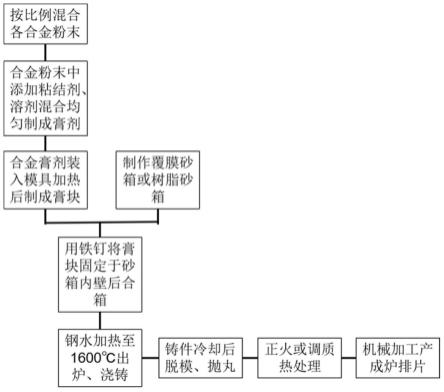
1.本发明涉及垃圾焚烧配件技术领域,尤其涉及一种垃圾焚烧炉用一体铸造复合耐磨炉排片制作工艺。
背景技术:2.炉排片是垃圾焚烧炉中机械炉排的主要部件,垃圾在炉排上燃烧。垃圾焚烧炉运行过程中,各级炉排进行不间断的往复运动,使垃圾不断翻转保证垃圾的充分燃烧。在这个过程中,由于上下级炉排片之间、炉排与垃圾之间存在着相互摩擦,同时由于垃圾分类不充分,其中还经常混入一些高硬度制品,造成实际运行中的炉排片工作面极易磨损,这就要求炉排片的工作面必须具备较好的耐磨性,炉排片作为燃烧的承载面,在提高耐磨性的基础上也要兼顾考虑耐热性。炉排是垃圾的主要载体,在往复运动过程中需承受较大的拉应力,同时由于垃圾成分复杂使得在燃烧过程中炉内极易发生结焦现象,当焦块较大时掉落在炉排上容易砸断炉排片,因此要求炉排片必须具备一定的抗拉强度、冲击韧性和塑性。但金属材料的硬度与塑性是负相关关系,现在常用的铸造方法往往无法同时提升这两个指标。
3.现有垃圾焚烧炉中的炉排片都是采用铸造工艺制成。铸成的炉排片通体为一种材料,炉排片的力学性能取决于铸造材料以及铸造工艺。但铸造成型后,硬度较高的炉排片强度和抗冲击能力往往均较差,强度和抗冲击能力好的炉排片往往耐磨性较差。同时由于铸造工艺的缺陷,成型的炉排片中还经常存在气孔、裂纹、凹坑等缺陷,加剧了炉排片的失效断裂。
4.对于运营企业,当炉排片磨损较大时或断裂后须尽快停炉进行更换,而停炉更换炉排片是一项耗时、耗力、成本投入巨大的工作,更换后的旧炉排片往往作为废品处理,也造成了极大的材料浪费,不利于节能环保,也给企业增加了运营成本支出。
技术实现要素:5.本发明的目的在于提出一种垃圾焚烧炉用一体铸造复合耐磨炉排片制作工艺,通过在铸造砂箱内壁镶嵌合金膏块,烘烤后浇铸钢水直接成型的以铸钢为炉排片基体、表面覆盖耐磨合金层的垃圾焚烧炉用一体铸造复合耐磨炉排片。成型后的一体铸造复合耐磨炉排片工作面具有耐热、高硬度,炉排片基体具备高抗拉强度、冲击韧性和塑性的力学性能特征,从而可以大幅提升炉排片使用寿命,降低企业运营成本。
6.为达此目的,本发明采用以下技术方案:
7.一种垃圾焚烧炉用一体铸造复合耐磨炉排片制作工艺,通过在铸造砂箱内壁镶嵌合金膏块,烘烤后浇铸钢水直接成型的以铸钢为炉排片基体、表面覆盖耐磨合金层的垃圾焚烧炉用一体铸造复合耐磨炉排片。
8.所述垃圾焚烧炉用一体铸造复合耐磨炉排片制作工艺具体包括以下步骤。
9.a、合金膏剂制作,所述合金膏剂包括合金粉末、硅酸钠水溶液、硼砂构成,所述合金粉末由铬碳粉、硅铁粉、锰铁粉、硼铁粉、钼铁粉、还原铁、钒铁粉按比例混合得到,在所述
合金粉末中添加硅酸钠水溶液、硼砂混合均匀。
10.b、所述合金膏块制作,将所述合金膏剂压入模具中,加热模具至不低于200℃,待固化后脱模制成合金膏块。
11.c、所述合金膏块定位,将所述合金膏块利用小铁钉固定于所述铸造砂箱内壁上,合上铸造砂箱。
12.d、所述合金膏块烘烤,所述合金膏块定位后,需进行烘烤,直至所述合金膏块内的水分完全烘出。
13.e、所述炉排片基体铸造,所述钢水浇注所述铸造砂箱,使钢水通过毛细渗透作用将所述合金膏块熔化并与之铸为一体。
