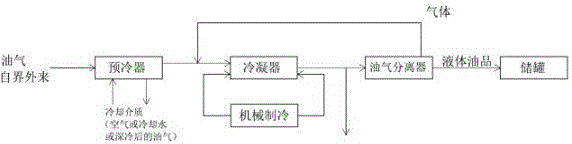
本发明属于废气处理和油气回收与排放控制技术领域,特别涉及一种新型集成油气深度回收与排放控制装置,可广泛应用于原油储运、炼油、石化、化工等行业需要处理含油气、含有毒、有害挥发性烃类油气的深度处理和回收,满足日益严格的环保排放指标要求。
背景技术:汽油、苯类油品等在储存、运输过程中挥发的油气对环境、健康和安全产生的危害越来越引起人们的重视。早在20世纪60年代国外发达国家就对装车、装船过程蒸发损耗油气进行回收技术的研究,20世纪70年代欧美等国已广泛应用油气回收技术于装车、装船等过程。在油气回收方面,欧盟各国都做出了明确规定,有的国家还对加装了油气回收装置的油库和加油站实行阶段性的财政补贴或税收减免的优惠。汽油、苯类等一些化工尾气对人体的危害近年来引起人们的广泛关注,这些尾气严重影响呼吸道和肺部健康,特别是苯类尾气是危险的致癌物质,因此,要保证在排放的废气中尽量减少汽油、苯类等有害物质含量。另外,含汽油、苯类等尾气无组织排放也造成了严重的能源浪费,据相关文献报道,我国仅2005年在石油类产品储运、装卸环节损失高达24.2亿元人民币。我国从1997年1月1日起实行《大气污染物综合排放标准》(GB16297-1996),2007年6月发布了《储油库大气污染物排放标准》(GB20950-2007)、《汽油运输大气污染物排放标准》(GB20951-2007)、《加油站大气污染物排放标准》(GB20952-2007),并于2007年8月1日开始实施。根据《储油库大气污染物排放标准》的要求,装油时产生的油气应进行密闭收集和回收处理,经过回收处理的油气排放浓度要≤25g/m3(非甲烷烃),处理效率要≥95%,同时标准规定了油气排放控制标准实施区域和时限要求。《石油炼制工业污染物排放标准》(GB31570-2015)也规定有机废气排放口非甲烷总烃去除效率≥95%。随着人们环保意识和节约意识的加强,我国将会制定更加严格的环保法规来限制废气排放中有害气体的含量,这就进一步要求油气回收装置处理效率要不断提高。目前,国内油气回收装置采用的方法分为冷凝法、吸收法、吸附法、膜分离法等,处理方法较为单一,处理效率较低,难以满足环保排放的要求。这些处理方法的集成工艺也相继被开发和研究,可在一定程度上满足环保排放要求。CN101342427B介绍了一种冷却→冷凝→吸附→真空再生→再生气循环的油气回收工艺,冷却步骤使用的冷却介质使用冷凝后的油气,可用于车船装卸油、原油油库切油、油罐大小呼吸等情况的油气回收。CN200943812Y介绍了一种加压、冷凝、喷淋相结合的油气回收装置,包括储气罐、吸收塔组、气体压缩机、喷淋油泵、吸收油泵和换热器。CN102895836B介绍了一种加油站用油气回收装置,该油气回收系统设置有压力传送器、温度传送器、压缩机、冷冻机组、气液分离器、膜分离器、吸附罐、流量计,采用压缩、冷凝、膜分离/吸附的复合装置,尾气排放浓度可低于15g/m³,油气回收率可达99%。CN102441313B介绍了一种油气回收方法,包括吸附段或吸收段,在吸附段或吸收段中,吸附剂或吸收剂将油气固定在吸附剂或吸收剂中,然后采用真空再生或加热再生的方式将饱和的吸附剂或吸收剂再生,再生过程得到浓缩再生气,浓缩再生气以汽油为吸收剂在浓缩再生气吸收塔内进行吸收,浓缩再生气吸收塔排放的再生尾气不循环回吸附段或吸收段,浓缩再生气吸收塔采用的汽油吸收剂温度为-15~10℃。但现有工艺和技术存在以下缺点:1)冷凝法能耗相对较大,且对设备材质及保温要求严格,装置投资成本及运行费用相对较高,另外由于油气中水分的存在易使系统结霜结冰;2)吸附法由于工艺及设备自身的特点导致其处理量不能过大,且吸附热效应明显,易造成吸附剂劣化甚至着火;3)吸收法存在溶剂再生工艺复杂、操作费用较高;膜分离法由于膜材料、膜组件制造成本高及使用寿命相对过短,造成其成本较高,且膜分离过程只是一个浓缩过程,不能将油气与空气彻底分开。
