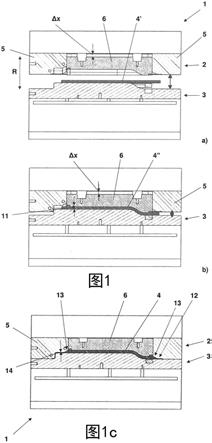
1.本发明涉及一种用于生产具有压制的二维或三维形状的夹层复合构件的方法,该复合构件具有至少一个由热塑性材料制成的具有两个相反的芯层表面的结构化的芯层,每个芯层表面直接或间接地结合到热塑性覆盖层。
背景技术:2.夹层复合构件广泛用于轻质结构,因为其具有非常高的单位面积载荷特性,同时具有低比重。对于承受重载荷的结构构件,这些夹层构件通常包括结构化的芯层、例如呈蜂窝状结构的芯层,其每一侧都结合纤维增强塑料覆盖层。尽管即使在大规模生产中也可以制造大面积的扁平的夹层复合构件,但仍然没有足够的生产方法可以在几分钟的周期内制造出连续纤维增强的夹层复合构件并具有指定的表面曲率。
3.大规模生产的方法、特别是具有均匀泡沫芯结构的连续纤维增强夹层构件的大规模生产方法,是众所周知的,但具有泡沫芯的夹层复合构件比具有结构芯的夹层复合构件具有更低的比机械刚度。此外,在模制在任一侧界定芯的覆盖层的同时使芯发泡的过程难以控制。
4.文献de102011006819 a1公开了一种制造三维轮廓夹层结构的方法,该夹层结构由两个热塑性覆盖层和位于它们之间的具有蜂窝结构的芯层组成。为了实现夹层结构的三维轮廓,蜂窝状芯层通过切割或分离加工方法进行预处理,以获得预期的三维轮廓。然后,通过将热塑性覆盖层热压到加工过的芯材上的过程,将热塑性覆盖层与芯层粘合在一起。很明显,这种方法仅适用于小批量生产或原型构建。
5.文献de4323590 a1公开了一种用于制造三维形状的层状复合构件的方法,该复合构件的芯层由泡沫热塑性材料构成,其在两侧与热塑性覆盖层粘合在一起。在这个过程中,芯层和覆盖层首先以松散的堆叠构造布置,然后在一个单一的热压过程中接合起来。在热压过程期间,两个覆盖层和芯层分别形成有粘合力的复合结合。
6.在ep3263321 a1中公开了一种与前述制造方法类似的用于制造具有增强泡沫芯的夹层板的方法。然而,在上述两种情况下,泡沫芯都没有提供与结构化的芯层相关的表面刚度和表面承载能力。
7.文献wo2013/143569a1公开了一种夹层复合构件的制造方法,该复合构件由蜂窝芯层和两个纤维增强热塑性覆盖层组成。该文献中公开的夹层构件的特殊特征在于,蜂窝芯层由基于纤维素的材料制成,其在作为变形过程的一部分的压力和热的作用下呈现相应的三维构造的构件形状。
8.除上述之外,涉及加工用于生产夹层构件的热固性材料的许多生产方法是已知的,例如真空灌注法、间隙浸渍法或树脂注射法。然而,热固性塑料在加工过程中的固化反应以及一些工艺步骤是手动执行的事实意味着其好处有限,即使不是完全不适合大规模制造。
9.文献ep1993808 b1公开了一种用于制造三维形状的夹层结构的方法,该结构被转移到具有压印模的压模中,压印模可以一个接一个地可变地移动以对其进行模制。夹层结构中的内芯层在不同区域受到不同程度的压缩,以至于形成折痕。
10.文献ep1626852 b1公开了一种复合构件及其制造方法,其中该构件以深拉法的方式二维成形并且包围其外周的热塑性材料通过压缩与其接合。
11.文献de102012002559 a1公开了一种用于制造不含热塑性材料的夹层复合构件的工具。
12.文献ep0894611 b1描述了一种通过压制至少包括第一和第二覆盖层以及位于它们之间的热塑性材料蜂窝芯的面板来生产机动车辆构件的方法,其中两个覆盖层由增强热塑性材料制成。在形状引起的曲率区域中形成附加的材料储存结构,抵消发生在任何地方的局部厚度减小。
