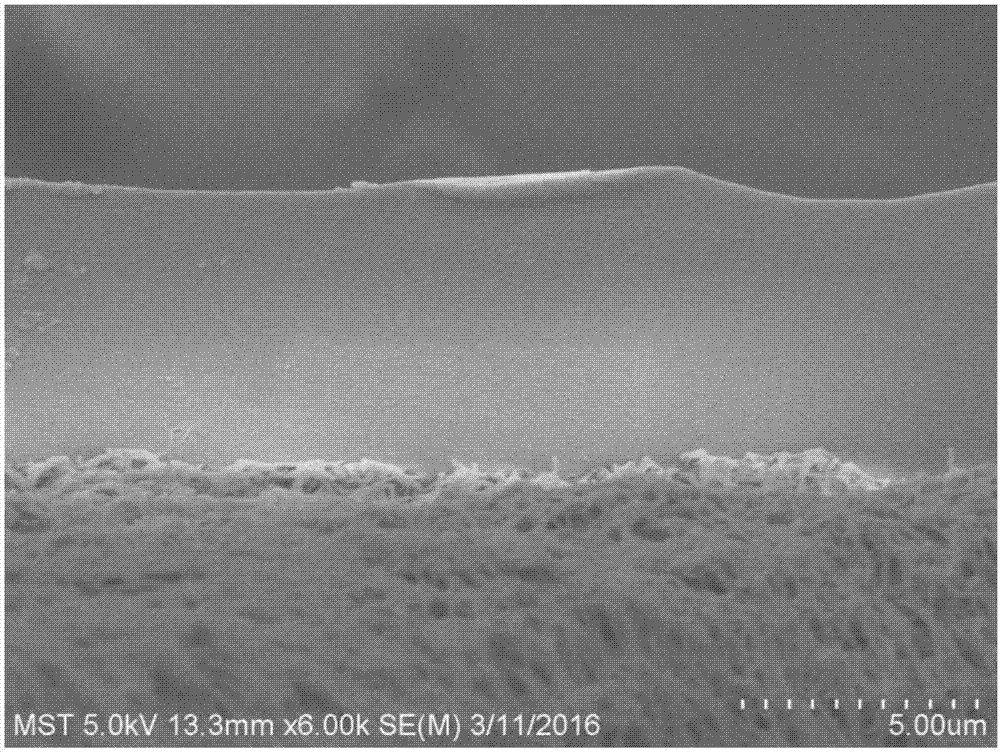
本发明涉及聚合物分离膜的制备方法,属于高分子聚合物膜领域。
背景技术:
挥发性有机物(VOCs)的无组织排放不仅会造成资源的大量浪费,还会引发环境污染,严重危害人体健康。因此国家已经制定了多条法律来限制VOCs的无组织排放。为了达到法律所规定的排放浓度,工业上已经开发出多种比较成熟的VOCs处理工艺如:吸收法、吸附法、冷凝法、生物法、膜分离法等。与其它几种分离方法相比膜分离法具有能耗小、操作简单、无二次污染、安全性能高等优点,被称为最具发展应用前景的气体分离技术。
由于三蝶烯独特的三维立体刚性结构和较大的内部自由空腔,是制备自具微孔聚合物的极佳材料。利用三蝶烯丰富的反应位点和衍生位点可以制备出网状的高分子材料,而网状的自具微孔聚合物因其具有的无定形结构、高稳定性及有机微孔等特性因而在气体吸附、氢气储存、气体分离等领域具有广泛的应用。但网状结构的自具微孔聚合物难溶于普通溶剂且易发生老化,因而大大限制了材料的推广应用。
技术实现要素:
本发明的目的在于提供一种三蝶烯基聚合物分离膜的制备方法,本方法解决了网状结构高分子材料难溶的特点,打破了网状结构聚合物因难溶易老化而难以在分离膜中应用的限制。
本发明的目的可以通过以下措施达到:
一种三蝶烯基聚合物分离膜的制备方法,其包括如下步骤:
(1)以含有活性基团的三蝶烯化合物、二酰氯化合物和含有醚键的二氨基化合物为单体,在缚酸剂存在下于非质子有机溶剂中进行聚合反应;反应后将得到的聚合物溶液倒入去离子水中进行沉析,过滤出沉析物并用甲醇洗涤,干燥,得到三蝶烯基聚合物;所述含有活性基团的三蝶烯化合物为多氨基取代的三蝶烯化合物或其衍生物;
(2)将三蝶烯基聚合物溶于非质子有机溶剂中制成铸膜液,涂覆于支撑体上并干燥,得到三蝶烯基聚合物分离膜。
本方法中,以含有活性基团的三蝶烯为第一单体,以二酰氯化合物为第二单体,以含有醚键的二氨基化合物为第三单体,在缚酸剂存在的条件下进行聚合反应。反应后将聚合物分离出后进一步采用甲醇进行洗涤干燥,随后再在非质子溶剂中溶解制备分离膜。本方法所制备的网络状结构的聚酰胺聚合物不仅能溶解于非质子溶剂,而且由此制得的分离膜均一性更高,分离性能更佳。
在步骤(1)中,对聚合物的清洗步骤具体为:聚合物溶液倒入去离子水中进行沉析,然后过滤出沉析物,用甲醇多次洗涤沉析物后过滤,将滤出物烘干后得到三蝶烯基聚合物;在一种优选条件下,滤出物采用烘箱干燥的方式烘干,烘干温度:40℃~120℃。
本发明的含有活性基团的三蝶烯化合物选自六氨基取代的三碟烯化合物或其衍生物、四氨基取代的三碟烯化合物或其衍生物、三氨基取代的三碟烯化合物或其衍生物、二氨基取代的三碟烯化合物或其衍生物中的任意一种。
在一种优选方案中,含有活性基团的三蝶烯化合物选自2,3,6,7,12,13-六氨基三碟烯、2,3,6,7-四氨基三碟烯、2,6,14-三氨基三蝶烯、2,7,14-三氨基三蝶烯、9,10-二甲基-2,6,14-三氨基三蝶烯、9,10-二甲基-2,7,14-三氨基三蝶烯、2,6-二氨基三蝶烯、2,7–二氨基三蝶烯等中的任意一种。
