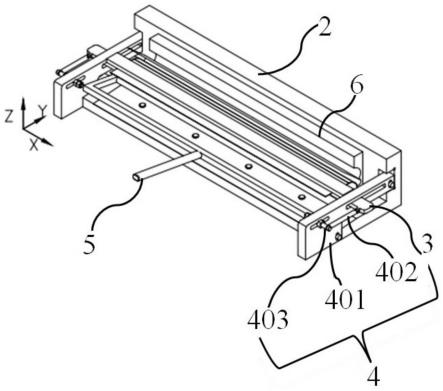
1.本发明涉及超薄玻璃贴合技术,具体地,涉及一种超薄玻璃贴合装置。此外,还涉及一种超薄玻璃贴合方法。
背景技术:2.超薄玻璃已经成为电子高新技术产品重要组成材料,由于玻璃具有高透过率和外观质感的特点,其应用领域已经越来越广,例如,在液晶显示屏、家用电器、仪器设备、数码照相机等电子产品上得到广泛运用。在电子产品的运用上,超薄玻璃需要与电子产品的载体进行贴合固定。
3.目前,通常采用真空贴合设备或数控设备进行贴合,但是,该类设备一次性投入过大,致使产品研发阶段成本高。而且,通常采用功能膜片贴合方法对超薄玻璃进行贴合固定,由于超薄玻璃与功能膜片的弯曲性能存在差异,现有技术在对超薄玻璃进行小曲率曲面贴合时会出现碎裂和气泡而导致成品良率低。此外,需要固定曲面载体对超薄玻璃进行贴合,而固定曲面往往是由工艺人员事先设计好的,但是在实际的贴合中,需要不断改变贴合曲面的曲率以得到最优曲面,致使效率低。
技术实现要素:4.本发明所要解决的技术问题是提供一种超薄玻璃贴合装置,该超薄玻璃贴合装置结构简单,不需要不断改变贴合曲面的曲率,操作简单,能够有效保证良品率,成本低廉。
5.本发明所要解决的技术问题是提供一种超薄玻璃贴合方法,该超薄玻璃贴合方法不需要不断改变贴合曲面的曲率,操作简单,能够有效保证良品率。
6.为了解决上述技术问题,本发明一方面提供一种超薄玻璃贴合装置,包括底座和贴合压辊,所述底座上设置有用于定位待贴合基体的基体固定部和用于定位贴合结构的载体层的边缘的载体层固定部,且所述底座上安装有用于与所述贴合结构的离型膜层连接且能够沿所述离型膜层被撕除方向移动的离型膜层连接部,所述贴合压辊配置为能够滚压所述贴合结构且使所述贴合结构的超薄玻璃层与所述待贴合基体贴合。
7.可选地,所述底座两侧分别设置有张紧部,所述张紧部上设置有限制所述离型膜层连接部移动方向的第一滑道,所述离型膜层连接部的端部与对应的所述张紧部之间安装有弹性件。
8.进一步地,所述张紧部包括滑道支座,所述滑道支座安装在所述底座的侧面,所述第一滑道设置在所述滑道支座上。
9.具体地,所述张紧部还包括连接销轴和设置在所述滑道支座上的第二滑道,所述连接销轴定位在所述第二滑道内,且通过所述弹性件与所述离型膜层连接部的对应端部连接。
10.可选地,所述贴合压辊包括柔性辊和固定支架,所述柔性辊两端分别通过滚轴与所述固定支架可转动连接。
11.可选地,所述贴合结构包括依次叠加的所述离型膜层、粘接层、所述超薄玻璃层和所述载体层。
12.进一步地,所述载体层与所述载体层固定部之间设置有限位结构。
13.具体地,所述限位结构包括设置在所述载体层上的定位孔,以及设置在所述载体层固定部上的定位柱。
14.可选地,所述载体层的面积大于所述离型膜层的面积,所述离型膜层的面积大于所述超薄玻璃层的面积。
15.本发明另一方面提供一种超薄玻璃贴合方法,基于上述技术方案中任一项所述的超薄玻璃贴合装置,包括如下步骤:
16.将所述待贴合基体安装在所述基体固定部上;
17.将所述贴合结构的离型膜层所在一面朝向所述待贴合基体,并将所述贴合结构的载体层的边缘定位在所述载体层固定部上;
18.将所述离型膜层靠近所述载体层固定部的一侧撕开,并将所述离型膜层的该侧连接在所述离型膜层连接部上;
