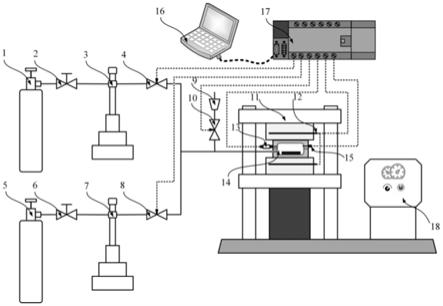
1.本发明属于聚合物微孔材料成型技术领域,具体涉及一种聚合物超临界流体混合发泡系统及方法。
背景技术:2.公开该背景技术部分的信息仅仅旨在增加对本发明的总体背景的理解,而不必然被视为承认或以任何形式暗示该信息构成已经成为本领域一般技术人员所公知的现有技术。
3.聚合物微孔材料主要通过发泡工艺获得内部泡孔结构,使用超临界流体作为物理发泡剂的聚合物微孔发泡工艺因具有发泡动力足、发泡倍率高、泡孔稳定性好、且无化学物质残留、环境友好等优势,受到了业界的广泛关注。
4.目前常用的超临界流体包括超临界二氧化碳、超临界氮气等,微孔发泡技术方法主要有间歇发泡、挤出发泡以及注塑发泡等。由于目前聚合物超临界流体发泡工艺大都只使用一种超临界流体发泡剂,导致在聚合物微孔材料泡孔结构的综合调控方面具有本质性不足:如单一的超临界二氧化碳所制备的聚合物多孔材料发泡倍率高但泡孔密度低、尺寸大,又如单一的超临界氮气所制备的聚合物多孔材料泡孔密度高、尺寸小,但发泡倍率相对较低。少数利用两种超临界气体混合后进行发泡,但所用方法与单一超临界流体发泡的方法基本相同,并未真正的实现混合发泡,尚不能实现聚合物微孔材料泡孔结构的调节和控制。
技术实现要素:5.针对上述现有技术中存在的问题,本发明的目的是提供一种聚合物超临界流体混合发泡系统及方法。
6.为了解决以上技术问题,本发明的技术方案为:
7.第一方面,一种聚合物超临界流体混合发泡系统,包括,超临界流体气源ⅰ、超临界流体气源ⅱ、气源ⅰ增压控制泵、气源ⅱ增压控制泵、第一高压电磁阀、第二高压电磁阀、反应釜、泄压管路,超临界流体气源ⅰ依次连接气源ⅰ增压控制泵、第一高压电磁阀,然后与反应釜的进气口连接,超临界流体气源ⅱ依次连接气源ⅱ增压控制泵、第二高压电磁阀,然后与反应釜的进气口连接,反应釜的进气口与泄压管路连接。
8.在聚合物超临界流体微孔发泡过程中,由于所用超临界流体的种类和性质不同,所制备的聚合物多孔材料的泡孔结构及性能也不相同。以常用的超临界二氧化碳和超临界氮气为例,对大多数聚合物材料而言,超临界二氧化碳溶解度高、扩散快,所制备的聚合物多孔材料发泡倍率高但泡孔密度低、尺寸大;而超临界氮气溶解度低、扩散慢,所制备的聚合物多孔材料泡孔密度高、尺寸小,但发泡倍率相对较低。由于目前聚合物超临界流体发泡工艺大都只使用一种超临界流体发泡剂,导致在聚合物微孔材料泡孔结构的综合调控方面具有本质性不足。
9.本发明的混合发泡系统及方法,能够精确控制超临界流体的注入分压、混合总压、饱和时间和发泡温度,配合下游反应釜的机械控制,建立稳定可靠的聚合物超临界流体混合发泡工艺,实现了聚合物微孔材料泡孔结构的可控可调。
10.本发明的混合发泡系统及方法建立了聚合物超临界流体混合发泡工艺,通过两种超临界流体发泡剂的不同分压配比,协同发挥两种超临界流体发泡剂的溶解和扩散特性,进而实现聚合物微孔材料泡孔结构的可控可调。制备的聚合物微孔材料在具有较高发泡倍率的同时内部泡孔尺寸小、密度高。
11.超临界流体气源ⅰ、气源ⅰ增压控制泵、第一高压电磁阀组成了气源ⅰ的进气管路,超临界流体气源ⅱ、气源ⅱ增压控制泵、第二高压电磁阀组成了气源ⅱ的进气管路。气源ⅰ的进气管路、气源ⅱ的进气管路出口分别连接反应釜。两种气源分别单独控制。增压控制泵用于控制气源的气压,高压电磁阀控制气源的流量。增压控制泵优选为高压注射泵。
12.在本发明的一些实施方式中,还包括气源ⅰ截止阀和气源ⅱ截止阀,气源ⅰ截止阀连接在超临界流体气源ⅰ与气源ⅰ增压控制泵之间,气源ⅱ截止阀连接在超临界流体气源ⅱ与气源ⅱ增压控制泵之间。截止阀控制气源的输出的启停。
