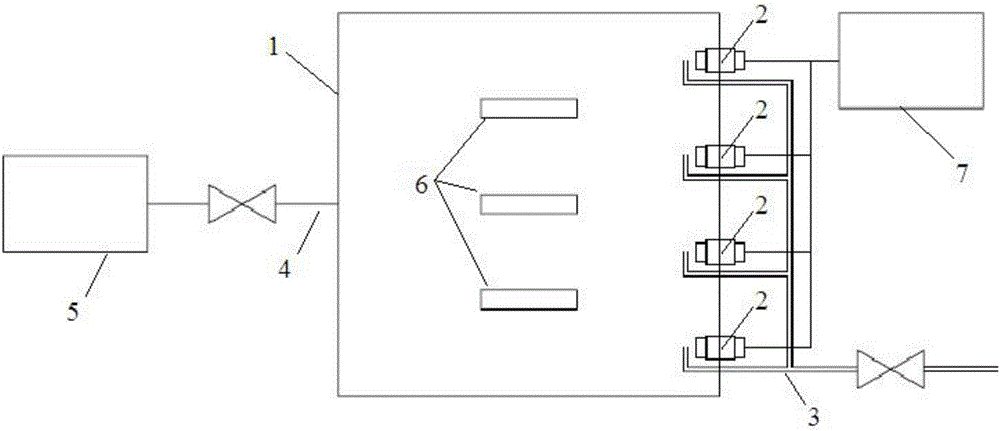
本发明属于等离子体技术领域,涉及到一种等离子体引发聚合表面涂层装置及方法,用于在基材表面制备聚合物涂层。
背景技术:
等离子体聚合是利用放电把有机类气态单体等离子体化,使其产生各类活性种,由这些活性种之间或活性种与单体之间进行加成反应形成聚合物的方法。等离子体聚合可分为等离子体态聚合和等离子体引发聚合两种形式,它们的区别是:等离子体态聚合整个反应过程中单体完全暴露于等离子体环境,而等离子体引发聚合中气体只在短时间内通过辉光放电形成的等离子体,使单体蒸汽发生气相反应生成活性中心,引发单体蒸汽在长时间无等离子体的后续过程中进行聚合反应。与等离子体态聚合产物存在结构复杂,反应重现性差,处理效果随时间衰减的问题相比,等离子体引发聚合方式可以较少破坏单体的结构,保留单体优良性能,使聚合产物结构较为单一,易于形成线性大分子产物;另一方面,通过与材料表面发生接枝反应,能够增强表面的附着力,使涂层效果不随时间衰减。
现有的等离子体引发聚合技术是通过脉冲调制高频辉光放电实现的。例如文献《表面涂层》(CN 1190545C)公开了一种疏水和/或疏油基材,其中包括利用脉冲调制高频辉光放电制备聚合物涂层的方法;文献《通过低压等离子体工艺施加保形纳米涂层的方法》(CN201180015332.1)也涉及利用脉冲调制高频辉光放电制备聚合物涂层的方法。这些现有技术必须采用脉冲调制高频辉光放电,是因为采用高频放电能够避免由于电极被聚合产物绝缘所造成的放电终止,高频放电即使电极被聚合产物绝缘情况下也可以维持,而采用脉冲调制使高频放电周期性开启/关断是为了满足等离子体引发聚合所需要的短时间放电和长时间无放电聚合,其中为了尽可能减少脉冲放电开启阶段等离子体作用于单体而产生的单体碎片,要尽可能缩短脉冲放电开启阶段时间。然而,现有技术所采用的脉冲调制高频辉光放电的方法需要使用具有脉冲调制功能的高频电源,且需要充入一定气压的载体气体来维持放电。其缺点是:脉冲调制高频电源结构复杂、价格昂贵;不易调整匹配,设备不易放大,工艺移植性不好;放电不稳定,工艺重复性不良;存在强射频电场易损伤基材;另外,充入载体气体使腔内气压较高,单体扩散不良,从而造成涂层不均匀等。
技术实现要素:
本发明要解决的技术问题是提供一种电火花等离子体引发聚合表面涂层装置及方法,以解决现有技术电源结构复杂、价格昂贵、不易调整匹配、设备不易放大,工艺移植性不好、放电不稳定、工艺重复性不良、存在强射频电场易损伤基材、需要载体气体、单体扩散不良、涂层不均匀的问题。
本发明所采用的技术方案如下:
一种电火花等离子体引发聚合表面涂层装置,其特征在于:在真空室内间隔安装多个火花塞,构成阵列,火花塞与电源连接,单体蒸汽管路连接在真空室内,单体蒸汽管路在位于火花塞的正前方设置出口,单体蒸汽管路另一端连接到单体蒸汽源,排气管位于真空室远离火花塞和单体蒸汽管路出口的一侧,排气管另一端与真空泵连接,待处理的基材放在真空室内。
所述的火花塞相邻间隔10cm-30cm进行安装。
所述单体蒸汽管路的出口与火花塞的距离为1cm-10cm。
所述电源产生的高压脉冲的峰值为5-20kV,脉宽为2-50μs,重复频率为1-1000Hz。
一种利用上述所述的电火花等离子体引发聚合表面涂层装置进行表面涂层的方法,其特征在于:主要包括以下步骤:
(1)待处理的基材放在真空室内,开启真空泵将真空室抽至压强1Pa以下;
(2)开启单体蒸汽管路,通入单体蒸汽,所述单体蒸汽含有不饱和碳碳键,其中一个不饱和碳原子上不含取代基;
(3)开启电源,电源产生高压脉冲加在火花塞上产生电火花,引发单体蒸汽聚合并沉积在基材表面形成涂层。
所述的步骤(2)中所述的单体包括二甲基乙烯基乙氧基硅烷,丙烯酸,甲基丙烯酸,甲基丙烯酸甲酯,甲基丙烯酸乙酯、甲基丙烯酸丁酯,丙烯酰胺,甲基丙烯酸-2-羟乙酯,2-丙烯酰胺-2-甲基丙磺酸,甲基丙烯酸长链酯类,如甲基丙烯酸正辛酯,甲基丙烯酸正十二酯,甲基丙烯酸正十四酯中的一种或几种。
