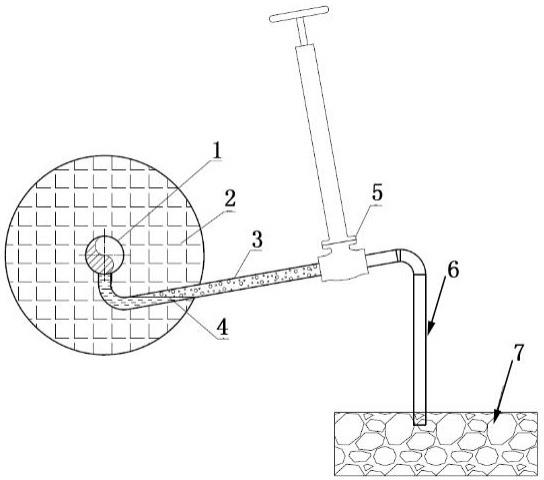
[0001]
本实用新型涉及一种低温液体管道排液管结构,特别涉及一种适合空分装置后备系统冷备状态下的低温液体管道的排液结构,冷量损失小,排液阀故障率低。
背景技术:[0002]
空分装置是利用低温精馏法,将空气分离出液氧、液氮、液氩,再经换热器复热,通过管道向外输送氧气、氮气等工业气体的化工装置单元。其生产出的高纯度品质的氧气、氮气是钢铁冶金、石油化工、煤化工等工业装置正常运行的重要保证。为了防止空分装置意外跳车对下游生产装置产生影响,一般会为空分装置配备大容量低温液体贮槽及配套的低温液体泵和气化器作为后备系统,目的在于当空分装置意外跳车时,能将低温液体迅速复热为气态紧急送往用户管网,避免造成下游生产装置因气体断供而连锁跳车。
[0003]
为了能够实现空分后备系统对事故工况的快速响应,尽快将低温液体加压、复热、气化并送出,一般将低温液体泵常年冷备怠速运转,而泵前的管道则常年充满了低温液体,这些低温液体管道的排液管通常是从主管的底部引出,连接90
°
弯头后水平穿出绝热层,再引至砾石坑排放,这种排液结构常常因为排液阀的保冷不到位,在排液阀进口前的排液管中不断有低温液体受热气化,形成鼓泡并不断向上运动至主管内,而新的低温液体又不断补入排液管内形成热管效应,造成了无法消除的冷量损失。同时,排液阀常年浸没在低温液体中,容易引起阀门填料渗冷冻结,甚至出现低温液体或气体顺填料处的缝隙外漏造成阀杆冻结无法操作的故障情况。后备系统低温液体排液管的常年跑冷,及排液阀的冻结故障隐患,威胁着空分装置安全、可靠、经济的运行原则。
技术实现要素:[0004]
本实用新型的目的主要是提供了一种结构简单,工程实现容易,冷量损失小,有助于降低低温液体排液阀故障率的低温液体管道排液管结构,解决了现有空分装置后备系统中存在的排液管冷量损失大,排液阀易发生冻结故障的技术问题。
[0005]
所述的一种空分装置后备系统中低温液体排液管结构,其特征在于包括低温液体水平主管、从低温液体水平主管底部引出的排液管及安装在排液管上的排液阀,所述低温液体水平主管包裹在绝热层内;从低温液体水平主管底部引出的排液管以10
°
~20
°
倾角斜向上布置并从绝热层内穿出,排液管内的部分低温液体复热气化,并在排液管内形成稳定的气液两相界面;排液阀的阀盖底部标高等于或略低于低温液体水平主管的中心标高。
[0006]
所述的一种空分装置后备系统中低温液体排液管结构,其特征在于所述低温液体水平主管为液氧不锈钢管、液氮不锈钢管或液氩不锈钢管,其管径范围为dn40~dn200;所述绝热层为泡沫玻璃绝热层,其对低温液体水平主管的包裹厚度为80mm~200mm。
[0007]
所述的一种空分装置后备系统中低温液体排液管结构,其特征在于所述排液管自低温液体水平主管底部以异径三通或支管台的形式接出,排液管在泡沫玻璃绝热层内以10
°
~20
°
的倾角斜向上穿出并连接排液阀。
[0008]
所述的一种空分装置后备系统中低温液体排液管结构,其特征在于所述排液阀安装于排液管穿出泡沫玻璃绝热层的200mm~500mm长度距离处,使得排液阀进口前的排液管内具有200mm~500mm长度的气柱隔热层。
[0009]
相对于现有技术,本实用新型取得的有益效果是:本申请的低温液体排液管结构,其结构简单,工程实现容易,在应用于空分装置后备系统中,能够有效避免排液管上因排液阀跑冷而引起的热管效应,大大降低了空分装置后备系统未投用时排液管内的低温液体的气化率,减少了排液阀长时间浸泡于低温液体环境中由于填料渗冷冻结导致的阀门故障。
附图说明
[0010]
图1为本申请的空分装置后备系统中低温液体排液管结构的结构示意图;
[0011]
图中:1-低温液体水平主管,2-绝热层,3-排液管,4-气液两相界面,5-排液阀,6-放液管,7-砾石坑。
具体实施方式
[0012]
下面结合具体实施例对本发明作进一步说明,但本发明的保护范围并不限于此。
[0013]
实施例:对照图1
[0014]
一种空分装置后备系统中低温液体排液管结构,包括低温液体水平主管1、从低温液体水平主管1底部引出的排液管3及安装在排液管3上的排液阀5。其中低温液体水平主管通常是位于空分装置后备系统中,例如:低温液体储槽的排放管、低温液体泵的进口管道或出口管道、水浴式汽化器的低温液体进口管、空浴式汽化器的低温液体进口管等等。
