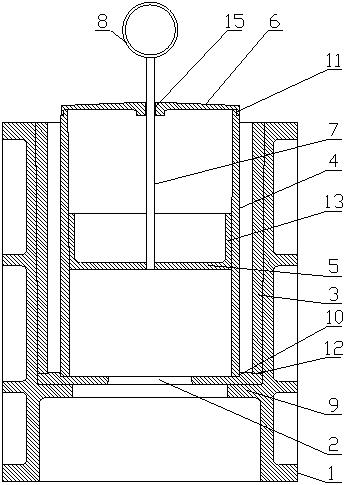
1.本实用新型属于水钻加工技术领域,特别涉及一种抛光滚筒的成型模具。
背景技术:2.水钻是一种非常重要的饰品和服饰的配件,传统的用于水钻的抛光滚筒都是整体形式的圆筒状的抛光轮对水钻的表面进行抛光。
3.现有的水钻加工磨轮,包括圆柱状的碳钢磨轮基体及套设于其外且沿其轴向设置的至少一个抛光滚筒,抛光滚筒为由氧化铈抛光粉、酚醛树脂等烧结而成,其具有使用寿命长、抛光面平整度高等优点,抛光滚筒为圆筒状结构且其与碳钢磨轮基体之间通过树脂胶粘在一起。抛光滚筒可通过如下工艺得到:原料混合、成型、加压、保压和加热固化等,在成型、加压和保压工序中均会用到成型模具,成型模具内具有与抛光滚筒的形状配合的成型模腔。
4.如申请号为cn201920326625 .5的专利公开了一种制备抛光滚筒上抛光圆筒的设备,所述抛光圆筒由定制的定形套制备而成,所述定形套包括内部中空设置的锥筒,所述锥筒上下两端外壁固定设置有连接台,上下连接台之间对称设置有螺纹通孔,在所述下连接台底部还设置有圆形挡板,所述圆形挡板半径不小于所述下连接台外缘所形成的圆形的半径,在圆形挡板中间固定安装有实心的圆锥筒柱,所述圆锥筒柱与所述锥筒同轴设置,所述圆形挡板周线方向上也间隔均匀设置有螺纹孔,上下连接台与所述圆形挡板之间通过螺栓进行紧固。
5.其中,抛光滚筒的制备过程为:将抛光粉、树脂、促进剂和固化剂等混合,加入成型模具中,再在压力机上压铸成型,保压于150℃左右加热固化5小时以上,冷却后进行精加工。
6.对于制备过程来说存在如下问题:需要加压和加热进行成型,设备复杂,能耗好,处理时间长(总时间大于12小时)等缺点;对于较大直径(玻璃珠的直径大于2.5mm)的产品的加工效果不好,容易让产品碎裂和出现裂纹。
7.对于产品来说存在如下问题:使用寿命短,对于加工2.6mm以上的水钻,寿命为20-25天(每天工作22小时以上)。
8.对于成型模具来说存在如下问题:为了脱模,产品通常具有锥度增加后续加工难度,且产品不易脱模。
技术实现要素:9.为了解决前述问题,本实用新型实施例提供了一种抛光滚筒的成型模具,更便于脱模。所述技术方案如下:
10.本实用新型实施例提供了一种抛光滚筒的成型模具,包括模具座1、模具座1内下部的垫板2、模具座1内且位于垫板2上侧的外模3、外模3内且位于垫板2上侧的内模4、内模4内中部的撑板5、内模4上端的压盖6和向下贯穿压盖6并可拆卸地设于撑板5上侧的拉杆7;
所述模具座1、垫板2、外模3、内模4、撑板5和压盖6均与抛光滚筒同轴设置,所述垫板2、外模3和内模4围成成型抛光滚筒的环槽;所述模具座1为圆筒状,其内下部同轴设有支撑环9,其内径由下至上逐渐变大;所述垫板2为圆环状,其置于支撑凸环9上,其外侧与模具座1的内壁间隙配合,其上侧同轴设有与内模4的下端配合的定位孔10;所述外模3为圆筒状,其下端置于垫板2的上侧,其上端与模具座1的上端平齐或较模具座1的上端高,其外壁与模具座1的内壁间隙配合;所述内模4为圆筒状,其由多片圆弧状的瓣片16组合而成,其内径由下至上逐渐变大,其下端插入定位孔10中,其上端较外模3的上端高;所述撑板5为与内模4的内壁中部配合的圆形结构;所述压盖6为与内模4的上端配合且向下敞口的圆盖,其盖设在内模4的上端。
11.进一步地,本实用新型实施例中的内模4的上端同轴设有环形凸台11,所述环形凸台11的直径小于内模4的外径且其与压盖6的内径配合,所述环形凸台11嵌入压盖6的盖口中。
12.其中,本实用新型实施例中的拉杆7为与抛光滚筒同轴设置的圆杆,其下端与撑板5的圆心螺纹连接,其上端设有拉环8。
13.优选地,本实用新型实施例中的压盖6的圆心处设有供拉杆7穿过的通孔15且其顶部由中心向外缘斜向下设置。
14.进一步地,本实用新型实施例中的撑板5的外缘向上翻折形成圆筒状的撑边13,所述撑边13与抛光滚筒同轴设置且其外侧与内模4的内壁中部紧配合。
