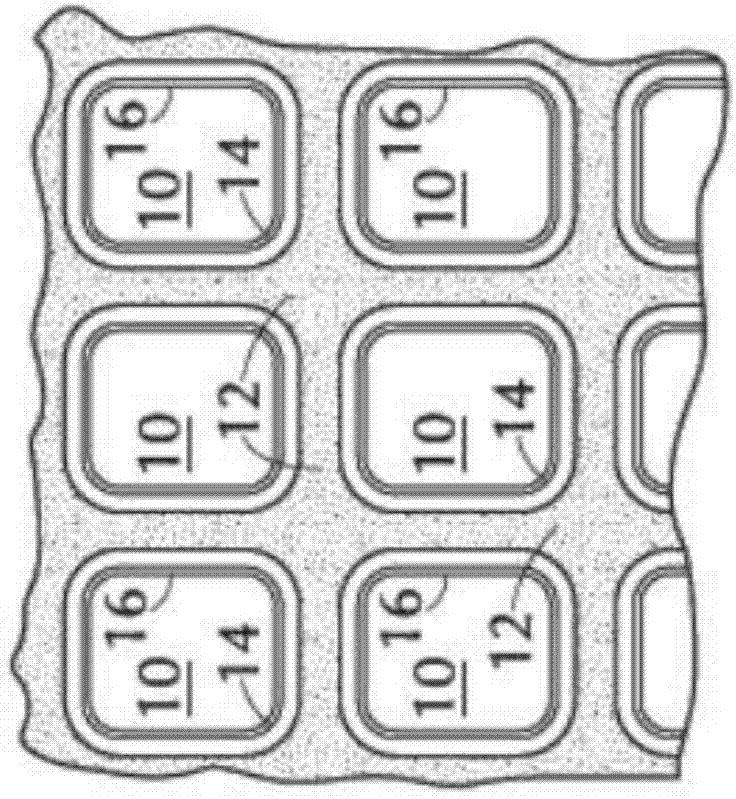
稀燃发动机,例如柴油发动机和稀燃汽油发动机的运行为使用者提供优异的燃料经济性并由于它们在稀燃条件下在高空/燃比下的运行而具有气相烃和一氧化碳的低排放。另外,柴油发动机在其燃料经济性、耐久性及其在低速下产生高扭矩的能力方面提供优于汽油(火花点火)发动机的显著优点。但是,从排放的角度看,柴油发动机可能存在比它们的火花点火对应物更严重的问题。由于柴油发动机排气是多相混合物,排放问题涉及颗粒物(PM)、氮氧化物(NOx)、未燃烃(HC)和一氧化碳(CO)。NOx是用于描述各种化学类型的氮氧化物的术语,尤其包括一氧化氮(NO)和二氧化氮(NO2)。NO受到关注,因为其在高层大气中转化成NO2,认为NO在这里在日光存在下经由一系列反应经历被称作光化学烟雾形成的过程。烃受到关注,因为它们是酸雨的显著成因。另一方面,地平面NO2具有作为氧化剂的高潜力并且是强的肺刺激物。有效减少稀燃发动机的NOx是难以实现的,因为高NOx转化率通常需要富还原剂条件。排气料流的NOx组分转化成无害组分通常需要用于在稀燃条件下运行的专用NOx减排策略。这些策略之一采用NOx的选择性催化还原(SCR),其涉及在还原剂(例如脲)存在下经SCR催化剂,例如氧化钒-二氧化钛基催化剂或用贱金属如Cu、Fe或其它贱金属助催化的沸石的NOx反应。当SCR催化剂的进料气体中的NO2/NOx比率充足时,可以观察到性能增强,尤其是在低温范围(即<250℃)内。包含分散在耐火金属氧化物载体上的贵金属如铂族金属(PGM)的氧化催化剂已知用于处理柴油发动机的排气以通过催化这些污染物的氧化将烃和一氧化碳气态污染物转化成二氧化碳和水。此类催化剂通常包含在被称作柴油机氧化催化剂(DOC)的单元中,将所述单元置于柴油供能的发动机的排气流径中以在排气排放到大气之前将其处理。通常,柴油机氧化催化剂在陶瓷或金属支承基底(例如流通型整料支承体)上形成,在基底上沉积一种或多种催化剂涂料组合物。除转化气态HC、CO和颗粒物的可溶性有机成分(SOF)外,含有铂族金属(其通常分散在耐火氧化物载体上)的氧化催化剂还促进氧化一氮(NO)氧化成二氧化氮(NO2)。用于处理内燃机排气的催化剂在相对低温运行期间,如发动机运行的初始冷启动期间较低效,因为发动机排气没有在足够高以有效催化转化排气中的有害组分的温度下。为此,可包括吸附剂材料,如沸石作为催化处理系统的一部分以吸附气态污染物,通常是烃,并在初始冷启动期间留住它们。随着排气温度提高,吸附的烃从吸附剂中驱出并在较高温度下经受催化处理。包含分散在耐火金属氧化物载体上的铂族金属(PGM)的氧化催化剂已知用于处理来自柴油发动机的废气排放。铂(Pt)在稀燃条件下、在燃料硫存在下的高温老化后仍然是DOC中用于氧化CO和HC的最有效的金属。使用钯(Pd)基催化剂的主要优点之一是Pd比Pt的成本低。但是,Pd基柴油机氧化催化剂通常表现出较高的用于CO和HC氧化的起燃温度,尤其是在用于处理含高硫含量(来自高含硫燃料)的排气时或在与HC存储材料一起使用时。特定组分的“起燃”温度被定义为50%的该组分反应的温度。含Pd的DOCs可能毒化Pt转化HCs和/或氧化NOx的活性,还可能使催化剂更容易硫中毒。这些特征通常限制富Pd的氧化催化剂在稀燃运行中的应用,尤其是对于轻型柴油机用途,其中发动机温度在大多数行驶条件下保持低于250℃。已经开发出具有含Pd/二氧化铈层的分层设计的低温CO氧化汽车催化剂。这些催化剂与传统Pt/Pd/氧化铝DOC配方相比由于在Pd/二氧化铈位点的氧活化而在低温区具有活性。但是,Pd/二氧化铈DOCs具有固有硫敏感性。Pd/二氧化铈位点可不可逆地被硫破坏,这最终转化成差CO性能。催化剂的脱硫在稀燃柴油机运行中需要高温(>740℃)或在富燃条件中需要较低温度(550-650℃)。由于大多数发动机制造商既不希望在这样高的稀燃温度下运行也未准备富燃惩罚(fuelpenalty),仍然需要提供具有改进的耐硫性的改进的柴油机氧化催化剂。WO2012/166868描述了包含沸石催化剂和负载型铂族金属催化剂的冷启动催化剂。该沸石催化剂包含贱金属、贵金属和沸石。该负载型铂族金属催化剂包含一种或多种铂族金属和一种或多种无机氧化物载体。在WO2012/166868中,至少一个实施例描述了涂布在基底上的Fe助催化的β沸石;然后将Pd添加到Fe-沸石涂布的基底上,Pt/氧化铝形成在Pd-Fe/沸石上的中间层,然后Pd/CeO2形成在Pt/氧化铝上的顶层。WO2012/085572描述了一种排气系统,其包含布置在第一蜂窝整料基底上的第一氧化催化剂,所述第一氧化催化剂包含负载在包含至少一种可还原氧化物的第一金属氧化物载体上的铂,其中第一氧化催化剂基本不含碱金属和碱土金属。在WO2012/085572中,硫阱(sulfursink)可包括分子筛,并且当包含时,该硫阱在第一层(或下层)中。尽管在柴油机氧化催化剂中使用分子筛材料,需要开发具有改进的耐硫性的改进的柴油机氧化催化剂。本发明的第一方面涉及一种氧化催化剂。在第一实施方案中,用于减少稀燃发动机的废气排放的氧化催化剂复合材料包含:具有长度、入口端和出口端的支承基底、在所述支承体上的氧化催化剂材料,所述氧化催化剂材料包含:包括第一耐火金属氧化物载体、稀土氧化物组分和钯(Pd)的第一氧化材料,第一氧化材料基本不含铂;包括第二耐火金属氧化物载体和10:1至1:10铂/钯比的铂(Pt)和钯(Pd)的第二氧化材料,第二氧化材料基本不含稀土氧化物;和包括第三耐火金属氧化物、铂(Pt)和任选钯(Pd)和用选自Cu、Fe、Co、Ni、Mn、V和Ag中一种或多种的金属助催化的分子筛的保护性覆层,所述保护性覆层基本不含稀土氧化物。在第二实施方案中,改进(modify)第一实施方案的氧化催化剂复合材料,其中第一氧化材料在所述支承基底上的底层中,第二氧化材料在所述底层上的中间层中,且所述保护性覆层在所述中间层上的上层中。在第三实施方案中,改进第一实施方案的氧化催化剂复合材料,其中第一氧化材料和第二氧化材料混合在所述支承基底上的共混底层中,且所述保护性覆层是在所述共混底层上的上层。在第四实施方案中,改进第一实施方案的氧化催化剂复合材料,其中第一氧化材料和第二氧化材料在所述支承基底上的分区底层中,且所述保护性覆层是在所述分区底层上的上层。在第五实施方案中,改进第四实施方案的氧化催化剂复合材料,其中第一氧化材料在入口端上且第二氧化材料在出口端上。在第六实施方案中,改进第四实施方案的氧化催化剂复合材料,其中第二氧化材料在入口端上且第一氧化材料在出口端上。在第七实施方案中,改进第一至第六实施方案任一项的氧化催化剂复合材料,其中第一、第二和第三耐火金属氧化物载体独立地包含氧化铝、氧化锆、氧化铝-氧化锆、氧化镧-氧化铝、氧化镧-氧化锆-氧化铝、氧化钡-氧化铝、氧化钡-氧化镧-氧化铝、氧化钡-氧化镧-氧化钕-氧化铝、氧化铝-氧化铬中一种或多种的氧化物。在第八实施方案中,改进第一至第七实施方案任一项的氧化催化剂复合材料,其中第一氧化材料包含大约1g/ft3至70g/ft3的量的钯且其中第二氧化材料包含大约5g/ft3至大约150g/ft3的量的钯和铂。在第九实施方案中,改进第一至第八实施方案任一项的氧化催化剂复合材料,其中所述稀土氧化物选自二氧化铈(Ce)、氧化镧(La)、氧化镨(Pr)、氧化钕(Nd)、氧化铕(Eu)、氧化钐(Sm)、氧化镱(Yb)以及他们的组合,和任选混在其中的稳定剂,所述稳定剂选自氧化锆(Zr)、氧化铌(Nb)、氧化钇(Y)、氧化铝(Al)以及它们的组合。在第十实施方案中,改进第一至第九实施方案任一项的氧化催化剂复合材料,其中基于第一氧化材料的重量计,Pd与稀土氧化物的比率在按重量计1至5的范围内。在第十一实施方案中,改进第一至第十实施方案任一项的氧化催化剂复合材料,其中第一氧化材料中的稀土氧化物组分以0.1g/in3至5g/in3的量存在。在第十二实施方案中,改进第一至第十一实施方案任一项的氧化催化剂复合材料,其中第一氧化材料中的稀土氧化物组分包含二氧化铈(Ce)。