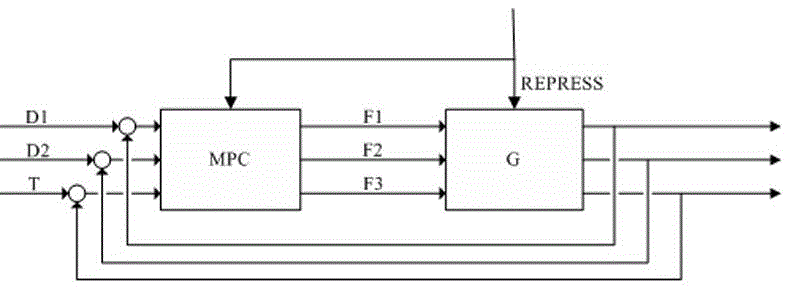
本发明涉及的是一种空分装置制氩系统的氮塞防控方法,属于空气分离控制工程技术领域。
背景技术:
氩是空气中含量最多的稀有气体,图1给出了一种空分制取氩的流程,原料空气经过在主塔低压塔的精馏,将在塔顶获得产品氮气,塔底得到产品氧,并在提馏段形成一个氩富集区;氩的提取就是通过从低压塔中下部抽取一定量的气相氩馏分,并进入粗氩塔进行精馏。由于粗氩塔塔板数较多,塔高不利于安装和保持垂直度,因而把粗氩塔分成粗氩塔Ⅰ和粗氩塔Ⅱ两段。粗氩塔Ⅱ顶部是粗氩冷凝器,冷源是来自于经液空过冷器的液空;在塔内,上升的粗氩气大部分被粗氩冷凝器冷凝下来作为回流液;在塔底,被冷凝的液体通过循环液氩泵增压后被送入粗氩塔Ⅰ顶部,作为粗氩塔Ⅰ的回流液。粗氩塔Ⅰ底部的液体靠位差和自重回到低压塔相应的部位。在粗氩冷凝器中,未被冷凝的粗氩气被引入到粗氩液化器中进行液化,然后将得到的粗液氩再送入精氩塔中进行氩、氮分离。
在上述制氩工艺流程中,为了获得高纯度的氩产品,监测、调节氩系统中的氮含量来防控氮塞是相当重要的。这是因为如果从低压塔抽取的氩馏分含氮过多,大量的氮进入粗氩塔内不能被粗氩冷凝器所冷凝,而积聚在冷凝器的粗氩侧,致使粗氩中的氮含量急剧增加,从而导致粗氩冷凝器温差减小,甚至为0。这样,粗氩气的冷凝量减少,氩馏分的抽出量亦减少,气体上升速度减慢,最终造成塔板漏液,粗氩塔精馏工况被破坏,出现“氮塞”问题。
目前,常规设计的制氩系统氮塞防控方案是依靠几套单回路PID组成的,但是单回路PID控制算法存在以下的不足:
⑴、空分制氩生产过程具有复杂的动态特性、强烈的非线性和回路之间的耦合性等特征,传统的单变量PID控制算法是不能取得满意的控制效果的。
⑵、分子筛纯化器切换升压过程对制氩系统氧、氩、氮组分的影响,常规PID控制是不能够预测的,从而不能提前采取控制作用预防氩系统中的氮含量超标。
因此,常规制氩系统氮塞防控方案是不能及时、准确的监测、预防和处理空分装置的氮塞。
技术实现要素:
为了克服已有空分制氩系统氮塞防控方案不能适应空分制氩操作的动态特性、强烈的非线性和回路之间的耦合性等不足,本发明提供一种能够实时在线监测和调节制氩系统中氧、氩、氮含量的变化,实现空分装置氮塞的在线实时监测与控制的空分装置制氩系统的氮塞防控方法。
本发明的目的是通过如下技术方案来完成,一种空分装置制氩系统的氮塞防控方法,所述的氮塞防控方法由如下步骤组成:
步骤一、确定控制方案的被控变量为氩馏分氩含量、氩馏分温度和粗氩塔Ⅱ顶部氩含量,操作变量为气氧取出量、纯液氮回流量和粗氩气提取量,扰动变量为事件变量—分子筛纯化器切换升压过程;
步骤二、通过装置阶跃序列测试和模型参数辨识,获得气氧取出量、纯液氮回流量分别与氩馏分氩含量、氩馏分温度之间的传递函数,以及粗氩气流量与粗氩塔Ⅱ顶部氩含量间的传递函数,其扰动传递函数是通过辨识分子筛纯化器切换升压时均压阀的阀位分别与氩馏分氩含量、氩馏分温度之间的突变过程数据所获得的;然后将各传递函数转化非参数预测模型—阶跃响应模型;
步骤三、从计算机集散控制系统(DCS)中读取k-1时刻各个操作变量的当前值,并得出k-1时刻各操作变量的变化量;
步骤四、通过预测控制算法预测在k-1时刻各操作变量变化量作用下,相应被控变量的未来变化;
