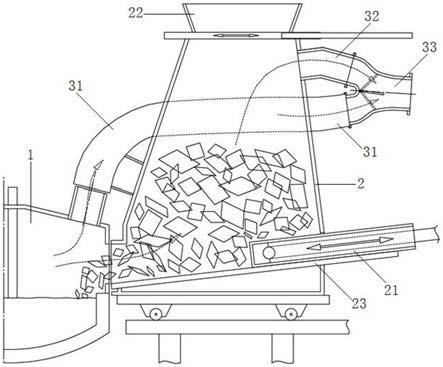
1.本发明属于电炉炼钢技术领域,具体涉及一种电炉烟气处理系统、配置有该电炉烟气处理系统的环保型炼钢电弧炉以及一种电炉炼钢生产方法。
背景技术:2.现代超高功率电弧炉炼钢过程中,由排放烟气带走的热量约占输入电能的一半,如此多的热量任由其耗散在排烟管道和周围环境中,是对资源和能源的极大浪费。为此,用排放烟气中蕴含的热量将入炉前的废钢加热到一定水平的废钢预热技术被开发出来;此类技术可以将烟气中的热量部分回收至预热后的废钢中,一方面可以减少烟气排放热量的浪费,另一方面预热后的废钢熔化需要的能量和时间减少,可实现降低冶炼能源消耗且提升生产率的双重功效。
3.如若用于电弧炉炼钢的废钢是清洁的,那么此类技术可以比较完美地实现对烟气中热量的部分回收,而不会对周边环境造成负面影响;所谓的清洁,是指废钢中不含油脂、油漆和塑料等有机化合物,特别是含氯的有机化合物。然而,清洁的废钢通常意味着来源少、价格高,这对于炼钢生产率和成本控制是不利的。来源广、价格低的废钢通常是社会废钢,此类废钢来自社会上各行各业的废弃产品,且回收过程中混杂在一起,基本上都不是清洁的。在利用烟气热量预热此类废钢过程中,烟气在其流动的上游阶段温度较高,可将废钢中混杂的有机化合物分解成有机小分子、一氧化碳和二氧化碳等的混合物;在流动过程中随着烟气的热量不断传递给温度较低的废钢,烟气温度不断降低;一般地,当温度降低至约850~250℃的区间时,烟气内含有的这些混合物开始反应并快速生成高致癌的二噁英。如果后续没有针对二噁英的处理措施,其将随除尘后的除尘灰和尾气进入生产和生活环境,对人类和其它生物的健康造成永久性伤害。
4.目前行之有效的处理措施是:将富含二噁英且温度较低的烟气用烧嘴加热至900℃以上并保持一定的时间,让二噁英在此高温下充分分解;然后,以喷淋水雾冷却的方式将其快速冷却至约250℃以下。如若不然,二噁英的分解产物在随后的缓慢冷却经历约850~250℃的区间时,又将重新反应并快速生成二噁英。但是,烧嘴的燃烧需要额外消耗天然气,对于天然气供应充足且价格合理的地区,这种方法是经济上较为可行的,反之,则需要其它的可替代方案。
技术实现要素:5.本发明涉及一种电炉烟气处理系统、配置有该电炉烟气处理系统的环保型炼钢电弧炉以及一种电炉炼钢生产方法,至少可解决现有技术的部分缺陷。
6.本发明涉及一种电炉烟气处理系统,包括烟气混合管道、与电炉烟道连接的第一烟气出口管以及与电炉废钢入口连接的废钢预热装置,所述废钢预热装置配置有第二烟气出口管,所述第一烟气出口管和所述第二烟气出口管均与所述烟气混合管道的入口端连通。
7.作为实施方式之一,所述烟气混合管道的入口端设有两进一出式三通调节阀,所述第一烟气出口管和所述第二烟气出口管分别与所述三通调节阀的两个入口端连接。
8.作为实施方式之一,所述三通调节阀为水冷阀。
9.作为实施方式之一,所述废钢预热装置包括废钢预热井,所述废钢预热井设有推钢机以及适于与电炉废钢入口对接的装料口,所述推钢机与所述装料口相对设置。
10.作为实施方式之一,所述废钢预热井为立式结构,在所述废钢预热井的顶部设有废钢受料斗。
11.作为实施方式之一,所述废钢预热井的底部设有行走机构。
12.本发明还涉及一种环保型炼钢电弧炉,包括电炉炉体,所述电炉炉体具有电炉烟道和电炉废钢入口,还包括如上所述的电炉烟气处理系统。
13.作为实施方式之一,所述电炉废钢入口开设于所述电炉炉体的炉壳侧壁上。
14.本发明还涉及一种电炉炼钢生产方法,包括:
15.电炉炼钢产生的电炉烟气中,一部分直接引出作为第一烟气,剩余部分在预热废钢后排出形成第二烟气,将第一烟气与第二烟气混合,其中,通过第一烟气与第二烟气的流量分配控制使混合烟气的温度在900℃以上。
