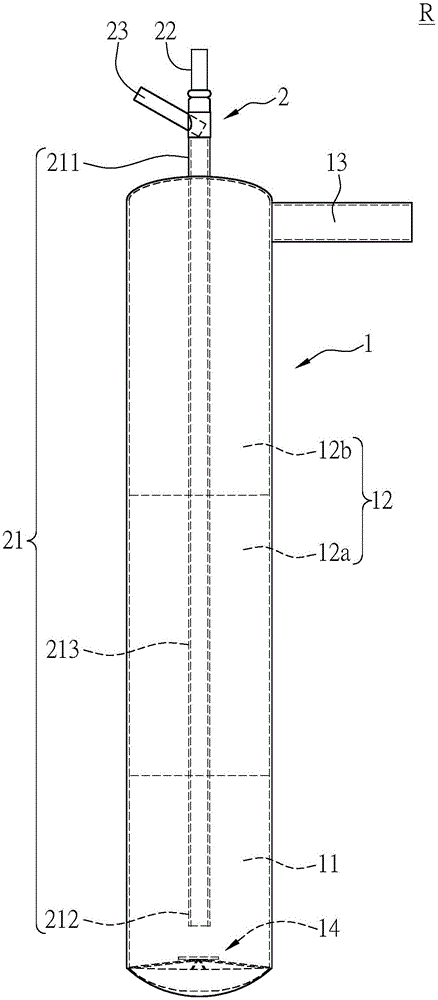
本发明涉及一种废有机溶剂的处理方法及装置,特别是涉及一种废有机溶剂的燃料化方法及装置和模块化反应器。
背景技术:
:有机溶剂因为其挥发性及溶解特性(能溶解一些不溶于水的物质)而有很广的用途。有机溶剂在生活中随处可见,例如,有机溶剂可以被用来制作涂料、黏着剂、清洁剂等。此外,有机溶剂也被使用于各种产业领域,例如,光电与半导体产业所使用的光阻剥离液、晶圆的清洗液与金属材料的表面处理液中都包含了有机溶剂。有机溶剂的优点固然很多,但若没有妥善处理废有机溶剂,其将会通过挥发、渗透等作用进入大气、地表及地下水中,且被动植物、人体所吸收,造成严重的环境污染与人体健康的损害。于是,便有了废有机溶剂的处置方法(如回收及处理方法)。然而,废有机溶剂在开始进行处置之前,需经过一些前处理步骤来除去干扰物质,这些前处理步骤通常会使用到大量的清水,因而存在二次污染的风险,且会增加处置的成本。直接焚化法、触媒焚化法及吸附法都是目前常用的废有机溶剂的处置方法,其各有优缺点。例如,直接焚化法虽然效率很高,且可回收热,但是此法危险性也较高,且不适用于处理卤化有机溶剂。相较之下,触媒焚化法虽然可在较低温的条件下分解有机溶剂,且同样可回收热,但是此法有触媒中毒的问题,且需考虑触媒的成本。吸附法虽能处理低浓度的有机溶剂,但是此法在回收操作上较麻烦,且吸附床的再生处理会产生污水问题。技术实现要素:本发明所要解决的技术问题在于,针对现有技术的不足提供一种废有机溶剂的燃料化方法及装置和模块化反应器。为了解决上述的技术问题,本发明所采用的其中一技术方案是:一种模块化反应器,用于利用废有机溶剂来生成气体燃料,所述模块化反应器包括一反应腔体以及一进料组件。所述反应腔体具有一气化区段以及至少一位于所述气化区段上方的反应区段。所述进料组件包括一输送管、一进气接头以及一进液接头,所述输送管具有一位于所述反应腔体外的第一端部以及一位于所述反应腔体内的第二端部,所述进气接头与所述进液接头均连接于所述第一端部,所述第二端部连通于所述气化区段。所述进气接头的延伸方向与所述第一端部的延伸方向相同,所述进液接头的延伸方向与所述第一端部的延伸方向不同。其中,所述进气接头用于导入一输送气体,以产生一从所述进液接头向所述输送管的所述第一端部的吸引力,以将一废有机溶剂从所述进液接头导入。在本发明的一实施例中,所述反应腔体为直立式,所述输送管具有一位于所述第一端部与所述第二端部之间的主体部,且所述主体部穿过所述反应区段而延伸至所述气化区段,以将被导入的所述废有机溶剂输送至所述气化区段进行气化。在本发明的一实施例中,所述气化区段内设置有一相对于所述输送管的所述第二端部的承接台,以接触被输送至所述气化区段的所述废有机溶剂。在本发明的一实施例中,所述进液接头相对于所述进气接头呈倾斜设置。在本发明的一实施例中,所述进液接头与所述进气接头呈垂直设置。在本发明的一实施例中,所述反应腔体为水平式,所述输送管具有一位于所述第一端部与所述第二端部之间的主体部,且所述主体部设置于所述气化区段内,以将被导入的所述废有机溶剂输送至所述气化区段进行气化。在本发明的一实施例中,所述反应腔体包括至少一设置于所述反应区段与所述气化区段之间的阻隔结构。在本发明的一实施例中,所述反应腔体具有一连接于所述反应区段的出料接头。为了解决上述的技术问题,本发明所采用的另外一技术方案是:一种废有机溶剂的燃料化装置,其使用上述的模块化反应器。