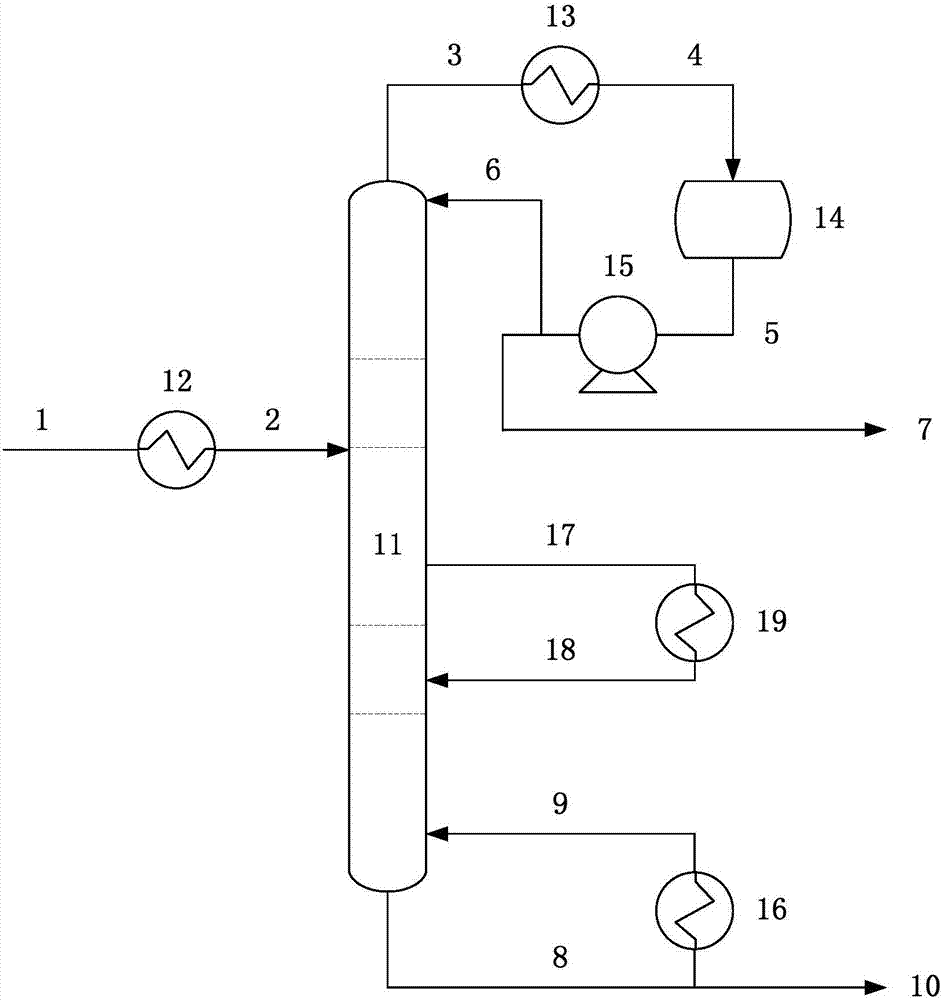
本发明涉及石油化工企业气体分馏
技术领域:
,具体地,涉及一种气体分馏装置脱丙烷塔扩产及节能的复合工艺。
背景技术:
:气体分馏装置是石油化工企业重要的轻烃分离装置,主要包含三塔分离技术和四塔分离技术。其中,三塔分离技术一般包含脱丙烷塔、脱乙烷塔和丙烯塔,四塔分离技术在此基础上还包含脱戊烷塔。气体分馏装置用于分离加工来自催化裂化、延迟焦化等装置的液化石油气,将其分离成为丙烯、丙烷、混合碳二、混合碳四和戊烷。脱丙烷塔的主要作用是将丙烯、丙烷、混合碳二和混合碳四、戊烷分离开来。近年来,随着部分老厂升级改造及催化裂化装置的技术改进,许多石油化工企业的液化气产量有所增加。同时,为了多产丙烯,部分气体分馏装置开始处理来自延迟焦化的液化气。部分石油化工企业现有的气体分馏装置面临处理量增大,液化气不能全部处理的瓶颈。脱丙烷塔作为气体分馏的第一个分馏塔,面临的瓶颈约束尤为突出。由于新增的液化气负荷不是成倍增长,不足以新建一套脱丙烷塔。因此,考虑企业建设投资的经济性,最好是在现有的塔器上进行微改造,不改变塔体直径,而使其满足生产需要。同时,在气体分馏装置中,脱丙烷塔再沸器主要消耗0.4mpa蒸汽,或120℃的热媒水。对于气体分馏装置,脱丙烷塔再沸器需要的热源温位较高,能级较高,是装置的关键能源消耗所在。因此,在扩大脱丙烷塔处理量的同时,需要考虑节能及再沸器、冷凝器的扩能问题。技术实现要素:为了在不改变现有脱丙烷塔塔体直径的情况下,提高脱丙烷塔的处理量并节省能耗,本发明提供了一种气体分馏装置脱丙烷塔扩产及节能的复合工艺。本发明提供了一种气体分馏装置脱丙烷塔扩产及节能的复合工艺,该复合工艺利用脱丙烷单元对原料进行分离,所述脱丙烷单元包括:脱丙烷塔、进料预热器、塔顶冷凝器、塔顶回流罐、塔顶回流泵和塔底再沸器;其中,提升脱丙烷塔进料温度,控制脱丙烷塔的进料温度介于60~90℃之间。通过上述技术方案,本发明的复合工艺可以在不改动分馏塔直径和塔内件的条件下,实现脱丙烷塔处理量增大5~30%,其中,提升脱丙烷塔进料温度可以实现脱丙烷塔处理量增大5~10%,提升脱丙烷塔进料温度并设置中间再沸器可以实现脱丙烷塔处理量增大10~30%。该工艺具有扩大脱丙烷塔处理量和降低脱丙烷塔再沸器热源所需较高品位热公用工程温位的优点。附图说明通过结合附图对本发明示例性实施方式进行更详细的描述,本发明的上述以及其它目的、特征和优势将变得更加明显。图1是一种常规气体分馏装置脱丙烷塔的流程示意图。