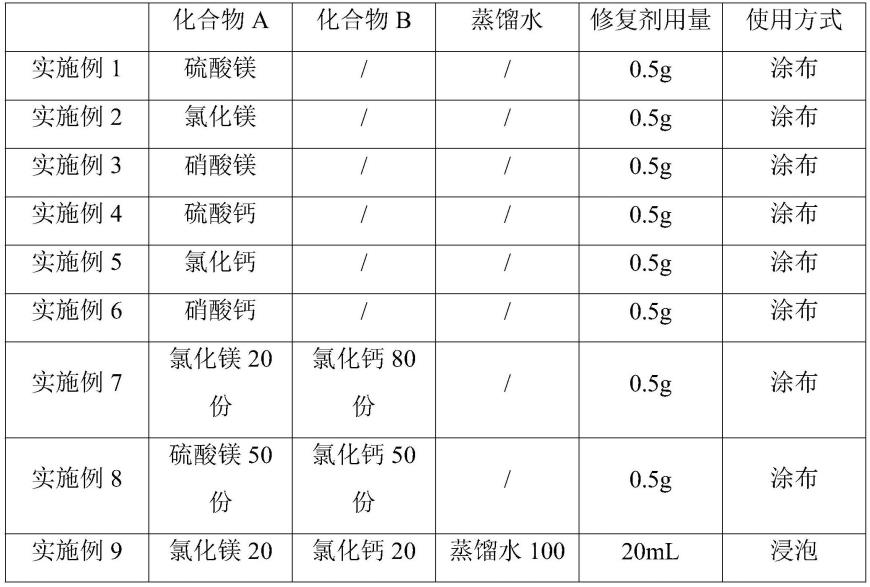
1.本发明涉及材料修复技术领域,特别是涉及一种丙烯酸盐聚合物材料的修复方法。
背景技术:2.丙烯酸盐聚合物是一种以丙烯酸盐为单体的高分子聚合物,它的主链与聚丙烯酸一样,但其侧链则是羧酸阳离子盐。大多数的丙烯酸盐聚合物都具有模量高、刚性大、耐热和绝缘性好等优点,被广泛应用于电子、机械、建筑工程等领域。在建筑工程领域,我国水利水电科学研究院和长江科学院先后于80年代中后期,在前人工作的基础上研发丙烯酸盐化学灌浆材料,其作用和原理是在一定引发剂下丙烯酸盐聚合成不溶于水的丙烯酸盐胶凝体聚合物并实现防渗堵漏的效果,此类材料也在长江三峡等工程上得到应用。
3.然而,在丙烯酸盐聚合物材料应用于多个领域的同时,其简便环保的材料修复方法却鲜有研究。以建筑工程领域用到的丙烯酸镁防水材料为例,该材料的聚合物不溶于水且喷涂成膜后有很好的黏着力,但当其经历强酸、强碱或高盐含量等环境后,聚合物材料会出现一定的降解,严重影响其防水能力。目前,只能通过重新施工或其它工法改变来克服此问题,但是这些方法都需要花费大量人力物力,会导致施工成本的巨大上升。
4.因此,有必要提供一种施工后的丙烯酸盐聚合物材料的修复方法,使其修复过程更简便环保。
技术实现要素:5.基于此,鉴于上述现有技术的不足,本发明的一个主要目的在于提供一种简便地丙烯酸盐聚合物材料的修复方法。
6.这了达到上述发明目的,本发明包括如下技术方案。
7.一种丙烯酸盐聚合物材料的修复方法,包括如下步骤:
8.(1)在待修复的丙烯酸盐聚合物材料的表面涂布修复化合物;和/或,
9.(2)用含有所述修复化合物的溶液浸泡或涂布或喷淋待修复的丙烯酸盐聚合物材料;
10.所述修复化合物由一种或者多种阳离子盐组成,其中,至少一种阳离子盐为二价阳离子盐或者大于二价的阳离子盐。
11.在其中一些实施例中,所述二价阳离子盐或者大于二价的阳离子盐中的阳离子选自:镁离子、钙离子、铝离子、锶离子、钡离子、钪离子、钇离子、钛离子、锆离子、钒离子、铌离子、铬离子、钼离子、锰离子、铁离子、钴离子、镍离子、铜离子、锌离子、镉离子、汞离子、镓离子、铟离子、铊离子、锗离子、锡离子、铅离子、锑离子、铋离子。
12.在其中一些实施例中,所述二价阳离子盐或者大于二价的阳离子盐中的阳离子选自:镁离子、钙离子、铝离子、铁离子、钴离子、镍离子、铜离子、锌离子。
13.在其中一些实施例中,所述修复化合物由一种或者多种阳离子盐组成,所述阳离
子盐为二价阳离子盐和/或大于二价的阳离子盐。
14.在其中一些实施例中,所述阳离子盐选自:硫酸镁、氯化镁、硝酸镁、硫酸钙、氯化钙、硝酸钙。
15.在其中一些实施例中,所述修复化合物的用量与所述丙烯酸盐聚合物材料的质量比为0.0001-10000:1,优选为0.1-100:1。具体用量需要根据待修复的丙烯酸盐聚合物材料的受损(分解或者降解)程度确定,如果受损严重,修复化合物的用量可以多一些,如果只是轻微的受损,用少量修复化合物即可获得很好的的修复效果。
