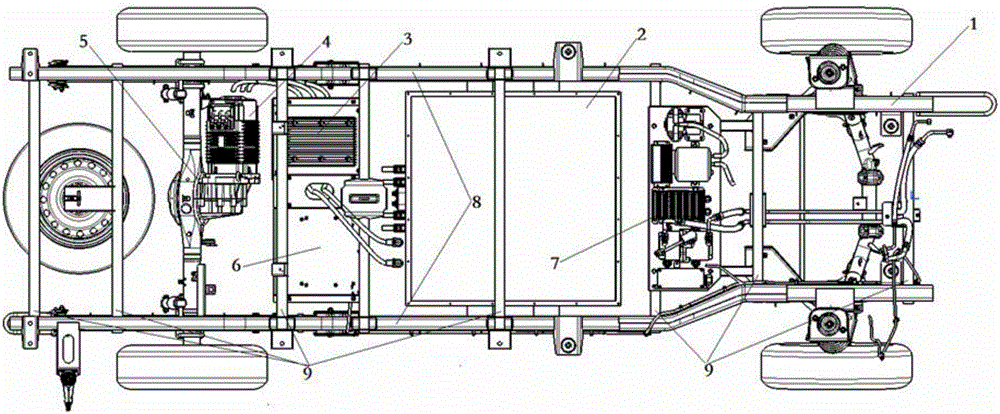
本发明涉及纯电动汽车技术领域,特别的涉及一种纯电动汽车底盘结构。
背景技术:
随着全球范围内能源和环境压力越来越大,节能环保的概念已经渗透到各个领域。对于汽车工业来讲,与传统的燃油和燃气发动机汽车相比,以动力电池作为动力源的电动汽车因其清洁环保的特点逐渐步入广泛的实用阶段。
国内现有电动小汽车底盘大多是从燃油车底盘改制而成,因电动机和发动机的安装结构和安装位置存在很大的差异,在动力系统以及驱动系统的空间布置上存在很多弊端。燃油车的底盘在设计时充分考虑了发动机的安装空间及传动系统的布置空间,底盘前部空间大,中后部空间紧凑,车架总成前端较宽,后端较窄。然而,纯电动汽车的底盘需要安装的电池较多,底盘中后部需要更大的安装空间,且驱动装置的各个部件所处的位置也与燃油车底盘不一样,从而使得驱动装置的布局也不够合理。另外,现有的电机安装大都是通过变速箱和传动轴将动力传递给驱动桥, 传动效率非常低。
另外大部分现有的电动小汽车底盘结构中,其电池包安装结构,均是采用开放式安装结构,方便单块电池的检修更换等操作,但这种结构还存在以下缺陷:1、车辆涉水深度能力较低,电池容易进水短路,遇到暴雨天气特别容易熄火。2、由于电动车需要设置相对比较复杂的电气系统以对电池和电机等构件进行管理,用于电力控制的构件较多相互之间容易产生干扰而影响车辆性能。3、电池包外部线缆过多,电池包整体性低导致稳定性差,单块电池容易产生松动或因积灰而短路等现象,不利于管理,电池使用寿命较短。
技术实现要素:
针对上述现有技术的不足,本发明所要解决的技术问题是:如何提供一种布局合理,能够提高车辆平衡性,提高电机传动效率,提高对电池保护效果,车辆涉水深度大,电气系统抗干涉性好,管理稳定可靠,电池使用寿命更长的纯电动汽车底盘结构。
为了解决上述技术问题,本发明采用了如下的技术方案:
一种纯电动汽车底盘结构,包括整体呈水平的矩形框架结构的车架,车架上安装有充电机、和充电机相连的电池总成、和电池总成相连的驱动电机,驱动电机安装在后桥上并和后轮驱动连接,还包括分别和驱动电机及电池总成相连的控制器以及用于和车辆操控系统相连的直流斩波器(DC/DC);其特征在于,车架包括两根水平且左右正对设置的主骨架和多根水平横向连接在主骨架之间的横梁,车架前半部靠近前轮位置处的主骨架具有一段前窄后宽的梯形段,所述直流斩波器安装布置在梯形段内,电池总成安装布置在梯形段位置后方相邻处,控制器和充电机左右并列地安装在电池总成和驱动电机之间的位置,电池总成包括一个密封设置的电池盒,电池安装在电池盒内,电池盒上设置接口和驱动电机、控制器以及充电机相连。
这样,本方案的纯电动汽车底盘结构车架结构布局合理,提高了车辆平衡性和稳定性,提高了电机传动效率,电池密封安装在电池盒内形成电池包,能够更好地提高车辆涉水性能,提高对电池保护效果,延长电池使用寿命。
作为优化,所述后桥包括管状的后桥壳体,设置后桥壳体内并用于和后轮相连的半轴,后桥壳体上焊接固定有主减速器,驱动电机固定安装在主减速器上,驱动电机输出轴通过花键和主减速器输出轴连接,主减速器输出端和半轴传动连接。
这样,提高车辆后桥总成的结构一体性,提高稳定性,具有结构合理,传动效率高的特点。
作为优化,所述电池盒下部焊接固定有一块沿左右方向设置的安装托架,安装托架整体呈凹形板状且凹形处和电池盒下表面中部贴合连接,安装托架两侧固定连接在车架的主骨架上。
