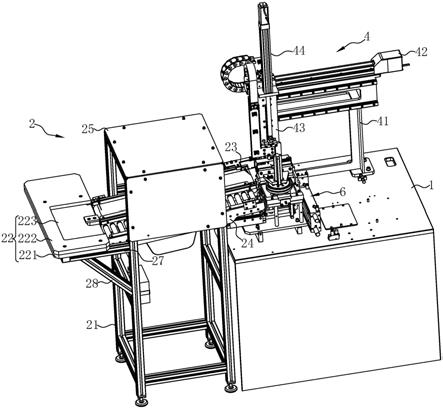
1.本技术涉及磁信号轮上料的领域,尤其是涉及一种磁信号轮充磁用上料装置。
背景技术:2.信号轮是汽车曲轴中十分重要的一部分,信号轮与曲轴传感器相配合,曲轴传感器通过读取齿数来确定曲轴位置,即发动机当前位置,以便打火。随着汽车行业的高速发展,普通的信号轮由于加工复杂已逐渐被磁信号轮所取代。
3.磁信号轮生产制造的复杂程度低,加工后只需充磁即可投入使用。具体请参考授权公告号为cn208672660u的中国专利,其公开了一种充磁橡胶转速信号轮,包括轮体、充磁橡胶圈和霍尔传感器,轮体具有主体部和安装部,安装部绕主体部的边缘周向设置;充磁橡胶圈套装在安装部上,充磁橡胶圈包括强磁段和弱磁段,强磁段与弱磁段连接组成磁段组件,磁段组件绕安装部形成充磁橡胶圈;霍尔传感器的感应头部正对且靠近充磁橡胶圈。
4.目前对磁信号轮进行充磁主要是采用充磁机,加工时,需通过工作人员将磁信号轮一个个的放置在充磁机上,以便充磁作业。
5.针对上述中的相关技术,发明人认为人工上料的方式存在有效率低的缺陷。
技术实现要素:6.为了提高工作效率,本技术提供一种磁信号轮充磁用上料装置。
7.本技术提供的一种磁信号轮充磁用上料装置,采用如下的技术方案:
8.一种磁信号轮充磁用上料装置,包括水平的工作台、位于工作台一侧的上料工位、安装在工作台上的用于暂放磁信号轮的待取用工位,以及设置在待取用工位上方、用于对磁信号轮进行转移的搬运工位;
9.上料工位至少包括机架、安装在机架上且一端延伸至工作台上方的上料传送部和下料传送部以及用于携带磁信号轮的载具,待取用工位位于上料传送部末端的一侧并且与下料传送部的始端衔接;
10.上料传送部输送满载的载具;下料传送部输送空载的载具;
11.工作台上设有将输送至上料传送部末端的载具拨送至待取用工位上的拨料机构,上料传送部上安装有与拨料机构联动以对上料传送部上的载具进行限位的挡料机构;
12.待取用工位上设有将空载的载具拨送至下料传送部上的卸料机构。
13.通过采用上述技术方案,作业时,通过上料传送部对满载的载具进行输送,输送至终端时,拨料机构将满载的载具拨送至待取用工位上,与此同时,挡料机构动作,即对上料传送部上其余的载具进行限位,载具就位后,搬运工位将载具上的磁信号轮逐个转移至充磁装置上进行充磁作业;当载具空载后,卸料机构将空载的载具拨送至下料传送部上进行输送,整个过程采用自动化作业,相较于人工上料的方式,工作效率更高。
14.优选的,所述上料传送部为皮带式输送机,上料传送部包括固定传送段以及铰接于固定传送段末端且表面与待取用工位表面相平齐的调节传送段。
15.通过采用上述技术方案,以便载具能够由调节传送段平稳的移动至待取用工位上。
16.优选的,所述调节传送段的末端水平设置有与自身输送方向相垂直的挡杆。
17.通过采用上述技术方案,载具被输送至调节传送段末端时,挡杆对载具进行限位,阻碍载具继续移动。
18.优选的,所述待取用工位至少包括水平设置在工作台上方且与调节传送段表面相平齐的上平台板、连接于上平台板与工作台表面之间的支撑柱以及安装在上平台板远离调节传送段一侧的挡块,挡杆延伸至上平台板表面并且与挡块相抵接。
19.通过采用上述技术方案,上平台板与调节传送段表面相平齐的设置,方便载具移动;拨料机构动作时,载具可沿挡杆移动至调节传送段上,直到与挡块接触;挡块和挡杆的设置,主要用于对载具进行导向和限位,避免载具移动的过程中发生偏移。
20.优选的,所述拨料机构包括水平设置在待取用工位远离待取用工位一侧且布置方向与调节传送段输送方向相垂直的拨料气缸、安装在拨料气缸的活塞杆自由端且竖直设置的端板以及固接于端板顶端且水平延伸至调节传送段上方的推板,拨料气缸固定于工作台上。
21.通过采用上述技术方案,初始状态下,推板位于调节传送段远离待取用工位一侧的边沿处,工作时,启动拨料气缸,使推板推动载具朝待取用工位上移动。
22.优选的,所述推板朝向待取用工位的一侧固接有推块,推块远离推板的一侧竖向开设有v形槽;
