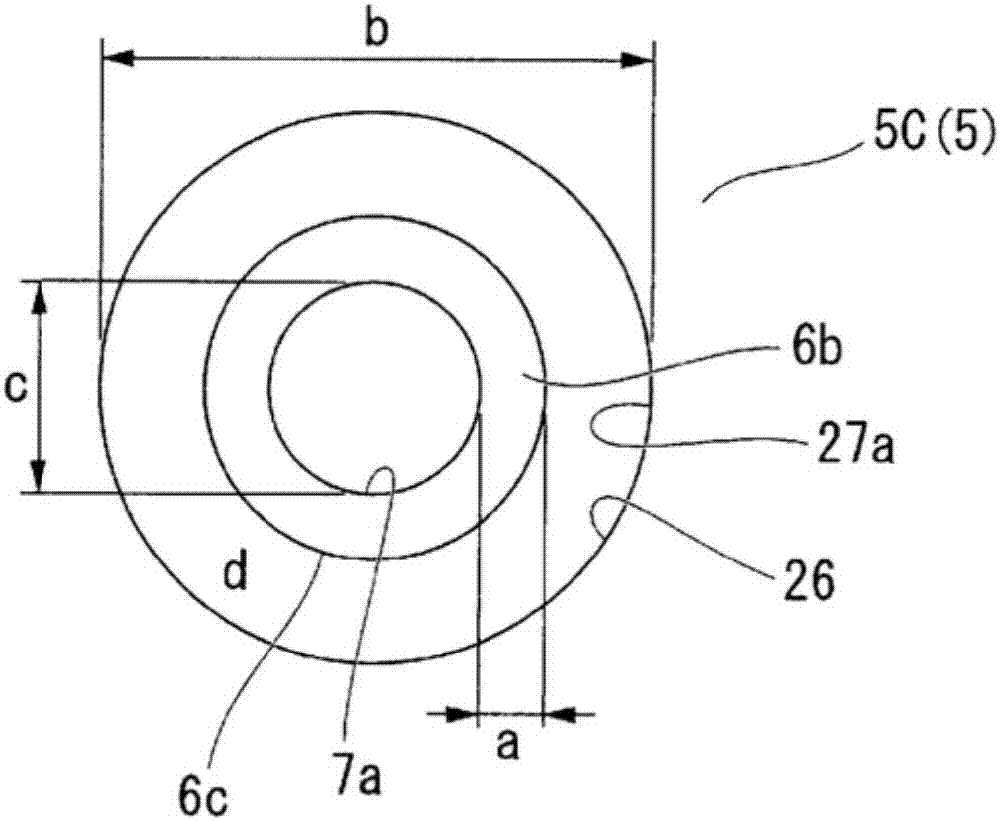
本发明涉及用于在长尺寸的中空多孔质基材的外周面涂布能形成多孔质膜层的制膜原液而制造中空纤维膜时所采用的中空纤维膜纺丝用喷嘴,以及使用该中空纤维膜纺丝用喷嘴的制造中空纤维膜的方法。
背景技术:
:近年来,由于对环境污染的关心高涨以及规定的强化,导致采用分离的完全性和紧凑性等优异的过滤膜的膜法所进行的水处理正受到瞩目。在这样的水处理的用途中,对过滤膜不仅要求分离特性和透过性能优异,而且还要求比现在更高的机械物性。作为耐压性优异的多孔质过滤膜,已知一种在中空多孔质基材的外周面形成有多孔质膜层的中空纤维膜。例如,专利文献1中提出了一种制造中空纤维膜的方法:在使打成圆绳的带子通过液体浸渍浴并脱泡之后,将该打成圆绳的带子和由可相分离的膜形成性树脂构成的制膜原液从双重环状结构的中空纤维膜纺丝用喷嘴挤出,通过湿式或干湿式纺丝法纺丝,从而制造中空纤维膜。此外,在专利文献2中提出了一种中空纤维膜纺丝用喷嘴,该喷嘴被设成:能抑制气体卷入至长尺寸的中空多孔质基材和制膜原液之间的复合部分,能抑制由气体的卷入产生的异常外径部和由局部的薄膜化造成的膜缺陷部的产生。在该中空纤维膜纺丝用喷嘴中设置有将插入有长尺寸的中空多孔质基材陆续送出的基材送出口、位于外侧以包围该基材送出口并且向中空多孔质基材的送出方向排出制膜原液的圆环状制膜原液排出口。此外,该中空纤维膜纺丝用喷嘴还设置有,用于排出从喷嘴前端至喷嘴外制膜原液包覆(复合)中空多孔质基材的外周面之处的区域中的那些空间中所存在的气体的通路。现有技术文献专利文献专利文献1:日本专利特开平5-7746号公报专利文献2:日本专利特开2007-126783号公报技术实现要素:发明所要解决的课题在采用了如上所述的中空纤维膜纺丝用喷嘴的中空纤维膜的制造方法中,有时由于设备的振动或中空多孔质基材的送出速度的变动、制膜原液中混入的气泡和制膜原液的拉丝性不均等而导致排出的制膜原液产生紊乱。此时,在上述专利文献1或专利文献2所记载的中空纤维膜的制造方法中,在喷嘴以外的制膜原液包覆于中空多孔质基材的外周面之处,有时制膜原液一时从中空多孔质基材剥离。如此地,纺丝过程中若在喷嘴以外的制膜原液包覆于中空多孔质基材的外周面之处制膜原液从中空多孔质基材剥离,则制膜原液变得不能跟随以一定速度从喷嘴送出的中空多孔质基材,由此制膜原液在喷嘴以外的制膜原液排出口附近成长为大块滴状。以下,将成长后的制膜原液块称为异常排出部。若在该状态下继续从制膜原液排出口排出制膜原液,则进一步大大地成长的异常排出部再度接触中空多孔质基材的外周面,再次开始将制膜原液涂布在中空多孔质基材。但是,在制膜原液自剥离至再次接触中空多孔质基材的外周面期间,在中空多孔质基材的外周面会产生未涂布有制膜原液的部分。此外,在异常排出部与中空多孔质基材的外周面所接触的部分中,制膜原液的厚度局部变大。这样的制膜原液的涂布斑对中空纤维膜而言是缺陷部分。尤其,在中空纤维膜的制造工序中,若在中空多孔质基材上存在较大的异常排出部,则在检查产品时需要去除缺陷部分的操作。而且,在作为接续纺丝工序的后工序的洗涤、干燥、卷绕工序等时,可能在中空纤维膜通过各装置的狭窄的开口部时在异常排出部产生阻塞,产生异常排出部缠绕于其他纺锤的中空纤维膜而受损等工序故障。因此,重要的是尽可能不产生异常排出部,以及即使产生了异常排出部,也止步于尽可能小的异常排出部。本发明是鉴于上述情况而成的,提供一种中空纤维膜的制造方法以及中空纤维膜纺丝用喷嘴,所述中空纤维膜的制造方法中,在制造时,在喷嘴外的制膜原液包覆于中空多孔质基材的外周面之处,抑制制膜原液从中空多孔质基材剥离,即使制膜原液剥离,制膜原液也迅速地再次附着于中空多孔质基材上,能够抑制制膜原液因异常排出部导致的缺陷部的发生以及在后工序中的故障的发生。用以解决课题的手段本发明具有以下的构成。[1]一种中空纤维膜的制造方法,是一种具有如下纺丝工序的中空纤维膜的制造方法,所述纺丝工序是:使用下述中空纤维膜纺丝用喷嘴,在中空多孔质基材的外周面涂布用于形成多孔质膜层的制膜原液,并使该制膜原液凝固的工序,其特征在于,从下述基材送出口送出的所述中空多孔质基材的送出速度vb相对于从下述制膜原液排出口排出的所述制膜原液的线速度va的牵伸比(vb/va)为1以上、6以下。(中空纤维膜纺丝用喷嘴)其中形成有插入所述中空多孔质基材的基材插通孔和流通所述制膜原液的制膜原液流路,并且所述制膜原液流通过所述制膜原液流路而被排出的环状制膜原液排出口,形成为隔着筒状壁包围所述基材送出口的外侧,所述基材送出口是所述中空多孔质基材通过所述基材插通孔而被送出的基材送出口。[2]根据[1]所述的中空纤维膜的制造方法,所述制膜原液排出口的开口面积是与所述中空多孔质基材的长度方向垂直的截面的截面积的3倍以下。[3]根据[1]或[2]所述的中空纤维膜的制造方法,所述制膜原液排出口的开口面积为15mm2以下。[4]根据[3]所述的中空纤维膜的制造方法,该制造方法使用40℃下的粘度为30000mpa·s以上的制膜原液。[5]一种中空纤维膜纺丝用喷嘴,是一种在中空多孔质基材的外周面涂布用于形成多孔质膜层的制膜原液的中空纤维膜纺丝用喷嘴,其特征在于,形成有插入所述中空多孔质基材的基材插通孔和流通所述制膜原液的制膜原液流路,并且所述制膜原液流通过所述制膜原液流路而被排出的环状制膜原液排出口,形成为隔着筒状壁包围所述基材送出口的外侧,所述基材送出口是所述中空多孔质基材通过所述基材插通孔而被送出的基材送出口,所述筒状壁的前端部的厚度为0.1mm以上、0.75mm以下。[6]根据[5]所述的中空纤维膜纺丝用喷嘴,所述制膜原液排出口的开口面积是与插入于所述基材插通孔的所述中空多孔质基材的长度方向垂直的截面的截面积的3倍以下。[7]根据[5]或[6]所述的中空纤维膜的制造方法,所述制膜原液排出口的开口面积为15mm2以下。[8]根据[5]~[7]的任一项所述的中空纤维膜纺丝用喷嘴,所述基材送出口的直径是插入于所述基材插通孔的所述中空多孔质基材的直径的1.01倍以上、1.20倍以下。[9]根据[5]~[8]的任一项所述的中空纤维膜纺丝用喷嘴,在所述制膜原液流路的所述制膜原液排出口附近,以1mm以上的长度形成有径直部,所述径直部以与所述制膜原液排出口相同的直径延伸至所述制膜原液排出口。[10]根据[5]~[9]的任一项所述的中空纤维膜纺丝用喷嘴,在所述制膜原液流路的所述制膜原液排出口附近,形成有延伸至所述制膜原液排出口的缩径部,所述缩径部的直径朝向所述制膜原液排出口逐渐变小。