技术实现要素:13.本发明所解决的问题是进一步开发一种用于制造具有压制的二维或三维形状的夹层复合构件的方法,该复合构件具有至少一个由热塑性材料制成的结构化的芯层,该结构化的芯层具有两个相反的芯层表面,每个芯层表面分别为其直接或间接地粘合到热塑性覆盖层,以这样的方式使得工业规模的大规模制造成为可能,并且还能够在构件的特定预定义的区域生产扁平和/或轻微至适度弯曲的夹层复合构件,每个区域都具有限定的芯层高度。还应该有可能生产这种具有密封的构件外周的夹层复合构件,由此保护内部结构化的芯层免受外部环境影响。以这种方式,应该可以在不超过几分钟的时间内生产出即用型的夹层复合构件,从而可以大量供应并具有很长的使用寿命。
14.本发明解决的问题的解决方案在权利要求1中陈述。权利要求14的主题是根据该解决方案设计的夹层复合构件。有利地改进本发明思想的特征是各个从属权利要求的主题或者可以从以下描述中看出、特别是参考示例性实施例可以看出。
15.根据上述解决方案,根据权利要求1的前序部分的特征生产具有压制的二维或三维形状的夹层复合构件的方法的特征在于以下方法步骤:
16.第一步是加热包含至少一个结构化的芯层的扁平的夹层半成品,其中覆盖层通过红外辐射、优选无接触地在其芯层表面接合,以便在待形成结构化的芯层的区域具有低于与芯层的热塑性材料相关的熔点的温度,并且两个覆盖层中的每一个的至少部分具有等于或高于与覆盖层的热塑性材料相关的熔点的温度。以这种方式,确保芯层的结构可以模制并在模制压缩期间保持其结构,并且两个覆盖层在模塑结束时参与与芯层表面的粘合。覆盖层分别由热塑性材料制成,该热塑性材料优选地由与结构化的芯层的热塑性材料相同的热塑性材料或相同类型的热塑性材料组成。这种热塑性材料有利地由部分结晶的热塑性塑料组成,其熔化温度构成结晶熔化温度。此外,覆盖层优选包含结构增强的连续纤维组分,其纤维长度应大于2cm,其中各个纤维随意布置或理想情况下完全穿过半成品一次并且大致单向布置或被实施为至少一层的编织结构。将覆盖层加热到热塑性基质的软化或熔化温度以上还允许纤维组分在软化的覆盖层内和芯层表面上滑动。在不打算进行成形的平坦半成品区域中,不熔化覆盖层可能进一步有利。
17.在一个优选的变型中,除了热塑性塑料之外,芯层还包含来自以下材料的至少一
种填充材料:滑石颗粒、白垩颗粒、玻璃粉或粉末以及由前面列出的纤维材料制成的短纤维,其中每一种都包含在覆盖层中。
18.然后,将加热的、目前为止扁平的夹层半成品转移到压制工具中,该压制工具包括至少两个压模半部,这些压模半部以沿空间轴线相对于彼此可线性移动的方式安装,其中至少第一压模半部具有至少两个压模段,该至少两个压模段沿空间方向相对于彼此可线性移动地安装。加热的夹层半成品被转移并插入压制工具中,使得夹层半成品与两个压模半部中的至少一个的至少部分区域形成表面接触。夹层半成品优选地贴靠或搁置在与具有至少两个压模段的压模半部相对的压模半部上,其中至少两个压模段被安装成沿空间方向相对于彼此可线性移动。在下文中,为了区分的目的,该压模半部将被称为第二压模半部。
19.加热的夹层半成品不一定但有利地通过负压定位和固定在第二压模半部的表面上。为此,第二压模半部的至少部分区域配备有真空抽吸元件,其保证夹层半成品牢固地粘附在压模半部的至少一个表面上并可靠地防止侧向滑动。
20.在“第一工艺步骤”的过程中,压制工具的两个压模半部沿空间方向朝向彼此移动,使得夹层半成品的至少部分区域与两个相对布置的压模半部表面接触,使得第一压模段在移动方向上移动在第一压模半部的相应的另一压模段之前,即第一压模段在运动方向上突出超过相应的另一压模段距离
△
