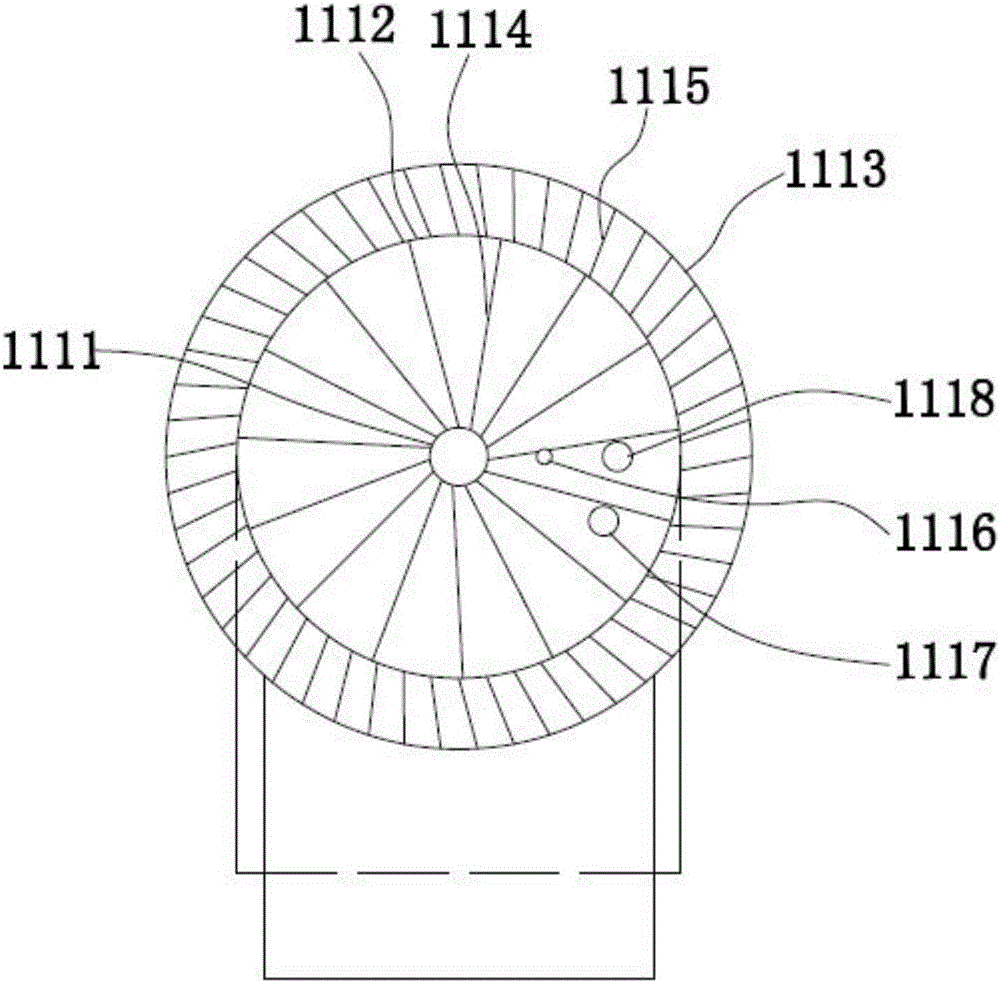
本发明属于节能环保技术领域,具体涉及一种采用低热值煤气发电的方法。
背景技术:
中国是世界上的钢铁生产大国,钢铁企业在冶炼过程中产生了大量的副产煤气,如高炉煤气、转炉煤气和焦炉煤气,其中,高炉煤气具有产量最大、热值最低、有毒有害、易燃易爆等特点。近年来,我国能源紧缺日趋突出,环保要求日益提高,高炉煤气发电在钢铁企业得到逐步应用,如申请号为201320444475.0的专利公开了一种全烧高炉煤气锅炉烟气余热回收利用系统,申请号为201320446384.0的专利公开了一种全烧高炉煤气锅炉烟气余热深度回收利用系统,但是上述高炉煤气发电系统仅着重提高烟气侧余热的回收利用,而未考虑汽水侧如何提高热效率;申请号为201510239804.1的专利公开了一种自备电厂燃烧冶金煤气的发电方法及系统,但其仅仅提供了一种钢铁企业煤气发电的概念和方法,没有相关发电系统。虽然高炉煤气发电在钢铁企业得到逐步应用,但是目前仍然存在锅炉燃烧不稳定、受热面布置不合理、热效率低等问题。
技术实现要素:
本发明实施例涉及一种采用低热值煤气发电的方法,至少可解决现有技术的部分缺陷。
本发明实施例涉及一种采用低热值煤气发电的方法,包括如下步骤:
步骤一,将LHV在3100kJ/Nm3以上的低热值煤气送入低热值煤气锅炉内燃烧,燃烧产生的烟气与所述低热值煤气锅炉内的换热面换热;其中,在过热器内产生13.7MPa、540℃的高温超高压的过热蒸汽,过热蒸汽送至汽轮机的高压缸中进行发电;
步骤二,从汽轮机高压缸中出来的蒸汽进入再热器中进行再次加热,从再热器出来的再热蒸汽进入低压缸进行发电;
步骤三,从低压缸出来的蒸汽经冷凝为冷凝水后,进入省煤器,从省煤器出来的水进入汽包;
步骤四,在汽包中,经汽水分离得到的水进入低热值煤气锅炉的水冷壁,在水冷壁中被加热为蒸汽或汽水混合物后回到汽包;经汽水分离得到的饱和蒸汽进入过热器中,并被加热为13.7MPa、540℃的高温超高压的过热蒸汽,再送至汽轮机的高压缸进行发电;
步骤五,循环进行上述步骤二至步骤四。
作为实施例之一,步骤一中,低热值煤气通过燃烧器结构送入至所述低热值煤气锅炉内燃烧;
所述燃烧器结构包括第一燃烧器层,所述第一燃烧器层包括布置于所述燃烧室前墙的至少一个第一燃烧器,或包括对冲布置于所述燃烧室前墙和后墙的多个第一燃烧器,各所述第一燃烧器均包括由内而外依次套接的点火气管、第一燃气管和第一助燃气管,所述第一燃气管连接有低热值煤气供应管;
所述第一燃气管和所述第一助燃气管出口端均设置有旋流叶片组,每一旋流叶片组的各旋流叶片环形布置于对应的气管内腔中,各旋流叶片均沿对应的气管的径向布置。
进一步地,所述燃烧器结构还包括第二燃烧器层,所述第二燃烧器层位于所述第一燃烧器层上方;所述第二燃烧器层包括布置于所述燃烧室前墙的至少一个第二燃烧器,或包括对冲布置于所述燃烧室前墙和后墙的多个第二燃烧器;各所述第二燃烧器均包括自内而外依次套接的第二燃气管、第二助燃气管、第三燃气管和第三助燃气管,各气管的出口端均设置有旋流叶片组,每一旋流叶片组的各旋流叶片环形布置于对应的气管内腔中,各旋流叶片均沿对应的气管的径向布置。
作为实施例之一,在所述低热值煤气锅炉的烟道末端设置空气预热器,经空气预热器预热的空气作为助燃气送至所述第一燃烧器层和/或所述第二燃烧器层利用。
作为实施例之一,发电机组启动过程中,通过高压旁路机构控制主蒸汽压力;
所述高压旁路机构包括并联布置的至少一个高压旁路,各所述高压旁路上均设有高旁压力阀,各所述高旁压力阀的减温水入口端均连接有一高压喷水管路,各所述高压喷水管路上均设有高旁喷水调节阀和高旁喷水隔离阀;
各所述高压旁路的控制方法均包括:通过对应的所述高旁压力阀的开度、对应的所述高旁压力阀前后蒸汽的焓值及减温水的焓值计算出所需的减温水量,再根据对应的所述高旁喷水调节阀前后的压力、对应的所述高旁喷水调节阀的等百分比特性曲线计算出对应的所述高旁喷水调节阀的开度。