为了解决上述的技术问题,本发明所采用的再一技术方案是:一种废有机溶剂的燃料化方法,其包括:将一输送气体导入一反应腔体,并通过所述输送气体所产生的一吸引力将一废有机溶剂导入所述反应腔体;将所述废有机溶剂气化,以形成一气相反应物;以及在缺氧及高温环境下对所述气相反应物进行热裂解。在本发明的一实施例中,在导入所述废有机溶剂的步骤之前,还包括:利用所述输送气体将氧气排出所述反应腔体外,以使所述反应腔体内的氧气含量不超过1%体积。在本发明的一实施例中,在导入所述废有机溶剂的步骤之中,所述输送气体与所述废有机溶剂的体积比为27.7至1000。在本发明的一实施例中,在进行热裂解的步骤之中,所述反应腔体的温度介于500至1200k之间。在本发明的一实施例中,所述输送气体为氮气或氩气,所述废有机溶剂为异丙醇或氢氧化四甲基铵。本发明的其中一有益效果在于,本发明所提供的模块化反应器,其能通过“进气接头与进液接头均连接于输送管的第一端部,其中进气接头的延伸方向与第一端部的延伸方向相同,进液接头的延伸方向与第一端部的延伸方向不同”的技术方案,以利用输送气体所产生的吸引力将废有机溶剂导入输送管,且随着输送气体进入反应腔体,从而反应生成气体燃料。本发明的另外一有益效果在于,本发明所提供的废有机溶剂的燃料化装置,其将多个模块化反应器串联在一起(即使用模块化反应器),可以一次处理更大量的废有机溶剂,且可以实现气体燃料的大规模连续化生产。本发明的再一有益效果在于,本发明所提供的废有机溶剂的燃料化方法,其能通过“将输送气体导入反应腔体,并通过输送气体所产生的吸引力将废有机溶剂导入反应腔体”的技术方案,以解决废有机溶剂的处理问题,同时产生再生能源。为使能更进一步了解本发明的特征及技术内容,请参阅以下有关本发明的详细说明与附图,然而所提供的附图仅用于提供参考与说明,并非用来对本发明加以限制。附图说明图1为本发明第一实施例的模块化反应器的整体结构示意图。图2为本发明第一实施例的模块化反应器的其中一顶部结构示意图。图3为本发明第一实施例的模块化反应器的另外一顶部结构示意图。图4为本发明第一实施例的模块化反应器的底部结构示意图。图5为本发明的废有机溶剂的燃料化装置的结构示意图。图6为本发明的废有机溶剂的燃料化方法的流程图。图7为本发明第二实施例的模块化反应器的整体结构示意图。图8显示本发明实施例的模块化反应器的反应腔体的其中一种内部设计。图9显示本发明实施例的模块化反应器的反应腔体的另外一种内部设计。图10显示本发明实施例的模块化反应器的反应腔体的再一种内部设计。图11显示本发明实施例的模块化反应器的反应腔体的又一种内部设计。具体实施方式由于废有机溶剂大多具有毒性,其不仅会危害人体的健康,还会对环境造成污染。此外,废有机溶剂的处理也是一大难题。为此原因,本发明提供了废有机溶剂的解决方案,用于将废有机溶剂转化成无毒性的气体燃料,而气体燃料可用来发电。也就是说,本发明在解决日益严重的废有机溶剂的处理问题的同时,可另外产生再生能源,兼具环保与能源效益。以下是通过特定的具体实施例来说明本发明所公开有关“废有机溶剂的燃料化装置及燃料化方法与其模块化反应器”的实施方式,本领域技术人员可由本说明书所公开的内容了解本发明的优点与效果。本发明可通过其他不同的具体实施例加以施行或应用,本说明书中的各项细节也可基于不同观点与应用,在不悖离本发明的构思下进行各种修改与变更。另外,本发明的附图仅为简单示意说明,并非依实际尺寸的描绘,事先声明。以下的实施方式将进一步详细说明本发明的相关技术内容,但所公开的内容并非用以限制本发明的保护范围。