技术实现要素:本实用新型目的在于解决上述问题,提供了一种采用压缩→初冷→深冷→膜分离→吸附→燃烧的组合方法,对油气进行回收处理的工艺方法,处理效率高,排放指标标准高,烃类回收率高,能够满足日益严格的环保排放要求,且同等处理效果和回收效果条件下,系统能耗相对较低。具体由以下技术方案实现:采用压缩+预冷+冷凝+膜分离+吸附+燃烧组合方法,对油气回收处理与排放控制。一种新型集成油气深度回收与排放控制装置,该装置由管道依次连接的压缩装置、冷凝装置、膜分离装置、吸附装置、燃烧装置、液态油回收装置组成,以上装置集成在一个方形钢制底盘上,形成橇装型式;所述的压缩装置由压缩机和与压缩机出口相连接的冷却器构成,压缩机为往复式压缩机或离心压缩机,冷却器为管壳式换热器,以循环水作为冷却介质,循环水走管程,油气走壳程;所述的冷凝装置由经管道依次连接的预冷器和冷凝器构成,预冷器进口经管道与压缩机冷凝器出口相连,预冷器和冷凝器为管壳式换热器,预冷器的冷却介质为冷凝后的低温油气,低温油气走管程,较高温油气走壳程,冷凝器的冷却介质为来自冷冻机组的制冷剂,制冷剂走管程,油气走壳程,其壳程进口与预冷器壳程出口相连,冷凝器出口与膜分离装置进口连接;所述的膜分离装置由一系列膜组件并联构成,膜组件内包含卷式或板式半透膜,经过膜分离装置筛分的组分,一部分经管道返回冷凝装置冷凝器再次冷凝,一部分输送至后续吸附装置继续处理;所述的吸附装置由吸附罐、排放筒、真空泵、冷却器构成,吸附罐设置两台立式钢制圆柱吸附罐,罐内装填活性炭、吸附树脂作为吸附剂,吸附罐底部设置有两个开口,分别与膜分离装置出口、真空泵入口相连,吸附罐顶部设置有一个开口,与排放筒相连,真空泵采用螺杆干式真空泵,真空泵出口与冷却器相连,冷却器为管壳式换热器,用循环水做冷却介质,循环水走管程,油气走壳程,换热器气体出口与冷凝器连接,液体出口与气液分离器连接;所述的液态油回收装置由气液分离器和回液泵构成,气液分离器侧面进口与预冷器、冷凝器、冷却器壳程低点连接,分离器顶部气体出口与冷凝器连接,底部出口与回液泵进口连接;所述的燃烧装置可分别选用热力燃烧或催化氧化燃烧,燃烧装置布置在吸附罐之后、排放筒之前的管道上,作为管道的一部分,热力燃烧器内布置有一系列的电阻丝,催化氧化燃烧器内设置有催化剂床层。该装置是由压缩系统、冷凝系统、膜分离系统、吸附系统、燃烧系统及液态油回收系统构成。压缩系统可采用一级压缩也可采用两级或多级压缩,采用一级压缩的,通过油气收集和输送系统来的油气由压缩机进口进入压缩机,压缩机对其做功,提高其压力后,经压缩机出口排出压缩机;如一级压缩不能满足油气后续处理压力要求,可采用二级压缩或多级压缩,多级压缩系统包括压缩机和级间冷却器,经过一级压缩机压缩做功,从一级压缩机出口排出的较高压油气进入级间冷却器,级间冷却器一般为管壳式换热器,油气走壳程,冷却介质(循环水)走管程,较高压的高温油气进入级间冷却器壳程入口,循环水进入级间冷却器管程入口,高温油气与循环水在级间冷却器换热,循环水从级间冷却器管程出口离开级间冷却器进入循环水冷却系统,高温油气得到冷却后,从级间冷却器壳程出口出来,进入二级压缩机进口,二级压缩机对油气进行做功,提高其压力,达到规定压力的油气从二级压缩机出口离开二级压缩机,去后续处理流程。冷凝系统包括油气预冷器、冷凝器、中间回液罐、冷冻机组、深度冷凝装置等,以上装置根据需要选择性配置。从压缩系统来的高压油气含有部分水蒸气,水蒸气在进入冷凝系统后会在装置内结冰,影响装置正常、稳定运行,故需对该油气进行除水。从压缩系统来的高压油气进入预冷器,预冷器一般为管壳式换热器,高压油气走壳程,从壳程入口进入,经过冷凝的低温油气走管程,从管程入口进入预冷器。