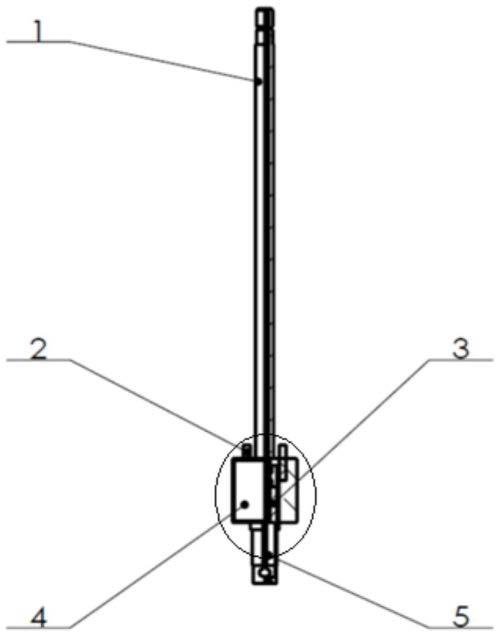
1.本发明涉及一种车灯热铆头技术领域,具体涉及一种车灯热铆头及其制作工艺。
背景技术:2.随着汽车行业的发展,汽车不断地轻量化已经成为趋势,装配生产效率也在不断提高。在汽车车灯装配领域,螺纹连接已经逐渐被重量更轻、装配效率更高的车灯热铆技术所取代,车灯热铆头已经成为铆接设备中十分关键的零部件,如何研究出热铆效率更高、寿命更长的车灯热铆头以及车灯热铆头的制作工艺已成为研究热点。
3.现有的技术中,车灯热铆头及其制作工艺存在以下问题:1、车灯热铆头的加热头为一种薄壁件,在加热使用时经常会出现端部碗装槽与前端连接处断裂的情况,因此需要找到合适的结构、材料与加工工艺,保证车灯热铆头发热集中在端部以及整体强度;2、车灯热铆头在通电加热后熔化汽车车灯上的铆柱,会导致塑料粘接在加热头碗装槽处,从而使得铆接质量变差,因此需要找到合适的防车灯粘接措施,保证车灯热铆头的正常工作;3、热铆头在装配的过程中会出现加热头与导线难焊接、灌封胶泄露等问题,因此需要找到合适的焊接工艺以及设计出合适的模具来进行灌封胶的灌封。为解决上述的技术问题,寻找一种车灯热铆头的制作工艺成为本领域技术人员所研究的重要课题。
技术实现要素:4.本专利要解决的问题是提供一种铆接效率高的车灯热铆头以及该车灯热铆头的装配工艺,提高车灯热铆头的铆接质量以及车灯热铆头制作的效率。为解决上述技术问题,本发明所采用的技术方案是:
5.一种车灯热铆头,其特征在于:包括陶瓷衬套,陶瓷衬套装配有冷却吹气管,冷却吹气管上端为与气管装配的阶梯轴,下端为与陶瓷衬套装配的阶梯轴;大电流导线焊接在加热头两端;陶瓷衬套装配在加热头中。
6.在上述的一种车灯热铆头,加热头包括加热头前管和加热头后管。加热头前管由两个阶梯轴构成一个整体,加热头前管前端有碗装槽,加热头后管为比加热头前管直径大的空心轴,加热头前管的前端部外圆直径小于后端部外圆直径,且加热头前管的前端部壁厚大于后端部壁厚。
7.在上述的一种车灯热铆头,加热头表面镀有化合物镀层,所述大电流导线和加热头外封装有耐高温绝缘外壳。
8.车灯热铆头的制作工艺,其特征在于:包括如下步骤:
9.步骤1,冷却吹气管的制作,冷却吹气管采用大小合适的不锈钢管,在不锈钢管的一端车削出与气管装配的阶梯轴,另一端车削出与陶瓷衬套装配的阶梯轴。
10.步骤2,大电流导线的组装,将pcv导线与铜导线通过紫铜管连接,连接处通过包裹热缩绝缘管进行绝缘保护,在pcv导线另一端安装铜端子;
11.步骤3,车灯加热头的制作,通过镗孔和铣削加工加热头前管和后管,再将后管插
入前管中进行钎焊连接,最后通过线切割进行开槽,通过等离子喷涂工艺为加热头表面镀上化合物镀层。
12.步骤4,车灯热铆头的组装,将大电流导线焊接到加热头两端,再将陶瓷衬套与加热头进行装配,再将冷却吹气管与陶瓷衬套进行装配。将加热头放入模具下模中,加热头前管在模具圆孔处进行定位,盖上上模,用锁紧螺钉锁紧。用注射器向模具中注入配好的灌封胶,常温放置10h或100℃-120℃加热3h。
