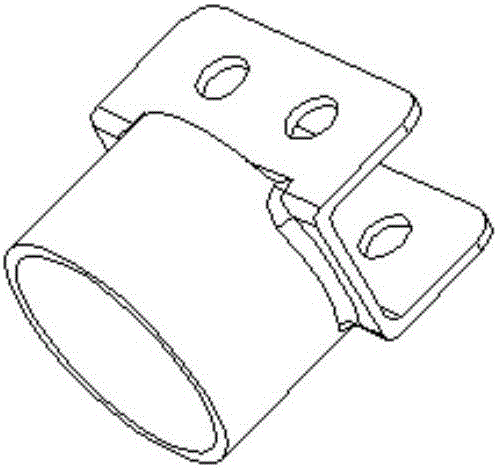
本发明涉及航天工程技术,具体地,涉及一种复合材料柔性铰链及其制造方法。
背景技术:
由于运载火箭载荷舱的有效空间及运载能力的限制,大型天线、太阳能电池帆板等都是以折叠压缩状送入太空,然后展开成所需要的几何构形。因此,可展结构是空间飞行器的重要组成部分,直接关系到空间飞行器的运行性能以及飞行任务的成败。此外,考虑到可展结构具有可重复利用性、便于运输和储存、施工周期短等特点,因此在航天领域得到了广泛应用。
铰链是可展结构的重要组成部分。传统的机械式典型铰链一般主要由公铰链、母铰链、关节轴承、平面蜗卷弹簧、展开指示器、锁定机构等组成,存在结构复杂、间隙控制难度大、重量高等缺点,以及摩擦、磨损及润滑等复杂问题。柔性铰链是一种利用其自身弹性变形来实现展开功能的新型铰链机构。与传统刚性铰链机构相比,柔性铰链具有重量轻、结构复杂度低、展开可靠度高、易于安装和维护等优点,可广泛应用于伸展臂、太阳能电池帆板、可展天线等各种空间可展航天结构中。
目前,我国进入可展结构研究领域的时间相对较晚,技术不够成熟。对于柔性铰链机构,有学者提出一种类似钢卷尺构型的卷尺弹簧及其组合铰链结构,整个结构采用金属材料;也有学者提出利用电加热实现展开功能的形状记忆复合材料可展开铰链,其展开装置需配备电加热装置。
技术实现要素:
针对现有技术中的缺陷,本发明的目的是提供一种复合材料柔性铰链及其制造方法。
根据本发明提供的复合材料柔性铰链,包括复合材料接头和复合材料管状柔性单元;
所述复合材料管状柔性单元的两端装配有所述复合材料接头。
优选地,所述复合材料接头、所述复合材料管状柔性单元采用碳纤维增强复合材料制成;
所述复合材料接头采用模压成型工艺成型;
所述复合材料管状柔性单元采用卷管成型工艺成型。
优选地,所述复合材料管状柔性单元的壁厚为0.12~0.48mm。
优选地,所述复合材料管状柔性单元设置有相对的U形通孔。
优选地,所述复合材料接头包括相连的空心圆柱段和平行翻边段;
所述平行翻边段上设置有连接孔。
优选地,所述复合材料接头的空心圆柱段外表面与所述复合材料管状柔性单元内表面通过胶粘剂胶接装配。
本发明提供的复合材料柔性铰链的制造方法,包括如下步骤:
步骤S1:裁剪复合材料接头和复合材料管状柔性单元铺层所用的碳纤维预浸料;
步骤S2:对复合材料接头进行铺层;
步骤S3:对铺层的复合材料接头进行固化;
步骤S4:将固化后的复合材料接头毛坯件脱模,打磨棱角、毛边、溢胶,并根据目标尺寸进行机加工后获得复合材料接头;
步骤S5:对复合材料管状柔性单元进行铺层,具体为,铺层时,利用卷管机依次旋转铺层,每层搭接且拼缝错开,对铺层进行压实形成管件;
步骤S6:利用卷管机在所述管件外部缠绕热缩带并进行固化;
步骤S7:将固化的管件脱模,并按目标尺寸机加工出相对的U形通孔后获得复合材料管状柔性单元;
步骤S8:将复合材料接头与复合材料管状柔性单元胶接装配成一体。
优选地,所述步骤S2具体为:
铺层时,先分别铺空心圆柱段和平行翻边段;
然后对空心圆柱段和平行翻边段整体连续铺层;
在空心圆柱段和平行翻边段最外侧铺上碳布。
优选地,在步骤S2中,所述复合材料接头铺层时,铺层至总铺层数的一半时需预压30min~40min,在铺层最外两层之前,进行合模预压,压力小于成型压力的50%。
优选地,在步骤S5中,所述复合材料管状柔性单元铺层完成后,采用碳纤维预浸料在复合材料管状柔性单元一端缠绕形成梯度增厚的加强段。
与现有技术相比,本发明具有如下的有益效果:
1、本发明采用轻质高强的碳纤维增强复合材料制造柔性铰链,减重效果明显;