高压油气与低温油气在预冷器进行换热,高压油气被冷却至约4℃,其中99%的水蒸气冷凝为水,从壳程低点排出预冷器进入中间回液罐液体入口。低温油气自管程出口离开预冷器进入后续处理系统(膜分离)。脱除了水的高压油气随即进入冷凝器,冷凝器一般为管壳式换热器,油气走壳程,从壳程入口进入冷凝器,来自冷冻系统的冷冻剂走管程,从管程入口进入,油气与冷冻剂在冷凝器内换热,油气被冷却至约-35℃,从冷凝器壳程出口排出,冷却过程中析出的液态烃类,从冷凝器壳程低点流出,进入中间回液罐液体入口。-35℃油气根据需要进一步进入深度冷凝装置冷凝或者返回预冷器作为冷却介质冷却高压油气。膜分离系统包括膜组件组成的膜装置。经过冷凝系统冷却脱除大部分烃类蒸汽的低浓度油气在真空泵的抽吸作用下进入膜分离系统,低浓度油气从膜分离装置入口进入膜分离装置,膜分离装置中有一半透膜,烃类蒸汽能穿过该膜,空气组分不能穿过该膜,于是烃类组分在膜装置一侧富集,称为富集侧,富集侧烃组分返回至冷凝系统进口,进行再次冷凝。不能穿过半透膜的空气组分和少部分未穿过半透膜的烃组分从膜装置出口排出,去后续处理流程(吸附)。吸附系统包括吸附罐、引风机、排放筒、真空泵、冷却器。来自膜分离系统的更低浓度的油气自吸附罐罐底入口进入吸附罐,吸附罐内装有吸附材料,一般活性炭。在吸附罐中油气中的烃组分被吸附,空气组分自罐顶出口离开吸附罐,经排放筒排入大气。在吸附罐内活性炭吸附一定时间后,停止吸附,关闭吸附罐底部入口阀门和顶部出口阀门,打开吸附罐底部抽真空阀门,启动真空泵,对吸附罐进行抽真空,被活性炭吸附的烃组分在减压作用下脱附,经吸附罐底部抽真空管道进入真空泵,经真空泵排入冷却器。冷却器一般为管壳式换热器,脱附的油气走壳程,循环水走管程,油气与循环水在冷却器换热,循环水从冷却器管程出口离开冷却器进入循环水冷却系统,油气得到冷却后,从冷却器壳程出口出来,冷凝下来的液态烃类经冷却器壳程低点流出,进入气液分离器液态进口。未被冷却的气体,返回至冷凝系统进口,进行再次冷凝。吸附系统设置两台吸附罐,一台罐进行吸附操作时,另一台进行脱附操作,两台罐吸附-脱附交替进行。进入气液分离器的各股流体在气液分离器内进行气-液分离,当分离器内液体体积达到50%时,回液泵启动,液态油品经气液分离器底部出口被抽送至储罐,当分离器内液体体积低于10%时,回液泵停止。气液分离器内的气体经分离器顶部出口排出罐外,返回至冷凝系统进口,进行再次冷凝。若经过吸附系统经排放筒排放的气体指标还达不到规定的排放标准,则需在排放筒前设置燃烧系统。燃烧系统包括热力燃烧器或催化氧化燃烧器,燃烧器为排放筒前管路的一部分,通过法兰形式和管道连接,热力燃烧器内设置一系列交错布置的电热丝,催化氧化燃烧器内设置具有针对性的氧化催化剂。采用热力燃烧器时,排放气中的可燃组分在灼热的电热丝网区域进行燃烧,最终转化为二氧化碳和水蒸气;采用催化氧化燃烧器时,排放气中的烃类组分在催化剂床层中进行反应,转化为二氧化碳和水蒸气。经过燃烧器后的排放气可达到最严格的排放指标。油气先进入压缩机进行压缩,压缩过程中部分重组分会液化,其余油气被加压,从压缩机出来的高压油气进入初冷器冷凝至约4℃,油气中的水蒸气液化成水排出,保障了进入深冷系统的油气不含水,不会因结冰造成冻管。从初冷器出来的油气进入深冷器,依据不同的油气组分和处理要求,深冷器冷却温度设定为-30℃~-180℃,在深冷器中油气中的大部分烃类组分被冷凝下来。不凝气进入膜分离系统进行筛分,膜分离系统将未凝气筛分为两类,一类可以透过半透膜,称为富集气(烃含量高),一类不可以透过半透膜,称为渗余气。富集气被打回深冷系统,再次进行冷凝,渗余气则进入后续吸附系统。从膜分离系统出来进入吸附系统的油气只含有分子量较小的油气组分,使用吸附剂对其进行吸附,未被吸附的组分进入后续燃烧系统。