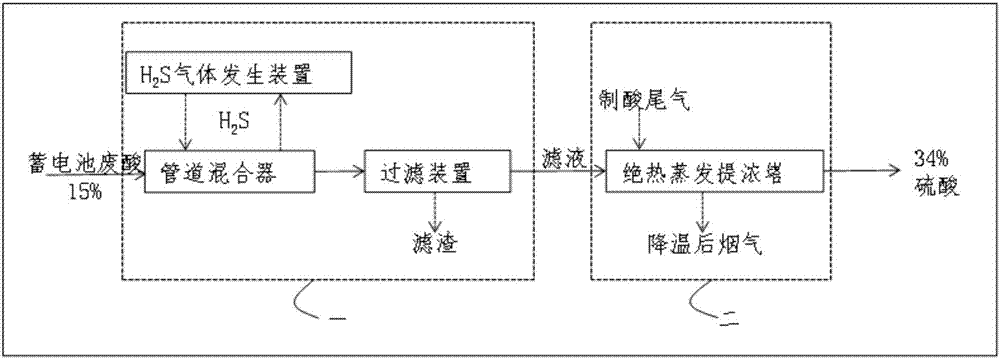
本发明属于废酸处理
技术领域:
,尤其涉及一种蓄电池废酸的资源化处理方法。
背景技术:
:硫酸作为一种重要的工业原料,可用于制造肥料、药物、炸药、颜料、洗涤剂、蓄电池等,也广泛应用于净化石油、金属冶炼以及染料等工业中。因为用处的不同,也使得硫酸的品质分为多种等级,其中用量最大的是工业硫酸和蓄电池酸。传统的工艺对于废酸的处理主要采用酸碱中和方式,此方法不仅成本巨大,硫酸资源没有得到再利用,同时会产生大量的废渣,由于含有重金属,这些废渣被列入危废行列,在环保要求越来越严格的今天,酸碱中和工艺已经不再适合用于废酸的处理。近几年,废酸资源化浓缩工艺技术为处理废酸开辟了一个新领域,且越来越受到企业的关注。相比于传统的处理工艺,废酸的资源化回收利用不仅创造了经济效益,同时也有效的解决了酸碱中和工艺中带来的危废渣排放的问题。然而在解决了资源化的问题后随之而来的是浓缩的能耗过大的问题,酸的浓缩伴随的是蒸汽的消耗,如果不降低蒸汽的消耗,在工业硫酸产能过剩的今天,其工艺价值也大打折扣,为此出现了一些可节约能耗的浓缩工艺,包括多效酸浓缩工艺和热风浓缩工艺。但即使如此,当前的工艺水平蒸发掉一吨水其蒸汽消耗依旧达到0.5-0.8t蒸汽,如果采用热风浓缩工艺,则要利用电能给气体加热,虽然蒸汽消耗减少,但会大幅增加系统的电耗。在耗费了较多能源的情况下,资源化得到的硫酸也仅仅是工业硫酸级别的较浓稀酸,对于企业而言用处不大,外售也无出路,非常尴尬。当前我国的工业硫酸因为大量的冶炼烟气制酸系统使得其产能处于过剩状况,销售价格约为200元/t,且存在销售困难的问题,而同样用量很大、价格是工业硫酸3-4倍的蓄电池酸却出现紧缺状况。这一方面由于汽车行业的快速发展,另一方面也与蓄电池用酸的品质要求较高,基本没有回收再利用有关。而在蓄电池硫酸的使用中,其浓度受温度,荷电态,使用期限等因素的影响,酸浓度会出现变化,同时酸中金属离子含量亦会增加,最终不能使用;同时在回收的过程中因为蓄电池的破碎、清洗等原因,会使蓄电池酸进一步稀释,同时也掺杂有一些固体杂质进入,这些都给蓄电池酸的回收利用带来了困难,这就导致使用后的蓄电池酸成为通常被认为废酸,很少回收利用情况;又由于蓄电池硫酸回收过程中需要消耗大量的能耗,使得企业对蓄电池废酸的回收基本上无真正利用起来,难以实现蓄电池酸的回收。因此,研究一种蓄电池废酸的资源化方法,以低成本的价格回收的蓄电池废酸并可再次作为蓄电池用酸,具有巨大的经济价值。技术实现要素:本发明所要解决的技术问题是,克服以上
背景技术:
中提到的不足和缺陷,提供一种能耗低的蓄电池废酸的资源化处理方法。为解决上述技术问题,本发明提出的技术方案为:一种蓄电池废酸的资源化处理方法,工艺流程图如图1所示,包括以下步骤:(1)向蓄电池废酸中通入h2s气体进行混合并净化,净化完成后固液分离,得到滤渣和滤液;此过程为蓄电池废酸的净化过程,主要用于除去蓄电池废酸中固体杂质(主要由蓄拆解过程中混入)和重金属(主要包括铅、铜、镉、砷等重金属),这些重金属来自蓄电池使用过程中极板的溶解,含量超出了蓄电池酸的标准;硫化氢气体与蓄电池废酸混合并进行反应,使得蓄电池废酸中的