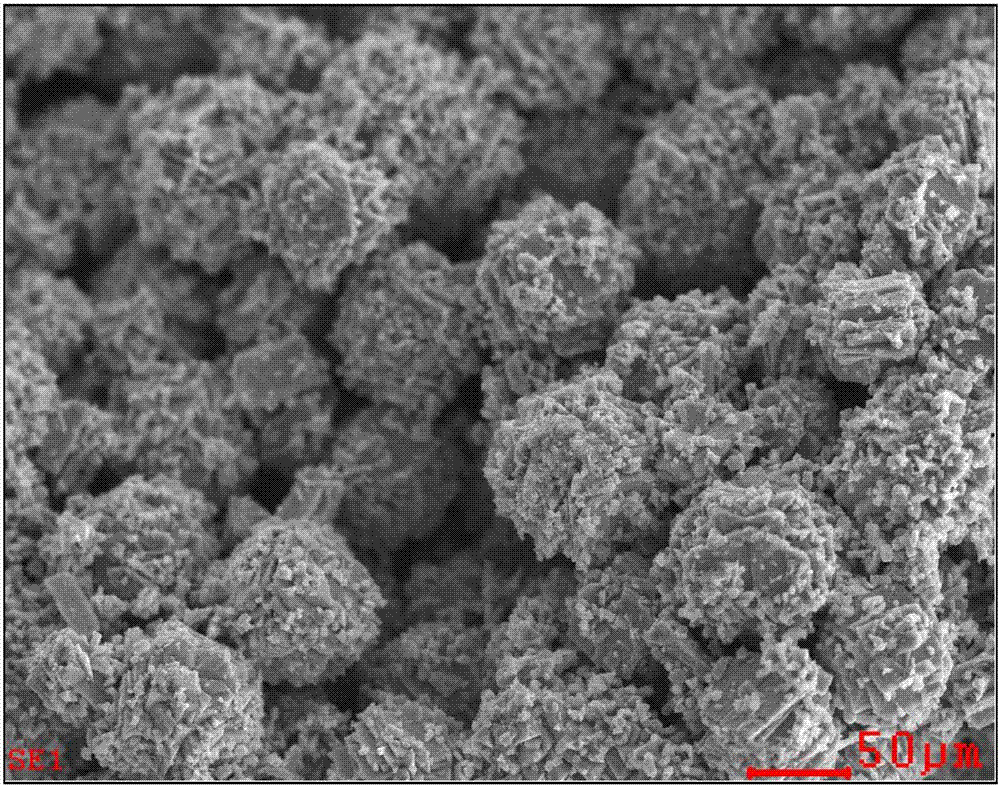
本发明属于催化剂
技术领域:
,具体涉及一种用于合成三羟甲基丙烷酯的催化剂及其制备方法。
背景技术:
:三羟甲基丙烷酯是一种重要的新戊基多元醇酯。三羟甲基丙烷酯由于季碳原子的β位上没有氢原子,可与羟基氧形成六元环共振结构,所以具有良好的氧化安定性、热稳定性、低温流动性和黏温性能等,已广泛用于航空润滑油、汽车润滑剂、空气压缩机油和抗燃液压油等领域。目前合成三羟甲基丙烷酯的主要工艺是酯化反应工艺,其催化剂有硫酸、磷酸等无机所、甲苯磺酸等有机酸,路易斯酸催化剂和固体超强酸催化剂等。随着对环境和能耗要求的日益严苛,产品性能的进一步提升,因而,对酯化反应所用的催化剂的要求也越来越高,因固体催化剂具有易于处理等优势,在酯化反应中应用广泛。但是目前的固体催化剂存在催化反应活性相对较低,催化剂用量相对较多,酯化反应时间长,催化剂处理难,产品性质提高难度大等问题。技术实现要素:有鉴于此,本发明要解决的技术问题在于提供一种用于合成三羟甲基丙烷酯的催化剂及其制备方法,本发明提供的用于合成三羟甲基丙烷酯的催化剂在进行酯化反应时催化剂用量少且活性相对较高,酯化反应时间短,反应结束后催化剂易于处理,得到的三羟甲基丙烷酯性能能够满足指标要求。本发明提供了一种用于合成三羟甲基丙烷酯的催化剂,所述催化剂为snxalyoz的复合催化剂,其中,x=4~6,y=1~2,z=5~8。本发明还提供了一种用于合成三羟甲基丙烷酯的催化剂的制备方法,包括以下步骤:a)将氯化亚锡、氯化铝和碳酸钠在溶剂存在的条件下进行加热反应,过滤洗涤后,得到前驱体;b)将所述前驱体在氮气气氛下焙烧,得到用于合成三羟甲基丙烷酯的催化剂。优选的,所述氯化亚锡、氯化铝和碳酸钠的摩尔比为(5~8):(1~3):(6.5~13.5)。优选的,所述溶剂选自乙醇或甲醇。优选的,所述加热反应的温度为40~70℃。优选的,所述焙烧的温度为260~400℃,所述焙烧的时间为12~24小时。优选的,所述洗涤为采用甲醇或乙醇洗涤,洗涤至无氯元素残留。本发明还提供了一种三羟甲基丙烷酯的制备方法,包括以下步骤:将三羟甲基丙烷与脂肪酸混合,在催化剂存在的条件下进行酯化反应,得到三羟甲基丙烷酯;所述脂肪酸选自c5~c7的脂肪酸中的一种或多种;所述催化剂选自权利要求1所述的催化剂或权利要求2~7中任意一项制备方法制备得到的催化剂。优选的,还包括酯化反应结束后,将得到的产物进行过滤,得到过滤物;将所述过滤物在甲醇/石油醚溶液中浸泡后焙烧,得到催化剂,所述催化剂为用于合成三羟甲基丙烷酯的催化剂。优选的,所述三羟甲基丙烷酯的羟值低于1.0mgkoh/g。与现有技术相比,本发明提供了一种用于合成三羟甲基丙烷酯的催化剂,所述催化剂为snxalyoz的复合催化剂,其中,x=4~6,y=1~2,z=5~8。