图2是针对图1所示的流程进行改进的本发明的一种优选实施方式的气体分馏装置脱丙烷塔扩产及节能复合工艺的流程示意图。图3示出了实施例1的丙烯精馏塔各塔板三种工况的水力学需求直径分布,横轴n为塔板数,纵轴d为塔直径。附图标记说明1-进料(预热前)2-进料(预热后)3-塔顶气(冷前)4-塔顶气(冷后)5-塔顶凝液6-塔顶回流7-塔顶产物8-塔底物流9-再沸物流10-塔底产物11-脱丙烷塔12-进料预热器13-塔顶冷凝器14-塔顶回流罐15-塔顶回流泵16-塔底再沸器17-中间再沸抽出物流18-中间再沸返塔物流19-中间再沸器具体实施方式下面将参照附图更详细地描述本发明的优选实施方式。现有气体分馏装置脱丙烷塔的工艺流程如图1所示,本发明在此基础上进行改进,本发明的复合工艺通过提升脱丙烷塔的进料温度以及优选设置中间再沸器,调节脱丙烷塔气液负荷分布,合理避免因处理量增大可能导致的液泛和淹塔,实现脱丙烷塔扩产。同时,由于提升脱丙烷塔进料温度、设置中间再沸器,可以合理降低脱丙烷塔再沸器的负荷,降低脱丙烷塔所需要的热公用工程的温位。具体地,本发明提供了一种气体分馏装置脱丙烷塔扩产及节能的复合工艺,该复合工艺利用脱丙烷单元对原料进行分离,如图2所示,所述脱丙烷单元包括:脱丙烷塔11、进料预热器12、塔顶冷凝器13、塔顶回流罐14、塔顶回流泵15和塔底再沸器16;其中,提升脱丙烷塔进料温度,控制脱丙烷塔的进料温度介于60~90℃之间。根据所述复合工艺,通过提升脱丙烷塔的进料温度可以实现脱丙烷塔处理量增大5~10%。优选地,所述复合工艺中,提升脱丙烷塔进料温度后,控制脱丙烷塔的进料温度介于60~80℃之间。优选地,所述复合工艺中,提升脱丙烷塔进料温度后,所述进料预热器12的热源由温度介于70~100℃之间热媒水提供。优选地,所述复合工艺中,在脱丙烷塔11上设置中间再沸器19,控制扩产工况中所述中间再沸器19的负荷占基准工况所述塔底再沸器16负荷的10~30%。优选地,所述复合工艺中,所述中间再沸器19位于脱丙烷塔11的提馏段中部。优选地,所述复合工艺中,设置脱丙烷塔中间再沸器19后,中间再沸器19的热源由温度介于70~100℃之间的热媒水提供。优选地,所述复合工艺中,控制所述脱丙烷塔11的操作压力在1.80~2.20mpa之间。本发明的复合工艺通过优化脱丙烷塔的进料温度,并优选设置中间再沸器来调节脱丙烷塔的气液负荷分布,合理避免因处理量增大可能导致的液泛和淹塔,从而实现脱丙烷塔的扩产,而且,脱丙烷塔所需要的热公用工程部分能由传统的120℃的热媒水或0.4mpa蒸汽改为温度更低的热媒水,因此也降低了能耗。下面通过实施例详细说明本发明,但本发明不受实施例的限制。