这样结构简单,方便电池盒安装结构的加工设置,同时提高了电池和装配固定的便捷性和可靠性。
作为优化,电池盒包括对合连接呈矩形体的盒体和盒盖,盒体和盒盖之间对合连接处各自具有水平向外延伸的法兰边,盒体和盒盖的法兰边之间压接有密封垫圈并靠螺栓固定。保证其密封固定效果。其中密封垫圈优选为EVA垫圈。具有良好的化学稳定性、耐老化性能和电信号隔绝性,保证空间密封和信号屏蔽效果。
作为优化,电池盒采用金属材料制得,电池盒内设置有BMS(电池管理系统)和电池相连,还设置有保险模块和继电控制电路模块,BMS和电池盒上的信号线接口相连,信号线接口和控制器相连。
这样,电池盒采用金属材料制得,并将部分管理控制元件集成到电池盒内,不仅仅简化了原高压配电盒,方便提高对电池包的控制效率,避免外部线缆缠绕,降低电气故障率,而且可以依靠金属电池盒的电磁屏蔽效果,更好地避免电气元件之间的相互干涉,提高控制的稳定性和可靠性。
作为优化,电池盒上的接口包括所述信号线接口,还包括单独设置的快充正接口、快充负接口、放电正接口和放电负接口,还包括集成了正负极端子的慢充接口。各接口通过继电控制电路模块与保险模块和电池相连。
这样,可以更好地方便电池盒和外部电器件的线路连接。同时设置了快充和慢充两种充电方式,以适用于不同的需求情况。
作为进一步优化,电池盒内电池的正极接出导线串联有一个总保险丝,再通过一路安装有主正接触器的放电正极电路连接到放电正接口,主正接触器具有一个和BMS相连的主继电器控制端;总保险丝后还设置有和放电正极电路并联的一路慢充正极电路和一路快充正极电路,慢充正极电路中串联安装一个慢充保险丝和慢充接触器后连接到慢充接口的正极端子,慢充接触器具有一个和BMS相连的慢充继电器控制端;快充正极电路中串联安装一个快充保险丝和快充接触器后连接到快充正接口,快充接触器具有一个和BMS相连的快充继电器控制端;
电池盒内电池的负极接出导线连接有一个分流器,然后再串联一个主负接触器后分别靠并联的电路连接到快充负接口、放电负接口和慢充接口中的负极端子,所述主负接触器具有一个和BMS相连的的总负继电器控制端。
这样的电路控制结构,方便更好地实现对电池盒内快充电路、慢充电路以及负载放电电路的控制管理,实现高压保险,提高安全性。实施时分流器优选为75MV/400A型号适应电流检测需求。各接触器采用工作电压12V的接触器以适应控制要求。
作为优化,电池盒上的接口还包括集成有正负极端子的DC/空调输出接口,电池盒内的电池正极接出的导线电路中位于主正接触器后方的放电正极电路上还并列设置有一个DC/空调正极电路,DC/空调正极电路中串联有DC/空调保险丝且和DC/空调输出接口的正极端子相连接;电池盒内的电池负极接出的导线电路中主负接触器后还并联设置有一路电路连接到DC/空调输出接口的负极端子。其中DC/空调输出接口用于和直流斩波器(DC/DC)以及车载空调相连接。
这样,采用简单的电路结构,在电池盒内集成保留了DC/空调的保险和控制功能,将这部分控制元件集成到电池包内,进一步简化了原高压配电盒的配置,同时更加利于会导致信号干扰的电气构件之间的干扰屏蔽,提高车辆系统整体电控稳定性。
作为优化,电池盒内的电池正极接出的导线电路中还设置有和主正接触器相并联的预充电路,预充电路中串联设置有一个预充电阻和预充接触器,预充接触器具有一个和BMS相连的预充继电器控制端。