本发明提供的snxalyoz复合催化剂为负载型的锡类催化剂,该催化剂催化三羟甲基丙烷酯的反应时用量少且活性相对较高,酯化反应时间短,反应结束后催化剂易于处理,得到的三羟甲基丙烷酯性能能够满足指标要求。结果表明,本发明负载的催化剂,催化合成三羟甲基丙烷酯,酯化率可达99.6%以上,催化剂可以重复使用3次以上,在本发明酯化反应的合成实施过程中,几乎不产生液废和固废。按本发明合成的三羟甲基丙烷酯的油品性能满足指标要求,通过gjb563腐蚀和氧化安定性实验,gb/t264的油品粘度试验,gb/t7304测试产品的酸值,均能满足指标要求,通过gb/t6540测试油品的色度不大于2,并进行油品的加速氧化试验,80℃,7天酸值增加不大于0.5mgkoh/g。gb/t17476测试油品的元素残留量。附图说明图1为实施例1制备的用于合成三羟甲基丙烷酯的催化剂能谱图;图2为实施例1制备的用于合成三羟甲基丙烷酯的催化剂扫描电镜图;图3为实施例1制备的用于合成三羟甲基丙烷酯的催化剂经过两次循环使用后的能谱图;图4为实施例1制备的用于合成三羟甲基丙烷酯的催化剂经过两次循环使用后的扫面电镜图。具体实施方式本发明提供了一种用于合成三羟甲基丙烷酯的催化剂,所述催化剂为snxalyoz催化剂,其中,x=4~6,y=1~2,z=5~8。其中,所述催化剂为氧化亚锡和氧化铝的复合型锡类催化剂,即snxalyoz催化剂,其中,x=4~6,y=1~2,z=5~8,用于催化合成三羟甲基丙烷酯。该催化剂催化三羟甲基丙烷酯的反应时用量少且活性相对较高,酯化反应时间短,反应结束后催化剂易于处理,得到的三羟甲基丙烷酯性能能够满足指标要求。本发明还提供了一种用于合成三羟甲基丙烷酯的催化剂的制备方法,包括以下步骤:a)将氯化亚锡、氯化铝和碳酸钠在溶剂存在的条件下进行加热反应,过滤洗涤后,得到前驱体;b)将所述前驱体在氮气气氛下焙烧,得到用于合成三羟甲基丙烷酯的催化剂。本发明首先将氯化亚锡、氯化铝和碳酸钠在溶剂存在的条件下进行加热反应。其中,所述氯化亚锡、氯化铝和碳酸钠的摩尔比为(5~8):(1~3):(6.5~13.5),优选为(6~7):(1.5~2.5):(8~12)。所述溶剂选自乙醇或甲醇。所述加热反应的温度为40~70℃,优选为50~60℃。所述加热反应为共沉淀反应,反应合成了碳酸亚锡和铝的混合物,所述碳酸亚锡和铝的混合物为沉淀,将所述沉淀过滤后洗涤,得到前驱体。本发明对所述过滤的方法没有特殊限制,本领域技术人员公知的过滤方法即可。将过滤后得到的滤饼进行洗涤,所述洗涤为采用甲醇或乙醇洗涤,洗涤至无氯元素残留。得到前驱体后,将所述前驱体在氮气气氛下焙烧,通过原位法得到用于合成三羟甲基丙烷酯的催化剂。所述焙烧的温度优选为260~400℃,更优选为300~350℃;所述焙烧的时间为12~24小时,更优选为16~20小时。本发明还提供了一种采用上述制备方法制备得到的用于合成三羟甲基丙烷酯的催化剂。