实施例1本例采用某石化企业30万吨/年气体分馏装置进行核算,原工艺流程如图1所示,原料为催化裂化装置脱硫液化气,流量为36.0t/h,其组成见表1。脱丙烷塔的直径为2200mm,塔板数为50。表1项目含量/mol%项目含量/mol%乙烷0.43乙烯0.02丙烯43.09丙烷5.45正丁烯6.40丁烷4.94异丁烯12.59异丁烷12.18顺丁烯5.76反丁烯8.17戊烷0.97本例的一种工艺流程如图2所示,其中,原料液化气1经进料预热器12与热媒水换热至80℃,然后进入脱丙烷塔11的中部,塔顶气3经塔顶冷凝器13冷凝后部分回流,塔顶产物7为c2、c3组分,进入下游设备;塔底产物10为c4、c5组分,塔底再沸器16的热源为0.4mpa蒸汽,塔的提馏段设置有中间再沸器19,热源为循环热媒水。本例中,工艺质量控制指标为:脱丙烷塔塔顶产物中c4~c5≤0.1mol%,塔釜产物中c2~c3≤0.1mol%。提供三种工况,通过表2所示的关键指标对比,验证本发明的复合工艺的优越性。工况一为某炼厂气体分馏装置现状工艺流程,如图1所示,原装置设有进料预热器12,预热后的进料温度为50℃,不设置中间再沸器。工况二为本发明的优选实施方式一,如图1所示,原装置设置进料预热器12,提升预热后进料温度至80℃,不设置中间再沸器。工况三为本发明的优选实施方式二,如图2所示,原装置设置进料预热器12,提升预热后的进料温度至80℃,并设置中间再沸器19,中间再沸器19负荷约为工况一塔底再沸器16负荷的15~20%。表2相比于工况一,工况二和工况三的工程改动内容包括:工况二:增大预热器换热面积,增大冷凝器换热面积。工况三:增大预热器换热面积,增大冷凝器换热面积,新增中间再沸器。图3是脱丙烷塔各塔板三种工况的水力学需求直径分布图。图3表明,工况二、工况三可以有效调节脱丙烷塔的气液负荷分布,合理避免因处理量增大可能导致的液泛和淹塔,实现脱丙烷塔扩产。脱丙烷塔处理量扩大5~10%时,优先推荐实施方式一,即工况二;脱丙烷塔处理量扩大10~20%时,优先推荐实施方式二,即工况三。在脱丙烷塔处理量扩大10%、20%时,塔底再沸器所消耗的0.4mpa蒸汽消耗量基本不变,新增处理量参照工况一所应增加的再沸器热公用工程消耗,全部由70~100℃的热媒水替代,降低了脱丙烷塔所需要的热公用工程的温位。以上已经描述了本发明的实施方式,上述说明是示例性的,并非穷尽性的,并且也不限于所披露的实施方式。在不偏离所说明的各实施方式的范围和精神的情况下,对于本
技术领域:
的普通技术人员来说许多修改和变更都是显而易见的。当前第1页12