在一种更优选的方案中,含有活性基团的三蝶烯化合物选自2,6,14-三氨基三蝶烯、2,7,14-三氨基三蝶烯、9,10-二甲基-2,6,14-三氨基三蝶烯、9,10-二甲基-2,7,14-三氨基三蝶烯、2,6-二氨基三蝶烯、2,7–二氨基三蝶烯中的一种。
本发明中的二酰氯化合物可选自草酰氯、丙二酰氯、丁二酰氯、戊二酰氯、己二酰氯、1,7-庚二酰氯、壬二酰氯、六氟戊二酰氯、癸二酰氯、1,8-二辛酰氯、对苯二甲酰氯、间苯二甲酰氯、邻苯二甲酰氯、1,4-环己二酰氯、均苯三甲酰氯、反丁烯二酰氯、四氟对苯二甲酰氯、六氟戊二酰氯、十二烷二酰二氯、1,8-二辛酰氯、2,6-氯甲酰吡啶、1,4-亚苯基二丙烯酰氯、反式-3,6-桥-亚甲基-1,2,3,6-四氢邻苯二甲酰氯、5-氨基-2,4,6-三碘-1,3-苯二羧酸酰氯、偶氮苯-4,4’-二羰酰氯、4,4'-联苯二乙酰氯、反式-环丁烷-1,2-二羰酰氯、1,4-亚苯基二丙烯酰氯、双酚A双氯甲酸酯中的任意一种。
在一种优选方案中,本发明中的二酰氯化合物可选自草酰氯、丙二酰氯、丁二酰氯、戊二酰氯、己二酰氯、1,7-庚二酰氯、癸二酰氯、对苯二甲酰氯、间苯二甲酰氯、邻苯二甲酰氯、1,4-环己二酰氯、均苯三甲酰氯、反丁烯二酰氯、四氟对苯二甲酰氯、六氟戊二酰氯中的一种。
本发明中的含有醚键的二氨基化合物可采用带氟基团或不带氟基团的含有醚键的二氨基化合物,例如双(3-氨丙基)醚、3,4-二氨基二苯醚、间苯二酚二缩水甘油醚、4,4'-二氨基二苯醚、新戊基乙二醇双(4-氨基苯基)醚、1,3-二(4-氨苯氧基)苯、N-甲基-N-(4-氨基苯氧乙基)-4-氨基苯乙胺、2,2-双[4-(4-氨基苯氧基)苯基]-1,1,1,3,3,3-六氟丙烷、2,2’-二氨基乙二醇二苯醚、1,8-二氨基-3,6-二氧杂辛烷、双[4-(3-氨基苯氧基)苯基]砜、1,4-丁二醇双(3-氨基丁烯酸酯)、4,4”-二氨基对三联苯、2,2-双[(4-氨基苯氧基)苯基]六氟丙烷、2,2-双(三氟甲基)-4,4-二氨基苯基醚、1,3-双(2-三氟甲基-4-氨基苯氧基)苯、1,4-双(2-三氟甲基-4-氨基苯氧基)苯、2,2-双[4-(4-氨基苯氧基)苯基]丙烷中的任意一种。
在一种优选方案中,本发明中的含有醚键的二氨基化合物选自3,4-二氨基二苯醚、4,4'-二氨基二苯醚、2,2-双[(4-氨基苯氧基)苯基]六氟丙烷、2,2-双(三氟甲基)-4,4-二氨基苯基醚、1,3-双(2-三氟甲基-4-氨基苯氧基)苯、1,4-双(2-三氟甲基-4-氨基苯氧基)苯、2,2-双[4-(4-氨基苯氧基)苯基]丙烷中的一种。
三种单体含有活性基团的三蝶烯化合物、二酰氯化合物和含有醚键的二氨基化合物之间的摩尔用量比为1:1.0~20.0:0.2~10;优选:1:2.0~10.0:0.5~5;缚酸剂的摩尔用量为二酰氯化合物摩尔量的1~10倍,优选:1.5-5倍。