本发明还提供了一种三羟甲基丙烷酯的制备方法,包括以下步骤:将三羟甲基丙烷与脂肪酸混合,在催化剂存在的条件下进行酯化反应,得到三羟甲基丙烷酯。所述催化剂选自上述催化剂或上述制备方法制备得到的催化剂。其中,所述脂肪酸选自c5~c7的脂肪酸中的一种或多种,优选为庚酸、辛酸和壬酸形成的混合酸。所述酯化反应的温度在210℃以下,反应时间优选为3~7小时。最终得到粗酯样品,所述粗酯样品再经固体碱吸附、过滤,所得产物酸值低于0.05mgkoh/g,并且具有更加优异的外观、储存安定性和抗氧化性能。在本发明中,所述酯化反应结束后,优选将得到的产物进行过滤,得到过滤物;将所述过滤物在甲醇/石油醚溶液中浸泡后焙烧,得到催化剂,所述催化剂为用于合成三羟甲基丙烷酯的催化剂。其中,所述甲醇/石油醚的体积比优选为1:3,所述浸泡时间优选为24小时,所述焙烧的温度优选,200~220℃,所述焙烧的环境为氮气气氛。焙烧后得到的催化剂可以重复用于三羟甲基丙烷酯的制备,重复使用的次数可以为5次以上,优选为2~5次。在本发明的一些具体实施方式中,所述催化剂循环使用3次后,得到的三羟甲基丙烷酯的羟值依然低于1.0mgkoh/g。本发明提供催化剂为snxalyoz的复合催化剂,其中,x=4~6,y=1~2,z=5~8。为负载型的锡类催化剂,该催化剂催化三羟甲基丙烷酯的反应时用量少且活性相对较高,酯化反应时间短,反应结束后催化剂易于处理,得到的三羟甲基丙烷酯性能能够满足指标要求。结果表明,本发明负载的催化剂,催化合成三羟甲基丙烷酯,酯化率可达99.6%以上,催化剂可以重复使用3次以上,在本发明酯化反应的合成实施过程中,几乎不产生液废和固废。按本发明合成的三羟甲基丙烷酯的油品性能满足指标要求,通过gjb563腐蚀和氧化安定性实验,gb/t264的油品粘度试验,gb/t7304测试产品的酸值,均能满足指标要求,通过gb/t6540测试油品的色度不大于2,并进行油品的加速氧化试验,80℃,7天酸值增加不大于0.5mgkoh/g。gb/t17476测试油品的元素残留量。为了进一步理解本发明,下面结合实施例对本发明提供的用于合成三羟甲基丙烷酯的催化剂及其制备方法以及应用进行说明,本发明的保护范围不受以下实施例的限制。实施例1以摩尔比为7:2:13的氯化亚锡、氯化铝和碳酸钠为原料,乙醇为溶剂,室温至40℃下,采用共沉淀的方法合成了碳酸亚锡和铝混合物,将上述混合物进行过滤,乙醇洗涤充分,滤饼至无氯元素残留。滤饼再于400℃,氮气气氛下焙烧24小时,冷却至室温,用于合成三羟甲基丙烷酯的催化剂。对上述催化剂进行电镜扫描和能谱测试,结果见图1、表1和图2,图1为实施例1制备的用于合成三羟甲基丙烷酯的催化剂的能谱图。表1为实施例1制备的用于合成三羟甲基丙烷酯的催化剂能谱结果。