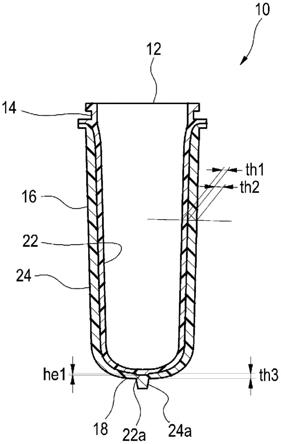
1.本发明涉及预制件、树脂制容器、以及用于制造预制件和树脂制容器的方法。
背景技术:2.专利文献1公开了一种具有两层结构的塑料瓶,在该结构中,内层由原生塑料制成,外层由再生塑料制成。专利文献2公开了一种用于层叠树脂成型品的制造方法,该制造方法包括:使用再生树脂成型管状的外层材料的外层成型过程;以及在外层材料的内表面侧上使用比外层材料薄的原生树脂来层叠并成型管状内层材料的内层成型过程。引用列表专利文献
3.专利文献1:jp-2002-103429-a专利文献2:jp-2002-104362-a
技术实现要素:技术问题
4.近年来,塑料垃圾造成的海洋污染被视为一个严重问题,国际上已启动3r(减少、再利用、回收)塑料的措施。对于食品/饮料/药瓶(食品容器),已经开发了一种吹塑预制件的方法,该预制件被注塑成内外两层结构,其中,原生材料用于与内容物接触的部分(内层),而再生材料用于非接触部分(外层)。然而,利用相关技术中的两层成型法,瓶的雾度(浊度)往往较大。难以制造具有足够透明度的瓶,并且商业化(实际应用)没有进展。
5.本发明的目的是提供可以形成具有两层结构并且即使在再生材料的使用比率大时也具有高透明度的树脂制容器的预制件、具有两层结构并且即使在再生材料的使用比率大时也具有高透明度的树脂制容器、以及用于制造预制件和树脂制容器的制造方法。技术方案
6.可以解决以上问题的本发明的一个方面是一种预制件,该预制件包括:开口部;主体部;以及底部,预制件具有两层结构,其中,主体部和底部包括由原生材料制成的内层和由再生材料制成的外层,其中,再生材料与预制件的总重量的重量比为50重量%或以上,其中,主体部中的外层的厚度与内层的厚度的比为1.5或以上,并且其中,由预制件成型的容器的主体部的雾度为1.8%或以下。
7.可以解决以上问题的本发明的另一方面是一种用于制造预制件的制造方法,预制件包括开口部、主体部以及底部,预制件具有两层结构,其中,主体部和底部包括由原生材料制成的内层和由再生材料制成的外层,制造方法包括:第一注塑过程,将原生材料或再生材料注射到第一模具中,以注塑内层材料或外
层材料;以及第二注塑过程,将在第一注塑过程中成型的内层材料或外层材料容纳在第二模具中,并将再生材料注射到内层材料的外侧以注塑外层材料,或者将原生材料注射到外层材料的内侧以注塑内层材料,其中,内层材料和外层材料被成型为使得再生材料与预制件的总重量的重量比为50重量%或以上,并且主体部中的外层的厚度与内层的厚度的比为1.5或以上。
8.可以解决以上问题的本发明的另一方面是一种树脂制容器,该树脂制容器包括:开口部;主体部;以及底部,树脂制容器具有两层结构,其中,主体部和底部包括由原生材料制成的内层和由再生材料制成的外层,其中,再生材料与树脂制容器的总重量的重量比为50重量%或以上,其中,主体部中的外层的厚度与内层的厚度的比为1.5或以上,并且其中,主体部的雾度为1.8%或以下。
9.可以解决以上问题的本发明的另一方面是一种用于制造树脂制容器的制造方法,制造方法包括:注塑预制件的注塑过程,预制件包括开口部、主体部以及底部,预制件具有两层结构,其中,主体部和底部包括由原生材料制成的内层和由再生材料制成的外层;温度调节过程,调节预制件的温度;以及吹塑过程,对预制件进行吹塑,以成型树脂制容器,其中,注塑过程包括:第一注塑过程,将原生材料或再生材料注射到第一模具中,以注塑内层材料或外层材料;以及第二注塑过程,将在第一注塑过程中成型的内层材料或外层材料容纳在第二模具中,并将再生材料注射到内层材料的外侧以注塑外层材料,或者将原生材料注射到外层材料的内侧以注塑内层材料,并且其中,在注塑过程中,内层材料和外层材料被成型为使得再生材料与预制件的总重量的重量比为50重量%或以上,并且主体部中的外层的厚度与内层的厚度的比为1.5或以上。本发明的有益效果
10.根据本发明,可以提供可以形成具有两层结构并且即使在再生材料的使用比率大时也具有高透明度的树脂制容器的预制件、具有两层结构并且即使在再生材料的使用比率大时也具有高透明度的树脂制容器、以及用于制造预制件和树脂制容器的制造方法。
附图说明
11.图1是例示了根据实施例的预制件的剖视图。图2是例示了根据实施例的树脂制容器的剖视图。图3是例示了根据实施例的预制件的制造过程的流程图。图4是例示了根据实施例的预制件的注塑模式的剖视图。
图5是例示了根据实施例的冷却预制件的模式的剖视图。图6是例示了根据实施例的冷却预制件的另一模式的剖视图。图7是例示了根据实施例的树脂制容器的制造过程的流程图。图8是例示了根据实施例的树脂制容器的制造装置的示意图。图9是例示了根据实施例的修改例的树脂制容器的制造过程的流程图。图10是例示了根据实施例的修改例的树脂制容器的制造装置的示意图。图11是例示了根据实施例的修改例的预制件的注塑模式的剖视图。