13.在本发明的一些实施方式中,泄压管路上设置第三高压电磁阀;进一步,泄压管路上设置消音器。第三高压电磁阀用于控制气体的卸放。
14.在本发明的一些实施方式中,还包括液压机,液压机包括上工作台和下工作台,反应釜配合设置在上工作台和下工作台之间。液压机包括液压控制装置,所述液压机、反应釜以及液压控制装置组成聚合物超临界流体发泡机械系统,其中,所述反应釜置于液压机的上下工作台之间,所述液压控制装置与液压机连接。
15.在本发明的一些实施方式中,还包括电热棒和温度传感器,电热棒埋设在液压机的上工作台和下工作台中,温度传感器与反应釜连接。温度传感器优选为热电偶。
16.在本发明的一些实施方式中,还包括压力传感器,压力传感器与反应釜连接。
17.在本发明的一些实施方式中,还包括控制器,控制器分别与第一高压电磁阀、第二高压电磁阀、第三高压电磁阀、温度传感器、压力传感器、液压机、电热棒电信号连接。
18.在本发明的一些实施方式中,所述反应釜优选为可以开合的盘式反应釜,内部直径优选为50~100mm,内部腔体高度优选为5~15mm。
19.第二方面,利用上述第一方面所述的系统进行聚合物超临界流体混合发泡方法,所述方法为:
20.控制器根据发泡工艺参数,加热反应釜,当到达发泡温度后进入精确控温;
21.在温度达到和进入保温后,控制器输出信号打开第一高压电磁阀,向反应釜中注入超临界流体气源ⅰ,当反应釜的内部压力超临界流体气源ⅰ的分压后,控制器输出信号关闭第一高压电磁阀,完成超临界氮气发泡剂的注入;
22.控制器输出信号打开第二高压电磁阀,向反应釜中注入超临界流体气源ⅱ,当反应釜内部压力达到设定的超临界流体混合总压后,控制器输出信号关闭第二高压电磁阀,完成超临界流体气源ⅱ发泡剂的注入;
23.反应釜的内部的聚合物坯料开始进入混合发泡饱和阶段,当达到设定的饱和时间后,打开泄压管路,对反应釜进行快速泄压并诱导聚合物坯料发泡。
24.在本发明的一些实施方式中,超临界流体气源ⅰ和超临界流体气源ⅱ为二氧化碳、
氮气或氩气。
25.在本发明的一些实施方式中,当反应釜的内部压力超临界流体气源ⅰ的分压后,延迟1-5s,然后关闭第一高压电磁阀。
26.在本发明的一些实施方式中,当反应釜的内部压力超临界流体气源ⅱ的分压后,延迟1-5s,然后关闭第二高压电磁阀。
27.在本发明的一些实施方式中,液压机的工作台压紧力为30~100kn。
28.在本发明的一些实施方式中,聚合物坯料为片状、块状、条状或其他几何尺寸外形的聚合物制品。
29.在本发明的一些实施方式中,聚合物坯料为聚丙烯(pp)、聚苯乙烯(ps)、热塑性聚氨酯弹性体(tpu)、聚对苯二甲酸-己二酸丁二醇酯(pbat)等。进一步的,由于pbat材料的分子链为直链结构,分子量相对较小,熔体强度低,结晶速率快,导致pbat材料发泡困难、发泡倍率低,同时发泡后的泡沫材料存在明显收缩现象且收缩率较大。通过本发明的发泡方法,有效解决了现有pbat泡沫材料发泡倍率低、泡孔尺寸不均、收缩率大且难以调控等技术问题,实现了大倍率低收缩pbat微孔泡沫材料的可控制备。
30.在本发明的一些实施方式中,气源ⅰ增压控制泵和气源ⅱ增压控制泵的压力范围为0-35mpa。
31.在本发明的一些实施方式中,超临界流体ⅰ分压优选为4~20mpa,超临界流体混合总压优选为5~30mpa;进一步,超临界流体ⅰ分压优选为4~10mpa,超临界流体混合总压优选为10~20mpa。
32.在本发明的一些实施方式中,发泡饱和温度为60~120℃,饱和时间为300~3600s。所述发泡饱和温度在本发明中又称为发泡温度。