步骤五、检测当前各被控变量的测量值,并和原预测值进行比较,对各被控变量的未来预测值进行校正;
步骤六、根据预测控制算法的控制性能指标,优化计算出各操作变量设定值的未来变化量。
作为优选:所述步骤一中,用被控变量氩馏分的温度反映其氮组分的变化比纯度指标更及时、直观;所述步骤一中,分子筛切换升压过程是作为一个事件变量引入到控制器的扰动变量中,控制器通过读取均压阀的阀位值来判断分子筛当前是否充压,并采取相应的调节动作。
作为优选:所述步骤一中,被控变量组成了两道防线来监测制氩系统是否发生氮塞,所述第一道防线包括:氩馏分中的氩含量和氩馏分温度,所述第二道防线是粗氩塔Ⅱ顶部氩含量。
作为优选:所述的预测控制算法是增加了前馈控制功能的预测控制算法,其可测扰动变量—分子筛充压过程为气氧取出量、纯液氮回流量两个操作变量提供前馈信息,此前馈控制方法计算出的控制作用分配后与预测控制算法计算出的控制作用叠加,形成最终的控制作用,具体步骤如下:
⑴初始化各被控变量的预测输出向量;
⑵控制器通过OPC数据接口从DCS中读取各被控变量的当前值和均压阀阀位的当前值,计算出被控变量的预测误差及均压阀阀位的变化量;
⑶根据预测误差校正各被控变量的预测输出值;
⑷被控变量预测值进行移位操作,将作为下一时刻的预测初值;
⑸计算各操作变量的控制增量,并将分子筛充压所产生的前馈输出分配后叠加到气氧流量控制增量和纯液氮回流控制增量上,形成最终的控制作用;
⑹利用移除前馈输出后的控制输出来计算各被控变量的预测输出。
本发明基于现有空分生产装置的计算机集散控制系统(DCS)和现有的组分分析仪、温度分析仪、流量表,采用集成前馈结合预测控制技术的算法;以被控变量氩馏分氩含量、氩馏分温度作为监测氮塞的第一道防线,以粗氩塔Ⅱ顶部氩含量作为其第二道防线;并将气氧取出量、上塔纯液氮回流量和粗氩气提取量作为调节氮塞的手段,实现了对空分制氩系统氧、氩、氮含量的实时在线监测与控制,取得了满意的控制效果,因此应用前景非常广阔。
本发明的有益效果主要表现在:⑴、能够适应空分制氩系统操作的动态特性、强烈的非线性和回路之间的耦合性,实现了对空分装置氮塞的有效预防和控制;⑵、能够克服分子筛纯化系统切换升压对氩系统的影响,实现了分子筛充压时对氩精馏过程的平稳控制;⑶、模型要求低、在线计算方便、控制综合效果好。
附图说明
图1是本发明所述空分装置制取氩的工艺流程图。
图中的标号是:1:产品氧气流量;F2:纯液氮回上塔流量;F3:粗氩气提取量;D1:氩馏分氩含量;D2:粗氩塔Ⅱ顶部氩含量;T:氩馏分温度。
图2是本发明所述制氩系统的氮塞防控方法原理框图。
图中的标号是:F1:产品氧气流量;F2:纯液氮回上塔流量;F3:粗氩气提取量;D1:氩馏分氩含量;D2:粗氩塔Ⅱ顶部氩含量;T:氩馏分温度;G:空分制氩系统;REPRESS:分子筛纯化器切换升压;MPC:设计了前馈控制功能的预测控制算法。
图3是本发明制氩系统重要组分氩馏分氩含量
图4是本发明粗氩塔Ⅱ顶部氩含量控制效果图。
图5是本发明前馈结合预测控制算法流程图
具体实施方式
下面结合附图并通过实施例对本发明作进一步说明:一种空分装置制氩系统的氮塞防控方法,所述的氮塞防控方法由如下步骤组成:
步骤一、确定控制方案的被控变量为氩馏分氩含量、氩馏分温度和粗氩塔Ⅱ顶部氩含量,操作变量为气氧取出量、纯液氮回流量和粗氩气提取量,扰动变量为事件变量—分子筛纯化器切换升压过程;