作为实施例之一,在再热器的出口蒸汽管路上旁接有低压旁路,所述低压旁路的蒸汽出口端旁接于所述低压缸的出口凝结管路上;
所述低压旁路上设有低旁压力阀,所述低旁压力阀的减温水入口端均连接有一低压喷水管路,所述低压喷水管路上设有低旁喷水调节阀和低旁喷水隔离阀。
作为实施例之一,所述低压旁路的控制方法包括:
所述低旁压力阀开启时,联锁开启所述低旁喷水隔离阀;
所述低旁压力阀全关时,延时15s关闭所述低旁喷水隔离阀。
作为实施例之一,所述低压旁路的控制方法包括:通过所述低旁压力阀的开度、所述低旁压力阀前后蒸汽的焓值及减温水的焓值计算出所需的减温水量,再根据所述低旁喷水调节阀前后的压力、所述低旁喷水调节阀的等百分比特性曲线计算出所述低旁喷水调节阀的开度。
本发明实施例至少具有如下有益效果:通过将低热值煤气送入低热值煤气锅炉中燃烧,并在过热器内产生13.7MPa、540℃的高温超高压的过热蒸汽,结合蒸汽一次再热的方式,可有效提高低热值煤气发电的效率。
附图说明
为了更清楚地说明本发明实施例或现有技术中的技术方案,下面将对实施例或现有技术描述中所需要使用的附图作简单地介绍,显而易见地,下面描述中的附图仅仅是本发明的一些实施例,对于本领域普通技术人员来讲,在不付出创造性劳动的前提下,还可以根据这些附图获得其它的附图。
图1为本发明实施例一中提供的燃烧器的结构示意图;
图2为图1中燃烧器的A向结构示意图;
图3为本发明实施例二中提供的燃烧器的结构示意图;
图4为图3中燃烧器的A向结构示意图;
图5为本发明实施例提供的低热值煤气发电系统的结构示意图;
图6为本发明实施例提供的高压旁路及低压旁路的结构示意图。
具体实施方式
下面将结合本发明实施例中的附图,对本发明实施例中的技术方案进行清楚、完整地描述,显然,所描述的实施例仅仅是本发明一部分实施例,而不是全部的实施例。基于本发明中的实施例,本领域普通技术人员在没有做出创造性劳动前提下所获得的所有其它实施例,都属于本发明保护的范围。
实施例一
如图1-图2,本发明实施例涉及一种燃烧器,包括由内而外依次套接的点火气管1111、第一燃气管1112和第一助燃气管1113,所述第一燃气管1112和所述第一助燃气管1113出口端均设置有旋流叶片组,每一旋流叶片组的各旋流叶片环形布置于对应的气管内腔中,各旋流叶片均沿对应的气管的径向布置。上述点火气管1111、第一燃气管1112及第一助燃气管1113优选为同轴套接;进一步还包括点火器1116,该点火器1116布置于第一燃气管1112内,且优选为靠近点火气管1111布置,进一步优选为与点火气管1111平行布置,其穿过布置于第一燃气管1112中的旋流叶片并靠近本燃烧器的喷口;该点火器1116优选为采用自动高能电子点火器1116,点火操作稳定可靠。上述点火气管1111连接有点火气供应管,点火气可采用焦炉煤气、转炉煤气、天然气、液化石油气或燃油等;上述第一燃气管1112连接有第一燃气供应管,本实施例中,上述燃烧器优选为用于低热值煤气的喷吹燃烧,上述第一燃气供应管优选为供应低热值煤气,进一步优选地,上述低热值煤气为高炉煤气;上述第一助燃气管1113连接有助燃气供应管,助燃气一般采用空气。
通过设置旋流叶片组,一方面,利于燃气与助燃气的强烈混合,保证燃气的燃烧持续进行,提高燃气燃烧的稳定性;另一方面,可在燃烧区域形成高温烟气回流区,利于燃气的着火燃烧,提高燃气燃烧的稳定性及燃烧完全性。将本燃烧器用于低热值煤气的燃烧时,可有效提高低热值煤气的燃烧效果及效率。
如图1和图2,各旋流叶片组的设置方式可以采取如下结构:上述第一燃气管1112中的旋流叶片组包括多个第一煤气旋流叶片1114,每一第一煤气旋流叶片1114的一端固定在点火气管1111上,另一端固定在第一燃气管1112上;上述第一助燃气管1113中的旋流叶片组包括多个第一助燃气旋流叶片1115,每一第一助燃气旋流叶片1115的一端固定在第一燃气管1112上,另一端固定在第一助燃气管1113上。如图2中所示,优选地,第一煤气旋流叶片1114的数量少于第一助燃气旋流叶片1115的数量;进一步地,沿第一燃气管1112的径向,第一煤气旋流叶片1114的长度大于第一助燃气旋流叶片1115的长度,以保证获得所需的两股气体旋流的切向速度及混合效果。