这样,采用简单的电路结构实现了对电池包输出负载端中负载的电容元件的预充,实现对负载端的预启动,更好地提高电气控制的稳定性并延长相应的电气构件使用寿命。同时该结构还能够实现控制端靠主正接触器控制或者预充接触器控制之间的切换,而且使其各自分别能够同时控制放电正接口所接负载和DC/空调输出接口所连接的负载,提高了控制的方便性和灵活性。实施时,预充电阻采用100R/250W的电阻,使其更加适应于负载输出端的针对性要求。
作为优化,电池盒内的电池正极或者负极接出的导线电路中还安装有一个检修用的总控制开关,所述总控制开关具有一个露出于电池盒的开关按钮。这样,更加方便实现检修安全控制以及提高打开电池盒时的安全性。
综上所述,本发明布局合理,能够提高车辆平衡性,提高电机传动效率,提高对电池保护效果,具有车辆涉水深度大,电气系统抗干涉性好,管理稳定可靠,电池使用寿命更长等优点。
附图说明
图1为本发明实施例的结构示意图。
图2为图1中单独电池盒的结构示意图。
图3为图2的电池盒内部的电气原理图。
具体实施方式
下面结合附图对本发明作进一步的详细说明。
具体实施时:如图1-3所示,一种纯电动汽车底盘结构,包括整体呈水平的矩形框架结构的车架1,车架上安装有充电机6、和充电机6相连的电池总成、和电池总成相连的驱动电机4,驱动电机4安装在后桥5上并和后轮驱动连接,还包括分别和驱动电机4及电池总成相连的控制器3(此处控制器主要是指驱动电机控制器MCU)以及用于和车辆操控系统相连的直流斩波器(DC/DC)7;其特点在于,车架1包括两根水平且左右正对设置的主骨架8和多根水平横向连接在主骨架之间的横梁9,车架前半部靠近前轮位置处的主骨架具有一段前窄后宽的梯形段,所述直流斩波器7安装布置在梯形段内,电池总成安装布置在梯形段位置后方相邻处,控制器和充电机左右并列地安装在电池总成和驱动电机之间的位置,电池总成包括一个密封设置的电池盒2,电池安装在电池盒2内,电池盒2上设置接口和驱动电机、控制器以及充电机相连。
这样的纯电动汽车底盘结构车架结构布局合理,提高了车辆平衡性和稳定性,提高了电机传动效率,电池密封安装在电池盒内形成电池包,能够更好地提高车辆涉水性能,提高对电池保护效果,延长电池使用寿命。
本实施方式中,所述后桥5包括管状的后桥壳体,设置后桥壳体内并用于和后轮相连的半轴,后桥壳体上焊接固定有主减速器,驱动电机4固定安装在主减速器上,驱动电机4输出轴通过花键和主减速器输出轴连接,主减速器输出端和半轴传动连接。这样,提高车辆后桥总成的结构一体性,提高稳定性,具有结构合理,传动效率高的特点。
本实施方式中,所述电池盒2下部焊接固定有一块沿左右方向设置的安装托架10,安装托架10整体呈凹形板状且凹形处和电池盒下表面中部贴合连接,安装托架两侧固定连接在车架的主骨架上。这样方便电池盒安装结构的加工设置,同时提高了电池和装配固定的便捷性和可靠性。
本实施方式中,电池盒2包括对合连接呈矩形体的盒体和盒盖,盒体和盒盖之间对合连接处各自具有水平向外延伸的法兰边,盒体和盒盖的法兰边之间压接有密封垫圈并靠螺栓固定。保证其密封固定效果。其中密封垫圈优选为EVA垫圈。具有良好的化学稳定性、耐老化性能和电信号隔绝性,保证空间密封和信号屏蔽效果。
本实施方式中,电池盒2采用金属材料制得,电池盒内设置有BMS(电池管理系统)和电池相连,还设置有保险模块和继电控制电路模块,BMS和电池盒2上的信号线接口11相连,信号线接口11和控制器(实施时,信号线接口同时连接驱动电机控制器MCU和整车控制器VCU,另外实现充电控制的信号线路也是通过信号线接口实现连接)相连。这样,不仅仅简化了原高压配电盒,方便提高对电池包的控制效率,避免外部线缆缠绕,降低电气故障率,而且可以依靠金属电池盒的电磁屏蔽效果,更好地避免电气元件之间的相互干涉,提高控制的稳定性和可靠性。