步骤二、通过装置阶跃序列测试和模型参数辨识,获得气氧取出量、纯液氮回流量分别与氩馏分氩含量、氩馏分温度之间的传递函数,以及粗氩气流量与粗氩塔Ⅱ顶部氩含量间的传递函数,其扰动传递函数是通过辨识分子筛纯化器切换升压时均压阀的阀位分别与氩馏分氩含量、氩馏分温度之间的突变过程数据所获得的;然后将各传递函数转化非参数预测模型—阶跃响应模型;
步骤三、从计算机集散控制系统(DCS)中读取k-1时刻各个操作变量的当前值,并得出k-1时刻各操作变量的变化量;
步骤四、通过预测控制算法预测在k-1时刻各操作变量变化量作用下,相应被控变量的未来变化;
步骤五、检测当前各被控变量的测量值,并和原预测值进行比较,对各被控变量的未来预测值进行校正;
步骤六、根据预测控制算法的控制性能指标,优化计算出各操作变量设定值的未来变化量。
本发明所述步骤一中,用被控变量氩馏分的温度反映其氮组分的变化比纯度指标更及时、直观;所述步骤一中,分子筛切换升压过程是作为一个事件变量引入到控制器的扰动变量中,控制器通过读取均压阀的阀位值来判断分子筛当前是否充压,并采取相应的调节动作。
所述步骤一中,被控变量组成了两道防线来监测制氩系统是否发生氮塞,所述第一道防线包括:氩馏分中的氩含量和氩馏分温度,所述第二道防线是粗氩塔Ⅱ顶部氩含量。
本发明所述的预测控制算法是增加了前馈控制功能的预测控制算法,其可测扰动变量—分子筛充压过程为气氧取出量、纯液氮回流量两个操作变量提供前馈信息,此前馈控制方法计算出的控制作用分配后与预测控制算法计算出的控制作用叠加,形成最终的控制作用,具体步骤如下:
⑴初始化各被控变量的预测输出向量;
⑵控制器通过OPC数据接口从DCS中读取各被控变量的当前值和均压阀阀位的当前值,计算出被控变量的预测误差及均压阀阀位的变化量;
⑶根据预测误差校正各被控变量的预测输出值;
⑷被控变量预测值进行移位操作,将作为下一时刻的预测初值;
⑸计算各操作变量的控制增量,并将分子筛充压所产生的前馈输出分配后叠加到气氧流量控制增量和纯液氮回流控制增量上,形成最终的控制作用;
⑹利用移除前馈输出后的控制输出来计算各被控变量的预测输出;
实施例:本发明以图1所示的内压缩流程空分装置为例,在标准工况下,该空分装置的氧气产量为20000Nm3/h,其控制方法的具体实施步骤为:
⑴、根据空分制氩工艺流程和控制要求,选取氩馏分氩含量、氩馏分温度和粗氩塔Ⅱ顶部氩含量作为被控变量,气氧取出量、纯液氮回流量和粗氩气提取量作为操作变量,分子筛切换升压过程作为事件变量引入到控制器的扰动变量中;
⑵、通过对各操作变量阶跃测试获得所需辨识数据,利用辨识软件FRONT-ID辨识出气氧取出量、纯液氮回流量分别与氩馏分氩含量、氩馏分温度之间的一阶传递函数,以及粗氩气流量与粗氩塔Ⅱ顶部氩含量间的一阶传递函数,其扰动传递函数模型是通过辨识分子筛纯化器切换升压时均压阀的阀位分别与氩馏分氩含量、氩馏分温度之间的突变过程数据所获得的;然后将各传递函数模型转化非参数预测模型—阶跃响应序列;
⑶、在DCS系统的局域网上增加一台上位机用来创建防控氮塞的预测控制器MPC(图2),其控制算法是设计了前馈控制功能的预测控制算法,其中,预测时域为P=30,控制周期T=60s;