吸附剂饱和后,通过真空泵减压对其进行解吸,解吸出来的油气组分进入冷凝器冷凝回收。一般设置两台并联的吸附装置,吸附-解吸交替进行,保证整套装置的连续运行。从吸附系统排出的气体为了满足最严格的排放指标,使用热力燃烧或催化燃烧对其进行处理,使其中所含的烃类组分尽可能的降低。该方法采用了压缩+预冷+冷凝+膜分离+吸附+燃烧的集成方法,对油气进行回收、处理,特别适用于油气深度处理与回收,回收效率高,能满足严格的排放指标,处理后排放尾气中有害成分特别是三苯、汽油类物质含量达到国家排放标准要求。对于大处理量的油气回收与排放控制装置,通过将气体压缩之后再进入油气回收系统,使气体体积流量减小,减小系统装置体积与管道直径,做到系统装置的轻量化。对于不同的油气组分回收要求,冷凝系统可分别采用预冷+冷凝或预冷+冷凝+深度冷凝的方式,满足不同组分的回收需求,合理的配置也在一定程度上起到节能的效果。膜分离装置布置在吸附装置之前,使得进入吸附装置的气体量大大减小,有毒有害与挥发性烃类物质含量也极大降低,吸附罐可以做的很小,降低了吸附罐的体积和吸附剂用量。对于不同的油气组分和排放控制要求,燃烧装置可分别选用热力燃烧或催化氧化燃烧,满足不同地区排放指标的要求,做到气体达标排放。该方法采用了压缩+冷凝+膜分离+吸附回收组合方法,冷凝系统未凝结下来的油气组分进入膜分离系统进一步浓缩,得到的渗透气(浓缩气)再次进入冷凝系统冷凝回收,充分发挥膜分离系统能耗低的优点,补充因冷凝系统冷凝温度高于气体露点造成的部分组分无法被冷凝下来的缺点,通过对低露点组分的不断富集,最终使其在冷凝系统冷凝。本实用新型的有益效果在于:1)回收率高,对各种烃类易挥发组分适应能力强,能满足严格的排放标准。(2)采用集成工艺,各单元操作参数得到最大程度的优化,系统能耗相对较低。(3)采用单级吸附,达到高回收率,操作费用低。(4)装置的回收物为液态,可计量。附图说明图1一种新型集成油气深度回收与排放控制装置结构示意图。图2冷凝系统示意图结构示意图。图中,1-压缩机,2-冷凝系统,3-膜组件,4-吸附罐A,5-吸附罐B,6-吸附电磁阀A,7-吸附电磁阀B,8-放空电磁阀A,9-放空电磁阀B,10-抽真空电磁阀A,11-抽真空电磁阀B,12-电磁阀G,13-电磁阀H,14-真空泵,15-冷却器,16-气液分离器,17-回液泵。具体实施方式以下结合说明书附图以及实施例对本实用新型进行进一步说明。如图-1所示,当油气量过大时,比如油气处理量超过10000m³/h,如果采用常压处理,会导致系统管道和装置体积过大,造成投资增加,不利于操作,这时应在油气进入系统装置前将其压缩。压缩过程由压缩机完成,压缩后的油气压力依据不同的油气组分及油气回收要求确定,一般为0.5MPa左右。油气从压缩机1入口进入压缩机1,经压缩机1做功,增大其压力,由压缩机1出口排出。压缩后的油气,一方面体积减少,另一方面部分油气会因压力的增大变成液态,减小后续油气回收与排放控制系统的负荷,液态烃类进入气液分离器16。在系统内采用压缩机时,压缩机为整个系统的动力,在不采用压缩系统时,在吸附罐后设置引风机,作为系统的动力。冷凝系统:如图-2所示,冷凝系统分为预冷和冷凝两部分,预冷器和冷凝器一般为管壳式换热器,油气走壳程,冷却介质走管程。油气首先由预冷器壳程入口进入预冷器,冷却介质由管程入口进入预冷器,冷却介质可以是空气、循环水,也可以是经过冷凝后的低温油气。油气与冷却介质在预冷器内换热,温度降至4℃左右,此时油气中的大部分水分凝结成液体由预冷器壳程低点流出,进入气液分离器入口,这样既使得进入后续冷凝装置的气体状态一致,防止水分结霜、冰冻,又减少了冷凝装置的功耗。采用空气做冷却介质的,空气换热器经管程出口排到大气;采用循环水做冷却介质的,循环水经管程出口排出去往循环水冷却系统;采用低温油气做冷却介质的,低温油气换热后,去往下一步处理单元。