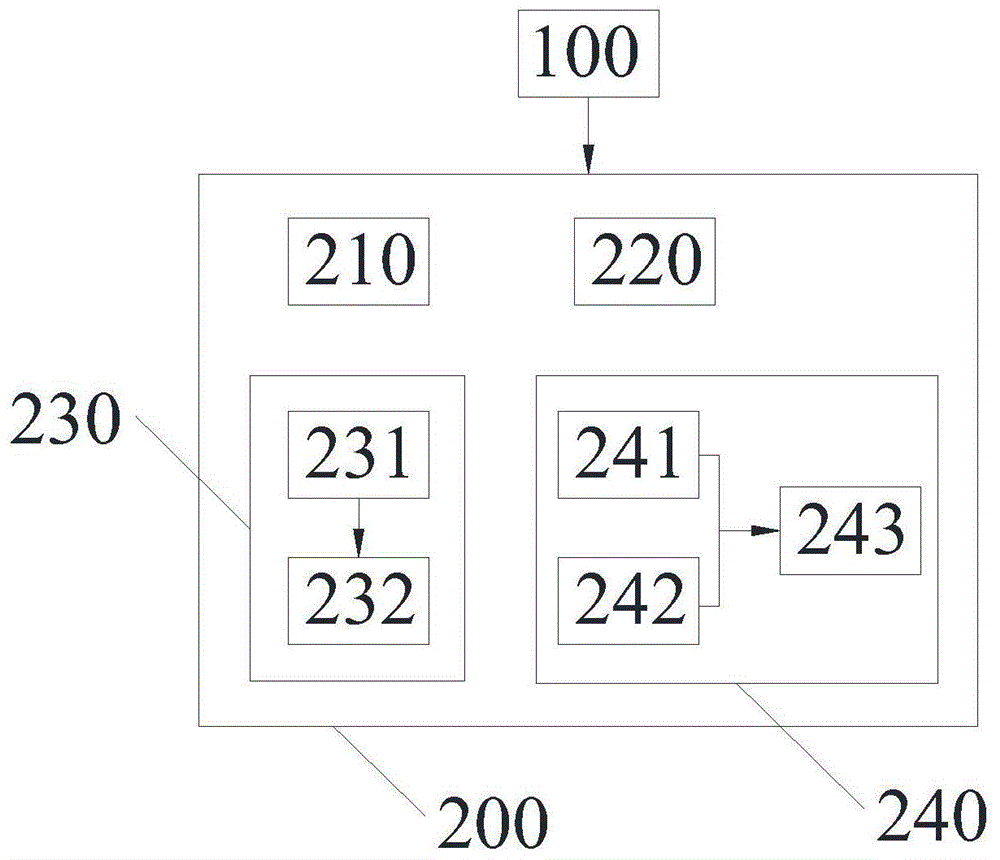
本发明涉及汽车制动
技术领域:
,具体地指一种电动汽车制动真空泵工作时间预测系统及其预测方法。
背景技术:
:新能源汽车行业快速发展,各主机制造厂新能源车型项目逐渐增多,由于成本限制,大多数新能源汽车的制动系统仍采用真空助力的方式,使用制动真空泵为纯电动汽车或者燃料电池汽车提供真空,是整车制动系统唯一的真空来源,对汽车安全有着关键意义。制动真空泵的寿命是有限的,一般通过设定开启和关闭的门限值,来控制制动真空泵的启动和停止,即当真空助力器前腔真空度低于设定的门限值时,制动真空泵工作提供真空补偿,保证整车的制动能力,当高于关闭门限值时,制动真空泵停止工作。如果制动真空泵的电机耐久性能低,有无法满足整车设计寿命的风险,电机设计性能过高,会导致成本上升,因此在设计阶段,通过理论方法计算制动真空泵在整车设计寿命中的实际工作次数与累计工作时间就非常具有价值。中国专利cn109707614a公开了一种制动真空泵寿命耐久测试设备及其使用方法。该提案设计了一套用于测试制动真空泵的试验台,通过实际试验的方式,来考核制动真空泵是否满足整车设计寿命的要求。台架试验是在零件设计开发中的一种重要且结果较为准确的验证手段,但台架资源需要样件、工装、费用等支持,适用于功能和性能验证阶段,无法在方案设计阶段对可行性做出快速评估。技术实现要素:本发明的目的就是要克服上述现有技术存在的不足,提供一种电动汽车制动真空泵工作时间预测系统及其预测方法,可以在前期设计阶段,精确地预测出制动真空泵的工作时间,从而简便快速的确定制动真空泵的选型。为实现上述目的,本发明提供一种电动汽车制动真空泵工作时间预测系统,包括通讯连接的信息获取模块和预测模块,所述信息获取模块用于获取整车生命周期内的整车总制动次数、整车总启动次数、制动减速度概率分布、制动真空泵初始真空度和制动真空泵开启真空度,所述预测模块包括:制动液压概率分布模块,所述制动液压概率分布模块用于根据制动减速度概率分布、制动减速度与制动液压的关系确定制动液压概率分布;制动次数模块,所述制动次数模块用于根据制动液压、制动真空泵初始真空度和制动真空泵开启真空度确定不同制动液压下制动真空泵开启所需的制动次数;开启次数模块,所述开启次数模块用于根据制动液压概率分布、整车总制动次数和不同制动液压下制动真空泵开启所需的制动次数确定整车生命周期内制动真空泵的总开启次数;工作时间模块,所述工作时间模块用于根据整车生命周期内制动真空泵的总开启次数、整车总启动次数以及制动真空泵抽气特性曲线确定在整车生命周期内制动真空泵的总工作时间。进一步地,所述开启次数模块还包括:开启次数求和模块,所述开启次数求和模块用于对不同制动液压下制动真空泵的开启次数进行求和;单次开启次数模块,所述单次开启次数模块用于根据制动液压概率分布、整车总制动次数和该制动液压下制动真空泵开启所需的制动次数得到不同制动液压下制动真空泵的开启次数;进一步地,所述工作时间模块包括:第一工作时间模块,所述第一工作时间模块用于根据制动真空泵抽气特性曲线和制动真空泵的总开启次数确定整车运行时的制动真空泵总开启时间;第二工作时间模块,所述第二工作时间模块用于根据制动真空泵抽气特性曲线和整车总启动次数得到定整车启动时的制动真空泵总开启时间;工作时间求和模块,所述工作时间求和模块用于对整车运行时的制动真空泵总开启时间和整车启动时的制动真空泵总开启时间进行求和。