⑷、气氧取出量、纯液氮回流量和粗氩气提取量各PID控制回路改为串级模式,其设定值由上层模型预测控制器MPC(图2)给定,而氩馏分氩含量、氩馏分温度和粗氩塔Ⅱ顶部氩含量的控制要求由工艺人员所确定;
⑸、投运制氩系统防氮塞模型预测控制器,则将控制器状态参数设为ON,停止投运预测控制器,则将状态参数设为OFF,且各控制回路切出预测控制器,返回到常规控制状态;
⑹、制氩系统防氮塞模型预测控制器根据当前时刻各操作变量气氧取出量、纯液氮回流量和粗氩气提取量的测量值,计算各操作变量的变化量;根据各被控变量氩馏分的氩含量、氩馏分温度和粗氩塔Ⅱ顶部氩含量的当前测量值来校正被控变量的预测值;由预测控制算法依据控制性能指标,优化计算出各操作变量的最优控制增量;同时,如果分子筛目前正在充压,则根据其当前均压阀的阀位与前一时刻阀位的差值,通过扰动模型计算前馈量,并将其分配计算后分别与原先计算的气氧取出控制增量、纯液氮回流控制增量叠加,作为此二者控制回路新的设定值。
图3-4显示了本控制方法在所述内压缩流程专利空分装置上的在线实时运行结果。分界线前为手动控制制氩系统两道防线的重要组分的波动曲线,分界线后为本控制方法运行后组分的波动曲线。在图3中,采用手动控制时,氩馏分氩含量的波动范围为7.5%~11.1%;预测控制器投运后,实际氩馏分氩含量的波动范围减小到8%~10%,且主要在9%上下波动。在图4中,控制器投运前,粗氩塔Ⅱ顶部氩含量的波动范围为98.4%~99.4%;本控制方法运行后,其波动范围缩小到98.9%~99.1%。从以上可以看出,本控制方法运行后,明显缩小了两重要组分的变化范围,使之在精馏过程中不超出工艺所要求的限定,有效的防控了制氩系统的氮塞。
本发明空分装置制氩系统氮塞的控制原理结构图如图2所示,它是通过选取氩馏分的氩含量、氩馏分温度和粗氩塔Ⅱ顶部氩含量各重要指标的测量值作为被控变量(CVs),其中,氩馏分的氩含量、氩馏分温度作为监测制氩系统是否发生氮塞的第一道防线,粗氩塔Ⅱ顶部氩含量作为其第二道防线;选取气氧取出量、上塔纯液氮回流量和粗氩气提取量作为操作变量(MVs);由预测控制器通过滚动优化,计算出当前各操作变量的最优控制增量,其中,气氧取出控制增量、上塔纯液氮回流控制增量用以调节主塔的氩馏分氩含量和氩馏分温度,粗氩气提取控制增量用来调节粗氩塔Ⅱ顶部氩含量。此外,预测控制器还增加了前馈控制功能,将影响氩馏分氩含量和氩馏分温度的分子筛纯化器切换升压过程作为事件变量引入到控制器的扰动变量(DVs)中,为气氧取出量和纯液氮回流量两个操作变量提供前馈信息。
空分装置制氩系统防氮塞的两道重要防线
空分装置生产过程中制氩系统发生氮塞的原因主要是由两个方面引起的,一方面是由于主塔氩馏分控制失常,另一方面是由于粗氩塔冷凝器热负荷过大。基于此,本发明设计了监测氮塞的两道重要防线:
⑴、第一道防线包括:氩馏分氩含量、氩馏分温度。它主要是用来监测从主塔抽取的氩馏分中氧、氩、氮含量的变化,在一般情况下,氩馏分氩含量可以准确的反映出氩馏分中各组分是否合格;但在实际操作中,有时会发生在氧含量不低的情况下却发生了不同程度的氮塞,因此,本发明增加了氩馏分温度作为监测指标,它主要是用来检验氩馏分中的氮含量是否超标,当氩馏分中的氮含量升高时,氩馏分温度就会下降,如果长时间运行,就有可能发生氮塞。此时,通过改变气氧取出量和上塔纯液氮回流量来调整氩馏分各组分的含量。