油气自预冷器壳程出口离开预冷器,之后经冷凝器壳程进口进入冷凝器。冷凝器的冷却介质一般为机械制冷载冷剂,根据不同的冷凝温度需求选用盐水、乙二醇、乙醇等。当油气回收率要求不高或油气组分露点较高易冷凝时,油气冷凝温度降至-35℃时即可满足要求,这时冷凝器使用一级机械制冷即可达到所需温度。当油气回收率要求较高且油气组分露点很低时,油气冷凝温度需降至-70℃方能满足要求,此时需要增加一级制冷系统,因为两级制冷系统的能耗相对一步制冷更节能。在冷凝器中冷凝下来的液态烃类经冷凝器壳程低点排出冷凝器进入气液分离器,未冷凝的液体则经壳程出口排出冷凝器,去往下一步处理单元。制冷剂在冷凝器管程和制冷系统间循环。膜分离系统:如图-1所示,从冷凝系统来的不凝气进入膜组件,由于膜的选择透过性,烃类物质透过膜进入富集侧,实现烃和空气(尾气)分离,富集侧高浓度烃类进入预冷器再次进行冷凝回收,空气(尾气)进入吸附系统,进行深度吸附处理。吸附系统:,如图-1所示,吸附系统包括吸附罐、排放筒、真空泵。来自膜分离系统的更低浓度的油气自吸附罐A4罐底入口进入吸附罐A4,此时阀门A6、阀门A8处于开启状态,阀门10A、12A处于关闭状态。吸附罐内装有吸附材料,一般为活性炭。在吸附罐A4中油气中的烃组分被吸附,空气组分自罐顶出口8离开吸附罐A4,经排放筒排入大气。在吸附罐A4内活性炭吸附一定时间后,停止吸附,关闭吸附罐底部吸附阀门A6和顶部放空阀门A8,打开吸附罐底部抽真空阀门A10,启动真空泵14,此时阀门6A、阀门8A、阀门12A处于关闭状态,阀门10A处于开启状态。真空泵14对吸附罐A4进行抽真空,被活性炭吸附的烃组分在减压作用下脱附,经吸附罐A4底部抽真空管道进入真空泵14,经真空泵14排入冷却器15。冷却器15一般为管壳式换热器,脱附的油气走壳程,循环水走管程,油气与循环水在冷却器换热,循环水从冷却器15管程出口离开冷却器15进入循环水冷却系统,油气得到冷却后,从冷却器15壳程出口出来,冷凝下来的液态烃类经冷却器壳程低点流出,进入气液分离器16液态进口。未被冷却的气体,返回至冷凝系统进口,进行再次冷凝。吸附系统设置两台吸附罐A/B,一台罐进行吸附操作时,另一台进行脱附操作,两台罐吸附-脱附交替进行。液体回收系统:如图-1,进入气液分离,16的各股流体在气液分离器16内进行气-液分离,当分离器内液体体积达到50%时,回液泵17启动,液态油品经气液分离器16底部出口被抽送至储罐,当分离器16内液体体积低于10%时,回液泵17停止。气液分离器16内的气体经分离器顶部出口排出罐外,返回至冷凝系统进口,进行再次冷凝。燃烧系统:如经过吸附系统处理后的尾气仍不能达到排放指标,则在吸附系统后设置燃烧系统。燃烧系统可以使催化氧化燃烧系统,也可以是热力燃烧系统。燃烧器为排放筒前管路的一部分,通过法兰形式和管道连接。催化氧化燃烧系统是在催化氧化燃烧器内布置针对油气特定组分发生氧化反应的催化剂,使油气在经过燃烧器时,烃类组分在催化剂的作用下与油气中的氧气反应,生成CO2和H2O,从而降低排放尾气中的烃类组分含量,达到合格排放。从吸附罐3/4来的气体由催化氧化燃烧器入口进入催化氧化燃烧器,在燃烧器内气体中的烃类组分在催化剂的作用下进行氧化反应,最终生成二氧化碳和水蒸气,达到排放指标放空。热力燃烧系统是在尾气管道的特定关键内设置电热丝,电热丝通电使温度达到1000℃以上,满足油气中烃类组分的燃烧温度,当油气中的可燃烃类组分经过灼热的电热丝时,在氧气的作用下燃烧,生成CO2和H2O,从而降低排放尾气中的烃类组分含量,达到合格排放。从吸附罐3/4来的气体由热力燃烧器入口进入热力燃烧器,在燃烧器内气体中的烃类组分在灼热的电阻丝作用下燃烧,最终生成二氧化碳和水蒸气,达到排放指标放空。