本实施例中,对于各旋流叶片组的设置,优选为采取如下的优选结构:所述第一燃气管1112出口端处设有第一环形毂,所述第一环形毂位于所述第一燃气管1112与所述点火气管1111之间;所述第一燃气管1112内的旋流叶片组包括多个第一旋流叶片和多个第二旋流叶片,各所述第一旋流叶片均固定于所述第一环形毂与所述点火气管1111之间,各所述第二旋流叶片均固定于所述第一环形毂与所述第一燃气管1112之间。其中,优选地,所述第一旋流叶片的数量少于所述第二旋流叶片的数量;进一步地,沿所述第一燃气管1112的径向,所述第一旋流叶片的长度大于所述第二旋流叶片的长度,使得两股第一燃气旋流的流量大致均衡。上述第一旋流叶片的旋向与上述第二旋流叶片的旋向可相同,也可不同;上述第一旋流叶片的倾斜角与上述第二旋流叶片的倾斜角可相同,也可不同;其中,各第一旋流叶片的旋向应保证在其射出的旋流中心可形成负压区,以利于高温烟气回流,利用高温烟气加热第一燃气及助燃气,提高燃烧效率;各第一旋流叶片的旋向优选为与第二旋流叶片的旋向相反,或旋向相同但倾斜角不同,以便于两股第一燃气旋流能够相交碰撞为宜,通过两股第一燃气旋流碰撞,便于形成紊流,提高第一燃气与助燃气的混合效果。
进一步优化上述燃烧器的结构,所述第一助燃气管1113出口端处设有第二环形毂,所述第二环形毂位于所述第一助燃气管1113与所述第一燃气管1112之间;所述第一助燃气管1113内的旋流叶片组包括多个第三旋流叶片,各所述第三旋流叶片均固定于所述第二环形毂与所述第一燃气管1112之间。第二环形毂与第一助燃气管1113之间可不设置旋流叶片,即第一助燃气管1113出口形成两股气流,其中外部射流为直流射流,内部射流为旋流,这种结构在一定程度上会使本燃烧器喷出的整体射流的气流拉长,但会使气流的旋转强度减弱、烟气回流区减小;因而,本实施例中,进一步优选在第二环形毂与第一助燃气管1113之间设置旋流叶片,即,所述第一助燃气管1113内的旋流叶片组还包括多个第四旋流叶片,各所述第四旋流叶片均固定于所述第二环形毂与所述第一助燃气管1113之间。同样地,第三旋流叶片的旋向与第四旋流叶片的旋向可相同,也可不同;第三旋流叶片的倾斜角与第四旋流叶片的倾斜角可相同,也可不同;优选为设置第三旋流叶片的旋向与第四旋流叶片的旋向相反,其中,第三旋流叶片的旋向优选为与上述第一燃气管1112中的第二旋流叶片的旋向相反且旋流对冲,可一定程度上提高第一燃气与助燃气的混合效果,而第四旋流叶片组则保证燃烧器喷出的整体射流具有一定的切向速度。
为获得所需的火焰特性(如方向、外形、刚性、铺展性等),以及保证煤气燃烧的完全性及燃烧的稳定性等,应兼顾第一燃气与助燃气的混合效果、烟气回流区的控制及各股旋流具有合适的切向速度,可视具体情况通过以下方式进行调节:
(1)调节第一旋流叶片组和第二旋流叶片组的数量比及叶片长度比;
(2)调节第一旋流叶片与第二旋流叶片的倾斜角;
(3)调节第三旋流叶片组和第四旋流叶片组的数量比及叶片长度比;
(4)调节第三旋流叶片与第四旋流叶片的倾斜角;
(5)调节第二旋流叶片与第三旋流叶片的倾斜角;
(6)调节第二旋流叶片组和第三旋流叶片组的数量比及叶片长度比;
更多的情况下,通过上述两种或两种以上的调节方式的结合来实现,以达到火焰刚性强、燃烧稳定、不脱火、不回火、火焰不发飘等特点为佳,针对低热值煤气的气体特性,应保证煤气与作为助燃气的空气混合均匀,以煤气能够燃烧完全为佳。本实施例中,可实现高炉煤气与助燃空气的体积比在1:5~1:10范围内调节。
