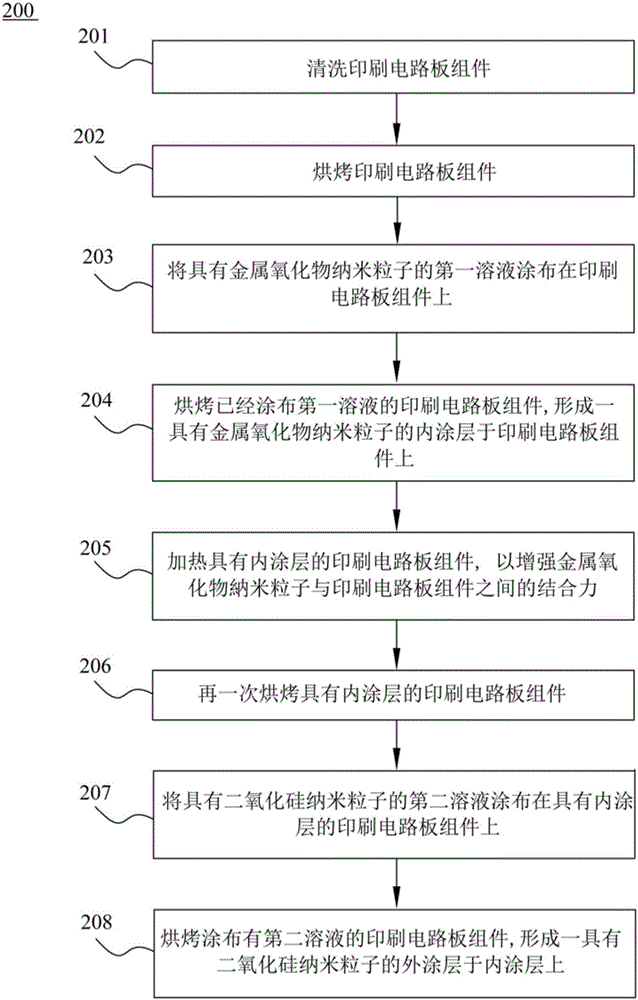
本发明涉及一种纳米涂层制备及涂布方法,尤其涉及一种纳米溶液、用该纳米溶液于装置上形成纳米涂层的方法以及具有纳米涂层的装置,该纳米涂层可以保护装置免于腐蚀与潮湿。
背景技术:
:科技的进步逐渐朝向微型化发展,因此如何抑制吸附环境的湿气以减少腐蚀的产生也变得越来越重要。由于集成电路元件尺寸愈来愈小,元件与元件之间间隔距离变得更相近,因此当外在环境因素使得导电端子吸附水气而形成少量的金属腐蚀时,容易导致整个电子元件的故障。故有必要找到一种制备一具有超疏水性纳米涂层的电子装置的方法,通过这种技术可以保护电子装置表面免于由外界化学反应所引起的潮湿与腐蚀,同时也能延长电子装置的使用寿命。此技术除了应用于电子装置外,亦可应用于其他工程系统如飞行载具、汽车、管道运输或舰艇等等,防止该些工程系统免于腐蚀和受潮,同时也可以提供较小的摩擦力。目前已知物品的表面属性,例如形态、粗糙程度以及成分,会影响表面润湿特性,使表面特性所能呈现的范围由超亲水性横跨至超疏水性。疏水性表面可以通过使用较大尺寸的纳米颗粒沉积在表面上,随后再沉积尺寸较小的纳米颗粒而形成一层疏水性薄膜。当形成疏水特性的表面后,其表面结构上会呈现较粗糙的特征,当水滴滑落在表面上,由于水的表面张力作用使水滴在这种粗糙表面的形状接近于球形,更加容易从表面上滚动,此种表现即为著名的莲花效应。目前市面上有许多制备一具有超疏水涂层的电子装置的技术,包括溶胶凝胶法(sol-gelmethod)、物理气相沉积法(physicalvapordeposition,pvd)和电浆辅助化学气相沉积法(plasma-enhancedchemicalvapordeposition,pecvd)等等。一般来说,溶胶凝胶技术通常是使用含有不同尺寸的颗粒溶液来涂布产生疏水薄膜,疏水薄膜中含有微米级和纳米级颗粒的混合物,用来防止水滴渗入装置。然而,采用溶胶凝胶技术难以控制溶液中纳米颗粒的凝聚和分散现象,导致产生粗糙程度较低的厚膜。而pvd或pecvd技术,则是利用气体反应物在真空腔内,利用物理反应或化学反应,将其汽化形成微粒子体,并进一步的以非常低的速度沉积在基板表面上,形成一层纳米级的薄膜。虽然使用pvd或pecvd技术沉积到基体表面上的疏水性材料通常有比较好的品质,但是,由于气体反应物原料昂贵,提高生产成本,此外,在进行pvd或pecvd的制造过程中,所使用的气体反应物通常具有毒性或易燃性,而且在高温制程中,可能导致损坏电子装置,故此技术仍有极大的发展障碍。综上所述,现有的制备方法仍有成本昂贵与不易涂布于电子产品表面的缺点而有待改进。技术实现要素:本发明的目的是针对上述现有技术的不足,提供一种纳米溶液、于装置上形成纳米涂层的方法及具有纳米涂层的装置,该纳米溶液涂布在装置上形成的纳米涂层为一超疏水性薄膜,可以保护装置免于腐蚀与潮湿,成本低且品质高。为达成上述目的,本发明的目的之一,在于提供一种具有纳米涂层的装置。具有纳米涂层的装置包括一印刷电路板组件与一纳米涂层。印刷电路板组件包括一印刷电路板以及设置在印刷电路板表面上的至少一个电子元件。纳米涂层设置于印刷电路板组件上,包括一内涂层与外涂层,内涂层主要包括粒径范围介于5~100nm的金属氧化物纳米粒子,外涂层主要包括粒径范围介于0.1~10nm的二氧化硅纳米粒子。其中,印刷电路板组件包括有多个细孔与缺口,大粒径的金属氧化物纳米粒子形成内涂层于印刷电路板组件上多个细孔与缺口内,而小粒径的二氧化硅纳米粒子在内涂层上形成外涂层,小粒径的二氧化硅纳米粒子亦能渗入金属氧化物纳米粒子的内涂层内而形成纳米涂层。其中,依照使用设计需求,印刷电路板组件的至少一部分可暴露于纳米涂层或暴露于外涂层。本发明的另一目的之一,在于提供一种于装置上形成纳米涂层的方法,其方法包括以下步骤:将具有金属氧化物纳米粒子的第一溶液作为第一溶质涂布在装置上,其中第一溶液包括具有粒径范围介于5~100nm的金属氧化物纳米粒子和一第一溶剂,且涂布方式可为喷洒、浸泡、滚轴涂布、印刷等相关技术;在一适当温度及时间下对涂布完第一溶液的装置进行烘烤使其移除第一溶剂,例如,在摄氏50℃~150℃下烘烤且持续5到30分钟,借此形成一具有金属氧化物纳米粒子的内涂层在装置上且增强内涂层与装置之间的结合力,例如,可使用加热方式在摄氏25℃~100℃且持续2到72小时;对形成内涂层的装置进行烘烤,例如,烘烤温度大约在摄氏50℃~150℃且持续10到30分钟;将具有二氧化硅纳米粒子的第二溶液作为第二溶质涂布在内涂层上,其中第二溶液包括具有粒径范围介于0.1~10nm的二氧化硅纳米粒子和一第二溶剂;对涂布完第二溶液的装置进行烘烤使其移除第二溶剂,例如,烘烤温度大约在摄氏50℃~150℃且持续10到30分钟,借此形成一具有二氧化硅纳米粒子的外涂层在内涂层上且增强内涂层与外涂层结合力,其中,在制程过程中,装置上的某些部分可应用遮罩材料进行遮罩处理。例如,有些部分在涂布第一溶液前,使用遮罩材料布置在装置的至少一部分,并在外涂层形成后,去除遮罩材料,暴露出所述部分,或是,有些部分会在涂布第二溶液前,使用遮罩材料布置在装置的至少一部分,并在外涂层形成后,去除遮罩材料,暴露出所述涂布有内涂层的部分。