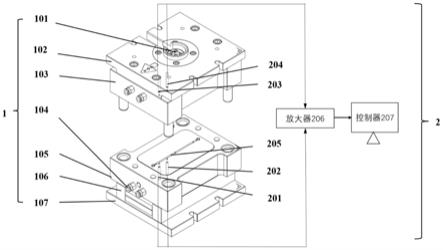
1.本发明涉及微结构注塑成型领域,具体涉及一种具有模内流变在线测量功能的微注塑模具及测控方法。
背景技术:2.注塑制品的生产过程中,聚合物状态参数的变化(温度、压力、粘度等)会影响最终产品表面表面粗糙度、飞边、翘曲、轮廓精度、表面剖面波纹等缺陷,影响产品的质量。在聚合物加工过程中,在线表征技术可对聚合物的状态进行表征,处理后的数据可用于工艺参数调控,对于灵活的生产过程越来越重要。
3.在现有的技术中,细微结构聚合物注塑成型过程中的流变测量主要借助于离线的流变测量技术,只能在脱离聚合物材料真实生产历程情况下测量物料的流变性能。微结构注射成型过程中聚合物材料的流变性能尚不明确,和传统的注塑成型过程中聚合物的状态存在差异。利用离线的流变测量技术无法准确获得传统注塑成型过程在聚合物流变状态,更无法对微结构注塑成型过程中聚合物的流变进行表征。
4.随着微注塑成型机技术的不断进步,目前螺杆或活塞系统的注射速率可达750mm/s,为细微结构注塑制品的流变测量创造了条件,集成细微结构注塑成型过程中聚合物流变状态的在线检测方法,可以为聚合物状态参数的调整提供参考,对于细微结构聚合物注塑成型过程检测调控具有非常重要的作用。有关科研人员采用该优势对微结构注塑成型机喷嘴处的细微结构聚合物的流变性能进行测量,推动了聚合物在线流变表征技术的发展。但模具内聚合物的流变状态与喷嘴处的聚合物仍存在差异,现有技术仍无法直接对实际生产过程中模具内细微结构聚合物的流变性能进行测控,细微结构注塑成型过程聚合物流变状态的在线准确测控仍存在的巨大的挑战。
技术实现要素:5.针对现有的细微结构塑料制品注塑成型过程中的质量缺陷,无法实现细微结构注塑成型过程聚合物流变状态的在线准确测控的不足,本发明提出一种具有模内流变在线测量功能的微注塑模具及测控方法,直接利用微注塑模具中具有圆形截面的流道结构,不占用额外的体积,在实现正常注塑成型功能的同时,可以对模具中聚合物成型过程的流变状态进行实时监测与调控。
6.本发明的目的通过如下的技术方案来实现:
7.一种具有模内流变在线测量功能的微注塑模具,其包括模具组件和流变测量组件;
8.所述模具组件包括从上到下依次设置的进料口、定模座板、定模板、动模板、垫块、动模座板;所述定模板和动模板内部设置有冷却管路;所述定模板、动模板锁模时形成有不少于两个的圆形截面的流道以及连接所述流道端部的产品型腔;所述流道沿进料口镜像排列,且所述流道的长径比l/d大于15;
9.所述流变测量组件包括出口温度传感器、进口温度传感器、出口压力传感器、进口压力传感器、放大器和控制器;所述出口温度传感器和出口压力传感器均布置在所述流道的出口附近,所述进口温度传感器和进口压力传感器布置在所述流道的进口附近;所述出口温度传感器、进口温度传感器、出口压力传感器、进口压力传感器均和所述放大器连接,所述放大器和控制器连接;
10.所述放大器用于接收传感器检测的信号,并将其放大后传入所述控制器;
11.所述控制器用于对所述放大器的信号进行处理计算,获得模具内聚合物的实时粘度;并对实时粘度进行分析,作为对注塑机塑化单元中聚合物的温度进行调节的参考;
12.进一步的,所述出口压力传感器、进口压力传感器均设置在所述流道的内壁面;所述出口温度传感器、进口温度传感器均设置在靠近所述流道的壁面的位置;
13.进一步的,所述出口温度传感器和出口压力传感器为温压一体化传感器,所述进口压力传感器、进口温度传感器也为温压一体化传感器;
14.本发明的另一目的在于提供一种利用上述任一方案所述具有模内流变在线测量装置的测控方法,该方法具体如下:
15.(1)选取所述流道的长径比大于10的一段作为测量流道,并将出口温度传感器、出口压力传感器布置在所述测量流道的下游端,将所述进口温度传感器、进口压力传感器布置在所述测量流道的上游端;
16.(2)聚合物熔体从进料口注入,经过所述流道填充满产品型腔;所述出口温度传感器、出口压力传感器、进口温度传感器、进口压力传感器实时测量聚合物熔体的进出口压力和温度,信号经所述放大器放大后传入所述控制器,所述控制器通过如下方式计算聚合物熔体的实时粘度差δη:
[0017][0018][0019]
其中,ηa为聚合物熔体的实时粘度,单位为pa
·
s;η为基于cross-wlf方程获得的聚合物加工设定粘度,单位为pa
·
s;τw为壁面剪切应力,单位为mpa;为壁面剪切速率,单位为s-1