本发明中的缚酸剂为有机碱或无机碱,优选选自吡啶、三乙胺、N,N-二异丙基乙胺、4-二甲氨基吡啶、三乙醇胺、碳酸钾、碳酸钠、碳酸氢钠、氢氧化钾、氢氧化钠中的任意一种。
在步骤(1)中,所述非质子有机溶剂选自甲基吡咯烷酮、二甲基甲酰胺、二甲基乙酰胺、二甲基亚砜、六甲基磷酰酰胺中的任意一种。
在步骤(1)中,聚合反应的温度为-5~15℃,反应时间为1~18小时,聚合反应在惰性气体保护下进行。
在步骤(2)中,一种具体的制膜方法为:将三蝶烯基聚合物溶于非质子有机溶剂后真空脱泡静置得到铸膜液,将铸膜液涂覆于支撑体上后烘箱干燥,得到三蝶烯基聚合物分离膜;在一种优选条件下,干燥温度为40℃~150℃,干燥时间为2小时~96小时。
在步骤(2)中,所述非质子有机溶剂选自甲基吡咯烷酮、二甲基甲酰胺、二甲基乙酰胺、二甲基亚砜、乙腈、二恶烷、六甲基磷酰酰胺中的任意一种。
在步骤(2)中,铸膜液的浓度为0.5~25wt%,优选1~20wt%,进一步优选5~15wt%。
本发明中的支撑体选自有机材料底膜或无机材料底膜,优选聚四氟乙烯、醋酸纤维素、陶瓷中任意一种。
目前三维立体网状自具微孔高分子材料因其特殊的微孔结构、优良的机械性能及热稳定性备受研究者的青睐,是目前最具应用前景的气体分离膜材料。但是因网状结构的存在而难溶于普通溶剂,在分离膜中的应用受到限制。本发明克服了因网状聚酰胺材料不溶于普通溶剂而使得制备的VOCs分离膜成膜性差、易老化、分离效率低的缺点。同时,通过调节制膜过程的一系列参数可以有效调控聚酰胺膜的VOCs分离性能以达到不同的分离要求。
附图说明
图1是本发明所得分离膜的断面SEM电镜图;
图2是本发明所得分离膜的表面SEM电镜图;
图3是本发明所得分离膜的表面SEM数码图;
图中,左图为三碟烯基聚合物分离复合膜;右图为聚四氟乙烯底膜。
具体实施方式
下面结合实施例对本发明做进一步说明,但本发明的保护范围不限于此:
三碟烯基聚合物分离膜的截留率计算公式如下:
其中:Pp为透过侧的VOCs浓度(ppm),Pb为原料侧VOCs浓度(ppm),R为截留率。
实施例1
取2,6,14-三氨基三蝶烯0.6g,2,2’-双(三氟甲基)-4,4’-二氨基苯基醚0.7g,癸二酰氯1.6g,放入250ml烧瓶中,在常温下加入50ml二甲基甲酰胺进行搅拌溶解,然后加入吡啶1ml。然后将温度降至-5℃反应5小时(氮气保护)。反应结束后就反应升温至室温然后加入150ml去离子水进行沉析。将沉析物过滤并用甲醇清洗3~4次后,将沉淀物在真空50℃的条件下烘干。本方法与专利CN201510883253.2的区别之一是将制备的聚合物洗涤纯化干燥后,再在非质子溶液中溶解制备复合膜,复合膜均一性更高,分离性能更好。
溶解性测试:
取干燥后的沉淀物进行溶解性测试,溶剂分别为氯仿、水、甲基吡咯烷酮、四氢呋喃、二甲基甲酰胺、二甲基乙酰胺、二甲基亚砜、六甲基磷酰酰胺、乙醚、环己烷、正庚烷。测试结果发现沉淀物在室温下可溶于二甲基甲酰胺、二甲基乙酰胺、二甲基亚砜、甲基吡咯烷酮、六甲基磷酰酰胺非质子极性溶剂。