本发明的另一目的之一,在于提供一种纳米溶液,包括金属氧化物纳米粒子与一溶剂,其中金属氧化物含有一种或多种选自铝、镓、铟、锡、铊、铅、铋、钪、钛、钒、铬、锰、铁、钴、镍、铜、锌、钇、锆、铌、钼、锝、钌、铑、钯、银、镉、镥、铪、钽、钨、铼、锇、铱、铂、金、汞的氧化物及其组合,金属氧化物纳米粒子的粒径范围介于5nm~100nm之间,且金属氧化物纳米粒子溶液具有约0.3%~5%的重量百分浓度,而溶剂可选自水、甲醇或乙醇中的其中一种或其任何组合。本发明的另一目的之一,在于提供另一种纳米溶液,包括二氧化硅纳米粒子与一种溶剂,所述二氧化硅纳米粒子的粒径范围介于0.1nm~10nm之间,且二氧化硅纳米粒子在溶液中的浓度为0.3%~5%重量百分浓度,而溶剂含有庚烷、十六烷以及甲基氢矽氧烷其中一种或其组合。如上所述,本发明的纳米涂层包括大粒径的金属氧化物纳米粒子与小粒径的二氧化硅纳米粒子,可应用于印刷电路板组件上,同时达到防水、防蚀且比现有技术的保护膜厚度更薄,不影响其电子元件散热性等其他功能,从而可更好地保护印刷电路板与其电子元件。附图说明图1是本发明的一实施例电子装置示意图,电子装置具有纳米涂层的印刷电路板组件。图2是本发明的一实施例涂布印刷电路板组件的流程图。图3a是本发明的一实施例显示水珠落于具有纳米涂层的玻璃基板上的状态图。图3b是图3a显示其中一粒水珠位于具有纳米涂层的玻璃基板上的近视图。图4是本发明的一实施例显示以动态光散射方法在室温下量测二氧化钛纳米粒子尺寸分布测量结果图。图5是本发明的一实施例显示以动态光散射方法在室温下量测二氧化钛纳米粒子尺寸分布另一测量结果图。图6是本发明的一实施例显示以动态光散射方法在室温下量测二氧化钛纳米粒子尺寸分布另一测量结果图。图7是本发明的一实施例显示以动态光散射方法在室温下量测二氧化钛纳米粒子尺寸分布另一测量结果图。图8是本发明的一实施例显示以动态光散射方法在室温下量测二氧化硅纳米粒子尺寸分布测量结果图。图9是本发明的一实施例显示以动态光散射方法在室温下量测二氧化硅纳米粒子尺寸分布另一测量结果图。图10是本发明的一实施例显示以动态光散射方法在室温下量测二氧化硅纳米粒子尺寸分布另一测量结果图。图11是本发明的一实施例显示以动态光散射方法在室温下量测二氧化硅纳米粒子尺寸分布另一测量结果图。图12是本发明的一实施例扬声器的爆炸图,扬声器具有涂布纳米涂层的元件以具备防水功能。图13是本发明的一实施例制造一电声装置的流程图。图14是本发明的一实施例涂布第二纳米涂层在振膜的流程图。图15a-15c是本发明的一实施例显示以动态光散射方法量测二氧化钛纳米粒子尺寸分布测量结果图。图16是本发明的一实施例显示以穿透式电子显微镜量测二氧化硅纳米粒子尺寸分布测量结果图。图17是本发明的一实施例显示以穿透式电子显微镜量测氟化纳米粒子尺寸分布测量结果图。图18是本发明的一实施例显示两个防尘网分别为具有纳米涂层(右侧)与未具有纳米涂层(左侧)的比较水滴在其上的表现图。图19是本发明的一实施例显示电声装置在涂布纳米涂层前后的平均频率响应图。图20是本发明的一实施例显示电声装置在涂布纳米涂层前后的平均频率响应差值结果图。图21是本发明的一实施例显示电声装置在涂布纳米涂层前后的平均总谐波失真结果图。图22是本发明的一实施例显示电声装置在涂布纳米涂层前后的平均总谐波失真差值结果图。具体实施方式为详细说明本发明的技术内容、构造特征、所实现的目的及功效,以下结合具体实施例并配合附图予以详细说明。要了解的是本说明书以下的揭露内容提供许多不同的实施例或范例,以公开各种不同实施例的不同特征。当然,这些特定的范例并非用以限定本发明。另外,本发明的说明中不同范例可能使用重复的参考符号及/或用字。这些重复符号或用字是为了简化与清晰的目的,并非用以限定各个实施例及/或所述外观结构的关系。再者,若是本说明书以下的揭露内容叙述了将第一特征形成于一第二特征的上或上方,即表示其包括了所形成的上述第一特征与上述第二特征是直接接触的实施例,亦包括了尚可将附加的特征形成于上述第一特征与上述第二特征之间,而使上述第一特征与上述第二特征可能未直接接触的实施例另外,以下发明揭露书不同范例可能重复使用相同的参考符号及/或标记。这些重复是为了简化与清晰的目的,并非用以限定本说明书中的不同实施例及/或结构之间有特定的关系。此外,本说明书中的空间相关用词。例如“在...下方”、“下方”、“较低的”、“上方”、“较高的”及类似的用词,是便于描述图示中一个元件或特征与另一个(些)元件或特征之间的关系。除了在图式中绘示的方位外,这些空间相关用词意欲包括使用中或操作中的装置的不同方位。装置可能被转向不同方位(旋转90度或其他方位),则在此使用的空间相关词也可依此相同解释。如本说明书中所使用,除非上下文另有清楚指示,否则单数形式“一”、“一种”、“该”及“所述”包括复数形式含意,对具体数值的引用至少包括该具体数值。因此,例如提到“印刷电路板组件”时,是指一种或多种这样的结构,以及本领域普通技术人员所熟知该印刷电路板组件的均等结构,等等。