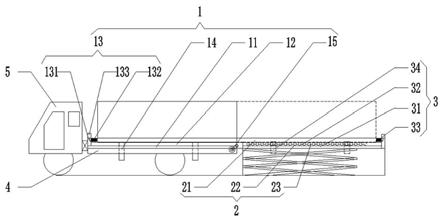
1.本发明涉及物流车辆技术领域,具体涉及一种基于云计算的物流货车复位装置。
背景技术:2.基于云计算的物流货车是在云计算的支持下,可以合理安排装货时间,选择最优路线的货车,货车上装载有连接云服务器的装置,可以随时更新了解车辆的调度信息,同时使货物的运输路线具有可追溯性,基于云计算的物流货车在云计算的路线优化下,如果再次对货车进行时间优化,运输企业将具有极大竞争优势。
3.目前对货车装货等待时间缩减最多的是甩挂运输,所谓甩挂运输就是带有动力的机动车将随车拖带的承载装置,包括半挂车、全挂车甚至货车底盘上的货箱甩留在目的地后,再拖带其他装满货物的装置返回原地,或者驶向新的地点,这种一辆带有动力的主车,卸下承载装置后再拖带其他承载装置的运输方式被称为甩挂运输;在相同的运输条件下,汽车运输生产效率的提高取决于汽车的载重量、平均运输速度和装卸停歇时间三个主要因素;甩挂运输可以缩减车辆装卸停歇时间,从而提高运输生产效率。
4.但是甩挂运输有它自身的限制性:1.费用高,挂车的价格本身就高于其它货车,货车装卸货箱需要使用天车;2.要求高,挂车对司机的技术要求高,天车为特种设备,有较高的技术要求;3.程序复杂,牵引车拖带挂车运营需要办理的证件多且繁琐;这些都成为甩挂运输快速发展的瓶颈,也是制约物流运输的桎梏。
技术实现要素:5.为解决现有基于云计算的物流货车的甩挂运输自身的费用高、要求高和程序复杂的问题,本发明提供一种基于云计算的物流货车复位装置,目的提供一种自动装卸车厢,不需要吊车吊装,方便调度的甩挂运输货车,解决挂车运输和装货的问题。
6.为了实现上述目的,本发明的技术方案是:一种基于云计算的物流货车复位装置,包括车头、车身和车厢,所述车身包括车架和液压系统,所述车厢与车架可拆卸地连接在一起,车厢在水平面的投影包围车架在水平面的投影,还包括车身部、车厢部和装货部,所述车厢经车厢部和车身部与所述车架可拆卸地连接或所述车厢经车厢部和装货部可拆卸地连接;所述车身部包括第一定位框、第一运行轨道、第一止停机构、第一定位柱和驱动机构;所述第一定位框为型钢焊接构成的与车厢等宽、长度大于车厢长度的格栅状的框架结构,所述第一定位框的右端中部设置有向左凹陷、开口向右的长方形的缺口,所述缺口的前后相对的内侧面上均设置有滑槽,所述滑槽为向右上方拱起的弧形的槽体,两个滑槽前后相对,所述第一定位框底面固定连接车架上表面;所述第一定位框的上表面上设置有分别位于缺口的前侧和后侧的两根互相平行的第一运行轨道,所述每个第一运行轨道均为开口向上的槽钢,第一运行轨道的右端与第
一定位框的右端平齐、左端与第一定位框的左端有间距,所述每个第一运行轨道左侧的第一定位框上表面均设置有一个第一止停机构,所述每个第一止停机构均由立柱、阻尼器和储油箱组成,所述立柱竖直固定在第一运行轨道的左端的第一定位框上表面上,立柱的左侧面与第一定位框的左侧面对齐,立柱的右侧面上部设置有阻尼器,所述阻尼器由油腔、第一弹簧和防撞板组成,所述油腔为两个开口正对的筒体互相套接形成的水平设置的中空柱体,油腔内部同轴设置有第一弹簧,油腔右端同轴设置有圆盘状的具有弹性的防撞板,所述油腔左端固定在立柱右侧面上,油腔内装有阻尼油,油腔左端周壁下部设置有贯穿油腔的泄油孔,所述油腔经泄油孔连接导管,所述导管的另一端连通置于立柱顶端的储油箱底面内壁,所述储油箱为侧壁上端带有透气孔的长方形箱体;所述第一定位框上设置有四个