[11]根据[5]~[10]的任一项所述的中空纤维膜纺丝用喷嘴,在所述制膜原液流路内备有分歧合流装置,该分歧合流装置是使流通所述制膜原液流路的所述制膜原液在重复进行分歧和合流的同时而流通内部的装置。[12]根据[5]~[11]的任一项所述的中空纤维膜纺丝用喷嘴,形成有2个以上的所述制膜原液流路,且形成有复合部,在所述复合部中,这些制膜原液流路在所述制膜原液排出口附近合流,流通各制膜原液流路的所述制膜原液在喷嘴内部积层复合。[13]根据[5]~[12]的任一项所述的中空纤维膜纺丝用喷嘴,形成有2个以上的所述制膜原液流路,每个所述制膜原液流路均具有导入所述制膜原液的原液导入部,以及自所述原液导入部流通而至的所述制膜原液在所述基材插通孔的外侧被储液成环状的原液储液部;储存被积层于外层侧的所述制膜原液的所述原液储液部,形成为比储存被积层于内层侧的所述制膜原液的所述原液储液部更靠下游侧,并偏离所述基材插通孔的轴方向。[14]根据[13]所述的中空纤维膜纺丝用喷嘴,各个所述原液导入部相互之间在所述基材插通孔的中心轴周围间隔60°以上而形成。[15]根据[11]~[14]的任一项所述的中空纤维膜纺丝用喷嘴,所述分歧合流装置是所述制膜原液在重复进行分歧和合流的同时通过内部的多孔体元件。[16]根据[11]~[14]的任一项所述的中空纤维膜纺丝用喷嘴,所述制膜原液流路具备所述制膜原液在所述基材插通孔的外侧被储液成环状的原液储液部,所述分歧合流装置是粒子填充于所述原液储液部的内部而成的填充层。[17]根据[11]~[14]的任一项所述的中空纤维膜纺丝用喷嘴,所述制膜原液流路具备所述制膜原液在所述基材插通孔的外侧被储液成环状的原液储液部,所述原液储液部具备分为上下2段以上的储液室。[18]根据[13]所述的中空纤维膜纺丝用喷嘴,在所述制膜原液流路设置有使所述制膜原液延迟通过喷嘴的延迟装置,所述延迟装置是在所述原液储液部与将所述制膜原液赋形为筒状的原液赋形部之间使制膜原液上下蜿蜒的蜿蜒部。发明的效果根据本发明,可以抑制在喷嘴外的制膜原液包覆于中空多孔质基材的外周面之处,制膜原液从中空多孔质基材剥离,即便制膜原液剥离,制膜原液也会迅速地再附着在中空多孔质基材,能够抑制制膜原液由异常排出部导致的缺陷部的发生以及在后工序中的故障的发生。附图说明图1是本发明的一实施方式的中空纤维膜纺丝用喷嘴的示意纵截面图。图2是与沿本发明的一实施方式的中空纤维膜纺丝用喷嘴的图1的箭头a的视图对应的截面图。图3是与沿本发明的一实施方式的中空纤维膜纺丝用喷嘴的图1的箭头a的视图对应的截面图上加入了中空多孔质基材和制膜原液的截面的图。图4是图1的中空纤维膜纺丝用喷嘴的b-b截面图。图5是图1的中空纤维膜纺丝用喷嘴的c-c截面图。图6是图1的中空纤维膜纺丝用喷嘴的d-d截面图。图7是本发明的其他实施方式的中空纤维膜纺丝用喷嘴的示意纵截面图。图8是本发明的其他实施方式的中空纤维膜纺丝用喷嘴的示意纵截面图。图9是本发明的其他实施方式的中空纤维膜纺丝用喷嘴的第2喷嘴块部分的示意纵截面图。图10是本发明的其他实施方式的中空纤维膜纺丝用喷嘴的示意纵截面图。图11是本发明的其他实施方式的中空纤维膜纺丝用喷嘴的第2喷嘴块部分的示意俯视图。图12是本发明的其他实施方式的中空纤维膜纺丝用喷嘴的示意纵截面图。符号说明1中空纤维膜纺丝用喷嘴2中空多孔质基材3第1制膜原液4第2制膜原液6c筒状壁7基材插通孔7a基材送出口14第1原液导入部15第2原液导入部21第1原液储液部23第1原液赋形部25第2原液储液部27复合部27a制膜原液排出口28第1制膜原液流路29第2制膜原液流路具体实施方式[中空纤维膜纺丝用喷嘴]本发明的中空纤维膜纺丝用喷嘴是用于制造在中空多孔质基材(支持体)的外周面形成有多孔质膜层的中空纤维膜的喷嘴。本发明的中空纤维膜纺丝用喷嘴可以是用于制造具备单层多孔质膜层的中空纤维膜的喷嘴,也可以是用于制造具备两层以上的多孔质膜层的中空纤维膜的喷嘴。以下,举出用于本发明的中空纤维膜的制造方法的本发明的中空纤维膜纺丝用喷嘴的一例进行说明。本实施方式所涉及的中空纤维膜纺丝用喷嘴1(以下称纺丝用喷嘴1)是用于制造在中空多孔质基材的外周面形成有由内层和外层构成的2层结构的多孔质膜层的中空纤维膜的中空纤维膜纺丝用喷嘴。该例的纺丝用喷嘴1如图1所示地构成为:在插入中空多孔质基材2的基材插通孔10在上下方向所形成的金属制的导入板11的下游侧的端面,被螺钉等可装卸地安装。导入板11在俯视图中为圆形,沿着其轴心形成有基材插通孔10。基材插通孔10从导入板11的上游侧的端面贯通至下游侧的端面为止。导入板11中除了形成有基材插通孔10之外,还形成有导入制膜原液的第1导入孔12和第2导入孔13。俯视图中,第1导入孔12和第2导入孔13位于导入板11上相比于基材插通孔10的更外侧并分别隔有间隔,形成为从导入板11的上游侧的端面至下游侧的端面为止与基材插通孔10平行。第1导入孔12中导入用于形成多孔质膜层的内层的第1制膜原液3。第2导入孔13中导入用于形成多孔质膜层的外层的第2制膜原液4。纺丝用喷嘴1具备有喷嘴主体5,该喷嘴主体5具备从导入板11侧依次重叠为3段的圆柱状的第1喷嘴块5a、第2喷嘴块5b以及第3喷嘴块5c。作为喷嘴主体5的材质,可以选择各种材质,基于耐热性、耐腐蚀性、强度等的观点,优选不锈钢材料(sus)。如图1以及图4~6所示,第1喷嘴块5a具备圆柱状的块主体51和圆筒状的筒状突起6,其中筒状突起6被一体设置为从与块主体51中的导入板11相反侧的端面的中央突出。筒状突起6具备基端侧的大径部6a和前端侧的小径部6b。大径部6a的轴心与小径部6b的轴心是一致的。筒状突起6的内部为插入中空多孔质基材2的基材插通孔7。从筒状突起6的前端至块主体51的导入板11侧的端面为止形成有基材插通孔7,基材插通孔7与形成于导入板11的基材插通孔10连通。如图1及图2所示,在筒状突起6的前端形成有基材送出口7a,该基材送出口7a送出通过了基材插通孔7的中空多孔质基材2。插入于导入板11的基材插通孔10中的中空多孔质基材2,通过第1喷嘴块5a的基材插通孔7,从基材送出口7a送出至外部。例如,可以采用通过被设置于纺丝用喷嘴1的下游侧的卷绕辊而从基材送出口7a连续地抽出中空多孔质基材2的形态等。基材送出口7a的直径c(图2)优选为相对于插入基材插通孔7的中空多孔质基材2的直径的1.01倍以上、1.20倍以下,更优选1.05倍以上、1.15倍以下。若基材送出口7a的直径在上述下限值以上,则基材在基材插通孔内的刮挂受到抑制,基材的送出稳定性得到提高。