关于本说明书中所提及数字或数值范围时术语“约”、“大约”或“大致”,意谓所提及的数字或数值范围为近似值,应当理解,该具体值形成了另一个实施例。在一些实施例中,上述数值的误差或范围是指于±10%,例如,如本说明书中所述,“约x”(此处x为数值)为较好地指所引用值±10%,且包括端点值。例如,术语“约8”较好地指7.2至8.8之间的值,且包括端点值;又如,术语“约8%”较好地指7.2%至8.8%之间的值,且包括端点值。在一些实施例中,所有范围均包括端点值以及其中的组合。例如,当引用“1至5”的范围时,所引用范围应当理解为包括“1至4”、“1至3”、“1至2”、“1至2和4至5”、“1至3和5”、“2至5”等范围。此外,当以肯定方式提供了一列备选项时,该列备选项可以理解为表示可以排除备选项中的任何一个,例如通过在权利要求中加上否定的限制实现。例如,当引用“1至5”的范围时,所引用范围应当理解为包括以否定方式排除1、2、3、4或5中任何一项的情形;因此,对“1至5”的引用可以理解为“1和3-5,但不包括2”,或者仅仅是“其中不包括2”。除非另有定义,否则于本说明书中所提及的“金属”应当理解是指来自由周期表中属于金属的元素,包括过渡金属及后过渡金属。所述“金属氧化物”可以选自以下群组中的一种或多种金属元素所组成的金属氧化物,例如(1)第一列过渡金属元素包括(但不限于):sc、ti、v、cr、mn、fe、co、ni、cu及zn;(2)第二列过渡金属元素包括(但不限于):y、zr、nb、mo、tc、ru、rh、pd、ag及cd;(3)第三列过渡金属元素包括(但不限于):la、hf、ta、w、re、os、ir、pt、au及hg;或(4)后过渡金属元素又称“贫金属”包括(但不限于):al、ga、in、tl、sn、pb、sb及bi。较佳地,所述金属氧化物的金属元素可选自al,ti,cr,mn,co,zn,mo,rh,pd,ag,w及au的至少一种金属元素。例如,在本发明中一些实施例所采用的金属氧化物为二氧化钛。图1为本发明提供一较佳实施例的一电子装置100示意图。该电子装置100包括一印刷电路板组件10和涂布在该印刷电路板组件10表面的一纳米涂层3。印刷电路板组件10包括一印刷电路板1以及设置在印刷电路板1上的一个或多个电子元件2。其中,该印刷电路板1及该些电子元件2的周边或表面因为在一些工艺制程中而形成多个细孔、缺口和其他结构而导致表面粗糙化。在本实施例中,该纳米涂层3包括金属氧化物纳米粒子和粒径尺寸小于金属氧化物纳米粒子的二氧化硅纳米粒子。该纳米涂层3包括一内涂层31和一外涂层32。内涂层31包括金属氧化物纳米粒子且形成于印刷电路板1与电子元件2上。外涂层32包括二氧化硅纳米粒子且形成于内涂层31上。如图1所示的内涂层31、外涂层32与印刷电路板组件10结构仅是示意图,其并未只限定于内、外两层结构关系。在一些实施例中,内涂层31的表面具有多个细孔、缺口和其他结构。当外涂层32形成在内涂层31上时,外涂层32和内涂层31之间可以相互渗透。在一些实施例中,外涂层32和内涂层31可以不是两个分开的层结构。一般来说,粒子越接近印刷电路板组件10的表面,其粒径尺寸增加。在一些实施例中,内涂层31可以渗入到印刷电路板组件10的多个细孔、缺口和其他结构中。其中,内涂层31包括具有粒径范围为5~100nm的金属氧化物纳米粒子。外涂层32包括具有粒径范围为0.1~50nm的二氧化硅纳米粒子,优选的为0.1~10nm的二氧化硅纳米粒子。本发明所属
技术领域:
中普通技术人员可了解,该些电子元件2可使用各式各样的主动及被动元件,例如一电容器、一电感器、一电阻器、一电晶体、一二极管、一连接器、一扬声器或一麦克风以及其类似的元件,以产生符合设计所需的结构装置于印刷电路板1上。同样地,本发明所属
技术领域:
中普通技术人员应可了解,所述印刷电路板组件10可以应用于在一电池、一耳机、一智能手机或是其他电子装置上。在一些实施例中,印刷电路板1是由fr-4(fr-4是一种耐燃材料等级的代号,所代表的意思是树脂材料经过燃烧状态必须能够自行熄灭的一种材料规格)复合材料所制成。在一些实施例中,所述纳米涂层3是由一具有金属氧化物纳米粒子的溶液以及一具有二氧化硅纳米粒子的溶液在进行挥发过程中而形成一层涂布在印刷电路板组件10上的纳米涂层3。在一些实施例中,所述金属氧化物纳米粒子溶液包括金属氧化物纳米粒子和一溶剂的混合溶液。其中金属氧化物纳米粒子溶液具有约0.3%~5%的浓度,而溶剂可选自水、甲醇或乙醇中的其中一种或其任何组合。在一些实施例中,金属氧化物纳米粒子溶液是透明的且亲水性的。在一些实施例中,所述二氧化硅纳米粒子溶液包括二氧化硅纳米粒子和一溶剂的混合溶液。其中二氧化硅纳米粒子溶液具有约0.3%~5%的浓度,而溶剂成分为庚烷、十六烷以及甲基氢矽氧烷等或其任何组合。在一些实施例中,二氧化硅纳米粒子溶液是透明的、疏水性的以及低挥发性的。在溶剂的帮助下,纳米粒子能够均匀分散在印刷电路板1与电子元件2表面上,以减少聚集现象,有助于增加粒子接触面积。