第一定位柱,所述四个第一定位柱中的两个第一定位柱位于第一定位框前侧的第一运行轨道前方,另外两个第一定位柱位于第一定位框后侧的第一运行轨道后方,每个所述第一定位柱均由液压油缸和固定头组成,所述液压油缸连接车身上的液压系统,所述液压油缸的缸体上端固定连接第一定位框底面,液压油缸的活塞杆由下向上穿过第一定位框的格栅孔,液压油缸的活塞杆的顶面连接固定头,所述固定头是上端为圆台状的中空柱体,固定头的周壁上设置有多个贯穿固定头周壁和中部连通的圆形通孔,所述每个圆形通孔内均设置有两个定位环,所述两个定位环分别靠近圆形通孔的内端和外端,所述圆形通孔内安装有圆柱状的伸缩柱,所述伸缩柱内端位于两个定位环之间,伸缩柱内端设置有与圆形通孔内壁滑动连接的凸环,伸缩柱周壁与靠近圆形通孔外端的定位环内壁滑动连接,固定头中部内装有液压油,固定头的中部下表面设置有贯穿固定头、连通固定头中部内的油孔,所述固定头经油孔连接液压管道,所述液压管道连接车身上的液压系统,所述液压油缸处于收缩状态时,固定头的顶面与第一运行轨道底面位于同一水平面;所述第一定位框的右端设置有驱动机构,所述驱动机构包括驱动电机、驱动链轮、转轴和伸缩油缸,所述驱动电机安装在第一定位框下表面右端,驱动电机的输出轴上连接有置于缺口左端正下方的驱动链轮,所述驱动链轮经链条连接置于缺口内的从动链轮,所述从动链轮固定连接在转轴上,所述转轴为圆形杆体,转轴位于第一定位框右端的缺口内,转轴的两端分别伸进呈相对状态的两个滑槽内,所述转轴位于滑槽内的端部均设置有第一滚轮,所述伸缩油缸连接车身上的液压系统,伸缩油缸的缸体左端铰接在缺口左侧内壁上,伸缩油缸的活塞杆右端铰接在从动链轮侧方的转轴周壁上,所述伸缩油缸的活塞杆与从动链轮之间的转轴周壁上设置有直径大于从动链轮直径的驱动齿轮;所述车厢部包括承载板、驱动齿条和滚轮组,所述承载板为长方形板体,承载板上表面与车厢下表面固定连接,承载板下表面中部设置有沿承载板长度方向的驱动齿条,所述驱动齿条在车厢位于车身部上方时与驱动齿轮啮合,所述驱动齿条包括一个固定齿条和两个活动齿牙,所述固定齿条固定在承载板下表面中部沿承载板长度方向上,固定齿条的左右两端均前后对称设置有沉孔,所述固定齿条每一端的沉孔的数量均为前后对应的两个,每个所述沉孔内均同轴设置有导向柱,所述导向柱伸出固定齿条,所述固定齿条每一端的两个导向柱上均共同套装有一个活动齿牙,所述活动齿牙与固定齿条的齿牙模数一致,所述活动齿牙的齿数为一个或两个,所述固定齿条和活动齿牙之间的导向柱上套装有第二弹簧,所述固定齿条每一端的两个导向柱的端部共同连接有一块位于活动齿牙外侧的封
板,所述驱动齿条前侧和后侧的承载板底面上均设置有与第一定位框上的第一运行轨道相对应的滚轮组,所述滚轮组长度小于承载板的长度、大于承载板长度的五分之四,所述滚轮组是由多个第二滚轮沿承载板长度方向间隔设置构成,所述滚轮组距离承载板两端均有间距,所述承载板底面设置有开口朝下的多个定位孔,所述在车厢左端面与呈自然状态下的阻尼器右端面接触时多个定位孔与第一定位框上的第一定位柱一一上下对应,所述定位孔为沉孔,定位孔与固定头高度一致,所述定位孔的下端设置有向外扩大的倒角,定位孔的中部设置有向外突出的环状槽体;所述装货部位于车身部右侧,所述装货部包括第二定位框、第二运行轨道、第二止停机构和第二定位柱,所述第二定位框与第一定位框形状一致,第二定位框的长度小于第一定位框的长度,第二定位框底面安装有升降支架,所述升降支架固定在地面上,第二定位框顶面与第一定位框上表面平齐,第二运行轨道、第二止停机构和第二定位柱分别与第一运行轨道、第一止停机构和第一定位柱形状大小一致,且第二运行轨道、第二止停机构和第二定位柱在第二定位框上的安装位置与第一运行轨道、第一止停机构和第一定位柱在第一定位框上的安装位置呈左右相对状态,所述在车厢右端面与呈自然状态下的第二定位柱的阻尼器左端面接触时,承载板底面多个定位孔与第二定位柱一一上下对应。