16.在其中一些实施例中,所述含有所述修复化合物的溶液是以水作为溶剂的水溶液。
17.在其中一些实施例中,所述含有所述修复化合物的溶液中所述修复化合物的质量浓度为0.00001%~80%,优选为1%~60%,更优选为15%~30%。
18.在其中一些实施例中,所述丙烯酸盐聚合物材料是经历强酸、强碱和/或高盐环境后出现降解或分解的丙烯酸盐聚合物材料。
19.在其中一些实施例中,所述丙烯酸盐聚合物材料选自:丙烯酸镁盐聚合物、丙烯酸钙盐聚合物、丙烯酸铝盐聚合物、丙烯酸锶盐聚合物、丙烯酸钡盐聚合物、丙烯酸钪盐聚合物、丙烯酸钇盐聚合物、丙烯酸钛盐聚合物、丙烯酸锆盐聚合物、丙烯酸钒盐聚合物、丙烯酸铌盐聚合物、丙烯酸铬盐聚合物、丙烯酸钼盐聚合物、丙烯酸锰盐聚合物、丙烯酸铁盐聚合物、丙烯酸钴盐聚合物、丙烯酸镍盐聚合物、丙烯酸铜盐聚合物、丙烯酸锌盐聚合物、丙烯酸镉盐聚合物、丙烯酸汞盐聚合物、丙烯酸镓盐聚合物、丙烯酸铟盐聚合物、丙烯酸铊盐聚合物、丙烯酸锗盐聚合物、锡盐聚合物、丙烯酸铅盐聚合物、丙烯酸锑盐聚合物、丙烯酸铋盐聚合物。
20.在其中一些实施例中,所述修复方法的操作温度为-30℃~70℃,优选0℃~45℃,更优选为25
±
5℃。
21.在其中一些实施例中,所述修复方法的修复时间为0.1min-24小时,更优选为0.1min-16小时;所述修复时间是指涂布后的反应时间,或者浸泡的时间。具体修复时间需要根据待修复的丙烯酸盐聚合物材料的受损(分解或者降解)程度确定,如果只是轻微的受损,用少量修复化合物涂布或者浸泡后即可立马获得很好的修复效果;如果受损严重,延长修复时间,或者增加修复化合物的用量同样能够获得很好的修复效果。
22.本发明的丙烯酸盐聚合物材料的修复方法具有以下有益效果:
23.本发明的修复方法,对于经历强酸、强碱或高盐含量等环境后的丙烯酸盐聚合物材料具有良好的修复效果,修复后的丙烯酸盐聚合物材料的机械性能和化学性能均可恢复到降解前的水平,克服了现有技术的不足,实现了丙烯酸盐聚合物材料的简便修复,可应用在电子器件、机械设备、建筑工程或防水工程的材料修复中。并且,本发明的丙烯酸盐聚合物的修复方法使用的材料是无毒无害物质,对环境和人体友好,安全环保。
附图说明
24.图1是本发明实施例1中的丙烯酸镁聚合物修复前后的照片(a是修复前;b是修复中;c是修复后;d是未降解前的丙烯酸镁聚合物)。
具体实施方式
25.下面通过具体实施例来进一步说明本发明的技术方案。本领域技术人员应该明了,所述实施例仅仅是帮助理解本发明,不应视为对本发明的具体限制。
26.除非另有定义,本发明所使用的所有的技术和科学术语与属于本发明的技术领域的技术人员通常理解的含义相同。本发明的说明书中所使用的术语只是为了描述具体的实施例的目的,不用于限制本发明。