⑵、第二道防线是粗氩塔Ⅱ顶部氩含量。它是监测制氩系统是否发生氮塞的最后一道防线,当氩馏分的氩含量高于10%且粗氩塔Ⅱ顶部氩含量低于98.6%的偏差逐渐加大时,通常说明空分制氩系统已经发生了一定程度的氮塞。此时,可以增加粗氩气去精氩塔的流量,以消除氮塞。
本发明所述的预测控制算法是增加了前馈控制功能的预测控制算法,分子筛纯化系统切换升压时,均压阀自动打开,使正在进行吸附工作的吸附器中的一部分空气进入再生吸附器中,进入精馏塔的空气量减少,造成上塔操作压力下降,氩馏分中氩、氮含量升高;吸附器卸压阶段,来自上塔的再生污氮气不会进入吸附器而经放空阀放空,如果放空阀没有及时打开,就可能使上塔憋压而引起操作压力升高,精馏效果降低,氩馏分中的氩含量减少,氮含量增加,此过程将会延缓甚至破坏粗氩塔精馏工况的建立。因此,为了降低分子筛纯化系统周期性切换对制氩系统精馏工况的影响,将分子筛纯化器升压过程作为一个事件变量引入到控制器的可测扰动变量中,控制器通过读取均压阀的阀位值来判断分子筛当前是否充压,从而为气氧取出量、纯液氮回流量两个操作变量提供前馈信息。
该前馈有助于在分子筛切换升压时,及时提前调整气氧流量和纯液氮回流量,使得氩馏分氩含量和氩馏分温度能够控制在所要求的范围内,提高控制系统的品质。
此前馈控制方法与预测控制算法的结合机理为:修改预测控制算法的控制作用输出部分,将可测扰动变量分子筛充压引起的控制作用气氧流量、纯液氮回流量和预测控制算法本身所计算出的控制作用叠加,形成最终的控制作用;对预测控制算法的预测部分,仅预测在上一次由预测控制算法本身计算出的控制作用下被控变量氩馏分氩含量和氩馏分温度的变化,即在上次计算产生的最终控制作用中减去由分子筛充压所引起的控制作用,将其作为预测控制算法计算预测输出时的控制作用增量。
其具体控制方法流程如下:
设制氩系统被控对象相对于所对应的操作变量的阶跃响应采样数据为sij(1),sij(2)…sij(N)(i=1…3j=1…3),N为模型长度。
动态矩阵为D=(ATQA+R)-1ATQ D*=L(ATQA+R)-1ATQ误差校正矩阵为移位矩阵为f是前馈转换系数,yr是控制要求。
⑴初始化被控变量氩馏分的氩含量、氩馏分温度和粗氩塔Ⅱ顶部氩含量的预测输出向量X=[x1,0(1) … x1,0(N) x2,0(1) … x2,0(N) x3,0(1) … x3,0(N)]T;
⑵控制器通过OPC数据接口从DCS中读取各被控变量的当前值y(k)=[y1(k)…y3(k)]T和分子筛充压时均压阀的当前阀位值d(k),计算出被控变量的预测误差e=y(k)-[x1,0(1) x2,0(1) x3,0(1)]T及均压阀阀位的变化量Δd(k)=d(k)-d(k-1);
⑶根据预测误差校正各被控变量的预测输出值X=X+H*e;
⑷被控变量预测值进行移位操作X=S0X,将作为下一时刻的预测初值;
⑸计算各操作变量的最优控制增量以及当前时刻的最优控制增量ΔUM(k)=D(yr-X),Δu(k)=D*(yr-X)并将分子筛充压所产生的前馈输出分配叠加到气氧流量控制增量和纯液氮回流控制增量上,形成最终的控制作用u(k)=u(k-1)+Δu(k)+f*Δd;
⑹利用移除前馈输出后的控制输出来计算各被控变量的预测输出X=X+ADM*ΔUM(k),重复步骤⑵—⑹,见图5所示。