16.作为实施方式之一,上述生产方法还包括:在电炉主熔化期,当炉膛内形成熔池后,打开炉壁氧枪和碳枪,开始往熔池吹氧喷碳造泡沫渣;当熔池液面以上的废钢接近全部熔化时,电弧被泡沫渣良好覆盖;
17.当熔池液面上升高度达到一定值时,将预热后的废钢分批加入电炉熔池内,废钢熔化速率与电弧输入功率及废钢加入速率相匹配,保证熔化过程全程泡沫渣覆盖熔池,实现钢液的良好精炼和熔渣的自动流出;
18.当熔池内钢液重量达到留钢和出钢要求时,测量钢液的温度和成分,当温度和成分满足出钢要求时,开始出钢,出钢重量达到目标值时停止出钢,熔池内留下一定比例的钢液和熔渣,以便于下一个冶炼循环的开启。
19.本发明至少具有如下有益效果:
20.本发明中,将一部分电炉烟气引出用于预热废钢,以实现对烟气余热的初步利用,另一部分电炉烟气直接引出并与预热废钢后的烟气进行混合,废钢预热装置排出的烟气中可能含有的二噁英可被用高温电炉烟气充分分解,因此,利用电炉烟气自身热量能同时实现废钢预热以及对废钢预热过程中产生的二噁英的处理,不需要额外消耗天然气等能源,环保性和经济性较佳。
附图说明
21.为了更清楚地说明本发明实施例或现有技术中的技术方案,下面将对实施例或现有技术描述中所需要使用的附图作简单地介绍,显而易见地,下面描述中的附图仅仅是本发明的一些实施例,对于本领域普通技术人员来讲,在不付出创造性劳动的前提下,还可以根据这些附图获得其它的附图。
22.图1为本发明实施例二提供的环保型炼钢电弧炉的结构示意图;
23.图2为本发明实施例四提供的自适应流量调节阀的安装结构示意图;
24.图3为本发明实施例四提供的自适应流量调节阀的结构示意图。
具体实施方式
25.下面对本发明实施例中的技术方案进行清楚、完整地描述,显然,所描述的实施例仅仅是本发明一部分实施例,而不是全部的实施例。基于本发明中的实施例,本领域普通技术人员在没有做出创造性劳动前提下所获得的所有其它实施例,都属于本发明保护的范围。
26.实施例一
27.如图1,本发明实施例提供一种电炉烟气处理系统,包括烟气混合管道33、与电炉烟道连接的第一烟气出口管31以及与电炉废钢入口连接的废钢预热装置,所述废钢预热装置配置有第二烟气出口管32,所述第一烟气出口管31和所述第二烟气出口管32均与所述烟气混合管道33的入口端连通。
28.上述电炉烟道可以是电炉炉盖上的第四孔烟道,可为电炉熔池炼钢反应过程产生的高温烟气提供排出通道;上述电炉废钢入口根据电炉加废钢设计要求可位于电炉炉盖上或者位于电炉炉壳侧壁,电炉烟气一部分可经该电炉废钢入口排出而进入废钢预热装置进行废钢预热操作,一部分可经上述电炉烟道排出,在无其它烟气排出通道的情况下,电炉烟气分为上述的两部分烟气气流。
29.本实施例提供的电炉烟气处理系统,将一部分电炉烟气引出用于预热废钢,以实现对烟气余热的初步利用,另一部分电炉烟气直接引出并与预热废钢后的烟气进行混合,废钢预热装置排出的烟气中可能含有的二噁英可被用高温电炉烟气充分分解,因此,利用电炉烟气自身热量能同时实现废钢预热以及对废钢预热过程中产生的二噁英的处理,不需要额外消耗天然气等能源,环保性和经济性较佳。
30.优选地,可在上述烟气混合管道33的入口端设置三通,该三通具有两个入口端和一个出口端,两个入口端分别与上述第一烟气出口管31和第二烟气出口管32连接,该三通的出口端即与该烟气混合管道33连接。
31.进一步地,为保证对二噁英的处理效果,优选为保证混合后的烟气温度在900℃以上,该目标温度可通过调节分配第一烟气出口管31和第二烟气出口管32的流量来实现,当然,需考虑电炉烟气产量以及废钢预热装置中的废钢量等因素,尽量在保证废钢预热效果的同时能够实现二噁英的充分分解;由于随着电炉冶炼进程的延续,电炉烟气持续地产生,废钢预热装置中的废钢预热效果一般能够得以保证。