上述调节方式,可通过在燃烧器安装前根据现场的低热值煤气的特性,通过对应的计算获得所需的各旋流叶片组的参数,选择相应的燃烧器进行安装。更为优选的方式是:在燃烧过程中,可实时调节各旋流叶片的倾斜角,以获得所需的燃烧状况;即每一旋流叶片的两端分别可转动安装于对应的安装部上,根据燃烧器工作环境的特点,每一旋流叶片两端的转轴与对应的轴承之间可采用耐高温润滑脂或耐高温润滑油润滑;每一旋流叶片组的各旋流叶片优选为通过同步传动机构实现同步转动调节,同步传动机构可以是齿轮啮合传动方式等常用的同步传动结构,具体结构此处不再赘述。
另外,可进一步设置监测机构,用于实时监测燃烧器的工作状况,以保证燃烧器安全稳定运行。该监测机构主要包括火焰监测器、压力监测器和温度监测器,可在该燃烧器的远离喷头的一端设置火焰观测孔1117及火焰监测器用孔1118。
实施例二
如图3-图4,本发明实施例涉及一种燃烧器,包括由内而外依次套接的第二燃气管1121、第二助燃气管1122、第三燃气管1123和第三助燃气管1124,各气管的出口端均设置有旋流叶片组,每一旋流叶片组的各旋流叶片环形布置于对应的气管内腔中,各旋流叶片均沿对应的气管的径向布置。
通过设置旋流叶片组,一方面,利于燃气与助燃气的强烈混合,保证燃气的燃烧持续进行,提高燃气燃烧的稳定性;另一方面,可在燃烧区域形成高温烟气回流区,利于燃气的着火燃烧,提高燃气燃烧的稳定性及燃烧完全性。
上述第二燃气管1121、第二助燃气管1122、第三燃气管1123和第三助燃气管1124优选为同轴套接。上述第二燃气管1121连接有第二燃气供应管,上述第三燃气管1123连接有第三燃气供应管,上述第二助燃气管1122及第三助燃气管1124均连接有助燃气供应管,助燃气一般采用空气。通过采用双燃气管的结构,对于两燃气管采用相同燃气的方式,即上述第二燃气供应管与上述第三燃气供应管连接相同的气源,可有效提高燃气与助燃气混合的效果,提高燃烧效率;对于两燃气管采用不同燃气的方式,即上述第二燃气供应管与上述第三燃气供应管连接不同的气源,可实现不同燃气的不同配比,进行燃烧优化,提高燃烧效率;同时,在其中一种燃气品质发生波动或断供时,另一种燃气的存在保证燃烧的可持续性,提高燃烧的稳定性且保证燃烧安全。本实施例中,上述第二燃气供应管优选为供应转炉煤气等高热值煤气;第三燃气供应管优选为供应低热值煤气,进一步优选地,上述低热值煤气为高炉煤气;上述高热值煤气与低热值煤气混合燃烧,一方面可根据钢铁厂转炉煤气和高炉煤气的富余量调节燃料比;另一方面,可通过调节转炉煤气和高炉煤气的比例,提高燃烧的效果及效率,从而有效提高低热值煤气的燃烧效果,利于提高烟气的品质。进一步地,本发明的采用低热值煤气进行发电的系统可实现纯烧高炉煤气的稳定燃烧,进行发电。
如图3和图4,各旋流叶片组的设置方式可以采取如下结构:上述第二燃气管1121中的旋流叶片组包括多个第二煤气旋流叶片1126,每一第二煤气旋流叶片1126的一端固定在设于该第二燃气管1121中的支撑毂1125上,另一端固定在第二燃气管1121上;上述第二助燃气管1122中的旋流叶片组包括多个第二助燃气旋流叶片1127,每一第二助燃气旋流叶片1127的一端固定在第二燃气管1121上,另一端固定在第二助燃气管1122上;上述第三燃气管1123中的旋流叶片组包括多个第三煤气旋流叶片1128,每一第三煤气旋流叶片1128的一端固定在第二助燃气管1122上,另一端固定在第三燃气管1123上;上述第三助燃气管1124中的旋流叶片组包括多个第三助燃气旋流叶片1129,每一第三助燃气旋流叶片1129的一端固定在第三燃气管1123上,另一端固定在第三助燃气管1124上。
如图4中所示,优选地,第二煤气旋流叶片1126的数量少于第二助燃气旋流叶片1127的数量;进一步地,沿第二燃气管1121的径向,第二煤气旋流叶片1126的长度大于第二助燃气旋流叶片1127的长度,以保证获得所需的两股气体旋流的切向速度及混合效果。第三煤气旋流叶片1128的数量少于第三助燃气旋流叶片1129的数量;进一步地,沿第三燃气管1123的径向,第三煤气旋流叶片1128的长度大于第三助燃气旋流叶片1129的长度,以保证获得所需的两股气体旋流的切向速度及混合效果。