14.f、铸件冷却后脱模、抛丸。
15.g、所述铸件热处理。
16.优选的,所述合金粉末粒径均为0.15-0.4mm,所述合金粉末各成分纯度及比例为。
17.高碳铬铁粉,纯度55%,质量配比36.4%。
18.硅铁粉,纯度为65%,质量配比1.8%。
19.锰铁粉,纯度60%,质量配比6%。
20.硼铁粉,纯度为20%,比例为4%。
21.钼铁粉,纯度60%,质量配比3.3%。
22.还原铁粉,纯度>98%,质量配比44.5%。
23.钒铁粉,纯度50%,质量配比4%。
24.优选的,所述硅酸钠水溶液质量比例为所述合金膏块质量的8%-10%。
25.优选的,所述硼砂质量比例为合金膏块质量的3%。
26.优选的,步骤d中所述合金膏块烘烤,烘烤温度不低于200℃,烘烤时间不少于2小时。
27.优选的,所述钢水为zg42crmo低合金钢,其余成分为:碳质量配比0.38-0.45%、硅质量配比0.6%、锰质量配比0.6-1.0%、磷质量配比0.025%、硫质量配比0.02%、铬质量配比0.8-1.2%、钼质量配比0.15-0.3%、镍质量配比0.4%、钒质量配比0.05%、铜质量配比0.3%。
28.优选的,步骤e中所述钢水出炉温度不低于1600℃,浇注温度不低于1560℃,同时钢水浇注过程连续不间断。
29.优选的,步骤g中热处理工艺为正火或调质处理。
30.优选的,所述合金膏块的厚度为4-5mm,所述钢水浇注成型的所述炉排片基体厚度不低于14mm。
31.本发明的有益效果为:
32.1、以本发明专利配比、制作的所述合金膏块经工艺成型的表面覆盖耐磨合金层作为炉排片工作面具有耐热、高硬度,有效减少了炉排片往复运动中上下级炉排片之间、炉排片与焚烧物之间造成的磨损。
33.2、以本发明专利配比、制作的所述以铸钢为炉排片基体,可以极大提升塑性指标,抗冲击能力好。
34.3、耐磨合金层与浇铸钢水成型的炉排片基体间以冶金态结合,结合强度高,解决
了目前炉排片铸造中硬度与塑性两指标不能兼容的问题,可以极大提升炉排片使用寿命,降低企业运行成本。
35.4、形成耐磨合金层所采用的合金膏剂由合金粉末、硅酸钠水溶液、硼砂构成,各组分简单易得,价格低廉;铸造工艺简单,适合大规模生产。
附图说明
36.图1是本发明一种垃圾焚烧炉用一体铸造复合耐磨炉排片制作工艺一个实施例的工艺流程图;
37.图2是本发明一种垃圾焚烧炉用一体铸造复合耐磨炉排片的三维立体图。
38.其中,耐磨合金层1、炉排片基体2。
具体实施方式
39.下面结合附图及具体实施方式进一步说明本发明的技术方案。
40.步骤a合金膏剂制作,所述合金膏剂包括合金粉末、硅酸钠水溶液、硼砂构成,硅酸钠水溶液作为粘结剂,使用该无机粘结剂的生产成本远低于树脂类有机粘结剂,无需酒精进行稀释,且粘结强度更高;硼砂作为熔剂,可以在浇铸初期保护合金粉末不受氧化,受热熔化后即能去除铁合金粉末表面的氧化膜;合金粉末由铬碳粉、硅铁粉、锰铁粉、硼铁粉、钼铁粉、还原铁、钒铁粉按比例混合得到,合金粉末的选择主要为加强耐磨合金层的耐磨、耐热、高硬度综合考虑实践得到,使用高碳铬铁粉可以在合金层中形成cr7c3等高硬度相组织,从而达到耐磨的效果,铬元素的加入也同时提高了合金层的耐热、耐蚀性。