在第十三实施方案中,改进第十二实施方案的氧化催化剂复合材料,其中所述Ce被选自Si、Mn、Fe、Co、Ni、Cu、In、Sn、Ir、Pr以及它们的组合的元素掺杂。在第十四实施方案中,改进第一至第十三实施方案任一项的氧化催化剂复合材料,其中所述保护性覆层包含具有六、八、十或十二环结构的分子筛。在第十五实施方案中,改进第一至第十四实施方案任一项的氧化催化剂复合材料,其中所述分子筛选自TypeA、菱沸石、毛沸石、ZSM-5、ZSM-11、ZSM-23、ZSM-48、镁碱沸石、辉沸石、八面沸石、丝光沸石、TypeL、Omega、Beta、AlPO4、硼硅酸盐、MeAPO、MeAPSO和SAPO。在第十六实施方案中,改进第一至第十五实施方案任一项的氧化催化剂复合材料,其中第二氧化材料中的铂/钯比在5:1至1:5的范围内。在第十七实施方案中,改进第一至第十六实施方案任一项的氧化催化剂复合材料,其中第二氧化材料中的铂/钯比在2:1至1:1的范围内。在第十八实施方案中,改进第一至第十七实施方案任一项的氧化催化剂复合材料,其中所述支承基底选自流通型整料、壁流式过滤器、泡沫或网。本发明的第二方面涉及一种处理柴油发动机排气料流的方法。在第十九实施方案中,一种处理柴油发动机排气料流的方法包括使排气料流与第一至第十八实施方案任一项的氧化催化剂复合材料接触,和使所述排气料流经过下游SCR催化剂。在第二十实施方案中,改进第十九实施方案的方法,其中所述下游SCR催化剂布置在壁流式过滤器上。本发明的第三方面涉及一种用于处理稀燃发动机排气料流的系统。在第二十一实施方案中,一种用于处理包含烃、一氧化碳、氮氧化物、颗粒物和其它排气组分的稀燃发动机排气料流的系统包含:经排气歧管与稀燃发动机流体连通的排气管道;第一至第十八实施方案任一项的氧化催化剂复合材料;和位于所述氧化催化剂复合材料下游的催化滤烟器和SCR催化剂。在第二十二实施方案中,改进第二十一实施方案的系统,其中所述SCR催化剂作为洗涂层存在于所述催化滤烟器上。在第二十三实施方案中,改进第二十一和第二十二实施方案的系统,其进一步包含在所述SCR催化剂下游的流通型整料上的第二SCR催化剂。在第二十四实施方案中,改进第二十一实施方案的系统,其中所述SCR催化剂在所述氧化催化剂复合材料下游的流通型整料上,且所述催化滤烟器在所述SCR催化剂下游。在第二十五实施方案中,改进第二十一实施方案的系统,其中所述催化滤烟器在所述氧化催化剂复合材料下游且所述SCR催化剂在所述催化滤烟器下游的流通型整料上。在第二十六实施方案中,改进第二十四实施方案的系统,其中所述催化滤烟器包含第二SCR催化剂。在第二十七实施方案中,改进第二十一至第二十六实施方案任一项的系统,其中所述SCR催化剂包含具有双六环(d6r)单元的分子筛。在第二十八实施方案中,改进第二十一至第二十七实施方案任一项的系统,其中所述SCR催化剂选自CHA、AEI或AFX骨架型沸石。图1是可包含根据一个或多个实施方案的氧化催化剂复合材料的蜂窝型耐火支承元件的透视图;图2是相对于图1放大的局部截面图,其显示图1中所示的气流通道之一的放大视图;图3显示根据一个或多个实施方案的氧化催化剂复合材料的截面图;图4显示根据一个或多个实施方案的氧化催化剂复合材料的截面图;图5显示根据一个或多个实施方案的氧化催化剂复合材料的截面图;图6是根据一个或多个实施方案的发动机处理系统的示意图;图7是根据一个或多个实施方案的发动机处理系统的示意图;图8是根据一个或多个实施方案的发动机处理系统的示意图;且图9是根据实施例的氧化催化剂复合材料的CO起燃(light-off)的曲线图;图10是根据实施例的氧化催化剂复合材料的HC起燃(light-off)的曲线图;图11是根据实施例的氧化催化剂复合材料的NO2/NOx起燃(light-off)的曲线图;图12是根据实施例的氧化催化剂复合材料的SO2排放的曲线图;且图13是根据实施例的氧化催化剂复合材料的SO2排放的曲线图。在描述本发明的几个示例性实施方案之前,要理解的是,这些实施方案仅例示本发明的原理和应用。因此要理解的是,可以对示例性实施方案作出许多修改并且可以设计其它布置而不背离如所公开的本发明的精神和范围。现行和未来的法规需要具有极低CO起燃温度的柴油机氧化催化剂(DOC)。Pd/二氧化铈技术提供一种解决方案,但产生新的问题,即硫不耐受。过去已考虑几种方法,如与铝、镧等的耐硫氧化物结合使用更耐硫的二氧化铈材料。这些催化剂表现出一定程度的恢复,但从未恢复到硫化前活性。根据本发明的一个或多个实施方案,尽管所要求保护的发明不应受特定操作理论限制,但已经确定的是,预防优于补救。换言之,在一个或多个实施方案中,已经确定的是,首先防止硫毒化活性位点而非找到稍后从活性位点清除硫的方式会产生具有改进的耐硫性的催化剂。根据本发明的实施方案,因此,已经确定的是,将保护性覆层并入氧化催化剂复合材料中产生具有改进的耐硫性的柴油机氧化催化剂。无意受制于理论,但认为,该保护性覆层充当硫清除剂,其储存硫,然后在较低温度下释放硫以使该催化剂在脱硫后恢复硫化前COT50起燃活性。根据一个或多个实施方案,提供用于减少稀燃发动机的废气排放的氧化催化剂复合材料,所述催化剂复合材料包含:具有长度、入口端和出口端的支承基底、在所述支承体上的氧化催化剂材料,所述氧化催化剂材料包含:包括第一耐火金属氧化物载体、稀土氧化物组分和钯(Pd)的第一氧化材料,第一洗涂层基本不含铂;包括第二耐火金属氧化物载体和10:1至1:10铂/钯比的铂(Pt)和钯(Pd)的第二氧化材料,第二层基本不含稀土氧化物;和包括第三耐火金属氧化物、铂(Pt)和任选钯(Pd)和用选自Cu、Fe、Co、Ni、Mn、V、Ag中一种或多种的金属助催化的分子筛的保护性覆层,所述保护性覆层基本不含稀土氧化物。关于本公开中所用的术语,提供下列定义。本文所用的术语“催化剂复合材料”是指包括具有一个或多个含有催化组分,例如有效催化CO、HC和NO的氧化的铂族金属组分的洗涂层的支承基底,例如蜂窝基底的催化制品。本文所用的术语“催化剂”或“催化剂组合物”或“催化剂材料”是指促进反应的材料。例如,“氧化材料”促进与排气中一种或多种组分的氧化反应。本文所用的术语“洗涂层”具有其在本领域中的普通含义,即施加到足够多孔以允许处理的气体料流经过的支承基底材料(如蜂窝型支承元件)上的催化材料或其它材料的薄粘附涂层。如本领域中理解,洗涂层获自浆料形式的粒子分散体,将其施加到基底上,干燥并煅烧以提供多孔洗涂层。本文所用的“Pt”或“铂”、“Pd”或“钯”和对其它铂族金属如“Rh”或“铑”的提及是指各自的铂族金属化合物、络合物等,其在催化剂煅烧或使用时分解或以其它方式转化成催化活性形式,通常是金属或金属氧化物。本文所用的术语“耐火金属氧化物载体”和“载体”是指在其上承载附加化学化合物或元素的下方高表面积材料。载体粒子具有大于的孔隙和宽孔隙分布。如本文定义,这样的金属氧化物载体不包括分子筛,尤其是沸石。在特定实施方案中,可以使用高表面积耐火金属氧化物载体,例如氧化铝载体材料,也称作“γ氧化铝”或“活性氧化铝”,其通常表现出超过60平方米/克(“m2/g”),通常高达大约200平方米/克或更高的BET表面积。这样的活性氧化铝通常是氧化铝的γ和δ相的混合物,但也可能含有显著量的η、κ和θ氧化铝相。可以使用活性氧化铝以外的耐火金属氧化物作为给定催化剂中的至少一些催化组分的载体。例如,散装二氧化铈、氧化锆、α氧化铝、二氧化硅、二氧化钛、锰和其它材料已知用于此类用途。本发明的一个或多个实施方案包括包含活化化合物的耐火金属氧化物载体,所述活化化合物选自氧化铝、氧化锆、二氧化硅、二氧化钛、二氧化铈、二氧化硅-氧化铝、氧化锆-氧化铝、二氧化钛-氧化铝、氧化镧-氧化铝、氧化镧-氧化锆-氧化铝、氧化钡-氧化铝、氧化钡-氧化镧-氧化铝、氧化钡-氧化镧-氧化钕-氧化铝、氧化锆-二氧化硅、二氧化钛-二氧化硅或氧化锆-二氧化钛或其组合。尽管许多这些材料具有BET表面积明显低于活性氧化铝的缺点,但该缺点往往由所得催化剂的更高耐久性或性能增强弥补。本文所用的术语“BET表面积”具有其普通含义——是指通过N2吸附测定表面积的Brunauer,Emmett,Teller法。也可以使用BET型N2吸附或解吸实验测定孔径和孔体积。