33.在本发明的一些实施方式中,第一高压电磁阀、第二高压电磁阀、第三高压电磁阀的工作压力优选为0~40mpa。
34.本发明一个或多个技术方案具有以下有益效果:
35.(1)通过计算机、plc控制器和相关阀门管路的协同控制,实现了聚合物超临界流体发泡过程中两种超临界流体发泡剂的混合注入,克服了传统聚合物超临界流体发泡系统只能注入一种超临界发泡剂的不足。
36.(2)利用超临界流体混合发泡系统,建立了聚合物超临界流体混合发泡工艺,通过两种超临界流体发泡剂的不同分压配比,协同发挥两种超临界流体发泡剂的溶解和扩散特性,进而实现聚合物微孔材料泡孔结构的可控可调。
37.(3)提供的聚合物超临界流体混合发泡系统及工艺方法稳定可靠,自动化程度和精度高,安全性好。
附图说明
38.构成本发明的一部分的说明书附图用来提供对本技术的进一步理解,本发明的示意性实施例及其说明用于解释本发明,并不构成对本发明的不当限定。
39.图1为聚合物超临界流体混合发泡系统的结构示意图。
40.图2为对比例1单一超临界二氧化碳发泡剂制备的pp微孔材料内部泡孔结构sem图。
41.图3为对比例2单一超临界氮气发泡剂制备的pp微孔材料内部泡孔结构sem图。
42.图4为实施例2混合发泡剂制备的pp微孔材料内部泡孔结构sem图。
43.图5为实施例3混合发泡剂制备的pp微孔材料内部泡孔结构sem图。
44.图6为本发明实施例4制备的pbat微孔材料内部泡孔结构sem图。
45.图7为本发明对比例3制备的pbat微孔材料内部泡孔结构sem图。
46.图8为本发明对比例4制备的pbat微孔材料内部泡孔结构sem图。
47.图9为本发明实施例4、对比例3、对比例4制备的pbat微孔材料发泡倍率对比图(初始时刻)。
48.图10为本发明实施例4、对比例3、对比例4制备的pbat微孔材料发泡倍率随时间变化曲线图。
49.图1中,1、超临界流体气源ⅰ;2、气源ⅰ截止阀;3、气源ⅰ增压控制泵;4、第一高压电磁阀;5、超临界流体气源ⅱ;6、气源ⅱ截止阀;7、气源ⅱ增压控制泵;8、第二高压电磁阀;9、消音器;10、第三高压电磁阀;11、液压机;12、电热棒;13、压力传感器;14、反应釜;15、温度传感器;16、计算机;17、plc控制器;18、液压控制装置。
具体实施方式
50.应该指出,以下详细说明都是例示性的,旨在对本发明提供进一步的说明。除非另有指明,本文使用的所有技术和科学术语具有与本发明所属技术领域的普通技术人员通常理解的相同含义。
51.需要注意的是,这里所使用的术语仅是为了描述具体实施方式,而非意图限制根据本技术的示例性实施方式。如在这里所使用的,除非上下文另外明确指出,否则单数形式也意图包括复数形式,此外,还应当理解的是,当在本说明书中使用术语“包含”和/或“包括”时,其指明存在特征、步骤、操作、器件、组件和/或它们的组合。下面结合实施例对本发明进一步说明
52.实施例1
53.聚合物超临界流体混合发泡系统,包括:瓶装氮气1、瓶装氮气截止阀2、瓶装氮气增压控制泵3、第一高压电磁阀4、瓶装二氧化碳5、瓶装二氧化碳截止阀6、瓶装二氧化碳增压控制泵7、第二高压电磁阀8、消音器9、第三高压电磁阀10、液压机11、电热棒12、压力传感器13、反应釜14、温度传感器15、计算机16、plc控制器17、液压控制装置18。
54.其中,所述瓶装氮气1、瓶装氮气截止阀2、瓶装氮气增压控制泵3、第一高压电磁阀4顺序连接组成超临界氮气增压管路,瓶装二氧化碳5、瓶装二氧化碳截止阀6、瓶装二氧化碳增压控制泵7、第二高压电磁阀8顺序连接组成超临界二氧化碳增压管路;所述第一高压电磁阀4出口与第二高压电磁阀8出口管路合并后与反应釜14连接组成超临界流体混合注入管路;所述第三高压电磁阀10、消音器9与合并后的超临界流体混合注入管路连接组成泄压气路。
