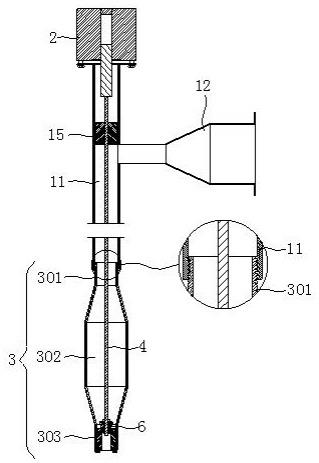
1.本实用新型涉及灌装设备结构领域,特别是指一种防带颗粒的液体或膏体堵料的灌装头。
背景技术:2.在包装机领域中,灌装结构的立式全自动包装机常用于液体或膏体等物料的自动灌装和包装。其中灌装结构通常是由进料气缸、送料管道、进料活塞、单向阀和灌装筒组成,气缸带动活塞在送料管道来回运动、通过单向阀开关来完成物料从灌装筒底部的出料孔输出的工作。在完成一次灌装出料工序后灌装筒的出料孔必须要有堵塞结构,才可避免液体或膏体向外渗漏。
3.如附图1所示,目前灌装结构的立式全自动包装机中普遍使用的防渗漏结构大多是在灌装筒11内连接一连杆13,该连杆13的下端连接一个堵漏头14,并且在灌装筒11的上端连接带动连杆13移动的动力单元,例如气缸2,当气缸2的活塞杆收缩时带动连杆13移动,使堵漏头14从灌装筒11底部出料孔向上移动,气缸2的活塞杆伸出时带动连杆13移动,使堵漏头14堵住灌装筒11底部出料孔(附图未示)。
4.此类结构中,堵漏头14在灌装筒11内移动,必然占据液体或膏体在灌装筒11内的流动空间,将极大的影响液体或膏体的流动,尤其对于带有颗粒的液体或者膏体而言,十分容易导致灌装筒11内部堵塞。并且堵塞后需要拆下灌装筒11清理,具体需要将气缸2拆卸,再抽出连杆13和堵漏头14,以及将灌装筒11和送料管道12分离,才可对灌装筒11进行清理。由此可见,现有技术中的灌装结构清理十分的麻烦。
技术实现要素:5.针对上述背景技术提出的不足,本实用新型提供一种防带颗粒的液体或膏体堵料的灌装头,以克服现有的问题。
6.本实用新型采用如下技术方案:
7.一种防带颗粒的液体或膏体堵料的灌装头,其特征在于,该灌装头包括灌装头本体、密封圈、堵头和拉杆;其中,
8.所述灌装头本体的两端分别为连接管和出料管,灌装头本体的中间为扩径管,所述连接管和所述出料管的截面内尺寸均小于所述扩径管的截面内尺寸,且所述连接管和所述出料管均和所述扩径管连通,使所述灌装头本体的两端贯穿,所述连接管可拆卸的连接至灌装筒;
9.所述密封圈具有贯穿的出料孔,且所述密封圈固定至所述出料管内;
10.所述拉杆的一端穿过所述灌装筒至位于所述灌装头本体内;
11.所述堵头为两端直径一大一小的锥形结构,且所述堵头固定至所述拉杆在所述灌装头本体内的一端,使所述堵头直径较小的一端朝向所述出料管;
12.当所述拉杆移动带动堵头移动压向所述出料管时,所述堵头将所述出料管堵住;
当所述拉杆移动带动堵头移动至所述扩径管内时,所述出料管敞开。
13.作为进一步的改进,所述拉杆位于所述灌装头本体内的一端设有一段外螺纹,该外螺纹适配连接限位螺母,且拉杆在靠近端部位置的两侧均设有卡槽,该卡槽适配连接卡接件,所述卡接件中间具有嵌入槽,且卡接件在所述嵌入槽的两侧为弹性部;所述堵头穿套在所述外螺纹外,使所述堵头直径较大的一端抵接在所述限位螺母,所述卡接件的所述嵌入槽套嵌套在所述外螺纹外,且两所述弹性部分别卡紧在两所述卡槽内,使所述卡接件抵在所述堵头直径较小的一端。
14.作为进一步的改进,所述拉杆位于所述灌装头本体内的一端设有一段外螺纹,该外螺纹适配连接限位螺母,且拉杆在靠近端部位置的两侧均设有卡槽,该卡槽适配连接卡接件,所述卡接件中间具有嵌入槽,且卡接件在所述嵌入槽的两侧为弹性部;所述堵头穿套在所述外螺纹外,使所述堵头直径较大的一端抵接在所述限位螺母,所述卡接件的所述嵌入槽套嵌套在所述外螺纹外,且两所述弹性部分别卡紧在两所述卡槽内,使所述卡接件抵在所述堵头直径较小的一端。
