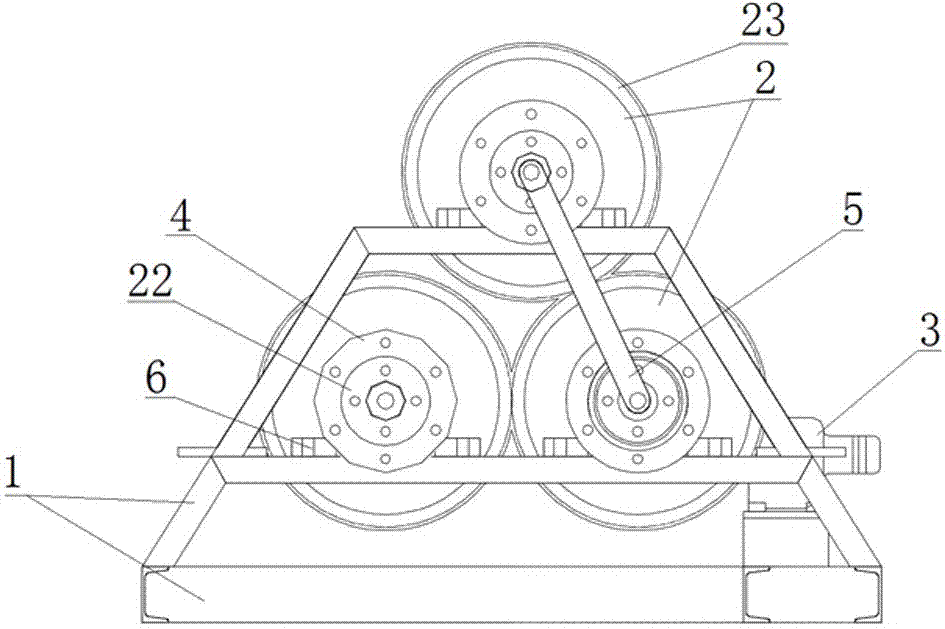
本实用新型涉及多相动态反应器。
背景技术:
随着重工业的发展及人们生活水平的提高,来自工业和生活的废物也越来越多,给环境污染治理造成很大的难题。废弃污染物主要包括固、液、气三态,治理方法也不尽相同,但固、液、气基本均需要与液体的化学试剂接触进行反应。针对固态污染物,传统的治理方法有填埋及化学反应等方法,针对化学反应方法,需要将固体污染物放入反应容器中并加入化学试剂与其进行反应,以使固体反应物逐渐与化学试剂反应转化为无害的物质。但由于固体为颗粒或块状,其与化学试剂反应时是逐层溶解的方式,并且是依靠化学试剂与其逐层反应使其体积逐渐缩小,整个过程需要花费很长时间,对于有些表面有一层不与化学试剂反应的保护层的固体污染物,化学试剂无法固体污染物内部的可反应物质反应,严重影响反应效率,还有一些反应物可能会在反应容器的壳体上结疤,严重时甚至堵塞相关管道,使废物处理速度和效率低下,造成设备长期运行时的能耗及化学试剂的过多消耗等,使其无法满足日益增加的废物的处理需求。
技术实现要素:
本实用新型的目的在于提供一种多相动态反应器,以解决固体废物处理的效率低下的技术问题。
为实现上述目的,本实用新型多相动态反应器的技术方案是:多相动态反应器包括支架和安装在支架上的滚筒,滚筒内部具有供物料反应的反应腔,滚筒的一端设有供物料进入的物料入口,滚筒的另一端设有供物料送出的物料出口,物料入口和物料出口与所述反应腔连通,所述滚筒传动连接有驱动滚筒的驱动装置。采用本实用新型的多相动态反应器,通过滚筒将滚筒内部的物料进行翻滚,物料内部的固体颗粒物在离心力作用下相互撞击以使颗粒物被逐层剥离打碎,以增大物料中固体颗粒与化学试剂的接触面积,提高反应效率;另外,此方式还可将具有不反应外部保护层的固体废物打碎,使其内部可反应物质反应,提高固体废除处理能力;另外,本实用新型多相动态反应器不仅可以针对固体废物进行处理,还能同时对液体和气体废物进行处理,以便适用于更复杂的混合废物的处理。
进一步地,所述反应腔内设有用于与物料碰撞以剥磨物料的磨剥件。采用磨剥件与物料中的固体颗粒相互碰撞方式对固体废物逐层剥离打磨,增加反应面积,与此同时配合化学试剂进行反应,使反应速率大大提高,提高固体废物的处理效率。
进一步地,所述反应腔内装有相对滚筒转动以对所述反应腔内的物料进行剥离打磨的活动碰撞件。采用活动碰撞件相对于固定在反应腔内壁上的磨剥件其碰撞几率更大,剥离效果更好。
进一步地,所述滚筒两端具有两块对滚筒内的活动碰撞件进行挡止以防活动碰撞件甩出的挡板,挡板中心线处设有开口,两个开口分别构成所述物料入口和物料出口。通过滚筒两端的挡板的挡止作用,可防止滚筒内部的活动碰撞件在离心力作用下甩出,物料出、入口设在挡板中心线处的目的以为了配合旋转接头使用,使滚筒在旋转时其物料依然连续流动。