在一个或多个实施方案中,第一和第二氧化材料和保护性覆层分别包含第一、第二和第三耐火金属氧化物载体。第一、第二和第三耐火金属氧化物载体各自或任一种可包含活化和/或稳定化的化合物,其选自氧化铝、氧化锆、氧化铝-氧化锆、氧化镧-氧化铝、氧化镧-氧化锆-氧化铝、氧化钡-氧化铝、氧化钡-氧化镧-氧化铝、氧化钡-氧化镧-氧化钕-氧化铝、氧化铝-氧化铬以及它们的组合。第一、第二和第三耐火金属氧化物载体可以是在组成、粒度或其它性质方面相同或不同类型的载体。换言之,第一、第二和第三耐火金属氧化物载体可以是相同载体,或第一和第二可以相同,或第一和第三可以相同,和第二和第三载体可以相同,或第一、第二和第三载体可以不同。本文所用的术语“铂族金属”或“PGM”是指元素周期表中定义中一种或多种化学元素,包括铂(Pt)、钯(Pd)、铑(Rh)、锇(Os)、铱(Ir)和钌(Rh)以及它们的混合物。在一个或多个实施方案中,第一氧化材料包含钯。通常,对第一氧化材料的钯含量没有具体限制。在具体实施方案中,第一氧化材料中的Pd载量可以为大约1g/ft3至大约70g/ft3,包括大约5g/ft3至大约50g/ft3、大约5g/ft3至大约40g/ft3、大约5g/ft3至大约30g/ft3、大约10g/ft3至大约50g/ft3、大约10g/ft3至大约30g/ft3、大约10g/ft3至大约30g/ft3、大约15g/ft3至大约50g/ft3、大约15g/ft3至大约40g/ft3、大约15g/ft3至大约30g/ft3、大约20g/ft3至大约50g/ft3、大约20g/ft3至大约40g/ft3、和大约20g/ft3至大约30g/ft3。在一个或多个具体实施方案中,第一氧化材料中的Pd载量为大约30g/ft3。在一个或多个实施方案中,第一氧化材料包含钯并且基本不含铂。本文所用的术语“基本不含铂”是指铂未被有意添加到第一氧化材料中,并且第一氧化材料中通常存在少于大约1重量%的铂。但是,本领域技术人员会认识到,在负载/涂布过程中,痕量铂可能从一种洗涂层组分迁移到另一种,以致可能在第一氧化材料中存在痕量铂。在一个或多个实施方案中,第一氧化材料包含稀土氧化物。本文所用的术语“稀土氧化物”是指选自二氧化铈(Ce)、氧化镧(La)、氧化镨(Pr)、氧化钕(Nd)、氧化铕(Eu)、氧化钐(Sm)、氧化镱(Yb)以及它们的组合的至少一种稀土金属氧化物和任选混在其中的稳定剂,该稳定剂选自氧化锆(Zr)、氧化铌(Nb)、氧化钇(Y)、氧化铝(Al)以及它们的组合。在一个或多个实施方案中,稀土氧化物包含二氧化铈。通常,对第一氧化材料的稀土氧化物含量没有具体限制。在具体实施方案中,第一氧化材料中的稀土氧化物载量可以为大约0.1g/in3至大约5g/in3,包括大约0.1至大约1.5g/in3、大约0.5至大约1.5g/in3。在一个或多个具体实施方案中,第一氧化材料中的稀土氧化物载量为大约0.75g/in3。在一个或多个实施方案中,稀土氧化物可被选自Si、Mn、Fe、Co、Ni、Cu、In、Sn、Ir、Pr以及它们的组合的元素掺杂。在具体实施方案中,稀土氧化物是二氧化铈,且二氧化铈被选自Si、Mn、Fe、Co、Ni、Cu、In、Sn、Ir、Pr以及它们的组合的元素掺杂。在一个或多个实施方案中,第一氧化材料中Pd与稀土氧化物的比率在基于第一氧化材料的重量%计的大约1至大约5重量%的范围内,包括基于第一氧化材料的重量%计大约1.5至大约2.5重量%。无意受制于理论,但认为,一定的Pd/稀土氧化物(特别是Pd/Ce)比率提供最佳活性,同时避免稀土氧化物和/或钯的浪费。在一个或多个实施方案中,第一氧化材料包含氧化铝(或氧化镧-氧化铝)、二氧化铈和钯。本领域技术人员会认识到,在这样的实施方案中,二氧化铈以基于第一氧化材料的总重量的大约30重量%至大约95重量%的量存在,包括基于第一氧化材料的总重量的大约40重量%至大约70重量%。在一个具体实施方案中,第一氧化材料包含大约49重量%的量的二氧化铈、大约49重量%的量的氧化铝(或氧化镧-氧化铝)和大约3重量%的量的钯。根据一个或多个实施方案,第二氧化材料包含第二耐火金属氧化物载体和铂(Pt)和钯(Pd)。第二氧化材料中的铂/钯比可以在宽范围内变化。通常,对第二氧化材料的铂/钯重量比没有具体限制。在一个或多个实施方案中,第二氧化材料的铂/钯重量比可以在大约10:1至1:10的范围内,包括在5:1至1:5的范围内和在2:1至1:1的范围内。在一个或多个实施方案中,第二氧化材料的铂/钯比可以是10:1、9:1、8:1、7:1、6:1、5:1、4:1、3:1、2:1、1:1、1:2、1:3、1:4、1:5、1:6、1:7、1:8、1:9或1:10。在一个或多个实施方案中,第二氧化材料中的铂和钯的载量可以为大约5g/ft3至200g/ft3,包括大约5g/ft3至大约150g/ft3和大约5g/ft3至大约100g/ft3。通常,对第二氧化材料的钯含量没有具体限制。对第二氧化材料的铂含量也没有具体限制。在具体实施方案中,第二氧化材料中的Pt载量可以为大约8g/ft3至大约160g/ft3,且第二氧化材料中的Pd载量可以为大约10g/ft3至大约100g/ft3。在一个或多个实施方案中,保护性覆层包括第三耐火金属氧化物、铂(Pt)和任选钯(Pd),和分子筛。通常,对保护性覆层的铂含量没有具体限制。在一个或多个实施方案中,保护性覆层中的铂载量可以在大约10g/ft3至100g/ft3范围内。通常,对保护性覆层的钯含量没有具体限制。在具体实施方案中,保护性覆层中的Pd载量可以在大约0g/ft3至50g/ft3范围内,包括大约0g/ft3至大约20g/ft3。在一个或多个实施方案中,保护性覆层中的总PGM载量可以为大约10至大约120g/ft3。无意受制于理论,但认为,当存在铂(Pt)时,应该避免稀土氧化物,特别是二氧化铈的存在,以避免对铂的催化活性的有害影响。根据一个或多个实施方案,第二氧化材料和保护性覆层基本不含稀土氧化物。本文所用的术语“基本不含稀土氧化物”是指没有稀土氧化物被有意添加到第二氧化材料或保护性覆层中,并且在第二氧化材料和保护性覆层中通常存在少于大约0.1重量%的稀土氧化物。但是,本领域技术人员会认识到,在负载/涂布过程中,痕量稀土氧化物可能从一种洗涂层组分迁移到另一种,以致在第二氧化材料或保护性覆层中可存在痕量稀土氧化物。在一个或多个具体实施方案中,第二氧化材料和保护性覆层基本不含二氧化铈。本文所用的术语“基本不含二氧化铈”是指没有二氧化铈被有意添加到第二氧化材料或保护性覆层中,并且在第二氧化材料和保护性覆层中通常存在少于大约0.1重量%二氧化铈。但是,本领域技术人员会认识到,在负载/涂布过程中,痕量二氧化铈可能从一种洗涂层组分迁移到另一种,以致在第二氧化材料或保护性覆层中可存在痕量二氧化铈。根据一个或多个实施方案,保护性覆层包括分子筛,以吸收气态污染物,特别是硫,并在初始冷启动期间留住它们。无意受制于理论,但认为,包括用选自Cu、Fe、Co、Ni、Mn、V和Ag中一种或多种的金属助催化的分子筛的保护层带来耐硫的氧化催化剂复合材料。本文所用的术语“耐硫性”或“抗硫性”是指氧化催化剂将排气中所含的NO、CO和HC氧化的能力在硫氧化物(SOx)存在下没有显著的活性下降。特别重要的是,本发明的保护性覆层可在过滤器再生中可实现的温度(<650℃)下容易脱硫而不需要如传统NOx捕集器通常所需的富脱硫策略。无意受制于理论,但认为,包括耐火金属氧化物、铂(Pt)和任选钯(Pd)和用选自Cu、Fe、Co、Ni、Mn、V和Ag中一种或多种的金属助催化的分子筛的保护性覆层防止硫毒化氧化催化剂复合材料的Pd/二氧化铈活性位点。本文所用的术语“分子筛”是指骨架材料,如沸石和其它骨架材料(例如同晶取代材料),其可以以微粒形式与一种或多种助催化剂金属结合用作催化剂。分子筛是基于含有通常四面体型位点并具有基本均匀的孔分布的氧离子大三维网络的材料,平均孔径不大于孔径由环尺寸限定。本文所用的术语“沸石”是指包括硅和铝原子的分子筛的一个具体实例。