因而形成一紧密性高、均匀性佳、厚度薄的纳米涂层3在印刷电路板组件10上。如图2所示,本发明提供一些实施例示出一使用金属氧化物纳米粒子和二氧化硅纳米粒子涂布于印刷电路板组件10上的示例性方法200。将印刷电路板组件10先放置于载台(未示出)上以执行稍后的步骤。清洗印刷电路板组件10以去除制造过程中形成的助焊剂残余物(步骤201)。在一些实施例中,步骤201可以使用超声波清洁设备(未示出)清洗,且进行清洗时的清洗温度(℃)是40℃~60℃的纯水中且清洁时间为10-30分钟。烘烤印刷电路板组件10以干燥印刷电路板组件10并使印刷电路板组件10上的多个细孔、缺口和其他结构暴露出来(步骤202)。在一些实施例中,步骤202可以使用烘焙设备(未示出),且进行烘烤时的烘烤温度(℃)为50℃~150℃且烘烤时间为10~30分钟。将一第一溶液涂布在印刷电路板组件10上(步骤203)。所述第一溶液包括作为第一溶质的金属氧化物纳米粒子和第一溶剂。在一些实施例中,步骤203可以使用浸渍、喷涂或刷涂等其他可能的方式使第一溶液涂布在印刷电路板组件10上。在一些实施例中,金属氧化物纳米粒子的粒径范围在5nm~100nm之间。在一些实施例中,第一溶液的浓度范围为0.3%~5%。烘烤已经涂布第一溶液的印刷电路板组件10,借由至少一种蒸发或热解的方式以去除第一溶剂并留下金属氧化物纳米粒子以形成内涂层31于印刷电路板组件10上(步骤204)。在一些实施例中,步骤204可以使用烘焙设备(未示出)进行烘烤,其烘烤温度(℃)为50℃~150℃且烘烤时间为5~30分钟。第一溶剂为水、甲醇或乙醇中的其中一种或其任何组合,借由第一溶剂可帮助金属氧化物纳米粒子更加均匀分散在印刷电路板组件10上。将具有内涂层31的印刷电路板组件10从载台上卸下。加热具有内涂层31的印刷电路板组件10以增强金属氧化物纳米粒子与印刷电路板组件10之间的结合力(步骤205)。在一些实施例中,步骤205将具有内涂层31的印刷电路板组件10进行加热,其中加热温度(℃)为25℃~100℃且加热时间为2~72小时。但本领域普通技术人员应能了解,本发明用于增强金属氧化物纳米粒子和印刷电路板组件10之间结合力的方式不应仅局限其加热方式,任何可增强结合力的方法或方式,皆应落入本发明精神与范畴内。在加热之后,将具有内涂层31的印刷电路板组件10放置在载台(未示出)中。烘烤具有内涂层31的印刷电路板组件10以暴露出内涂层31的多个细孔、缺口和其他结构(步骤206)。在一些实施例中,步骤206可以使用烘焙设备(未示出)进行烘烤,其烘烤温度(℃)为50℃~150℃且烘烤时间为10~30分钟。在一些实施例中,在进行增强金属氧化物纳米粒子与印刷电路板组件10之间的结合力(步骤205)之后,以及烘烤具有内涂层31的印刷电路板组件10(步骤206)之前还包括步骤:检查具有内涂层31的印刷电路板组件10的外观以及步骤:清洗有内涂层31的印刷电路板组件10。将一第二溶液涂布在内涂层31(步骤207)。所述第二溶液包括作为第二溶质的二氧化硅纳米粒子和第二溶剂。在一些实施例中,步骤207可以使用浸渍、喷涂或刷涂等其他可能的方式使第二溶液涂布在内涂层31上。在一些实施例中,二氧化硅纳米粒子的粒径范围在0.1~10nm之间。在一些实施例中,第二溶液的浓度范围为0.3%~5%,第二溶剂成分为庚烷、十六烷以及甲基氢矽氧烷等或其任何组合,借由第二溶剂可帮助二氧化硅纳米粒子更加均匀的分散在内涂层31上。烘烤已经涂布第二溶液的印刷电路板组件10,借由至少一种蒸发或热解的方式以去除第二溶剂并留下二氧化硅纳米粒子作为外涂层32于内涂层31上(步骤208)。在一些实施例中,步骤208可以使用烘焙设备(未示出)进行烘烤,其烘烤温度(℃)为50℃~150℃且烘烤时间为10~30分钟。接着,检查形成纳米涂层3的印刷电路板组件10的外观与功能。在一些实施例中,为了因应设计上的需求,可能有一个或多个的电子装置100的构件不需要涂布纳米涂层3。例如,当印刷电路板组件10包括需要暴露在外的一扬声器、一麦克风或是一开关时。因此,将第一溶液和第二溶液涂布在印刷电路板组件10时,需要遮罩这些构件。在一些实施例中,麦克风和开关可以在进行清洗印刷电路板组件10(步骤201)前先进行遮罩作业,因为麦克风上的振膜和开关都需要避免接触水气或其他液体以免受潮。在一些实施例中,开关可以在涂布第二溶液于内涂层31上(步骤207)之前进行遮罩作业。例如,开关可以在涂布第二溶液于内涂层31上(步骤207)之前以及在进行强化金属氧化物纳米粒子与印刷电路板组件10之间的结合力(步骤205)之后进行遮罩作业。因为具有二氧化硅纳米粒子的第二溶液会影响开关的功能。在另一个例子中,开关可以在进行烘烤具有内涂层31的印刷电路板组件10(步骤206)之前以及进行强化金属氧化物纳米粒子与印刷电路板组件10之间的结合力(步骤205)之后进行遮罩作业。最后,在形成外涂层32之后,再将这些遮罩在构件上的材料移除使其暴露出一个或多个构件或一个或多个有内涂层的构件。在本发明中所提及的有关温度值都是摄氏温标(℃),还有,有关溶液的浓度表示为重量百分比(wt.