13.步骤5,耐高温绝缘外壳的制作;将模具上下模拆开,取出封装好绝缘胶的热铆头,在热铆头耐高温绝缘外壳上套上绝缘热缩管。
14.在上述的车灯热铆头的制作工艺,冷却吹气管一端阶梯轴可与标准气管配合,在冷却吹气时无法脱落;另一端阶梯轴在灌封后可使冷却吹气管更加难以脱落。
15.在上述的车灯热铆头的制作工艺,加热头所采用含铬25%、镍20%以及铁55%的铁铬镍合金金属材料升温速率高、强度高,该加热头可更加快速地实现热铆动作且使用寿命长。
16.在上述的车灯热铆头的制作工艺,加热头前管前端阶梯轴及腰孔槽结构可使端部碗装槽较大,在通电加热时将发热集中在碗装槽处。
17.在上述的车灯热铆头的制作工艺,加热头前管前端壁厚较后端更大,增强此处薄壁强度的同时减小电阻,从而提高使用寿命。
18.在上述的车灯热铆头的制作工艺,加热头表面镀有化合物镀层,该镀层可提高加热头强度,同时车灯热铆头在实现高温铆接时不与车灯工件产生粘连,所述化合物镀层包括内层和外层,内层为用于提高强度并保护内部合金不被氧化的氮化钛层,外层为防止高温粘接的特氟龙。
19.因此,本发明具有如下优点:1.该热铆头在高温下有较高的强度,使用寿命较高;2.该热铆头在3v电压通电1.2s碗装槽即可达到160℃的车灯塑料熔化温度;3.该热铆头不易与塑料发生粘接,不会因长时间工作而降低效率;4.该热铆头制作工艺简单高效,生产效率较高。
附图说明
20.图1为本发明的车灯热铆头整体示意图。
21.图2为图1中圆圈处的放大结构示意图。
22.图3为本发明的车灯热铆头的加热头示意图。
23.图4为本发明的车灯热铆头耐高温绝缘外壳模具示意图。
24.图中:1.冷却吹气管、2.大电流导线、3.陶瓷衬套、4.耐高温绝缘外壳、5.加热头、6.加热头前管、7.加热头后管、8模具上模、9.模具下模。
具体实施方式
25.为了更好地理解本发明专利,下面结合附图和具体实施方式对本发明专利作进一步的说明。
26.如图一所示车灯热铆头整体示意图,包括冷却吹气管1、大电流导线2、陶瓷衬套3、耐高温绝缘外壳4和加热头5。冷却吹气管1上端为与气管装配的阶梯轴,下端为与陶瓷衬套
3装配的阶梯轴,由车削加工而成;大电流导线2焊接在加热头5两端;陶瓷衬套3装配在加热头5中,耐高温绝缘外壳4由灌封胶固化而成,表面包裹有高温绝缘灌封胶。加热头5采用的铁铬镍合金的屈服强度为205mp,在800℃的高温下才会发生软化,大大提高了热铆头的使用寿命,并且加热时间由1.2s缩短为0.8s,提升了33%;表面涂层为氮化钛与特氟龙为热和电的良导体,大量铆接后几乎无塑料粘接,车灯残次品率下降。
27.冷却吹气管选取合适的孔径及长度,满足车灯热铆头加热后对加热头的及时冷却;大电流导线可承受100a以上的电流、与加热头实现焊接;陶瓷衬套和耐高温绝缘外壳可承受200℃以上的高温;加热头的材料为一种金属材料,该金属材料在通电加热时具有较快的温升速度,同时在工作温度下能够保持较高的强度;加热头表面有某种化合物镀层,可防止车灯熔化后的粘接。