15.作为进一步的改进,所述卡接件的两所述弹性部一端连接弧形的连接部,两所述弹性部的另一端均向所述嵌入槽的中间弯折形成限位部,所述嵌入槽套嵌套在所述外螺纹外之后,所述外螺纹位于所述连接部和所述限位部之间。
16.作为进一步的改进,所述卡接件还连接限位件,所述限位件的两端初始状态均为弯折90
°
的弯折杆,两所述弯折杆分别穿过两所述限位部的所述限位孔之后,弯折至所述卡接件的表面。
17.作为进一步的改进,所述连接管螺旋连接的嵌入所述灌装筒内,使所述灌装头本体固定在所述灌装筒的底部,并且可拆卸。
18.由上述对本实用新型结构的描述可知,和现有技术相比,本实用新型具有如下优点:本实用新型的结构中,所述堵头堵住所述出料管内的所述出料孔可避免在暂停灌装时液体或膏体渗漏的现象。所述扩径管的结构相当于扩大所述堵头在所述灌装头本体内移动范围的空间,即扩大了所述扩径管的内壁和所述堵头之间的间隙,使所述堵头移动至所述扩径管内后,带有颗粒的液体或膏体即可顺畅地经由所述扩径管内壁和所述堵头之间的间隙向下流动,并从所述出料孔流出以完成灌装,从而避免堵料的现象。另外,若需要清理所述堵头及其周边位置时,将所述灌装头本体从所述灌装筒下端取下,即可对所述灌装头本体和所述堵头进行清理,十分方便。
附图说明
19.图1为现有技术中的结构灌装管的结构示意图。
20.图2为安装本实用新型的灌装筒的立体结构示意图。
21.图3为安装本实用新型的灌装筒的剖面结构示意图。
22.图4为本实用新型中,堵头上升至离开出料孔后的剖面结构示意图。
23.图5为拉杆连接堵头的立体结构示意图。
24.图6为拉杆连接堵头的剖面结构示意图。
25.图7为拉杆连接堵头一端的正面结构示意图。
26.图8为卡接件连接限位件的立体结构示意图。
27.图9为应用本实用新型的立式全自动包装机的正面结构示意图。
28.图10为灌装头本体设置在成型模具下的结构示意图。
具体实施方式
29.下面参照附图说明本实用新型的具体实施方式。
30.如附图2和3所示,一种防带颗粒的液体或膏体堵料的灌装头包括灌装头本体3、密封圈5、堵头6和拉杆4。其中,所述灌装头本体3用于连接至灌装筒11的输出端,所述灌装筒2即为输出液体或膏体的流道。
31.再参照附图3和4所示,所述拉杆4的一端穿过所述灌装筒11至位于所述灌装头本体3内,且所述拉杆4在所述灌装头本体3内的一端固定连接所述堵头6。所述拉杆4的另一端连接至一气缸2的活塞杆21,该气缸2固定至所述灌装筒11的上端,且该气缸2的活塞杆21伸入所述灌装筒11内。进一步地,该气缸2可由立式全自动包装机的控制系统进行控制,通过气缸2的活塞杆21伸缩可带动所述拉杆4移动,从而实现所述拉杆4带动所述堵头6在所述灌装头本体3内移动。
32.优选的,继续参照附图3,所述灌装筒11靠近所述气缸2的一端内可固定密封套15,所述密封套15为油封等位移密封圈的结构。所述拉杆4穿过该密封套15,所述密封套15的结构用于防止液体或膏体向上从所述气缸2一端流出。所述灌装筒11可从一侧通过送料管道2连接至立式全自动包装机(附图未示)的出料口,使液体或膏体从送料管道2输入至所述灌装筒11内,并向下流向所述灌装头本体3内。
33.继续参照附图3,所述灌装头本体3的两端分别为连接管301和出料管303,灌装头本体3的中间为扩径管302,所述连接管301和所述出料管303均和所述扩径管302连通,使所述灌装头本体3的两端贯穿。所述连接管301用于连接至所述灌装筒11,并且所述连接管301的内径大于所述堵头6的外径,使所述堵头6可从所述连接管301穿入所述灌装头本体3内。所述堵头6为两端直径一大一小的锥形结构,所述堵头6固定至所述拉杆4之后,所述堵头6直径较小的一端朝向所述出料管303。
