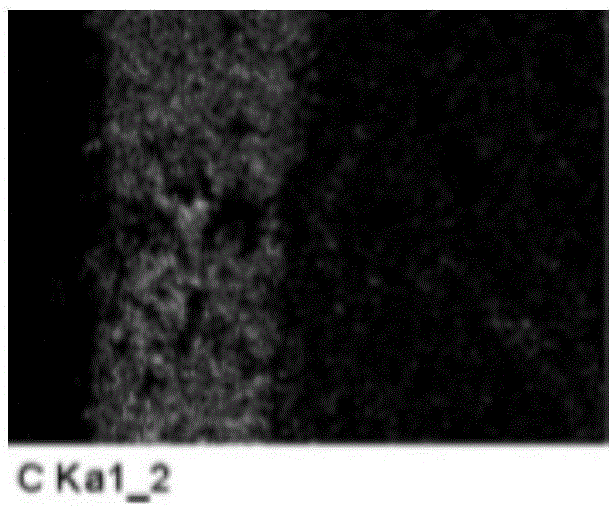
本发明属于涂料领域,具体地说,涉及一种环保型涂料、制备方法、应用及使用方法。
背景技术:
:随着外墙建筑及装修效果的不断提升,建筑涂料的需求也越来越大。不同于传统的外墙墙体,建筑外墙板材(如:保温装饰板)表面致密,传统建筑涂料很难在其表面渗透,容易造成附着不良的问题。目前,外墙建筑装饰板材多采用纤维水泥板为基材,采用涂布涂料进行装饰,仿制大理石效果。涂料可分为单组份涂料和双组份涂料。单组份涂料一般属于不需要交联固化,仅需溶剂挥发即可形成漆膜(属于物理反应);双组份涂料一般是属于交联固化,两种组份混合后产生交联反应形成漆膜(属于化学反应)。纤维水泥板密度大,表层疏松。可以采用双组份水性环氧树脂涂料,利用环氧树脂分子链中的羟基和环氧基交联反应成膜,具有较好的附着力。但是,水性环氧树脂涂料存在以下问题:1、环氧涂料的官能团交联反应需要在一定温度下进行,温度较低时,反应慢,甚至无法成膜;2、环氧涂料整体粘度上升较快,容易固化,较短的时间间隔内就要进行生产设备的清理,防止在生产过程中树脂固化。采用单组份涂料苯丙、纯丙或硅丙乳液等乳液为成膜物质,由于乳液具有较大粒径,在密实的纤维水泥板表面,渗透性较差,导致附着力较差,但成膜后耐水性较好。可以采用添加增强剂的成分制得单组份涂料,但制得的单组份涂料十分不稳定,热贮温度为55℃时,存放时间小于7天,无法进行批量生产。有鉴于此特提出本发明。技术实现要素:本发明要解决的技术问题在于克服现有技术的不足,提供一种环保型涂料、制备方法、应用及使用方法,本发明将环保型涂料分成两个相互独立包装的液体组分a和增强剂组分b,使液体组分a中的有效成分在液体中更加稳定存在,提高环保型涂料的保存时间,解决了含有上述组分的环保型涂料无法批量生产和无法长时间储存的问题。为解决上述技术问题,本发明采用技术方案的基本构思是:一种环保型涂料,包括相互独立分装的液体组分a和增强剂组分b,按质量份数比计,原料各成分组成如下:液体组分a包括:增强剂组分b包括:硅酸盐和/或硅溶胶10~30份。在液体组分a中加入增强剂组分b,能够提高涂料的渗透性,增强其附着力,但是液体组分a和增强剂组分b混合后制成单组分涂料,热储状态下,很容易在涂料中产生颗粒状物质,降低涂料的成膜性,使涂料的性能大打折扣,甚至无法使用。实验发现,增强剂组分b长期存在于单组分涂料中,很容易造成乳液的聚凝,使乳液中的溶质析出,这一物理变化是导致颗粒形成的主要原因。本发明将环保型涂料分成两个相互独立包装的液体组分a和增强剂组分b,使液体组分a中的有效成分在液体中更加稳定存在,提高环保型涂料的保存时间,解决了含有上述组分的环保型涂料无法批量生产的问题。在使用时,将液体组分a和增强剂组分b混合均匀即可使用,涂覆后,利用水分的挥发形成漆膜,因此,受温度影响小,即使在较低的温度下也能成膜,受限小;二者混合后,开放时间长,减少浪费。所述液体组分a的粘度为70-100ku;优选地,所述液体组分a的粘度为80±5ku。将液体组分的粘度调整到70-100ku的范围,能够满足生产过程的上漆量,而且,在该粘度和浓度下加入增强剂组分b,乳液中的溶质不易产生凝聚;另外,粘度大,虽然能够大大提高生产过程上漆量,但是,液体组分a和增强剂组分b混合时,乳液稳定性下降,而且上漆量大,涂料消耗量大,低于该粘度范围,生产过程上漆量较少,达不到附着力要求。