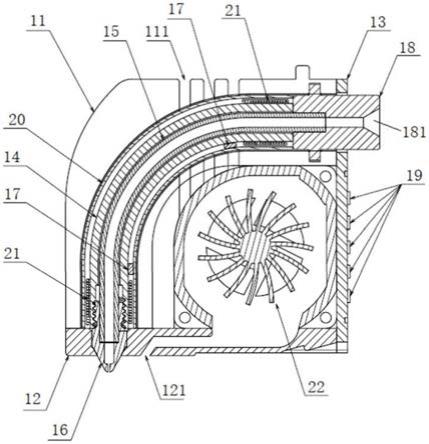
1.本实用新型涉及增材制造技术领域,尤其是涉及一种用于增材制造的材料挤出装置。
背景技术:2.熔融层积增材制造是将热熔性材料经过加热融化,通过数位控制的细微喷嘴在立体空间内将材料挤喷出来并层层堆积成型的一种制造方式。
3.专利cn201720466635.x提供了一种3d打印机喷头及3d打印机,该变径喷头将变径喷头1、加热块2、进料柔性喉管3、风扇4和散热主体5等各个模块组合拼装而成,如此设置使得整体结构的零件较松散且体积较大。
技术实现要素:4.本实用新型的目的在于提供一种用于增材制造的材料挤出装置,以缓解现有技术中存在的熔融层积增材制造设备的零件较松散且体积较大的技术问题。
5.本实用新型提供一种用于增材制造的材料挤出装置,包括:壳体、均设置于所述壳体内的挤出组件、加热组件以及散热组件;所述挤出组件包括金属管、套装于所述金属管内的柔性喉管和用于挤出熔融材料的变径喷头,所述金属管的中心线为圆弧线;所述加热组件用于为所述金属管提供热源;所述金属管的外侧设有温度传感器,所述温度传感器、所述加热组件和所述散热组件电连接,用于对所述金属管的温度形成闭环控制。
6.进一步的,所述金属管与所述变径喷头相对的一端设有进料接头;所述进料接头的进料方向与所述变径喷头的出料方向相垂直设置。
7.进一步的,所述壳体包括外壳、下压板和侧压板;所述外壳设置为两块且相平行扣合连接,所述下压板扣合连接于所述外壳的底端;所述侧压板扣合连接于所述外壳的侧面;所述下压板与所述侧压板邻近设置;所述变径喷头具有锥状结构,所述锥状结构配合所述下压板上的锥形孔,压装于所述下压板;所述进料接头穿设所述侧压板并与所述外壳通过凹凸结构卡接。
8.进一步的,所述温度传感器、所述加热组件和所述散热组件的电源集成设置为插头;所述插头设置于所述侧压板。
9.进一步的,所述变径喷头的内端夹设于所述金属管与所述柔性喉管之间的环形空间内。
10.进一步的,所述变径喷头的内孔为台阶孔;所述台阶孔的内孔段与所述柔性喉管间隙配合,用于固定所述柔性喉管的出料端;所述台阶孔的外孔段为细微丝状孔,用于喷出熔融材料。
11.进一步的,所述变径喷头的外壁与所述金属管的内壁螺纹连接;或者,所述变径喷头与所述金属管一体成型设置。
12.进一步的,所述进料接头的内端与所述柔性喉管间隙配合,用于固定所述柔性喉
管的进料端,所述进料接头的外端设有进料锥孔,用于热熔性材料的进入;所述进料锥孔与所述柔性喉管连通。
13.进一步的,所述加热组件包括保温结构和电热丝;所述保温结构包覆于所述金属管,所述电热丝缠绕于所述金属管,且位于所述金属管与所述保温结构之间。
14.进一步的,所述散热组件包括风扇;所述壳体上设有进风口和出风口,所述进风口与所述风扇的风道入口相通,所述出风口与所述风扇的风道出口相通;所述出风口朝向所述变径喷头设置。
15.有益效果:
16.本实用新型提供的用于增材制造的材料挤出装置,柔性喉管套装于金属管内,加热组件用于为金属管提供热源,同时金属管的外侧设有温度传感器,温度传感器与散热组件电连接,在具体工作时,加热组件、温度传感器和散热组件三者配合可以将柔性喉管内的热熔性材料加热至所需温度,使所需温度的熔融材料通过变径喷头挤出;再者,金属管的中心线为圆弧线,如此设置,可相对增加热熔性材料在柔性喉管内的时间,提高熔融效果,同时,还可合理利用壳体内的空间,有利于减小整体体积,使得整体更加简洁紧凑,外形小巧。
附图说明
17.为了更清楚地说明本实用新型具体实施方式或现有技术中的技术方案,下面将对具体实施方式或现有技术描述中所需要使用的附图作简单地介绍,显而易见地,下面描述中的附图是本实用新型的一些实施方式,对于本领域普通技术人员来讲,在不付出创造性劳动的前提下,还可以根据这些附图获得其他的附图。
18.图1为现有技术;
19.图2为本实用新型实施例提供的用于增材制造的材料挤出装置的剖视图。
20.图标:
[0021]1‑
喷嘴;2
‑
加热块;3
‑
进料喉;4
‑
风扇;5
‑
散热主体;
[0022]
11
‑
外壳;12
‑
下压板;13
‑
侧压板;14
‑
金属管;15
‑
柔性喉管;16
‑
变径喷头;17
‑
温度传感器;18
‑
进料接头;19
‑
插头;20
‑
保温结构;21
‑
电热丝;22
‑
风扇;
[0023]
111
‑
进风口;121
‑
出风口;
[0024]