具体实施方式
12.下文中,将参照附图描述本发明的实施例。注意,为了便于描述,附图所例示的各个构件的尺寸可以与各个构件的实际尺寸不同。
13.首先,将参照图1描述根据实施例的预制件10。图1是预制件10的剖视图。预制件10是管状树脂成型品,包括:开口部12;与开口部12连续的颈部14;与颈部14连续的主体部16;以及与主体部16连续的底部18。主体部16和底部18具有包括内层22和外层24的两层结构。内层22由是未用过的树脂材料的原生材料制成。外层24由通过回收使用过的树脂材料而制备的再生材料制成。作为原生材料和再生材料的基材,使用在无定形状态下具有透明度的热塑性树脂(结晶塑料),诸如聚对苯二甲酸乙二醇酯(pet)树脂。预制件10用于成型稍后描述的树脂制容器30。
14.再生材料与预制件10的总重量的重量比为50重量%以上。重量比从树脂材料的回收率的观点出发优选60重量%以上,从待成型容器的透明度的观点出发优选70重量%以下。主体部16中的外层24的厚度th2与内层22的厚度th1的比为1.5以上。该比从待成型容器的透明度的观点出发优选3.0以下。
15.通过注塑形成的浇口痕迹22a和24a分别存在于预制件10的底部18中的内层22和外层24中。底部18中的内层22的浇口痕迹22a的高度he1小于外层24的厚度th3。
16.接着,将参照图2描述根据实施例的容器30。图2是容器30的剖视图。容器30是通过吹塑预制件10而获得的瓶状树脂制容器。容器30包括与开口部12连续的颈部14、与颈部14连续的主体部36、以及与主体部36连续的底部38。与预制件10类似,主体部36和底部38具有两层结构,该结构包括由原生材料制成的内层42和由再生材料制成的外层44。
17.再生材料与容器30的总重量的重量比以及主体部36中的外层44的厚度th12与内层42的厚度th11的比分别和再生材料与预制件10的总重量的重量比以及主体部16中的外层24的厚度th2与内层22的厚度th1的比相同,由此将省略其描述。
18.容器30的主体部36的雾度为1.8%以下,更优选1.4%以下,进一步优选1.0%以下。虽然没有特别限制,但是雾度的下限可以是0.1%。这里提及的雾度是通过选择主体部36的任意10个部分进行测量而得到的值的平均值。雾度根据“塑料:透明材料的雾度的确定(jis-k7136:2000)”使用雾度计来测量。容器30是即使在再生材料的使用比率大的情况下也具有高透明度的两层结构的树脂制容器,并且可以实现塑料材料的高回收率,同时具有高实用性。
19.接着,将参照图3至图6描述用于预制件10的制造方法。图3是例示了预制件10的制造过程的流程图。图4是例示了预制件10的注塑模式的图。图5和图6是例示了在注塑预制件
10之后的冷却模式的图。
20.如图3所示,根据本实施例的用于制造预制件10的制造方法包括内层材料成型过程s1和外层材料成型过程s2,这两个过程是注塑过程的两个步骤。这里,将参照图4描述各个过程。在内层材料成型过程s1中,经由第一浇口58将原生材料注射到由第一模具50限定的空腔中,该第一模具包括第一腔模具52、第一注射芯模具54和颈部模具56。第一模具50包括第一热流道模具59。第一热流道模具59具有阀销59a,其可在流路中朝向第一浇口58移动,熔融状态的树脂材料(例如,约255℃的熔融状态的pet树脂)流经该流路。即,第一模具50的第一浇口58被构造为阀门浇口。当完成将原生材料填充到空腔中时,将第一模具50的模具夹紧保持预定的时间段,其后打开第一模具50,使得成型内层材料60。在第一腔模具52和第一注射芯模具54中设置有用于冷却内层材料60的冷却介质(流体)流经的回路(介质流动孔或介质流动槽),并且冷却介质被适当地设定在例如约5℃至约20℃的范围内。
21.将成型的内层材料60与第一注射芯模具54和颈部模具56一起提起,并与第一腔模具52分离。进一步地,将第一注射芯模具54进一步提起并与内层材料60分离。然后,通过旋转部分(未示出)使内层材料60在被颈部模具56保持的状态下与颈部模具56一起旋转,并且将内层材料60布置在第二腔模具72上方。在外层材料成型过程s2中,将保持内层材料60的颈部模具56夹紧到第二注射芯模具55和第二腔模具72上,使得内层材料60容纳在包括第二腔模具72、第二注射芯模具55和颈部模具56的第二模具70中。然后,经由第二浇口78将熔融状态的再生材料注射到由第二模具70限定的空腔中的内层材料60的外侧上的部分。第二模具70包括第二热流道模具79。第二热流道模具79可具有阀销,其可在树脂材料流经的流路中朝向第二浇口78移动。即,第二模具70的第二浇口78可被构造为阀门浇口。当完成将再生材料填充到空腔中时,将第二模具70的模具夹紧保持预定的时间段,其后打开第二模具70,使得成型包括外层材料80和内层材料60的预制件10。