15.具体地,本实用新型实施例中的内模4由三片瓣片16组成,包括两片大瓣片和一片小瓣片,所述小瓣片的圆心角小于等于60
°
,所述大瓣片的圆心角大于等于120
°
。
16.优选地,本实用新型实施例中的瓣片16的两端包覆有牛皮纸14。
17.本实用新型实施例提供的技术方案带来的有益效果是:本实用新型实施例提供了一种抛光滚筒的成型模具,更便于脱模。
附图说明
18.图1是本实用新型实施例中的抛光滚筒的成型模具的结构示意图;
19.图2是内模的结构示意图;
20.图3是本实用新型实施例提供的抛光滚筒的制备方法的流程图。
21.图中:1模具座、2垫板、3外模、4内模、5撑板、6压盖、7拉杆、8拉环、9支撑凸环、10定位孔、11环形凸台、12圆环槽、13撑边、14牛皮纸、15通孔、16瓣片。
具体实施方式
22.为使本实用新型的目的、技术方案和优点更加清楚,下面将结合附图对本实用新型作进一步地详细描述。
23.实施例1
24.实施例1公开了一种抛光滚筒的制备方法,该方法包括:
25.s101:依次混入805树脂18kg、抛光粉55kg和助剂,助剂包括促进剂0.5kg、固化剂0.4kg、邻苯二甲酸二丁酯0.2kg和硫酸镁1.5kg,室温下搅拌15分钟得到浇注液。
26.s102:在成型模具上涂抹脱模油。
27.s103:将浇注液加入成型模具中,浇注液装满成型模具前对其顶部进行搅拌。
28.s104:浇注完成后,于室温下静置60分钟。
29.s105:将产品和内模4一起从外模3中取出。
30.s106:室温下静置120分钟后将产品与内模4分离。
31.s107:对产品进行精加工。
32.整个加工时间小于8h,易于工厂处理。
33.对产品进行测试:水钻加工的玻璃珠直径为3.0mm,使用时间为35天,水钻表面的粗糙度小于40nm,加工的产品基本无碎裂,无明显裂纹。
34.实施例2
35.实施例2公开了一种抛光滚筒的制备方法,该方法包括:
36.s101:依次混入805树脂20kg、抛光粉54kg和助剂,助剂包括促进剂0.5kg、固化剂0.5kg、邻苯二甲酸二丁酯0.25kg和硫酸镁1.8kg,室温下搅拌18分钟得到浇注液。
37.s102:在成型模具上涂抹脱模油。
38.s103:将浇注液加入成型模具中,浇注液装满成型模具前对其顶部进行搅拌。
39.s104:浇注完成后,于室温下静置60分钟。
40.s105:将产品和内模4一起从外模3中取出。
41.s106:室温下静置110分钟后将产品与内模4分离。
42.s107:对产品进行精加工。
43.整个加工时间小于8h,易于工厂处理。
44.对产品进行测试:水钻加工的玻璃珠直径为2.6mm,使用时间为37天,水钻表面的粗糙度小于40nm,加工的产品基本无碎裂,无明显裂纹。
45.实施例3
46.参见图1和2,实施例3提供了一种抛光滚筒的成型模具,包括模具座1、模具座1内下部的垫板2、模具座1内且位于垫板2上侧的外模3、外模3内且位于垫板2上侧的内模4、内模4内中部的撑板5、内模4上端的压盖6和向下贯穿压盖6并可拆卸地设于撑板5上侧的拉杆7等。模具座1、垫板2、外模3、内模4、撑板5和压盖6均与抛光滚筒同轴设置,垫板2、外模3和内模4围成成型抛光滚筒的环槽。其中,模具座1为圆筒状,其内下部同轴设有支撑环9,其内径由下至上逐渐变大以便于脱模,其内壁光滑。其中,支撑环9为与模具座1同轴设置的圆环,其内径较垫板2的内径大。垫板2为圆环状,其置于支撑凸环9上,其外侧与模具座1的内壁间隙配合,其上侧同轴设有与内模4的下端配合的定位孔10(具体为竖向设置的圆孔,其与垫板2的中心孔构成阶梯孔,以便于顶杆(通常情况下不用,优选通过拉杆7将撑板5分离)穿过以向上顶出撑板5),其内径小于内模4的内径。