32.在其中一个实施例中,上述流量分配调节可通过三通调节阀实现,也即所述烟气混合管道33的入口端设有两进一出式三通调节阀,所述第一烟气出口管31和所述第二烟气出口管32分别与所述三通调节阀的两个入口端连接。该三通调节阀显然可以调节其两个入口端的烟气流量,该阀门可由市面购得,具体结构此处不作赘述。优选地,该三通调节阀为水冷阀,工作可靠性高,具有较长的服役寿命。
33.为避免混合烟气在后续处理过程中重新产生二噁英,上述混合烟气管道可连接喷淋冷却装置,例如采用蒸发冷却器对混合烟气进行快速冷却。
34.接续上述电炉烟气处理系统,如图1,所述废钢预热装置包括废钢预热井2,所述废钢预热井2设有推钢机21以及适于与电炉废钢入口对接的装料口,所述推钢机21与所述装料口相对设置。在其中一个实施例中,该废钢预热井2为立式结构,即该废钢预热井2为竖井;进一步地,在该废钢预热井2的顶部设有废钢受料斗22,在该废钢受料斗22的底部设有
加料阀,在需要向废钢预热井2内补充废钢时此阀打开,加料完毕后此阀关闭,可为废钢预热井2提供封闭环境条件,该废钢受料斗22用于向废钢预热井2加入废钢时提供支撑和导向,也用于在加料阀打开时对上升的烟气流股进行导向。
35.如图1,上述电炉废钢入口开设在电炉炉体1的炉壳侧壁上,废钢预热井2的装料口位于其井壁上,则该废钢预热井2布置于电炉炉体1的侧方,而非正上方,一则可以降低厂房的高度、节约投资成本;一则即使废钢预热井2的水冷元件漏水,也不会进入电炉熔池,从而避免蒸汽闪爆对设备和人身造成的威胁,而废钢预热井2的水冷元件数量众多,冶炼过程发生漏水的概率很高。
36.可选地,如图1,在上述废钢预热井2的底部设有耐冲击耐磨底板23,用于吸收废钢加入至井内过程中的跌落冲击能量,同时能够耐受废钢在底板23上的滑动过程造成的磨损。上述推钢机21可布置在该底板23上,能够将滞留在底板23上的预热废钢推动并经由装料口和电炉废钢入口进入电炉内;该推钢机21可采用液压缸作为动力。
37.进一步优选地,如图1,所述废钢预热井2的底部设有行走机构,使得该废钢预热井2可以移动,灵活度高,不仅可便于电炉冶炼生产控制,也能适用于不同的电炉冶炼生产,而且便于废钢预热井2和电炉的检修。
38.当然,本领域其他结构的废钢预热装置也适用于本实施例中,此处不作一一例举。
39.实施例二
40.如图1,本发明实施例提供一种环保型炼钢电弧炉,包括电炉炉体1以及上述实施例一所提供的电炉烟气处理系统,所述电炉炉体1具有电炉烟道和电炉废钢入口,显然,该电炉烟道与上述第一烟气出口管31连接,该电炉废钢入口与上述废钢预热装置连接。
41.该电炉烟道及电炉废钢入口在电炉炉体1上的设置在上述实施例一中已有述及,此处不作赘述。
42.实施例三
43.本发明实施例提供一种电炉炼钢生产方法,包括:
44.电炉炼钢产生的电炉烟气中,一部分直接引出作为第一烟气,剩余部分在预热废钢后排出形成第二烟气,将第一烟气与第二烟气混合,其中,通过第一烟气与第二烟气的流量分配控制使混合烟气的温度在900℃以上。
45.该电炉炼钢生产方法可基于上述实施例一所提供的电炉烟气处理系统或实施例二所提供的环保型炼钢电弧炉实现。
46.进一步地,上述生产方法还包括:在电炉主熔化期,当炉膛内形成熔池后,打开炉壁氧枪和碳枪,开始往熔池吹氧喷碳造泡沫渣;当熔池液面以上的废钢接近全部熔化时,电弧被泡沫渣良好覆盖;
47.当熔池液面上升高度达到一定值时,将预热后的废钢分批加入电炉熔池内,废钢熔化速率与电弧输入功率及废钢加入速率相匹配,保证熔化过程全程泡沫渣覆盖熔池,实现钢液的良好精炼和熔渣的自动流出;
48.当熔池内钢液重量达到留钢和出钢要求时,测量钢液的温度和成分,当温度和成分满足出钢要求时,开始出钢,出钢重量达到目标值时停止出钢,熔池内留下一定比例的钢液和熔渣,以便于下一个冶炼循环的开启。