在本实施例中,在前一预制件10的外层材料成型过程s2期间执行下一预制件10的内层材料成型过程s1。另外,在第二腔模具72和第二注射芯模具55中,设置有用于冷却外层材料80和内层材料60的冷却介质流经的回路,并且冷却介质被适当地设定在例如约5℃至约20℃的范围内。注意,冷却介质的温度(即冷却强度)在第一模具50和第二模具70中可以不同(例如,第二模具70的冷却介质的温度被设定为低于第一模具50的冷却介质的温度)。进一步地,即使在第二模具70中,冷却强度在第二腔模具72和第二注射芯模具55中也可以不同(例如,第二腔模具72的冷却介质的温度被设定为低于第二注射芯模具55的冷却介质的温度)。
22.在内层材料成型过程s1和外层材料成型过程s2中,通过使用第一模具50和第二模具70来成型内层材料60和外层材料80,该第一模具和第二模具被设计为使得再生材料(外层材料80)与预制件10的总重量的重量比为50重量%以上,并且预制件的主体部16中的外层24(外层材料80)的厚度与内层22(内层材料60)的厚度的比为1.5以上。在此,第一模具50中的第一浇口58的长度le1小于预制件10的底部18中的外层24(外层材料80)的厚度th3。
23.当根据本实施例的用于制造预制件10的制造方法包括在外层材料成型过程s2之后冷却预制件的冷却过程s3时,可以缩短注塑过程的冷却时间,这从生产效率的观点出发是优选的(图3)。在此提及的冷却过程s3不包括当保持第二模具70的模具夹紧时利用第二模具70冷却预制件10的过程。在此,将参照图5和图6描述冷却过程s3的模式。
24.图5是例示了冷却过程s3的模式状态的图。在图5所例示的冷却过程s3中,将从第
二模具70释放的预制件10容纳在第三腔模具100中,并且使空气引入构件110与预制件10气密地接触。空气引入构件110包括中空且内部设置有气流孔的杆构件112和装配芯(吹制芯构件)114。杆构件112被容纳在装配芯114内部,以便可上下移动。在杆构件112的末端设置有喷射或抽吸空气可以通过的内侧流动口116。空气的温度根据预制件10或容器30的厚度被适当地设定在例如约0℃至约20℃(常温)的范围内。装配芯114被构造为当空气引入构件110插入到预制件10中时(当空气引入构件110与预制件10气密地接触时)装配到颈部14中(与其紧密接触)。因此,可以防止预制件10内的空气从颈部14泄漏到装配芯114的外部。杆构件112与装配芯114之间的间隙是用于向预制件10供应空气和从其排出空气的空气流路。由装配芯114的末端和杆构件112形成的间隙构成喷射或抽吸空气可以通过的外侧流动口118。内侧流动口116和外侧流动口118可以分别是空气吹送口和排出口。例如,空气从空气引入构件110的空气吹送口供给到预制件10中,并且空气从空气引入构件110的排出口排出到预制件10的外部,从而冷却预制件10。另外,在第三腔模具100中还设置有用于冷却外层材料80的冷却介质的回路,并且流体介质被适当地设定在例如约5℃至约80℃、更优选地10℃至70℃、并且还更优选地20℃至65℃的范围内。
25.图6是例示了冷却过程s3的另一模式状态的图。在图6所例示的冷却过程s3中,将从第二模具70释放的预制件10容纳在第四腔模具120中,并且将预制件10夹在第四腔模具120与被构造成可上下移动的芯模具130之间,从而冷却预制件10。第四腔模具120和芯模具130还设置有回路,被设定在例如约5℃至约80℃、更优选地10℃至70℃、并且还更优选地20℃至65℃的范围内的冷却介质流经该回路。
26.接着,将参照图4至图7描述用于制造容器30的制造方法。图7是例示了容器30的制造过程的图。如图7例示,根据本实施例的用于制造容器30的制造方法包括注塑预制件10的注塑过程s11、调节预制件10的温度的温度调节过程s12、以及吹塑预制件10以成型容器30的吹塑过程s13。
27.首先,将描述注塑过程s11。注塑过程s11包括在用于制造预制件10的制造方法中描述的内层材料成型过程s1和外层材料成型过程s2。在注塑过程s11中,如预制件10的内层材料成型过程s1和外层材料成型过程s2所述,成型内层材料60和外层材料80,使得再生材料(外层材料80)与预制件10的总重量的重量比为50重量%以上,并且预制件的主体部16中的外层24(外层材料80)的厚度与内层22(内层材料60)的厚度的比为1.5以上。在内层材料成型过程s1中使用的第一模具50、在外层材料成型过程s2中使用的第二模具70以及在注塑过程s11中采用的其它模式与在用于预制件10的制造方法(图4)中描述的那些类似,因此将省略其描述。