根据一个或多个实施方案,要认识到,通过由其结构类型定义分子筛,意在包括该结构类型和具有与该分子筛材料相同的结构类型的任何和所有同型骨架材料,如SAPO、ALPO和MeAPO材料。在更具体的实施方案中,对铝硅酸盐沸石结构类型的提及是将该材料限制为不包括取代在骨架中的磷或其它金属的分子筛。但是,为清楚起见,本文所用的“铝硅酸盐沸石”不包括铝磷酸盐材料,如SAPO、ALPO和MeAPO材料,且更广义的术语“沸石”意在包括铝硅酸盐和铝磷酸盐。术语“铝磷酸盐”是指分子筛的另一具体实例,包括铝和磷酸根(phosphate)原子。铝磷酸盐是具有相当均匀的孔径的结晶材料。沸石是具有相当均匀的孔径的结晶材料,根据沸石的类型和包含在沸石晶格中的阳离子的类型和量,孔径为大约3至10埃。沸石通常包含2或更大的氧化硅/氧化铝(SAR)摩尔比。通常,分子筛,例如沸石,被定义为具有由共角TO4四面体构成的开放三维骨架结构的铝硅酸盐,其中T是Al或Si,或任选P。平衡阴离子骨架的电荷的阳离子与骨架氧松散缔合,并且剩余孔体积被水分子填充。非骨架阳离子通常可交换,并且水分子可除去。在一个或多个实施方案中,分子筛组分包含SiO4/AlO4四面体并通过共用的氧原子连接形成三维网络。在另一些实施方案中,分子筛组分包含SiO4/AlO4/PO4四面体。一个或多个实施方案的分子筛组分主要根据由(SiO4)/AlO4或SiO4/AlO4/PO4四面体的刚性网络形成的空隙的几何区分。就形成入口开口的原子而言,空隙的入口由6、8、10或12个环原子形成。在一个或多个实施方案中,分子筛组分包含不大于12,包括6、8、10和12的环尺寸。在一个或多个实施方案中,分子筛可基于用于识别结构的骨架拓扑。通常,可以使用任何结构类型的分子筛,如结构类型ABW、ACO、AEI、AEL、AEN、AET、AFG、AFI、AFN、AFO、AFR、AFS、AFT、AFX、AFY、AHT、ANA、APC、APD、AST、ASV、ATN、ATO、ATS、ATT、ATV、AWO、AWW、BCT、BEA、BEC、BIK、BOG、BPH、BRE、CAN、CAS、SCO、CFI、SGF、CGS、CHA、CHI、CLO、CON、CZP、DAC、DDR、DFO、DFT、DOH、DON、EAB、EDI、EMT、EON、EPI、ERI、ESV、ETR、EUO、FAU、FER、FRA、GIS、GIU、GME、GON、GOO、HEU、IFR、IHW、ISV、ITE、ITH、ITW、IWR、IWW、JBW、KFI、LAU、LEV、LIO、LIT、LOS、LOV、LTA、LTL、LTN、MAR、MAZ、MEI、MEL、MEP、MER、MFI、MFS、MON、MOR、MOZ、MSO、MTF、MTN、MTT、MTW、MWW、NAB、NAT、NES、NON、NPO、NSI、OBW、OFF、OSI、OSO、OWE、PAR、PAU、PHI、PON、RHO、RON、RRO、RSN、RTE、RTH、RUT、RWR、RWY、SAO、SAS、SAT、SAV、SBE、SBS、SBT、SFE、SFF、SFG、SFH、SFN、SFO、SGT、SOD、SOS、SSY、STF、STI、STT、TER、THO、TON、TSC、UEI、UFI、UOZ、USI、UTL、VET、VFI、VNI、VSV、WIE、WEN、YUG、ZON或其组合。在一个或多个实施方案中,分子筛组分可包括所有铝硅酸盐、硼硅酸盐、镓硅酸盐、MeAPSO和MeAPO组合物。在一个或多个实施方案中,分子筛可以是天然或合成沸石,如八面沸石、菱沸石、斜发沸石、丝光沸石、硅质岩、沸石X、沸石Y、超稳沸石Y、ZSM-5、ZSM-12、SSZ-3、SAPO5、菱钾铝矿或β沸石。在一个或多个具体实施方案中,分子筛选自TypeA、菱沸石、毛沸石、ZSM-5、ZSM-11、ZSM-23、ZSM-48、镁碱沸石、辉沸石、八面沸石、丝光沸石、TypeL、Omega、beta、AlPO4、硼硅酸盐、MeAPO、MeAPSO和SAPO。在一个或多个具体实施方案中,分子筛具有BEA结构类型。分子筛的氧化硅/氧化铝比可以在宽范围内变化。在一个或多个实施方案中,分子筛具有2至300,包括5至250;5至200;5至100;和5至50范围内的硅铝摩尔比(SAR)。在一个或多个具体实施方案中,分子筛具有10至200、10至100、10至75、10至60、和10至50范围内;15至100、15至75、15至60、和15至50范围内;20至100、20至75、20至60、和20至50范围内的硅铝摩尔比(SAR)。在一个或多个实施方案中,保护性覆层包含0.1至2g/in3,包括0.25至1.5g/in3、0.25至1.0g/in3和0.25至0.8g/in3总量的分子筛。在一个具体实施方案中,保护性覆层包含大约0.7g/in3总量的分子筛。一个或多个实施方案的保护性覆层的分子筛随后与一种或多种助催化剂金属,尤其例如铁(Fe)、铜(Cu)、钴(Co)、镍(Ni)、锰(Mn)、钒(V)和银(Ag)离子交换。本文所用的术语“助催化的”是指有意添加到分子筛材料中的组分,而非该分子筛中固有的杂质。因此,有意添加助催化剂从而与没有有意添加助催化剂的催化剂相比提高催化剂的活性。为了促进从排气中吸收硫,在一个或多个实施方案中,将合适的金属交换到氧化催化剂复合材料的保护性覆层的分子筛中。根据一个或多个实施方案,保护性覆层包含用选自Cu、Fe、Co、Ni、Mn、V、Ag以及它们的组合的金属助催化的分子筛。在具体实施方案中,分子筛用Cu、Fe以及它们的组合助催化。该分子筛的助催化剂金属含量在一个或多个实施方案中为至少大约0.1重量%,按氧化物计算,在无挥发物基础上报道。在具体实施方案中,助催化剂金属包含Fe,并且按Fe2O3计算的Fe含量为最多大约10重量%,包括大约9、大约8、大约7、大约6、大约5、大约4、大约3、大约2、大约1、大约0.5和大约0.1重量%,在每种情况下基于保护性覆层的总重量计,在无挥发物的氧化物基础上报道。在具体实施方案中,按Fe2O3计算的Fe含量为大约1至大约5重量%。在一个非常具体的实施方案中,按Fe2O3计算的Fe含量为保护性覆层的重量的大约1.5重量%。根据本发明的氧化催化剂复合材料的各组分可以由含有如上所述的相应载体材料的洗涂层形成。在洗涂层中还可包括其它添加剂,如粘合剂和稳定剂。如美国专利No.4,727,052中所公开,可以将多孔载体材料(如活性氧化铝)热稳定化以防止不合意的氧化铝在高温下从γ至α的相变。稳定剂可选自碱土金属组分,其选自镁、钡、钙和锶。当存在时,稳定剂材料可以在涂层中以大约0.01g/in3至大约0.15g/in3的量加入。通常,对氧化催化剂中的各个组分(第一氧化材料、第二氧化材料、保护性覆层)的洗涂层载量没有具体限制。在一个或多个实施方案中,第一氧化材料、第二氧化材料和保护性覆层中一种或多种可具有0.1g/in3至6.0g/in3范围内,包括大约0.1g/in3至大约4.5g/in3范围内的洗涂层载量。在一个或多个实施方案中,然后将包括保护性覆层和第一和第二氧化材料的氧化催化剂施加到陶瓷或金属流通型整料或壁流式过滤器上。本文所用的术语“层”用于指示柴油机氧化催化剂复合材料在支承基底上的位置。要认识到,洗涂层组分通常没有特定成层顺序。在一个或多个实施方案中,第一氧化材料在支承基底上的底层中,第二氧化材料在底层上的中间层中,且保护性覆层在中间层上(或上方)的上层中。在一个或多个实施方案中,第一氧化材料和第二氧化材料混合在支承基底上的共混底层中,且保护性覆层是该共混底层上(或上方)的上层。本领域技术人员会认识到,组分的混合可以是均匀的,但在一些情况下可以在该涂层中选择单独组分的局部浓缩以减轻负面相互作用,例如将Pt和稀土氧化物(例如二氧化铈)相互作用减至最低可能是有益的。在一个或多个实施方案中,第一氧化材料和第二氧化材料以分区关系在支承基底上的分区底层中,且保护性覆层是该分区底层上(或上方)的上层。在这样的实施方案中,第一氧化材料可以在入口端且第二氧化材料可位于出口端。在另一些实施方案中,第二氧化材料可以在入口端且第一氧化材料可位于出口端。本领域技术人员会认识到,上游/入口区和下游/出口区可以至少部分搭接。在一个或多个实施方案中,上游/入口区至少部分搭接在下游/出口区上。