x。在该过程中,在前的第一压模段与两个覆盖层之一形成表面接触,而相应的另一覆盖面已经贴靠在相对的、相应的另一压模半部上,并有利地由真空支撑。两个压模半部向彼此的进一步移动导致加热的夹层半成品在第一压模段和第二压模半部之间在两个或三个维度上被预压制,直到达到第一压模段和第二压模半部之间的第一最小间距。在这种情况下,第一最小间距对应于可分配给预压制的夹层半成品的最大厚度。在蜂窝状芯层的情况下,其蜂窝脊优选平行于两个压模半部朝向彼此移动的空间方向定向,蜂窝单元高度、即蜂窝脊的长度仅在压制过程中减小,并且覆盖层略有增加,增加的量取决于工具间隙(如果有的话)。夹层体成形而没有使芯层厚度突减的第一压制工艺步骤也可以分几个阶段进行,通过多部分压缩模具段从内向外地进行。
21.至少一个在前压模段优选地配备有真空抽吸元件,其对准以面向压制间隙的表面构成模压间隙的一部分。随后,与第一、在前压模段接触的覆盖层表面区域优选地通过负压部分或完全地被抽吸并固定地附接到第一压模段。由于在相对的接触区域处与预压制的夹层半成品的两侧接触,夹层半成品通过接触冷却来冷却。这又导致接触的覆盖层区域的热塑性材料在先前熔化的覆盖层表面区域处部分或完全固化。这种有针对性的固化和夹层半成品与在前压模段的优选的基于真空的粘合对这些夹层区域具有稳定作用。这种稳定减少或完全防止在随后的第二压制工艺步骤期间预压制的夹层半成品中的不期望的变形。
22.在随后的第二压制工艺步骤过程中,第一压模半部的相应另一压模段在空间方向上移动向相对的第二压模半部,而第一压模段相对于相对的第二压模半部静止,即夹层半成品在与第一压模段的接触区域中没有受到任何进一步的压力。通过其移动,相应的另一压模段在与未受先前预压制影响的直接或间接相邻地区域与预模制的夹层半成品接触,直到在相应的另一压模工具和第二个压模半部之间达到第二最小间距。第二最小间距优选地选择为使得覆盖层和芯层的热塑性材料在该区域中被压实以形成多层层压部。在该压制步骤中存在的压力、特别是在待压实的外周区域和与其直接相邻的预模制的夹层半成品的区域中的压力、以及高温导致覆盖层粘结地焊接至由芯层产生的塑料薄膜。
23.正是这种压实的多层层压部以及第一和第二最小间距之间的过渡区域有效地为内部相邻的结构化的芯层形成了不漏液体的密封。
24.根据相应的另一压模段的形状及其相对于相对布置的第二压模半部的移动性质,在夹层半成品的借助第一压模段预模制的区域和夹层复合构件的最终通过相应的另一压模段模制的区域之间形成几何形状上可定义的、具有恒定或陡的侧面的过渡性质的三维过渡轮廓。
25.在压制之后但在构件最终模制成形之前,成形的夹层构件在压制工具中多停留几秒钟以使其冷却。在此期间,所有覆盖层区域的热塑性基质完全凝固,构件温度基本下降。此时,可以有利地利用残余负压来减少空气夹杂,提高表面质量。
26.在一个优选的变型中,扁平的夹层半成品的加热通过红外辐射进行,使得夹层半成品的在第二次压制过程中被接合以形成密封的构件外周的区域和/或例如在形状过渡几何形状内经历更大的芯层厚度减小的那些区域被加热,使得这些区域过热并通过自发熔化损失一些厚度或高度,在一些情况下在红外辐射加热和/或成形前。随后,这使得三层层压部中的覆盖层基质和成形的芯层之间更好的粘合,该芯层熔化成塑料薄膜并重新成形,以及芯层内相邻过渡几何形状中芯脊的不显著的屈曲。
27.根据该解决方案的方法也可以直接与热塑性塑料注射成形相结合,从而允许另一种形式的自由度。