28.接着,将描述温度调节过程s12。温度调节过程s12是将注塑的预制件10的温度调节到适于吹塑的温度范围的过程。在温度调节过程s12中,通过使用温度调节舱、温度调节芯、红外加热器等来调节预制件10的温度。另外,在温度调节过程s12中,可以采用在用于预制件10的制造方法的冷却过程s3中描述的模式(图5和图6),并且可以在冷却预制件的同时调节温度。当温度调节过程s12采用在用于预制件10的制造方法的冷却过程s3中描述的模式时,容器30的生产效率提高,这是优选的。特别地,当在后述的图8所示的树脂制容器的热型坯式制造装置中连续地进行预制件10和容器30的制造时,容器30的生产效率提高,这是优选的。另外,在使用热型坯式吹塑法连续地进行两层预制件的注塑和吹塑时,内层22与外
层24之间的边界部分冷却不充分(逐渐冷却),雾度可能增加。然而,当在温度调节过程s12中采用冷却过程s3中描述的模式(图5和图6)时,可以提高边界部分的冷却效率,同时保持吹塑所需的热量,并且可以降低容器30的雾度。当在温度调节过程s12中采用冷却过程s3时,流经第三腔模具100、第四腔模具120和芯模具130的冷却介质的温度被适当地设定在例如约10℃至约65℃的较宽范围内。
29.接着,将描述吹塑过程s13。在吹塑过程s13中,将预制件10容纳在吹制腔模具中。随后,在通过拉伸杆可选地拉伸预制件10的同时,通过从吹制芯模具引入吹制空气使预制件10膨胀成容器30的形状,从而制造容器30。其后,将容器30从模具中释放。根据上述过程制造容器。
30.在此,将参照图8描述根据本实施例的容器30的制造装置150。图8是容器30的制造装置150的功能框图。制造装置150包括用于制造预制件10的注塑部152、用于调节所制造的预制件10的温度的温度调节部154、用于吹制预制件10以制造容器30的吹塑部(吹制装置的示例)156、以及用于取出所制造的容器30的取出部158。在制造装置150中,按注塑部152、温度调节部154、吹塑部156和取出部158的顺序通过传送部分(未例示)来传送预制件10和容器30。作为注塑部152、温度调节部154和吹塑部156的模式,采用在用于预制件10的制造方法和用于容器30的制造方法中描述的模式(图4至图6)的配置。制造装置150是树脂制容器的热型坯式制造装置,并且连续地进行预制件10及容器30的制造。
31.同时,在国际上启动塑料的3r的措施期间,采取各种回收措施,其最终目标是“瓶到瓶”的回收,即使在pet容器的领域中。例如,洗涤剂/调色剂pet瓶(非食品容器)通常使用通过粉碎用过的pet瓶获得的碎片材料或回收的球团料和原生材料的混合材料制造。另一方面,食品/饮料/药品pet瓶(食品容器)使用原生材料制造,很少使用再生材料。这是因为这种pet瓶需要具有高度的卫生安全性。因此,已经开发了一种吹塑预制件的方法,该预制件被注塑成内外两层结构,其中,原生材料用于与内容物接触的部分(内层),而再生材料用于非接触部分(外层)。
32.然而,利用相关技术中的两层成型法,瓶的雾度(浊度)往往较大。难以制造具有足够透明度的瓶,并且商业化(实际应用)没有进展。另外,同样在使用混合材料的情况下,考虑到瓶的透明度,将回收球团料的使用比例(重量比)限制在至多约30重量%,并且需要进一步改进。
33.根据具有上述构造的预制件10,可以形成具有两层结构并且即使当再生材料的使用比率大时也具有高透明度的树脂制容器30。具体地,可以形成透明度与由含有30重量%的回收球团料的混合材料制成的两层预制件所形成的容器相当的树脂制容器。
34.另外,在预制件10中,由于浇口痕迹22a的高度“he1”小于底部18中的外层24的厚度“th3”,所以原生材料在注射再生材料时熔化并与再生材料混合的发生可以得到抑制。因此,可以提供一种预制件10,其中,可以抑制其底部18的变白,并且可以由该预制件形成具有两层结构且透明度高的树脂制容器30。
35.另外,与原生材料相比,再生材料具有更高的结晶速率,并且可能变白。为了抑制再生材料的变白,首先成型由原生材料制成的内层材料60,然后成型由再生材料制成的外层材料80。然而,发现了以下情况:出现了这样的现象,即,由于再生材料的注射,在原生材料可能结晶并逐渐冷却的温度范围内(例如,在pet树脂的情况下为约150℃)对原生材料进
行再加热,并且在原生材料与再生材料之间的界面中可能出现变白(结晶)。因此,通过降低原生材料与预制件10的总重量的重量比并且减小内层22相对于外层24的厚度,增加了由第一模具50和第二模具70(第二注射芯模具55)对内层22的冷却效率,使得可以成功地抑制原生材料与再生材料之间的界面中的变白。即,根据上述用于制造预制件10的制造方法,成型由原生材料制成的内层材料60,其后成型由再生材料制成的外层材料80,并且内层材料60和外层材料80被成型为使得再生材料与预制件10的总重量的重量比为50重量%以上,并且主体部16中的外层24的厚度th2与内层22的厚度th1的比为1.5以上。因此,可以提供预制件10,其能够形成具有两层结构并且即使在再生材料的使用比率大时也具有高透明度的树脂制容器30。