7.进一步地,所述第一运行轨道的右端、第二运行轨道的左端均设置有向外扩大的开口。
8.进一步地,所述滑槽所在圆环的圆心位于驱动电机的输出轴的中心轴线上,滑槽的左端位于电机输出轴的正上方。
9.进一步地,所述固定齿条的沉孔内的第二弹簧处于收缩状态时的长度小于沉孔深度,第二弹簧的自然长度大于等于导向柱的长度。
10.进一步地,所述第一止停机构的阻尼器的油腔正对承载板的左侧面,第二止停机构的阻尼器的油腔正对承载板的右侧面。
11.进一步地,所述驱动齿轮推动驱动齿条向左移动,使车厢位于第一定位框上,当承载板左端与第一止停机构的阻尼器的油腔接触,所述固定齿条左端的沉孔内的第二弹簧处于收缩状态时,第一定位柱与定位孔上下对应;所述驱动齿轮推动驱动齿条向右移动,使车厢位于第二定位框上,当承载板右端与第二止停机构的阻尼器的油腔接触,所述固定齿条右端的沉孔内的第二弹簧处于收缩状态时,第二定位柱与定位孔上下对应。
12.进一步地,所述装货部和车厢部连接时,第二定位柱伸进定位孔内,第二定位柱的伸缩柱伸进定位孔的环状槽体内;所述车身部和车厢部连接时,第一定位柱伸进定位孔内,第一定位柱的伸缩柱伸进定位孔的环状槽体内。
13.进一步地,所述车厢由车身部转移向装货部或由装货部转移向车身部时,升降支架与车架高度一致,第一定位框上表面与第二定位框上表面平齐。
14.进一步地,所述车身和车厢上均装载有基于云计算的物流运输系统,所述基于云计算的物流运输系统,包括:车身定位监控模块,车厢定位监控模块,以及联网云计算模块;车厢定位监控模块包括gps定位器、信息存储器和信息发送器,实时存储与向联网云计算模块发送本车厢的gps定位和装载信息。
15.所述车身定位监控模块包括gps定位器、信息存储器、信息发送器和地图显示器,车身定位监控模块用于实时定位本车位置、本车需要运送的车厢的目的地位置和车厢的装
载信息进行实时显示,并显示下一次的车厢预选信息,所述gps定位器与联网云计算模块通过互联网连接;所述联网云计算模块用于获取所有物流车辆的车牌号,车辆型号和车辆位置,获取车辆所装载的车厢编号,并根据车辆位置和车厢目的地分配最佳运送路线;获取车辆即将到达的目的地所在位置附近的车厢编号和车厢装载信息,并将获取的所有目的地所在位置附近的车厢的收货地址按照最佳运送路线进行排列,提供车主选择,以便供车主选择和确定下次装载的车厢的详细信息,用来指导车辆前往,在卸下当前车厢后可以立即前往装载下一个车厢进行下一次的运送。
16.通过上述技术方案,本发明的有益效果为:本发明的基于云计算的物流货车复位装置可以将物流用小型货车改造成为甩挂运输车,既解决了大型挂车费用高的问题,又不需要办理复杂的手序和证件,又可以适用于小型的物流企业,在不加重企业的负担的前提下提高运输效率,加快物流速度,提升企业的核心竞争力。
17.本发明使用小型货车、中型货车或重型货车作为应用车辆,费用少,使用灵活,且对司机的要求不高,只需要c1或b2驾驶证即可,不需要牵引车的a1证,证件好考,办理证件也不复杂,对工人的技术要求降低,工人的工资成本降低,使得企业可以快速配套,尽早提升物流效率。
