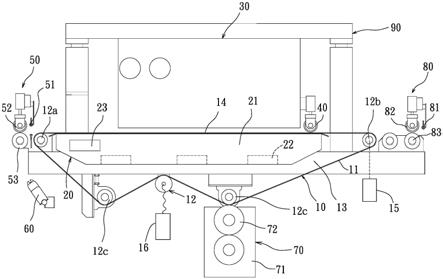
1.本发明是有关于一种基材表面处理装置,特别是有关于一种基材于输送制作过程中,对基材的上、下表面进行清除粉尘的技术领域。
背景技术:2.在目前的ic载板制造技术领域中,对于制造过程中大都必须使用到绝缘胶片基材,但此基材无论在其制造过程或是运输过程中,都会使得基材的表面存在一些可移动胶粒,而这些存在基板表面的胶粒若不处理时,是会造成制造线路良率降低问题。举例来说,铜箔基板(ccl)常见的有半固化绝缘胶片与捲装两种形式,可依客户要求裁切小尺寸(panel size)片状的胶片。但在裁切胶片时,因胶片的胶系配方不同而容易产生许多粉尘分布在裁切边缘,往往造成下游客户制程的挑战,必须清除粉尘来提高电路制作的良率。
3.续就裁切制程所产生的粉尘问题,已有业者提出一种可在成叠的胶片四周施以热风或红外线,对切断面胶粉破裂的边缘作一次性的热封边的动作,可以减少胶片粉尘在后续制程中所发生的掉落问题。惟,这种热封边方式对于胶片非边缘的两面的大面积表面上的胶粉均没有任何处理,对于印刷电路板线路密度越来越高,线路宽度也相对越来越高,所以制作线路所使用的铜箔也越来越薄的严苛要求条件下,当铜箔基板的表面洁净度不够时,会造成光学元件的劣化或是电路的缺陷,使得制造良率降低,在高阶的高密度多层板尤为重要。因此,如何有效解决基板的表面尘粒以提高制作良率是亟待解决的问题。
技术实现要素:4.有鉴于上述习知技艺的问题,本发明的主要目的就是提供一种可让基材平整输送,并透过压轮黏附的清洁方式同时清除输送装置与基材表面的粉尘,使基材具有良好的表面洁净度。
5.本发明的次要目的就是提供一种基材连续经由两次输送过程中,能在基材不翻转的情况下进行上、下表面处理,并有效解决附着于基材表面的粉尘问题。
6.本发明的再一目的就是一种可消除基材表面的静电现象,可容易且快速的清除基材表面的粉尘问题。
7.本发明所采用的技术手段如下所述。
8.根据本发明的目的,提出一种基材表面处理装置,包括一输送模组、一负压抽气模组、一加热模组以及至少一抵压黏轮。输送模组包括一输送带与复数个输送轮,输送带环设于此些输送轮以形成一空间与一工作区域,此些输送轮间隔位于空间中,输送带用以输送至少一基材至工作区域。负压抽气模组设置于输送模组的空间中,负压抽气模组用以负压吸附基材的表面于工作区域上。加热模组邻近于输送模组,输送模组位于加热模组与负压抽气模组之间,加热模组对基材表面进行加热以热融其上的胶粒。抵压黏轮位于加热模组的一侧,抵压黏轮用以黏附基材表面的胶粒。
9.依据上述技术特征,更包括一入料模组,该入料模组包括一入料感测器、相对设置
的一第一入料抵压轮与一第二入料轮,该第一入料抵压轮设置于该入料感测器上,该第二入料轮邻近该些输送轮中最靠近工作区域的该输送轮。
10.依据上述技术特征,更包括一静电消除器,该静电消除器设置在邻近该输送带的该工作区域。
11.依据上述技术特征,更包括一清洁模组,该清洁模组设置于该输送模组的一侧,该清洁模组包括一清洁本体与装设于该清洁本体的至少一清洁抵压轮,该清洁抵压轮邻近至少一该输送轮,且该清洁抵压轮与前述输送轮相对设置,并分别抵压该输送带的两表面。
12.依据上述技术特征,更包括一出料模组,该出料模组包括一出料感测器、相对设置的一第一出料抵压轮与一第二出料轮,该第一出料抵压轮设置于该出料感测器上,该第二出料轮邻近该些输送轮中最靠近工作区域的该输送轮。
13.依据上述技术特征,其中该负压抽气模组包括一负压腔体与至少一抽气单元,该负压腔体具有一开口,该输送带具有复数个吸气孔,该开口与该些吸气孔相连通,放置于该工作区域的该基材与该些吸气孔间经由该抽气单元抽气驱动而形成的负压状态,使该基材被吸附至该输送带的该工作区域上。
