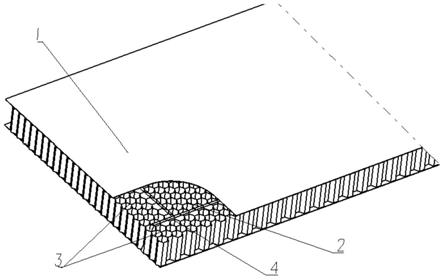
1.本发明属于航空复合材料制造技术领域,涉及一种蜂窝夹层结构制造方法,具体涉及一种大厚度高倒角蜂窝夹层结构制造工艺方法。
背景技术:2.在民用飞机翼身整流罩的制备过程中,由于蜂窝夹层结构具有比强度高,比模量高,重量轻等特点,是飞机复合材料制件通常采用的结构形式。随着飞机整流罩对于刚度和减重要求的提高,飞机翼身整流罩设计为大厚度高倒角蜂窝夹层结构形式,该结构形式在减重的同时,尽可能增加整流罩刚度,减小整流罩在飞行过程中的形变量。
3.由于蜂窝倒角较大,并且在局部区域蜂窝倒角大于60
°
。若选择阴模进行大厚度高倒角蜂窝夹层结构成型,则在蜂窝斜面区较难确认其施加足够的成型压力,同时制备出的夹层结构外型面平整度较差。由于阳模制备的大厚度高倒角复合材料制件气动面为贴膜面,其表面平整性较好,为此,选择阳模成型。大厚度高倒角蜂窝夹层结构基于减重要求,蜂窝容重较低,其在成型过程中,蜂窝斜面容易发生凹陷,变形,收缩滑移现象。具体是大厚度高倒角蜂窝夹层结构在成型过程中,蜂窝斜面区受压,由于蜂窝侧向抗压强度小于预浸料成型工艺压力,在夹层结构成型过程中,发生蜂窝侧向凹陷、滑移变形现象,导致蜂窝夹层结构变形,蒙皮材料发生褶皱和弯曲,限制了蜂窝夹层结构的应用。
4.采用常用的预浸料拴系等方式无法解决上述蜂窝的凹陷变形。
技术实现要素:5.为了解决上述问题,本发明提供了一种大厚度高倒角蜂窝夹层结构制造工艺方法,在大厚度蜂窝夹层结构蜂窝边缘采用高密度蜂窝作为保护,同时采用稳定化措施,增强大厚度高倒角蜂窝抗滑移和变形能力,然后制备蜂窝夹层结构,解决大厚度高倒角蜂窝夹层结构制备过程中斜面区蜂窝的塌陷,变形滑移现象。
6.本发明的技术方案是:
7.一种大厚度高倒角蜂窝夹层结构制造工艺方法,在大厚度蜂窝边缘区一定范围内,将大厚度蜂窝更换成大厚度高密度蜂窝,使用胶膜和预浸料使加工后的大厚度蜂窝稳定化后,对蜂窝斜面进行高倒角加工。
8.进一步的,具体包括以下步骤:
9.步骤一,根据需要的蜂窝芯层大小,将大厚度蜂窝切割为去掉边缘部分的大小,边缘部分大于需倒角部分;
10.步骤二,切割与边缘大小一致的大厚度高密度蜂窝,将切割好的大厚度蜂窝与大厚度高密度蜂窝进行拼接;
11.步骤三,拼接完成后对拼接蜂窝的上下表面铺贴胶膜和预浸料进行稳定化;
12.步骤四,对稳定化后的拼接蜂窝的进行高倒角加工;
13.步骤五,将完成高倒角加工的拼接蜂窝作为夹芯,铺贴胶膜和蒙皮预浸料,将夹芯
外表面全部覆盖,固化成型,得到大厚度高倒角蜂窝夹层结构。
14.进一步的,步骤二中,根据大厚度蜂窝需倒角的范围,切割出1至4块大厚度高密度蜂窝,每块大厚度高密度蜂窝的厚度与大厚度蜂窝相同,大厚度高密度蜂窝的宽度稍大于需要倒角的范围,大厚度高密度蜂窝的长度确保能够与大厚度蜂窝拼接出需要的蜂窝芯层长度。
15.进一步的,步骤一中,将大厚度蜂窝切割为外径小于需要的蜂窝芯层边缘倒角范围的结构,步骤二中,对大厚度高密度蜂窝进行切割,得到一个大厚度高密度蜂窝环,环内径大小形状与切割好的大厚度蜂窝外径匹配,环外径与需要的蜂窝芯层外径匹配。
16.进一步的,步骤二中,采用发泡胶膜胶接或者填充料填充拼接的方式拼接大厚度蜂窝和大厚度高密度蜂窝。
17.进一步的,大厚度高密度蜂窝的容重至少是大厚度蜂窝容重的两倍。
18.进一步的,步骤三的稳定化方法是:采用烘箱或热压罐法进行固化,固化温度为120℃~190℃,固化时间为:90min~240min,固化压力为:0.05mpa~0.4mpa。
19.进一步的,步骤五的固化成型方法是:采用烘箱或热压罐法进行固化,固化温度为120℃~190℃,固化时间为:90min~240min,固化压力为:0.3mpa~0.4mpa。
20.本发明的优点是:
21.1、本发明采用蜂窝高倒角斜面区更换为高密度蜂窝,并将高密度蜂窝与夹芯低密度蜂窝共同稳定化,其共同加强了高密度蜂窝与低密度蜂窝的侧向强度,同时增加了蜂窝高倒角区的抗压能力,解决了大厚度蜂窝在蜂窝夹层成型过程中的蜂窝斜面区的凹陷、滑移问题;
22.2、本发明详细设计了大厚度蜂窝和大厚度高密度蜂窝的要求,能够满足本发明目的的需要;
23.3、本发明的方法详细,细致,容易实现,并且制造成本低。
附图说明
24.图1是本发明大厚度高倒角蜂窝稳定化示意图;