18.本发明的基于云计算的物流货车复位装置可以自动装卸车厢,不需要吊车吊装,方便调度。
19.本发明的驱动机构可以驱动车厢左右移动,驱动齿条的固定齿条两端设置有活动齿牙,提高驱动机构的容错率,延长使用寿命。
20.本发明的第一定位柱和第二定位柱可以将车厢定位,且方便使用,定位牢固,防止装货和运输过程中车厢移位,保证运输和装货安全。
附图说明
21.图1是本发明结构示意图;图2是本发明的车身部的俯视图;图3是图2的a
‑
a向剖视图;图4是图3的b部放大图;图5是图3的c部放大图;图6是本发明的第一定位柱的结构示意图;图7是本发明的车厢部的主视图;图8是本发明的车厢部的仰视图;图9是图8的d
‑
d向剖视图;图10是本发明的驱动齿条的结构示意图;图11是本发明的装货部的俯视图。
22.附图中标号为:1为车身部,2为车厢部,3为装货部,4为车架,5为驾驶室,11为第一定位框,12为第一运行轨道,13为第一止停机构,14为第一定位柱,15为驱动机构,21为承载板,22为滚轮组,23为驱动齿条,31为第二定位框,32为第二运行轨道,33为第二止停机构,
34为第二定位柱,111为缺口,112为滑槽,131为立柱,132为阻尼器,133为储油箱,141为液压油缸,142为固定头,151为驱动电机,152为驱动链轮,153为从动链轮,154为转轴,155为伸缩油缸,156为驱动齿轮,211为定位孔,231为固定齿条,232为活动齿牙,233为导向柱,1321为油腔,1322为第一弹簧,1323为防撞板,1421为圆形通孔,1422为定位环,1423为伸缩柱,2311为沉孔,2312为第二弹簧。
具体实施方式
23.下面结合附图和具体实施方式对本发明作进一步说明:需要说明的是,下面描述中使用的词语“前”、“后”、“左”、“右”、“上”、“下”、“底面”和“顶面”等方向词汇指的是附图中的方向,词语“内”和“外”分别指的是朝向或远离特定部件几何中心的方向。
24.如图1~图11所示,一种基于云计算的物流货车复位装置,包括车头5、车身和车厢,所述车身包括车架4和液压系统,所述车厢与车架4可拆卸地连接在一起,车厢在水平面的投影包围车架4在水平面的投影,还包括车身部1、车厢部2和装货部3,所述车厢经车厢部2和车身部1与所述车架4可拆卸地连接或所述车厢经车厢部2和装货部3可拆卸地连接;所述车身部1包括第一定位框11、第一运行轨道12、第一止停机构13、第一定位柱14和驱动机构15;所述第一定位框11为型钢焊接构成的与车厢等宽、长度大于车厢长度的格栅状的框架结构,所述第一定位框11的右端中部设置有向左凹陷、开口向右的长方形的缺口111,所述缺口111的前后相对的内侧面上均设置有滑槽112,所述滑槽112为向右上方拱起的弧形的槽体,两个滑槽112前后相对,所述第一定位框11底面固定连接车架4上表面;所述第一定位框11的上表面上设置有分别位于缺口111的前侧和后侧的两根互相平行的第一运行轨道12,所述每个第一运行轨道12均为开口向上的槽钢,第一运行轨道12的右端与第一定位框11的右端平齐、左端与第一定位框11的左端有间距,所述每个第一运行轨道12左侧的第一定位框11上表面均设置有一个第一止停机构13,所述每个第一止停机构13均由立柱131、阻尼器132和储油箱133组成,所述立柱131竖直固定在第一运行轨道12的左端的第一定位框11上表面上,立柱131的左侧面