;δp为测量通道的进出口之间的压力降,单位为pa;r为测量通道的半径,单位为m;l为测量通道的长度,单位为m;为表观剪切速率,为管壁处牛顿型流体的剪切速率,单位为s-1
;tn为第n次合模时塑化单元中聚合物熔体的温度,单位为℃;t为当前聚合物熔体的温度,单位为℃;δt为注塑机塑化单元的调节温度,单位为℃;可利用塑化加热套的功率调节;δ为设定的粘度阈值,单位为pa
·
s;η0为零剪切粘度,单位为pa
·
s,为剪切速率,单位为s-1
,τ
*
为向剪切变稀转变时的临界剪切应力,单位为mpa。
[0020]
(4)利用实时粘度差控制注塑机塑化单元的温度,进而控制模具内聚合物熔体的实时粘度。
[0021]
本发明的有益效果是:
[0022]
(1)本发明所提供的具有模内流变在线测量功能的微注塑模具及测控方法,将流
变测量组件集成于微注塑模具之中,实时检测通过微注塑模具流道中聚合物粘度,方便高效、结构紧凑、体积小,节省安装空间;
[0023]
(2)选取流道的一段作为测量通道,考虑了聚合物在圆形测量通道中粘弹性的变化,确保聚合物在流道中充分发展,测量精度较高。
[0024]
(3)用聚合物熔体在线流变状态为指标,利用多次合模时塑化单元的温度来调控检测微注塑模具内聚合物熔体的流变状态,动态调整塑化加热套的加热功率,进而调整聚合物的状态,降低细微结构塑料制品注塑成型过程中的缺陷。
[0025]
(4)相比与传统的塑料制品的生产过程,本发明可以实现聚合物熔体流变监测控制,实现塑料注塑制品的高质量快速生产。
附图说明
[0026]
图1为本发明微注塑模具的立体结构图;
[0027]
图2为本发明所涉及微注塑模具内流道示意图;
[0028]
图3为本发明涉及的数字电路处理方框图;
[0029]
图中:模具包括模具组件1、流变测量组件2、加热套3、进料口101、定模座板102、定模板103、冷却管路104、动模板105、垫块106、动模座板107、出口温度传感器201、进口温度传感器202、出口压力传感器203、进口压力传感器204、流道205、测量流道2051、放大器206、控制器207。
具体实施方式
[0030]
下面根据附图和优选实施例详细描述本发明,本发明的目的和效果将变得更加明白,应当理解,此处所描述的具体实施例仅仅用以解释本发明,并不用于限定本发明。
[0031]
如附图1所示,在本实施例中,一种具有模内流变在线测量功能的微注塑模具,包括模具组件1和流变测量组件2。
[0032]
模具组件包括从上到下依次设置的进料口101、定模座板102、定模板103、动模板105、垫块106、动模座板107。定模板103和动模板105内部设置有冷却管路104;定模板103、动模板105锁模时形成有少于两个的圆形截面的流道205以及连接流道端部的产品型腔;流道沿进料口101镜像排列,且流道207的长径比l/d大于15。流道205的数量根据需要来设定,不少于两个都可以。
[0033]
流变测量组件包括出口温度传感器201、进口温度传感器202、出口压力传感器203、进口压力传感器204、放大器206和控制器207。出口温度传感器201和出口压力传感器203均布置在流道205的出口附近,进口温度传感器202和进口压力传感器204布置在流道207的进口附近。出口温度传感器201、进口温度传感器202、出口压力传感器203、进口压力传感器204均和放大器206连接,放大器206和控制器207连接。放大器206用于接收传感器检测的信号,并将其放大后传入所述控制器;控制器207用于对放大器206的信号进行处理计算,获得模具内聚合物的实时粘度;并对实时粘度进行分析,作为对注塑机塑化单元中聚合物的温度进行调节的参考。
[0034]
优选地,出口温度传感器201和出口压力传感器203为温压一体化传感器,能够同时测量温度和压力。进口压力传感器204、进口温度传感器202也为温压一体化传感器。
[0035]
本发明的细微结构注塑成型过程聚合物流变性能的在线监测方法是通过若干传感器实现微注塑模具内聚合物成型过程的粘度测量的。如图2所示,聚合物熔体通过浇口进入流道205后充满产品型腔,选取流道205中流体流动稳定的一段作为测量通道2051,测量通道2051具有圆形截面的结构形式,通道的长径比l/d严格控制大于10。为了保证流变测量的准确性,防止聚合物流体的弹性形变造成测量误差,测量通道2051侧壁安装的温度传感器202和压力传感器204位于流道205的上游,测量通道2051侧壁安装的出口温度传感器201和出口压力传感器203位于流道205的下游。由进口压力传感器204检测测量通道2051进口处管壁聚合物熔体的压力p1,由出口压力传感器203检测测量通道2051出口处管壁聚合物熔体的压力p2,根据进出口压力计算进出口压差δp。