%)或体积百分比。在一些实施例中,二氧化硅纳米粒子可以是无固定形状且疏水性的二氧化硅颗粒。二氧化硅颗粒(例如,热解法二氧化硅)是由供应商所提供,且未经过任何化学改质。这些二氧化硅颗粒在涂布表面上提供所需的疏水性质。在一些其它实施例中,二氧化硅颗粒可以被化学改质。二氧化硅纳米粒子因表面羟基(-oh)含量高,这些羟基可以与基板和/或金属氧化物纳米粒子表面上的羟基反应,进而促进共价键的形成以提高纳米涂层的粘附性。在一些实施例中,可以使用表面活性剂或分散剂在含有纳米粒子的溶液或悬浮液中。在一些实施例中,纳米涂层3的厚度小于200nm。例如,依据电子装置100的用途,纳米涂层3的厚度优选的在5nm~100nm、10nm~20nm的范围内。如图3a、图3b所示。本发明提供一实施例的水珠在具有纳米涂层3的玻璃基板上所呈现的状态图。纳米涂层3包括二氧化钛纳米粒子和二氧化硅纳米粒子,其中二氧化硅纳米粒子的粒径比二氧化钛纳米粒子的粒径还要小,因而呈现出有层次的结构和较高的表面粗糙度,所以拥有疏水性质。如图3a所示,由于纳米涂层3的超疏水性效应,水珠落在涂布有纳米涂层3的玻璃基板上后分散而形成更微小的水珠。图3b是根据图3a中其中一微小水珠的近视图。当水滴滴落在具有纳米涂层3的玻璃基板表面上时,水珠与涂布有纳米涂层3的玻璃基板之间的接触角θ约为128°±2°,一般来说,θ≥90°,或θ≥110°,或θ≥130°,或150°≥θ≥110°,或150°≥θ≥90°,在本发明一些实施例中,具有纳米涂层3的装置可以使表面具有较少的摩擦力或其他功能。以下实施例是用于进一步了解本发明的优点,并非用于限制本发明的申请专利范围。纳米涂层可以借由使用以下两种溶液(或混合物或悬浮液)制成。第一溶液具有金属氧化物纳米粒子,其制备方法包括以下步骤:将金属粉末与蒸馏水加入血清瓶中,形成金属粉末溶液;调整金属粉末溶液的ph值,借由加入不同溶剂调节ph值在6.5到9.5范围内,其中溶剂包括酸性溶剂,如硝酸、氢氟酸、硫酸或盐酸,和中性溶剂,如异丙醇、丙酮或酒精,以及碱性溶剂,如氢氧化钠、氢氧化钾或氨水;在适当的温度与时间下加热溶液并剧烈搅拌,例如,加热温度大约在摄氏50℃~150℃且持续10到20小时。最后得到具有金属氧化物纳米粒子的第一溶液,其中金属氧化物纳米粒子的粒径约为5~100nm,而且在室温下,此溶液是亲水性且透明的。在本发明的实施例中,其中金属氧化物纳米粒子优选的为粒径范围5nm~100nm之间的二氧化钛(tio2)纳米粒子,且tio2纳米粒子占第一溶液中0.3%~5%的重量百分浓度范围,优选的为0.8%~1.5%的重量百分浓度范围内,且其第一溶液的密度为1.01g/cm3。请参考图4到图7,是采用动态光散射方法在室温下量测第一溶液中tio2纳米粒子尺寸分布结果图。图4显示了一个根据本发明的实施例在室温下第一溶液具有直径约为72.11nm的100%tio2纳米粒子。图5显示了一个根据本发明的实施例在室温下第一溶液具有直径约为72.70nm的100%tio2纳米粒子。图6显示了一个根据本发明的实施例在室温下第一溶液具有直径约为8.191nm的100%tio2纳米粒子。图7显示了一个根据本发明的实施例在室温下第一溶液具有直径约为7.406nm的100%tio2纳米粒子。第二溶液具有二氧化硅纳米粒子,其制备方法包括以下步骤:将二氧化硅粉末与蒸馏水加入血清瓶中,形成二氧化硅粉末溶液;调整二氧化硅粉末溶液的ph值,借由加入不同溶剂调节ph值在6.5到9.5范围内,其中溶剂包括酸性溶剂,如硝酸、氢氟酸、硫酸或盐酸,和中性溶剂,如异丙醇、丙酮或酒精,以及碱性溶剂,如氢氧化钠、氢氧化钾或氨水;再加入有机溶剂如正己烷、正庚烷、正辛烷、正十二烷、十四烷,或正十六烷;最后加入催化剂,如铁、铬、锰或钼金属材料;并且在适当温度与时间下加热溶液并剧烈搅拌,例如,加热温度大约在摄氏50℃~150℃且持续1到10小时;接着得到一个形成上下两层的混合溶液,其中上层为粒径范围较小的二氧化硅纳米粒子溶液;最后萃取混合溶液的上层作为第二溶液。第二溶液在室温下具有粒径分布约0.1~50nm的二氧化硅纳米粒子,而且,此溶液为透明且具有疏水性与低挥发性。在本发明实施例中,第二溶液包括庚烷和十六烷及甲基氢聚矽氧烷(约重量百分浓度0.1-5%),二氧化硅(sio2)纳米粒子的粒径范围优选的为0.1nm~10nm之间。其中,sio2纳米粒子占第二溶液中0.1%~5%的重量百分浓度范围内,优选的为0.3%~5%的重量百分浓度范围内,且其第二溶液的密度约为0.774g/cm3。请参考图8到图11,是采用动态光散射方法在室温下量测第二溶液中sio2纳米粒子尺寸分布结果图。图8显示了一个根据本发明的实施例在室温下第二溶液具有直径约为0.8184nm的100%sio2纳米粒子。图9显示了一个根据本发明的实施例在室温下第二溶液具有直径约为1.164nm的100%sio2纳米粒子。图10显示了一个根据本发明的实施例在室温下第二溶液具有直径约为33.23nm的100%sio2纳米粒子。图11显示了一个根据本发明的实施例在室温下第二溶液具有直径约为25.13nm的100%sio2纳米粒子。