若基材送出口7a的直径为上述上限值以下,则从制膜原液排出口27a排出的第1制膜原液3以及第2制膜原液4包覆中空多孔质基材2的外周面时的角度会变浅。如图1、图5及图6所示,第2喷嘴块5b具备圆柱状的块主体52和圆筒状的筒状突部8,其中筒状突部8被一体设置为从与块主体52中的导入板11相反侧的端面的中央突出。在块主体52中的块主体51侧的端面,形成有俯视形状为圆形的凹部20。凹部20被形成为:其内径大于筒状突起6的大径部6a的外径,而凹部20的内壁面环绕大径部6a。喷嘴主体5的内部中的凹部20和大径部6a之间的空间被设成圆环状的第1原液储液部21。圆环状的第1原液储液部21的中心与筒状突起6的大径部6a的轴心一致。如图1以及图4所示,在第1喷嘴块5a的块主体51与第2喷嘴块5b的块主体52重叠的部分形成有第1原液导入部14。第1原液导入部14在俯视图中位于块主体51中的基材插通孔7的外侧,并且与块主体52的凹部20的外周部分相对应,并且从块主体51的上游侧的端面与凹部20相通地与基材插通孔7平行而形成。第1原液导入部14的底面与凹部20的底面在同一平面上。第1原液导入部14与第1导入孔12连通,被设成可流入导入至第1导入孔12的第1制膜原液3。与第1原液导入部14的长度方向垂直的截面形状优选圆形。此外,第1原液导入部14截面形状并不限定于圆形。此外,第1原液导入部14的直径并无特别限定。流通第1原液导入部14而至的第1制膜原液3被设成流入至第1原液储液部21。第1原液储液部21中,自第1原液导入部14流入而至的第1制膜原液3在筒状突起6中的大径部6a的周围以圆环状被储液。具体来讲,自第1原液导入部14流入至第1原液储液部21的第1制膜原液3,在第1原液储液部21内分为两支并分别以圆弧状流动,在与第1原液导入部14的相反侧合流而成为圆环状。在俯视图中的筒状突部8的中央,形成有与凹部20连通并延伸至筒状突部8的前端面的贯通孔22。贯通孔22被形成为其内径大于筒状突起6的小径部6b的外径,而贯通孔22的内壁面环绕小径部6b。贯通孔22和小径部6b之间的空间被设成圆筒状的第1原液赋形部23。圆筒状的第1原液赋形部23的轴心与筒状突起6的小径部6b的轴心一致。在第1原液储液部21中被设为圆环状的第1制膜原液3,流入至第1原液赋形部23而被赋形为圆筒状。如图1以及图6所示,在第3喷嘴块5c中的块主体52侧的端面,形成有俯视形状为圆形的凹部24。凹部24被形成为其内径大于筒状突部8的外径,而凹部24的内壁面环绕筒状突部8。喷嘴主体5的内部的凹部24和筒状突部8之间的空间被设成圆环状的第2原液储液部25。圆环状的第2原液储液部25的中心与筒状突起6的小径部6b的轴心一致。纺丝用喷嘴1中,在第2喷嘴块5b的块主体52形成有第1原液储液部21,在第2喷嘴块5b的更下侧的第3喷嘴块5c形成有第2原液储液部25。即,储存被积层于外层侧的第2制膜原液4的第2原液储液部25,形成为比储存被积层于内层侧的第1制膜原液3的第1原液储液部21更靠下游侧,并偏离基材插通孔7的轴方向。本发明中,如同纺丝用喷嘴1一样地,储存积层于外层侧的制膜原液的原液储液部,形成为比储存积层于内层侧的制膜原液的原液储液部更靠下游侧,并偏离基材插通孔的轴方向。由此可以在宽度方向紧凑地设计喷嘴,可以提高制膜装置的操作性和生产率。在第1喷嘴块5a的块主体51和第2喷嘴块5b的块主体52和第3喷嘴块5c所重叠的部分,形成有第2原液导入部15。第2原液导入部15在俯视图中位于块主体51和块主体52的第1原液导入部14的外侧,并且与第3喷嘴块5c的凹部24的外周部分相对应的位置,并且与基材插通孔7平行而形成为从块主体51的上游侧的端面与凹部24相通。第1原液导入部14的底面与凹部24的底面在同一平面上。第2原液导入部15与第2导入孔13连通,被形成为导入至第2导入孔13的第2制膜原液4流入第2原液导入部15。与第2原液导入部15的长度方向垂直的截面形状优选圆形。此外,第2原液导入部15的截面形状并不限定于圆形。此外,第2原液导入部15的直径并无特别限定。该例中,第1原液导入部14和第2原液导入部15被形成为:俯视图中基材插通孔7和第1原液导入部14以及第2原液导入部15排列为一条直线。本发明中,多个原液导入部各自在俯视图中相互在基材插通孔的中心轴周围间隔60°以上的间隔而形成。在能够多层之间分散沿着轴方向的裂纹起点,可以抑制裂纹的形成方面,如此形成多个原液导入部的形态是优选的。流通第2原液导入部15而至的第1制膜原液3流入至第2原液储液部25。第2原液储液部25中,自第2原液导入部15流入而至的第2制膜原液4在筒状突部8的周围以圆环状被储液。具体来讲,自第2原液导入部15流入至第2原液储液部25的第2制膜原液4,在第2原液储液部25内分为两支并分别以圆弧状流动,在与第2原液导入部15的相反侧合流而成为圆环状。在俯视图中的第3喷嘴块5c的中央,形成有与凹部24相连通并且延伸至与第2喷嘴块5b相反侧的端面的贯通孔26。贯通孔26被形成为其内径大于筒状突起6的小径部6b的外径,而贯通孔26的内壁面环绕小径部6b。此外,贯通孔26的内径比贯通孔22的内径稍大。喷嘴主体5的内部中的贯通孔22和小径部6b之间的空间为圆筒状的复合部27。圆筒状的复合部27的轴心与筒状突起6中的小径部6b的轴心是一致的。在第2原液储液部25中被设成圆环状的第2制膜原液4,流入至复合部27,被赋形为圆筒状,同时在第1制膜原液3的外层被积层层叠。如图1~3所示,在第3喷嘴块5c中的与第2喷嘴块5b相反侧的端面,形成有作为复合部27的开口端的圆环状的制膜原液排出口27a。制膜原液排出口27a位于基材送出口7a的外侧并包围基材送出口7a,以隔着形成筒状突起6的小径部6b的前端部的筒状壁6c的状态而形成。如此地,在喷嘴主体5的内部形成有包含第1原液导入部14、第1原液储液部21以及第1原液赋形部23的第1制膜原液流路28,以及含有第2原液导入部15、第2原液储液部25的第2制膜原液流路29。而且,第1制膜原液流路28和第2制膜原液流路29在喷嘴主体5内的制膜原液排出口27a附近的复合部27合流。流通第1制膜原液流路28而至的第1制膜原液3和流通第2制膜原液流路29并且在复合部27中在第1制膜原液3的外层被积层复合的第2制膜原液4,从制膜原液排出口27a以圆筒状被排出。自制膜原液排出口27a排出的圆筒状的第1制膜原液3和第2制膜原液4,连续地包覆自基材送出口7a送出的中空多孔质基材2的外周面。