在上述粘度范围内,既能够满足混合后涂料的稳定性,又可实现良好的上漆量,且搅拌装置的输出功率适中,更加节能。所述乳液包括苯丙乳液、纯丙乳液和硅丙乳液中的一种或者几种的混合;优选地,所述苯丙乳液、纯丙乳液和硅丙乳液中相应溶质的粒径为0.1~0.2μm。采用苯丙乳液、纯丙乳液和硅丙乳液中的一种或者几种的混合,不需要交联固化,仅需溶剂挥发即可形成漆膜,受温度影响小,即使在较低的温度下也能成膜。所述消泡剂包括矿物油类消泡剂或有机硅消泡剂中的一种或者几种的混合;所述成膜助剂包括二丙二醇丙醚、二丙二醇丁醚和texanol中的一种或者几种的混合;所述增稠剂包括碱溶涨型增稠剂、聚氨酯型增稠剂和无机型增稠剂中的一种或者几种的混合。所述硅酸盐包括硅酸锂、硅酸钠、硅酸钾中的一种或者几种的混合。无机涂料硅酸锂、硅酸钠和硅酸钾,为分子溶液,具有渗透性好、硬度高的特点,在液体组分a中加入上述物质,增加了涂料的渗透性、附着力好,而且,成膜后硬度高,弥补了液体组分a渗透性差、硬度小、附着力差的缺陷,二者相互补充,提高了涂料的性能。一种上述的环保型涂料的制备方法,在水中加入液体组分a中的其他各组分,混合后得到液体混合物a,加水调整液体混合物a的粘度至70-100ku,并进行包装得到独立包装的液体混合物a;将增强剂组分b中的各组分混合,得到混合物b,并进行包装得到独立包装的混合物b;将独立包装的液体混合物a和独立包装的混合物b进行包装,得到环保型涂料。将液体混合物a和增强剂组分b单独制备,在使用时,将二者现场混合后再进行涂覆,提高环保型涂料的保存时间,解决了含有上述组分的环保型涂料无法批量生产的问题。加水调整液体混合物a的粘度至70-100ku,既保证涂料的稳定性,使其储存时间长,又能实现生产过程中的上漆要求。在水中加入液体组分a中的其他各组分,包括以下步骤,在水中先加入乳液,搅拌使乳液与水混合均匀,再向其中加入消泡剂和成膜助剂,搅拌使其充分溶解,最后加入增稠剂充分搅拌。所述液体混合物a的制备方法,包括以下步骤:(1)取20~30份水,向其中加入30~60份的乳液,搅拌混合均匀,再向其中0.05~0.3份的消泡剂和0.5~3份的成膜助剂得到混合液,加入成膜助剂后搅拌至成膜助剂充分溶解;(2)向混合液中加入0.2~1份的增稠剂,充分搅拌,测试粘度,最后加入调整粘度的水调整液体组分a的粘度至70-100ku,得到液体混合物a;优选地,(1)中,加入成膜助剂后搅拌时间为1-20分钟,搅拌时,搅拌装置的转速为600~900转/分钟;更优选地,(1)中,加入成膜助剂后搅拌15分钟左右。调整粘度的水与溶解水的水质可以相同也可以不同,但最好相同。一种上述环保型涂料在纤维水泥板材上的应用。一种上述的环保型涂料的使用方法,使用时,将增强剂组分b加入液体组分a中,搅拌混合均匀后,即可使用;优选地,混合时,对液体组分a进行搅拌,在搅拌的过程中逐渐加入增强剂组分b。现场使用时,将增强剂组分b加入液体组分a中,搅拌混合均匀后,涂料更加均匀,使用更加方便,不会出现出厂时和使用时产品质量差距较大的问题。