本发明还提供一种基于上述所述的电动汽车制动真空泵工作时间预测系统的预测方法,包括:分别获取整车生命周期内的整车总制动次数z、整车总启动次数s、制动减速度概率分布a—x、制动真空泵初始真空度po和制动真空泵开启真空度pstart;根据制动减速度概率分布a—x、制动减速度a与制动液压pn的关系得到制动液压概率分布pn—x;根据制动液压pn确定单次制动真空度消耗值an,再根据制动真空泵初始真空度po和制动真空泵开启真空度pstart确定不同制动液压下制动真空泵开启所需的制动次数zn;根据制动液压概率分布pn—x和不同制动液压下制动真空泵开启所需的制动次数zn得到制动真空泵的总开启次数n;根据整车生命周期内制动真空泵的总开启次数n以及制动真空泵的抽气特性曲线确定制动真空泵的总工作时间t。进一步地,所述制动减速度概率分布a—x为制动减速度在多个连续区间段的制动次数占比。进一步地,所述制动液压概率分布pn—x的确定方法包括,根据每个制动减速度区间段中的最大制动减速度标定对应的多个制动液压,得到每个制动液压的占比。进一步地,不同制动液压下真空泵开启所需的制动次数zn的确定方法包括,将制动真空泵初始真空度po和制动真空泵开启真空度pstart之差除以单次制动真空度消耗值an,将所得的比值取整之后加1。进一步地,所述制动真空泵的总开启次数n的确定方法包括,对不同制动液压下制动真空泵的开启次数nn进行求和。进一步地,不同制动液压下制动真空泵的开启次数nn的确定方法包括,根据制动液压概率分布pn—x得到该制动液压的占比,将该制动液压的占比乘以整车总制动次数z,然后除以该制动液压下制动真空泵开启所需的制动次数zn。进一步地,所述制动真空泵的总工作时间t的确定方法包括,根据制动真空泵抽气特性曲线确定整车运行时的制动真空泵单次开启时间t2,然后乘以制动真空泵的总开启次数n得到整车运行时的制动真空泵总开启时间tkq;同时根据制动真空泵抽气特性曲线确定整车启动时的制动真空泵单次开启时间t1,然后乘以整车总启动次数s得到定整车启动时的制动真空泵总开启时间tqd,对整车运行时的制动真空泵总开启时间tkq和整车启动时的制动真空泵总开启时间tqd进行求和。本发明的有益效果:1、预测结果精确度高,确保满足制动设计要求:本发明通过制动真空泵工作时间预测系统,构建了整车生命周期内的总制动次数、总启动次数、制动减速度概率分布以及制动真空泵抽气特性曲线与制动真空泵的总工作时间之间的计算模型,且在确定制动真空泵的总开启次数以及整车启动时的制动真空泵总开启时间时均为极限状态下的取值,保证了制动真空泵的总工作时间的预测结果为极限状态下的最大值,从而确保所选择的制动真空泵完全能够满足制动的需求。2、缩短开发周期。本发明的预测可以提前到前期设计阶段进行,只需根据设计要求进行理论计算,无需进行试验,极大的缩短了制动真空泵选型的开发周期。附图说明图1为本发明的预测系统结构图。图2为本发明的预测方法流程图。图3为制动真空泵抽气特性曲线。图中各部件标号如下:信息获取模块100、预测模块200、制动液压概率分布模块210、制动次数模块220、开启次数模块230、开启次数求和模块231、单次开启次数模块232、工作时间模块240、第一工作时间模块241、第二工作时间模块242、工作时间求和模块243。具体实施方式下面具体实施方式用于对本发明的权利要求技术方案作进一步的详细说明,便于本领域的技术人员更清楚地了解本权利要求书。本发明的保护范围不限于下面具体的实施例。本领域的技术人员做出的包含有本发明权利要求书技术方案而不同于下列具体实施方式的也是本发明的保护范围。