第一实施例请参阅图1,本发明提供一种模块化反应器r,其可利用废有机溶剂来生成气体燃料。模块化反应器r实际上可为一流化床反应器或一固定床反应器,但不受限于此。模块化反应器r包括一反应腔体1及一进料组件2。在反应器的设计上,进料组件2能利用一输送气体来驱使废有机溶剂进入反应腔体1,反应腔体1先将有机溶剂气化(gasification),再将气相有机溶剂热裂解(pyrolysis),以得到气体燃料。废有机溶剂可为含有碳氢化合物的有机溶剂,其具体可举出:醇类、醇醚类、酯类及芳烃类等,但不受限于此。废有机溶剂的来源主要为半导体厂、化学工厂等。若以得到甲烷气体为目标,废有机溶剂优选为异丙醇(ipa)或氢氧化四甲基铵(tmah)。另外,输送气体可为氮气或惰性气体(如氩气),但不受限于此。在本实施例中,反应腔体1为直立式,反应腔体1具有一气化区段11及至少一位于气化区段11上方的反应区段12,其中反应区段12连接一出料接头13。废有机溶剂进入反应腔体1后,会先在气化区段11被加热气化,气相有机溶剂(气相反应物)再往上流动至反应区段12进行热裂解。从出料接头13回收生成物,再进行分离纯化,便可以得到所需的气体燃料。需要说明的是,反应区段12的数量可视废有机溶剂所需要的裂解反应的次数而定,例如,针对废异丙醇,反应区段12可进一步区分为第一反应区段12a(初级反应区段)及位于第一反应区段12a上方的第二反应区段12b(二次反应区段)。如此,异丙醇气体可先在第一反应区段12a中反应生成丙酮与氢气或生成丙烷与水,其中丙酮可继续在第二反应区段12b中反应生成甲烷与烯酮。为使异丙醇较倾向反应生成丙酮与氢气,第一反应区段12a的温度可优选为500至1200,更优选为775k。在此温度下,生成丙酮的速率为生成丙烷的速率的14倍。另外,为防止模块化反应器r发生爆炸,在废有机溶剂进入反应腔体1之前,可利用输送气体将氧气排出反应腔体1外,以形成缺氧环境,反应腔体1内的氧气含量不超过1%体积。也就是说,气相有机溶剂是在缺氧及高温环境下进行热裂解。另外,为提高废有机溶剂的转化率,在进料时的输送气体与废有机溶剂的体积比可优选为27.7至1000。请参阅图2及图3,进料组件2包括一输送管21、一进气接头22及一进液接头23,输送管21具有一第一端部211、一第二端部212及一位于第一端部211与第二端部212之间的主体部213。其中第一端部211位于反应腔体1外,且进气接头22与进液接头23均连接于第一端部211。第二端部212位于反应腔体1内,且连通于气化区段11。主体部213穿过反应区段12而延伸至气化区段11。值得注意的是,进气接头22的延伸方向与第一端部211的延伸方向相同,进液接头23的延伸方向与第一端部211的延伸方向不同。例如,进液接头23可相对于进气接头22呈倾斜设置(如图2所示),或者,进液接头23可与进气接头22呈垂直设置(如图3所示)。如此,当输送气体经过第一端部211时,进液接头23内部与外界大气压力会存在一压力差,也就是说,进液接头23内部的压力小于外界大气压力。在此压力差的作用下,可以产生一进气接头22向第一端部211的吸引力,以驱使废有机溶剂从进气接头22进入输送管21,而后随着输送气体进入反应腔体1的气化区段11。请参阅图2及图3,为避免在反应过程中出现气体或液体倒流的现象,可以在进气接头22上安装一气体逆止阀221,并在进液接头23上安装一液体逆止阀231。