在另一些实施方案中,下游/出口区至少部分搭接在上游/入口区上。在一个或多个实施方案中,上游/入口区和下游/出口区可以直接相互邻接。在再一些实施方案中,在上游/入口区和下游/出口区之间可存在间隙。本文所用的术语“上游”和“下游”是指根据发动机排气料流从发动机到排气管的流动的相对方向,发动机在上游位置且排气管和任何污染减轻制品如过滤器和催化剂在发动机的下游。本文所用的术语“料流”广义地指可能含有固体或液体颗粒物的流动气体的任何组合。术语“气态料流”或“排气料流”是指气态成分的料流,如稀燃发动机的排气,其可能含有夹带的非气态组分,如液滴、固体微粒等。稀燃发动机的排气料流通常进一步包含燃烧产物、不完全燃烧的产物、氮氧化物、可燃和/或碳质颗粒物(烟炱)和未反应的氧气和氮气。根据一个或多个实施方案,氧化催化剂复合材料可进一步包含位于支承基底和底层之间的内涂层。在一个或多个实施方案中,内涂层包含氧化铝,尤其是γ-氧化铝。在存在该内涂层的实施方案中,在支承基底上涂布该内涂层,然后可以在该内涂层上(顶部)涂布底层。在一个或多个实施方案中,内涂层可包含一种或多种铂族金属和/或沸石。支承基底本文所用的术语“支承体”和“基底”是指耐火金属氧化物载体被置于其上(通常以含有许多其上带有催化物类的载体的洗涂层的形式)的整料。根据一个或多个实施方案,基底可以是常用于制备DOC催化剂的任何材料并通常包含泡沫、金属或陶瓷蜂窝结构。可以使用任何合适的基底,如具有许多从基底入口至出口面贯穿其中的细平行气流通道以使通道对流过其中的流体开放的类型的整料基底。从它们的流体入口到它们的流体出口基本为直线路径的通道由壁划定,催化材料作为“洗涂层”涂布在壁中,因此流过通道的气体接触催化材料。通过制备在液体介质中含有指定固含量(例如30-50重量%)的载体的浆料,然后将其涂布到支承基底上并干燥以提供洗涂层而形成洗涂层。整料基底的流道是薄壁通道,其可具有任何合适的横截面形状和尺寸,如梯形、矩形、正方形、正弦曲线、六角形、椭圆形、圆形等。此类结构可含有大约60至大约600或更多个气体入口(即“孔隙”)/平方英寸横截面。陶瓷基底可以由任何合适的耐火材料,例如堇青石、堇青石-α氧化铝、氮化硅、碳化硅、钛酸铝、锆莫来石、锂辉石、氧化铝-二氧化硅氧化镁、硅酸锆、硅线石、硅酸镁、氧化锆、透锂长石、α-氧化铝、铝硅酸盐等制成。可用于根据一个或多个实施方案的氧化催化剂复合材料的基底也可以是金属性质的并可以由一种或多种金属或金属合金构成。金属基底可以以各种形状如波纹片或整料形式使用。合适的金属载体包括耐热金属和金属合金,如钛和不锈钢,以及以铁为基本或主要组分的其它合金。催化剂复合材料的制备根据一个或多个实施方案的氧化催化剂复合材料可以在单层或在多层中形成,包括至少两个层和至少三个层。在一些情况下,可以合适地制备一种催化材料浆料并使用该浆料在基底上形成多个层。氧化催化剂复合材料可通过已知方法制备,例如初湿含浸。下面阐述代表性方法。氧化催化剂复合材料可以在整料基底上成层制备。对于特定洗涂层的第一层,将高表面积耐火金属氧化物如γ氧化铝的细碎粒子在适当的赋形剂,例如水中制浆。然后将基底一次或多次浸渍在此类浆料中,或可以在基底上涂布该浆料,以在基底上沉积所需载量的金属氧化物。为了并入如铂族金属(例如钯、铂、铑和/或组合)和稳定剂和/或助催化剂之类的组分,可以在基底涂布之前作为水溶性或水分散性化合物或络合物的混合物在浆料中并入这些组分。或者,可以在将该浆料施加到整料基底上之后以水分散性溶液的形式加入铂族金属、稳定剂和助催化剂。此后,该涂布基底通过例如在400-600℃下加热大约10分钟至大约4小时而煅烧。当需要铂和/或钯时,铂和钯组分以化合物或络合物的形式使用以实现组分在耐火金属氧化物载体(例如活性氧化铝)上的分散。本文所用的术语“铂组分”和“钯组分”是指在其煅烧或使用时分解或以其它方式转化成催化活性形式(通常是金属或金属氧化物形式)的任何化合物、络合物等。通常,使用该铂族金属的可溶化合物或络合物的水溶液。合适的化合物的非限制性实例包括硝酸钯、四氨合硝酸钯、氯化铂、四氨合乙酸铂和硝酸铂。在煅烧步骤的过程中或至少在该复合材料的使用的初始阶段的过程中,此类化合物转化成金属或其化合物的催化活性形式。制备分层催化剂复合材料的任何层的合适的方法是制备所需铂族金属化合物(例如铂化合物和/或钯化合物)的溶液和至少一种载体的混合物,所述载体例如为细碎的高表面积耐火金属氧化物载体,例如γ氧化铝(其足够干燥以吸收基本所有溶液以形成湿固体,其随后与水合并以形成可涂布浆料)。在一个或多个实施方案中,浆料是酸性的,具有例如大约2至小于大约7的pH。可以通过将足量的无机酸或有机酸添加到该浆料中降低该浆料的pH。当考虑酸和原材料的相容性时,可以使用无机酸和有机酸的组合。无机酸包括,但不限于,硝酸。有机酸包括,但不限于,乙酸、丙酸、草酸、丙二酸、琥珀酸、谷氨酸、己二酸、马来酸、富马酸、邻苯二甲酸、酒石酸、柠檬酸等。此后,如果需要,可以将水溶性或水分散性化合物和/或稳定剂,例如乙酸钡,和助催化剂,例如硝酸镧添加到该浆料中。在一个或多个实施方案中,粉碎浆料以使基本所有固体具有小于18微米的粒度。粉碎可以在球磨机或其它类似设备中实现,且该浆料的固含量可以为例如大约20-60重量%或30-40重量%。可以以与如对在基底上沉积第一层所述相同的方式在第一层上制备和沉积另外的层,即第二层。参照图1更容易理解根据一个或多个实施方案的氧化催化剂复合材料。图1显示根据一个或多个实施方案的基底2。参照图1,基底2是具有圆柱外表面4、上游端面6和与端面6基本相同的下游端面8的圆柱形。基底2具有在其中形成的多个细平行气流通道10。如图2中看出,气流通道10由壁12形成并从上游端面6到下游端面8贯穿基底2,气流通道10通畅以允许流体,例如气体料流经其气流通道10纵向流过基底2。如图2中更容易看出的那样,壁12的尺寸和配置使得气流通道10具有基本规则的多边形,在所示实施方案中为基本正方形,但根据美国专利No.4,335,023具有圆角。洗涂层14附着或涂布到基底元件的壁12上。如图2中所示,在洗涂层14上涂布另一洗涂层16。在一个或多个实施方案中,可以在第一洗涂层下方将第三洗涂层(未显示)施加到基底上。这种第三洗涂层被视为内涂层并且如本文所用,“内涂层”是指接触基底的洗涂层。本领域技术人员会认识到,根据一个或多个实施方案,洗涂层14可包含第一氧化材料、第二氧化材料、保护性覆层以及它们的组合。根据一个或多个实施方案,另外的洗涂层16可包含第一氧化材料、第二氧化材料、保护性覆层或其组合。在一个或多个实施方案中,可以在下方基底上施加第三洗涂层(未显示)并可根据一个或多个实施方案包含第一氧化材料、第二氧化材料、保护性覆层或其组合。如图1和2中所示,基底2包括由气流通道10提供的空隙空间,且这些气流通道10的横截面积和划定通道的壁12的厚度随基底元件的类型而变。类似地,施加到此类基底上的洗涂层的重量视情况而变。因此,在描述洗涂层或催化金属组分或该组合物的其它组分的量时,使用组分重量/单位体积催化剂基底的单位是方便的。因此,在本文中使用单位克/立方英寸(“g/in3”)和克/立方英尺(“g/ft3”)表示每体积基底元件(包括基底元件的空隙空间的体积)的组分重量。参照图3-5更容易理解包括第一氧化材料、第二氧化材料和保护性覆层的根据一个或多个实施方案的氧化催化剂复合材料。图3显示用于减少来自柴油发动机的废气排放物的分层氧化催化剂复合材料20的一个实施方案。在一个或多个实施方案中,基底22通常包含蜂窝基底的许多通道24,为清楚起见在横截面中仅显示一个通道。基底22具有入口或上游端26和出口或下游端28,并含有三个分开的涂布洗涂层。在一个或多个实施方案中,第一氧化材料是在基底22上的底层30;一个或多个实施方案的第二氧化材料是在底层30上的中间层32,且保护性覆层是在中间层32上的上层34。根据一个或多个实施方案,氧化催化剂复合材料可进一步包含位于基底22和底层30之间的内涂层(未显示)。在一个或多个实施方案中,内涂层包含氧化铝,尤其是γ-氧化铝。