如图1所示,一种电动汽车制动真空泵工作时间预测系统,包括通讯连接的信息获取模块100和预测模块200,信息获取模块100用于获取整车生命周期内的整车总制动次数、整车总启动次数、制动减速度概率分布、制动真空泵初始真空度、制动真空泵开启真空度以及制动真空泵抽气特性曲线,预测模块200包括互相之间并行计算的制动液压概率分布模块210、制动次数模块220、开启次数模块230、工作时间模块240,他们的功能如下:制动液压概率分布模块210用于根据制动减速度概率分布、制动减速度与制动液压的关系确定制动液压概率分布;其中,制动减速度概率分布a—x为制动减速度在多个连续区间段的制动次数占比,详见表1。表1制动减速度概率分布表制动减速度a占比x0<a≤0.2x10.2<a≤0.3x20.3<a≤0.4x30.4<a≤0.5x40.5<a≤0.6x50.6<a≤0.7x60.7<a≤0.8x70.8<a≤0.9x80.9<a≤1x9x﹥1x10制动次数模块220用于根据制动液压、制动真空泵初始真空度和制动真空泵开启真空度确定不同制动液压下制动真空泵开启所需的制动次数;开启次数模块230用于根据制动液压概率分布、整车总制动次数和不同制动液压下制动真空泵开启所需的制动次数确定整车生命周期内制动真空泵的总开启次数;工作时间模块240用于根据整车生命周期内制动真空泵的总开启次数、整车总启动次数以及制动真空泵抽气特性曲线确定在整车生命周期内制动真空泵的总工作时间。上述技术方案中,开启次数模块230还包括开启次数求和模块231和单次开启次数模块232。其中,开启次数求和模块231用于对不同制动液压下制动真空泵的开启次数进行求和;单次开启次数模块232用于根据制动液压概率分布、整车总制动次数和该制动液压下制动真空泵开启所需的制动次数得到不同制动液压下制动真空泵的开启次数。上述技术方案中,工作时间模块240包括第一工作时间模块241、第二工作时间模块242和工作时间求和模块243。第一工作时间模块241用于根据制动真空泵抽气特性曲线和制动真空泵的总开启次数确定整车运行时的制动真空泵总开启时间;第二工作时间模块242用于根据制动真空泵抽气特性曲线和整车总启动次数得到定整车启动时的制动真空泵总开启时间;工作时间求和模块243用于对整车运行时的制动真空泵总开启时间和整车启动时的制动真空泵总开启时间进行求和。如图2所示,上述的电动汽车制动真空泵工作时间预测系统的预测方法如下:1、获取参数信息通过信息获取模块100分别获取整车生命周期内的整车总制动次数z、整车总启动次数s、制动减速度概率分布a—x、制动真空泵初始真空度po、制动真空泵开启真空度pstart、制动真空泵抽气特性曲线。由于在整车设计阶段,需要对制动真空泵进行选型,针对某一款制动真空泵,制动真空泵初始真空度po、制动真空泵开启真空度pstart以及制动真空泵抽气特性曲线是确定的,但是需要确定制动真空泵的设计寿命,使得设计寿命大于其总工作时间,因此需要预测出制动真空泵的最大总工作时间。而整车总制动次数z、整车总启动次数s和制动减速度概率分布a—x是整车设计阶段的设定值。2、确定制动液压概率分布由于在踩下制动踏板时,制动踏板的开度是与制动减速度一一对应的,而制动踏板的开度又与制动管路中的制动液压一一对应,因此制动减速度与制动液压一一对应,由于制动减速度越大,其单次制动的制动真空度消耗值越大,使得需要更少次数的制动就能降低制动真空度低于制动真空泵开启真空度,从而触发制动真空泵开启的次数增多,增大了制动增空泵的工作时间,因此为了制动真空泵的设计寿命能够完全满足各种工况下的总工作时间,需要取制动减速度的最大值,因此根据每个制动减速度区间段中的最大制动减速度标定对应的多个制动液压,详见表2,得到每个制动液压的占比,从而得到制动液压概率分布,详见表3。