取共聚物0.8g,溶于10ml二甲基甲酰胺,完全溶解后真空脱泡静置2小时,将所得铸膜液涂在聚四氟乙烯支撑体上,在80℃烘箱中烘24小时,得到三蝶烯基含氟聚酰胺膜。
测试本例得到的复合膜对于N2/C6H6体系的分离性能,当温度为25℃,压力为10kpa时,渗透流速为0.24L/m2min,经过膜分离后,环己烷浓度由原料侧的30000ppm降低至渗透侧的90ppm,截留率为99.7%。
测试本例得到的复合膜对于N2/C6H6体系的分离性能,当温度为25℃,压力为2kpa时,渗透流速为0.10L/m2min,经过膜分离后,环己烷浓度由原料侧的30000ppm降低至渗透侧的12ppm,截留率为99.96%。
实施例2
取2,7,14-三氨基三蝶烯0.3g,1,3-双(2-三氟甲基-4-氨基苯氧基)苯0.428g,戊二酰氯0.546g,放入250ml烧瓶中,在常温下加入40ml二甲基甲酰胺进行搅拌溶解,然后加入三乙胺1.5ml,然后将温度降至0℃反应10小时(氮气保护)。反应结束后升温至室温然后加入100ml去离子水进行沉析。将沉析物过滤并用甲醇清洗3~4次后,将沉淀物在真空60℃的条件下烘干。本方法与专利CN201510883253.2的区别之一是将制备的聚合物洗涤纯化干燥后,再在非质子溶液中溶解制备复合膜,复合膜均一性更高,分离性能更好。溶解性测试:
取干燥后的沉淀物进行溶解性测试,溶剂分别为氯仿、水、甲基吡咯烷酮、四氢呋喃、二甲基甲酰胺、二甲基乙酰胺、二甲基亚砜、六甲基磷酰酰胺、乙醚、环己烷、正庚烷。测试结果发现沉淀物在室温下可溶于二甲基甲酰胺、二甲基乙酰胺、二甲基亚砜、甲基吡咯烷酮、六甲基磷酰酰胺非质子极性溶剂。
取共聚物0.5g,溶于10ml二甲基甲酰胺,完全溶解后真空脱泡静止2小时,将所得铸膜液涂在聚醚酰亚胺支撑体上,在90℃真空烘箱中烘36小时,得到三蝶烯基含氟聚酰胺膜。
测试本例得到的复合膜对于N2/C6H6体系的分离性能,当温度为25℃,压力为10kpa时,渗透流速为0.25L/m2min,经过膜分离后,环己烷浓度由原料侧的30000ppm降低至渗透侧的120ppm,截留率为99.6%。
实施例3
取9,10-二甲基-2,6,14-三氨基三蝶烯0.45g,1,3-双(2-三氟甲基-4-氨基苯氧基)苯0.6g,己二酰氯0.85g,放入250ml烧瓶中,在常温下加入45ml二甲基甲酰胺进行搅拌溶解,然后加入N,N-二异丙基乙胺0.5ml。然后将温度降至5℃反应12小时(氮气保护)。反应结束后升温至室温然后加入120ml去离子水进行沉析。将沉析物过滤并用甲醇清洗3~4次后,将沉淀物在真空70℃的条件下烘干。本方法与专利CN201510883253.2的区别之一是将制备的聚合物洗涤纯化干燥后,再在非质子溶液中溶解制备复合膜,复合膜均一性更高,分离性能更好。
溶解性测试:
取干燥后的沉淀物进行溶解性测试,溶剂分别为氯仿、水、甲基吡咯烷酮、四氢呋喃、二甲基甲酰胺、二甲基乙酰胺、二甲基亚砜、六甲基磷酰酰胺、乙醚、环己烷、正庚烷。测试结果发现沉淀物在室温下可溶于二甲基甲酰胺、二甲基乙酰胺、二甲基亚砜、甲基吡咯烷酮、六甲基磷酰酰胺非质子极性溶剂。
取共聚物0.6g,溶于10ml二甲基甲酰胺,完全溶解后真空脱泡静止2小时,将所得铸膜液涂在聚偏氟乙烯支撑体上,在100℃烘箱中烘48小时,得到三蝶烯基含氟聚酰胺膜。
测试本例得到的复合膜对于N2/C6H6体系的分离性能,当温度为25℃,压力为10kpa时,渗透流速为0.32L/m2min,经过膜分离后,环己烷浓度由原料侧的30000ppm降低至渗透侧的240ppm,截留率为99.2%。
实施例4
取9,10-二甲基-2,6,14-三氨基三蝶烯0.45g,1,4-双(2-三氟甲基-4-氨基苯氧基)苯0.336g,对苯二甲酰氯0.72g,放入250ml烧瓶中,在常温下加入40ml二甲基甲酰胺进行搅拌溶解,然后加入三乙醇胺1ml。然后将温度降至10℃反应15小时(氮气保护)。反应结束后升温至室温然后加入110ml去离子水进行沉析。将沉析物过滤并用甲醇清洗3~4次后,将沉淀物在真空70℃的条件下烘干。本方法与专利CN201510883253.2的区别之一是将制备的聚合物洗涤纯化干燥后,再在非质子溶液中溶解制备复合膜,复合膜均一性更高,分离性能更好。
溶解性测试:
取干燥后的沉淀物进行溶解性测试,溶剂分别为氯仿、水、甲基吡咯烷酮、四氢呋喃、二甲基甲酰胺、二甲基乙酰胺、二甲基亚砜、六甲基磷酰酰胺、乙醚、环己烷、正庚烷。测试结果发现沉淀物在室温下可溶于二甲基甲酰胺、二甲基乙酰胺、二甲基亚砜、甲基吡咯烷酮、六甲基磷酰酰胺非质子极性溶剂。
取共聚物0.7g,溶于10毫升二甲基甲酰胺,完全溶解后真空脱泡静止2小时,将所得铸膜液涂在聚砜支撑体上,在110℃真空烘箱中烘60小时,得到三蝶烯基含氟聚酰胺膜。
测试本例得到的复合膜对于N2/C6H6体系的分离性能,当温度为25℃,压力为10kpa时,渗透流速为0.31L/m2min,经过膜分离后,环己烷浓度由原料侧的30000ppm降低至渗透侧的273ppm,截留率为99.09%。
实施例5
取2,7,14-三氨基三蝶烯0.3g,2,2-双[4-(4-氨基苯氧基)苯基]丙烷0.428g,均苯三甲酰氯0.538g,放入250ml烧瓶中,在常温下加入45ml二甲基甲酰胺进行搅拌溶解,然后加入4-二甲氨基吡啶2.5ml。然后将温度降至15℃反应18小时(氮气保护)。反应结束后升温至室温然后加入100ml去离子水进行沉析。将沉析物过滤并用甲醇清洗3~4次后,将沉淀物在真空80℃的条件下烘干。本方法与专利CN201510883253.2的区别之一是将制备的聚合物洗涤纯化干燥后,再在非质子溶液中溶解制备复合膜,复合膜均一性更高,分离性能更好。
溶解性测试:
取干燥后的沉淀物进行溶解性测试,溶剂分别为氯仿、水、甲基吡咯烷酮、四氢呋喃、二甲基甲酰胺、二甲基乙酰胺、二甲基亚砜、六甲基磷酰酰胺、乙醚、环己烷、正庚烷。测试结果发现沉淀物在室温下可溶于二甲基甲酰胺、二甲基乙酰胺、二甲基亚砜、甲基吡咯烷酮、六甲基磷酰酰胺非质子极性溶剂。
取共聚物0.7g,溶于7ml二甲基甲酰胺,完全溶解后真空脱泡静止两小时,将所得铸膜液涂在醋酸纤维素支撑体上,在120℃烘箱中烘72小时,得到三蝶烯基含氟聚酰胺膜。
测试本例得到的复合膜对于N2/C6H6体系的分离性能,当温度为25℃,压力为10kpa时,渗透流速为0.36L/m2min,经过膜分离后,环己烷浓度由原料侧的30000ppm降低至渗透侧的276ppm,截留率为99.08%。
实施例6
取2,6,14-三氨基三蝶烯0.455g,3,4-二氨基二苯基醚0.363g,戊二酰氯0.823g,放入250ml烧瓶中,在常温下加入30ml二甲基甲酰胺进行搅拌溶解,然后加入三乙醇胺1.5ml。然后将温度降至0℃反应10小时(氮气保护)。反应结束后升温至室温然后加入110ml去离子水进行沉析。将沉析物过滤并用甲醇清洗3~4次后,将沉淀物在80℃的条件下烘干。本方法与专利CN201510883253.2的区别之一是将制备的聚合物洗涤纯化干燥后,再在非质子溶液中溶解制备复合膜,复合膜均一性更高,分离性能更好。
溶解性测试:
取干燥后的沉淀物进行溶解性测试,溶剂分别为氯仿、水、甲基吡咯烷酮、四氢呋喃、二甲基甲酰胺、二甲基乙酰胺、二甲基亚砜、六甲基磷酰酰胺、乙醚、环己烷、正庚烷。测试结果发现沉淀物在室温下可溶于二甲基甲酰胺、二甲基乙酰胺、二甲基亚砜、甲基吡咯烷酮、六甲基磷酰酰胺非质子极性溶剂。
取共聚物0.6g,溶于10毫升二甲基甲酰胺,完全溶解后真空脱泡静止2小时,将所得铸膜液涂在聚砜支撑体上,在100℃真空烘箱中烘60小时,得到三蝶烯基聚酰胺膜。
测试本例得到的复合膜对于N2/C6H6体系的分离性能,当温度为25℃,压力为10kpa时,渗透流速为0.32L/m2min,经过膜分离后,环己烷浓度由原料侧的30000ppm降低至渗透侧的150ppm,截留率为99.5%。
以上实施例仅为说明发明的技术思想,不能以此限定本发明的保护范围,凡是按照本发明提出的技术思想,在技术方案基础上所做的任何改动,均落入本发明保护范围之类:本发明未涉及的技术均可通过现有技术加以实现。
对比例1
重复专利CN201510883253.2中实施例3的方法,采用2,6,1 4-三氨基三蝶烯、癸二酰氯作为合成的主要单体,吡啶作为缚酸剂,甲基吡咯烷酮作为溶剂进行合成反应,其具体步骤如下:将1mol的2,6,1 4-三氨基三蝶烯,3mol的吡啶,2mol的癸二酰氯加入到甲基吡咯烷酮溶液中搅拌溶解,在温度为2℃(氮气保护)条件下,反应3.5h,反应结束后升温至室温然后加入去离子水进行沉析。将沉析物过滤并用甲醇清洗后,将沉淀物在真空80℃的条件下烘干。
取烘干后的聚合物0.7g,溶于7ml二甲基甲酰胺溶液中,聚合物不能完全溶解,得不到均一的铸膜液。