另一实施例为一示例性方法,于一印刷电路板组件上形成纳米涂层的方法,步骤为:使用一溶剂清洗印刷电路板组件10然后在60℃下干燥10分钟。接着将清洗完的印刷电路板组件浸入第一溶液中约5-10秒,然后在150℃下烘烤5分钟,在50℃下烘烤8小时。接着在80℃下预热10分钟后,再将印刷电路板组件浸入第二溶液中5-10秒。然后将印刷电路板组件在100℃下烘烤20分钟。尽管在本发明中所采用的实施例为一印刷电路板组件,然而其他材料如金属、玻璃、塑胶基板或其他电子产品等等亦能使用本发明的涂布纳米涂层技术。在下文中,将解释本发明的一些实施例中具有纳米涂层的印刷电路板组件的性能测试结果。耐腐蚀性测试i以下测试为采用目前现有的气相沉积技术所形成的薄膜与本发明的技术形成的纳米涂层进行耐腐蚀性测试比较。一般来说,使用气相沉积技术所形成的薄膜厚度较难以控制,所以当薄膜的厚度越厚,尽管其保护效果提升,但是被沉积的印刷电路板组件表现性能则会变差。在此测试中,分别有两测试产品进行比较,所述测试产品为印刷电路板组件,其中一个是由气相沉积技术形成薄膜保护,其薄膜厚度约在3μm~5μm的范围之间,另一个则是使用本发明的技术形成纳米涂层。测试步骤如下所述:每5分钟点一次盐水在两个测试产品上的各个电子元件持续一小时,之后再将两个测试产品放入40℃的环境中以干燥电子元件。每一天重复两次上述步骤后,进行电子元件的功能测试,直到两个测试产品上的所有电子元件都无法运作。测试结果如表一所示:借由气相沉积形成薄膜的印刷电路板组件其腐蚀速率比本发明的技术形成纳米涂层的印刷电路板组件其腐蚀速率较快。故,本发明的实施方式所形成的纳米涂层具有更好的耐腐蚀性性质。表一、耐腐蚀性测试后结果耐腐蚀性测试ιι另一测验为本发明的纳米涂层化学耐久性测试。在本测试中,一公端连接器上电性连接一具有纳米涂层的一印刷电路板组件。测试步骤如下:将具有纳米涂层的印刷电路板组件及公端连接器浸泡在人工汗液内,然后取出,再与连接器母端进行充电一小时,每一次充电结束,再次将具有纳米涂层的印刷电路板组件和公端连接器浸泡在人工汗液内,并重复执行充电和浸泡200次,观察充电期间连接器的充电电压、充电电流以及充电指示灯的情况,直到充电失败无法运作功能,测试结果如表二所示:浸泡在人工汗液的连接器公端并没有受到盐水腐蚀的影响而且皆在标准范围内正常运作。表二、化学耐久性测试结果测试项目电压电流指示灯测试结果在标准范围内在标准范围内正常运作防水测试i此测试主要目的为判断具有纳米涂层的印刷电路板组件是否有防水功能,在本实施例中使用两个耳机进行本发明的涂布技术,使其形成纳米涂层保护其印刷电路板组件。测试步骤如下:将耳机放入水中,并记录在水中播放功能的时间,直到播放功能无法运作。测试结果如表三所示:其在水中平均运作时间为207.5分钟,因此涂布有本发明的纳米涂层的耳机有效地达到防水功能。表三、防水测试记录结果防水测试ιι在本项测试中,采用本发明的技术形成一具有纳米涂层的印刷电路板组件连接一电池组进行防水测试。测试步骤如下:将具有纳米涂层的印刷电路板组件连接电池组放入水中30分钟,并观察电池组是否能正常运作,测试结果如表四所示:形成纳米涂层的印刷电路板组件所连接的电池组可以在水中正常地运作。表四、防水测试结果检查项目目视检查电子功能测试可靠度测试测试结果通过通过通过电阻量测测验在本测验中,主要目的是确认具有纳米涂层的印刷电路板组件是否会影响其上的表面电阻,故在本实施例中分别在涂布纳米涂层之前与之后的印刷电路板组件量测其上的表面电阻值变化。测试步骤如下:先量测未涂布纳米涂层的印刷电路板组件上两个测试点的电阻值,然后将印刷电路板组件进行涂布作业,形成纳米涂层后再量测原先两个测试点的电阻值。测试结果如表五所示:涂布完纳米涂层的印刷电路板组件并不会影响其上的表面电阻值,涂布纳米涂层后的印刷电路板组与涂布前的印刷电路板组其表面电阻值差异仅在1%以内。表五、电阻测试结果电流量测测验在本项测试中,主要目的是确认具有纳米涂层的印刷电路板组件是否会影响其上的表面电流,故在本实施例中分别在涂布纳米涂层之前与之后的印刷电路板组件量测其上的表面电流值变化。测试步骤如下:先量测涂布纳米涂层之前的印刷电路板组件上四个测试点的电流值,然后涂布印刷电路板组件形成纳米涂层,之后再量测原先四个测试点的电流值。其测试结果如表六所示:形成纳米涂层的印刷电路板组件并不会影响表面电流值,差异值都仅在±1%内。表六、电流测试结果本发明所揭露的涂布纳米涂层的方法是使用印刷电路板组件作为实施例,但跟据本发明所揭露的涂布纳米涂层的实施方法亦可应用于其它装置中。例如,当电缆连接印刷电路板组件时,电缆和印刷电路板组件同时被涂布纳米涂层。在涂布纳米涂层后,电缆可具有较好的防水性质,较好的耐腐蚀性和较小的摩擦力。另外,本领域普通技术人员还可以在上述涂布纳米涂层的过程中,在不同的装置上改变其清洁、烘烤和加热过程中的温度参数和时间参数,当然,这些依据本发明精神所做的变化,应包括在本发明所要求的保护范围内。