外模3为圆筒状,其下端置于垫板2的上侧,其上端与模具座1的上端平齐(优选)或较模具座1的上端高以避免浇注液进入外模3与模具座1之间的间隙,其外壁(为上大下小的圆锥)与模具座1的内壁间隙配合,其外壁光滑,其通常情况下不用从模具座1上拆除。内模4为圆筒状,其由多片圆弧状的瓣片16组合而成,其内径由下至上逐渐变大以便于撑板5的放入,其下端插入定位孔10中,其上端较外模3的上端高以避免浇注液进入内模4内。撑板5(直径与内模4的内壁中部的直径相同)为与内模4的内壁中部配合的圆形结构。压盖6为与内模4的上端配合且向下敞口的圆盖,其盖设在内模4的上端。内模4的下端通过定位孔10向内缩紧,其上端通过压盖6向内缩紧,其中部通过
撑板5向外撑开;通过以上三个位置的作用可保证内模4的稳定性。
47.其中,本实用新型实施例中的模具座1的内壁、外模3的外壁和内模4的内壁的锥角均为1
°
。当然,根据需要也可为其他锥度。
48.进一步地,参见图1,本实用新型实施例中的内模4的上端同轴设有环形凸台11(内壁与内模4的内壁平齐),环形凸台11的直径小于内模4的外径且其与压盖6的内径配合,环形凸台11嵌入压盖6的盖口中。
49.其中,参见图1,本实用新型实施例中的拉杆7为与抛光滚筒同轴设置的圆杆,其下端与撑板5的圆心(其上对应设有螺孔)螺纹连接,其上端设有拉环8(具体为圆环,其位于压盖6的上方)。
50.优选地,参见图1,本实用新型实施例中的压盖6的圆心处设有供拉杆7穿过的通孔15(具体为竖向设置的圆孔)且其顶部(最好光滑)由中心向外缘斜向下设置以保证浇注液进入内模4与外模3之间。
51.进一步地,参见图1,本实用新型实施例中的撑板5的外缘向上翻折形成圆筒状的撑边13,撑边13与抛光滚筒同轴设置且其外侧(最好光滑)与内模4的内壁(最好光滑)中部紧配合。
52.具体地,参见图2,本实用新型实施例中的内模4由三片瓣片16组成以便于将内模4从产品中拆出,包括两片大瓣片和一片小瓣片,小瓣片的圆心角小于等于60
°
,大瓣片的圆心角大于等于120
°
。小瓣片与大瓣片接触的两端的端面的角度要保证小瓣片能向内取出。
53.优选地,参见图2,本实用新型实施例中的瓣片16的两端(与大瓣片接触的两端)包覆有牛皮纸14以起密封作用。内模4可由圆钢管切割加工而成。
54.实施例4
55.参见图3,本实用新型实施例提供了一种抛光滚筒的制备方法,该方法包括:
56.s101:按配比依次混入805树脂、抛光粉和助剂,助剂包括促进剂、固化剂、邻苯二甲酸二丁酯和硫酸镁,室温下搅拌10-20分钟得到浇注液。
57.s102:在成型模具(通常为垫板2上侧、外模3内壁和内模4外壁)上涂抹脱模油。
58.s103:将浇注液加入成型模具中,浇注液快装满成型模具前对其顶部进行搅拌,基本装满成型模具时(如浇注液顶部距外模3顶端1cm处停止浇注)将浇注液的顶部抚平。
59.s104:浇注完成后,于室温下静置40-75分钟。
60.s105:将产品和内模4一起从外模3中取出,如果分离困难,将产品、内模4和外模3一起从模具座1中取出。
61.s106:室温下静置100-150分钟后将产品与内模4分离,该过程中,产品会持续发热。
62.s107:对产品进行精加工(包括外圆磨和内圆糙面处理(如加工螺旋线))。
63.具体地,在步骤s103中,拉杆7未固定在撑板5上,通过盖子将压盖6上的通孔15遮蔽。在步骤s105中,将拉杆7安装在撑板5上,通过上拉拉杆7将产品和内模4一起从外模3中取出。若不能将产品和内模4从外模3中取出,通过向上顶压垫板2将产品、内模4和外模3从模具座1中取出。在步骤s106中,通过上拉拉杆7将撑板5和压盖6从内模4分离,先向内拆除小瓣片,再拆除两片大瓣片得到产品。
64.以上所述仅为本实用新型的较佳实施例,并不用以限制本实用新型,凡在本实用
新型的精神和原则之内,所作的任何修改、等同替换、改进等,均应包含在本实用新型的保护范围之内。