49.其中,在第一炉冶炼前,可使上述废钢预热井2移动至远离电炉炉体1,让出炉盖打
开所需空间,随后电炉炉盖打开,用吊车将装有指定重量废钢的料篮移动至电炉炉体1正上方,料篮下降至一定高度后打开料篮底部将废钢落入电炉炉体1内,料篮提升、移走后关闭电炉炉盖。随后,使上述废钢预热井2移动至与电炉炉体1连接,向废钢预热井2内加入一定重量的废钢后关闭加料阀;向废钢预热井2加废钢的方式,可以有料篮加料、输送带加料和小车斜坡上料等形式,加料时可以在废钢受料斗22上设置烟罩,以便更好地捕集加料阀打开过程由井内逸散的烟尘。
50.在接下来的冶炼循环中,不用再通过打开炉盖向电炉炉体1内加入废钢,废钢全部经由废钢预热井2预热后进入电炉炉体1内。当废钢预热井2内现存的废钢重量降低至一定水平时及时补加即可,以实现废钢预热井2内烟气流动的适宜阻力和良好的废钢预热效果。一般地,对应一炉出钢重量的废钢预热井2废钢加料次数为2~4次,视井内废钢的堆密度而定。
51.由于废钢预热井2内预热后的废钢小批次近乎连续地加入电炉内,每次加入的那一小批次都接近预热至最高温度,可实现烟气热量的最大化回收。另外,由于每加入一小批次废钢所占据的熔池空间都不太多,因此无需设计专门的电弧炉炉膛及熔池,将传统非预热型超高功率电弧炉稍加改动便可成为上述环保型电弧炉,可实现现有设备的利旧改造。
52.实施例四
53.本发明实施例提供一种电弧炉,可作为上述实施例二所提供的环保型炼钢电弧炉的进一步优化。
54.该电弧炉包括炉壳和炉盖,所述炉壳及所述炉盖均内嵌有水冷面板11,对于水冷面板11在炉壳内以及在炉盖内的设置均为本领域常规技术,此处不作赘述。
55.优选地,所述炉壳的水冷面板11和/或所述炉盖的水冷面板11为长寿型面板,所述长寿型面板的冷却水流量可调。其中,优选为炉壳内的水冷面板11和炉盖内的水冷面板11均采用该长寿型面板。本实施例提供的电弧炉,通过设计水冷面板11的冷却水流量可调,可根据炼钢过程的冶炼工况,按需实时调节当前水冷面板11的冷却水流量,使得调节后的冷却水流量正好匹配当前水冷面板11的热负荷要求,而不会造成冷却水流量的过量和相应的动力消耗损失,同时也不至于大幅提升冷却水出口平均温度,避免水冷面板11局部位置处因冷却水流速较低产生欠热沸腾而导致传热能力恶化的情况,提高水冷面板11的服役寿命。
56.一般地,水冷面板11配置有冷却水循环管路,也即上述长寿型面板配置有冷却水循环管路,其中,该冷却水循环管路包括连接面板入水口与冷却水给水主管141的进水管路131以及连接面板出水口与冷却水回水主管142的回水管路132。
57.基于上述冷却水流量可调的需求,在其中一个实施例中,可在上述冷却水循环管路上设有流量调节单元,例如在进水管路131和/或回水管路132上设置流量控制阀,进一步可在该水冷面板11的安装处设置测温传感器,通过该测温传感器与流量控制阀联锁,可实现对水冷面板11冷却水流量的自动调节。当然,在水冷面板11的蛇形管道内设置流量调节阀等也为可行方案,但考虑水冷面板11工作环境的恶劣程度,此处设置的流量调节阀需选用耐高温阀门。
58.本实施例提供一种优选方案,可在不需要消耗外部能源、也不涉及控制信号收发的情况下实现上述冷却水流量自适应调节的目的,具体地:
59.如图2和图3,所述流量调节单元包括自适应流量调节阀12,所述自适应流量调节阀12包括阀壳121、中空芯壳122和调节机构,所述芯壳122固定安装于所述阀壳121内并将阀壳121内腔分隔为冷水流通室和热水流通室,所述芯壳122内滑设有隔热活塞123并将芯壳122内腔分隔为冷腔和热腔,所述冷腔与所述热腔内均填充有热变形介质125,所述冷腔至少部分位于所述冷水流通室内,所述热腔至少部分位于所述热水流通室内;所述调节机构与所述隔热活塞123连接并且调节区位于所述冷水流通室或所述热水流通室内;所述阀壳121上开设有与所述冷水流通室连通的冷水入口1211和冷水出口1212,所述进水管路131包括连接所述冷水入口1211与所述冷却水给水主管141的第一进水管段以及连接所述冷水出口1212与所述面板入水口的第二进水管段;所述阀壳121上开设有与所述热水流通室连通的热水入口1213和热水出口1214,所述回水管路132包括连接所述面板出水口与所述热水入口1213的第一回水管段以及连接所述热水出口1214与所述冷却水回水主管142的第二回水管段。
60.上述阀壳121与第一进水管段之间、阀壳121与第二进水管段之间、阀壳121与第一回水管段之间以及阀壳121与第四回水管段之间均可采用法兰连接形式。上述芯壳122部分伸入至冷水流通室内,以便使得其冷腔至少部分地位于冷水流通室内;同样地,上述芯壳122部分伸入至热水流通室内,以便使得其热腔至少部分地位于热水流通室内。上述芯壳122显然应具有一个直线段,以便于隔热活塞123作直线运动,该直线段可采用方形或圆形截面,依隔热活塞123的形状而定;在其中一个实施例中,该芯壳122可采用长条形壳体,在另外的实施例中,可在上述直线段的两端分别连接球状壳体段,两个球状壳体段分别伸入至冷水流通室和热水流通室内。
61.如图3,在芯壳122伸入处,可将阀壳121设计成球状/近似球状,保证伸入的芯壳122四周都能接触到水流,水流在芯壳122周围形成绕流,换热效果较好,能提高芯壳122感温准确性和响应速度。
62.进一步地,上述芯壳122优选为采用导热性较好的材料,例如选用导热系数大、比热容低的金属,能较好地将水流温度传递给热变形介质125;本实施例中,采用铜质构件。芯壳122厚度在满足结构强度和刚度要求的前提下,宜尽可能薄,以提高上述自适应流量调节阀12的响应速度。
63.上述热变形介质125能随温度的变化而呈现出体积的显著变化,优选为选用比热容低并且对芯壳122和活塞123无腐蚀作用的气体,本实施例中,冷腔和热腔内填充的热变形介质125均选用氮气。隔热活塞123将冷腔内的热变形介质125和热腔内的热变形介质125隔离开来,实现两个空间之间的独立密封和热量交换隔离;隔热活塞123的厚度选择宜使得当它发生移动后,冷腔和热腔内的热变形介质125不会受到对向侧外部绕流的冷却水热量交换的过多影响。
64.由于冷腔和热腔内热变形介质125的体积变化,可推动上述隔热活塞123进行滑动,并带动调节机构进行相应的调节动作,实现对冷水流通室/热水流通室内的流通面积的控制,从而达到调节水冷面板11内的冷却水流量的目的。可见,本实施例中,通过感应水冷面板11自身冷却水温度的变化来实现水冷面板11冷却水流量的调节,不需要消耗外部能源,也不涉及控制信号的收发,工作可靠性高,因此便于在炼钢电弧炉的复杂工作环境下安装和长时间服役。
65.上述调节机构可以是采用位移调节方式或转角调节方式,根据调节方式不同采用不同的结构即可,此为阀门领域常规技术,其与隔热活塞123之间进行相应地连接,并且应满足:当水冷面板11回水温度升高时,水冷面板11冷却水流量增大,当水冷面板11回水温度降低时,水冷面板11冷却水流量减小,直至隔热活塞123两侧压力达到平衡。本实施例中,上述调节机构采用位移调节方式,能简化自适应流量调节阀12的结构,确保在炼钢电弧炉的复杂工作环境下具有较高的工作可靠性。在其中一个实施例中,如图3,所述调节机构包括阀杆124和设于所述热水流通室内的阀座126,所述阀杆124连接于所述隔热活塞123上并且自所述热腔穿出至所述热水流通室内,所述阀杆124的自由端具有与所述阀座126适配的调节部;通过隔热活塞123的直线位移,带动阀杆124作直线运动,从而带动调节部靠近或远离阀座126,达到流量调节的目的。