铅、铜、镉、砷等金属离子与硫化氢气体快速反应,生成沉淀,进而可以除去;同时采用h2s气体进行除杂不仅可以除去重金属,而且还不会引入二次杂质;(2)将所述滤液通入绝热蒸发提浓塔中,使滤液和高温烟气进行充分接触,得到一次提浓硫酸;此过程为酸的绝热蒸发提浓,由于蓄电池在拆解过程中混入了不同浓度的酸,同时清洗极板等也会使酸进一步稀释,因此需要进行提浓后才能再次应用于蓄电池酸中;使高温烟气与稀酸(即所述滤液)充分接触,通过气液换热的方式使稀酸中水汽化,达到提浓的效果,成为一次提浓硫酸;同时,高温烟气经过绝热蒸发提浓塔后变成降温后烟气,可送至烟囱外排;本工段管道阀门等采用材质为钢衬四氟材质。上述的资源化处理方法,优选的,还包括多效逆流蒸发提浓步骤,其具体操作为:将所述一次提浓硫酸依次通入预热蒸发器、二效蒸发器和一效蒸发器,完成多效蒸发,得到二次提浓硫酸。蒸发器(包括预热蒸发器、二效蒸发器和一效蒸发器)核心设备壳体为搪玻璃容器或者碳化硅容器,可耐高温、强腐蚀。一次提浓硫酸先经过预热蒸发器后进入了二效蒸发器,然后再进入一效蒸发器,这种形式形成逆流。本工段管道阀门等采用材质为钢衬四氟材质。上述的资源化处理方法,优选的,所述预热蒸发器的热源来自于二次提浓硫酸。上述的资源化处理方法,优选的,利用不低于150℃的蒸汽对一效蒸发器进行换热蒸发;利用130-135℃的蒸汽对二效蒸发器进行换热蒸发。上述的资源化处理方法,优选的,所述130-135℃的蒸汽为一效蒸发器产生的二次蒸汽。上述的资源化处理方法,优选的,所述步骤(2)中,高温烟气为高温制酸尾气,温度为75℃。当前的制酸工艺中,制酸尾气具有含水率几乎为零、烟温约为75℃,烟气中除含有少量二氧化硫外不含其它空气污染物的特点;这样的制酸尾气气量为10000nm3,烟温从75℃降至45℃时,能使0.2m3水蒸发,而在当前的制酸系统中,这部分尾气的热能几乎都被忽略,未加以利用。而本发明创新性地利用制酸尾气作为热源,可以使稀酸中的水分随制酸尾气带走,从而达到稀酸的绝热蒸发提浓目的。高温制酸尾气非常干净,没有其他杂质,不会给酸带来污染,保证了浓缩后酸的品质可以再次用于蓄电池,蓄电池用酸的价格数倍于通常的工业硫酸。采用高温制酸尾气是算浓缩能耗降低核心,也是保证回收的酸品质满足蓄电池用酸的基础。上述的资源化处理方法,优选的,所述步骤(1)中,h2s气体来自于硫化氢发生装置;所述混合过程在管道混合器中进行;h2s气体与蓄电池废酸在管道混合器中混合之后产生的硫化氢尾气返回至硫化氢发生装置。上述的资源化处理方法,优选的,所述一次提浓硫酸在二效蒸发器进行换热蒸发的过程中对二效蒸发器进抽真空处理或抽负压处理。采用真空装置控制二效蒸发器中的压力,控制二效蒸发器的绝对压力小于60kpa,保证二效蒸发器中的硫酸达到沸点,使水和硫酸分离,达到酸浓缩的目的。上述的资源化处理方法,优选的,所述步骤(1)中,固液分离的方式为通过过滤装置进行过滤;所述过滤装置为膜过滤器,材质为钢衬塑,通过膜过滤器进行过滤后滤液中的固体含量满足蓄电池酸标准。上述的资源化处理方法,优选的,所述绝热蒸发提浓塔中采用的设备为文氏管或者动力波装置,材质采用的是耐高温玻璃钢材质,能确保高温烟气和滤液进行气液充分接触,进行气液传热,保证绝热蒸发效果。