23.载具至少包括基板以及连接在基板上以供磁信号轮套装的立柱,基板的上表面插接固定有可嵌入v形槽内的定位杆。
24.通过采用上述技术方案,拨料气缸的活塞杆收缩的过程中,推块的v形槽卡接在定位杆上,并带动调节传送段上的载具沿挡杆朝待取用工位的方向移动,实现拨料。
25.优选的,所述挡料机构包括安装在固定传送段远离下料传送部一侧的承托件以及设置在承托件上且与推板配合以对载具进行限位的限位组件。
26.通过采用上述技术方案,限位组件能够在拨料机构的动作下对载具进行限位或非限位,以实现联动作业。
27.优选的,所述承托件为开口朝上的u形结构,承托件包括承接板、一体连接在承接板两侧的第一侧板和第二侧板,第一侧板固定在固定传送段的支架上;
28.限位组件包括至少两根固接在第一侧板和第二侧板之间且相互平行的导轴、滑动于导轴上的滑块、连接在第二侧板与滑块之间的压簧、固定在滑块远离承接板一侧且延伸至调节传送段上方的限位板以及固接在限位板一侧且延伸至固定传送段上方的限位块;初始状态下,推板在拨料气缸的带动下对限位板施加外力,使得压簧被压缩、限位块收回至固定传送段的一侧。
29.通过采用上述技术方案,初始状态下,推板在拨料气缸的带动下对限位板施加外力,使得压簧被压缩、滑块与第二侧板抵接、限位块收回至固定传送段的一侧;当拨料气缸的活塞杆收缩时,推板逐渐与限位板分离,分离的过程中,滑块在压簧的弹力作用下带动限位板复位,并使限位块由固定传送段一侧伸出至固定传送段的上方,此时,限位块对固定传送段上剩余的载具进行限位;当拨料气缸的活塞杆伸出时,推板带动限位板复位,使得限位
块收回至固定传送段的一侧,解除限位。
30.优选的,所述搬运工位包括位于调节传送段远离待取用工位一侧且固定在工作台上的固定架、安装在固定架上且沿调节传送段输送方向布置的无杆气缸、固接在无杆气缸的外部执行滑块上且朝向待取用工位一侧设置的联动板以及安装在联动板远离固定架一侧且竖直设置的升降气缸,升降气缸的活塞杆朝下布置,并且升降气缸的活塞杆的自由端连接有平行气爪,平行气爪的两爪臂上分别固接有夹取杆;
31.立柱的外壁上至少加工有一对沿自身轴向延伸以供夹取杆伸入直切削槽。
32.通过采用上述技术方案,搬运时,通过无杆气缸和升降气缸调整平行气爪的位置,平行气爪就位后,两爪臂上的夹取杆在升降气缸的控制下伸入条形块与磁信号轮的中心孔孔壁之间形成的空隙内,通过驱动两爪臂相背运动,使得夹取杆将磁信号轮从载具上取下并转移至充磁装置处进行充磁作业。
33.优选的,所述卸料机构包括安装在上平台板下方的工作台上且沿调节传送段的输送方向布置的卸料气缸,以及固接于卸料气缸的活塞杆上且竖直穿过上平台板的卸料板,上平台板对应卸料板穿过的位置开设有供卸料板滑动的导槽;
34.基板远离立柱的一侧开设有至少一端贯穿基板的条形槽,基板表面位于条形槽一侧的位置开设有与条形槽垂直连通的退板槽,退板槽远离条形槽的一端贯穿基板,卸料板完成卸料后通过退板槽与基板分离。
35.通过采用上述技术方案,拨料机构拨送载具的过程中,卸料板由条形槽的开口端伸入至条形槽内,载具就位后,卸料板位于条形槽和退板槽的交叉处;启动卸料气缸时,卸料气缸收缩并通过卸料板将载具拨送至下料传送部上,而卸料板则由退板槽脱离载具并复位。
36.综上所述,本技术包括以下至少一种有益技术效果:
37.1.本技术中的上料装置在作业时,通过上料传送部对满载的载具进行输送;通过拨料机构将满载的载具拨送至待取用工位上;通过挡料机构对上料传送部上其余的载具进行限位;通过搬运工位将载具上的磁信号轮逐个转移至充磁装置上进行充磁作业;通过卸料机构将空载的载具拨送至下料传送部上进行输送;整个过程采用自动化作业,相较于人工上料的方式,工作效率大大提高;
38.2.通过在调节传送段上设置挡杆,用于对载具进行限位和导向,以便拨料机构将满载的载具拨送至待取用工位上。
附图说明
39.图1是本技术实施例的上料装置的整体结构结构示意图;
40.图2是体现待取用工位、上料传送部、拨料机构、挡料机构之间位置关系的结构示意图;
41.图3是体现高度调整机构具体结构的示意图;