28.根据该解决方案构造的具有压制的二维或三维形状的夹层复合构件,具有至少一个由热塑性材料制成并具有两个相反的芯层表面的结构化的芯层,并且包括热塑性覆盖层,每个覆盖层直接或间接地粘合到两个芯层表面,其特征在于至少一个三维过渡轮廓,其整体地将夹层复合构件的第一区域连接到夹层复合构件的相邻第二区域,形成压实和焊接的多层层压部,其中,在所述第一区域中结构化的芯层将两个覆盖层彼此分开,在所述第二区域中包含两个覆盖层和作为塑料膜的结构化的芯层。
29.优选地实施为陡侧面或平坦倒角的三维过渡轮廓围绕边缘、沿着夹层复合构件的外周周向边界延伸。与其结合或替代地,可以在夹层复合构件内设置过渡轮廓,使得包含结构化的芯层并且将两个覆盖层彼此分开的第一区域围绕第二区域的至少一部分。
30.根据本发明的夹层复合构件可以在第一区域中具有三维变形,该变形至少在其区域中偏离平坦的表面延伸,例如呈由结构化的芯层和两个覆盖层组成的平坦复合结构的波浪曲率的形式。
31.夹层复合构件的两个覆盖层优选地由热塑性材料制成,优选地以芳族聚酰胺、碳、陶瓷、玻璃、石英或玄武岩纤维的形式的连续纤维构件添加到该热塑性材料中。各个纤维理想地尺寸定制和布置为使得它们一次完全穿过夹层半成品并且以至少一层大致单向布置,或者它们具有编织结构的形式。
32.根据该解决方案的夹层复合构件可优选用作汽车、大篷车、造船和飞机制造领域中的承重构件,或者用作光伏模块或太阳能热能模块或运动产中的承重结构。
附图说明
33.在下文中,将根据示例性实施例并参照附图来描述本发明,该描述只用于示例性目的,而不限制本发明的总体构思。图中:
34.图1a-1c示出了顺序图像,以说明根据本解决方案的具有结构化的接收芯层和密封的构件外周的夹层复合构件的成形;
35.图2代表具有扁平结构的夹层半成品;
36.图3a示出了夹层复合构件成品的纵向截面;以及
37.图3b-3g示出了该纵向截面的详细视图。
具体实施方式
38.根据本解决方案的方法能够在1到几分钟的周期内使用压制工具1从具有结构化的芯层8和覆盖在该芯层的两侧的两个覆盖层9的扁平的夹层半成品4'在两个连续的工艺步骤中生产二维或三维形状的夹层复合构件4。在线性工具闭合移动期间启动用于成形的两个连续工艺步骤。借助垂直或水平闭合压制工具执行线性闭合移动,下面将参考图1a至c进行解释。
39.图1a至图1c分别示出了在按时间连续的方法情况下压制工具1的横截面图。压制工具1具有两个优选地为金属的压模半部2、3,它们在闭合状态下包围出腔,待生产的夹层复合构件4最终形成在该腔内,参见图1c。
40.压制工具1配备有两个可移动的压模半部2、3,它们沿空间方向r可线性移动、优选地如图所示垂直或水平移动,其中如图所示的上部的第一压模半部2包括两个压模段5、6,该两个压模段5、6沿空间方向r以相对于彼此可线性移动的方式安装。在这种情况下,与第一压模半部2相对定位的第二压模半部3构造为单个部件。
41.在图1a所示的开始情况下,第一压模段6相对于相应的另一压模段5移动距离
△
x并且相对于相应的另一压模段5向下突出。这样的构造能够实现两阶段压制过程,同时临时稳定最初重塑的几何形状。
42.优选地由透气材料、例如多孔铝、泡沫金属或烧结金属制成的真空吸盘集成在压模段5、6中和下部的压模半部3的表面上,并连接到设置在工具侧面的对应的负压源。
43.在图1a所示的情况下,扁平的夹层半成品4'位于下部的压模半部3的表面上。
44.图2示出这种类型的扁平的夹层半成品4',其具有结构化的芯层8和两个覆盖层9、10,芯层和每个覆盖层均由相同的热塑性材料制成。芯层8具有并排布置的蜂窝或圆柱体形式的结构化的构造。覆盖层9、10包含用于增强目的的连续纤维,其中各个纤维理想地完全穿过半成品一次并且以至少一层单向布置或设置为编织结构的形式。