27.本发明的术语“包括”和“具有”以及它们任何变形,意图在于覆盖不排他的包含。例如包含了一系列步骤的过程、方法、装置、产品或设备没有限定于已列出的步骤或模块,而是可选地还包括没有列出的步骤,或可选地还包括对于这些过程、方法、产品或设备固有的其它步骤。
28.在本发明中提及的“多个”是指两个或两个以上。“和/或”,描述关联对象的关联关系,表示可以存在三种关系,例如,a和/或b,可以表示:单独存在a,同时存在a和b,单独存在b这三种情况。字符“/”一般表示前后关联对象是一种“或”的关系。
29.以下为具体实施例。以下实施例中所用的原料,如无特殊说明,均可从常规商业途径得到;所采用的工艺,如无特殊说明,均采用本领域的常规工艺。以下如无特殊说明,室温指的25
±
5℃。
30.实施例1
31.将丙烯酸镁聚合物裁切成厚3mm,长宽2cm
×
1.5cm的测试件(1g),再将测试件放入氢氧化钠水溶液(0.1mol/l)中浸泡8小时,浸泡后的测试件体积膨胀,成凝胶状,说明丙烯酸镁聚合物在氢氧化钠水溶液的浸泡下发生了降解。将浸泡后的测试件取出,取0.5g硫酸镁涂布于该测试件的表面,12小时后对测试件进行性能测试,测试结果如表2所示。
32.表2中拉伸强度使用电子万能试验机在室温下进行测定,测试件标距在实验测试中具体设定为10mm,夹具拉伸速率在实验测试中具体设定为5mm
·
min-1
,测试件性状由目测得到。
33.实施例2
34.将丙烯酸镁聚合物裁切成厚3mm,长宽2cm
×
1.5cm的测试件(1g),再将测试件放入氢氧化钠水溶液(0.1mol/l)中浸泡8小时,浸泡后的测试件体积膨胀,成凝胶状,说明丙烯酸镁聚合物在氢氧化钠水溶液的浸泡下发生了降解。将浸泡后的测试件取出,取0.5g氯化镁涂布于该测试件的表面,12小时后对测试件进行性能测试,测试结果如表2所示。
35.实施例3
36.将丙烯酸镁聚合物裁切成厚3mm,长宽2cm
×
1.5cm的测试件(1g),再将测试件放入氢氧化钠水溶液(0.1mol/l)中浸泡8小时,浸泡后的测试件体积膨胀,成凝胶状,说明丙烯酸镁聚合物在氢氧化钠水溶液的浸泡下发生了降解。
37.将浸泡后的测试件取出,取0.5g硝酸镁涂布于该测试件的表面,12小时后对测试件进行性能测试,测试结果如表2所示。
38.实施例4
39.将丙烯酸镁聚合物裁切成厚3mm,长宽2cm
×
1.5cm的测试件(1g),再将测试件放入氢氧化钠水溶液(0.1mol/l)中浸泡8小时,浸泡后的测试件体积膨胀,成凝胶状,说明丙烯酸镁聚合物在氢氧化钠水溶液的浸泡下发生了降解。将浸泡后的测试件取出,取0.5g硫酸
钙涂布于该测试件的表面,12小时后对测试件进行性能测试,测试结果如表2所示。
40.实施例5
41.将丙烯酸镁聚合物裁切成厚3mm,长宽2cm
×