与第一定位框11的左侧面对齐,立柱131的右侧面上部设置有阻尼器132,所述阻尼器132由油腔1321、第一弹簧1322和防撞板1323组成,所述油腔1321为两个开口正对的筒体互相套接形成的水平设置的中空柱体,油腔1321内部同轴设置有第一弹簧1322,油腔1321右端同轴设置有圆盘状的具有弹性的防撞板1323,所述油腔1321左端固定在立柱131右侧面上,油腔1321内装有阻尼油,油腔1321左端周壁下部设置有贯穿油腔1321的泄油孔,所述油腔1321经泄油孔连接导管,所述导管的另一端连通置于立柱131顶端的储油箱133底面内壁,所述储油箱133为侧壁上端带有透气孔的长方形箱体;所述第一定位框11上设置有四个第一定位柱14,所述四个第一定位柱14中的两个第一定位柱14位于第一定位框11前侧的第一运行轨道12前方,另外两个第一定位柱14位于第一定位框11后侧的第一运行轨道12后方,每个所述第一定位柱14均由液压油缸141和固定头142组成,所述液压油缸141连接车身上的液压系统,所述液压油缸141的缸体上端固定连接第一定位框11底面,液压油缸141的活塞杆由下向上穿过第一定位框11的格栅孔,液压
油缸141的活塞杆的顶面连接固定头142,所述固定头142是上端为圆台状的中空柱体,固定头142的周壁上设置有多个贯穿固定头142周壁和中部连通的圆形通孔1421,所述每个圆形通孔1421内均设置有两个定位环1422,所述两个定位环1422分别靠近圆形通孔1421的内端和外端,所述圆形通孔1421内安装有圆柱状的伸缩柱1423,所述伸缩柱1423内端位于两个定位环1422之间,伸缩柱1423内端设置有与圆形通孔1421内壁滑动连接的凸环,伸缩柱1423周壁与靠近圆形通孔1421外端的定位环1422内壁滑动连接,固定头142中部内装有液压油,固定头142的中部下表面设置有贯穿固定头142、连通固定头142中部内的油孔,所述固定头142经油孔连接液压管道,所述液压管道连接车身上的液压系统,所述液压油缸141处于收缩状态时,固定头142的顶面与第一运行轨道12底面位于同一水平面;所述第一定位框11的右端设置有驱动机构15,所述驱动机构15包括驱动电机151、驱动链轮152、转轴154和伸缩油缸155,所述驱动电机151安装在第一定位框11下表面右端,驱动电机151的输出轴上连接有置于缺口111左端正下方的驱动链轮152,所述驱动链轮152经链条连接置于缺口111内的从动链轮153,所述从动链轮153固定连接在转轴154上,所述转轴154为圆形杆体,转轴154位于第一定位框11右端的缺口111内,转轴154的两端分别伸进呈相对状态的两个滑槽112内,所述转轴154位于滑槽112内的端部均设置有第一滚轮,所述伸缩油缸155连接车身上的液压系统,伸缩油缸155的缸体左端铰接在缺口111左侧内壁上,伸缩油缸155的活塞杆右端铰接在从动链轮153侧方的转轴154周壁上,所述伸缩油缸155的活塞杆与从动链轮153之间的转轴154周壁上设置有直径大于从动链轮直径的驱动齿轮156;所述车厢部2包括承载板21、驱动齿条23和滚轮组22,所述承载板21为长方形板体,承载板21上表面与车厢下表面固定连接,承载板21下表面中部设置有沿承载板21长度方向的驱动齿条23,所述驱动齿条23在车厢位于车身部1上方时与驱动齿轮156啮合,所述驱动齿条23包括一个固定齿条231和两个活动齿牙232,所述固定齿条231固定在承载板21下表面