19.使用所述贴合压辊从所述载体层的被定位的边缘开始沿贴合方向滚压所述贴合结构,同时,所述离型膜层连接部将所述离型膜层逐渐撕起,直至贴合完成。
20.通过上述技术方案,本发明的有益效果如下:
21.将贴合结构的载体层的边缘固定在载体层固定部上,而且将贴合结构的离型膜层靠近载体层固定部的一侧撕开,并将该侧与离型膜层连接部连接,在贴合过程中,从贴合结构的载体层的被固定边缘一侧开始,利用贴合压辊对贴合结构滚压,同时离型膜层连接部会将离型膜层逐渐撕开;能够防止碎裂和气泡的出现,保证贴合的良品率。整体结构简单,成本较低,而且,不需要如现有技术一般不断改变贴合曲面的曲率,操作过程简单,有效提升工作效率。
22.本发明的其它特征和优点将在随后的具体实施方式部分予以详细说明。
附图说明
23.附图是用来提供对本发明的进一步理解,并且构成说明书的一部分,与下面的具体实施方式一起用于解释本发明,但并不构成对本发明的限制。在附图中:
24.图1是本发明具体实施方式中的超薄玻璃贴合装置的结构示意图之一;
25.图2是图1中沿a-a向的剖视图;
26.图3是本发明具体实施方式中的超薄玻璃贴合装置的结构示意图之二;
27.图4是本发明具体实施方式中的超薄玻璃贴合装置的结构示意图之三;
28.图5是本发明具体实施方式中的超薄玻璃贴合装置的立体结构示意图之一;
29.图6是本发明具体实施方式中的超薄玻璃贴合装置的立体结构示意图之二;
30.图7是本发明具体实施方式中的超薄玻璃贴合装置的立体结构示意图之3;
31.图8是本发明具体实施方式中的贴合压辊的结构示意图;
32.图9是本发明具体实施方式中的贴合结构的结构示意图之一;
33.图10是本发明具体实施方式中的贴合结构的结构示意图之二;
34.图11是本发明具体实施方式中的超薄玻璃贴合装置的使用状态结构示意图;
35.图12是图11中沿b-b向的剖视图;
36.图13是本发明具体实施方式中的超薄玻璃贴合装置的使用状态立体结构示意图。
37.附图标记说明
38.1贴合结构
ꢀꢀꢀꢀꢀꢀꢀꢀꢀꢀꢀꢀꢀꢀꢀꢀꢀꢀꢀꢀꢀꢀ
101离型膜层
39.102粘接层
ꢀꢀꢀꢀꢀꢀꢀꢀꢀꢀꢀꢀꢀꢀꢀꢀꢀꢀꢀꢀꢀꢀ
103超薄玻璃层
40.104载体层
ꢀꢀꢀꢀꢀꢀꢀꢀꢀꢀꢀꢀꢀꢀꢀꢀꢀꢀꢀꢀꢀꢀ
1041定位孔
41.2底座
ꢀꢀꢀꢀꢀꢀꢀꢀꢀꢀꢀꢀꢀꢀꢀꢀꢀꢀꢀꢀꢀꢀꢀꢀꢀꢀ
201基体固定部
42.202载体层固定部
ꢀꢀꢀꢀꢀꢀꢀꢀꢀꢀꢀꢀꢀꢀꢀꢀ
2021定位柱
43.3离型膜层连接部
ꢀꢀꢀꢀꢀꢀꢀꢀꢀꢀꢀꢀꢀꢀꢀꢀ
4张紧部
44.401滑道支座
ꢀꢀꢀꢀꢀꢀꢀꢀꢀꢀꢀꢀꢀꢀꢀꢀꢀꢀꢀꢀ
402弹性件
45.403连接销轴
ꢀꢀꢀꢀꢀꢀꢀꢀꢀꢀꢀꢀꢀꢀꢀꢀꢀꢀꢀꢀ
404第一滑道
46.405第二滑道
ꢀꢀꢀꢀꢀꢀꢀꢀꢀꢀꢀꢀꢀꢀꢀꢀꢀꢀꢀꢀ
5贴合压辊
47.501柔性辊
ꢀꢀꢀꢀꢀꢀꢀꢀꢀꢀꢀꢀꢀꢀꢀꢀꢀꢀꢀꢀꢀꢀ
502滚轴
48.503固定支架
ꢀꢀꢀꢀꢀꢀꢀꢀꢀꢀꢀꢀꢀꢀꢀꢀꢀꢀꢀꢀ
6待贴合基体
具体实施方式
49.以下结合附图对本发明的具体实施方式进行详细说明,应当理解的是,此处所描述的具体实施方式仅用于说明和解释本发明,本发明的保护范围并不局限于下述的具体实施方式。
50.在本发明的描述中,需要说明的是,除非另有明确的规定和限定,术语“设置”、“安装”、“连接”应做广义理解,例如,可以是固定连接,也可以是可拆卸连接,或者是一体连接;可以是直接连接,也可以是通过中间媒介间接连接,可以是两个元件内部的连通或两个元件的相互作用关系。对于本领域的普通技术人员而言,可以根据具体情况理解上述术语在本发明中的具体含义。