41.步骤b所述合金膏块制作,将合金粉末按比例预混合,添加粘结剂(硅酸钠水溶液)、熔剂(硼砂)混合均匀后压入膏块模具中,模具中安装有电加热棒,通电加热至不低于200℃,待固化后脱模制成合金膏块,合金膏块和根据模具进行各面特定形状,以配合后续铸造砂箱内与钢水的冶金态结合。
42.步骤c所述合金膏块定位,用小铁钉固定于所述铸造砂箱内壁上,防止钢水浇铸时合金膏块脱落或移位。
43.步骤d所述合金膏块烘烤,所述合金膏块定位后,需进行烘烤,直至所述合金膏块内的水分完全烘出,烘烤是为了把合金膏块里面的水蒸气烤出来,如果有游离水或结晶水,会导致耐磨合金层有缺陷。
44.步骤e所述炉排片基体铸造,通过铸造砂箱,将所述合金膏块定位在所述铸造砂箱内壁上,钢水浇注所述铸造砂箱,使钢水通过毛细渗透作用将所述合金膏块熔化并与之铸为一体,通过该方式致使耐磨合金层与浇铸钢水成型的炉排片基体间以冶金态结合。
45.步骤f铸件冷却后脱模、抛丸。
46.步骤g所述铸件热处理,耐磨合金层含碳量高,热处理对耐磨合金层硬度影响不大,热处理工艺参数主要应考虑炉排片基体材质的性能调整优化,但也不应因此工序导致合金层产生破坏性缺陷。
47.优选的,所述合金粉末粒径均为0.15-0.4mm,所述合金粉末各成分纯度及比例为。
48.高碳铬铁粉,纯度55%,质量配比36.4%。
49.硅铁粉,纯度为65%,质量配比1.8%。
50.锰铁粉,纯度60%,质量配比6%。
51.硼铁粉,纯度为20%,比例为4%。
52.钼铁粉,纯度60%,质量配比3.3%。
53.还原铁粉,纯度>98%,质量配比44.5%。
54.钒铁粉,纯度50%,质量配比4%。
55.优选的,所述硅酸钠水溶液质量比例为所述合金膏块质量的8%-10%。硅酸钠水溶液用量<8%则合金膏块粘结强度不够,脱模时容易破碎,硅酸钠水溶液用量>10%则最终形成的耐磨合金层容易发生气孔缺陷。
56.优选的,所述硼砂质量比例为合金膏块质量的3%。
57.优选的,步骤d中所述合金膏块烘烤,烘烤温度不低于200℃,烘烤时间不少于2小时。烘烤方式可以为电阻炉烘烤或人工喷枪火烤,该烘烤温度与时间能保证合金膏块里面的水蒸气烤出来。
58.优选的,所述钢水为zg42crmo低合金钢,其余成分为:碳质量配比0.38-0.45%、硅质量配比0.6%、锰质量配比0.6-1.0%、磷质量配比0.025%、硫质量配比0.02%、铬质量配比0.8-1.2%、钼质量配比0.15-0.3%、镍质量配比0.4%、钒质量配比0.05%、铜质量配比0.3%。该配比铸造的炉排片基体在不高于300℃的环境中使用,也具有较高的热强度,且具备高碳高铬铸钢无法达到的塑韧性。
59.优选的,步骤e中所述钢水出炉温度不低于1600℃,浇注温度不低于1560℃,同时钢水浇注过程连续不间断。若钢水浇注间断,则会发生合金膏块不熔或气孔、夹渣缺陷。
60.优选的,步骤g中热处理工艺为正火或调质处理。热处理时,正火/调质保温时间不宜过长,减少合金层碳元素的迁移,保证基体金属良好的力学性能。热处理工艺参数主要应考虑基体材质的性能调整优化,但也不应因此工序导致合金层产生破坏性缺陷。