采用上述技术方案后,本发明与现有技术相比具有以下有益效果:1、本发明将环保型涂料分成两个相互独立包装的液体组分a和增强剂组分b,使液体组分a中的有效成分在液体中更加稳定存在,提高环保型涂料的保存时间,解决了含有上述组分的环保型涂料无法批量生产的问题;2、在使用时,将液体组分a和增强剂组分b混合均匀即可使用,涂覆后,利用水分的挥发形成漆膜,因此,成膜温度低,可实现常温成膜,受限小;成膜时间短,提高工作效率,降低人工成本;二者混合后,开放时间长,减少浪费。3、将液体组分的粘度调整到70-100ku的范围能,能够满足混合涂料的稳定性,而且,在该粘度下加入增强剂组分b,保证生产过程中的上漆要求;4、本发明的涂料既具有较好的附着力,又具有较强的耐水性;5、生产成本低,本发明的涂料成本可以降低至水性双组份环氧涂料成本的一半。下面结合附图对本发明的具体实施方式作进一步详细的描述。附图说明附图作为本发明的一部分,用来提供对本发明的进一步的理解,本发明的示意性实施例及其说明用于解释本发明,但不构成对本发明的不当限定。显然,下面描述中的附图仅仅是一些实施例,对于本领域普通技术人员来说,在不付出创造性劳动的前提下,还可以根据这些附图获得其他附图。在附图中:图1是本发明实施例一板材的平面元素分布图;图2是本发明对比例1板材的平面元素分布图;图3是本发明实施例一低温干燥时间和成膜性能检测图;图4是本发明对比例1低温干燥时间和成膜性能检测图。需要说明的是,这些附图和文字描述并不旨在以任何方式限制本发明的构思范围,而是通过参考特定实施例为本领域技术人员说明本发明的概念。具体实施方式为使本发明实施例的目的、技术方案和优点更加清楚,下面将结合本发明实施例中的附图,对实施例中的技术方案进行清楚、完整地描述,以下实施例用于说明本发明,但不用来限制本发明的范围。实施例一一种环保型涂料,包括相互独立分装的液体组分a和增强剂组分b,按质量份数比计,原料各成分组成如下:液体组分a包括:增强剂组分b包括:硅酸盐和硅溶胶10份。所述液体组分a的粘度75±5ku。硅酸盐和硅溶胶的重量比为1:1。其中,消泡剂选择为yh-203,成膜助剂为二丙二醇丙醚,增稠剂选择碱溶胀增稠剂t-900,硅酸盐为硅酸锂。所述苯丙乳液中溶质的粒径为0.1~0.2μm。该环保型涂料的制备方法,包括以下步骤,1)制备液体混合物a:(1)取20份重量的水,向其中加入乳液,在600~900转/分钟下搅拌混合均匀,再向其中消泡剂和成膜助剂得到混合液,加入的成膜助剂搅拌时间为15分钟,以保证成膜助剂充分溶解;(2)向混合液中加入0.2份的增稠剂,充分搅拌,检测粘度,最后加入水调整液体组分a的粘度至75±5ku,得到液体混合物a;2)制备增强剂组分b:将硅酸盐和硅溶胶混合,得到混合物b,并进行包装得到独立包装的混合物b;3)将独立包装的液体混合物a和独立包装的混合物b进行包装,得到环保型涂料。该环保型涂料的使用方法,使用时,将增强剂组分b逐渐加入液体组分a中,搅拌混合均匀后,即可进行涂覆使用。该环保型涂料可应用于纤维水泥板材上。实际表干时间10min,5℃低温成膜要求无异常,低温成膜检测结果,漆膜成膜良好,耐擦洗>1000次。实施例二一种环保型涂料,包括相互独立分装的液体组分a和增强剂组分b,按质量份数比计,原料各成分组成如下:液体组分a包括:增强剂组分b包括:硅酸盐和硅溶胶15份。