本实施方式中,电池盒2上的接口包括所述信号线接口11,还包括单独设置的快充正接口12、快充负接口13、放电正接口14和放电负接口15,还包括集成了正负极端子的慢充接口16。各接口通过继电控制电路模块与保险模块和电池相连。这样,可以更好地方便电池盒和外部电器件的线路连接。同时设置了快充和慢充两种充电方式,以适用于不同的需求情况。
本实施方式中,电池盒内电池的正极接出导线串联有一个总保险丝19,再通过一路安装有主正接触器20的放电正极电路连接到放电正接口14,主正接触器20具有一个和BMS相连的主继电器控制端;总保险丝19后还设置有和放电正极电路并联的一路慢充正极电路和一路快充正极电路,慢充正极电路中串联安装一个慢充保险丝21和慢充接触器22后连接到慢充接口16的正极端子,慢充接触器22具有一个和BMS相连的慢充继电器控制端;快充正极电路中串联安装一个快充保险丝23和快充接触器24后连接到快充正接口12,快充接触器24具有一个和BMS相连的快充继电器控制端;
电池盒内电池的负极接出导线连接有一个分流器25,然后再串联一个主负接触器26后分别靠并联的电路连接到快充负接口13、放电负接口15和慢充接口16中的负极端子,所述主负接触器26具有一个和BMS相连的的总负继电器控制端。
这样的电路控制结构,方便更好地实现对电池盒内快充电路、慢充电路以及负载放电电路的控制管理,实现高压保险,提高安全性。实施时分流器优选为75MV/400A型号适应电流检测需求。各接触器采用工作电压12V的接触器以适应控制要求。
本实施方式中,电池盒上的接口还包括集成有正负极端子的DC/空调输出接口17,电池盒内的电池正极接出的导线电路中位于主正接触器20后方的放电正极电路上还并列设置有一个DC/空调正极电路,DC/空调正极电路中串联有DC/空调保险丝27且和DC/空调输出接口17的正极端子相连接;电池盒内的电池负极接出的导线电路中主负接触器后还并联设置有一路电路连接到DC/空调输出接口17的负极端子。其中DC/空调输出接口用于和直流斩波器(DC/DC)以及车载空调相连接。
这样,采用简单的电路结构,在电池盒内集成保留了DC/空调的保险和控制功能,将这部分控制元件集成到电池包内,进一步简化了原高压配电盒的配置,同时更加利于会导致信号干扰的电气构件之间的干扰屏蔽,提高车辆系统整体电控稳定性。
本实施方式中,电池盒内的电池正极接出的导线电路中还设置有和主正接触器相并联的预充电路,预充电路中串联设置有一个预充电阻28和预充接触器29,预充接触器29具有一个和BMS相连的预充继电器控制端。
这样,采用简单的电路结构实现了对电池包输出负载端中的负载电容构件的预充,实现对负载端的预启动,更好地提高电气控制的稳定性并延长相应的电气构件使用寿命。同时该结构还能够实现控制端靠主正接触器控制或者预充接触器控制之间的切换,而且使其各自分别能够同时控制放电正接口所接负载和DC/空调输出接口所连接的负载,提高了控制的方便性和灵活性。实施时,预充电阻采用100R/250W的电阻,使其更加适应于负载输出端的针对性要求。
本实施方式中,电池盒内的电池正极或者负极接出的导线电路中还安装有一个检修用的总控制开关,所述总控制开关具有一个露出于电池盒2的开关按钮18。这样,更加方便实现检修安全控制以及提高打开电池盒时的安全性。