45.图2中所示的夹层半成品4'在其被放入压制工具1之前或期间被处理到一定的热状态。该热状态的限定特征是覆盖层9和10的热塑性材料达到高于其熔化温度的温度,并且芯层8的热塑性材料达到等于或低于其熔化温度的温度。夹层半成品4'的加热优选地紧接在成形之前借助于施加到两侧的红外辐射加热进行。
46.两阶段压制过程以压制工具1的闭合移动开始,其中第一压模半部2相对于第二压模半部3移动,在当前情况下是垂直向下移动。夹层半成品4'在成形之前和成形期间通过真空吸盘至少附接到第二压模半部3的下侧。
47.图1b示出上部的压模半部2已经垂直下降,并且原始扁平的夹层半成品4'已经通过与施加有压制力的在前的第一压模段6接触而预成形的情况。在保留芯层8的结构的同时进行夹层半成品4'的预压制。当达到预成形的夹层半成品4'之间的最小间距11时,图1b所
示的用于获得预成形的夹层半成品4”的成形过程结束。第一最小间距11对应于预压制的夹层半成品4'的最大层厚。优选地,与夹层半成品4'的覆盖层9、10与第一压模段6以及第二压模半部3的表面之间的随后的过渡轮廓靠近的所有接触区域在预压制期间都提供有负压,这样负压对夹层半成品4”和压制模具1之间的接触区域的影响用于防止芯层8的芯失效和/或不期望的芯高度降低。
48.在进行随后的第二次压制工艺步骤之前的时间,预成形的夹层半成品4”被储存在与夹层半成品4”接触的压模段6和压模半部3内并冷却,并且没有任何会改变预成形的夹层半成品4”的形状的进一步的模制力。夹层半成品通过接触冷却,通过在预压制的夹层半成品4”的两侧的相反接触区域上的接触进行冷却。这导致在先前熔化的覆盖层表面区域处接触的覆盖层的热塑性材料的部分或全部固化。这种有针对性的固化以及夹层半成品4”优选地由于负压而粘附到在前的压模段6具有稳定这些夹层区域的效果。这种稳定减少或完全防止在随后的第二压制工艺步骤中预压制的夹层半成品的不期望的变形。这种稳定状态的持续时间至少为1秒。
49.在第二压制工艺步骤中,夹层半成品4”的先前未接触的子区域通过相应的另一压模段5对于相对的第二压模半部3的移动被重新成形和压制,而第一压模段6相对于第二压模半部3静止。随着闭合移动的进行,夹层芯在第一压模段6侧向之外的区域中被压缩,直到在相应的另一压模段5和第二压模半部3之间达到第二最小间距14,从而形成压实的层压部12。这些压实的构件区域12根据构件的形状和压模段(5、6)的设计可以模制为围绕构件的外周延伸和/或在夹层构件内延伸。
50.根据压模段的构造和形状,结构上保留的芯层区域和外周压实的层压区域12之间的过渡部13可以是陡侧面或恒定的。
51.根据所使用的压制工具或甚至所使用的注塑机器,这里解释的压制方法可以与其他常规加工步骤、例如随后用冲头修边或通过注塑进一步功能化相结合。
52.根据本解决方案的方法生产的夹层复合构件可以包括具有限定的芯高度的平坦和弯曲的夹层区域。芯高度取决于腔内的间隙宽度,见图1c。
53.在夹层复合构件4成形有结构被保留的芯层的区域与相邻的压实的层压区域12之间的过渡部13可以成形为例如倒角。
54.在压制之后但在构件最终模制成形之前,成形的夹层构件在压制工具中多停留几秒钟以使其冷却。在此期间,所有覆盖层区域的热塑性基质完全凝固,构件温度基本下降。此时,可以有利地利用残余负压来减少空气夹杂,提高表面质量。
55.围绕构件的外周周向延伸的压实的层压部可以密封夹层的内部以防止空气和流体渗透,同时可以用作接合部。还可以创建紧凑的层压区域,就像在夹层复合构件4成品内具有对应的过渡一样。