筒状壁6c的前端部的厚度a(图2)优选0.1mm以上、0.75mm以下,更优选0.25mm以上、0.60mm以下。若筒状壁6c的厚度a在上述范围内,则自制膜原液排出口27a排出的第1制膜原液3和第2制膜原液4包覆中空多孔质基材2的外周面时的角度会变浅。此外,包覆上的第1制膜原液3和第2制膜原液4被中空多孔质基材2斜斜地牵拉时的角度也变浅。由此,第1制膜原液3和第2制膜原液4稳定地包覆中空多孔质基材2的外周面。此外,若筒状壁6c的厚度a在上述范围内,则自制膜原液排出口27a排出的第1制膜原液3和第2制膜原液4至包覆中空多孔质基材2的外周面为止的距离会变短。因此,自制膜原液排出口27a排出之后,至包覆中空多孔质基材2的外周面为止的期间,第1制膜原液3和第2制膜原液4处于不稳定状态的时间会缩短。由于这些情况,在纺丝用喷嘴1外的第1制膜原液3和第2制膜原液4包覆中空多孔质基材2的外周面之处,第1制膜原液3和第2制膜原液4从中空多孔质基材2的外周面剥离的情况容易受到抑制。此外,若筒状壁6c的厚度a在上述范围内,则即使在制造过程中,在第1制膜原液3和第2制膜原液4包覆中空多孔质基材2的外周面之处,从该外周面剥离的情况下,由此形成的异常排出部和中空多孔质基材2的外周面之间的距离也较短。因此,异常排出部再次接触中空多孔质基材2的外周面时的时间变短。即使在第1制膜原液3和第2制膜原液4如此地从中空多孔质基材2剥离的情况下,也更迅速地再度附着,异常排出部变得更小。此外,若筒状壁6c的厚度a在上述范围内,则在筒状突起6的前端部确保充分的耐压强度也会变得容易。制膜原液排出口27a的开口面积d(图2)优选是与插入基材插通孔7的中空多孔质基材2的长度方向垂直的截面的截面积的3倍以下,更优选是1~2.5倍。由此,在纺丝用喷嘴1外的第1制膜原液3和第2制膜原液4包覆中空多孔质基材2的外周面之处,第1制膜原液3和第2制膜原液4从中空多孔质基材2的外周面剥离的情况容易受到抑制。制膜原液排出口27a的开口面积d(图2)优选是15mm2以下,更优选是1mm2以上、15mm2以下。若制膜原液排出口27a的开口面积在15mm2以下,则在纺丝用喷嘴1外的第1制膜原液3和第2制膜原液4包覆中空多孔质基材2的外周面之处,第1制膜原液3和第2制膜原液4从中空多孔质基材2的外周面剥离的情况容易受到抑制。制膜原液排出口27a的外径b(图2)优选是1~6mm,更优选是2~5mm。本发明中优选:在制膜原液流路的制膜原液排出口附近,以与制膜原液排出口相同的直径延伸至制膜原液排出口的径直部,以1mm以上的长度形成。该例中,优选:使第1制膜原液流路28以及第2制膜原液流路29的制膜原液排出口27a附近的复合部27以与制膜原液排出口27a相同的直径具有从制膜原液排出口27a延伸1mm以上的径直部。由此,可以稳定地进行制膜原液向下方的排出。另外,本发明中也优选:在制膜原液流路的制膜原液排出口附近,形成有延伸至制膜原液排出口的缩径部,使得直径随着向制膜原液排出口而逐渐变小。例如,也优选:使第1制膜原液流路28以及第2制膜原液流路29的制膜原液排出口27a附近的复合部27具有延伸至制膜原液排出口27a的缩径部,使得直径随着向制膜原液排出口27a而逐渐变小。由此,可以缩短制膜原液通过狭窄的流路的长度,因此可以进一步降低排出制膜原液的必要压力,提高生产稳定性。本发明中优选在制膜原液流路内具备分歧合流装置,该分歧合流装置是使流通制膜原液流路的制膜原液重复进行分歧和合流的同时通过内部的装置。由此,在所制造的中空纤维膜的多孔质膜层形成沿着轴方向的裂纹起点这一情况受到抑制。作为分歧合流装置,例如可以举出制膜原液重复进行分歧和合流的同时通过内部的多孔体元件。作为多孔体元件,例如可以举出国际公开第2012/070629号中举出的元件,优选是具有三维网眼结构的多孔质体。所谓具有三维网眼结构的多孔质体是以下结构的多孔质体:形成有制膜原液在通过内部时并不直线性地流动而是在分歧为上下方向或横方向的同时进行通过的三维流路。作为多孔体元件,基于强度、热传导性、耐化学试剂性、结构均匀性方面,优选是金属微粒子的烧结体。此外,多孔体元件并不限定于金属微粒子的烧结体,也可以是金属纤维的烧结体、金属丝网的积层体或烧结积层体、陶瓷多孔体、多孔板的积层体或烧结积层体、金属微粒子的填充体等。优选设多孔体元件为圆筒状,使得制膜原液从多孔体元件的外周面朝向内周面通过。本发明中特别优选在原液储液部内设置圆筒状的多孔体元件。作为具备多孔体元件的中空纤维膜纺丝用喷嘴,例如举出图7中例示的中空纤维膜纺丝用喷嘴100(以下称纺丝用喷嘴100)。纺丝用喷嘴100具有喷嘴主体110,该喷嘴主体110具备自上依次重叠为三段的第1喷嘴块111、第2喷嘴块112以及第3喷嘴块113。第1喷嘴块111、第2喷嘴块112以及第3喷嘴块113形成为与纺丝用喷嘴1中的第1喷嘴块5a、第2喷嘴块5b及第3喷嘴块5c同样的形态。在第1喷嘴块111中的块主体111a和圆筒状的筒状突起111b的内部,形成有插入中空多孔质基材的基材插通孔114。在筒状突起111b的前端形成有将通过了基材插通孔114的中空多孔质基材送出的基材送出口114a。形成于喷嘴主体110内部的第2喷嘴块112的块主体112a的凹部115与筒状突起111b的大径部111c之间的空间被设成圆环状的第1原液储液部132。第1喷嘴块111的块主体111a和第2喷嘴块112中的块主体112a中形成有与第1原液储液部132相通的第1原液导入部131。形成于第2喷嘴块112的筒状突起112b的贯通孔116与筒状突起111b的小径部111d之间的空间被设成圆筒状的第1原液赋形部133。第1原液储液部132中设置有圆筒状的多孔体元件117。此外,形成于喷嘴主体110内部的第3喷嘴块113的凹部118与筒状突部112b之间的空间被设成圆环状的第2原液储液部142。在第1喷嘴块111的块主体111a、第2喷嘴块112的块主体112a以及第3喷嘴块113,形成有与第2原液储液部142相通的第2原液导入部141。形成于第3喷嘴块113的贯通孔119与筒状突起111b的小径部111d之间的空间被设成圆筒状的复合部143。在第3喷嘴块113的下端面,形成有作为复合部143的开口端的圆环状的制膜原液排出口143a。第2原液储液部142中设置有圆筒状的多孔体元件120。制膜原液排出口143a位于基材送出口114a的外侧并包围基材送出口114a,并且以隔着形成筒状突起111b的小径部111d的前端部的筒状壁111e的状态形成。筒状壁111e的前端部的厚度优选0.1mm以上、0.75mm以下,更优选0.25mm以上、0.60mm以下。