在存在内涂层的实施方案中,在基底22上涂布内涂层(未显示),然后第一氧化材料在涂布在内涂层(未显示)上(顶部)的底层30中。图4显示用于减少来自柴油发动机的废气排放物的分层氧化催化剂复合材料40的一个实施方案。在一个或多个实施方案中,基底42通常包含蜂窝基底的许多通道44,为清楚起见在横截面中仅显示一个通道。基底42具有入口或上游端46和出口或下游端48并含有两个分开的涂布洗涂层。在一个或多个实施方案中,混合第一氧化材料和第二氧化材料以在基底42上形成共混底层50,且保护性覆层是在共混底层50上的上层52。根据一个或多个实施方案,氧化催化剂复合材料可进一步包含位于基底42和底层50之间的内涂层(未显示)。在一个或多个实施方案中,内涂层包含氧化铝,尤其是γ-氧化铝。在存在内涂层的实施方案中,在基底42上涂布该内涂层(未显示),然后混合第一氧化材料和第二氧化材料以形成涂布在内涂层(未显示)上(顶部)的共混底层50,且保护性覆层是在共混底层50上的上层52。在一个或多个实施方案中,内涂层(未显示)可包含一种或多种铂族金属和/或沸石。图5显示具有包括上游区70和下游区72的轴向分区底层(它们可统称为分区底层(70/72))的分层氧化催化剂复合材料60的一个示例性实施方案。参照图5,在一个或多个实施方案中,基底62通常包含蜂窝基底的许多通道64,为清楚起见在横截面中仅显示一个通道。基底62具有入口端66和在入口端66下游的出口端68并含有两个分开的涂布洗涂层。基底62具有轴向长度L。在一个或多个实施方案中,第一和第二氧化材料以分区关系作为分区底层(70/72)涂布在基底62上。且保护性覆层作为上层或顶层74涂布在分区底层(70/72)上。上层或顶层74在分区底层(70/72)顶部(或上方)从基底62的入口端66延伸经过基底62的轴向长度L至出口端68。在一个或多个实施方案中,第一氧化材料在入口或上游端,且第二氧化材料在出口或下游端。第一氧化材料区70从基底62的入口端66延伸小于基底62的整个轴向长度L。第一氧化材料区70的长度在图5中标作第一区域70a。第二氧化材料区72从基底62的出口端68延伸小于基底62的整个轴向长度L。第二氧化材料区72的长度在图5中标作第二区域72a。根据一个或多个实施方案,氧化催化剂复合材料仍可进一步包含位于基底62和第一氧化材料区70和第二氧化材料区72之间的内涂层(未显示)。在存在内涂层的实施方案中,在基底62上涂布该内涂层,然后第一和第二氧化材料以分区关系涂布在该内涂层上(顶部),且保护性覆层作为上层或顶层74涂布在该分区底层上。可以反转第一氧化材料区70和第二氧化材料区72的顺序以使第二氧化材料区72在第一氧化材料区70上游(未显示)。本领域技术人员会认识到,上游区和下游区可以至少部分搭接(未图示)。在一个或多个实施方案中,上游区至少部分搭接下游区。在另一些实施方案中,下游区至少部分搭接上游区。在一个或多个实施方案中,所述至少部分搭接为大约0.1%至大约50%。在进一步实施方案中,上游区和下游区可以直接相互邻接。在再一些实施方案中,在上游区和下游区之间可存在间隙。排放处理系统一个或多个实施方案的氧化催化剂复合材料可用在包含一个或多个用于处理柴油机废气排放的其他部件的集成排放处理系统中。因此,本发明的另一方面的实施方案涉及用于处理来自柴油发动机的气态排出料流的系统。排气料流可包含烃、一氧化碳、氮氧化物、颗粒物和其它排气组分,如硫。在一个或多个实施方案中,排气处理系统包含经排气歧管与柴油发动机流体连通的排气管道;一个或多个实施方案的氧化催化剂复合材料;和与该氧化催化剂复合材料流体连通的下列一项或多项:位于一个或多个实施方案的氧化催化剂复合材料下游的催化滤烟器(CSF)和选择性催化还原(SCR)催化剂/制品。在一个或多个具体实施方案中,排气处理系统包含经排气歧管与柴油发动机流体连通的排气管道;一个或多个实施方案的氧化催化剂复合材料;和与该氧化催化剂复合材料流体连通的直接涂布到过滤器上(在过滤器上的SCR)并位于该氧化催化剂复合材料下游的选择性催化还原(SCR)催化剂/制品。额外的流通型SCR催化剂可任选位于该过滤器上的SCR下游。在另一些实施方案中,排气处理系统包含经排气歧管与柴油发动机流体连通的排气管道;一个或多个实施方案的氧化催化剂复合材料;和与该氧化催化剂复合材料流体连通的涂布在一个或多个实施方案的氧化催化剂复合材料下游的流通型整料上的选择性催化还原(SCR)催化剂/制品,和在SCR催化剂/制品下游的催化滤烟器。在再一些实施方案中,排气处理系统包含经排气歧管与柴油发动机流体连通的排气管道;一个或多个实施方案的氧化催化剂复合材料;和与该氧化催化剂复合材料流体连通的在一个或多个实施方案的氧化催化剂复合材料下游的催化滤烟器,和涂布在催化滤烟器下游的流通型整料上的选择性催化还原(SCR)催化剂/制品。在一个或多个实施方案中,催化滤烟器包含第二SCR催化剂/制品。除通过使用根据一个或多个实施方案的氧化催化剂复合材料处理废气排放外,可以使用滤烟器除去颗粒物。通常,滤烟器位于氧化催化剂复合材料下游。在一个或多个实施方案中,滤烟器是催化滤烟器(CSF)。CSF可包含被含有一种或多种用于烧除捕集的烟炱和/或氧化排气料流排放物的催化剂的洗涂层涂布的基底。一般而言,该烟炱燃烧催化剂可以是用于烟炱燃烧的任何已知催化剂。例如,CSF可以用一种或多种高表面积耐火氧化物(例如氧化铝或二氧化铈-氧化锆)涂布以用于未燃烃和在一定程度上颗粒物的燃烧。烟炱燃烧催化剂可以是包含一种或多种铂族金属(PGM)催化剂(铂、钯和/或铑)的氧化催化剂。参照图6-8更容易理解示例性排放处理系统,它们描绘根据本发明的一个或多个实施方案的排放处理系统的示意图。图6显示排放处理系统80的一个示例性实施方案,其包含经排气歧管与柴油发动机81流体连通的排气管道82;和根据一个或多个实施方案的柴油机氧化催化剂复合材料83。在柴油机氧化催化剂复合材料83中,未燃的气态和挥发性烃(即VOF)和一氧化碳在很大程度上燃烧形成二氧化碳和水。排气料流接着经排气管线85送往下游选择性催化还原(SCR)催化剂86。SCR催化剂86紧邻位于氧化催化剂复合材料83下游,在氧化催化剂和SCR催化剂之间没有中间催化剂材料。将氨前体(例如脲水溶液)经管线84注入排气管线85。添加了氨的排气料流经排气管线85送往用于处理和/或转化NOx的SCR催化剂86。在一个具体实施方案中,任选催化滤烟器(CSF)87可位于SCR催化剂下游,并且排气料流可经任选排气管道88送往CSF87。一般而言,可以使用任何已知的过滤器基底,包括例如蜂窝壁流式过滤器、缠绕或填充纤维过滤器、开孔泡沫、烧结金属过滤器、网等,壁流式过滤器特别合适。可用于负载CSF组合物的壁流式基底具有沿基底的纵轴延伸的多个细的基本平行的气流通道。通常,各通道在基底主体的一端封闭,相邻通道在相反端面封闭。此类整料支承体可含有多达大约700个或更多流道(或“孔隙”)/平方英寸横截面,尽管可以使用远远更少的量。例如,支承体可具有大约7至600,更通常大约100至400个孔隙/平方英寸(“cpsi”)。孔隙可具有矩形、正方形、圆形、椭圆形、三角形、六边形或其它多边形的横截面。壁流式基底通常具有0.002至0.02英寸的壁厚度。典型的壁流式过滤器基底由陶瓷类材料,如堇青石、-氧化铝、碳化硅、氮化硅、钛酸铝、氧化锆、莫来石、锂辉石、氧化铝-二氧化硅-氧化镁或硅酸锆、或多孔耐火金属构成。过滤器基底也可以由陶瓷或金属纤维复合材料形成。在另一些实施方案中,参照图7更容易理解示例性排放处理系统,其描绘排放处理系统90的示意图。参照图7,含有气态污染物(例如未燃烃、一氧化碳和NOx)和颗粒物的排气料流经排气管线92从稀燃发动机91,如柴油机传送至柴油机氧化催化剂(DOC)93,其为根据本发明的一个或多个实施方案的氧化催化剂复合材料的形式。在DOC93中,未燃的气态和挥发性烃(即VOF)和一氧化碳在很大程度上燃烧形成二氧化碳和水。排气料流接着经排气管线94送往催化滤烟器(CSF)95,其捕集排气料流内存在的颗粒物。任选将CSF95催化以被动再生。在经CSF95除去颗粒物后,该排气料流经排气管线96传送。将氨前体(例如脲水溶液)经管线97注入排气管线96。