根据本发明又另一实施例提供一涂布纳米涂层于装置的方法,该方法包括以下步骤:将装置进行清洗作业;将装置进行烘烤作业;应用一第一溶液涂布于装置上,其中第一溶液具有作为一第一溶质的金属氧化物纳米粒子,金属氧化物纳米粒子的粒径范围为5~100nm;将涂布于装置的第一溶液借由至少一种蒸发或热解的方式,留下第一溶质形成一内涂层于装置上;增强金属氧化物纳米粒子与装置之间的结合力;烘烤形成内涂层的装置;应用一第二溶液于内涂层上,第二溶液具有一作为第二溶质的二氧化硅纳米粒子,二氧化硅纳米粒子粒径范围为0.1~10nm;将涂布于装置的第二溶液借由至少一种蒸发或热解的方式留下第二溶质形成一外涂层于内涂层上。在一些实施例中,清洗作业可使用一种超声波清洗设备。第一溶液涂布于装置上的方法可为一种浸泡、喷洒或涂刷等的方式。第二溶液涂布于装置上的方法可为一种浸泡、喷洒或涂刷等的方式。一种蒸发或热解的方式在涂布有第一溶液的装置上可使用一种烘烤设备。一种蒸发或热解的方式在涂布有第二溶液的装置上可用一种烘烤设备。在一些实施例中,该涂布装置的方法进一步包括一检查具有内涂层的装置外观步骤与一清洗具有内涂层的装置步骤,此步骤位于增强金属氧化物纳米粒子与装置之间的结合力步骤之后与烘烤形成内涂层的装置之前。其中增强金属氧化物纳米粒子与装置之间结合力的步骤可使用一热处理方式增强。在一些实施例中,金属氧化物纳米粒子在第一溶液中的重量百分浓度约为0.3%~5%。二氧化硅纳米粒子在第二溶液中的重量百分浓度约为0.3%~5%。第一溶剂为水、甲醇或乙醇中的其中一种或其任何组合。而第二溶剂成分为庚烷、十六烷以及甲基氢矽氧烷等或其任何组合。在一些实施例中,于装置上形成纳米涂层的方法进一步包括一遮罩步骤与一移除遮罩材料步骤,所述遮罩步骤是使用遮罩材料在装置上一个或多个区域以避免后续作业而影响装置功能。在一些实施例中,可在装置清洗作业之前进行遮罩步骤;亦可在涂布一第一溶液于装置上之前进行遮罩步骤与装置进行烘烤作业步骤之后;亦可在涂布一第二溶液布于装置上之前与进行增强金属氧化物纳米粒子与装置之间结合力之后进行遮罩步骤,最后,在形成外涂层之后,再将这些遮罩在构件上的材料移除使其暴露一个或多个区域或一个或多个内涂层。又另一实施例,请参考图12,为本发明一实施例扬声器1200的爆炸图,扬声器1200的元件涂布有纳米涂层以具备防水功能。扬声器1200包括一驱动元件1210、一印刷电路板组件1220、一振膜1230、一防尘网1240以及其他元件。其他元件可包括一铁心1251、一永久磁铁1252、一华司1253、一框架1254和一弹波1255。驱动元件1210借由导线1256电性连接印刷电路板组件1220。印刷电路板组件1220包括一印刷电路板1221和设置于印刷电路板1221上的多个电子元件1222。印刷电路板组件1220连接驱动元件1210,使驱动元件1210能驱动振膜1230。在一些实施例中,振膜1230由纤维材料制成,例如人工纤维材料或是皮革。驱动元件1210可以是一种动铁式驱动元件、一种动圈式驱动元件或一种压电式驱动元件。该些电子元件1222可以是安装在印刷电路板1221上的电阻器、电容器、电感器、电晶体或其他元件。在一些实施例中,为了使电声装置,如扬声器1200能够发出全频段的声音,即低频、中频和高频,印刷电路板组件1220先处理输入的电信号,然后再将电信号转换为多个频带信号,该些频带信号被分送到驱动元件1210上驱动振动振膜1230从而产生声音。在本实施例中,印刷电路板组件1220先涂布一第一纳米涂层,所述第一纳米涂层包括一具有金属氧化物纳米粒子的内涂层和一具有二氧化硅纳米粒子的外涂层,其中金属氧化物纳米粒子的粒径尺寸比二氧化硅纳米粒子的粒径尺寸大。在一些实施例中,内涂层的表面和周边因为一些制程工艺而产生多个微小细孔,缺口和其他结构。当外涂层形成在内涂层上时,外涂层会渗透进入内涂层的多个微小细孔,缺口和其他结构。在一些实施例中,外涂层和内涂层可以不是分层结构,例如,金属氧化物纳米粒子和二氧化硅纳米粒子可以形成在同一层,二氧化硅纳米粒子渗透到金属氧化物纳米粒子之间的空隙,例如细孔或缺口中,而在印刷电路板组件上形成包括金属氧化物纳米粒子和二氧化硅纳米粒子的纳米涂层。在本实施例中,振膜1230被涂布一第二纳米涂层,所述第二纳米涂层包括氟化纳米粒子,例如含氟聚合物粒子。所述一种含氟聚合物用于形成氟化纳米粒子,如含氟塑料颗粒、全氟聚合物,例如聚四氟乙烯、全氟醚、全氟酯或全氟酯改性的矽氧烷,但并不局限于此范围内。在一些实施例中,含氟聚合物纳米粒子包括碳原子与氟原子键结(例如c-f)和/或碳原子与羟基键结(例如c-oh)。例如,在一些实施例中,氟化纳米粒子由全氟醚、全氟酯、全氟醚、或全氟酯改性的矽氧烷制成。这种氟化纳米粒子的粒径范围可以在1~150nm、10~100nm、50~100nm或72±21nm的平均值或25~75nm的范围或其任何组合。请参考图13,本发明提供一实施例的涂布纳米涂层在电声装置的方法1300,其包括以下步骤:形成第一纳米涂层于印刷电路板组件1220上且形成第二纳米涂层于振膜1230上(步骤1302)。印刷电路板组件1220、驱动单元1210、振膜1230和其他元件一起组装形成电声装置(步骤1304)。