34.所述连接管301和所述灌装筒11可以是通过设置螺纹的方式连接,具体可以是附图3中所示的所述连接管301螺旋的套入所述灌装筒11内实现固定,使液体或膏体可经由所述灌装筒11再从所述连接管301注入所述灌装头本体3内,同时此设置螺纹连接的结构还可使所述灌装头本体3实现可拆卸,方便对所述灌装头本体3内部和所述堵头6进行清理。
35.继续参照附图3和4,所述出料管303用于使流入所述灌装头本体3内的液体或膏体排出,并且所述出料管303和所述连接管301的截面内尺寸均小于所述扩径管302的截面内尺寸。也即,所述连接管301和所述出料管303的内径均小于所述扩径管302的内径。此所述扩径管302的结构相当于扩大所述堵头6在所述灌装头本体3内移动范围的空间,即扩大了所述扩径管302的内壁和所述堵头6之间的间隙,使带有颗粒的液体或膏体均可顺畅地经由所述扩径管302内壁和所述堵头6之间的间隙向下流动,完成灌装,有效的避免了堵料的现象,由此可见本实用新型亦可适用于颗粒等物料的灌装。
36.继续参照附图4,所述密封圈5固定至所述出料管303内,并且所述密封圈5的中心具有贯穿的出料孔501,该出料孔501用于使液体或膏体流出。当所述拉杆4移动带动堵头6移动压向所述出料管303时,所述堵头6直径较小的一端嵌入至所述密封圈5的所述出料孔
501内,以实现将所述出料管303完全堵住,从而使液体或膏体无法从所述出料管303流出;当所述拉杆4移动带动堵头6移动至所述扩径管302内时,所述出料管303敞开,以使液体可从所述出料孔501流出。另外,所述密封圈5和所述堵头6的均可以橡胶材质,通过此材质的弹性使所述堵头6移动至将所述出料孔501堵住后,可实现完全所述出料管303的密封。
37.优选的,所述出料管303的管口边缘向中心弯折形成阻挡部304,此所述阻挡部304的结构用于挡住所述密封圈5,同时可起到一定的密封作用。进一步的,所述密封圈5的外侧壁可嵌入并固定若干密封环51,以实现所述密封圈5和所述出料管303之间的间隙密封。安装所述密封圈5时,将所述密封圈5从所述连接管301嵌入至所述灌装头本体3内,再通过所述拉杆4或其他杆状物体将所述密封圈5推入所述出料管303内,实现所述密封圈5的装配固定。
38.如附图5和6所示,所述堵头6通过限位螺母7和卡接件8固定至所述拉杆4的一端。具体的,再参照附图7,所述拉杆4位于所述灌装头本体3内的一端设有一段外螺纹401,该外螺纹401适配连接所述限位螺母7,所述外螺纹401在靠近所述拉杆4端部位置的两侧均设有卡槽402,该卡槽402适配连接所述卡接件8。再参照附图8,所述卡接件8可以是金属冲压形成的钣金件,卡接件8的结构为,卡接件8的中间具有嵌入槽801,卡接件8在所述嵌入槽801的两侧为弹性部803,两所述弹性部803的一端均向所述嵌入槽801的中间弯折形成限位部805,两所述弹性部803的另一端连接弧形的连接部804,通过该连接部804的连接可使两所述弹性部803在向外弯折后具有向中间恢复的弹性。
39.继续参照附图5和6,装配所述堵头6时,先将所述限位螺母7连接至所述外螺纹401,且螺旋连接至所述外螺纹401的根部,使所述限位螺母7紧固在所述拉杆4上;之后将所述堵头6穿套在所述外螺纹401外,使所述堵头6直径较大的一端抵接在所述限位螺母7;最后将所述卡接件8的两所述弹性部803向外撑开,再将所述嵌入槽701套嵌套在所述外螺纹401外,松开两所述弹性部803,使两所述弹性部803的一部分分别卡紧在两所述卡槽402内,所述外螺纹401位于所述连接部804和所述限位部805之间,同时使所述卡接件8抵在所述堵头6直径较小的一端,至此即可完成所述堵头6的固定。此固定结构中所述卡槽402可限制所述卡接件8,避免所述卡接件8向下掉落,并且所述连接部804和所述限位部805可与所述拉杆4形成相互限制,避免卡接件8移动,最终使所述卡接件8可挡住所述堵头6,避免所述堵头6向下掉落。