与现有技术相比,本发明的优点在于:(1)本发明针对于蓄电池废酸所提出的资源化工艺,能耗低,回收产物经济效益高,实现了低成本地回收蓄电池废酸,回收的蓄电池废酸满足蓄电池酸用酸标准。(2)本发明充分利用高温制酸尾气作为绝热蒸发过程中的热源,大大降低了能耗成本,同时绝热蒸发后制酸尾气中除湿度增加、烟温下降外,其余状态不改变,可直接外排,并不会额外增加对环境的污染。(3)本发明可以根据蓄电池废酸浓度的要求可仅采用绝热蒸发对稀酸进行提浓,也可将绝热蒸发与多效蒸发相结合,根据实际需求进行工艺的灵活选择。(4)本发明将绝热蒸发提浓和多效逆流蒸发提浓工艺结合,由于绝热蒸发提浓过程利用的是高温烟气将酸中的水分汽化实现酸中的水与硫酸分离,不需要消耗额外的蒸汽,充分做到了节能降耗,运行成本低廉的技术效果;多效逆流蒸发提浓过程中,预热蒸发器的热源来自于二次提浓硫酸,二效蒸发器的热源来自于一效蒸发器产生的二次蒸汽,进一步充分起到节能降耗,运行成本低廉的效果。(5)本发明的工艺在电耗、蒸汽消耗及循环冷却水消耗上都较小,具体如表1所示。表1不同酸资源化工艺蒸发一吨水能耗比较工艺热风浓缩+多效浓缩多效浓缩本发明工艺电耗(度)25-3510-205-10循环水消耗(m3)12-2020-350-12蒸汽消耗(t)0.3-0.50.5-0.80-0.3附图说明图1是本发明的蓄电池废酸资源化处理方法的工艺流程图。图2是本发明实施例1的蓄电池废酸的资源化处理方法的流程图。图3是本发明实施例2的蓄电池废酸的资源化处理方法的流程图。图4是本发明实施例2中多效蒸发系统中进行提浓的工艺流程图。具体实施方式为了便于理解本发明,下文将结合说明书附图和较佳的实施例对本文发明做更全面、细致地描述,但本发明的保护范围并不限于以下具体实施例。除非另有定义,下文中所使用的所有专业术语与本领域技术人员通常理解含义相同。本文中所使用的专业术语只是为了描述具体实施例的目的,并不是旨在限制本发明的保护范围。除非另有特别说明,本发明中用到的各种原材料、试剂、仪器和设备等均可通过市场购买得到或者可通过现有方法制备得到。实施例1:本实施例中待处理的蓄电池废酸处理量为2t/h,酸浓度为15%,其中含有少量重金属和固体杂质;本实施例中采用的高温制酸尾气(75℃)气量为50000nm3/h,要求处理后酸液中硫酸浓度达到34%,杂质含量符合蓄电池酸用酸标准;绝热蒸发提浓塔中采用的设备为动力波装置,材质采用的是耐高温玻璃钢材质。本实施例中绝热蒸发后酸浓度理论计算:10000nm3烟气绝热蒸发带走的水份:0.23m3(烟气降低至45℃时所带走的水分)绝热蒸发水分带走水份:0.23*5=1.15m3/h稀酸要求处理量:2t/h(酸浓度15%)绝热蒸发后酸浓:根据上述计算结果,进行绝热蒸发后酸浓可达到35.3%。