表2制动减速度与制动液压标定表制动减速a制动液压p0.20p10.30p20.40p30.50p40.60p50.70p60.80p70.90p81p91.1p10表3制动液压概率分布表制动液压p占比xp1x1p2x2p3x3p4x4p5x5p6x6p7x7p8x8p9x9p10x103、确定不同制动液压下制动真空泵开启所需的制动次数zn由于制动液压与制动真空度消耗值存在一一对应关系,因此根据制动液压pn可以标定单次制动真空度消耗值an,而制动真空泵需要满足开启条件必须使制动真空泵初始真空度po和降低到小于或等于制动真空泵开启真空度pstart,需要间断多次进行制动动作,才能使得制动真空泵开启,因此不同制动液压下制动真空泵开启所需的理论制动次数zn表达为由于此数值不一定是整数,因此实际的制动次数应该是大于此数值最近的整数,因此不同制动液压下制动真空泵开启所需的制动次数zn表达为作为一种优选方案,其中制动真空泵初始真空度po可以取制动真空泵关闭真空度pstop,因为每一次制动真空泵开启后都会把真空度抽至pstop才关闭,直到下一次开启,在这个中间阶段,由于制动真空泵会存在一点自然消耗,使得真空度稍低于pstop,因此将制动真空泵关闭真空度pstop作为制动真空泵初始真空度,算出来的制动次数zn最大,使得最终的制动真空泵总工作时间最大。表4制动液压与制动真空度消耗值标定表制动液压p制动真空度消耗值anp1a1p2a2p3a3p4a4p5a5p6a6p7a7p8a8p9a9p10a104、确定制动真空泵的总开启次数n制动真空泵的总开启次数n为不同制动液压下制动真空泵的开启次数nn之和;不同制动液压下制动真空泵的开启次数nn的确定方法为,根据制动液压概率分布pn—x得到该制动液压的占比,将该制动液压的占比乘以整车总制动次数z得到该制动液压下的总制动次数,然后除以该制动液压下制动真空泵开启所需的制动次数zn,制动真空泵的总开启次数n表示为5、确定制动真空泵的总工作时间制动真空泵的总工作时间t为整车运行时的制动真空泵总开启时间tkq和整车启动时的制动真空泵总开启时间tqd之和;其中,整车运行时的制动真空泵总开启时间tkq是指,整车完成了启动,制动真空度达到制动真空泵的关闭真空度p之后,由于踩制动踏板导致制动真空泵开启的总时间;整车启动时的制动真空泵总开启时间是指整车在启动阶段制动真空度从初始值到制动真空度达到制动真空泵的关闭真空度的总工作时间,为了考虑极限工况,假设每次启动时,制动真空度的初始值均为0,这样所求的制动真空泵的总工作时间最大。上述技术方案中,如图3所示,根据制动真空泵抽气特性曲线确定整车运行时的制动真空泵单次开启时间t2,即制动真空度从开启真空度pstart到关闭真空度pstop的工作时间,然后乘以制动真空泵的总开启次数n得到整车运行时的制动真空泵总开启时间tkq;同时根据制动真空泵抽气特性曲线确定整车启动时的制动真空泵单次开启时间t1,即制动真空度从0到关闭真空度pstop的工作时间,然后乘以整车总启动次数s得到定整车启动时的制动真空泵总开启时间tqd,制动真空泵的总工作时间t表示为t=n·t2+s·t1。最后,考虑到制动真空泵的设计寿命需要满足要求,且又不能增大成本,因此既需要使制动真空泵的设计寿命大于制动真空泵的总工作时间,又要使制动真空泵的设计寿命不能超过制动真空泵的总工作时间太多,依此选择合适设计寿命的制动真空泵的型号。当前第1页12