40.此外,两所述弹性部803均设有限位孔802,所述限位孔802可方便利用钩子钩住,以将所述弹性部803向外拉,使两所述弹性部803向外撑开。所述卡接件8还可连接限位件9,所述限位件9的两端初始状态均为弯折90
°
的弯折杆901。所述嵌入槽801套嵌套在所述外螺纹401外之后,由于所述堵头6具有为橡胶具有柔韧性,因此可将所述限位件9推入所述堵头6和所述卡接件8之间,再将限位件9的两所述弯折杆901分别穿过两所述限位部805的所述限位孔802,之后将所述弯折杆901弯折至如附图8所示的贴近所述卡接件8的表面,通过此所述限位件9的连接即可将所述弹性部803锁住,避免两所述弹性部803在其他外力的作用下向外撑开,使所述卡接件8不会掉落,即保证所述堵头6始终固定在所述拉杆4的端部。
41.如附图9和10所示,本实用新型的结构可设置在立式立式全自动包装机1中用于包装膜10成型的成型模具16内,其中所述灌装筒11固定在成型模具16内,使所述灌装头本体3位于成型模具16的下端,且所述连接管301位于所述成型模具16内,所述扩径管302和出料
管303延伸出成型模具16下。工作时,立式立式全自动包装机1将包装膜10自上而下的输送,包装膜10的经过成型模具16,并且包装膜10的侧边及底部完成热封成型后,可通过控制所述气缸2的活塞杆21上升,使所述拉杆4带动所述堵头6上升至所述扩径管302内,从而使所述密封圈5的所述出料孔501敞开,以使液体或膏体可从所述出料孔501向下流出;之后控制所述气缸2的活塞杆21下降,使所述拉杆4带动所述堵头6下降至将所述出料孔501堵住,此时即可完成一个包装袋101的液体或膏体的灌装。由此可见,此采用本实用新型的灌装方式可便于实现定量灌装,同时可有效的避免液体或膏体渗漏的现象。另外,所述连接管301和出料管303直径小于所述扩径管302的结构中,所述连接管301连接在所述成型模具16内,有利于缩小成型模具16的尺寸,以减小包装袋101的成型尺寸,所述出料管303向下伸出所述成型模具16的下端,使本实用新型可对接灌装袋口较为狭小的包装袋101,由此可见采用本实用新型的结构灌装时,可将包装袋101设计得更小,有利于节省包装膜10,即,可节省包装耗材。
42.综上所述,本实用新型的结构应用于立式全自动包装机1后,所述堵头6堵住所述出料管303内的所述出料孔501可避免在暂停灌装时(例如在包装袋101成型时)液体或膏体渗漏。所述扩径管302的结构相当于扩大了所述扩径管302的内壁和所述堵头6之间的间隙,使所述堵头6移动至所述扩径管302内后,带有颗粒的液体或膏体均可顺畅地经由所述扩径管302和所述堵头6之间的间隙向下流动,并从所述出料孔501流出以完成灌装。另外,在长时间使用后,若需要清理所述堵头6及其周边的位置,或者需要更换所述堵头6和所述密封圈5时,只需将所述灌装头本体3从所述灌装筒11下端取下,即可对所述灌装头本体3和所述堵头6进行清理,或者将所述堵头6和所述密封圈5取下更换,均十分的方便。
43.上述仅为本实用新型的具体实施方式,但本实用新型的设计构思并不局限于此,凡利用此构思对本实用新型进行非实质性的改动,均应属于侵犯本实用新型保护范围的行为。