181
‑
进料锥孔。
具体实施方式
[0025]
应当理解,此处所描述的具体实施例仅仅用以解释本实用新型,并不用于限定本实用新型。
[0026]
下面结合附图,对本实用新型的一些实施方式作详细说明。在不冲突的情况下,下述的实施例及实施例中的特征可以相互组合。
[0027]
本实施例提供的一种用于增材制造的材料挤出装置,参照图2,该材料挤出装置包括壳体、均设置于壳体内的挤出组件、加热组件以及散热组件;挤出组件包括金属管14、套装于金属管14内的柔性喉管15和用于挤出熔融材料的变径喷头16,金属管14的中心线为圆弧线;加热组件用于为金属管14提供热源;金属管14的外侧设有温度传感器17,温度传感器17、加热组件和散热组件电连接,用于对金属管14的温度形成闭环控制。
[0028]
本实施例提供的用于增材制造的材料挤出装置,柔性喉管15套装于金属管14内,加热组件用于为金属管14提供热源,同时金属管14的外侧设有温度传感器17,温度传感器17与散热组件电连接,在具体工作时,加热组件、温度传感器17和散热组件三者配合可以将柔性喉管15内的热熔性材料加热至所需温度,使所需温度的熔融材料通过变径喷头16挤出。
[0029]
再者,金属管14的中心线为圆弧线,如此设置,可相对增加热熔性材料在柔性喉管15内的时间,提高熔融效果;同时,还可合理利用壳体内的空间,有利于减小整体体积,使得整体更加简洁紧凑,外形小巧。
[0030]
本实施例中的金属管14可采用铜管,当然,也可以使用其他导热材质替代,只要能够实现导热的材质均在本实用新型的保护范围之内。
[0031]
可选的,柔性喉管15优先选用特氟龙材质,同时可由硅胶、聚酰亚胺等其他任何耐高温材质替代。
[0032]
其中,温度传感器17优选为玻璃封装热敏电阻,可由热电偶或其他类型温度传感器17替代,并且可固定于金属管14的任何位置,并且数量可不做限制。
[0033]
例如,温度传感器17可以设置为一个;或者设置为多个,多个温度传感器17的平均值作为金属管14的实际温度值。
[0034]
本实施例中,金属管14的中心线为圆弧线,该圆弧线的弧形以及设置形式可以有多种。对于立方结构来说,在对角线处设置为圆弧形的金属管14的长度最大。
[0035]
具体的,金属管14与变径喷头16相对的一端设有进料接头18;进料接头18的进料方向与变径喷头16的出料方向相垂直设置,如此设置,可实现金属管14长度的最大化,如此设置,可进一步增加热熔性材料在柔性喉管15内的时间,进一步提高熔融效果。
[0036]
本实施例中,金属管14为90
°
圆弧弯折设置。
[0037]
其他实施例中,不限于为90
°
,其他角度均可,以配合实际应用需求。
[0038]
本实施例中,壳体可以为多种结构,例如由多块板件焊接而成;或者,多块板件通过紧固件连接而成。
[0039]
在本技术的一种实施方式中,壳体包括外壳11、下压板12和侧压板13;外壳11设置为两块且相平行扣合连接,下压板12扣合连接于外壳11的底端;侧压板13扣合连接于外壳11的侧面;下压板12与侧压板13邻近设置;变径喷头16具有锥状结构,锥状结构配合下压板12上的锥形孔,压装于下压板12;进料接头18穿设侧压板13并与外壳11通过凹凸结构卡接。
[0040]
以上设置可便于壳体内部部件的拆装,同时,变径喷头16的锥状结构配合下压板12上的锥形孔,有利于对变径喷头16进行定位安装,防止变径喷头16在纵向发生偏移;同样地,进料接头18穿设侧压板13并与外壳11通过凹凸结构卡接,有利于对进料接头18进行定位安装,防止进料接头18在横向发生偏移。
[0041]
具体的,进料接头18的外壁上设有凸台,外壳11上设有与凸台相适配的凹槽。
[0042]
作为一种变形,还可在进料接头18的外壁上设置凹槽,在外壳11上设有与凹槽相适配的凸台。
[0043]
请继续参照图2,温度传感器17、加热组件和散热组件的电源集成设置为插头19;插头19设置于侧压板13,如此设置,便于位于壳体内部的温度传感器17、加热组件和散热组件连通电源,并且操作起来也比较方便。
[0044]
本实施例中,变径喷头16的内端夹设于金属管14与柔性喉管15之间的环形空间内,如此设置,可使变径喷头16的安装更加牢靠。
[0045]
需要说明的是,变径喷头16由熔融材料进入的一端为内端,相应的一端为外端。
[0046]