所述单体的结构中含有卤素官能团或其他官能团,所述卤素官能团为F,Cl,Br,I中的一种或多种,所述其他官能团为羟基,羧基,环氧基团,硅氧基团中一种或多种。
本发明的上述技术方案与现有技术相比具有以下优点:
(1)火花塞电源结构简单、价格低、无需调整匹配。
(2)火花塞数量和阵列面积可根据需要增加扩展,设备容易放大,工艺移植性好。
(3)放电稳定,工艺重复性好。
(4)不存在强射频电场,不损伤基材。
(5)不需要载体气体,单体扩散良好,涂层均匀。
附图说明
图1是实现本发明方法的装置结构示意图。
图中:1、真空室,2、火花塞,3、单体蒸汽管路,4、排气管,5、真空泵,6、基材,7、电源。
具体实施方式
下面结合附图和具体实施例详细说明本发明,但本发明并不局限于具体实施例。
实施例1
如图1中,在真空室内相邻间隔10cm安装多个火花塞,构成阵列,火花塞与电源连接,电源产生的高压脉冲峰值为5kV,脉宽为2μs,重复频率为1000Hz,单体蒸汽通过单体蒸汽管路送入真空室内,单体蒸汽管路连接在真空室内,且在与火花塞的正前方距离为1cm处设置出口,单体蒸汽管路另一端连接到单体蒸汽源,排气管位于真空室远离火花塞和单体蒸汽管路出口的一侧,与真空泵连接,待处理的基材放在真空室内。
实施例2
一种使用实施例1所述的电火花等离子体引发聚合表面涂层装置进行表面涂层的方法,主要包括以下步骤:
(1)将待处理的基材放在真空室内,开启真空泵将真空室抽至压强1Pa;
(2)开启单体蒸汽管路通入单体蒸汽,所述单体蒸汽含有至少一个不饱和碳碳键,其中一个不饱和碳原子上不含取代基,优选的单体为丙烯酸和甲基丙烯酸丁酯;
(3)电源产生高压脉冲加在火花塞上产生电火花,电火花作用于单体蒸汽,引发单体蒸汽聚合并沉积在基材表面形成涂层。
实施例3
如图1中,在真空室内相邻间隔30cm安装多个火花塞,构成阵列,火花塞与电源连接,电源产生的高压脉冲峰值为20kV,脉宽为50μs,重复频率为1Hz,单体蒸汽通过单体蒸汽管路送入真空室内,单体蒸汽管路连接在真空室内,且在与火花塞的正前方距离为10cm处设置出口,单体蒸汽管路另一端连接到单体蒸汽源,排气管位于真空室远离火花塞和单体蒸汽管路出口的一侧,与真空泵连接,待处理的基材放在真空室内。
实施例4
一种使用实施例3所述的电火花等离子体引发聚合表面涂层装置进行表面涂层的方法,主要包括以下步骤:
(1)将待处理的基材放在真空室内,开启真空泵将真空室抽至压强0.4Pa;
(2)开启单体蒸汽管路,通入单体蒸汽,所述单体蒸汽含有至少一个不饱和碳碳键,其中一个不饱和碳原子上不含取代基,优选的单体为二甲基乙烯基乙氧基硅烷;
(3)电源产生高压脉冲加在火花塞上产生电火花,电火花作用于单体蒸汽,引发单体蒸汽聚合并沉积在基材表面形成涂层。
实施例5
如图1中,在真空室内相邻间隔20cm安装多个火花塞,构成阵列,火花塞与电源连接,电源产生的高压脉冲峰值为10kV,脉宽为25μs,重复频率为500Hz,单体蒸汽通过单体蒸汽管路送入真空室内,单体蒸汽管路连接在真空室内,且在与火花塞的正前方距离为5cm处设置出口,单体蒸汽管路另一端连接到单体蒸汽源,排气管位于真空室远离火花塞和单体蒸汽管路出口的一侧,与真空泵连接,待处理的基材放在真空室内。
实施例6
一种使用实施例5所述的电火花等离子体引发聚合表面涂层装置进行表面涂层的方法,主要包括以下步骤:
(1)将待处理的基材放在真空室内,开启真空泵将真空室抽至压强0.06Pa;
(2)开启单体蒸汽管路,通入单体蒸汽,所述单体蒸汽含有至少一个不饱和碳碳键,其中一个不饱和碳原子上不含取代基,优选的单体为甲基丙烯酸乙酯;
(3)电源产生高压脉冲加在火花塞上产生电火花,电火花作用于单体蒸汽,引发单体蒸汽聚合并沉积在基材表面形成涂层。