表1实施例1制备的用于合成三羟甲基丙烷酯的催化剂能谱结果elementwt%at%ck01.8806.59ok21.8957.56alk01.1601.80sk06.3708.36snl66.7923.68cak01.9102.01matrixcorrectionzaf图2为实施例1制备的用于合成三羟甲基丙烷酯的催化剂的扫描电镜图。实施例2以摩尔比为5:1:7的氯化亚锡、氯化铝和碳酸钠为原料,乙醇为溶剂,50℃下,采用共沉淀的方法合成了碳酸亚锡和铝混合物,将上述混合物进行过滤,乙醇洗涤滤饼,至无氯元素残留。滤饼再于260℃,氮气气氛下焙烧24小时,冷却至室温,用于合成三羟甲基丙烷酯的催化剂。对上述催化剂进行如实施例1的测试,得到与实施例1相似的结果。实施例3以摩尔比为8:3:10的氯化亚锡、氯化铝和碳酸钠为原料,乙醇为溶剂,55℃下,采用共沉淀的方法合成了碳酸亚锡和铝混合物,将上述混合物进行过滤,乙醇洗涤滤饼,至无氯元素残留。滤饼再于350℃,氮气气氛下焙烧20小时,冷却至室温,用于合成三羟甲基丙烷酯的催化剂。对上述催化剂进行如实施例1的测试,得到与实施例1相似的结果。实施例4将不同配比的三羟甲基丙烷与脂肪酸(摩尔比为1:2:1的庚酸、辛酸和壬酸形成的混合酸)混合,以实施例1制备的催化剂为催化剂,在不同的温度和时间以及不同催化剂含量的条件下进行酯化反应,得到三羟甲基丙烷酯。具体反应条件和结果见表3。按照实施例4编号4的反应条件进行酯化反应后,将得到的产物进行处理,处理方法为:将得到的产物过滤,得到过滤物;将所述过滤物在体积比为1:3的甲醇/石油醚溶液中浸泡24小时后在220℃的条件下焙烧,得到催化剂。将上述经过处理后的催化剂第二次在实施例4编号4的条件下进行催化反应后,接着再按照上述方法进行处理,循环上述催化以及产物处理的过程2次。将经过2次循环使用的催化剂经过回收处理后,对其进行sem和能谱测试,结果见图3、表2和图4,图3为实施例1制备的用于合成三羟甲基丙烷酯的催化剂经过两次循环使用后的能谱图。表2为实施例1制备的用于合成三羟甲基丙烷酯的催化剂经过两次循环使用后的能谱结果。表2实施例1制备的用于合成三羟甲基丙烷酯的催化剂经过两次循环使用后的能谱结果图4为实施例1制备的用于合成三羟甲基丙烷酯的催化剂经过两次循环使用后的扫面电镜图。对比例1将不同配比的三羟甲基丙烷与脂肪酸(摩尔比为1:2:1的庚酸、辛酸和壬酸形成的混合酸)混合,以草酸亚锡为催化剂,在不同的温度和时间以及不同催化剂含量的条件下进行酯化反应,得到三羟甲基丙烷酯。具体反应条件和结果见表3。表3不同催化剂对酯化反应的活性表3中,n(三羟):n(脂肪酸)为三羟甲基丙烷与脂肪酸的摩尔比。催化剂及用量中的“用量”指催化剂的用量占三羟甲基丙烷与脂肪酸总质量的百分比由表3可知,脂肪酸过量的情况下,草酸亚锡和锡类催化剂均可以使三羟甲基丙烷酯酯化完全,羟值较低,满足酯化要求。