所述液体组分a的粘度80±5ku,硅酸盐和硅溶胶的重量比1:1。其中,消泡剂选择为yh-203,成膜助剂为二丙二醇丙醚,增稠剂选择碱溶胀增稠剂t-900,硅酸盐为硅酸锂。所述苯丙乳液中溶质的粒径为0.1~0.2μm。该环保型涂料的制备方法,包括以下步骤,1)制备液体混合物a:(1)取25份重量的水,向其中加入乳液,在600~900转/分钟下搅拌混合均匀,再向其中消泡剂和成膜助剂得到混合液,加入的成膜助剂搅拌时间为15分钟,以保证成膜助剂充分溶解;(2)向混合液中加入0.8份的增稠剂,充分搅拌,检测粘度,最后加入水调整液体组分a的粘度至80±5ku,得到液体混合物a;2)制备增强剂组分b:将硅酸盐和硅溶胶混合,得到混合物b,并进行包装得到独立包装的混合物b;3)将独立包装的液体混合物a和独立包装的混合物b进行包装,得到环保型涂料。该环保型涂料的使用方法,使用时,将增强剂组分b逐渐加入液体组分a中,搅拌混合均匀后,即可进行涂覆使用。该环保型涂料可应用于纤维水泥板材上。实际表干时间12min,5℃低温成膜要求无异常,低温成膜检测结果,漆膜成膜良好,耐擦洗>1000次。实施例三一种环保型涂料,包括相互独立分装的液体组分a和增强剂组分b,按质量份数比计,原料各成分组成如下:液体组分a包括:增强剂组分b包括:硅酸盐和硅溶胶30份。所述液体组分a的粘度95±5ku,硅酸盐和硅溶胶的重量比为1:1。其中,消泡剂选择为yh-203,成膜助剂为二丙二醇丙醚,增稠剂选择碱溶胀增稠剂t-900,硅酸盐为硅酸锂。所述苯丙乳液中溶质的粒径一般为0.1~0.2μm。该环保型涂料的制备方法,包括以下步骤,1)制备液体混合物a:(1)取30份重量的水,向其中加入乳液,在600~900转/分钟下搅拌混合均匀,再向其中消泡剂和成膜助剂得到混合液,加入的成膜助剂搅拌时间为20分钟,以保证成膜助剂充分溶解;(2)向混合液中加入增稠剂,充分搅拌,检测粘度,最后加入水调整液体组分a的粘度至95±5ku,得到液体混合物a;2)制备增强剂组分b:将硅酸锂和硅溶胶混合,得到混合物b,并进行包装得到独立包装的混合物b;3)将独立包装的液体混合物a和独立包装的混合物b进行包装,得到环保型涂料。该环保型涂料的使用方法,使用时,将增强剂组分b逐渐加入液体组分a中,搅拌混合均匀后,即可进行涂覆使用。该环保型涂料可应用于纤维水泥板材上。实际表干时间8min,5℃低温成膜要求无异常,低温成膜检测结果,漆膜成膜良好,耐擦洗>1000次。实施例四本实施例与实施例一的区别在于,在制备液体混合物a时,先在水中加入消泡剂和成膜助剂混合均与后,搅拌至成膜助剂充分溶解,再向其中加入乳液,最后加入增稠剂。其他成分、用量与步骤与实施例一相同。实际表干时间12min,5℃低温成膜要求无异常,低温漆膜成膜良好,耐擦洗>1000次。实施例五本实施例与实施例一的区别在于,在制备液体混合物a时,先在水中加入消泡剂和成膜助剂混合均与后,搅拌至成膜助剂充分溶解,再向其中增稠剂,最后再加入乳液。其他成分、用量与步骤与实施例一相同。实际表干时间10min,5℃低温成膜要求无异常,低温漆膜成膜良好,耐擦洗>1000次。实施例六本实施与实施例一的区别在于,所述乳液为纯丙乳液和硅丙乳液;所述硅酸盐为硅酸锂、硅酸钠和硅酸钾;所述消泡剂为矿物油类消泡剂和有机硅消泡剂;所述成膜助剂为二丙二醇丙醚、二丙二醇丁醚和texanol;所述增稠剂为碱溶涨型、聚氨酯型和无机型增稠剂。