14.依据上述技术特征,其中该加热模组包括一座体与装设于该座体上的一加热器,该座体具有相连通的一循环空间、一进风口与一排风口。
15.依据上述技术特征,其中该加热模组进一步包括一温控单元,该温控单元电性连接该加热器,该温控单元用以控制该加热器的加热温度。
16.依据上述技术特征,其中该加热模组进一步包括一温度感测器,该温度感测器电性连接该温控单元,该温度感测器用以感测该循环空间内的温度,该温控单元根据该温度感测器的一感测讯号以相应控制该加热器的运作。
17.依据上述技术特征,更包括一升降模组,该升降模组耦接于该加热模组,该升降模组用以控制该加热模组上升远离该输送带,以及控制该加热模组下降靠近该输送带。
18.依据上述技术特征,输送模组更包括一速度控制器与一冷却器,该速度控制器耦接于该输送带,用以控制该输送带的运作速度,该冷却器耦接于该些输送轮。
19.根据本发明的另一目的,提出一种基材表面处理装置,包括二输送模组、二负压抽气模组、二加热模组以及二抵压黏轮。二输送模组为相邻设置并呈镜射结构,每一该输送模组包括一输送带与复数个输送轮,该输送带环设于该些输送轮以形成一空间与一工作区域,该些输送轮间隔位于该空间中,该输送带用以输送至少一基材至该工作区域。二负压抽气模组分别对应设置于二该第一输送模组的该空间中,一个该负压抽气模组用以负压吸附该基材的上表面于一个该第一输送模组的该工作区域上,另一该负压抽气模组用以负压吸附该基材的下表面于另一个该第一输送模组的该工作区域上。二加热模组,分别设置邻近于二该输送模组,每一输送模组对应位于一个该加热模组与该负压抽气模组之间,二该加热模组分别对该基材的该上表面与该下表面进行加热,以热融该上表面与该下表面的胶粒。二抵压黏轮,分别位于二该加热模组的一侧,该抵压黏轮用以黏附该基材的该上表面与该下表面的该胶粒。
20.依据上述技术特征,其中该更包括一入料模组,位于其中一该输送模组的一侧,该入料模组包括一入料感测器、相对设置的一第一入料抵压轮与一第二入料轮,该第一入料抵压轮设置于该入料感测器上,该第二入料轮邻近该些输送轮中最靠近工作区域的该输送
轮。
21.依据上述技术特征,更包括一出料模组,位于另一个该输送模组的一侧,且该出料模组远离该入料模组,该出料模组包括一出料感测器、相对设置的一第一出料抵压轮与一第二出料轮,该第一出料抵压轮设置于该出料感测器上,该第二出料轮邻近该些输送轮中最靠近工作区域的该输送轮。
22.依据上述技术特征,更包括二个以上的静电消除器,分别设置在邻近该入料模组与该出料模组处。
23.依据上述技术特征,更包括二清洁模组,分别设置于每一该输送模组的一侧,每一该清洁模组包括一清洁本体与装设于该清洁本体的至少一清洁抵压轮,该清洁抵压轮邻近至少一该输送轮,且该清洁抵压轮与该输送轮相对设置,并分别抵压该输送带的两表面。
附图说明
24.图1为本发明的基材表面处理装置的第一实施例结构示意图。
25.图2为本发明的基材入料状态示意图。
26.图3为本发明的负压模组的结构示意图。
27.图4为本发明的加热模组的结构示意图。
28.图5为本发明的清洁基材表面的状态示意图。
29.图6为本发明的升降模组的作动状态图。
30.图7为本发明的基材进行出料的状态示意图。
31.图8为本发明的基材表面处理装置的第二实施例结构示意图。
32.图9为本发明的基材位于两个输送模组之间的状态示意图。
33.图10为本发明的基材进行另一表面处理的状态示意图。
34.图11为本发明的基材进行出料的状态示意图。
35.图号说明:100:基材10、10’:输送模组11、11’:输送带111: 吸气孔12、12’、12a、12b、12b’、12c:输送轮13: 空间14、14’: 工作区域15: 速度控制器16: 冷却器20、20’:负压抽气模组21: 负压腔体211: 开口22: 抽气单元23: 真空驱动器30、30’: 加热模组