本实施例的蓄电池废酸的资源化处理方法,流程图如图2所示,具体工艺步骤如下:(1)将浓度为15%的蓄电池废酸首先进入管道混合器中,然后与从硫化氢气体发生装置制备的硫化氢气体混合,混合后多余的气体(硫化氢尾气)回到硫化氢气体发生装置,混合过程中硫化氢气体与蓄电池废酸中的铅、铜、镉、砷等金属离子快速反应,生成沉淀;将混合完成后的物料通过过滤装置(膜过滤器)进行过滤,得到滤渣和滤液;滤渣为蓄电池废酸中的固体杂质和重金属,予以除去;(2)将步骤(1)后所得的滤液进入绝热蒸发提浓塔中与高温烟气进行充分接触进行绝热蒸发,高温制酸尾气温度由75℃降至45℃后送至烟囱排放,此时,从绝热蒸发提浓塔中出来的酸浓度达到34%(此处酸浓度与理论值35.3%接近,这是由于热量的损失,在实际生产中不可能完全达到理论值),可送至蓄电池酸使用工段使用。本实施例整个过程能耗如表2所示。表2蓄电池废酸资源化能耗表项目名称单位时间能耗蒸发1t水能耗电耗6.26度/h7度/t水循环水消耗0m3/h0m3/t水蒸汽消耗0t/h0t/t水实施例2:本实施例待处理的蓄电池废酸处理量为2t/h,酸浓度为15%,含有少量重金属和固体杂质;本实施例中采用的高温制酸尾气(75℃)气量为50000nm3/h,要求处理后酸浓达到55%,杂质含量符合蓄电池酸用酸标准;绝热蒸发提浓塔中采用的设备为文氏管,材质采用的是耐高温玻璃钢材质。本实施例中绝热蒸发后酸浓度理论计算:10000nm3烟气绝热蒸发带走的水份:0.18m3(烟气降低至55℃时所带走的水分)绝热蒸发水分带走水份:0.18*5=0.9m3/h稀酸要求设计处理量:2t/h(按酸浓度15%计算)绝热蒸发后酸浓:根据上述计算结果,进行绝热蒸发后酸浓可达到27.3%。本实施例的蓄电池废酸的资源化处理方法,流程图如图3所示,具体工艺步骤如下:(1)将酸浓度为15%的蓄电池废酸首先进入管道混合器中,与从硫化氢气体发生装置制备的硫化氢气体混合,混合后多余的气体(硫化氢尾气)回到硫化氢气体发生装置,混合过程中硫化氢气体与蓄电池废酸中的铅、铜、镉、砷等金属离子快速反应,生成沉淀;将混合完成后的物料通过过滤装置(膜过滤器)进行过滤,得到滤渣和滤液;滤渣为蓄电池废酸中的固体杂质和重金属,予以除去;(2)将步骤(1)后所得的滤液进入绝热蒸发提浓塔中与高温烟气进行充分接触进行绝热蒸发,高温制酸尾气温度由75℃降至55℃后送至烟囱排放,此时,从蒸发提浓塔中出来的酸浓度达到26%(此处酸浓度与理论值27.3%接近,这是由于热量的损失,在实际生产中不可能完全达到理论值);(3)将步骤(2)得到的26%的酸进入多效蒸发系统中进一步提浓,至硫酸浓度达到55%后送至蓄电池酸使用工段使用;其中,在多效蒸发系统中进行提浓的工艺见图4所示;具体步骤为:将26%稀酸进入预热蒸发器进行预热,预热所需热源由提浓后55%高温硫酸提供;然后将预热后的稀硫酸送入二效蒸发器进行换热蒸发,热源为来自一效蒸发产生的二次蒸汽(约135℃),通过二效加热蒸发后,稀酸酸浓由26%提升至33%,二次蒸汽冷凝水降温外排;经过二效蒸发提浓的稀酸送至一效蒸发器进行换热蒸发(在二效蒸发器进行换热蒸发的过程中对二效蒸发器进行抽负压处理,绝对压力<60kpa),加热源为一次蒸汽(约150℃),经过一效加热蒸发后,稀酸酸浓由33%提升至55%,降温后输送至稀酸储罐进行储罐备用;一次蒸汽冷凝水回供热系统再利用。整个过程能耗如表3所示。表3蓄电池废酸资源化能耗表项目名称单位时间能耗蒸发1t水能耗电耗12度/h8.25度/t水循环水消耗15m3/h10.3m3/t水蒸汽消耗0.38t/h0.26t/t水当前第1页12