51.此外,术语“第一”、“第二”仅用于描述的目的,而不能理解为指示或暗示相对重要性或隐含指明所指示的技术特征的数量,因此,限定有“第一”、“第二”的特征可以明示或隐含地包括一个或更多个所述特征。
52.在本发明的描述中,需要理解的是,方位术语基于附图所示的方位或位置关系,仅是为了便于描述本发明和简化描述,而不是指示或暗示所指的装置或元件必须具有特定的方位、以特定的方位构造和操作,因此不能理解为对本发明的限制。
53.为了方便描述,参照图13,建立直角坐标系,y方向与贴合压辊5滚压的方向相同,z方向表示上下方向,x方向表示左右方向。此外,本发明中的超薄玻璃的厚度通常在0.3mm到0.03mm之间,超薄玻璃可以实现弯曲,而其厚度小于0.2mm时则可以拥有可折叠的特性。
54.参照图1至图13,本发明提供了一种超薄玻璃贴合装置,包括底座2和贴合压辊5,底座2上设置有基体固定部201和载体层固定部202,基体固定部201用于放置定位待贴合基体6,载体层固定部202与贴合结构1的载体层104的边缘连接,用于定位贴合结构1,底座2上还安装有离型膜层连接部3,离型膜层连接部3用于与贴合结构1的离型膜层101连接,并且离型膜层连接部3能够沿离型膜层101被撕除方向移动,在贴合过程中,贴合压辊5滚压贴合结构1,使贴合结构1的超薄玻璃层103与待贴合基体6贴合。
55.其中,由于离型膜层连接部3与离型膜层101连接,使得贴合结构1在贴合过程中始终保持,贴合压辊滚压后的区域才与待贴合基体贴合,未滚压的区域始终不与待贴合基体贴合,以有效保证良品率。而且,整体结构简单,成本较低,操作简单,提升工作效率。
56.根据本发明的超薄玻璃贴合装置,可以实现一种超薄玻璃贴合方法,如下步骤:
57.将待贴合基体6安装在基体固定部201上;
58.将贴合结构1的离型膜层101所在一面朝向待贴合基体6,并将贴合结构1的载体层104的边缘定位在载体层固定部202上;
59.将离型膜层101靠近载体层固定部202的一侧撕开,并将离型膜层101的该侧连接在离型膜层连接部3上;
60.使用贴合压辊5从载体层104的被定位的边缘开始沿贴合方向滚压贴合结构1,同时,离型膜层连接部3将离型膜层101逐渐撕起,直至贴合完成。
61.上述操作过程简单,而且,能够避免贴合不良,不需要如现有技术一般不断改变贴合曲面的曲率以得到最优曲面,具有较高的工作效率。
62.具体地,参照图9和图10,贴合结构1包括依次叠加的离型膜层101、粘接层102、超薄玻璃层103和载体层104。
63.为了将载体层104与载体层固定部20进行固定,在载体层104与载体层固定部202之间设置有限位结构。具体地,参照图6和图10,可以在载体层104上设置定位孔1041,载体层固定部202上设置定位柱2021,通过定位孔1041与对应的定位柱2021之间的插装配合,实现载体层104与载体层固定部202之间的定位。载体层104上的定位孔1041的位置要避开离型膜层101,防止发生干涉。当然,限位结构不局限于上述设计,也可以为其它结构形式,例如,在载体层固定部202上设置卡扣等定位结构,将载体层104固定在载体层固定部202上,或者,也可以为其它定位固定结构。另外,还可以在载体层固定部202上设置真空孔或真空槽,提供吸附力以对载体层104进行固定。