本实施例中,对于各旋流叶片组的设置,优选为采取如下的优选结构:所述第二燃气管1121出口端处设有支撑毂1125和第三环形毂,所述支撑毂1125、所述第三环形毂及所述第二燃气管1121由内而外依次套接;所述第二燃气管1121内的旋流叶片组包括多个第五旋流叶片和多个第六旋流叶片,各所述第五旋流叶片均固定于所述第三环形毂与所述支撑毂1125之间,各所述第六旋流叶片均固定于所述第三环形毂与所述第二燃气管1121之间。其中,优选地,所述第五旋流叶片的数量少于所述第六旋流叶片的数量;进一步地,沿所述第二燃气管1121的径向,所述第五旋流叶片的长度大于所述第六旋流叶片的长度,使得两股第二燃气旋流的流量大致均衡。上述第五旋流叶片的旋向与上述第六旋流叶片的旋向可相同,也可不同;上述第五旋流叶片的倾斜角与上述第六旋流叶片的倾斜角可相同,也可不同;其中,各第五旋流叶片的旋向应保证在其射出的旋流中心可形成负压区,以利于高温烟气回流,利用高温烟气加热第二燃气及助燃气,提高燃烧效率;各第五旋流叶片的旋向优选为与第六旋流叶片的旋向相反,或旋向相同但倾斜角不同,以便于两股第一燃气旋流能够相交碰撞为宜,通过两股第二燃气旋流碰撞,便于形成紊流,提高第二燃气与助燃气的混合效果。
作为实施例之一,所述第二助燃气管1122出口端处设有第四环形毂,所述第四环形毂位于所述第二助燃气管1122与所述第二燃气管1121之间;所述第二助燃气管1122内的旋流叶片组包括多个第七旋流叶片及多个第八旋流叶片,各所述第七旋流叶片均固定于所述第四环形毂与所述第二燃气管1121之间,各所述第八旋流叶片均固定于所述第四环形毂与所述第二助燃气管1122之间。第七旋流叶片的旋向与第八旋流叶片的旋向可相同,也可不同;第七旋流叶片的倾斜角与第八旋流叶片的倾斜角可相同,也可不同;优选为设置第七旋流叶片的旋向与第八旋流叶片的旋向相反,其中,第七旋流叶片的旋向优选为与上述第二燃气管1121中的第六旋流叶片的旋向相反且旋流对冲,可一定程度上提高第二燃气与助燃气的混合效果,而第八旋流叶片的旋向优选为与上述第三燃气管1123中的旋流叶片组的旋向相反且旋流对冲,可一定程度上提高第三燃气与助燃气的混合效果。
作为实施例之一,所述第三助燃气管1124出口端处设有第五环形毂,所述第五环形毂位于所述第三助燃气管1124与所述第三燃气管1123之间;所述第三助燃气管1124内的旋流叶片组包括多个第九旋流叶片,各所述第九旋流叶片均固定于所述第五环形毂与所述第三燃气管1123之间。第五环形毂与第三助燃气管1124之间可不设置旋流叶片,即第三助燃气管1124出口形成两股气流,其中外部射流为直流射流,内部射流为旋流,这种结构在一定程度上会使本燃烧器喷出的整体射流的气流拉长,但会使气流的旋转强度减弱、烟气回流区减小;因而,本实施例中,进一步优选在第五环形毂与第三助燃气管1124之间设置旋流叶片,即,所述第三助燃气管1124内的旋流叶片组还包括多个第十旋流叶片,各所述第十旋流叶片均固定于所述第五环形毂与所述第三助燃气管1124之间。同样地,第九旋流叶片的旋向与第十旋流叶片的旋向可相同,也可不同;第九旋流叶片的倾斜角与第十旋流叶片的倾斜角可相同,也可不同。
为获得所需的火焰特性(如方向、外形、刚性、铺展性等),以及保证煤气燃烧的完全性及燃烧的稳定性等,应兼顾各燃气与助燃气的混合效果、烟气回流区的控制及各股旋流具有合适的切向速度,可视具体情况通过以下方式进行调节:
(1)调节第五旋流叶片组和第六旋流叶片组的数量比及叶片长度比;
(2)调节第五旋流叶片与第六旋流叶片的倾斜角;
(3)调节第七旋流叶片组和第八旋流叶片组的数量比及叶片长度比;
(4)调节第七旋流叶片与第八旋流叶片的倾斜角;
(5)调节第六旋流叶片与第七旋流叶片的倾斜角;