添加了氨的排气料流经排气管线96送往用于处理和/或转化NOx的下游选择性催化还原(SCR)部件98。在一个或多个实施方案中,排气料流可经任选排气管道99送往位于SCR催化剂98下游的任选氨氧化催化剂(AMOx)100以除去任何从该系统中逸出的氨。本文所用的术语“氨破坏催化剂”或“氨氧化催化剂(AMOx)”是指促进NH3的氧化的催化剂。在具体实施方案中,AMOx催化剂可包含铂族金属,如铂、钯、铑或它们的组合。这样的AMOx催化剂可用于包括SCR催化剂的排气处理系统。如共同转让的美国专利No.5,516,497(其整个内容经此引用并入本文)中论述,可以使含有氧气、氮氧化物和氨的气态料流顺序经过第一和第二催化剂,第一催化剂促进氮氧化物的还原,第二催化剂促进过量氨的氧化或其它分解。如美国专利No.5,516,497中所述,第一催化剂可以是包含沸石的SCR催化剂,第二催化剂可以是包含沸石的AMOx催化剂。AMOx和/或SCR催化剂组合物可以涂布在流通式或壁流式过滤器上。如果使用壁流式基底,所得系统能够与气态污染物一起除去颗粒物。壁流式基底可以由本领域中公知的材料,如堇青石、钛酸铝或碳化硅制成。要理解的是,催化组合物在壁流式基底上的载量取决于基底性质,如孔隙率和壁厚度,并通常低于在流通型基底上的载量。另一示例性排放处理系统显示在图8中,其描绘排放处理系统101的示意图。参照图8,含有气态污染物(例如未燃烃、一氧化碳和NOx)和颗粒物的排气料流经排气管线104从稀燃发动机102,如柴油发动机传送至柴油机氧化催化剂(DOC)106,其为根据本发明的实施方案的氧化催化剂复合材料的形式。在DOC106中,未燃的气态和挥发性烃(即VOF)和一氧化碳在很大程度上燃烧形成二氧化碳和水。排气料流接着经排气管线108传送。将氨前体(例如脲水溶液)经管线110注入排气管线108。添加了氨的排气料流经排气管线108送往负载在催化滤烟器内的选择性催化还原组分(在过滤器上的SCR)112,以捕集排气料流内存在的颗粒物并处理和/或转化NOx。任选地,该排气料流可经管线114送往下游选择性催化还原(SCR)催化剂元件116以进一步处理和/或转化NOx。在一个或多个实施方案中,排气料流可经任选排气管道118送往位于SCR催化剂元件116下游的任选氨氧化催化剂(AMOx)120以除去任何从该系统中逸出的氨。在这些实施方案中,合适的SCR部件位于一个或多个实施方案的氧化催化剂复合材料下游。适用于该排放处理系统的SCR催化剂部件能在低于600℃的温度下有效催化NOx组分的还原,以致甚至在通常与较低排气温度相关的低负荷条件下也能处理足够的NOx水平。在一个实施方案中,根据添加到系统中的还原剂的量,SCR催化剂制品能将至少50%的NOx组分转化成N2。组合物的另一合意属性在于,其具有选择性催化任何过量NH3氧化成N2和H2O的能力,以使NH3不排放到大气中。排放处理系统中所用的可用的SCR催化剂组合物还应该对高于650℃的温度具有耐热性。在上游催化滤烟器的再生过程中可能遇到这样的高温。例如在美国专利Nos.4,961,917('917专利)和5,516,497(两者都全文经此引用并入本文)中描述了合适的SCR催化剂组合物。'917专利中公开的组合物包括基于助催化剂+沸石总重量的大约0.1至30重量%,尤其是大约1至5重量%的量存在于沸石中的铁和铜助催化剂之一或两者。除它们催化NOx被NH3还原成N2的能力外,所公开的组合物还可促进过量NH3被O2氧化,尤其是对具有较高助催化剂浓度的那些组合物而言。可根据本发明的一个或多个实施方案使用的其它具体SCR组合物包括8-环小孔分子筛。本文所用的术语“小孔”是指小于大约5埃,例如大约~3.8埃的孔开口。术语“8环”沸石是指具有8环孔开口和双六环次级结构单元并具有通过4环结构单元连接双六环结构单元而得的笼状结构的沸石。沸石由次级结构单元(SBU)和复合结构单元(CBU)构成,并且表现为许多不同的骨架结构。次级结构单元含有最多16个四面体原子并且是非手性的。复合结构单元不需要是非手性的,并且可能不是必须用于构造整个骨架。例如,一类沸石在其骨架结构中具有单4环(s4r)复合结构单元。在该4环中,“4”是指四面体硅和铝原子的位置,并且氧原子位于四面体原子之间。其它复合结构单元包括例如单6环(s6r)单元、双4环(d4r)单元和双6环(d6r)单元。d4r单元通过连接两个s4r单元产生。d6r单元通过连接两个s6r单元产生。在d6r单元中,存在12个四面体原子。具有d6r次级结构单元的沸石骨架类型包括AEI、AFT、AFX、CHA、EAB、EMT、ERI、FAU、GME、JSR、KFI、LEV、LTL、LTN、MOZ、MSO、MWW、OFF、SAS、SAT、SAV、SBS、SBT、SFW、SSF、SZR、TSC和WEN。在一个或多个实施方案中,SCR催化剂包含具有双六环(d6r)单元的分子筛。在一个具体实施方案中,SCR催化剂包含CHA、AEI或AFX骨架型沸石。在一个非常具体的实施方案中,SCR催化剂包含CHA骨架型沸石。SCR催化剂可含有助催化剂金属,例如铜、铁、钴、镍、镧、铈、锰、钒、银或其组合。更具体地,SCR催化剂可含有选自铜、铁或其组合的助催化剂金属。在一个或多个实施方案中,示例性CHA骨架型沸石具有大于大约15的氧化硅/氧化铝比(SAR)和超过大约0.2重量%的铜含量。在一个更具体的实施方案中,氧化硅/氧化铝摩尔比为大约15至大约256,且铜含量为大约0.2重量%至大约5重量%。用于SCR的其它可用的组合物包括具有CHA骨架结构的非沸石分子筛。例如,可以根据一个或多个实施方案使用硅铝磷酸盐,如SAPO-34、SAPO-44和SAPO-18。其它可用的SCR催化剂可包括包含V2O5、WO3和TiO2中一种或多种的混合氧化物。处理方法本发明的另一方面涉及处理包含一氧化碳、烃、NOx和颗粒物的柴油机排气料流的方法。在一个或多个实施方案中,该方法包括使排气料流与一个或多个实施方案的氧化催化剂复合材料接触。现在参照下列实施例描述本发明的实施方案。在描述本发明的几个示例性实施方案之前,要理解的是,本发明不限于下列描述中阐述的构造或工艺步骤的细节。本发明能有其它实施方案并且能以各种方式实施或进行。实施例对比例A:134.5g/ft34/1=Pt/Pd,使用氧化铝的技术(无二氧化铈)底层:用硝酸钯的水溶液浸渍1.60g/in3的高孔隙率、二氧化硅稳定化(5重量%)氧化铝,以产生27g/ft3的最终干Pd含量。将所得混合物充分分散在水中。使用含有Pt前体的水溶液将该金属浸渍到含Pd的氧化铝浆料上,以产生67.5g/ft3的最终干Pt含量和2.5/1的Pt/Pd比。在初始pH调节(用硝酸,然后酒石酸)至4.1后,将该浆料研磨至16μm的粒度d90,最终pH调节至4.1,随后涂布到整料上,在空气中在140℃下干燥。顶层:0.60g/in3的高度多孔二氧化硅稳定化(5重量%)氧化铝,在其上浸渍铂的水溶液,以产生37.8g/ft3的最终干Pt含量。将所得混合物充分分散在水中。在初始pH调节(用硝酸和/或酒石酸)至4.1后,将该浆料研磨至15μm的粒度d90。将预研磨的含Pt的浆料与0.5g/in3沸石(BEA型,高SAR)混合。在添加水下充分混合后,将最终pH调节至4.0,总固含量为38%。随后将该浆料涂布到第一层上,在140℃下干燥并在空气中在590℃下煅烧。对比例B:130g/ft32/1=Pt/Pd,使用二氧化铈的技术底层:将硝酸钯溶液逐滴添加到已含有50重量%二氧化铈的1.0g/in3高孔隙率γ-氧化铝(Ce-Al50-50)中。这一洗涂层中的总二氧化铈含量因此为0.5g/in3。所得料(frit)含有在二氧化铈上的3.8重量%Pd。将该混合物分散在水和酸(例如乙酸)中,用硝酸将pH调节至5.3,然后将0.1g/in3的另一高孔隙率氧化铝添加到该浆料中并充分混合,接着二次pH调节至4.7,随后研磨至20μm的粒度d90。最终浆料的总Pd含量为33.34g/ft3,固含量为36%。涂布到整料上,接着在空气中在140℃下干燥。中间层:使用硝酸钯的水溶液浸渍0.85g/in3的用5%二氧化硅稳定化的高孔隙率氧化铝,以产生10.83g/ft3的最终干Pd含量。