进一步地,所述滚筒至少包括一个首级滚筒和一个末级滚筒,滚筒之间通过旋转接头和管道依次串连贯通,首级滚筒的所述物料入口处设有用于与进料管道连接的旋转接头。通过设置多个滚筒,相互之间通过旋转接头和管道串接,并且针对不同滚筒设置不同尺寸的活动碰撞件,物料先进入首级滚筒时其尺寸较大,相应的采用与之适配的第一种尺寸的活动碰撞件对其进行逐层磨剥反应,然后尺寸变小的物料进入中间滚筒,中间滚筒内设有与变小的物料尺寸相配的第二种尺寸的活动碰撞件,对其进行进一步剥磨,起到逐层剥磨、针对性更强,反应效率更高;首级滚筒的物料入口处设置旋转接头的目的是为了方便物料与首级滚筒之间的对接,保证输送物料的同时不影响滚筒的转动;另外,采用多个滚筒的方式相对于一根长滚筒,其转动时中间部分因不同轴误差导致离心力较大的问题也得以改善,使滚筒使用寿命更长,同时,滚筒转动时对滚筒的支架的振动也更小,使之间与滚筒之间的连接部位不易损坏,且降低了振动时的噪声。
进一步地,所述末级滚筒的物料出口处设有用于与出料管道连接的旋转接头。末级滚筒设置旋转接头的目的是为了方便物料出口与外部管道的对接,使正常输送物料的同时不影响末级滚筒的转动。
进一步地,所述滚筒外周上固设有齿圈,所述驱动装置包括电机以及与电机的输出轴传动连接的主动齿轮,主动齿轮与所述齿圈啮合传动。通过在滚筒外周固设齿圈,并由电机及与之相连的齿轮和齿圈配合以带动滚筒转动的方式,使滚筒的端部得以空出来以便作为管道连通的接口,此方式布置合理,不仅方便滚筒之间的连接,而且便于减小整体的长度,使布局更紧凑。
进一步地,所述滚筒包括首级滚筒、中间滚筒和末级滚筒,中间滚筒的物料入口与首级滚筒的物料出口连接,中间滚筒的物料出口与末级滚筒的物料入口连接,三个滚筒上的所述齿圈依次啮合传动,三滚筒的齿圈中的一个与所述主动齿轮啮合传动。三个滚筒之间通过滚筒外部的齿圈依次啮合传动,只要其中一个滚筒转动,其余两个滚筒便会作为首级滚筒的从动件跟随滚动,因此只需要其中一个滚筒外部的齿圈与电极上的主动齿轮啮合即可。
进一步地,所述支架包括上下两层,上层设有一套轴承座组件,轴承座组件包括两个对称的轴承座,下层并列设有两套所述轴承座组件,三套所述轴承座组件呈三角形布置,所述三个滚筒分别安装在三套所述轴承座组件上。对于三个并列滚筒,呈三角形布置时其结构更紧凑,通过轴承从滚筒两端滚动支撑滚筒,以便滚筒的中部留出足够空间供齿圈之间啮合传动。
进一步地,所述活动碰撞件为钢珠。钢珠作为活动碰撞件,其本身的使用寿命较长,其对滚筒内部的反应腔内壁的损伤和磨损最小,以便增加滚筒的使用寿命,而且钢珠相对与其他有棱角的活动碰撞件,其噪音也最小。
附图说明
图1为本实用新型多相动态反应器的具体实施例的主视结构示意图;
图2为图1的左视图;
图3为图1的俯视图;
图中:1-支架,2-滚筒,21-物料入口,22-物料出口,23-齿圈,3-电机,31-主动齿轮,4-旋转接头,5-连接管,6-轴承座。
具体实施方式
下面结合附图对本实用新型的实施方式作进一步说明。