[0036]
如图3所示,进口温度传感器202、进口压力传感器204、出口温度传感器201、出口压力传感器203将检测到的信号经过放大器206放大,放大后的信号经过a/d转换后发送到控制器207中。控制器207接收来自进口温度传感器202、进口压力传感器204、出口温度传感器201、出口压力传感器203的信号并进行处理计算、显示实时粘度。控制器207对计算得到的实时粘度进行分析,结合cross-wlf方程,并利用算法处理,分析该聚合物熔体所处的状态,利用多次合模时塑化单元的温度来调控检测微注塑模具内聚合物熔体的流变状态,计算模具内聚合物熔体的实时粘度,当实时粘度与设定粘度之间的差值不大于设定的阈值时,则认为聚合物熔体粘度达到合理的范围,实现聚合物模内流变状态的在线控制,确保聚合物达到最优的流动状态,降低微注塑成型过程中产品的缺陷,实现细微结构注塑制品的快速高效成型。
[0037]
在本实施例中,上述聚合物模内流变的在线测控方法,可以采用如下测控步骤:
[0038]
主要利用圆管剪切应力的计算公式和weissenberg-rabinowtsich剪切速率公式来对微注塑模具内聚合物流变状态进行计算。
[0039]
剪切应力τw计算公式如下:
[0040][0041]
剪切速率计算公式如下:
[0042][0043]
式中:δp为测量通道之间的压力降,单位为pa;r为测量通道的半径,单位为m;l为测量通道的长度,单位为m;为表观剪切速率,为管壁处牛顿型流体的剪切速率,单位为s-1
。
[0044]
首先将流经测量通道的任何聚合物熔体视为牛顿型流体,通过压力传感器测量得到的压力降计算管壁处物料承受的剪切应力τw,测量出熔体的体积流量或者平均流速后,可求得管壁处的表观剪切速率
[0045]
根据具体聚合物的性质,即管壁处的剪切应力τw和表观剪切速率之间的本构关系或者测量得到的的关系曲线,即可求出聚合物熔体流经测量通道时在管壁处的真实剪切速率
[0046]
由管壁的剪切应力τw和剪切速率得到某一聚合物物料在模具中的粘度
[0047]
聚合物粘度状态的调控基于cross-wlf方程,建立起热塑性材料粘度的温度、剪切速率和压力的相关性,具体表达公式如下:
[0048][0049]
其中:
[0050]
a2=a3+d3+p
[0051]
其中η为聚合物熔体的粘度,单位为pa
·
s;η0为零剪切粘度,单位为pa
·
s;为剪切速率,单位为s-1
;τ
*
为向剪切变稀转变时的临界剪切应力,单位为mpa;t为温度,单位为℃;t
*
为玻璃化转变温度,单位为℃;p为压力,单位为pa;d1、a1、a3和d3是拟合数据系数。
[0052]
通过调整塑化单元的加热功率来对模具内聚合物流变状态进行调整,即控制模具内聚合物熔体的实时粘度:
[0053][0054][0055]
其中:δη为当前测量粘度ηa与聚合物加工设定粘度η之间的差值,单位为pa
·
s;tn为前n次合模时塑化单元中聚合物熔体的温度,单位为℃;t为当前聚合物熔体的温度,单位为℃;δt为调节温度,可利用塑化加热套的功率调节,单位为℃;δ为设定的粘度阈值,单位为pa
·
s。
[0056]
考虑到调控过程产生的延迟,当前温度利用n次合模时塑化单元熔体温度来近似,进而调控检测微注塑模具内聚合物熔体的流变状态,计算模具内聚合物熔体的实时粘度,当实时粘度与设定粘度之间的差值不大于设定的阈值时,则认为聚合物熔体粘度已达到合理的范围。
[0057]
本发明中用于粘度计算的方法,选取流道中流体流动稳定的一部分流道作为测量通道,避免聚合物粘弹性的变化对测量带来的误差,确保聚合物在流道中充分发展,因此测量结果必然具有较高的准确性。通过该测量方法,无需复杂昂贵的毛细管流变仪,也可以对细微结构注塑成型过程中模具内聚合物的流变性能进行表征,检测聚合物在模具型腔中粘度对于产品的影响。
[0058]
本领域普通技术人员可以理解,以上所述仅为发明的优选实例而已,并不用于限制发明,尽管参照前述实例对发明进行了详细的说明,对于本领域的技术人员来说,其依然可以对前述各实例记载的技术方案进行修改,或者对其中部分技术特征进行等同替换。凡在发明的精神和原则之内,所做的修改、等同替换等均应包含在发明的保护范围之内。