42.图4是体现拨料机构和挡料机构在初始状态下的配合关系以及待取用工位、拨料机构和卸料机构具体结构的示意图;
43.图5是体现磁信号轮具体结构的示意图;
44.图6是体现载具结构的示意图;
45.图7是体现条形槽和退板槽位置及连接关系的结构示意图;
46.图8是体现拨料机构动作后,挡料机构处于限位状态的结构示意图;
47.图9是凸显挡料机构位置的结构示意图;
48.图10是体现挡料机构具体结构的示意图;
49.图11是体现搬运工位与上料传送部和待取用工位之间位置关系的结构示意图;
50.图12是体现搬运工位具体结构的示意图;
51.图13是体现搬运工位对磁信号轮进行夹取的状态示意图。
52.附图标记说明:1、工作台;2、上料工位;21、机架;22、操作台;221、下操作板;222、上操作板;223、u形开口槽;23、上料传送部;231、固定传送段;232、调节传送段;233、挡杆;24、下料传送部;25、u形罩;26、载具;261、基板;262、盘托;263、立柱;264、直切削槽;265、减负孔;266、条形槽;2661、第一开口;267、退板槽;2671、第二开口;268、定位杆;27、托架;28、斜支撑;29、高度调整机构;291、支座;292、调整板;2921、腰型槽;293、底座;294、双向螺杆;295、立板;2951、第二斜面;296、定位螺栓;297、托板;298、支撑板;2981、第一斜面;299、螺栓紧固件;3、待取用工位;31、下平台板;32、上平台板;33、支撑柱;34、挡块;35、导槽;4、搬运工位;41、固定架;42、无杆气缸;43、联动板;44、升降气缸;45、平行气爪;46、夹取杆;5、磁信号轮;51、轮本体;52、中心孔;53、检测孔;54、异形孔;6、拨料机构;61、拨料气缸;62、端板;63、推板;64、推块;65、v形槽;7、挡料机构;71、承托件;711、承接板;712、第一侧板;713、第二侧板;714、安装板;72、限位组件;721、导轴;722、滑块;723、压簧;724、限位板;725、复位板;726、限位块;8、卸料机构;81、卸料气缸;82、卸料板。
具体实施方式
53.以下结合附图1
‑
13对本技术作进一步详细说明。
54.本技术实施例公开了一种磁信号轮充磁用上料装置。参照图1和图2,上料装置包括工作台1,工作台1的一侧设有上料工位2,工作台1的表面设有待取用工位3,待取用工位3的上方设有搬运工位4,搬运工位4固定于工作台1上;上料工位2主要用于对磁信号轮5进行批量输送;待取用工位3主要用于暂放小批量的磁信号轮5;搬运工位4主要用于将磁信号轮5逐个转移至充磁装置上进行充磁作业,整个过程采用自动化作业,相较于人工上料的方式,工作效率更高。
55.上料工位2包括机架21、水平固定于机架21一侧的操作台22、安装在机架21上且一端背离操作台22延伸至工作台1上方的上料传送部23和下料传送部24、罩设在上料传送部23和下料传送部24外侧的u形罩25以及用于小批量携带磁信号轮5的载具26;上料传送部23和下料传送部24并排设置且两者均由机架21朝工作台1的方向斜向上延伸,待取用工位3位于上料传送部23末端的一侧并且与下料传送部24的始端衔接;上料传送部23主要用于对满载的载具26进行输送;下料传送部24主要用于对空载的载具26进行输送,以便载具26能够循环使用。
56.工作台1上设有拨料机构6,用于将输送至上料传送部23末端的载具26拨送至待取用工位3上。上料传送部23上安装有与拨料机构6联动作业的挡料机构7,当拨料机构6将位于最前端的满载的载具26拨送至待取用工位3上时,挡料机构7对上料传送部23上其余的满载的载具26进行限位。
57.参照图1,机架21上位于操作台22下方的位置固接有托架27,托架27包括由三根支杆连接而成的u形架,u形架的两自由端垂直固接在机架21一侧,使得u形架所形成的面为平面,为提高u形架的承载能力,在机架21与u形架之间加设斜支撑28。