56.图3a示出了夹层复合构件4成品的纵向截面,除了外周压实的区域12,其中,两个覆盖层9、10与芯层8共同压制以形成整体或实际上整体的材料复合物,其包含过渡区域b1,与其相邻的未成形区域b2,以及随后的2d和3d成形区域b3。
57.过渡区域b1在图3b和图3c中详细示出,其中图3b是示出了覆盖层9、10和布置在它们之间的芯层8的结构壁的照片细节表示,图3c示出了示意性局部纵向截面,其中纵向截面的相应下半部示出在过渡区域b1中。图3d和图e示出了未成形区域b2的对应图示,图3f和图
g示出了成形区域b3。
58.优选的蜂窝状芯层8包括结构壁15,其相反的结构壁边缘分别粘合到两个覆盖层9、10之一,其中类似于焊缝的热塑性材料的材料堆积16设置在结构壁边界的每一侧,每一个堆积都与覆盖层9、10接合,堆积与覆盖层9、10和结构壁15结合为一体。
59.在过渡区域b1中,结构壁高度从区域b2中未成形的结构壁高度h开始向下降低,在压实的边缘区域12与覆盖层9、10形成完整的膜结构。由于压制力和靠近覆盖层9、10的结构壁15和覆盖层9、10本身的比热塑性基体的熔化温度更高的最高温度引起的高度降低,结构壁15开始变形,至少在靠近覆盖层9、10的区域中并且覆盖层9、10自身熔化到焊缝状材料堆积中。这导致更强的焊缝状材料堆积,结构壁高度h进一步降低。此外,剪切力导致材料堆积16相对于结构壁15并切向于覆盖层9、10的变形。形成足状变形部16',结构壁15从该变形部延伸。
60.结构壁15在未成形的夹层复合构件区域b2内的两个覆盖层9、10之间基本线性地延伸。热塑性材料的焊缝状材料堆积16位于每个结构壁边界的两侧,并且每个堆积都在这些区域中与覆盖层9、10和结构壁15整体结合。
61.在具有压制的二维或三维形状的夹层复合构件4的区域b3内,热塑性材料的焊缝状材料堆积16表现出剪切力引起的变形,该变形与相邻的覆盖层单向延伸,使得根据曲率在结构壁边界的一侧形成越来越多的材料堆积16',这在图3f和图g的详细示出中可以特别清楚地看到。理想地,结构壁15在该区域b3中也基本上是未成形的、即直的。然而,由于夹层复合构件4的曲率过大、区域b2和b3中的结构壁高度h降低过快和/或覆盖层9、10中的温度太低,可能会发生偏离的结构壁变形,这会导致结构壁15上覆盖层9、10的滑动运动受阻,因此导致焊缝状材料堆积16的剪切变形较小,而是产生结构壁15本身的剪切变形。覆盖层温度不够高的原因是在用红外辐射进行热处理期间热能输入不足和/或从红外辐射热处理完成到第一次压制工艺步骤开始的转移时间过长。
62.附图标记列表
[0063]1ꢀꢀꢀꢀꢀꢀꢀ
压制工具
[0064]2ꢀꢀꢀꢀꢀꢀꢀ
第一压模半部
[0065]3ꢀꢀꢀꢀꢀꢀꢀ
另一压模半部
[0066]4ꢀꢀꢀꢀꢀꢀꢀ
夹层复合构件
[0067]
4'
ꢀꢀꢀꢀꢀꢀ
扁平的夹层半成品
[0068]4”ꢀꢀꢀꢀꢀ
预压制的夹层半成品
[0069]5ꢀꢀꢀꢀꢀꢀꢀ
相应的另一压模段
[0070]6ꢀꢀꢀꢀꢀꢀꢀ
第一压模段
[0071]7ꢀꢀꢀꢀꢀꢀꢀ
扁平的夹层半成品
[0072]8ꢀꢀꢀꢀꢀꢀꢀ
芯层
[0073]
9、10
ꢀꢀꢀ
覆盖层
[0074]
11
ꢀꢀꢀꢀꢀꢀ
第一最小距离
[0075]
12
ꢀꢀꢀꢀꢀꢀ
压实的层复合部
[0076]
13
ꢀꢀꢀꢀꢀꢀ
过渡部
[0077]
14
ꢀꢀꢀꢀꢀꢀ
第二最小距离
[0078]
15
ꢀꢀꢀꢀꢀꢀ
结构壁
[0079]
16
ꢀꢀꢀꢀꢀꢀ
材料堆积
[0080]
16'
ꢀꢀꢀꢀꢀ
单侧材料堆积
[0081]
b1
ꢀꢀꢀꢀꢀꢀ
过渡区域
[0082]
b2
ꢀꢀꢀꢀꢀꢀ
未成形区域
[0083]
b3
ꢀꢀꢀꢀꢀꢀ
成形区域。