纺丝用喷嘴100中形成有包含第1原液导入部131、第1原液储液部132及第1原液赋形部133的第1制膜原液流路130,以及包含第2原液导入部141、第2原液储液部142的第2制膜原液流路140。而且,第1制膜原液流路130和第2制膜原液流路140在复合部143合流。流通第1制膜原液流路131而至的第1制膜原液流入第1原液储液部132而在多孔体元件117的外侧成为圆环状。成为圆环状的第1制膜原液在从多孔体元件117的外周面朝向内周面重复地进行细分歧和合流的同时通过该多孔体元件117内,流入第1原液赋形部133。此外,流通第2制膜原液流路141而至的第2制膜原液流入第2原液储液部142而在多孔体元件120的外侧成为圆环状。成为圆环状的第2制膜原液在从多孔体元件120的外周面朝向内周面重复地进行细分歧和合流的同时通过该多孔体元件120内,流入复合部143。复合部143中,第2制膜原液积层复合在从第1原液赋形部133流入而至的第1制膜原液的外侧,并且从制膜原液排出口143a排出。自制膜原液排出口143a排出的第1制膜原液和第2制膜原液,连续地包覆自基材送出口114a送出的中空多孔质基材的外周面。作为分歧合流装置,例如也可以采用粒子填充于原液储液部而成的填充层。作为粒子的形状,如可以举出球状、矩形状、填料状、不均匀的三维结构物等。粒子的材质并无特别限定,可以举出以不锈钢、合金等的金属;玻璃、陶瓷等为代表的无机物;特氟龙(注册商标)、聚乙烯等的不会被制膜原液侵蚀的树脂等。作为粒子的具体例子,如可以举出钢球等。可以适当地确定粒子的大小和数量。可以适当地确定填充层的高度。作为具备填充层的中空纤维膜纺丝用喷嘴,例如举出图8以及图9中例示的中空纤维膜纺丝用喷嘴200(以下称纺丝用喷嘴200)。纺丝用喷嘴200是制造在中空多孔质基材的外侧层叠有1层多孔质膜层的中空纤维膜的纺丝用喷嘴。纺丝用喷嘴200具有喷嘴主体210,该喷嘴主体210自上依次具备重叠为两段的第1喷嘴块211以及第2喷嘴块212。在第1喷嘴块211中的块主体211a和自块主体211a向下方突出的圆筒状的筒状突起211b之间的内部,形成有插入中空多孔质基材的基材插通孔213。在筒状突起211b的前端形成有基材送出口213a,该基材送出口213a中,中空多孔质基材通过基材插通孔213后被送出。形成于喷嘴主体210内部的第2喷嘴块212的上侧部分的凹部214与筒状突起211b之间的空间被设成圆环状的原液储液部222。第1喷嘴块211和第2喷嘴块212中,形成有通过原液储液部222的原液导入部221。在第2喷嘴块212的下侧部分形成有与凹部214相通的贯通孔215。在喷嘴主体210的内部的贯通孔215与筒状突起211b之间的空间被设成圆筒状的原液赋形部223。在第2喷嘴块212的下端面形成有作为原液赋形部223的开口端的圆环状的制膜原液排出口223a。原液储液部222内形成有填充了粒子216的填充层217。制膜原液排出口223a位于基材送出口213a的外侧并包围基材送出口213a,并且以隔着形成筒状突起211b的前端部的筒状壁211c的状态形成。筒状壁211c的前端部的厚度优选0.1mm以上、0.75mm以下,更优选0.25mm以上、0.60mm以下。如此地,在纺丝用喷嘴200中形成有包含原液导入部221、原液储液部222及原液赋形部223的制膜原液流路220。流通原液导入部221而至的制膜原液流入原液储液部222,在朝向下方重复地进行细分歧和合流的同时通过填充层217中,之后流入原液赋形部223,自制膜原液排出口223a排出。制膜原液排出口223a排出的制膜原液,连续地包覆自基材送出口213a送出的中空多孔质基材的外周面。本发明的中空纤维膜纺丝用喷嘴中,当制膜原液流路具备原液储液部时,原液储液部也可以具备在上下分为2段以上的储液室。由此,可抑制在所制造的中空纤维膜的多孔质膜层形成沿着轴方向的裂纹起点。例如,本发明的中空纤维膜纺丝用喷嘴可以是图10及图11例示的中空纤维膜纺丝用喷嘴300(以下称纺丝用喷嘴300)。纺丝用喷嘴300具有喷嘴主体310,该喷嘴主体310具备自上依次重叠为三段的第1喷嘴块311、第2喷嘴块312以及第3喷嘴块313。在第1喷嘴块311中的块主体311a和自块主体311a向下方突出的圆筒状的筒状突起311b的内部形成有插入中空多孔质基材的基材插通孔314。在筒状突起311b的前端形成有基材送出口314a,该基材送出口314a中中空多孔质基材通过基材插通孔314后被送出。形成于喷嘴主体310的内部中的第2喷嘴块312的块主体312a的上侧部分的凹部315与筒状突起311b的大径部311c之间的空间被设成第1储液室322a。此外,形成于第3喷嘴块313的上侧部分的凹部317和第2喷嘴块312的筒状突部312b之间的空间被设成第2储液室322b。第1喷嘴块311的块主体311a中形成有与第1储液室322a相通的原液导入部321。此外,第2喷嘴块312的块主体312a中,以沿着形成第1储液室322a的块主体312a的内壁面地形成有从第1储液室322a通至第2储液室322b的8个供给路323。如此地,纺丝用喷嘴300中具备上下分为2段的第1储液室322a和第2储液室322b的原液储液部322。第1储液室322a具备在俯视图中截面为圆环状的圆环部325a和8个外周部325b,该8个外周部325b是块主体312a的内壁面从圆环部325a朝向外侧形成凹部的样子。8个供给路323分别在第1储液室322a中的8个外周部325b中形成。俯视图中,第1储液室322a中的1个外周部325b的位置与原液导入部321的位置是一致的。此外,该例中,8个外周部325b被形成为:各外周部325b的底面从配置有原液导入部321的一侧朝向其相反侧阶段性地降低。通过如此地在各外周部325b设置阶段差,使得制膜原液从各供给路323更为均等地供给至第2储液室322b中。第2储液室322b具备俯视图中截面为圆环状的圆环部325c和8个外周部325d,该8个外周部325d是在圆环部325c的上部中第3喷嘴块的内壁面朝向外侧形成凹部的样子。制膜原液被设成从8个供给路323分别供给至8个外周部325d。喷嘴主体310的内部中的形成于第2喷嘴块312的筒状突部312b的贯通孔316与筒状突起311b的小径部311d之间的空间,以及在第3喷嘴块313的下侧部分形成为与凹部317连通的贯通孔318与筒状突起311b的小径部311d之间的空间被设成圆筒状的原液赋形部324。