58.操作台22包括叠放设置的下操作板221和上操作板222,两者通过螺栓固定在u形架上,上操作板222开设有u形开口槽223,u形开口槽223的开口对应于上料传送部23的始端和下料传送部24的末端,空载的载具26可在下料传送部24的输送下滑动至下操作板221上,并暂留在u形开口槽223内,以便工作人员回收。
59.参照图2和图3,上料传送部23为皮带式输送机,皮带式输送机包括固定传送段231以及铰接于固定传送段231末端的调节传送段232,调节传送段232的表面与待取用工位3的表面相平齐。调节传送段232的末端水平设置有与自身输送方向相垂直的挡杆233,挡杆233固定于调节传送段232的支架上,用于对输送至调节传送段232上的满载的载具26进行限位。此处需要说明的是,调节传送段232和待取用工位3上每次只能容纳一个载具26。
60.参照图3,调节传送段232的正下方设有高度调整机构29,用于调整调节传送段232的角度,以便调节传送段232的表面与待取用工位3的表面相平齐。高度调整机构29包括固定在工作台1上表面的支座291,支座291可为块状,支座291的上表面放置有调整板292,调整板292的尺寸大于支座291。调整板292远离支座291一侧的中心处固接有块状的底座293,底座293上通过轴承转动连接有一根双向螺杆294,双向螺杆294的长度方向与调节传送段232的输送方向相垂直。以底座293为中心,双向螺杆294两侧的杆体上加工有反向螺纹,双向螺杆294两侧加工有反向螺纹的杆体上分别螺纹连接有竖直设置的立板295,立板295的下表面抵接于调整板292上,转动双向螺杆294时,两立板295可相对或相背运动。
61.参照图3,为了避免调节的过程中立板295从双向螺杆294的端部脱落,在每块立板295靠近调整板292的一侧至少设有两根定位螺栓296,调整板292对应定位螺栓296的板面上分别开设与定位螺栓296一一对应的腰型槽2921,腰型槽2921沿双向螺杆294的轴向延伸,定位螺栓296的杆体穿过腰型槽2921并且与立板295螺纹连接,定位螺栓296的端帽抵接于调整板292远离立板295的一侧。
62.调节传送段232正下方位于两立板295之间的位置设有水平的托板297,托板297的两侧分别一体连接有与调节传送段232的支架相连接的支撑板298,立板295抵接在支撑板298上,在托板297和两支撑板298之间开设有沿两者厚度方向贯穿的镂空槽,用于减轻重量。在支撑板298相对立板295的一侧加工有第一斜面2981,第一斜面2981沿双向螺杆294的轴向朝调节传送段232外侧斜向上延伸,在立板295相对支撑板298的一侧加工有与第一斜面2981相贴合的第二斜面2951。
63.参照图3,当驱动双向螺杆294带动两立板295相对运动时,第二斜面2951沿第一斜面2981朝靠近托板297的方向移动,使托板297带动调节传送段232上升;当驱动双向螺杆294带动两立板295相背运动时,第二斜面2951沿第一斜面2981朝远离托板297的方向移动,使托板297带动调节传送段232下降。
64.在托板297与调整板292之间设有螺栓紧固件299,当调节传送段232的角度调整完毕后,可通过螺栓紧固件299进行加固,从而提高调整后的稳定性。
65.参照图4,拨料机构6包括水平设置在待取用工位3远离上料传送部23一侧且固定于工作台1上的拨料气缸61,拨料气缸61的布置方向与调节传送段232的输送方向相垂直,
拨料气缸61的活塞杆的自由端固接有竖直设置的端板62,端板62的高度高于挡杆233的高度,端板62的顶端固接有水平延伸至调节传送段232上方的推板63,推板63朝向待取用工位3的一侧固接有推块64,推块64远离推板63的一侧竖向开设有v形槽65。初始状态下,拨料气缸61的活塞杆处于伸出状态,推块64位于调节传送段232远离待取用工位3一侧的边沿处。
66.参照图5,需要说明的是,磁信号轮5包括轮本体51,轮本体51的圆周面为充磁面,充磁面上充有多个间隔设置的强磁段和弱磁段。轮本体51的中心处开设有中心孔52,轮本体51上环绕中心孔52的位置开设有多个呈圆周等距分布的检测孔53,其中一相邻的两检测孔53之间开设有异形孔54。