1.5cm的测试件(1g),再将测试件放入氢氧化钠水溶液(0.1mol/l)中浸泡8小时,浸泡后的测试件体积膨胀,成凝胶状,说明丙烯酸镁聚合物在氢氧化钠水溶液的浸泡下发生了降解。将浸泡后的测试件取出,取0.5g氯化钙涂布于该测试件的表面,12小时后对测试件进行性能测试,测试结果如表2所示。
42.实施例6
43.将丙烯酸镁聚合物裁切成厚3mm,长宽2cm
×
1.5cm的测试件(1g),再将测试件放入氢氧化钠水溶液(0.1mol/l)中浸泡8小时,浸泡后的测试件体积膨胀,成凝胶状,说明丙烯酸镁聚合物在氢氧化钠水溶液的浸泡下发生了降解。将浸泡后的测试件取出,取0.5g硝酸钙涂布于该测试件的表面,12小时后对测试件进行性能测试,测试结果如表2所示。
44.实施例7
45.将氯化镁和氯化钙按20份:80份的质量比混合,得到修复混合物。
46.将丙烯酸镁聚合物裁切成厚3mm,长宽2cm
×
1.5cm的测试件(1g),再将测试件放入氢氧化钠水溶液(0.1mol/l)中浸泡8小时,浸泡后的测试件体积膨胀,成凝胶状,说明丙烯酸镁聚合物在氢氧化钠水溶液的浸泡下发生了降解。将浸泡后的测试件取出,取0.5g修复混合物涂布于该测试件的表面,12小时后对测试件进行性能测试,测试结果如表2所示。
47.实施例8
48.将硫酸镁和氯化钙按50份:50份的质量比混合,得到修复混合物。
49.将丙烯酸镁聚合物裁切成厚3mm,长宽2cm
×
1.5cm的测试件(1g),再将测试件放入氢氧化钠水溶液(0.1mol/l)中浸泡8小时,浸泡后的测试件体积膨胀,成凝胶状,说明丙烯酸镁聚合物在氢氧化钠水溶液的浸泡下发生了降解。将浸泡后的测试件取出,取0.5g修复混合物涂布于该测试件的表面,12小时后对测试件进行性能测试,测试结果如表2所示。
50.实施例9
51.将20重量份的氯化镁和20重量份的氯化钙溶解于100重量份的蒸馏水中,得到修复混合液。
52.将丙烯酸镁聚合物裁切成厚3mm,长宽2cm
×
1.5cm的测试件(1g),再将测试件放入氢氧化钠水溶液(0.1mol/l)中浸泡8小时,浸泡后的测试件体积膨胀,成凝胶状,说明丙烯酸镁聚合物在氢氧化钠水溶液的浸泡下发生了降解。将浸泡后的测试件取出,再浸泡于20ml修复混合液中,12小时后对测试件进行性能测试,测试结果如表2所示。
53.实施例10
54.将20重量份的氯化钙溶解于100重量份的蒸馏水中,得到修复混合液。
55.将丙烯酸镁聚合物裁切成厚3mm,长宽2cm
×
1.5cm的测试件(1g),再将测试件放入氢氧化钠水溶液(0.1mol/l)中浸泡8小时,浸泡后的测试件体积膨胀,成凝胶状,说明丙烯酸镁聚合物在氢氧化钠水溶液的浸泡下发生了降解。将浸泡后的测试件取出,再浸泡于20ml修复混合液中,12小时后对测试件进行性能测试,测试结果如表2所示。
56.对比例1
57.将丙烯酸镁聚合物裁切成厚3mm,长宽2cm
×