64.在具体实施例中,离型膜层101可以采用pe(聚乙烯塑料)、opp(邻苯基苯酚)、pc(聚碳酸酯)等材质制备,优选采用pet(聚对苯二甲酸乙二醇酯)材质制备,离型膜层101的厚度在0.05mm-0.2mm之间。离型膜层101用于保护粘接层102,粘接层102为oca光学胶,其厚度在10um-500um,oca光学胶是一种用于胶结透明光学元件的特种粘胶剂;oca光学胶在超薄玻璃层103外形上有所内缩,防止在贴合时出现边部oca光学胶溢出的问题。整个离型膜层101在沿超薄玻璃层103贴合方向的两条边上都有外扩,具体而言,离型膜层101在整个离型膜层101沿超薄玻璃层103贴合方向的两条边上比超薄玻璃层103大,一般地,离型膜层101的单边比超薄玻璃层103单边大5mm-100mm,离型膜层101的面积大于超薄玻璃层103的面积。
65.载体层104为超薄玻璃层103在贴合时提供固定面和保护作用,其材质可以为pe离型膜、pet离型膜、opp离型膜、pc离型膜等,优选为pet离型膜;载体层104厚度在0.08mm-0.3mm之间。整个载体层104应在超薄玻璃层103外形上有所外扩,防止在贴合时超薄玻璃层103的表面被损伤,载体层104的面积大于离型膜层101的面积。
66.在具体实施例中,参照图6,底座2左右两侧分别设置有张紧部4,张紧部4包括滑道支座401,滑道支座401安装在底座2的侧面,在滑道支座401上设置有第一滑道404,第一滑道404设置在滑道支座401上靠近基体固定部201的一侧,离型膜层连接部3的两端分别卡装
在第一滑道404内,并且离型膜层连接部3能够沿着第一滑道404移动,离型膜层连接部3的端部与对应的张紧部4之间安装有弹性件402;其中,弹性件402可以为弹簧、橡胶等制成的弹性零部件。滑道支座401上还设置有沿z方向的竖向滑槽,销轴穿过竖向滑槽将滑道支座401固定在底座2的侧面,滑道支座401可以沿z方向移动一定距离,使张紧部4能够沿z方向上下调节其定位位置,从而能够控制贴合结构1在z方向上的高度,避免贴合时出现贴合压辊5还未压过的区域率先与待贴合基体6贴合而出现的贴合不良。
67.进一步地,张紧部4还包括连接销轴403和第二滑道405,第二滑道405设置在滑道支座401上远离基体固定部201的一侧,优选地,第一滑道404与第二滑道405平齐。连接销轴403定位在第二滑道405内,连接销轴403通过弹性件402与离型膜层连接部3的对应端部连接;一方面,可以通过调节连接销轴403,以适应不同长度的弹性件402,另一方面,方便调整对离型膜层连接部3施加的张紧力。
68.作为贴合压辊5的一种具体结构形式,参照图8,贴合压辊5包括柔性辊501和固定支架503,柔性辊501两端分别通过滚轴502与固定支架503可转动连接,使柔性辊501能够绕其中心轴旋转。
69.其中,柔性辊501的材质为橡胶、硅胶等弹性材料,柔性辊501外圆半径必须小于待贴合基体6贴合曲面的最小曲率半径,以保证柔性辊501能沿待贴合基体6贴合曲面的截面线,在该曲面上做完整位移。