2、本发明集动力与锁定功能于一身,具有提供动力及自动锁定功能,不需要额外设置加热或锁定等装置,结构复杂度低,展开可靠度高、易于安装和维护。
3、本发明所提供的复合材料柔性铰链的制造方法工艺简单、技术成熟、制造周期短、生产成本低。
附图说明
通过阅读参照以下附图对非限制性实施例所作的详细描述,本发明的其它特征、目的和优点将会变得更明显:
图1为本发明中复合材料柔性铰链的结构示意图;
图2为本发明中复合材料接头的结构示意图;
图3为本发明中复合材料管状柔性单元的结构示意图。
图中:
1为复合材料接头;2为复合材料管状柔性单元。
具体实施方式
下面结合具体实施例对本发明进行详细说明。以下实施例将有助于本领域的技术人员进一步理解本发明,但不以任何形式限制本发明。应当指出的是,对本领域的普通技术人员来说,在不脱离本发明构思的前提下,还可以做出若干变形和改进。这些都属于本发明的保护范围。
在本实施例中,本发明提供的复合材料柔性铰链,包括复合材料接头和复合材料管状柔性单元;
所述复合材料管状柔性单元的两端装配有所述复合材料接头。
所述复合材料接头、所述复合材料管状柔性单元采用碳纤维增强复合材料制成;
所述复合材料接头采用模压成型工艺成型;
所述复合材料管状柔性单元采用卷管成型工艺成型。
所述复合材料管状柔性单元的壁厚为0.12~0.48mm。
所述复合材料管状柔性单元设置有相对的U形通孔。
所述复合材料接头包括相连的空心圆柱段和平行翻边段;
所述平行翻边段上设置有连接孔。
所述复合材料接头的空心圆柱段外表面与所述复合材料管状柔性单元内表面通过胶粘剂胶接装配。
本发明提供的复合材料柔性铰链的制造方法,包括如下步骤:
步骤S1:裁剪复合材料接头和复合材料管状柔性单元铺层所用的T800碳纤维预浸料和复合材料管状柔性单元铺层所用单层厚度为0.03mm的T300超薄碳纤维预浸料。
步骤S2:对复合材料接头进行铺层;
步骤S3:对铺层的复合材料接头按相应预浸料的固化制度固化;
步骤S4:将固化后的复合材料接头毛坯件脱模,打磨棱角、毛边、溢胶,并根据目标尺寸进行机加工后获得复合材料接头;
步骤S5:对复合材料管状柔性单元进行铺层,铺层时,利用卷管机依次旋转铺层,每层略微搭接且拼缝错开,对铺层进行压实形成管件;
步骤S6:利用卷管机在所述管件外部缠绕热缩带并按相应预浸料的固化制度固化;
步骤S7:将固化的管件脱模,并按目标尺寸机加工出相对的U形通孔后获得复合材料管状柔性单元;
步骤S8:将复合材料接头与复合材料管状柔性单元胶接装配成一体。胶粘剂固化后,经过表面清理,即可获得复合材料柔性铰链。
所述步骤S2具体为:
铺层时,先分别铺空心圆柱段和平行翻边段;
然后对空心圆柱段和平行翻边段整体连续铺层;
在空心圆柱段和平行翻边段最外侧铺上1层T300碳布,碳布裁剪区域尽量避开棱边。
在步骤S2中,所述复合材料接头铺层时,铺层至总铺层数的一半时需预压30min~40min,在铺层最外两层之前,模并上压机合模预压,压力小于成型压力的50%。
在步骤S5中,所述复合材料管状柔性单元铺层完成后,采用T800碳纤维预浸料在复合材料管状柔性单元一端缠绕形成梯度增厚的加强段。
在步骤S5中,所述复合材料管状柔性单元铺层前,将用于复合材料管状柔性单元铺层的成型芯模需预热至40℃。
在步骤S7中,相对的U形通孔机加工完成后,对U形通孔的边打磨出平滑倒角。
在步骤S8中,所述胶粘剂为常温固化胶粘剂。
以上对本发明的具体实施例进行了描述。需要理解的是,本发明并不局限于上述特定实施方式,本领域技术人员可以在权利要求的范围内做出各种变形或修改,这并不影响本发明的实质内容。