67.参照图5和图6,载具26包括基板261、安装在基板261上表面的盘托262以及固定在盘托262远离基板261一侧且竖直设置的立柱263,立柱263的外壁上加工有沿自身轴向延伸且呈圆周等距分布的四个直切削槽264,磁信号轮5依次套放于立柱263上。
68.参照图6和图7,基板261上开设有四个减负孔265,用于减小载具26的重量。基板261远离立柱263的一侧开设有一对相互平行的条形槽266,两条形槽266以立柱263所在的竖直面为中心轴对称设置且靠近基板261的边沿,条形槽266沿拨料气缸61的收缩方向延伸且至少延伸端由基板261的侧面贯穿,形成第一开口2661;基板261上还开设有分别与两条形槽266垂直连通的退板槽267,退板槽267与条形槽266之间呈l形,且退板槽267由基板261靠近边沿的侧面贯穿而出,形成第二开口2671。
69.参照图1和图6,基板261的上表面插接固定有定位杆268,定位杆268位于基板261上远离第一开口2661的一侧,将载具26放置在上料传送部23上进行输送时,需要将条形槽266的第一开口2661朝向下料传送部24的一侧布置。
70.参照图6和图8,拨料气缸61的活塞杆收缩时,推块64的v形槽65卡接在定位杆268上,从而带动调节传送段232上的载具26沿挡杆233朝待取用工位3的方向移动。
71.参照图9和图10,挡料机构7包括安装在固定传送段231远离待取用工位3一侧的承托件71以及滑动设置在承托件71上的限位组件72;承托件71为开口朝上的u形结构,具体包括承接板711、一体连接在承接板711两侧的第一侧板712和第二侧板713,承接板711远离第一侧板712一侧的板面上固接有安装板714,安装板714和第一侧板712远离第二侧板713的表面平齐,承托件71通过螺栓穿过安装板714以固定在固定传送段231的支架上。
72.限位组件72包括至少两根固接在第一侧板712和第二侧板713之间且相互平行的导轴721、通过直线轴承滑动于导轴721上的滑块722、设置在第二侧板713与滑块722之间的压簧723以及固定在滑块722远离承接板711一侧的限位板724;第二侧板713和滑块722相对的一侧均开设有容纳槽,压簧723的两端分别插接固定至两容纳槽内;限位板724朝调节传送段232的一侧延伸,在限位板724的延伸端设有复位板725,复位板725包括一体成型的倾斜段和水平段,复位板725的倾斜段通过螺栓固定在限位板724上,限位板724朝向固定传送段231的一侧固接有限位块726。
73.参照图6和图9,压簧723处于自然状态时,滑块722抵接在第一侧板712上,限位块726探出至固定传送段231的传送带的上方并通过限制定位杆268以对载具26进行拦截。
74.参照图4和图10,初始状态时,推板63在拨料气缸61的带动下对复位板725的水平段施加外力,使得压簧723收缩、滑块722与第二侧板713抵接、限位块726随限位板724收回至固定传送段231的外侧,此时,限位组件72为非限位状态。
75.参照图8和图10,当拨料机构6启动时,拨料气缸61的活塞杆收缩,使推板63逐渐与复位板725的水平段分离,分离的过程中,滑块722在压簧723的弹力作用下带动限位板724复位,并使限位块726由固定传送段231一侧伸出至固定传送段231的上方,此时,限位组件72为限位状态;参照图7和图8,随着拨料气缸61的活塞杆的继续收缩,推块64将调节传送段232上的载具26拨送至待取用工位3上。
76.参照图1和图8,待取用工位3包括水平固定于工作台1上方的下平台板31、位于下平台板31正上方的上平台板32、连接于下平台板31与上平台板32之间的支撑柱33以及安装在上平台板32远离调节传送段232一侧的挡块34,上平台板32的表面与调节传送段232的表面相平齐,以便载具26能够被顺利拨送至待取用工位3上。上述的位于调节传送段232末端的挡杆233延伸至上平台板32表面并且与挡块34相抵接,用于对载具26进行限位和导向,以便载具26能够准确就位。