36.另外,在上述用于制造预制件10的制造方法中,由于注射原生材料的第一浇口58的长度le1小于底部18中的外层24的厚度th3,因此减小了形成在内层材料60中的浇口痕迹22a的高度he1,并且可以防止原生材料在注射再生材料时熔化并与再生材料混合。因此,可以提供一种预制件10,其中,可以抑制其底部18中由结晶等引起的变白,并且可以由该预制件形成具有两层结构且透明度高的树脂制容器30。
37.另外,在上述用于制造预制件10的制造方法中,由于设置了在外层材料成型过程s2之后冷却预制件10的冷却过程s3,所以可以缩短在注塑时预制件10的冷却时间。因此,可以在预制件10的冷却期间开始下一个预制件10的成型,可以提高生产效率。
38.另外,由于在上述用于制造预制件10的制造方法的冷却过程s3中通过送入和排出空气来冷却预制件10,所以可以加速预制件10的冷却。因此,可以提供一种预制件10,其可以形成具有两层结构且透明度更优异的树脂制容器30,同时提高预制件10的生产效率。
39.另外,由于在上述用于制造预制件10的制造方法的冷却过程s3中,预制件10被夹在第四腔模具120与芯模具130之间,所以可以加速预制件10的冷却。因此,可以提供一种预制件10,其可以形成具有两层结构且透明度更优异的树脂制容器30,同时提高预制件10的生产效率。
40.另外,根据上述用于制造容器30的制造方法,在成型预制件10的内层材料60之后成型预制件10的外层材料80,并且预制件10的内层材料60和外层材料80被成型为使得再生材料与预制件10的总重量的重量比为50%重量以上,并且主体部16中的外层24的厚度th2与内层22的厚度th1的比为1.5以上。因此,可以提供一种容器30,其具有两层结构并且即使在再生材料的使用比率大时也具有高透明度。另外,关于相关技术中的热型坯式两层成型法,由于容器的雾度往往变大,并且难以制造具有足够透明度的瓶,因此商业化(实际应用)没有进展。根据上述方法,特别是在热型坯式两层成型法中,可以提供具有两层结构并且即使当再生材料的使用比率大时也具有高透明度的容器30。
41.另外,由于在上述用于制造容器30的制造方法中的注塑过程s11和温度调节过程s12采用在用于制造预制件10的制造方法中描述的模式,所以可以形成具有两层结构并且透明度更优异的树脂制容器,可以缩短容器成型的周期时间,并且可以提高生产效率。
42.尽管在上述实施例中描述了在内层材料成型过程s1之后执行外层材料成型过程s2的模式,但是本发明不限于该模式。图9是例示了根据上述实施例的修改例的树脂制容器的制造过程的流程图。如图9所示,第一注塑过程s31、第一温度调节过程s32、第二注塑过程s33、第二温度调节过程s34和吹塑过程s35可以以这个顺序执行来制造树脂制容器。在成型
预制件时,可以以第一注塑过程s31、第一温度调节过程s32、第二注塑过程s33和第二温度调节过程s34的顺序执行。
43.该修改例中的第一注塑过程s31是成型预制件的内层材料和外层材料中的任何一个的过程,第二注塑过程s33是成型预制件的内层材料和外层材料中的没有在第一注塑过程s31中成型的一个以成型预制件的步骤。第一温度调节过程s32是调节在第一注塑过程s31中成型的预制件的内层材料或外层材料的温度的过程。第一温度调节过程s32可以是冷却预制件的内层材料或外层材料的步骤。在第一注塑过程s31与第二注塑过程s33之间的第一温度调节过程s32中,对首先成型的预制件的内层材料或外层材料进行后冷却(特别地,对上面将在第二注塑过程s33中层叠树脂材料的表面进行后冷却),使得可以实现两层预制件的雾度降低(通过抑制内层材料与外层材料之间的界面中的变白来降低雾度)和成型周期缩短。第二温度调节过程s34是调节在第二注塑过程s33中成型的预制件的温度的过程。第二温度调节过程s34可以是冷却预制件的过程。吹塑过程s35是吹塑在第二温度调节过程s34中调节了温度的预制件以获得树脂制容器的过程。
44.图10是例示了根据上述实施例的修改例的树脂制容器的制造装置350的示意图。如图10例示,制造装置350是六工作台型的制造装置,其包括:包括第一注射装置362的第一注塑部352;第一温度调节部354;包括第二注射装置363的第二注塑部353;第二温度调节部355;吹塑部356;以及取出部358。在制造装置350中,通过包括旋转盘等的传送装置370沿图中示出的箭头方向传送预制件和树脂制容器,并根据上述制造过程对预制件和树脂制容器进行成型。作为工作台的具体模式,可以适当地采用上述实施例的模式。