将所得混合物分散在水中。使用含有氨合物稳定化的铂的水溶液作为Pt前体,将其添加到含Pd的浆料中,以产生20.83g/ft3的最终干Pt含量和1.9/1的Pt/Pd比。在pH调节(用硝酸,然后酒石酸)至4.1后,将该浆料研磨至16μm的粒度d90,随后涂布到底层上,接着在空气中在140℃下干燥。顶层:1.30g/in3的高度多孔氧化铝(含5重量%锰),在其上浸渍铂的水溶液,以产生65g/ft3的最终干Pt含量。将所得混合物分散在水中。在pH调节(使用硝酸和/或酒石酸)至4.3后,将该浆料研磨至20μm的粒度d90。将预研磨的含Pt的浆料与0.5g/in3沸石(BEA型)混合。在添加水下充分混合后,最终分散体研磨产生17μm的d90。将pH再调节至4.3,总固含量为38%。随后将该浆料涂布到中间层上,在140℃下干燥并在空气中在590℃下煅烧。实施例C:135g/ft33/2=Pt/Pd,使用二氧化铈的技术底层:将硝酸钯溶液(底层中的总Pd的80%)添加到0.75g/in3高度多孔γ-氧化铝(含4%氧化镧)和0.75g/in3纯二氧化铈的物理混合物中。所得料(frit)含有在二氧化铈上的2.0重量%Pd。将该混合物分散在水和酸(例如乙酸)中并研磨至15μm的粒度d90。将剩余(20%)硝酸钯溶液添加到预研磨的浆料中,用更多酸(乙酸和酒石酸)分散并研磨至7μm的粒度d90。最终浆料由在二氧化铈上的2.4重量%Pd和31g/ft3总Pd载量构成。将含有上文提到的所有组分的浆料涂布到整料上并在空气中在140℃下干燥。中间层:用硝酸钯的水溶液浸渍1.4g/in3的用5%二氧化硅稳定化的高孔隙率氧化铝,以产生20g/ft3的最终干Pd含量。将所得混合物分散在水中。在具有适当容积的大容器中充分搅拌含2%Pt的胶体铂悬浮液以分散铂粒子。将该分散的Pd料(frit)在不断搅拌下缓慢添加到Pt悬浮液中,以产生40g/ft3的干Pt含量和2的Pt/Pd比。在pH调节(用硝酸,然后酒石酸)至4.5后,将该浆料研磨至16μm的粒度d90。随后将该浆料涂布到底层上,在空气中在140℃下干燥。顶层:用硝酸钯的水溶液浸渍0.70g/in3的高度多孔氧化铝(含5重量%二氧化硅)以产生3g/ft3的最终干Pd含量。将所得混合物分散在水中。在具有适当容积的大容器中充分搅拌含2%Pt的胶体铂悬浮液以分散铂粒子。将该分散的Pd料(frit)在不断搅拌下缓慢添加到Pt悬浮液中,以产生42g/ft3的干Pt含量和14的总Pt/Pd比。在pH调节(用硝酸和/或酒石酸)至4.5后,将该浆料研磨至20μm的粒度d90。将预研磨的含贵金属的浆料与0.7g/in3含铁沸石(BEA型,1.5重量%Fe)混合。在添加水下充分混合后,将pH调节至4.3,总固含量固定为35%。随后将该浆料涂布到中间层上,在空气中在140℃下干燥并在空气中在590℃下煅烧。催化剂性能评估在配备用于同时计量两种或更多种气体的几个气体管线的烘箱中进行烘箱老化。所有催化剂一起在烘箱中在800℃下水热(10%O2和10%蒸汽)老化16小时。升温阶段持续4小时至所需老化温度,催化剂在800℃下保持16小时。打开烘箱门以使催化剂突然和快速冷却。在瞬态发动机试验单元上进行发动机台架评估。该台架配备具有1.6l发动机排量的四缸Euro6轻型柴油机。对于排放测量,使用三管线系统AVLAMA400。此外,FTIRAmluk/MKS系统可用于SOx和NOx检测。对于起燃(light-off)(稳态)评估,将各整料适当装罐并置于具有1.6l发动机排量的四缸轻型柴油机的排气管线中的下游。起燃需要单独程序用于CO/HC和NO氧化评估。对于CO和HC,发动机以排气再循环模式(EGR)运行以产生大量CO和HC气体排放物,而NO起燃不用EGR模式进行以促进高发动机NOx排放。排气料流(发动机排放物)中的典型浓度分别恒定在1200、99和110ppm(CO、HC和NOx排放;CO/HC起燃)和315、50和700ppm(CO、HC和NOx排放;NO起燃)。在这两种程序中都使用3-4℃/min的升温速率。催化剂使用具有3l发动机排量的六缸发动机通过在300-350℃下经催化剂燃烧高硫燃料(350ppm)或通过在具有2l发动机排量的四缸发动机的排气管线中直接注入气态SO2来硫化。如下实现脱硫:(1)在硫化催化剂上游安置燃烧器(具有燃料喷射)柴油机氧化催化剂以产生可在下游利用的所需脱硫温度或(2)使用定义明确的发动机运行模式在硫化催化剂本身上产生放热。硫化/脱硫方法在这一研究中都采用并且硫化催化剂释放的SO2量不在任何程度上依赖于所用方法。图9显示对比例A和B的烘箱老化催化剂和实施例C的CO起燃曲线。与催化剂A相比,催化剂C和B表现出在较低温度下的较高CO转化率。图10显示对比例A和B的烘箱老化催化剂和实施例C的HC起燃曲线。催化剂C的HC起燃性能明显优于催化剂A和催化剂B。所有催化剂的铂族金属成本相当。图11显示对比例A和B的烘箱老化催化剂和实施例C的NO2/NOx起燃曲线。催化剂A和C表现出相当的NO氧化(顶层中的Pt量类似),催化剂B总体上更好,但催化剂B顶层中的Pt多30%)。所有催化剂的铂族金属成本相当。图9-11的结果概括在表1中。表1:起燃实施例A实施例B实施例CCOT50(℃)163153143COT70(℃)167162148HCT70(℃)170166155(T80)NO2/NOx@300℃(%)555952表2显示对比例A和实施例C的烘箱老化、硫化和脱硫催化剂的CO起燃结果。表2还显示对比例A和实施例C的烘箱老化、硫化和脱硫催化剂的HC起燃结果。催化剂C表现出更高的硫敏感性,催化剂A(Pt/Pd氧化铝)较不敏感。这两种催化剂都从硫化中恢复。表2:起燃实施例A实施例CCOT50(℃)/烘箱老化163143COT50(℃)/硫化166163COT50(℃)/脱硫160144HCT70(℃)/烘箱老化170155(T80)HCT70(℃)/硫化174163HCT70(℃)/脱硫168156(T80)NO2/NOx@300℃(%)/烘箱5552NO2/NOx@300℃(%)/+S5152NO2/NOx@300℃(%)/-S4951表3显示对比例B和实施例C的烘箱老化、硫化和脱硫催化剂的CO起燃结果。这两种催化剂都表现出较高的硫敏感性(较高的COT50),但是,催化剂C恢复至烘箱老化T50值,而催化剂B没有。表3还显示对比例B和实施例C的烘箱老化、硫化和脱硫催化剂的HC起燃曲线。催化剂C显著恢复,而催化剂B没有从硫中恢复。表3:起燃实施例B实施例CCOT50(℃)/烘箱老化153143COT50(℃)/硫化176163COT50(℃)/脱硫171144HCT70(℃)/烘箱老化162155(T80)HCT70(℃)/硫化183163HCT70(℃)/脱硫180156(T80)NO2/NOx@300℃(%)/烘箱5952NO2/NOx@300℃(%)/+S5952NO2/NOx@300℃(%)/-S6051图12显示来自硫化催化剂A和C的SO2排放。这两种催化剂在入口温度为大约650℃的高温稀燃脱硫后都释放类似量的SO2。这两种催化剂的放热也类似。图13显示来自硫化二氧化铈催化剂B和C的SO2排放。只有催化剂C在高温稀燃脱硫后释放SO2,即使这两种催化剂的入口和床温度相同。本说明书通篇中提到“一个实施方案”、“某些实施方案”、“一个或多个实施方案”或“实施方案”是指联系该实施方案描述的特定要素、结构、材料或特征包括在本发明的至少一个实施方案中。因此,如“在一个或多个实施方案中”、“在某些实施方案中”、“在一个实施方案中”或“在实施方案中”之类的术语在本说明书通篇各处的出现不一定是指本发明的同一实施方案。此外,特定要素、结构、材料或特征可以以任何合适的方式组合在一个或多个实施方案中。尽管在本文中已参照特定实施方案描述了本发明,但要理解的是,这些实施方案仅例示本发明的原理和应用。本领域技术人员显而易见的是,可以对本发明的方法和装置作出各种修改和变动而不背离本发明的精神和范围。因此,本发明旨在包括在所附权利要求和它们的等同物的范围内的修改和变动。当前第1页1 2 3