1.5cm的测试件(1g),再将测试件放入氢氧化钠水溶液(0.1mol/l)中浸泡8小时,浸泡后的测试件体积膨胀,成凝胶状,说明丙烯
酸镁聚合物在氢氧化钠水溶液的浸泡下发生了降解。将浸泡后的测试件取出,再浸泡于20ml蒸馏水中,12小时后对测试件进行性能测试,测试结果如表2所示。
58.对比例2
59.将丙烯酸镁聚合物裁切成厚3mm,长宽2cm
×
1.5cm的测试件(1g),再将测试件放入氢氧化钠水溶液(0.1mol/l)中浸泡8小时,浸泡后的测试件体积膨胀,成凝胶状,说明丙烯酸镁聚合物在氢氧化钠水溶液的浸泡下发生了降解。将浸泡后的测试件取出,取0.5g氯化钠涂布于该测试件的表面,12小时后对测试件进行性能测试,测试结果如表2所示。
60.对比例3
61.将丙烯酸镁聚合物裁切成厚3mm,长宽2cm
×
1.5cm的测试件(1g),再将测试件放入氢氧化钠水溶液(0.1mol/l)中浸泡8小时,浸泡后的测试件体积膨胀,成凝胶状,说明丙烯酸镁聚合物在氢氧化钠水溶液的浸泡下发生了降解。将浸泡后的测试件取出,取0.5g硫酸钾涂布于该测试件的表面,12小时后对测试件进行性能测试,测试结果如表2所示。
62.对比例4
63.将20重量份的硫酸钠溶解于100重量份的蒸馏水中,得到修复混合液。
64.将丙烯酸镁聚合物裁切成厚3mm,长宽2cm
×
1.5cm的测试件(1g),再将测试件放入氢氧化钠水溶液(0.1mol/l)中浸泡8小时,浸泡后的测试件体积膨胀,成凝胶状,说明丙烯酸镁聚合物在氢氧化钠水溶液的浸泡下发生了降解。将浸泡后的测试件取出,再浸泡于20ml修复混合液中,12小时后对测试件进行性能测试,测试结果如表2所示。
65.表1.实施例1~10和对比例1~4修复化合物或混合物组成(重量份)及使用方式
66.[0067][0068]
表2.原测试件、实施例1~10和对比例1~4测试件拉伸强度和形状
[0069][0070][0071]
由表2结果可知,实施例1-10相比对比例1-4,经实施例修复处理(按照本发明的丙
烯酸盐聚合物材料的修复方法)后,丙烯酸盐聚合物的性状恢复良好,并且能够恢复到原始测试件的拉伸强度,而经对比例处理的丙烯酸盐聚合物的性状无明显变化,并且拉伸强度相比浸泡后的测试件也没有明显变化。说明本发明的丙烯酸盐聚合物材料的修复方法对被碱浸泡损伤的丙烯酸盐聚合物有很好的修复作用。
[0072]
以上所述实施例的各技术特征可以进行任意的组合,为使描述简洁,未对上述实施例中的各个技术特征所有可能的组合都进行描述,然而,只要这些技术特征的组合不存在矛盾,都应当认为是本说明书记载的范围。
[0073]
以上所述实施例仅表达了本发明的几种实施方式,其描述较为具体和详细,但并不能因此而理解为对发明专利范围的限制。应当指出的是,对于本领域的普通技术人员来说,在不脱离本发明构思的前提下,还可以做出若干变形和改进,这些都属于本发明的保护范围。因此,本发明专利的保护范围应以所附权利要求书为准。