45.尽管在上述实施例中描述了包括在内层材料成型过程s1之后执行外层材料成型过程s2的两步注塑过程的模式,但是可以采用在外层材料首先成型之后成型内层材料的模式。下文中,将参照图11描述本实施例的修改例。图11是例示了根据上述实施例的修改例的预制件210的注塑模式的剖视图。
46.下文中,将基于成型预制件210并由预制件210成型树脂制容器的制造装置来描述本修改例。根据本修改例的制造装置除了注塑部的构造不同以外,与上述实施例和修改例中描述的制造装置150和制造装置350类似。本修改例的制造装置的注塑部包括成型外层材料280的第一模具250和在外层材料280的内侧上成型内层材料260的第二模具270(参见图11)。
47.第一模具250包括第一腔模具252、第一注射芯模具254和颈部模具256。第一模具250被构造为通过将再生材料浇注到由这些模具的模具夹紧限定的空腔中来形成外层材料280。再生材料从第一热流道模具259供应,并经由第一浇口258浇注到空腔中。
48.第一热流道模具259具有阀销259a,其可在再生材料流经的流路中朝向第一浇口258移动。阀销259a被构造为在再生材料被填充到空腔中之后通过第一浇口258移动到靠近第一注射芯模具254的位置。因此,在外层材料280的底部的中央部分中形成厚度小于周边部分的厚度的薄膜部281。
49.第二模具270包括第二腔模具272、第二注射芯模具255和颈部模具256。颈部模具256是在保持通过第一模具250成型的外层材料280的状态下移动到第二模具270的位置的共用颈部模具。第二注射芯模具255的芯直径比第一注射芯模具254的芯直径小内层材料260的层厚度。另外,第二腔模具272的俯视图中的凹部的尺寸(直径)与第一腔模具252的俯
视图中的凹部的尺寸(直径)相同。第二模具270被构造为通过将原生材料浇注到由这些模具的模具夹紧限定的空腔中而在由第一模具250成型的外层材料280的内侧上形成内层材料260。
50.原生材料从第二热流道模具279供应,并经由第二浇口278浇注到空腔中。在外层材料280中形成的薄膜部281由于原生材料的流动而破裂,由此原生材料浇注到空腔中。当外层材料280的薄膜部281破裂时,在预制件210的底部218(外层材料280的底部)形成开口部282。浇注到空腔中的原生材料经由开口部282填充到空腔中。
51.在本修改例中,采用了两步注塑过程,其中,执行由第一模具250成型外层材料280的外层材料成型过程,其后执行由第二模具270在外层材料280的内侧成型内层材料260的内层材料成型过程。在本修改例中,预制件210被成型为使得再生材料与通过两步注塑过程形成的预制件210的总重量的重量比以及主体部中的外层的厚度相对于内层的厚度的比类似于上述实施例中的那些。另外,在本修改例中,容器被成型为使得由预制件210形成的容器的主体部的雾度与上述实施例中的雾度类似。
52.在本修改例中,与在内层材料成型过程s1之后执行外层材料成型过程s2的方法(参见图7)不同,在第一注塑过程中首先成型的外层材料280(再生材料)中没有形成浇口痕迹。因此,进一步降低了原生材料和再生材料在预制件210的底部区域中熔融并混合的可能性,并且可以更可靠地抑制底部的变白(结晶等)。在第二注塑过程中注射的内层材料260(原生材料)的注射量小于在第一注塑过程中注射的外层材料280(再生材料)的注射量,并且首先成型的外层材料280的再加热程度也降低。因此,在原生材料与再生材料之间的界面中发生变白(结晶)的现象不太可能发生。因此,在本修改例中,可以更容易地制造和提供可以形成具有两层结构且具有高透明度的树脂制容器的预制件210。
53.本修改例优选通过图9的制造方法和图10的制造装置350来进行。这是因为由再生材料制成的预制件210的厚外层材料280除了在第一注塑过程s31(第一模具250)中冷却之外,还可在第一温度调节过程s32(第一温度调节部354)中另外冷却(进行后冷却)。因此,可以充分冷却预制件210的厚外层材料280,以降低其温度,由此可以抑制由于在第二注塑过程s33(第二模具270)中注射原生材料而导致的外层材料280的温度升高(再加热)。因此,可以进一步减轻预制件210的变白,并且可以制造具有较低雾度值的容器。实施例
54.下文中,将描述本实施例的示例。注意,本发明的技术范围不限于本示例。本发明的技术范围由请求保护范围或其等同范围限定。
55.通过使用本实施例中描述的制造装置150并且改变在预制件的注塑中使用的树脂材料,进行示例1、示例2、示例3的具有两层结构的树脂制容器的制造试验。
56.示例1的容器由具有图1所示结构的预制件形成,该预制件包括由pet原生材料(bk-2180,三菱化学(mitsubishi chemical)有限公司制造)制成的内层和由pet再生材料(lcg-1810,墨西哥pet one有限公司制造)制成的外层。原生材料与总重量的重量比为38%,再生材料与总重量的重量比为62%。预制件主体部中的内层厚度是1.8mm,预制件主体部中的外层厚度是2.98mm。