在第3喷嘴块313的下端面形成有作为原液赋形部324的开口端的圆环状的制膜原液排出口324a。制膜原液排出口324a位于基材送出口314a的外侧并包围基材送出口314a,以隔着形成筒状突起311b的小径部311d的前端部的筒状壁311e的状态而形成。筒状壁311e的前端部的厚度优选0.1mm以上、0.75mm以下,更优选0.25mm以上、0.60mm以下。纺丝用喷嘴300中,如此地形成有包含原液导入部321、原液储液部322以及原液赋形部324的制膜原液流路320。流通原液导入部321而至的制膜原液流入原液储液部322的第1储液室322a,一部分成为圆环状而流入原液赋形部324,与此同时剩余部分从各供给路323被供给至第2储液室322b。被供给至第2储液室322b的制膜原液以圆环状而流入原液赋形部324。而且,流通原液赋形部324而至的制膜原液从制膜原液排出口324a排出,并连续地包覆从基材排出口314a排出的中空多孔质基材2的外周面。此外,本发明中优选在制膜原液流路上设置有使制膜原液延迟通过喷嘴的延迟装置。作为上述延迟装置,优选在原液储液部和原液赋形部之间使制膜原液上下蜿蜒的蜿蜒部。本发明的中空纤维膜纺丝用喷嘴也可以是图12所例示的中空纤维膜纺丝用喷嘴400(以下称纺丝用喷嘴400)。纺丝用喷嘴400具有喷嘴主体410,该喷嘴主体410自上依次具备重叠为三段的第1喷嘴块411、第2喷嘴块412以及第3喷嘴块413。在第1喷嘴块411中的块主体411a和自块主体411a向下方突出的圆筒状的筒状突起411b的内部,形成有插入中空多孔质基材的基材插通孔414。在筒状突起411b的前端形成有基材送出口414a,中空多孔质基材通过基材插通孔414被该基材送出口414a送出。在第1喷嘴块411的块主体411a的下端侧,形成有圆环状的凹部415,其包围筒状突起411b。在喷嘴主体410的内部中的凹部415和第2喷嘴块412之间的空间被设成第1原液储液部432。在块主体411a形成有与第1原液储液部432相通的第1原液导入部431。在第2喷嘴块412的上侧形成有俯视形状为圆形的凹部416。凹部416被形成为第2喷嘴块412的内壁面环绕筒状突起411b。在凹部416的中央部中形成有与第2喷嘴块412的下端面相通的贯通孔417。从第1喷嘴块411的下端面形成有圆筒状的第1堰418,该第1堰418形成为包围筒状突起411b并且深入凹部415内向下延伸(垂下)。第1堰418的前端距离凹部416的底面有一段距离。此外,在第2喷嘴块412的凹部416的底面中的贯通孔417的周围,形成有进入第1堰418内竖起的第2堰419。第2堰419的前端距离第1喷嘴块411的下端面有一段距离。由此,在凹部416内形成有蜿蜒部433,该蜿蜒部433使从第1原液储液部432流入而至的制膜原液以维持其形状为圆环状的状态朝向中心上下蜿蜒行走。在喷嘴主体410的内部中的贯通孔417和筒状突起411b之间的空间被设成圆筒状的第1赋形部434。在第2喷嘴块412的下端侧,在比凹部416的更靠外侧形成有圆环状的凹部420,其包围筒状突起411b。喷嘴主体410的内部中的凹部420和第3喷嘴块413之间的空间被设成第2原液储液部442。在第1喷嘴块411的块主体411a和第2喷嘴块412上形成有与第2原液储液部442相通的第2原液导入部441。在第3喷嘴块413的上侧形成有俯视形状为圆形的凹部421。凹部421被形成为第3喷嘴块413的内壁面环绕筒状突起411b。在凹部421的中央部形成有与第3喷嘴块413的下端面相通的贯通孔422。在凹部421内,分别从第2喷嘴块412的下端面和凹部421的底面突出的圆筒状的第1堰423和第2堰424被形成为2个2个地将筒状突起411b包围,以使在俯视图中朝向中心交替。第1堰423的前端自凹部421的底面间隔一段距离。第2堰424的前端自第2喷嘴块412的底面间隔一段距离。由此,在凹部421内形成有蜿蜒部443,该蜿蜒部443使从第2原液储液部442流入而至的制膜原液以维持其形状为圆环状的状态朝向中心上下蜿蜒行走。在喷嘴主体410的内部中的贯通孔422和筒状突起411b之间的空间被设成圆筒状的复合部444。在第3喷嘴块413的下端面形成有作为复合部444的开口端的圆筒状的制膜原液排出口444a。制膜原液排出口444a位于基材送出口414a的外侧,并包围基材送出口414a,以隔着形成筒状突起411b的前端部的筒状壁411c的状态而形成。筒状壁411c的前端部的厚度优选0.1mm以上、0.75mm以下,更优选0.25mm以上、0.60mm以下。纺丝用喷嘴400中,如此地形成有包含第1原液导入部431、第1原液储液部432以及蜿蜒部433以及第1原液赋形部434的第1制膜原液流路430;和包含第2原液导入部441、第2原液储液部442以及蜿蜒部443的第2制膜原液流路440。而且,第1制膜原液流路430和第2制膜原液流路440在复合部444合流。流通第1原液导入部431而至的第1制膜原液流入第1原液储液432而成为圆环状。而且,流入蜿蜒部433的第1制膜原液在上下蜿蜒行走的同时流通,向第1赋形部434流入。此外,流通第2原液导入部441而至的第2制膜原液流入第2原液储液442而成为圆环状。而且,流入蜿蜒部443的第2制膜原液在上下蜿蜒行走的同时流通,向复合部444流入。复合部444中,第2制膜原液积层复合于自第1原液赋形部434流入而至的第1制膜原液的外侧,并从制膜原液排出口444a排出。自制膜原液排出口444a排出的第1制膜原液以及第2制膜原液连续地包覆自基材送出口414a送出的中空多孔质基材的外周面。[中空纤维膜的制造方法]通过本发明的中空纤维膜的制造方法制造的中空纤维膜,是多孔质膜层形成于中空多孔质基材(支持体)的外周面的中空纤维膜。本发明的中空纤维膜的制造方法可以是制造具有单层多孔质膜层的中空纤维膜的方法,也可以是制造具有2层以上的多孔质膜层的中空纤维膜的方法。本发明的中空纤维膜的制造方法包括如下纺丝工序:通过中空纤维膜纺丝用喷嘴将用于形成多孔质膜层的制膜原液涂布于中空多孔质基材的外周面,通过凝固液使该制膜原液凝固。在本发明的中空纤维膜的制造方法中,纺丝工序之后可以采用用于得到中空纤维膜的公知工序。以下,示出本发明的中空纤维膜的制造方法的一例进行说明。作为本发明的中空纤维膜的制造方法,例如可以举出包括下述的纺丝工序、洗涤工序、去除工序、干燥工序以及卷绕工序的方法。纺丝工序:通过中空纤维膜纺丝用喷嘴将用于形成多孔质膜层的制膜原液涂布于中空多孔质基材的外周面,通过凝固液使该制膜原液凝固,得到中空纤维膜前驱体的工序。