其他成分与方法与实施例一相同。有机硅消泡剂可以为二甲基硅油,碱溶涨型增稠剂可以为碱溶胀增稠剂t-900。采用上述物质的实验结果与实施例一的结果相似。实际表干时间10min,5℃低温成膜要求无异常,低温漆膜成膜良好,耐擦洗>1000次。对比例1水性双组份环氧涂料:该水性双组份环氧涂料由普通128树脂和曼尼期碱固化剂混合而成。其中,曼尼期碱固化剂的制备方法如下:向装有搅拌器、热电偶、冷凝器、蒸馏接收器和加料漏斗的1升3颈烧瓶中加入272克(2摩尔)间亚二甲苯基二胺(“mxda”)和94克(1摩尔)苯酚。用氮气吹扫烧瓶内容物并将其加热至48℃。在保温47-50℃的同时,在60分钟内向混合物中滴加144克(2摩尔)丁醛。在47-54℃下保温另外的60分钟后,升温至160℃,在这一升温过程中收集所有的馏出液。在160℃保温20分钟后,升温至170℃。45分钟后冷却烧瓶内容物并且出料,即得。水性双组份环氧涂料的制备方法:将128树脂、上述方法制备的曼尼期碱固化剂和水按照重量比1:1.5:2混合,采用搅拌装置以1200转/min的搅拌速度进行搅拌,混合均匀后即得水性双组份环氧涂料。对比例2专利201410834619.2中的实施例一。对比例3将实施例一中的独立包装的液体混合物a和独立包装的混合物b混合,搅拌混合均匀后,制得的混合物,保存10天后进行检测。对比例4本对比例与对比例3的区别在于,保存30天后进行检测。对比例5本对比例与实施例一的区别在于,本对比例中调节液体组分的粘度调整到120ku,液体组分a和增强剂组分b混合时,出现絮凝现象,而实施例一中未见该现象。对比例6本对比例与实施例一的区别在于,本对比例中调节液体组分的粘度调整到50ku,存放时间与实施例一基本相同,液体组分a和增强剂组分b混合后进行涂覆时,底板隐约可见,而采用实施例一的涂料进行涂覆,未见该现象。实验结果:实施例一与对比例1的涂料的性能检测,检测方法与检测结果如下,性能标准采用jg/t210-2007中外墙底漆一等品的检测方法及检测性能。1、涂料渗透性检测检测仪器:sem(扫描电子显微镜,型号hitachis-3400n),edx(能量色散x射线光谱仪,型号horibaadd0009x射线光谱仪)。样品前处理:样品台上粘结导电胶带,涂膜样品直接粘在导电胶带上,进行喷金前处理。测试条件:表征条件为真空状态<0.1mpa,工作距离10mm,加速电压15kv,加速电流30ma,利用仪器测试得到元素分布信息。将实施例一的环保型涂料混合后涂覆在纤维水泥板材上,采用sem-edx---元素分布法,进行检测,选取板材剖面进行扫描,扫描结果如图1所示。将对比例1的水性双组份环氧涂料涂覆在纤维水泥板材上,采用sem-edx---元素分布法进行检测,检测条件与实施例一相同,同样选取板材剖面进行扫描,扫描结果如图2所示。结果分析,从板材的平面元素分布来看:纤维水泥板材分别经水性双组份环氧涂料涂覆和实施例一的涂料涂覆处理后,从碳元素(图片中白色部分)的渗透分布对比来看,实施例一的涂料渗透性优于水性双组份环氧涂料,由于本发明的涂料渗透的更深,从另外一方面弥补了自身强度的不足。