(6)调节第三燃气管1123中的旋流叶片组的数量和叶片长度;
(7)调节第三燃气管1123中的旋流叶片组和第八旋流叶片组的数量比及叶片长度比;
(8)调节第九旋流叶片组和第十旋流叶片组的数量比及叶片长度比;
更多的情况下,通过上述两种或两种以上的调节方式的结合来实现,以达到火焰刚性强、燃烧稳定、不脱火、不回火、火焰不发飘等特点为佳,针对低热值煤气的气体特性,应保证低热值煤气与高热值煤气及作为助燃气的空气混合均匀,以煤气能够燃烧完全为佳。本实施例中,可实现高炉煤气、转炉煤气与助燃空气的体积比在1:1:7~1:3:12范围内调节。
上述调节方式,可通过在燃烧器安装前根据现场的低热值煤气及转炉煤气的特性,通过对应的计算获得所需的各旋流叶片组的参数,选择相应的燃烧器进行安装。更为优选的方式是:在燃烧过程中,可实时调节各旋流叶片的倾斜角,以获得所需的燃烧状况;即每一旋流叶片的两端分别可转动安装于对应的安装部上,根据燃烧器工作环境的特点,每一旋流叶片两端的转轴与对应的轴承之间可采用耐高温润滑脂或耐高温润滑油润滑;每一旋流叶片组的各旋流叶片优选为通过同步传动机构实现同步转动调节,同步传动机构可以是齿轮啮合传动方式等常用的同步传动结构,具体结构此处不再赘述。
另外,可进一步设置监测机构,用于实时监测燃烧器的工作状况,以保证燃烧器安全稳定运行。该监测机构主要包括火焰监测器、压力监测器和温度监测器,可在该燃烧器的远离喷头的一端设置火焰观测孔及火焰监测器用孔。
实施例三
本发明实施例涉及一种燃烧器结构11,用于布置于锅炉1的燃烧室上,其包括第一燃烧器层,所述第一燃烧器层包括布置于所述燃烧室前墙的至少一个第一燃烧器,或包括对冲布置于所述燃烧室前墙和后墙的多个第一燃烧器,各所述第一燃烧器均包括由内而外依次套接的点火气管1111、第一燃气管1112和第一助燃气管1113。
进一步还包括第二燃烧器层,所述第二燃烧器层位于所述第一燃烧器层上方;所述第二燃烧器层包括布置于所述燃烧室前墙的至少一个第二燃烧器,或包括对冲布置于所述燃烧室前墙和后墙的多个第二燃烧器;各所述第二燃烧器均包括自内而外依次套接的第二燃气管1121、第二助燃气管1122、第三燃气管1123和第三助燃气管1124。
其中,优选地,上述各第一燃烧器均采用上述实施例一所提供的燃烧器,上述各第二燃烧器均采用上述实施例二所提供的燃烧器;各第一燃烧器及各第二燃烧器的具体结构此处不再赘述。
实施例四
如图5,本发明实施例涉及一种低热值煤气锅炉1,包括炉体,所述炉体包括有燃烧室、水平烟道和竖直烟道,所述水平烟道内布置有过热器13,所述竖直烟道内自上而下依次布置有再热器14和省煤器15。其中,过热器13的出口端可与外设的蒸汽利用机构的蒸汽入口连通,再热器14的入口端则与上述蒸汽利用机构的蒸汽出口端连通,再热器14的出口端则与该蒸汽利用机构的蒸汽入口连通,省煤器15的入口端则可与连接于上述蒸汽利用机构的乏汽出口端的凝汽机构连接。进一步地,所述燃烧室的内壁至少部分为水冷壁17;优选为该燃烧室的内壁均采用水冷壁17。进一步地,该低热值煤气锅炉1还配置有汽包12,所述汽包12内设有汽水分离装置,所述汽包12具有水出口、水入口、汽水混合物入口和气出口,各所述水冷壁17的入口端均与所述水出口连通,各所述水冷壁17的出口端均与所述汽水混合物入口连通,所述水入口与所述省煤器15的出口端连通,所述气出口与所述过热器13的入口端连通。
上述蒸汽利用机构一般为发电机构,即包括汽轮机2和发电机3。
上述低热值煤气锅炉1中涉及的汽水介质走向大致如下:
低热值煤气在该低热值煤气锅炉1内燃烧,燃烧产生的烟气与所述低热值煤气锅炉1内的换热面换热;其中,在过热器13内产生过热蒸汽,过热蒸汽送至蒸汽利用机构进行利用;
从蒸汽利用机构出来的蒸汽进入再热器14中进行再次加热,从再热器14出来的再热蒸汽进入该蒸汽利用机构进行利用;
从该蒸汽利用机构出来的乏汽经凝汽机构冷凝为冷凝水后,进入省煤器15,从省煤器15出来的水进入汽包12;