[0015]
所述低温液体水平主管1可以是液氧不锈钢管、液氮不锈钢管或液氩不锈钢管,其管径范围为dn40~dn200;所述绝热层2对低温液体水平主管1的包裹厚度为80mm~200mm。
[0016]
所述排液管3自低温液体水平主管1底部以异径三通或支管台的形式接出,具体方式可以是:低温液体水平主管1底部通接一个较小长度的竖直管段,再经热煨弯管焊接后,进行焊接排液管3。其中所述竖直管段是通过焊接异径三通或支管台的方式从低温液体水平主管1下方接出。
[0017]
排液管3在泡沫玻璃绝热层2内以10
°
~20
°
的倾角斜向上穿出并连接排液阀5,所述排液阀5可以是焊接于排液管3上,其采用低温液体专用调节阀或长阀杆型截止阀。排液阀5常年处于关闭状态,其阀盖底部标高等于或略低于低温液体水平主管1的中心标高。
[0018]
所述低温液体水平主管1包裹在保冷良好的绝热层2内(绝热层2可采用泡沫玻璃绝热层),从低温液体水平主管1底部引出的排液管3以10
°
~20
°
倾角斜向上布置,在穿出绝热层2后,排液管3内的低温液体开始复热气化,因气相密度较液相小,排液阀5进口前形成的气柱高度逐渐变大,直至将气液两相界面顶回至被绝热层2包裹的排液管3管段内。所述排液阀5安装于排液管3穿出泡沫玻璃绝热层2的200mm~500mm长度距离处,即可使排液阀5进口前的排液管3内具有200mm~500mm长度的气柱隔热层,由于气柱中气体(如氧气、氮气、氩气等)的导热系数小于保冷材料泡沫玻璃的导热系数,有效杜绝了排液管中液体和排液阀接触形成冷桥,良好隔绝了低温液体和外部环境的热量交换。
[0019]
对照图1可以看出,采用本实用新型的低温液体排液管结构,在排液阀5处于关闭状态时:排液管3内的部分低温液体复热气化,在排液管3内形成液相、气液两相界面4和气
相,气液两相界面4略高于排液管弯头的最低处部位的液位高度,且气液两相界面4形成于排液管同绝热层的交界处。气液两相界面4上方的气相即为气柱隔热层,气柱隔热层与外部环境形成稳态换热,因气体具有非常小的热传导系数(基本在0.025w/m
·
℃以下),气柱在沿排液管的轴线方向上具有非常大的温度梯度,成为了排液管中低温液体和外部环境之间的有效热阻,降低了排液管剖面上的冷流密度和冷通量,亦阻止了外部环境的热量传导到低温液体水平主管中,减小了整个管道系统的冷量损失。
[0020]
在本申请中,所述排液管的向上倾角为10
°
~20
°
,合理的排液管倾角保证了排液管中的气柱高度,形成的有效热阻能够在排液管和绝热层交界处的排液管内形成稳定的气液两相界面,从而杜绝了排液管的常年跑冷现象。
[0021]
排液阀5的阀盖底部标高应等于或略低于低温液体水平主管1的中心标高,这是因为:根据帕斯卡静压传递原理,气柱和低温液体在同一水平标高处的压力相等,当后备系统投用完毕或停车检修需要排空管道中低温液体时,在打开排液阀后能利用主管中液体压力快速排空低温液体,从而降低工人的操作时间。
[0022]
对照图1,排液阀5的出口可以安装放液管6,放液管6的出口端伸入到砾石坑7内。当后备系统投用完毕或停车检修需要排空管道中低温液体时,打开排液阀5,低温液体通过放液管6排入到砾石坑7内。在砾石坑7内,低温液体能够很好的向四周扩散蔓延,通过浸润砾石表面,大大提高了低温液体同环境的对流传热面积,加快了低温液体蒸发速度。
[0023]
实施例1:
[0024]
采用本实用新型的空分装置液氮后备系统中的液氮排液管结构,包括通往中压液氮泵的dn100液氮水平主管以及该主管的dn25排液管道,液氮水平主管采用厚度为150mm的泡沫玻璃绝热层进行保冷。从液氮水平主管的底部通过支管台引出一个100mm长度的dn25竖直管段,经现场热煨弯管焊接后,进行焊接dn25排液管。所述dn25排液管以15
°
的上倾角穿出泡沫玻璃绝热层。dn25排液管的倾斜长度为550mm,焊接一个排液阀(排液阀采用低温液体专用长杆截止阀)后,排液阀的出口接弯头向下引至砾石坑进行安全排放。在中压液氮泵正常冷备过程中,排液阀前形成一段高度为100mm,长度约为400mm的气柱,阻断了外部环境和低温液体的热量交换。
[0025]
本说明书所述的内容仅仅是对发明构思实现形式的列举,本发明的保护范围不应当被视为仅限于实施例所陈述的具体形式。