28.如图三所示车灯热铆头的加热头示意图,包括加热头前管6和加热头后管7。前管由两个阶梯轴构成,加热头前管6前端有碗装槽,该部位为热铆接的工作部位,可将车灯柱熔化,通过铆接力铆接成图钉状,前端外圆直径比后端小,且壁厚更大,从而使电阻集中在前端,使得在通电使用时发热集中在前端碗装槽处;加热头后管7为比加热头前管6直径稍大的空心轴,前管插入后管通过钎焊实现装配。前管阶梯轴难加工,通过改变后管的长度可制作出不同长度的车灯热铆头,从而满足不同车灯热铆接的需求。
29.如图四所示车灯热铆头耐高温绝缘外壳模具示意图,包括模具上模8和模具下模(9)。上模有4个螺纹过孔及2个脱模通孔,下模有4个螺纹底孔。在上模及下模内壁涂上脱模剂,将焊接后的加热头放入下模中,盖上上模,灌入灌封胶。灌封胶固化后,松开螺钉,敲打插入脱模通孔的螺钉,完成车灯热铆头的脱模。
30.本发明涉及的车灯热铆头组成部分的制作工艺,包括不锈钢冷却吹气管加工工艺、绝缘隔热陶瓷衬套加工工艺、大电流导线加工工艺、耐高温绝缘外壳加工工艺、加热头加工工艺、热铆头装配工艺,不同组成部分的制作工艺步骤如下:
31.步骤1、选取表面抛光的无缝不锈钢管进行车削加工。接气管端车削两个阶梯轴用来防止气管脱落,插入端车削一段长插入段与两个阶梯轴,保证在灌封后吹气管无法抽出。
32.步骤2、采用注浆成型的方式完成绝缘陶瓷衬套的毛坯件加工,再通过钻削的方式完成对陶瓷衬套中心孔的精加工。
33.步骤3、大电流导线由pvc电子线、铜导线、紫铜压线管、铜端子几个部分组成。将一段75mm的pcv电子线和一段15mm的铜导线分别插入紫铜压线管中,将压线管压平后将熔化后的焊锡滴入,使得三者连接牢固;再将pcv电子线的另一端连接铜端子,同样将熔化后的焊锡滴入,最后在导线连接处套上绝缘热缩管,完成大电流导线的制作。
34.步骤4、耐高温绝缘外壳选择使用高温绝缘灌封胶进行制作,采用灌胶模具成型的方式。
35.步骤5、加热头分为前管和后管。薄壁结构通过车削和钻削加工,前管前端碗装槽通过铣削加工。
36.步骤6、将加热头后管插入前管中,采用钎焊的方式将两管连成一个整体。再通过线切割加工在加热头中间开一个1mm的槽。
37.步骤7、先打磨后管待焊接处镀层,在加热头后管后端涂上助焊剂,熔化少量焊锡丝滴在后管后端涂有助焊剂的部位,再将高电流导线的铜线端缠绕一部分焊锡丝,将其放
置在后管焊锡处,使用电烙铁进行焊接。
38.步骤8、将陶瓷衬套插入到加热头的指定位置,再将冷却吹气管插入到陶瓷的孔中。
39.步骤9、在模具上用棉签涂上脱模剂,将加热头前管放入绝缘外壳模具的下模中,盖上上模,拧紧4个锁紧螺钉。使用注射剂注入绝缘灌封胶,常温放置10h或100℃-120℃加热3h。冷却固化后在绝缘外壳处加一层的绝缘热缩管。
40.本文中所描述的具体实施例仅仅是对本发明精神作举例说明。本发明所属技术领域的技术人员可以对所描述的具体实施例做各种各样的修改或补充或采用类似的方式替代,但并不会偏离本发明的精神或者超越所附权利要求书所定义的范围。