实施例5将不同配比的三羟甲基丙烷与脂肪酸(摩尔比为1:2:1的庚酸、辛酸和壬酸形成的混合酸)混合,以实施例1制备的催化剂为催化剂,在反应温度210℃的条件下进行酯化反应7小时,得到三羟甲基丙烷酯。具体反应条件和结果见表4。表4不同原料配比得到的产物的酸值表4中,n(脂肪酸):n(三羟)为脂肪酸与三羟甲基丙烷的摩尔比。实施例6将摩尔比为1:3.5的三羟甲基丙烷与脂肪酸(摩尔比为1:2:1的庚酸、辛酸和壬酸形成的混合酸)混合,以实施例1制备的催化剂为催化剂,在不同的反应温度条件下进行酯化反应7小时,得到三羟甲基丙烷酯。具体反应条件和结果见表5。表5不同反应温度得到的产物的酸值实施例7将摩尔比为1:3.5的三羟甲基丙烷与脂肪酸(摩尔比为1:2:1的庚酸、辛酸和壬酸形成的混合酸)混合,以实施例1制备的催化剂为催化剂,在不同催化剂用量,210℃的反应温度条件下进行酯化反应7小时,得到三羟甲基丙烷酯。具体反应条件和结果见表6。表6不同催化剂用量得到的产物的酸值表6中,催化剂用量mcat:m总指催化剂用量与三羟甲基丙烷与脂肪酸总量的百分比。实施例8将实施例1制备得到的催化剂在实施例7编号3的条件下进行催化反应后,将得到的产物进行处理,处理方法为:将得到的产物过滤,得到过滤物;将所述过滤物在体积比为1:3的甲醇/石油醚溶液中浸泡24小时后在220℃的条件下焙烧,得到催化剂。将上述经过处理后的催化剂第二次在实施例7编号3的条件下进行催化反应后,测定产物的酸值以及酯化率。接着再按照上述方法进行处理,循环上述催化以及产物处理的过程4次。测定不同循环次数产物的酸值和酯化率,结果见表7,表7为不同循环次数条件下产物的酸值以及酯化率。表7不同循环次数条件下产物的酸值以及酯化率循环次数粗酯酸值mgkoh/g酯化率%1010020.299.9630.499.9340.9299.82实施例9将实施例7中编号2得到的粗品三羟甲基丙烷酯经固体碱吸附、过滤得到精制的三羟甲基丙烷酯,测定精制的三羟甲基丙烷酯的性能,结果见表6。对比例2按照实施例7编号2的制备方法,仅将催化剂改变为硫酸催化剂体系,得到粗品三羟甲基丙烷酯;将得到的粗品三羟甲基丙烷酯按照实施例9的方法经固体碱吸附、过滤得到精制的三羟甲基丙烷酯,测定精制的三羟甲基丙烷酯的性能,结果见表8。表8不同催化合成的三羟甲基丙烷酯(5102)性能的比较通过gjb563腐蚀和氧化安定性实验,gb/t264的油品粘度试验,gb/t7304测试产品的酸值,均能满足指标要求,通过gb/t6540测试油品的色度不大于2,并进行油品的加速氧化试验,80℃,7天酸值增加不大于0.5mgkoh/g。gb/t17476测试油品的元素残留量。以上所述仅是本发明的优选实施方式,应当指出,对于本
技术领域:
的普通技术人员来说,在不脱离本发明原理的前提下,还可以做出若干改进和润饰,这些改进和润饰也应视为本发明的保护范围。当前第1页12