凝固工序:通过凝固液使涂布于中空多孔质基材的外周面的该制膜原液凝固,得到中空纤维膜前驱体的工序。洗涤工序:将残留于上述中空纤维膜前驱体的溶剂洗涤除去的工序。去除工序:将残留于上述洗涤后的中空纤维膜前驱体的开孔剂去除,形成中空纤维膜的工序。干燥工序:使上述去除工序后的中空纤维膜干燥的工序。卷绕工序:卷绕干燥后的中空纤维膜的工序。(纺丝工序)纺丝工序中,使自基材送出口送出的中空多孔质基材的送出速度vb相对于从中空纤维膜纺丝用喷嘴的制膜原液排出口排出的制膜原液的线速度va的牵伸比(vb/va)为1以上、6以下,将制膜原液涂布于中空多孔质基材的外周面。若vb/va为1以上、6以下,则线速度va充分地接近送出速度vb,由此在制膜原液包覆于中空多孔质基材的外周面之处,制膜原液变得难以从中空多孔质基材剥离。此外,即使在该处制膜原液从中空多孔质基材剥离的情况下,也变得更快速地再附着,异常排出部变小。vb/va为1以上、6以下,优选2以上、5.5以下。自基材送出口送出的中空多孔质基材的送出速度vb优选10~50m/分,更优选15~45m/分。此外,在本发明中,通过用齿轮泵等供给至中空纤维膜纺丝用喷嘴的制膜原液的供给量除以自制膜原液排出口的开口面积,从而求出自制膜原液排出口排出的制膜原液的线速度va。此外,从在中空纤维膜纺丝用喷嘴的下游拉出中空多孔质基材的卷绕辊等的驱动辊的旋转速度,求出自基材送出口送出的中空多孔质基材的送出速度。例如,在采用上述纺丝用喷嘴1时,将中空多孔质基材2导入到导入板11的基材插通孔10,向第1导入孔12导入第1制膜原液3,向第2导入孔13导入第2制膜原液4。导入基材插通孔10的中空多孔质基材2插入纺丝用喷嘴1的基材插通孔7,自基材送出口7a送出。导入于第1导入孔12和第2导入孔13的第1制膜原液3以及第2制膜原液4,分别流通纺丝用喷嘴1的第1制膜原液流路28和第2制膜原液流路29。而且,在复合部27中,被赋形为圆筒状,同时第2制膜原液4在第1制膜原液3的外侧被积层复合而自制膜原液排出口27a排出。以被积层复合的状态自制膜原液排出口27a排出的第1制膜原液3以及第2制膜原液4,包覆于喷嘴外自基材送出口7a送出的中空多孔质基材2的外周面。由此,第1制膜原液3以及第2制膜原液4被涂布于中空多孔质基材2的外周面。此时,分别调节自制膜原液排出口27a排出的第1制膜原液3以及第2制膜原液4的线速度va和自基材送出口7a送出的中空多孔质基材2的送出速度vb,将牵伸比(vb/va)控制为1以上、6以下。作为中空多孔质基材,可以使用用于中空纤维膜的公知的基材。作为中空多孔质基材的具体例子,例如可以举出用聚酯纤维、聚丙烯纤维等的各种原材料的纤维制成带子的中空状的编织带、丝带等。中空多孔质基材可以是将各种原材料单独使用而成的基材,也可以是将各种原材料组合2种以上而成的基材。作为用于中空状的编织带、丝带的纤维,可以举出合成纤维、半合成纤维、再生纤维、天然纤维等。作为纤维的形态,可以是单丝、多丝、纱线中的任意种。此外,作为中空多孔质基材也可以使用通过熔融延伸法而得到的多孔质中空纤维膜。此外,也可以是将上述中空多孔质基材浸渍于膜形成辅助液中而成的基材,也可以是在上述中空多孔质基材的外周面上涂布膜形成辅助液而成的基材。基于基材的生产率、基材与多孔质膜层的粘附性方面,作为中空多孔质基材优选是由1根多丝形成的编织带。中空多孔质基材的形态,只要是在垂直于基材的长度方向的截面中存在1个以上的在长度方向连通的中空部,并且流体从基材的外周面向中空部移动,进而能够向长度方向上移动的形态即可。具体地,中空多孔质基材的中空部的截面形状和基材截面的外周形状并无特别限定,可以是圆形、异形等任何形状。此外,中空部的截面形状和基材截面的外周形状可以相同,也可以不同。考虑到耐压性、赋形性等时,基材截面的外周形状优选是圆形。中空多孔质基材的外径,优选0.3mm以上、5mm以下。中空多孔质基材的外径变动尤其会对纺丝稳定性或膜厚等的品质带来影响,因此优选尽可能使用外径的变动小的中空多孔质基材。例如,在使用垂直于基材的长度方向的截面形状为圆形、并且外径为0.3mm以上、5mm以下的范围内的中空多孔质基材时,优选使该中空多孔质基材的外径的变动幅度在±0.3mm以下。本发明中,优选在插入中空纤维膜纺丝用喷嘴的基材插通孔之前对中空多孔质基材进行热处理。由此,中空多孔质基材的伸缩性变低,而且外径尺寸变得更稳定。作为制膜原液,可以使用用于形成中空纤维膜的多孔质层的公知的液体。制膜原液是将膜形成性树脂以及以控制相分离为目的的开孔剂溶解于会成为这些物质的良溶剂的有机溶剂而成的溶液。作为膜形成性树脂,可以使用用于形成中空纤维膜的多孔质膜层的普通树脂。作为膜形成性树脂的具体例子,例如可以举出聚砜树脂、聚醚砜树脂、砜化聚砜树脂、聚偏氟乙烯树脂、聚丙烯腈树脂、聚酰亚胺树脂、聚酰胺酰亚胺树脂、聚酯酰亚胺树脂等。可以根据需要,适当选择这些物质而使用,尤其,基于耐化学试剂性优异的观点,优选聚偏氟乙烯树脂。作为开孔剂,例如可以使用以聚乙二醇为代表的一元醇系、二元醇系、三元醇系、聚乙烯基吡咯烷酮等的亲水性高分子。可以根据需要适当选择这些物质而使用,尤其,基于增稠效果优异,优选聚乙烯基吡咯烷酮。作为有机溶剂,只要是能将膜形成性树脂和添加剂都溶解的溶剂即可,例如可以使用二甲基亚砜、二甲基乙酰胺、二甲基甲酰胺等。此外,制膜原液中也可以在不妨碍控制相分离的范围内使用开孔剂以外的添加剂作为任意成分。本发明中,优选使用在40℃下的粘度为30000mpa·s以上的制膜原液,更优选60000mpa·s以上的制膜原液,进一步优选150000mpa·s以上的制膜原液。制膜原液的粘度越高,越容易将多孔质膜层中的孔控制得小,能更缩小空隙,因此中空纤维膜的品质会提升。此外,也容易抑制即便牵伸比高,从中空纤维膜纺丝用喷嘴排出的制膜原液变得不稳定的情况。当如使用纺丝用喷嘴1的情况一样地使用2种以上的制膜原液,并将制膜原液分别在中空多孔质基材的外周面上涂布2层以上时,优选这些制膜原液的至少一种在40℃下的粘度是30000mpa·s以上,更优选是60000mpa·s以上,进一步优选是150000mpa·s以上。制膜原液在40℃下的粘度的上限值优选是500000mpa·s,更优选是300000mpa·s。此外,在将2种以上的制膜原液涂布于中空多孔质基材的外周面上时,优选:制膜原液中的至少一种所含的膜形成性树脂的分子量分布为3以下,并且涂布于外层侧的制膜原液所含的膜形成性树脂的分子量分布比涂布于内层侧的制膜原液所含的膜形成性树脂的分子量分布更广。