中部沿承载板21长度方向上,固定齿条231的左右两端均前后对称设置有沉孔2311,所述固定齿条231每一端的沉孔2311的数量均为前后对应的两个,每个所述沉孔2311内均同轴设置有导向柱233,所述导向柱233伸出固定齿条231,所述固定齿条231每一端的两个导向柱233上均共同套装有一个活动齿牙232,所述活动齿牙232与固定齿条231的齿牙模数一致,所述活动齿牙232的齿数为一个或两个,所述固定齿条231和活动齿牙232之间的导向柱233上套装有第二弹簧2312,所述固定齿条231每一端的两个导向柱233的端部共同连接有一块位于活动齿牙232外侧的封板,所述驱动齿条23前侧和后侧的承载板21底面上均设置有与第一定位框11上的第一运行轨道12相对应的滚轮组22,所述滚轮组22长度小于承载板21的长度、大于承载板21长度的五分之四,所述滚轮组22是由多个第二滚轮沿承载板21长度方向间隔设置构成,所述滚轮组22距离承载板21两端均有间距,所述承载板21底面设置有开口朝下的多个定位孔211,所述在车厢左端面与呈自然状态下的阻尼器132右端面接触时多个定位孔211与第一定位框11上的第一定位柱14一一上下对应,所述定位孔211为沉孔,定位孔211与固定头142高度一致,所述定位孔211的下端设置有向外扩大的倒角,定位孔211的中部设置有向外突出的环状槽体;所述装货部3位于车身部1右侧,所述装货部3包括第二定位框31、第二运行轨道32、第二止停机构33和第二定位柱34,所述第二定位框31与第一定位框11形状一致,第二定
位框31的长度小于第一定位框11的长度,第二定位框31底面安装有升降支架,所述升降支架固定在地面上,第二定位框31顶面与第一定位框11上表面平齐,第二运行轨道32、第二止停机构33和第二定位柱34分别与第一运行轨道12、第一止停机构13和第一定位柱14形状大小一致,且第二运行轨道32、第二止停机构33和第二定位柱34在第二定位框31上的安装位置与第一运行轨道12、第一止停机构13和第一定位柱14在第一定位框11上的安装位置呈左右相对状态,所述在车厢右端面与呈自然状态下的第二定位柱34的阻尼器左端面接触时,承载板21底面多个定位孔211与第二定位柱34一一上下对应。
25.所述第一运行轨道12的右端、第二运行轨道32的左端均设置有向外扩大的开口。
26.所述滑槽112所在圆环的圆心位于驱动电机151的输出轴的中心轴线上,滑槽112的左端位于电机输出轴的正上方。
27.所述固定齿条231的沉孔2311内的第二弹簧2312处于收缩状态时的长度小于沉孔2311深度,第二弹簧2312的自然长度大于等于导向柱233的长度。
28.所述第一止停机构13的阻尼器132的油腔1321正对承载板21的左侧面,第二止停机构33的阻尼器132的油腔1321正对承载板21的右侧面。
29.所述驱动齿轮156推动驱动齿条23向左移动,使车厢位于第一定位框11上,当承载板21左端与第一止停机构13的阻尼器132的油腔1321接触,所述固定齿条231左端的沉孔2311内的第二弹簧2312处于收缩状态时,第一定位柱14与定位孔211上下对应;所述驱动齿轮156推动驱动齿条23向右移动,使车厢位于第二定位框31上,当承载板21右端与第二止停机构33的阻尼器132的油腔1321接触,所述固定齿条231右端的沉孔2311内的第二弹簧2312处于收缩状态时,第二定位柱34与定位孔211上下对应。