2、附着力、粘接强度及耐水性能分析表1涂料的附着力、粘接强度及耐水性能从上述性能检测结果来看,本发明的涂料性能完全达到水性双组份环氧涂料的标准。但是,本发明配方的成本是水性双组份环氧涂料成本的一半。3、表干时间和低温成膜性能检测将实施例一、对比例1、对比例3和对比例4涂覆在相同的纤维水泥板材上,采用f-dom仪器检测的表干时间和低温成膜性能,如表2所示。实施例一的检测结果如图3所示,对比例1的检测结果如图4所示。表2表干时间和低温成膜性能对比例1的水性双组份环氧涂料与实施例一的本发明的涂料相比,实施例一的实际表干时间大大降低,更加节约时间,而且,漆模成膜好,耐擦洗。对比例3和对比4与实施例一相比,混合后形成单组分涂料后,存放时间越长稳定性差,成膜效果差,涂覆后,耐洗刷能力急剧降低。这是由于混合后,长时间放置,溶液产生聚凝,形成固体颗粒析出,使成膜性和耐擦洗性大大降低。4、可使用时间影响表3可使用时间水性双组份环氧涂料在搅拌过程中出现凝胶现象,这使得生产过程中滚涂出现粘度上升的现象,实施例一不存在这类现象。结合f-dom检测结果,说明有水存在的情况下底漆不会出现凝胶,水分挥发后能快速干燥成膜,完全符合生产线的特点和要求。5、存放时间的比较热贮温度为55℃时,实施例一-实施例五以及对比例1,2,5,6的存放时间(单位为月)比较,如下表所示。表4存放时间存放时间(月)实施例一13实施例二14实施例三13实施例四11实施例五11对比例110对比例22对比例513对比例612实施例一-实施例三与实施例四和实施例五比较,实验结果显示,液体组分a的配制过程中,各组分的加入顺序不同,也会影响其保存时间,采用实施例一-实施例三的方法进行配制,不易絮凝,存放时间更长。实施例一-实施例五与对比例1进行比较,从实验结果上可以看出,采用本发明的涂料与水性双组份环氧涂料相比,存放时间明显高于水性双组份环氧涂料,而且,本发明的配方成本更低,市场竞争力更高。实施例一-实施例五与对比例2进行比较,本发明的涂料的保存时间明显高于201410834619.2中的涂料的保存时间。实施例一-实施例五与对比例3进行比较,对比例3中,在将液体组分a和增强剂组分b混合后10天后进行检测,其成膜性已经异常,出现成膜性差的问题,其正常的存放时间小于10天,实验发现,其存放时间一般为7天,而采用本发明将液体组分a和增强剂组分b单独包装,使用时再进行混合的方法制备的实施例一-实施例五的环保型涂料,其存放时间均大大提高。实施例一-实施例五与对比例5和6进行比较,调节液体组分的粘度调整在70-100ku,液体混合物a的稳定性提高。对比例5粘度高,对液体混合物a的稳定性不会产生影响,不会影响涂料的保存时间,但是液体混合物a与增强剂组分b混合时,会出现絮凝的现象;对比例6粘度过低,对液体混合物a的稳定性具有一定影响,使其保存时间略有减小。以上所述仅是本发明的较佳实施例而已,并非对本发明作任何形式上的限制,虽然本发明已以较佳实施例揭露如上,然而并非用以限定本发明,任何熟悉本专利的技术人员在不脱离本发明技术方案范围内,当可利用上述提示的技术内容作出些许更动或修饰为等同变化的等效实施例,但凡是未脱离本发明技术方案的内容,依据本发明的技术实质对以上实施例所作的任何简单修改、等同变化与修饰,均仍属于本发明方案的范围内。当前第1页1 2 3