由此,容易在既维持透水性能的同时又在内部形成致密结构。使涂布于中空多孔质基材的外周面上的制膜原液通过凝固液凝固,而作成中空纤维膜前驱体。中空多孔质基材上的制膜原液在凝固液中以相分离的状态凝固。本发明中,从提高透水性能方面,优选采用干湿式纺丝法,该干湿式纺丝法中,在中空纤维膜纺丝用喷嘴和凝固液之间,设置有在空气中移动规定距离的行走区间。此外,本发明中,也可以采用从中空纤维膜纺丝用喷嘴直接向凝固液中排出制膜原液的湿式纺丝。凝固液是不会溶解膜形成性树脂的溶剂,必须是开孔剂的良溶剂。作为凝固液,可以举出水、乙醇、甲醇等或这些物质的混合物。尤其,从操作环境、运行管理方面,优选用于制膜原液的溶剂和水的混合液。(洗涤工序)例如,用洗涤液洗涤中空纤维膜前驱体,将残留于中空纤维膜前驱体的溶剂洗涤去除。作为洗涤液,因洗涤效果高而优选水。作为使用的水,举出自来水、工业用水、江河水、井水等。此外,也可以在这些水中混合醇、无机盐类、氧化剂、表面活性剂等后使用。(去除工序)用氧化剂去除残留于洗涤后的中空纤维膜前驱体中的开孔剂,而形成中空纤维膜。具体来讲,将洗涤后的中空纤维膜前驱体浸渍于含有次氯酸盐等氧化剂的药液中,在气相中加热而氧化分解开孔剂,之后用洗涤液洗涤,从而去除开孔剂。通过去除在中空纤维膜前驱体中的制膜原液凝固而形成的层中残留的开孔剂,从而在该开孔剂所残留的部分形成孔,进而形成多孔质膜层,成为中空纤维膜。(干燥工序)对中空纤维膜进行干燥的方法并无特别限定,例如举出采用热风干燥机等的干燥机的方法等。(卷绕工序)将干燥后的中空纤维膜用筒管等的卷绕装置卷绕。在中空多孔质基材的外周面涂布制膜原液时,牵伸比(vb/va)越大,包覆于中空多孔质基材的外周面的制膜原液越大大地被拉延。因此,以设备的振动或中空多孔质基材的送出速度的变动为首,由制膜原液中混入的气泡或制膜原液的拉丝性不均等导致制膜原液的排出紊乱时,容易受到其影响,在喷嘴外的制膜原液包覆于中空多孔质基材的外周面之处,制膜原液容易从中空多孔质基材的剥离。而与此相对,在本发明的中空纤维膜的制造方法中,通过在纺丝工序中控制牵伸比(vb/va)为1以上、6以下,由此包覆于中空多孔质基材的外周面的制膜原液被拉延的程度会变小,因此即使制膜原液的排出紊乱,也变得难以受其影响。因此,能够抑制喷嘴外的制膜原液包覆在中空多孔质基材的外周面之处制膜原液从中空多孔质基材的剥离。此外,即使制膜原液剥离,制膜原液也会迅速再附着于中空多孔质基材,因而能够抑制制膜原液由异常排出部导致的缺陷部的发生以及在后工序中的故障的发生。此外,本发明并不被上述实施方式限定,可以在不脱离其宗旨的范围内进行各种设计变更。本发明的中空纤维膜的制造方法可以是制造具有单层多孔质膜层的中空纤维膜的方法,也可以是制造具有2层以上的多孔质膜层的中空纤维膜的方法。以下,通过实施例详细地说明本发明,但本发明不被以下记载所限定。[实施例1]使用图1~6所示的纺丝用喷嘴1制造中空纤维膜。作为中空多孔质基材2,采用了将5根聚酯纤维(纤度:84dtex,长丝数:36)集束为1根之后,通过圆纬机进行针织而编成中空状编织带的基材。此外,中空多孔质基材2采用了在纺丝用喷嘴1的上游用200℃的加热模(口径2.5mm)连续进行拉拔热处理使之低伸缩化、外径尺寸稳定化后的基材。中空多孔质基材2的外径是2.5mm,内径是1.5mm。作为第1制膜原液3使用了表1所示组成的制膜原液r1。作为第2制膜原液4使用了表1所示组成的制膜原液r2。另外,使用的原料如下所述。聚偏氟乙烯a:arkema制,商品名kynar-301f。聚偏氟乙烯b:arkema制,商品名kynar-9000hd。聚乙烯基吡咯烷酮:日本触媒公司制,商品名pvp-k79。n,n-二甲基乙酰胺。[表1]制膜原液r1制膜原液r2聚偏氟乙烯a12质量%20质量%聚偏氟乙烯b12质量%0质量%聚乙烯基吡咯烷酮12质量%10质量%n,n-二甲基乙酰胺64质量%70质量%制膜原液温度60℃60℃制膜原液中的聚偏氟乙烯浓度24质量%20质量%在纺丝用喷嘴1中,设筒状壁6c的厚度a为0.4mm、制膜原液排出口27a的外径b为4.52mm、内径为3.5mm、开口面积为6.42mm2。而且,设自制膜原液排出口27a排出的第1制膜原液3以及第2制膜原液4的线速度va为5.63m/分,设自基材送出口7a送出的中空多孔质基材2的送出速度vb为15m/分,设牵伸比(vb/va)为2.7,在中空多孔质基材2的外周面涂布第1制膜原液3以及第2制膜原液4。接着,将在中空多孔质基材2的外周面涂布第1制膜原液3以及第2制膜原液4而成的物质浸渍于凝固液浴中收纳的凝固液中,使第1制膜原液3以及第2制膜原液4凝固后提拉,用以一定速度旋转的卷绕辊提拉,使提拉速度达到每分钟15m,在80~100℃的热水中进行洗涤而得到中空纤维膜。[实施例2~4、比较例1、2]将筒状壁6c的厚度a、制膜原液排出口27a的外径b、内径以及开口面积、第1制膜原液3以及第2制膜原液4的线速度va、中空多孔质基材2的送出速度vb、牵伸比(vb/va)如表2所示地变更以外,其余与实施例1同样地设定而得到中空纤维膜。[评价方法](异常排出部的大小)对于得到的中空纤维膜,测定中空多孔质基材2的外周面上的异常排出部的最大外径tmax,将该最大外径tmax作为异常排出部的大小。若最大外径tmax为4.5mm,则在纺丝工序之后的工序中难以发生故障,因此将最大外径tmax为4.5mm以下的结果设为合格,将最大外径tmax超过4.5mm的结果设为不合格。(异常排出部的个数)测量每1000km中空纤维膜长的异常排出部的个数。每1000km中空纤维膜长的异常排出部的个数小于1个的范围,基于该异常排出部导致的故障处置操作的发生频率和伴随与此的成本增加幅度的观点,是可容许的范围。因此,设每1000km中空纤维膜长的异常排出部的个数小于1个的情况为合格,设1个以上的情况为不合格。实施例1~4以及比较例1、2的纺丝条件和评价结果如表2所示。[表2]在牵伸比(vb/va)为1以上、6以下的实施例1~4中,每1000km中空纤维膜长的异常排出部的个数小于1个,此外异常排出部的最大外径tmax都是4.5mm以下。另一方面,在牵伸比(vb/va)超过6的比较例1中,每1000km中空纤维膜长的异常排出部的个数为3.34个,异常排出部的直径为6.8mm,都是不能容许的数值。同样地,在牵伸比(vb/va)超过6的比较例2中,每1000km中空纤维膜长的异常排出部的个数为3.65个,是不能容许的数值。当前第1页12