30.所述装货部3和车厢部2连接时,第二定位柱34伸进定位孔211内,第二定位柱34的伸缩柱1423伸进定位孔211的环状槽体内;所述车身部1和车厢部2连接时,第一定位柱14伸进定位孔211内,第一定位柱14的伸缩柱1423伸进定位孔211的环状槽体内。
31.所述车厢由车身部1转移向装货部3或由装货部3转移向车身部1时,升降支架与车架4高度一致,第一定位框11上表面与第二定位框31上表面平齐。
32.所述车身和车厢上均装载有基于云计算的物流运输系统,所述基于云计算的物流运输系统,包括:车身定位监控模块,车厢定位监控模块,以及联网云计算模块;车厢定位监控模块包括gps定位器、信息存储器和信息发送器,实时存储与向联网云计算模块发送本车厢的gps定位和装载信息包括目前装载状态、目前车厢内货物的发送目的地、预计装满时间等。
33.所述车身定位监控模块包括gps定位器、信息存储器、信息发送器和地图显示器,车身定位监控模块用于实时定位本车位置、本车需要运送的车厢的目的地位置和车厢的装载信息进行实时显示,并显示下一次的车厢预选信息,所述gps定位器与联网云计算模块通过互联网连接;所述联网云计算模块用于获取所有物流车辆的车牌号,车辆型号和车辆位置,获取车辆所装载的车厢编号,并根据车辆位置和车厢目的地分配最佳运送路线;获取车辆即将到达的目的地所在位置附近的车厢编号和车厢装载信息,并将获取的所有目的地所在位置附近的车厢的收货地址按照最佳运送路线进行排列,提供车主选择,以便供车主选择和确定下次装载的车厢的详细信息,用来指导车辆前往,在卸下当前车厢后可以立即前往装
载下一个车厢进行下一次的运送。
34.本实施例的升降支架采用苏州科讯机械设备有限公司生产的固定式升降平台。
35.本发明在使用时有两种复位状态,一种是装货复位,即车厢脱离车架4运行到装货部3上并固定位置,等待装货的复位状态;另一种是运输复位,车厢装货结束,由装货部3运行到车架4上并固定位置,等待运输的复位状态。
36.基于云计算的物流货车(车头5、车身和车厢)在云计算的支持下,确定运输路线和需要的卸货位置,将车厢复位定位在卸货位置的装货部3上,再从根据指引从已经装好货物的装货部3上重新装载一个新的装好货物的车厢,从而达到甩挂运输的状态。
37.所述装货复位状态是指货车车身调整车辆位置到车尾与装货部3对齐,使第二定位柱34连接车身上的液压系统,启动升降支架使装货部3的第二定位框31上表面与车身部1的第一定位框11上表面平齐,并倒车到与装货部3靠近,货车调整好位置后,启动伸缩油缸155,伸缩油缸155拉动转轴154向滑槽112的左上侧滑动,转轴154带动驱动齿轮156沿滑槽112向上移到与承载板下表面的驱动齿条23相啮合状态(即图3和图5的虚线位置),此时,启动驱动电机151,驱动电机151的链轮通过链条带着从动链轮153旋转,从而使转轴154带动驱动齿轮156顺时针旋转,使驱动齿条23带着车厢向右移动,如图1所示虚线状态所示,当车厢右端向右移动到装货部3上的第二定位框31右端时,车厢下方的承载板21右端与第二止停机构33的阻尼器132接触,阻尼器132被承载板21向右压,油腔1321体积减小,油腔1321内的阻尼油经泄油孔向储油箱133内流动,泄油孔远小于油腔1321截面,泄油孔的油腔1321内的第一弹簧1322共同作用对车厢进行减速,在油腔1321压缩后车厢停止并被第二止停机构33的第一弹簧1322反向推动车厢向左移动,直到第一弹簧1322回恢复原长度,在第二止停机构33的第一弹簧1322反向推动车厢向移动的过程中,第二止停机构33的阻尼油由储油箱133向油腔1321内流动,对第一弹簧1322的作用力进行消减,避免第一弹簧1322作用力过大使车厢移动过快,承载板21上的定位孔211在油腔1321内的第一弹簧1322恢复原长时与第二定位柱34对齐,第二定位柱34向上升起进入定位孔211内,第二定位柱34顶端的伸缩柱1423伸出固定头142限制车厢的移动,实现装货复位状态。