进一步的,变径喷头16的内孔为台阶孔;台阶孔的内孔段与柔性喉管15间隙配合,用于固定柔性喉管15的出料端;台阶孔的外孔段为细微丝状孔,用于喷出熔融材料。
[0047]
本实施例中,变径喷头16的外壁与金属管14的内壁螺纹连接。
[0048]
其他实施例中,变径喷头16与金属管14一体成型设置。
[0049]
请继续参照图1,进料接头18的内端与柔性喉管15间隙配合,用于固定柔性喉管15的进料端,进料接头18的外端设有进料锥孔181,用于热熔性材料的进入;进料锥孔181与柔性喉管15连通,如此设置,在实现柔性喉管15稳定安装的基础上,还便于热熔性材料进入柔性喉管15。
[0050]
在本技术的一种实施例中,加热组件包括保温结构20和电热丝21;保温结构20包覆于金属管14,电热丝21缠绕于金属管14,且位于金属管14与保温结构20之间。
[0051]
金属管14的外表面由保温结构20包覆,使热量不易散发,节约能耗并使金属管14的温度易于控制。
[0052]
柔性喉管15由不沾材料制成,嵌套于金属管14的内部,金属管14的外表面被电热丝21缠绕,通过热传导为金属管14内嵌套的柔性喉管15内的热熔性材料提供热源。
[0053]
其中,保温结构20可以为隔热材质制成的隔热管。可选的,保温结构20优先选用特氟龙材质,同时可由硅胶、聚酰亚胺等其他任何耐高温材质替代。
[0054]
可选的,电热丝21优选为镍铬发热丝,可由镍铁铬铝、钨丝等任意其他合金电阻丝替代;同时,电热丝21可以在金属管14的任何位置进行缠绕,并且缠绕长度、层数、厚度可以不做限制。
[0055]
其中,为调整加热效果,可通过改变电热丝21的数量或通过调整缠绕金属管14的疏密程度、缠绕长度、层数、厚度等方式。
[0056]
本实施例中,散热组件包括风扇22;壳体上设有进风口111和出风口121,进风口111与风扇22的风道入口相通,出风口121与风扇22的风道出口相通;出风口121朝向变径喷头16设置。
[0057]
具体的,气流受风扇22工作所形成的负压从进风口111进入壳体,并首先为金属管14提供散热,然后气流进入风扇22后从出风口121喷出,为工作状态的变径喷头16挤喷出的熔融材料降温。
[0058]
该用于增材制造的材料挤出装置的一种工作过程为:
[0059]
热熔性材料由进料接头18的进料锥孔181进入柔性喉管15;
[0060]
电热丝21和风扇22均启动;
[0061]
温度传感器17实时采集金属管14的温度信息,并将该温度信息发送给控制器,控制器接收该温度信息并与预设温度值进行比较,当金属管14的温度高于预设温度值时,控制器将控制风扇22工作,并增加风扇22的转速,加快散热;反之,控制器将控制风扇22工作并减小风扇22的转速,减缓散热;或者,控制器关闭风扇22;
[0062]
热熔性材料被加热呈熔融状态,并沿柔性喉管15逐渐从变径喷头16处挤出。
[0063]
需要说明的是,在该装置使用前,可预先启动电热丝21,对金属管14进行预热,以
确保熔融效果。
[0064]
可选的,风扇22可采用涡轮风扇。
[0065]
综合以上,该用于增材制造的材料挤出装置具有以下优势:
[0066]
1、用于增材制造的材料挤出装置集成加热组件、材料熔融挤出组件和散热组件于一体,并考虑到尽可能提高材料挤出装置的壳体的内部空间使用率,节约纵向空间,通过对金属管14呈90度的圆角导向设置,使熔融材料可以由水平方向进入柔性喉管15内,经过加热的柔性喉管15开始软化,并逐渐升温熔融,最后纵向挤出,整体结构简洁紧凑,外形小巧。
[0067]
2、为了保证安装结构合理、易于控制批量生产精度和装配误差,本实施例中的变径喷头16由下压板12的锥形孔压装于壳体内,控制纵向装配公差,进料接头18通过侧压板13压装于壳体内,控制横向装配公差,这样只要控制生产制造中各零部件的加工精度,即可控制产品的整体精度质量,材料挤出装置作为一个整体,可直接替换安装,无需客户自行调教。
[0068]
3、本实施例将挤出组件、加热组件和散热组件集成安装于壳内,降低甚至避免了烫伤和机械伤害风险。
[0069]
最后应说明的是:以上各实施例仅用以说明本实用新型的技术方案,而非对其限制;尽管参照前述各实施例对本实用新型进行了详细的说明,本领域的普通技术人员应当理解:其依然可以对前述各实施例所记载的技术方案进行修改,或者对其中部分或者全部技术特征进行等同替换;而这些修改或者替换,并不使相应技术方案的本质脱离本实用新型各实施例技术方案的范围。