本实用新型的多相动态反应器的具体实施例,如图1至图3所示,包括支架1和安装在支架1上的滚筒2,滚筒2内部具有供待反应物料反应的反应腔,滚筒2的两端分别设有供物料进出的物料入口21和物料出口22,物料入口21和物料出口22与反应腔连通,支架1上还安装有驱动滚筒2转动的驱动电机3,反应腔内装有相对滚筒2转动以对反应腔内的物料进行剥磨的钢珠。物料(待处理废物和参与反应的化学试剂)从滚筒2的物料入口21进入滚筒2内部的反应腔,反应腔内部钢珠随滚筒2的转动而滚动,钢珠、反应腔内壁以及物料中的颗粒物之间相互摩擦与撞击,将颗粒物一层层剥离并打磨,使其与反应腔中的化学试剂充分接触并反应,以提高反应速率和反应效率。
如图1-3所示,支架1包括位于底部的支撑板和焊接在支撑板上的两个对称的梯形耳架,梯形耳架中部具有一根横梁,以将支架1分为上下两层,最上层的横梁中间安装有一个轴承座6,下层横梁(即梯形耳架中部的横梁)上安装有两个并列的轴承座6,两个轴承座6与位于上层的轴承座6呈三角形布置,以使结构紧凑。在其他实施例中,滚筒2及相对应的轴承座也可采用一排的布置方式,以适应一个方向要求尺寸较小的情况。两个梯形耳架对称设置且梯形耳架上的六个轴承座6构成三对轴承座6组,每对轴承座6组可安装一个滚筒2。安装时滚筒2的两端通过轴承与轴承座6连接,三个滚筒2安装后保证三个滚筒2的轴线平行,且在转动时相互无干涉。
滚筒2包括一个圆柱筒,滚筒2的内部具有可供物料和化学试剂在其中反应的反应腔,滚筒2的两端分别具有一个挡板,挡板可防止滚筒2转动时其内部的钢珠甩出。两挡板上位于挡板的中心线处设有物料入口21和物料出口22,且物料入口21和物料出口22连接有旋转接头4,旋转接头4具有旋转密封作用,以便在滚筒2转动的同时不影响物料的进出。在其他实施例中,滚筒2也不仅仅只能为圆柱形,也可替换为多边形棱柱,如六棱柱;滚筒2两端的挡板可以是圆形或多边形,挡板可以是与滚筒2一体加工也可以是相互密封连接。
滚筒2的反应腔内部装有多个钢珠,在其他实施例中,钢珠也可替换为其他耐腐蚀、耐磨损的合金或不锈钢等材质。钢珠可在滚筒2转动时跟随滚筒2在反应腔内部滚动,以便对反应腔内的物料的固体颗粒物进行剥离、打磨,以便物料可以更充分、迅速的反应。在其他实施例中,钢珠作为也可替换为圆柱滚子或带孔的小长方体等其他活动碰撞件;当钢珠出现从物料出、入口甩出的情况时,可通过在物料出入口设置筛网的方式对其进行挡止,但需保证筛网的孔径能供物料中的固体颗粒通过且钢珠不会通过。
在其他实施例中,滚筒2内设置的活动碰撞件也可替换为固定在反应腔上的磨剥件,如在反应腔的内壁上均匀铰接可在滚筒2的转动方向上转动的碰撞块,或者反应腔内壁上均匀布置凸出的悬臂状碰撞块,以便在转动时对物料内的固体颗粒进行碰撞打磨。
滚筒2的外周位于两端之间固设有齿圈23,齿圈23的位置以方便与其他齿圈23或齿轮配合和方便整体的布置为准,可根据具体情况调整齿圈23距离滚筒2两端的距离。滚筒2一共设有三个,分为首级滚筒、中间滚筒和末级滚筒,三个滚筒2呈三角形并列平行设置,位于支架1上层的首级滚筒的一端作为反应器的物料入口21,另一端与位于支架1下层的中间滚筒最近的一端通过连接管5和旋转接头4连接,保证连接处密封性能,中间滚筒的另一端与末级滚筒的一端通过连接管5和旋转接头4连接,同样保证密封性能,末级滚筒的另一端即为反应器的物料出口22。