25.图2是本发明大厚度高倒角稳定化后蜂窝倒角示意图;
26.图3是本发明大厚度高倒角蜂窝夹层结构成型示意图;
27.其中,1—稳定化预浸料,2—大厚度蜂窝,3—大厚度高密度蜂窝,4—拼接处,5—高倒角,6—上层蒙皮预浸料,7—下层蒙皮预浸料。
具体实施方式
28.本部分是本发明的实施例,用于解释和说明本发明的技术方案。
29.一种大厚度高倒角蜂窝夹层结构制造工艺方法,在大厚度蜂窝边缘区一定范围内,将大厚度蜂窝更换成大厚度高密度蜂窝,使用胶膜和预浸料使加工后的大厚度蜂窝稳定化后,对蜂窝斜面进行高倒角加工。
30.具体包括以下步骤:
31.步骤一,根据需要的蜂窝芯层大小,将大厚度蜂窝切割为去掉边缘部分的大小,边缘部分大于需倒角部分;
32.步骤二,切割与边缘大小一致的大厚度高密度蜂窝,将切割好的大厚度蜂窝与大厚度高密度蜂窝进行拼接;
33.步骤三,拼接完成后对拼接蜂窝的上下表面铺贴胶膜和预浸料进行稳定化;
34.步骤四,对稳定化后的拼接蜂窝的进行高倒角加工;
35.步骤五,将完成高倒角加工的拼接蜂窝作为夹芯,铺贴胶膜和蒙皮预浸料,将夹芯外表面全部覆盖,固化成型,得到大厚度高倒角蜂窝夹层结构。
36.步骤二中,根据大厚度蜂窝需倒角的范围,切割出1至4块大厚度高密度蜂窝,每块大厚度高密度蜂窝的厚度与大厚度蜂窝相同,大厚度高密度蜂窝的宽度稍大于需要倒角的范围,大厚度高密度蜂窝的长度确保能够与大厚度蜂窝拼接出需要的蜂窝芯层长度。
37.步骤一中,将大厚度蜂窝切割为外径小于需要的蜂窝芯层边缘倒角范围的结构,步骤二中,对大厚度高密度蜂窝进行切割,得到一个大厚度高密度蜂窝环,环内径大小形状与切割好的大厚度蜂窝外径匹配,环外径与需要的蜂窝芯层外径匹配。
38.步骤二中,采用发泡胶膜胶接或者填充料填充拼接的方式拼接大厚度蜂窝和大厚度高密度蜂窝。
39.大厚度高密度蜂窝的容重至少是大厚度蜂窝容重的两倍。
40.步骤三的稳定化方法是:采用烘箱或热压罐法进行固化,固化温度为120℃~190℃,固化时间为:90min~240min,固化压力为:0.05mpa~0.4mpa。
41.步骤五的固化成型方法是:采用烘箱或热压罐法进行固化,固化温度为120℃~190℃,固化时间为:90min~240min,固化压力为:0.3mpa~0.4mpa。
42.本发明的原理如下:
43.本发明提供一种大厚度高倒角蜂窝夹层结构成型工艺方法,在大厚度高倒角蜂窝夹层结构成型过程中,由于减重要求,采用低密度蜂窝作为夹芯材料,同时为了增加夹层结构刚性,蜂窝斜面区倒角较高,一般大于60
°
以上,低密度蜂窝斜面区无法抵抗预浸料的固化压力,在蜂窝斜面区发生凹陷,收缩变形情况。在大厚度高倒角蜂窝夹层结构成型过程中,蜂窝发生变形或者塌陷而产生滑移显现,导致大厚度蜂窝夹层结构在成型过程中,产生变形或塌陷等缺陷。
44.在大厚度高倒角蜂窝夹层结构成型过程中,高倒角蜂窝斜面区产生凹陷现象,其无法采用拴系等方法消除,为此,本发明采用蜂窝高倒角斜面区更换为高密度蜂窝,并将高密度蜂窝与夹芯低密度蜂窝共同稳定化,其共同加强了高密度蜂窝与低密度蜂窝的侧向强度,同时增加了蜂窝高倒角区的抗压能力,解决了大厚度蜂窝在蜂窝夹层成型过程中的蜂窝斜面区的凹陷、滑移问题。
45.举一个实际例子:
46.大厚度高倒角蜂窝夹层结构为:蜂窝区尺寸为650mm
×
1000mm,蜂窝厚度为60mm,蜂窝边缘区倒角为70
°
。大厚度蜂窝夹层结构的制造过程如下所述:
47.步骤一,将60mm厚度的容重为48g/cm3蜂窝裁剪尺寸为540mm
×
890mm,同时将60mm厚度容重为128g/cm3的蜂窝裁剪为:2块890mm
×
55mm和2块550mm
×
55mm;采用发泡胶膜进行高密度蜂窝和中间低密度蜂窝拼接,在拼接后的蜂窝上下表面分别铺贴一层胶膜和一层预浸料,然后进热压罐进行固化,固化工艺按照预浸料的固化工艺条件;
48.步骤二,将固化后蜂窝边缘进行加工,产生蜂窝斜面倒角,蜂窝斜面倒角角度为
70
°
。
49.步骤三,在模具表面铺贴蜂窝夹层结构下蒙皮预浸料,然后铺贴一层胶膜,将蜂窝放置在胶膜表面,然后铺贴一层上表面胶膜和上蒙皮预浸料,预浸料铺贴完毕后,放置隔离膜,透气毡辅助材料,采用真空袋膜和密封胶条密封后,送入热压罐进行夹层结构固化,其固化工艺按照预浸料的固化工艺条件。