70.参照图1至图13,本发明优选实施方式的超薄玻璃贴合装置,包括底座2和贴合压辊5,底座2包括基体固定部201和载体层固定部202,基体固定部201用于放置定位待贴合基体6,待贴合基体6安装固定在基体固定部201后,与载体层固定部202之间具有顺滑、渐进的贴合延伸平面;载体层固定部202上设置有定位柱2021和真空孔,贴合结构1的载体层104的边缘区域设置有定位孔1041,通过定位孔1041和定位柱2021将贴合结构1的载体层104定位在载体层固定部202上。贴合结构1包括顺次叠加设置的离型膜层101、粘接层102、超薄玻璃层103和载体层104。在底座2的左右两侧分别安装张紧部4,张紧部4包括滑道支座401、弹性件402、连接销轴403第一滑道404、第二滑道405和竖向滑道,销轴穿过竖向滑道将滑道支座401安装固定在底座2的侧面上,第一滑道404和第二滑道405开设在滑道支座401上,并且沿着从靠近基体固定部201向远离基体固定部201的方向依次布置,两个第一滑道404之间安装有离型膜层连接部3,离型膜层连接部3的端部插入对应的第一滑道404中,并且第二滑道405内定位安装连接销轴403,连接销轴403与离型膜层连接部3的对应端部通过弹性件402连接,离型膜层连接部3用于与贴合结构1的离型膜层101连接。贴合压辊5包括柔性辊501和固定支架503,柔性辊501两端分别通过滚轴502与固定支架503可转动连接,使柔性辊501能够绕其中心轴旋转。在贴合时,柔性辊501伸入底座2内,并且从载体层固定部202向基体固定部201的方向滚压贴合结构1,使超薄玻璃层103与待贴合基体6贴合。
71.下面对具体的超薄玻璃贴合方法进行描述,以更好地说明本发明的技术方案。
72.将待贴合基体6贴靠放置在基体固定部201上;
73.使载体层104所在一面向上,将贴合结构1通过载体层104的定位孔1041定位在载体层固定部202上;
74.启动真空吸附设备,通过载体层固定部202上真空孔对载体层104进行固定;
75.将贴合结构1的离型膜层101靠近载体层固定部202一侧撕起,并将离型膜层101的
该侧固定在离型膜层连接部3上;
76.将贴合压辊5伸入,使柔性辊501滚压在载体层104靠近载体层固定部202的一侧;
77.沿着贴合方向推动贴合压辊5,同时通过离型膜层连接部3逐渐撕起离型膜层101,直至完成贴合,使超薄玻璃层103贴合在待贴合基体6上。
78.其中,可以通过滑道支座401上的竖向滑道调节张紧部4的高度,从而控制贴合结构1的厚度,避免贴合时出现贴合压辊5还未压过的区域率先与待贴合基体6贴合而出现贴合不良。
79.通过上述技术方案,本发明通过简单的结构,经济的方式,实现超薄玻璃在小曲率曲面上的贴合,有效减低研发成本。
80.具体地,通过一边贴合一边滚压的方式,实现超薄玻璃对曲面的自适应贴合,有效杜绝超薄玻璃在贴合时的碎裂和出现的气泡,提高生产质量。
81.而且,基于超薄玻璃的弹性特点,实现超薄玻璃对曲面的自适应贴合,无需多次更改贴合曲面曲率,提高了研发阶段的调试效率。
82.以上结合附图详细描述了本发明的优选实施方式,但是,本发明并不限于上述实施方式中的具体细节,在本发明的技术构思范围内,可以对本发明的技术方案进行多种简单变型,这些简单变型均属于本发明的保护范围。
83.另外需要说明的是,在上述具体实施方式中所描述的各个具体技术特征,在不矛盾的情况下,可以通过任何合适的方式进行组合。为了避免不必要的重复,本发明对各种可能的组合方式不再另行说明。
84.此外,本发明的各种不同的实施方式之间也可以进行任意组合,只要其不违背本发明的思想,其同样应当视为本发明所公开的内容。