物料通过首级滚筒的物料入口21,也即反应器的物料入口21后在首级滚筒的反应腔中一边通过钢珠剥离一边反应,并连续的向中间滚筒中通入,经过中间滚筒后经更进一步的反应,同样地,继续经过末级滚筒反应并从物料出口22流出,物料连续的依次经过三个滚筒2并在三个滚筒2中依次反应,以最终将固体颗粒及其他物质反应充分。在三个滚筒2中设置的钢珠的尺寸可根据反应的需要设置不同的粒径尺寸,以针对逐渐变小的固体颗粒物进行更精细的剥离与进一步反应。
三个滚筒2外部的齿圈23可相互啮合传动,如图2所示,首级滚筒的齿圈23与中间滚筒的齿圈23啮合,中间滚筒的齿圈23与末级滚筒的齿圈23啮合,末级滚筒的齿圈23通过固定在支架1的底板上的电机3及其输出轴上的主动齿轮31带动,电机3转动带动电机3输出轴上的主动齿轮31转动,主动齿轮31带动与其啮合的末级滚筒的齿圈23转动,齿圈23与滚筒2相互固定,因此滚筒2随齿圈23同步转动,滚筒2内部的钢珠在滚筒2内部的反应腔中也随之滚动,同样地,第二、首级滚筒也随之转动,使三个滚筒2同步转动,内部的钢珠同时对各自所在反应腔中的物料进行剥离打磨。
在其他实施例中,滚筒2之间齿圈23的传递顺序也可替换为电机3的主动齿轮31带动中间滚筒转动,中间滚筒同时带动首、末级滚筒随其同步转动;同样的,电机3的主动齿轮31也可与首级滚筒的齿圈23啮合传动;滚筒2的数量也不仅仅只能是三个,也可根据反应物反应的难易调整为一个或四个等,针对容易剥离和反应的物料可采用滚筒2数较少的反应器,并可通过调整物料向反应器中的流速以控制反应的程度,针对较难剥离和反应的物料,尤其是其中含有大颗粒或难剥离的颗粒的物料,可采用多个滚筒2,逐层剥离,以使反应充分,多个滚筒2相对于一根长度很长的滚筒2,其不仅结构更紧凑也能避免一个滚筒2中部离心力太大而造成的一系列问题;反应器的物料入口21和物料出口22也可替换为物料入口21在下层,物料出口22在上层;当待反应物料需要加热时,可在滚筒2的外部套装加热装置。
本实用新型多相动态反应器在使用时:装配时,将装好钢珠的滚筒2分别装在轴承座6上,保证滚筒2在轴承座6内的轴承内转动灵活,通过旋转接头4和连接管5分别将三个滚筒2串连成一个具有一个物料入口21和一个物料出口22的整体,并保证物料入口21和物料出口22之间的通道畅通。将物料输送管连接在反应器物料入口21处的旋转接头4上,将接收物料的容器的管道连接在反应器的物料出口22的旋转接头4上,完成安装对接。工作时,开动反应器,然后将待反应物料和反应的化学试剂通入反应器内,物料中的固体颗粒在反应腔内的钢珠的碰撞打磨下逐层剥离,剥离的同时化学试剂与其不停的反应,使固体颗粒逐层变小,直至从反应器的物料出口22送出以前就完全被反应掉。当物料为液体、气体或气、液、固三相混合物时,其在反应器内与化学试剂反应的同时被反应腔中的钢珠打散搅匀,以增加接触面积,加快反应速率。当待处理废物为热解时才能反应或加热能增大反应速率时,在滚筒2外部套设加热装置,如加热炉套。