31:座体311: 循环空间312: 进风口313: 排风口32:加热器33: 温控单元34: 温度感测器40、40’:抵压黏轮50: 入料模组51: 入料感测器52: 第一入料抵压轮53: 第二入料轮60: 静电消除器70: 清洁模组71: 清洁本体72: 清洁抵压轮80: 出料模组81: 出料感测器82: 第一出料抵压轮83: 第二出料轮90、90’:升降模组。
具体实施方式
36.在此先说明本发明的整体结构组成,请参阅图1,为本发明的基材表面处理装置的第一实施例结构示意图。基材表面处理装置包括一输送模组10、一负压抽气模组20、一加热模组30以及至少一抵压黏轮40。输送模组10包括一输送带11与复数个输送轮12,该输送带11环设于此些输送轮12以形成一空间13与一工作区域14。其中,此些输送轮12的配置方式是至少两个输送轮12a、12b水平设置抵靠于输送带11上,其他输送轮12c远离输送带11位置,故输送带11环设于此些输送轮12即可形成空间13,被两个输送轮12a、12b水平设置并抵靠的输送带11区域则作为工作区域14。输送模组10更包括一速度控制器15与一冷却器16。速度控制器15耦接于输送带11,用以控制输送带11的运作速度,冷却器16耦接于此些输送轮12,借由冷却器控制此些输送轮12的运作温度,使此些输送轮12可以冷却输送带11受热而蓄积的能量,避免输送带11持续升温。
37.负压抽气模组20设置于输送模组10的空间13中,负压抽气模组20包括一负压腔体21与至少一抽气单元22,抽气单元22可为直流风扇,负压抽气模组20更包括一真空驱动器23,真空驱动器23耦接抽气单元22,用以控制抽气单元的运作,可适当调整负压腔体21内的真空度。加热模组30邻近于输送模组10,输送模组10位于加热模组30与负压抽气模组20之间,加热模组30与负压抽气模组20呈上、下相对应设置。抵压黏轮40位于加热模组30的一侧,在此的抵压黏轮40为加热抵压黏轮,加热模组30能够控制抵压黏轮40的加热温度,目的
在于黏附基材表面上的胶粒,容后详述。
38.其中,基材表面处理装置更包括一入料模组50与一静电消除器60。入料模组50包括一入料感测器51、相对设置的一第一入料抵压轮52与一第二入料轮53。第一入料抵压轮52设置于入料感测器51上,第二入料轮53邻近此些输送轮12中最靠近工作区域14的输送轮12a。静电消除器60设置在邻近输送带11的工作区域14。
39.基材表面处理装置更包括一清洁模组70。清洁模组70设置于输送模组10的一侧,清洁模组70包括一清洁本体71与装设于清洁本体71的至少一清洁抵压轮72,清洁抵压轮72邻近至少一输送轮12c,且清洁抵压轮72与前述输送轮12c相对设置,用以抵压输送带11的两表面。具体来说,当输送带11在传动运作时,借由输送轮12c与清洁抵压轮72之间夹持抵靠输送带11的两表面,清洁抵压轮72的表面具有黏性,能够黏附输送带11表面的粉尘,使得输送带11在传动过程中能够持续进行表面处理而维持洁净度,进而解决对基材所造成的污染问题。
40.基材表面处理装置更包括一出料模组80。出料模组80包括一出料感测器81、相对设置的一第一出料抵压轮82与一第二出料轮83。第一出料抵压轮82设置于出料感测器81上,第二出料轮83邻近此些输送轮12中最靠近工作区域14的输送轮12b。
41.承接上述的结构组成说明,接着详述本发明的实际运作方式。如图2所示,为本发明的基材入料状态示意图。将一基材100,如铜箔基板置入于基材表面处理装置中,基材100的两表面经由入料模组50的第一入料抵压轮52与第二入料轮53夹持抵靠后,入料感测器51会侦测基材100已入料的入料感测讯号,负压抽气模组20与加热模组30根据入料感测讯号开始运作。值得注意的是,基材100输送至输送模组10之前,利用静电消除器60消除基材100表面的静电现象,以避免基材100表面的静电累积,同时消除输送带11表面静电,使清洁模组70对输送带11表面清洁更为容易。