57.示例2的容器由具有图1所示结构的预制件形成,该预制件包括由原生材料和再生材料的混合材料(由三菱化学有限公司制造的bk-2180和墨西哥pet one有限公司制造的
lcg-1810的混合物)制成的内层和外层,其中再生材料占总重量的比例为30%。原生材料与总重量的重量比为70%。预制件主体部中的内层厚度是1.8mm,预制件主体部中的外层厚度是2.98mm。
58.示例3的容器由具有图1所示结构的预制件形成,该预制件包括由再生材料(lcg-1810,墨西哥pet one有限公司制造)制成的内层和外层。预制件主体部中的内层厚度是1.8mm,预制件主体部中的外层厚度是2.98mm。
59.使用雾度计(ndh-300,日本电色工业(nippon denshoku industries)株式会社制造)测量示例1至3的容器的主体部的雾度。通过选择示例1至3的容器的主体部的任意10个部分进行测量而得到的值的平均值分别为1.74%、1.75%和2.69%。当通过将主体部的厚度设定为0.5mm来进行转换时,示例1至3中的雾度值分别是1.36%、1.49%和2.13%。发现在示例1和2的容器中,雾度低于其中仅使用再生材料的示例3的容器的雾度,并且透明度良好。另外,发现即使示例1的容器中的再生材料的使用比率高于示例2的容器,示例1的容器也表现出与示例2的容器相当的雾度值,并且示例1的容器在具有高回收率的同时具有优异的透明度。
60.本发明并不限于上述实施例,并且可以适当地修改或改进。上述实施例中的部件的材料、形状、尺寸、数值、形式、数量、布置位置等是可选的,并且不受限制,只要能够实现本发明即可。
61.例如,尽管在上述实施例中描述了原生材料和再生材料使用pet树脂作为基材的模式,但是也可以使用以pe树脂、pp树脂等作为基材的材料。然而,在本实施例的模式中,pet树脂是优选的。
62.下文中,将列举从上述实施例及其修改例中提取的方面。【1】一种预制件,包括:开口部;主体部;以及底部,预制件具有两层结构,其中,主体部和底部包括由原生材料制成的内层和由再生材料制成的外层,其中,再生材料与预制件的总重量的重量比为50重量%以上,其中,主体部中的外层的厚度与内层的厚度的比为1.5以上,并且其中,由预制件成型的容器的主体部的雾度为1.8%以下。【2】根据【1】的预制件,其中,底部中的内层的浇口痕迹的高度小于底部中的外层的厚度。【3】一种用于制造预制件的制造方法,预制件包括开口部、主体部以及底部,预制件具有两层结构,其中,主体部和底部包括由原生材料制成的内层和由再生材料制成的外层,制造方法包括:第一注塑过程,将原生材料或再生材料注射到第一模具中,以注塑内层材料或外层材料;以及第二注塑过程,将在第一注塑过程中成型的内层材料或外层材料容纳在第二模具中,并将再生材料注射到内层材料的外侧以注塑外层材料,或者将原生材料注射到外
层材料的内侧以注塑内层材料,其中,内层材料和外层材料被成型为使得再生材料与预制件的总重量的重量比为50重量%以上,并且主体部中的外层的厚度与内层的厚度的比为1.5以上。【4】根据【3】的用于制造预制件的制造方法,其中,第一注塑过程是将原生材料注射到第一模具中以注塑内层材料的内层材料成型过程,并且其中,第二注塑过程是将内层材料容纳在第二模具中并将再生材料注射到内层材料的外侧以注塑外层材料的外层材料成型过程。【5】根据【4】的用于制造预制件的制造方法,其中,第一模具中的注射原生材料的浇口的长度小于预制件的底部中的外层的厚度。【6】根据【3】的用于制造预制件的制造方法,其中,第一注塑过程是将再生材料注射到第一模具中以注塑外层材料的外层材料成型过程,并且其中,第二注塑过程是将外层材料容纳在第二模具中并将原生材料注射到外层材料的内侧以注塑内层材料的内层材料成型过程。【7】根据【3】至【6】中任一项的用于制造预制件的制造方法,还包括:冷却过程,在第二注塑过程之后冷却预制件。【8】根据【7】的用于制造预制件的制造方法,其中,在冷却过程中,将预制件容纳在腔模具中,使空气引入构件与预制件气密地接触,以及通过将空气从空气引入构件的空气吹送口送入预制件中并且将空气从空气引入构件的排出口排出到预制件的外部来冷却预制件。【9】根据【7】的用于制造预制件的制造方法,其中,在冷却过程中,通过将预制件夹在腔模具与芯模具之间来冷却预制件。【10】根据【3】至【6】中任一项的用于制造预制件的制造方法,还包括:第一冷却过程,在第一注塑过程之后冷却内层材料或外层材料;以及第二冷却过程,在第二注塑过程之后冷却预制件。【11】根据【10】的用于制造预制件的制造方法,其中,在第一冷却过程和第二冷却过程中,将预制件容纳在腔模具中,使空气引入构件与预制件气密地接触,以及通过将空气从空气引入构件的空气吹送口送入预制件中并且将空气从空气引入构件的排出口排出到预制件的外部来冷却预制件。【12】根据【10】的用于制造预制件的制造方法,其中,在第一冷却过程和第二冷却过程中,通过将预制件夹在腔模具与芯模具之间来冷却预制件。【13】一种树脂制容器,包括:
开口部;主体部;以及底部,树脂制容器具有两层结构,其中,主体部和底部包括由原生材料制成的内层和由再生材料制成的外层,其中,再生材料与树脂制容器的总重量的重量比为50重量%以上,其中,主体部中的外层的厚度与内层的厚度的比为1.5以上,并且其中,主体部的雾度为1.8%以下。【14】一种用于制造树脂制容器的制造方法,制造方法包括:注塑预制件的注塑过程,预制件包括开口部、主体部以及底部,预制件具有两层结构,其中,主体部和底部包括由原生材料制成的内层和由再生材料制成的外层;温度调节过程,调节预制件的温度;以及吹塑过程,对预制件进行吹塑,以成型树脂制容器,其中,注塑过程包括:第一注塑过程,将原生材料或再生材料注射到第一模具中,以注塑内层材料或外层材料;以及第二注塑过程,将在第一注塑过程中成型的内层材料或外层材料容纳在第二模具中,并将再生材料注射到内层材料的外侧以注塑外层材料,或者将原生材料注射到外层材料的内侧以注塑内层材料,并且其中,在注塑过程中,内层材料和外层材料被成型为使得再生材料与预制件的总重量的重量比为50重量%以上,并且主体部中的外层的厚度与内层的厚度的比为1.5以上。【15】根据【14】的用于制造树脂制容器的制造方法,其中,第一注塑过程是将原生材料注射到第一模具中以注塑内层材料的内层材料成型过程,并且其中,第二注塑过程是将内层材料容纳在第二模具中并将再生材料注射到内层材料的外侧以注塑外层材料的外层材料成型过程。【16】根据【15】的用于制造树脂制容器的制造方法,其中,第一模具中的注射原生材料的浇口的长度小于预制件的底部中的外层的厚度。【17】根据【14】的用于制造树脂制容器的制造方法,其中,第一注塑过程是将再生材料注射到第一模具中以注塑外层材料的外层材料成型过程,并且其中,第二注塑过程是将外层材料容纳在第二模具中并将原生材料注射到外层材料的内侧以注塑内层材料的内层材料成型过程。【18】根据【14】至【17】中任一项的用于制造树脂制容器的制造方法,其中,在温度调节过程中冷却在注塑过程中成型的预制件。【19】根据【18】的用于制造树脂制容器的制造方法,其中,在温度调节过程中,
将预制件容纳在腔模具中,使空气引入构件与预制件气密地接触,以及通过将空气从空气引入构件的空气吹送口送入预制件中并且将空气从空气引入构件的排出口排出到预制件的外部来冷却预制件。【20】根据【18】的用于制造树脂制容器的制造方法,其中,在温度调节过程中,通过将预制件夹在腔模具与芯模具之间来冷却预制件。【21】根据【14】至【17】中任一项的用于制造树脂制容器的制造方法,其中,温度调节过程包括第一温度调节过程和第二温度调节过程,其中,第一温度调节过程是在第一注塑过程之后冷却内层材料或外层材料的过程;并且其中,第二温度调节过程是在第二注塑过程之后冷却预制件的过程。【22】根据【21】的用于制造树脂制容器的制造方法,其中,在第一冷却过程和第二冷却过程中,将预制件容纳在腔模具中,使空气引入构件与预制件气密地接触,以及通过将空气从空气引入构件的空气吹送口送入预制件中并且将空气从空气引入构件的排出口排出到预制件的外部来冷却预制件。【23】根据【21】的用于树脂制容器的制造方法,其中,在第一冷却过程和第二冷却过程中,通过将预制件夹在腔模具与芯模具之间来冷却预制件。
63.本技术基于申请日为2019年6月12日、序列号为2019-109558的日本专利申请,其全部内容以引用的方式结合于此。进一步地,完全结合在此列出的所有参考文献。附图标记列表
64.10、210:预制件,12:开口部,14:颈部,16:主体部,18、218:底部,22:内层,24:外层,22a、24a:浇口痕迹,30:容器,36:主体部,38:底部,42:内层,44:外层,50、250:第一模具,52、252:第一腔模具,54、254:第一注射芯模具,55、255:第二注射芯模具,56、256:颈部模具,58、258:第一浇口,59、259:第一热流道模具,59a、259a:阀销,60、260:内层材料、70、270:第二模具,72、272:第二腔模具,78、278:第二浇口,79、279:第二热流道模具,80、280:外层材料,282:开口部,100:第三腔模具,110:空气引入构件,120:第四腔模具,130:芯模具,150、350:制造装置,152:注塑部,154:温度调节部,156、356:吹塑部,158、358:取出部,352:第一注塑部,353:第二注塑部,354:第一温度调节部,355:第二温度调节部,362:第一注射装置,363:第二注射装置,370:传送装置。