请参考图14,本发明提供一实施例的涂布第二纳米涂层在振膜1230的方法1400。其包括以下步骤:将振膜1230置于自动浸泡机中(步骤1402),其中自动浸泡机包括一第三溶液,第三溶液包括一第三溶质与一第三溶剂,第三溶质为氟化纳米粒子,第三溶剂包括主要溶剂和次要溶剂,主要溶剂是一种水或乙醇,次要溶剂是乙二醇,其中,第三溶液的浓度范围约为3%~20%。在一些实施例中,可以使用其他方式将第三溶液涂布于振膜1230上,例如喷洒或刷涂或其他方法处理。烘烤已涂布有第三溶液的振膜1230(步骤1404),借由至少一种挥发和热解的方式挥发或热解第三溶剂以留下第三溶液中的氟化纳米粒子在振膜1230上。例如,可以使用烘焙设备(图中未示)烘烤已涂布有第三溶液的振膜1230,其中较好地烘烤温度(℃)大约在60℃~200℃下且持续烘烤10-120分钟。形成一具有氟化纳米粒子的第二纳米涂层于振膜1230上。防尘网1240用来防止外在异物进入振膜1230内,其可以使用纤维材料制成,例如人造纤维或皮革。同时,防尘网1240亦可使用纳米涂层涂布技术。涂布防尘网1240的方法与涂布振膜1230的方法大致相同。在本实施例中,一种涂布防尘网1240的方法描述如下:将防尘网1240放置于装载器(图未示出)上以便于进行后续步骤处理。将防尘网1240置于自动浸泡机中,其中自动浸泡机包括第三溶液,所述第三溶液包括第三溶质与第三溶剂,第三溶质为氟化纳米粒子,第三溶剂包括主要溶剂和次要溶剂,主要溶剂是一种水或乙醇,次要溶剂是乙二醇,其中,第三溶液的浓度范围约为3%~20%。在一些实施例中,可以使用其他方式将第三溶液涂布于防尘网1240上,例如喷洒或刷涂或其他方法处理。烘烤已涂布有第三溶液的防尘网1240,借由至少一种挥发和热解的方式留下第三溶液中的氟化纳米粒子在防尘网1240上,例如,可以使用烘焙设备(未示出)烘烤已涂布有第三溶液的防尘网1240,其中较好地烘烤温度(摄氏)在60℃~200℃且持续烘烤10-120分钟。在一些实施例中,第一纳米涂层包括二氧化钛(tio2)纳米粒子与二氧化硅(sio2)纳米粒子,第二纳米涂层包括氟化纳米粒子。以下提供各纳米粒子的粒径尺寸量测结果图。图15a-15c为根据本发明的一实施例以动态光散射方法量测二氧化钛纳米粒子尺寸分布测量结果图。图16为根据本发明的一实施例以穿透式电子显微镜观察二氧化硅纳米粒子尺寸分布测量结果图。图17为根据本发明的一实施例以穿透式电子显微镜观察氟化纳米粒子尺寸分布测量结果图。图15a-15c的量测结果显示,二氧化钛粒子的主要粒径尺寸分布约为32~36nm范围内,次要粒径尺寸分布约为110~220nm范围内。图16的量测结果显示二氧化硅纳米粒子粒径尺寸分布约为1~2.5nm范围内(平均1.7±0.4nm)。图17的量测结果显示氟化纳米粒子粒径尺寸分布约为50~100nm范围内(平均72±21nm)。氟化纳米粒子可以是全氟酯或全氟酯改性的矽氧烷。为了确认纳米涂层是否会影响电声装置的声音品质,故进行一些测试实验,以了解涂布纳米涂层之前与之后的电声装置表现。请参考图18,图中所示为比较两组防尘网分别为具有第二纳米涂层(右侧)与未具有第二纳米涂层(左侧)的水滴在其上的表现图。两组防尘网皆为纤维材质,第一组防尘网未涂布具有氟化纳米粒子的第二纳米涂层,当水滴落入在防尘网上时,会将防尘网弄湿。第二组防尘网则涂布具有氟化纳米粒子的第二纳米涂层,因涂完后使防尘网表面具有疏水性,故水滴在表面上仍为水珠状。此两组防尘网另组装成电声装置进行声音表现测试,测试结果如表七所示:表七、两组防尘网比较结果请参考图19到图22,测验为了确认纳米涂层是否会影响电声装置的声音表现,故进行频率响应(fr)和总谐波失真(thd)的实验。此实验中使用两个相同的电声装置进行比较,每一个电声装置至少包括一印刷电路板组件、一振膜和一防尘网,其中一个电声装置的元件未涂布任何纳米涂层,另一个电声装置分别在印刷电路板组件上涂布第一纳米涂层,在振膜上涂布第二纳米涂层以及在防尘网上涂布第二纳米涂层。实验中,将两个电声装置分别播放声音,并进行频率响应(fr)和总谐波失真(thd)的测试。频率响应(fr)测试结果如图19与图20所示,从图19中可以观察出涂布纳米涂层后的电声装置在频率响应测验中没有受到影响,再由图20中可以观察得知频率响应差值两者发生变化最大的是高频段区域(10k~14khz)但仅有约2~4db的差值。总谐波失真(thd)测试结果如图21与图22所示,从图21中可以观察出涂布纳米涂层后的电声装置在总谐波失真测验中没有受到影响,再由图22中可以观察得知总谐波失真差值两者仅有约0.2%的变化。前面所述概括了几个实施例的特征,使得本领域技术人员可更好地理解本发明的各个方面。本领域技术人员应该明白他们可以将本发明当作基础,用来设计或修改用于执行相同目的和/或获得在此介绍的实施例的相同好处的其他过程和结构。本领域技术人员也可意识到这样等同的构造并不脱离本发明的精神和保护范围,并且在不脱离本发明的精神和保护范围的情况下,他们可以在此做各种改变、替换和修改。当前第1页12