42.再如图3所示,为本发明的负压模组的结构示意图。输送带11用以输送基材100至工作区域14,负压抽气模组20用以负压吸附基材100的表面于工作区域14上。具体来说,负压腔体21具有一开口211,输送带11具有复数个吸气孔111,开口211与此些吸气孔111相连通。其中,输送带11可为铁氟龙多孔性耐高温的输送带。放置于工作区域14的基材100与此些吸气孔111间经由抽气单元22抽气驱动而形成的负压状态,使基材100被吸附至输送带11的工作区域14上。负压抽气模组20主要是提供均匀且平整的真空吸附平面,让负压吸附于输送带11上的基材100可以连续稳定输送的状态下,平整地被适当的加热与压平而不需要翻转,进而解决习知技术因为过多的夹取弯折,将导致基材100表面破裂而产生胶粉的问题。
43.同时请参阅图4,为本发明的加热模组的结构示意图,当负压抽气模组20与加热模组30为同时运作,在此进一步说明本发明的加热模组30结构设计。加热模组30包括一座体31与装设于座体31上的一加热器32。座体31具有相连通的一循环空间311、一进风口312与一排风口313。加热模组30进一步包括一温控单元33,温控单元33电性连接加热器32,温控单元33用以控制加热器32的加热温度。加热模组30进一步包括一温度感测器34,温度感测器34电性连接温控单元33,温度感测器34用以感测循环空间311内的温度,温控单元33根据温度感测器34的一感测讯号以相应控制该加热器32的运作。
44.具体来说,加热器32,例如电热加热器配合温控单元33的回授温度,进而控制辐射
热量。座体31的进风口312导入空气至循环空间311后,空气经由加热器32加热后生成热风,并提供适当的热风加速基材100表面的胶粒软化,由于座体31更具有回风通道314,回风通道314与循环空间311连通,排风口313设于回风通道314中,因此循环空间311中的热风能够经由回风通道314经排风口313逸散至外,如此能够保持基材100表面的胶粒温度直至基材100输送离开加热模组30,回风风道314用于确保加热所产生的异味不致散出循环空间311外部,保持工作环境良好。
45.如图5所示,为本发明的清洁基材表面的状态示意图。经由加热模组30适度软化基材100表面的胶粉颗粒,此加热温度不至于触发基材100固化。抵压黏轮40位于加热模组30的一侧,当基材100输送离开加热模组30后,基材100会受抵压黏轮40抵压于输送带11上,此时加热模组30能够控制抵压黏轮40的表面加热温度,抵压黏轮40用以黏附基材100表面上已软化的胶粒,以解决后续基材100制程所产生的胶粒掉落问题。
46.再如图6所示,为本发明的升降模组的作动状态图。基材表面处理装置更包括一升降模组90,升降模组90耦接于加热模组30。升降模组90用以控制加热模组30上升远离输送带11,以及控制加热模组30下降靠近输送带11。本发明考量避免能源的损失问题,因此利用升降模组90的升降运作方式,利用入料感测器51感测基材100入料的入料感测讯号,升降模组90控制加热模组30下降靠近输送带11,可以准时加热基材100。当然,在无需加热的状态下,升降模组90用以控制加热模组30上升远离输送带11,避免输送带11持续升温。除此之外,升降模组90方便加热模组30的后续清洁或维修。
47.再如图7所示,为本发明的基材进行出料的状态示意图。基材100的两表面经由出料模组80的第一出料抵压轮82与第二出料轮83夹持抵靠后,出料感测器81会侦测基材100已出料的出料感测讯号,负压抽气模组20与加热模组30根据出料感测讯号停止运作。基材100出料后即可输送下一站,进行基材100堆叠。