77.参照图11和图12,搬运工位4包括位于调节传送段232远离待取用工位3一侧且固定在工作台1上的固定架41,固定架41上安装有沿调节传送段232输送方向布置的无杆气缸42,根据实际需要,无杆气缸42可选用磁偶无杆气缸或机械式无杆气缸,无杆气缸42的外部执行滑块722朝向待取用工位3的一侧固接有联动板43,联动板43远离固定架41的一侧安装有竖直设置的升降气缸44,参照图13,升降气缸44的活塞杆朝下布置并且活塞杆的自由端通过气缸浮动接头连接有平行气爪45,平行气爪45的两爪臂上固接有竖直延伸的夹取杆46。为保证搬运工位4运行过程中的稳定性,可在平行气爪45和联动板43之间以及联动板43和固定架41之间设置直线导轨,用于导向。
78.参照图12和图13,工作时,通过无杆气缸42和升降气缸44调整平行气爪45的位置,平行气爪45就位后,通过驱动两爪臂相背运动,使得夹取杆46将磁信号轮5取下并转移至充磁装置处进行充磁作业。
79.参照图8和图11,待取用工位3上设有卸料机构8,用于将空载的载具26从上平台板32表面拨送至下料传送部24上;下料传送部24为滚筒式输送机,当空载的载具26被拨送至下料传送部24上时,载具26可在自身重力的作用下沿下料传送部24滑动。
80.卸料机构8包括固定于下平台板31上表面的卸料气缸81,卸料气缸81的布置方向与调节传送段232的输送方向一致,且卸料气缸81的活塞杆朝向拨料气缸61,卸料气缸81的活塞杆的自由端固接有竖直向上延伸的卸料板82,卸料板82的顶端穿过上平台板32并且位于上平台板32的上方,上平台板32对应卸料板82的位置开设有导槽35,导槽35的开设方向与卸料气缸81的活塞杆的活动方向一致。
81.参照图7和图8,初始状态下,卸料气缸81的活塞杆为伸出状态,卸料板82位于导槽35靠近拨料气缸61的一端,拨料机构6沿挡杆233拨送载具26的过程中,卸料板82由条形槽266的第一开口2661伸入至条形槽266内,当载具26完全被拨送至待取用工位3上时,卸料板82正对退板槽267的第二开口2671;启动卸料气缸81时,卸料气缸81收缩并通过卸料板82将载具26拨送至下料传送部24上,参照图8和图11,卸料板82则由退板槽267的第二开口2671与载具26分离。
82.本技术实施例的实施原理为:工作人员依次将多个满载的载具26放置在固定传送部上进行输送,放置时,保证条形槽266的第一开口2661朝向下料传送部24的一侧;当位于最前端的满载的载具26被输送至调节传送段232上时,拨料机构6启动并且挡料机构7与拨
料机构6联动,具体进行以下两步连续的动作:
83.动作一:拨料气缸61的活塞杆收缩,带动推板63逐渐与复位板725的水平段分离,分离的过程中,滑块722在压簧723的弹力作用下带动限位板724复位,复位的过程中,限位块726由固定传送段231一侧伸出至固定传送段231的传送带的上方,对固定传送段231上其余的满载的载具26进行限位;
84.动作二:拨料气缸61的活塞杆收缩过程中,推块64逐渐朝载具26的方向移动,当v形槽65卡接在定位杆268上时,推块64带动调节传送段232上的载具26朝待取用工位3上移动,当载具26被完全拨送至待取用工位3上时,拨料气缸61停止动作;
85.完成上述两步动作后,搬运工位4启动,即通过无杆气缸42和升降气缸44调整平行气爪45的位置,平行气爪45就位后,两爪臂上的夹取杆46伸入磁信号轮5的中心孔52孔壁与立柱263之间的空隙内,通过驱动两爪臂相背运动,使得夹取杆46将磁信号轮5从载具26上取下并转移至充磁装置处进行充磁作业;当载具26上的最后一个磁信号轮5被夹取后,拨料气缸61伸出,并通过推板63带动限位组件72恢复初始状态,与此同时,卸料机构8启动,即卸料气缸81的活塞杆收缩,使卸料板82将空载的载具26拨送至下料传送部24上,而空载的载具26则在自身重力的作用下朝操作台22运动,循环往复。
86.以上均为本技术的较佳实施例,并非依此限制本技术的保护范围,故:凡依本技术的结构、形状、原理所做的等效变化,均应涵盖于本技术的保护范围之内。