61.优选的,所述合金膏块的厚度为4-5mm,所述钢水浇注成型的所述炉排片基体厚度不低于14mm。合金膏块厚度超过5mm(即炉排片基体厚度的1/3),则钢水热量不足以熔化合金膏块合金粉末,无法形成完整的耐磨合金层。
62.实施例1:合金粉末按高碳铬铁粉,纯度55%,质量配比36.4%;硅铁粉,纯度为65%,质量配比1.8%;锰铁粉,纯度60%,质量配比6%;硼铁粉,纯度为20%,比例为4%;钼铁粉,纯度60%,质量配比3.3%;还原铁粉,纯度为99%,质量配比44.5%;钒铁粉,纯度50%,质量配比4%;粒径均为0.15mm预混合,添加合金膏块质量8%的硅酸钠水溶液,添加合金膏块质量3%的硼砂,混合均匀后压入膏块模具中,模具中安装有电加热棒,通电加热至200℃,待固化后脱模制成厚度为4mm的合金膏块;用小铁钉将合金膏块固定于所述铸造砂箱内壁上,利用人工喷枪对合金膏块进行200℃的烘烤2.5个小时,铸造砂箱采用钢水底注法,设置多个内浇道且与炉排片侧面连接,避免浇注时钢水直接冲刷合金膏块,砂箱分型面的选择应确保膏块的完整性并便于镶嵌,钢水为zg42crmo低合金钢,其余成分为:碳质量配比0.38%、硅质量配比0.6%、锰质量配比0.6%、磷质量配比0.025%、硫质量配比0.02%、铬质量配比0.8%、钼质量配比0.15%、镍质量配比0.4%、钒质量配比0.05%、铜质量配比0.3%;保证在出炉温度1600℃,浇注温度1560℃状态下浇注,同时钢水浇注过程连续不间断;钢水会通过毛细渗透作用将合金膏块熔化并与之铸为一体,铸件冷却后脱模、抛丸;采用正火方式进行热处理。
63.实施例2:合金粉末按按高碳铬铁粉,纯度55%,质量配比36.4%;硅铁粉,纯度为65%,质量配比1.8%;锰铁粉,纯度60%,质量配比6%;硼铁粉,纯度为20%,比例为4%;钼铁粉,纯度60%,质量配比3.3%;还原铁粉,纯度为99%,质量配比44.5%;钒铁粉,纯度50%,质量配比4%;粒径均为0.4mm预混合,添加合金膏块质量10%的硅酸钠水溶液,添加合金膏块质量3%的硼砂,混合均匀后压入膏块模具中,模具中安装有电加热棒,通电加热至210℃,待固化后脱模制成厚度为5mm的合金膏块;用小铁钉将合金膏块固定于所述铸造砂箱内壁上,利用电阻炉烘烤对合金膏块进行210℃的烘烤2个小时,铸造砂箱采用钢水底注法,设置多个内浇道且与炉排片侧面连接,避免浇注时钢水直接冲刷合金膏块,砂箱分型面的选择应确保膏块的完整性并便于镶嵌,钢水为zg42crmo低合金钢,其余成分为:碳质量配比0.45%、硅质量配比0.6%、锰质量配比1.0%、磷质量配比0.025%、硫质量配比0.02%、铬质量配比1.2%、钼质量配比0.3%、镍质量配比0.4%、钒质量配比0.05%、铜质量配比0.3%;保证在出炉温度1700℃,浇注温度1650℃状态下浇注,同时钢水浇注过程连续不间断;钢水会通过毛细渗透作用将合金膏块熔化并与之铸为一体,铸件冷却后脱模、抛丸;采用调质方式进行热处理。
64.以上结合具体实施例描述了本发明的技术原理。这些描述只是为了解释本发明的原理,而不能以任何方式解释为对本发明保护范围的限制。基于此处的解释,本领域的技术人员不需要付出创造性的劳动即可联想到本发明的其它具体实施方式,这些方式都将落入本发明的保护范围之内。