55.其中,所述第一高压电磁阀4、第二高压电磁阀8、第三高压电磁阀10、压力传感器13、温度传感器15、电热棒12通过线缆与plc控制器17连接组成超临界流体混合发泡控制系统;所述plc控制器17与计算机16连接并进行交互。
56.其中,所述液压机11、反应釜14以及液压控制装置18组成聚合物超临界流体发泡
机械系统,其中,所述反应釜14置于液压机11的上下工作台之间,所述液压控制装置18与液压机11连接。
57.其中,所述电热棒12埋设于液压机11上下工作台内部,用以加热工作台和反应釜14;所述压力传感器13、温度传感器15分别安装在反应釜14的两侧,用以测量反应釜14的内部压力和温度。
58.实施例2
59.(1)聚合物坯料发泡前准备:所述聚合物超临界流体混合发泡系统启动前,将聚合物坯料(聚丙烯pp)放入反应釜14中,后将反应釜14放置于液压机11工作台上,通过液压控制装置18操作液压机11上下工作台闭合并压紧反应釜14。
60.按照聚合物超临界流体混合发泡工艺,设定气源ⅰ增压控制泵3输出压力为超临界流体ⅰ分压,设定气源ⅱ增压控制泵7输出压力为超临界流体混合总压,启动气源ⅰ增压控制泵3和气源ⅱ增压控制泵7。
61.(2)超临界流体混合发泡剂注入:启动系统,在计算机界面设定聚合物超临界流体混合发泡工艺参数:超临界流体ⅰ分压,超临界流体混合总压、发泡温度、饱和时间,点击“开始”。plc控制器17接收到发泡工艺参数后,接通电热棒12开始加热,直到温度传感器15检测到的温度达到发泡温度后,进入精确保温。
62.在温度达到和进入保温后,plc控制器17输出信号打开第一高压电磁阀4,向反应釜14中注入超临界氮气,当压力传感器13检测到的反应釜14内部压力达到设定的超临界流体ⅰ分压(4mpa)后,延迟2s,plc控制器17输出信号关闭第一高压电磁阀4,完成超临界氮气发泡剂的注入。
63.关闭第一高压电磁阀4后,plc控制器17输出信号打开第二高压电磁阀8,向反应釜14中注入超临界二氧化碳,当压力传感器13检测到的反应釜14内部压力达到设定的超临界流体混合总压(12mpa)后,延迟2s,plc控制器17输出信号关闭第二高压电磁阀8,完成超临界二氧化碳发泡剂的注入。
64.(3)聚合物坯料饱和与发泡:关闭第二高压电磁阀8后,反应釜14内的聚合物坯料进入混合发泡饱和阶段,plc控制器17进入饱和计时,直到时间达到设定的饱和时间。饱和时间达到后,pcl控制器17输出信号打开第三高压电磁阀10,对反应釜14进行快速泄压并诱导聚合物坯料发泡。
65.泄压完成后,plc控制器17输出信号,关闭第三高压电磁阀14,关闭保温,提示发泡完成,并等待下一循环。
66.(4)聚合物微孔材料取出:通过液压控制装置18操作液压机11上下工作台开启,取下反应釜14,冷却后打开并取出制备的聚合物微孔材料,放入新的坯料,进入下一工艺循环。
67.实施例3
68.相比于实施例2,超临界流体ⅰ分压为4mpa,超临界流体混合总压为12mpa。其它方法步骤与实施例2相同。
69.对比例1
70.相比于实施例2,注入单一超临界二氧化碳发泡剂,没有注入超临界流体ⅰ,超临界流体混合总压为12mpa。其它方法步骤与实施例2相同。具体步骤如下:
71.(1)聚合物坯料发泡前准备:所述聚合物超临界流体混合发泡系统启动前,将聚合物坯料放入反应釜14中,后将反应釜14放置于液压机11工作台上,通过液压控制装置18操作液压机11上下工作台闭合并压紧反应釜14。