在汽包12中,经汽水分离得到的水进入低热值煤气锅炉1的水冷壁17,在水冷壁17中被加热为蒸汽或汽水混合物后回到汽包12;经汽水分离得到的饱和蒸汽进入过热器13中,并被加热为过热蒸汽,再送至蒸汽利用机构进行利用。
进一步优选地,所述竖直烟道内还布置有空气预热器16,所述空气预热器16位于所述省煤器15下方;经空气预热器16预热的空气可作为助燃气在该低热值煤气锅炉1的燃烧器中利用。
实施例五
如图5,本发明实施例涉及一种低热值煤气锅炉1,其基本结构与上述实施例四中的低热值煤气锅炉1的结构相同,在其燃烧室上布置有燃烧器结构11,该燃烧器结构11优选为采用上述实施例三所提供的燃烧器结构11。
通过上述的燃烧器结构11,可保证低热值煤气的稳定燃烧,同时结合上述的锅炉1受热面布置方式和蒸汽介质的一次再热,使得本锅炉1适用于LHV(低热值)在3100kJ/Nm3以上的高炉煤气的发电,可达到13.7MPa/540℃/540℃的高温超高压参数,发电效率达36%以上。
实施例六
如图5,本发明实施例涉及一种低热值煤气发电系统,包括锅炉1及汽轮机2,该锅炉1优选为采用上述实施例四或实施例五提供的低热值煤气锅炉1,该锅炉1的具体结构此处不再赘述;而上述实施例四中涉及的蒸汽利用机构即采用发电机构。上述汽轮机2包括高压缸21和低压缸22,所述高压缸21的蒸汽入口通过第一蒸汽管路与所述过热器13的出口端连通,所述高压缸21的蒸汽出口通过第二蒸汽管路与所述再热器14的入口端连通,所述低压缸22的蒸汽入口通过第三蒸汽管路与所述再热器14的出口端连通。
进一步地,如图5,所述低压缸22的蒸汽出口连接有冷凝管路,所述冷凝管路上设有凝汽器61及凝结水泵62,所述冷凝管路的出口端与所述省煤器15的入口端连通。其中,进一步在所述冷凝管路上还设有低压加热器63和高压加热器66,所述凝汽器61、所述凝结水泵62、所述低压加热器63及所述高压加热器66沿凝结水流通方向依次布置。进一步还可在冷凝管路上设置除氧器64,该除氧器64优选为布置于低压加热器63与高压加热器66之间;进一步还可在冷凝管路上设置给水泵65,该给水泵65优选为布置于除氧器64与高压加热器66之间。上述结构中,凝汽器61可以为卧式或立式结构,优选为采用双流程、单壳体的凝汽器61,其可采用弹性支撑;上述的低压加热器63可以为一级、两级或两级以上;上述的高压加热器66可以为一级、两级或两级以上;上述的除氧器64应能满足系统滑压运行工况。
进一步优化上述系统的结构,如图5和图6,该低热值煤气发电系统还包括高压旁路机构和低压旁路机构;所述高压旁路机构的蒸汽入口端旁接于所述第一蒸汽管路上,所述高压旁路机构的蒸汽出口端旁接于所述第二蒸汽管路上;所述低压旁路机构的蒸汽入口端旁接于所述第三蒸汽管路上,所述低压旁路机构的蒸汽出口端旁接于所述冷凝管路上且旁接点位于所述凝汽器61与所述低压缸22蒸汽出口之间。其中,如图6,所述高压旁路机构包括并联布置的至少一个高压旁路4,各所述高压旁路4上均设有高旁压力阀41,各所述高旁压力阀41的减温水入口端均连接有一高压喷水管路,各所述高压喷水管路上均设有高旁喷水调节阀42和高旁喷水隔离阀43;本实施例中,优选为包括4个上述的高压旁路4,其中,每个高旁压力阀41的最大通流量为汽轮机2调节阀全开功率(VWO)工况下锅炉1主蒸汽流量的25%。所述低压旁路机构包括并联布置的至少一个低压旁路5,各所述低压旁路5上均设有低旁压力阀51,各所述低旁压力阀51的减温水入口端均连接有一低压喷水管路,各所述低压喷水管路上均设有低旁喷水调节阀52和低旁喷水隔离阀53;本实施例中,可仅采用一个上述的低压旁路5,当然可视实际情况增加低压旁路5的数量。
上述高压旁路机构和低压旁路机构的作用在于:(1)改善机组冷、热、温态启动性能。缩短启动时间,形成蒸汽流道,减小启动对于锅炉1燃料量的限制。减小机组热应力,特别是热态启动,提高机组寿命,回收工质。(2)冷却、保护再热器14。(3)锅炉1超压保护。(4)可实现停汽轮机2时甩锅炉1负荷。(5)可以实现停机不停炉,维持锅炉1最低稳燃负荷。具体地:
高压旁路机构的主要作用是在机组启动过程中,通过调整高旁压力阀41的开度来控制主蒸汽压力,以适应机组起动的各阶段对主蒸汽压力的要求。高压旁路机构具有三种控制模式:机组从锅炉1点火、升温、升压到机组带负荷运行至满负荷,高压旁路机构经历阀位方式、定压方式、滑压方式三个控制阶段。
各所述高压旁路4的控制方法均包括:
(1)通过对应的所述高旁压力阀41的开度、对应的所述高旁压力阀41前后蒸汽的焓值及减温水的焓值计算出所需的减温水量,再根据对应的所述高旁喷水调节阀42前后的压力、对应的所述高旁喷水调节阀42的等百分比特性曲线计算出对应的所述高旁喷水调节阀42的开度。
(2)高旁旁路对蒸汽的温度调节目标值的设定值可调,上限根据热力系统计算设置,下限为高旁压力阀41后蒸汽过热度+30℃。
(3)高压旁路减温水截止门也随高旁压力阀41联动。这要在所有操作模式中进行精确的蒸汽温度控制,要求控制器能很好地匹配高压旁路4的各种运行情况(低负荷、高负荷下的快开等),在所有运行情况下进行精确的温度控制,对于保护承受强大压力的阀门和管道来说至关重要。
(4)高旁压力阀41具有过热器13安全保护功能,能够快速开启,具有2种快速开启阀门方式:通过DCS控制逻辑快速开启高旁压力阀41,开启时间≤10s;通过控制台操作按钮及就地压力开关安全快速开启回路开启阀门,即当操作按钮按下或者压力开关动作时,安全快速开启回路开启高旁压力阀41,开启时间≤2s。
(5)高压旁路机构具有快开功能,主蒸汽压力与设定值偏差大于设定偏差值时,汽机跳闸,操作员发出快开指令。
各所述低压旁路5的控制方法均包括:
(1)对应的低旁压力阀51开启(开度>3%)时联锁开启对应的低旁喷水隔离阀53;对应的低旁压力阀51全关(开度<2.5%)时延时15秒关闭低旁喷水隔离阀53。低旁喷水隔离阀53也可以根据操作员的指令开关。
(2)在低旁压力阀投自动、低旁压力阀51快开或者快关时,低旁喷水调节阀52自动切为自动控制。
(3)通过对应的低旁压力阀51的开度、对应的低压旁路5前后蒸汽的焓值和减温水的焓值计算出所需的减温水量,再根据对应的低旁喷水调节阀52前后的压力、对应的低旁喷水调节阀52的等百分比特性曲线计算出对应的低旁喷水调节阀52的开度。
(4)低压旁路机构具有快开快关功能。当高压旁路4快开时,联动低压旁路5快开。当有至少一种如下情形发生时,低压旁路5快关机构动作:凝汽器61真空低、凝汽器61温度高、凝汽器61水位高、减温水压力低。
实施例七
本发明实施例涉及一种采用低热值煤气发电的方法,包括如下步骤:
步骤一,将LHV在3100kJ/Nm3以上的低热值煤气送入低热值煤气锅炉1内燃烧,燃烧产生的烟气与所述低热值煤气锅炉1内的换热面换热;其中,在过热器13内产生13.7MPa、540℃的高温超高压的过热蒸汽,过热蒸汽送至汽轮机2的高压缸21中进行发电;
步骤二,从汽轮机2高压缸21中出来的蒸汽进入再热器14中进行再次加热,从再热器14出来的再热蒸汽进入低压缸22进行发电;
步骤三,从低压缸22出来的蒸汽经冷凝为冷凝水后,进入省煤器15,从省煤器15出来的水进入汽包12;
步骤四,在汽包12中,经汽水分离得到的水进入低热值煤气锅炉1的水冷壁17,在水冷壁17中被加热为蒸汽或汽水混合物后回到汽包12;经汽水分离得到的饱和蒸汽进入过热器13中,并被加热为13.7MPa、540℃的高温超高压的过热蒸汽,再送至汽轮机2的高压缸21进行发电;
步骤五,循环进行上述步骤二至步骤四。
其中,上述的低热值煤气锅炉1采用上述实施例四或实施例五所提供的低热值煤气锅炉1。
以上所述仅为本发明的较佳实施例而已,并不用以限制本发明,凡在本发明的精神和原则之内,所作的任何修改、等同替换、改进等,均应包含在本发明的保护范围之内。