该调节部可为阀板等零部件;在可选的实施例中,如图3,所述调节部为形成于阀杆124自由端的调节塞1241,所述阀座126横隔于所述热水流通室内并且相适配地开设有阀孔。进一步地,如图3,上述热水流通室可为直角式腔室,包括直线段入口室、直线段出口室以及连接该直线段入口室和直线段出口室的过渡室,芯壳122的一端可伸入至该过渡室内,上述阀座126可以是横隔在过渡室与直线段出口室连接处的隔板,上述阀杆124优选为与该直线段出口室同轴,通过阀杆124的位移即能调节阀孔与调节塞1241之间的间隙大小。通过对上述调节塞1241形状的设计,可实现对冷却水流量的不同调节特性,优选采用圆锥状或旋转抛物体状的调节塞1241。
66.进一步地,所述芯壳122的供所述阀杆124穿设的穿设孔处进行滑动密封,防止热变形介质125与冷却水相互渗透。
67.以炉壳水冷面板11为例,对上述自适应流量调节阀12的工作过程进行大致说明:
68.(1)当炼钢过程还未开始、电弧炉还处于冷态时,调节塞1241与阀孔之间维持一初始间距,使得自适应流量调节阀12及冷却水循环管路保持一定的初始流量,此初始流量对应的水冷面板11内冷却水平均流速通常在0.5~1.5m/s之间;此初始流量一方面保证自适应流量调节阀12自适应调节功能的顺利启动,另一方面则有利于将水冷面板11内的气泡冲刷带走,以避免造成水冷面板11冷却能力恶化。此时,在冷水流通室和热水流通室内,芯壳122外绕流的冷却水温度一致,相应地冷腔与热腔内热变形介质125的体积维持不变,使得调节塞1241与阀孔之间的间距维持不变。
69.(2)炼钢过程启动后,水冷面板11接收到来自炉内的热辐射和热对流,导致流经水冷面板11的冷却水温度上升,上升的幅度取决于作用于其上的热流密度和冷却水流量的瞬时相对大小。随后,温度上升的冷却水将热量传递给热腔内的热变形介质125,使得后者体积发生膨胀、压力上升。冷水流通室内的冷却水温度维持不变,则冷腔内热变形介质125的体积和压力维持先前水平,使得隔热活塞123两侧压力不同,在压差作用下隔热活塞123向冷腔侧移动;在隔热活塞123的带动下,阀杆124也向上移动,使得调节塞1241与阀孔之间间距变大,增加阀孔出流面积并减小局部阻力系数,从而增大了水冷面板11内部的冷却水流量。
70.当活塞123上下两侧的压力一致时,隔热活塞123的移动随之停止。
71.冷却水流量的增加提高了水冷面板11的冷却强度,若此时水冷面板11接收的热流密度不再升高,则增加的冷却水流量将降低冷却水回水的温度;此时,热腔内热变形介质125的体积缩小、压力下降,在压差作用下隔热活塞123带动阀杆124向热腔侧移动,使得调
节塞1241与阀孔之间间距变小,减小阀孔出流面积并增加局部阻力系数,从而减小了水冷面板11内部的冷却水流量。在一定的热流密度下,上述过程最终会处于一个平衡状态,此时增加的冷却水流量和温度正好与当前热流密度相匹配,不至于让冷却水温度上升太高。正常冶炼工况下,冷却水回水出口平均温度在7~15℃范围内;极端冶炼工况下,如电弧暴露过长时,冷却水回水出口平均温度不超过28℃。
72.(3)当水冷面板11不再接收来自炉内的热量时,如停炉冷却过程,热水流通室内的冷却水温度会不断降低,热腔内热变形介质125的体积和压力不断减小,在压差作用下隔热活塞123带动阀杆124不断向热腔侧移动,使得调节塞1241与阀孔之间间距持续变小,逐步减小阀孔出流面积同时增加局部阻力系数,从而使得水冷面板11内部的冷却水流量持续降低。最终,当冷水流通室和热水流通室内的冷却水温度一致时,调节塞1241与阀孔之间间距恢复至初始值。
73.以上所述仅为本发明的较佳实施例而已,并不用以限制本发明,凡在本发明的精神和原则之内,所作的任何修改、等同替换、改进等,均应包含在本发明的保护范围之内。