72.按照聚合物超临界流体混合发泡工艺,设定气源ⅱ增压控制泵7输出压力为超临界流体混合总压,启动气源ⅱ增压控制泵7。
73.(2)超临界流体混合发泡剂注入:启动系统,在计算机界面设定聚合物超临界流体混合发泡工艺参数:超临界流体混合总压、发泡温度、饱和时间,点击“开始”。plc控制器17接收到发泡工艺参数后,接通电热棒12开始加热,直到温度传感器15检测到的温度达到发泡温度后,进入精确保温。
74.在温度达到和进入保温后,plc控制器17输出信号打开第二高压电磁阀8,向反应釜14中注入超临界二氧化碳,当压力传感器13检测到的反应釜14内部压力达到设定的超临界流体混合总压(12mpa)后,延迟2s,plc控制器17输出信号关闭第二高压电磁阀8,完成超临界二氧化碳发泡剂的注入。
75.(3)聚合物坯料饱和与发泡:关闭第二高压电磁阀8后,反应釜14内的聚合物坯料进入混合发泡饱和阶段,plc控制器17进入饱和计时,直到时间达到设定的饱和时间。饱和时间达到后,pcl控制器17输出信号打开第三高压电磁阀10,对反应釜14进行快速泄压并诱导聚合物坯料发泡。
76.泄压完成后,plc控制器17输出信号,关闭第三高压电磁阀14,关闭保温,提示发泡完成,并等待下一循环。
77.(4)聚合物微孔材料取出:通过液压控制装置18操作液压机11上下工作台开启,取下反应釜14,冷却后打开并取出制备的聚合物微孔材料,放入新的坯料,进入下一工艺循环。
78.对比例2
79.相比于实施例2,注入单一超临界氮气发泡剂,没有注入二氧化碳发泡剂,超临界流体混合总压为12mpa。其它方法步骤与实施例2相同。
80.实施例2-3和对比例1-2制备聚合物微孔材料的主要工艺参数如表1所示:
81.表1 实施例2-3和对比例1-2的主要工艺参数
[0082][0083]
实施例2-3和对比例1-2制备的聚合物微孔材料内部泡孔结构如图2-图5所示,可以看出:单一超临界二氧化碳发泡剂(超临界流体ⅰ分压为0mpa)制备的pp微孔材料发泡倍率高,但内部泡孔尺寸大、密度小(图2);单一超临界氮气发泡剂(超临界流体ⅰ分压为12mpa)制备的pp微孔材料内部泡孔尺寸小、密度大,但发泡倍率较小(图3);超临界流体混
合发泡工艺(超临界流体ⅰ分压分别为:4mpa,实施例2;实施例3,8mpa)制备的pp微孔材料的发泡倍率高,同时其内部泡孔尺寸小、密度高,泡孔结构较单一超临界流体发泡有明显改善(图4、图5,图4为实施例2,图5为实施例3)。
[0084]
实施例4
[0085]
一种聚合物超临界流体混合发泡方法,所用原料为pbat,牌号ecoflex c1200,密度为1.26g/cm3(iso 1183),熔体流动指数为3.8g/10min(iso 1133);所用发泡剂为纯度99.9%的超临界co2和超临界n2,将烘干后的pbat粒料加入双螺杆挤出机,经熔融挤出后制得直径3.5mm,长25mm的条形坯料;
[0086]
发泡方法为:与实施例2的区别为:发泡饱和温度为110℃,超临界流体ⅰ为氮气,超临界流体ⅰ分压为8mpa,超临界流体ⅱ为二氧化碳,总压为12mpa,饱和时间为720s。得到pbat微孔泡沫材料。
[0087]
对比例3
[0088]
为比较本发明方法制备的pbat微孔泡沫材料的发泡效果,选择与实施例4相同条件下的单一超临界co2间歇发泡制备的pbat泡沫材料做为对比例3。
[0089]