48.上述除了能对基材100的单一表面处理达到有效的洁净度之外,本发明更提出一种无需将基材100翻转就可以达到双表面处理的方式,如图8所示,为本发明的基材表面处理装置的第二实施例结构示意图。基材表面处理装置包括二输送模组10、10’、二负压抽气模组20、20’、二加热模组30、30’、以及二抵压黏轮 40、40’。在第二实施例中的输送模组10、负压抽气模组20、加热模组30以及抵压黏轮40的细部结构与配置关系与第一实施例相同,第二实施例与第一实施例具有相同的元件与相同的标号,且相同的部份不再赘述,在此仅说明差异之处。上述组成元件第一实施例仅使用一组,用来处理基材100的单一表面,而在第二实施例中是使用两组,先后处理基材100的上、下表面,且二输送模组10为相邻设置并呈镜射结构。
49.基材表面处理装置的入料模组50位于其中一输送模组10的一侧,入料模组50的第二入料轮53邻近此些输送轮12中最靠近工作区域14的输送轮12a。出料模组80位于另一个输送模组10’的一侧,且出料模组80远离入料模组50,出料模组80的第二出料轮83邻近此些输送轮12’中最靠近工作区域14’的输送轮12b’。基材表面处理装置二个以上的静电消除器60,分别设置在邻近入料模组50与出料模组80处。
50.在第二实施例中,输送模组10、负压抽气模组20、加热模组30以及抵压黏轮40作为一组基材100的上表面处理程序,另一组输送模组10’、负压抽气模组20’、加热模组30’、以及抵压黏轮 40’作为一组基材100的下表面处理程序。由第一实施例中已得知,基材100的
上表面处理经过入料、加热、出料已完成洁净之后,由于上述两组处理程序为相邻且呈镜像结构,基材100无须翻转可持续输送至输送模组10’进行基材的下表面处理程序,如图9所示,为本发明的基材位于两个输送模组之间的状态示意图。当基材100输送离开加热模组30后,基材100会受抵压黏轮40抵压于输送带11上,此时加热模组30能够控制抵压黏轮40的上表面加热温度,抵压黏轮40用以黏附基材100的上表面101已软化的胶粒,而基材的下表面102是抵靠输送带11。接着基材100u经由输送模组10’的输送轮12a’传动至工作区域14’时,基材100的上表面101是负压吸附于输送带11’上,如图10所示,为本发明的基材进行另一表面处理的状态示意图。负压抽气模组20’用以负压吸附基材100的上表面101于工作区域14’上,此时基材100的下表面102是朝向加热模组30’,升降模组90’控制加热模组30’下降靠近输送带11’,加热模组30’对基材100的下表面102进行加热运作,于适度软化基材100的下表面102的胶粉颗粒之后,持续输送基材100至抵压黏轮40’,借由抵压黏轮40’用以黏附基材100的下表面102上已软化的胶粒。
51.再如图11所示,为本发明的基材进行出料的状态示意图。在持续输送基材100至出料模组80之前,可利用静电消除器60消除基材100表面的静电现象,以避免基材100表面的静电累积,同时消除输送带11’表面静电,使清洁模组70对输送带11’表面清洁更为容易。基材100的两表面经由出料模组80的第一出料抵压轮82与第二出料轮83夹持抵靠后,出料感测器81会侦测基材100已出料的出料感测讯号,负压抽气模组20’与加热模组30’根据出料感测讯号停止运作。基材100出料后即可输送下一站,进行基材100堆叠。
52.综观上述,可见本发明在突破先前的技术下,对结构上的创新改良与表面处理方式,利用加热与负压吸附后进行黏附尘粒,能有效提高基材表面处理的洁净度,且基材无须翻面的制作过程不仅可提高生产速度,又可解决基材制作过程中所产生的胶粒问题。除了减少污染的累积与产品间交互污染,同时利用新颖的加热模组结构设计,可维持制作过程中环境无异味。