38.所述运输复位状态是货车车身调整车辆位置到车尾与装货部3对齐,使第二定位柱34连接车身上的液压系统,启动升降支架使装货部3的第二定位框31上表面与车身部1的第一定位框11上表面平齐,并倒车到与装货部3靠近,货车调车好位置后,启动伸缩油缸155,伸缩油缸155拉动转轴154向滑槽112的左上侧滑动,转轴154带动驱动齿轮156沿滑槽112向左上方移动到与承载板下表面的驱动齿条23左端相啮合状态(即图3和图5的虚线位置),此时,第二定位柱34的伸缩柱1423收缩、第二定位柱34向下收缩,使车厢呈可移动状态,启动驱动电机151,驱动电机151的链轮通过链条带着从动链轮153旋转,从而使转轴154带动驱动齿轮156逆时针旋转,使驱动齿条23带着车厢向左移动,当车厢左端向左移动到车身部1的第一定位框11左端时,车厢下方的承载板21左端与第一止停机构13的阻尼器132接触如图1所示实线状态所示,阻尼器132被承载板21向左压,油腔1321体积减小,油腔1321内的阻尼油经泄油孔向储油箱133内流动,泄油孔远小于油腔1321截面,泄油孔的油腔1321内的第一弹簧1322共同作用对车厢进行减速,在油腔1321压缩后车厢停止并被油腔1321和第一弹簧1322反向推动车厢向右移动,直到第一弹簧1322回恢复原长度,在第一弹簧1322反向推动车厢向移动的过程中,阻尼油由储油箱133向油腔1321内流动,对第一弹簧1322的作
用力进行消减,避免第一弹簧1322作用力过大使车厢移动过快,承载板21上的定位孔211在油腔1321内的第一弹簧1322恢复原长时与第一定位柱14对齐,第一定位柱14向上升起进入定位孔211内,第一定位柱14顶端的伸缩柱1423伸出固定头142限制车厢的移动,实现运输复位状态。
39.本发明的基于云计算的物流货车复位装置可以将物流用小型货车改造成为甩挂运输车,既解决了大型挂车费用高的问题,车厢型号,外观一致的情况下不需要办理复杂的手序和证件,可以适用于小型的物流企业,在不加重企业的负担的前提下提高运输效率,加快物流速度,提升企业的核心竞争力。
40.本发明使用小型货车、中型货车或重型货车作为应用车辆,费用少,使用灵活,且对司机的要求不高,只需要c1或b2驾驶证即可,不需要牵引车的a1证,证件好考,办理证件也不复杂,对工人的技术要求降低,工人的工资成本降低,使得企业可以快速配套,尽早提升物流效率。
41.本发明的基于云计算的物流货车复位装置可以自动装卸车厢,不需要吊车吊装,方便调度。
42.本发明的驱动机构15可以驱动车厢左右移动,驱动齿条23的固定齿条231两端设置有活动齿牙,提高驱动机构15的容错率,延长使用寿命。
43.本发明的第一定位柱14和第二定位柱34可以将车厢定位,且方便用不用,定位牢固,防止装货和运输过程中车厢移位,保证运输和装货安全。
44.以上结合附图详细描述了本发明的优选实施方式,但是,本发明并不限于上述实施例,在不违背本发明的精神即公开范围内,可以对本发明的技术方案进行多种变形。