一种超临界co2间歇发泡制备pbat微孔泡沫材料制备方法,所用原料为pbat,牌号ecoflex c1200,密度为1.26g/cm3(iso 1183),熔体流动指数为3.8g/10min(iso1133);所用发泡剂为纯度99.9%的超临界co2,将烘干后的pbat粒料加入双螺杆挤出机,经熔融挤出后制得直径3.5mm,长25mm的条形坯料。
[0090]
发泡方法:与实施例4的方法区别为:不注入超临界流体ⅰ,直接超临界流体ⅱ,及二氧化碳,达到总压。其它步骤与实施例4相同,得到pbat微孔泡沫材料。
[0091]
对比例4
[0092]
为比较本发明方法制备的pbat微孔泡沫材料的发泡效果,选择与实施例1相同条件下的单一超临界n2间歇发泡制备的pbat泡沫材料做为对比例2。
[0093]
一种超临界n2间歇发泡制备pbat微孔泡沫材料制备方法,所用原料为pbat,牌号ecoflex c1200,密度为1.26g/cm3(iso 1183),熔体流动指数为3.8g/10min(iso 1133);所用发泡剂为纯度99.9%的超临界n2,将烘干后的pbat粒料加入双螺杆挤出机,经熔融挤出后制得直径3.5mm,长25mm的条形坯料。
[0094]
发泡方法:与实施例4的方法区别为:不注入超临界流体ⅱ,直接超临界流体ⅰ,即氮气,达到总压。其它步骤与实施例4相同,得到pbat微孔泡沫材料。
[0095]
利用排水法和分析天平对pbat坯料和实施例4、对比例3、对比例4制得的pbat泡沫材料的密度进行测量,并在此基础上计算pbat泡沫材料的发泡倍率,计算公式如下:
[0096]
ψ=ρs/ρf[0097]
式中:
[0098]
ρ
f-pbat泡沫材料的密度;
[0099]
ρ
s-pbat坯料的密度。
[0100]
根据上述测量计算方法,在制备泡沫材料后1h内每隔10min测量和计算一次实施例4、对比例3、对比例4制得的pbat泡沫材料的发泡倍率,以及在5h后再次测量和计算一次实施例4、对比例3、对比例4制得的pbat泡沫材料的发泡倍率,得到泡沫材料的发泡倍率随时间的变化曲线,即对应泡沫材料的收缩情况。
[0101]
本实施例4、对比例3、对比例4制备的pbat微孔泡沫材料内部泡孔结构如图6-图8所示,制得泡沫材料初始时刻的发泡倍率如图9所示,可以发现:在初始时刻,对比例3使用单一超临界co2间歇发泡制备的pbat泡沫材料发泡倍率最大,达26.2,但其内部泡孔尺寸最大、密度最小;对比例4使用单一超临界n2间歇发泡制备的pbat泡沫材料内部泡孔尺寸较小、密度较大,但发泡倍率最低,仅有6.3;实施例4使用超临界co2和超临界n2混合发泡制备的pbat泡沫材料内部泡孔尺寸致密均匀,泡孔大小和密度与对比例4相当,同时发泡倍率明显提升,达到16.8。
[0102]
进一步的,实施例4、对比例3、对比例4制备的pbat微孔材料发泡倍率随时间变化情况如图10所示,可见:对比例3制备的pbat泡沫材料发泡倍率随时间急剧减小、收缩非常明显,60min后收缩64.1%,300min后收缩79.4%;对比例4制备的pbat泡沫材料发泡倍率随时间减小不大,收缩很小,300min后收缩4.7%,但由于其初始发泡倍率很小,收缩程度意义不大;实施例4制备的pbat泡沫材料发泡倍率随时间略有减小,但程度不大,60min后收缩4.3%,300min后收缩5.9%。综上,实施例4制备的pbat微孔泡沫材料发泡倍率大,收缩率低,且泡孔结构致密,具有良好开发和应用前景。
[0103]
以上所述仅为本发明的优选实施例而已,并不用于限制本发明,对于本领域的技术人员来说,本发明可以有各种更改和变化。凡在本发明的精神和原则之内,所作的任何修改、等同替换、改进等,均应包含在本发明的保护范围之内。