请参阅图4,为使被输送气体带入的废有机溶剂能够完全气化,模块化反应器r还包括一辅助气化组件14,其设置于反应腔体1的气化区段11。辅助气化组件14包括一承接台141及一导热结构142,承接台141与导热结构142可为高导热金属(如铝、铜等)所制成,但不受限于此。其中导热结构142固设在气化区段11底部,导热结构142可包括多个呈放射状排列的导热片(未标号),但不受限于此。承接台141固设在导热结构142上,且相对于输送管21的第二端部212。如此,导热结构142可以提高气化区段11中的温度分布均匀性,且废有机溶剂一旦进入气化区段11,就会立即接触到承接台141而充分受热。请参阅图5,并配合图1,本发明还提供一种废有机溶剂的燃料化装置d,其将多个模块化反应器r串联在一起,以一次处理更大量的废有机溶剂,并且,可以实现气体燃料的大规模连续化生产。具体来说,前面的模块化反应器r的出料接头13可通过一管线p与后面的模块化反应器r的进料组件2的进气接头22连通。如此,即便前面的模块化反应器r的气体流出物中仍有未反应的气相有机溶剂(如异丙醇气体)与气相中间产物(如丙酮气体),这些气相有机溶剂与气相中间产物可进入后面的模块化反应器r继续进行热裂解反应,而得到最终产物(如甲烷气体)。请参阅图6,本发明还提供一种废有机溶剂的燃料化方法,其包括:步骤s100,将输送气体导入反应腔体,并通过输送气体所产生的吸引力将废有机溶剂导入反应腔体;步骤s102,将废有机溶剂气化,以形成一气相反应物;及步骤s104,在缺氧及高温环境下对气相反应物进行热裂解。在本实施例中,可优选在导入废有机溶剂之前,利用输送气体将氧气排出反应腔体外,以使反应腔体内的氧气含量不超过1体积%。在导入废有机溶剂时,输送气体与废有机溶剂的体积比可优选为27.7至1000。在进行热裂解时,反应腔体的温度可优选为500至1200,更优选为775k。第二实施例请参阅图7,本实施例提供一种模块化反应器r,其包括一反应腔体1及一进料组件2。本实施例的不同之处在于,反应腔体1为水平式,以克服一些设置场所的限制,例如本实施例之模块化反应器r可固定在厂房天花板上使用。在本实施例中,反应腔体1具有一气化区段11、至少一位于气化区段11上方的反应区段12及至少一设置于气化区段11与反应区段12之间的阻隔结构15,其中阻隔结构15用于使气相有机溶剂(气相产物)从气化区段11沿着一预定路径流动至反应区段12。阻隔结构15可为一不透气的隔板,但不受限于此。阻隔结构15上可形成有一气体流道结构(图中未显示)。进料组件2包括一输送管21、一进气接头22及一进液接头23,输送管21具有一第一端部211、一第二端部212及一位于第一端部211与第二端部212之间的主体部213。其中第一端部211位于反应腔体1外,且进气接头22与进液接头23均连接于第一端部211,主体部213与第二端部212均位于气化区段11内。值得注意的是,进气接头22的延伸方向与第一端部211的延伸方向相同,进液接头23的延伸方向与第一端部211的延伸方向相不同。如此,在反应腔体1为水平式的架构下,进料组件2也能利用一输送气体来驱使废有机溶剂进入反应腔体1。虽然在图7中,进料组件2所包括的进液接头23相对于进气接头22呈倾斜设置,但是根据不同的需要,进液接头23也可与进气接头22呈垂直设置。第三实施例请参阅图8至图11,本实施例提供多种不同的反应腔体1的内部设计如下。首先,如图8所示,反应腔体1内包括多个不透气隔板3、多个透气载板4、多个触媒载体5、至少一不透气的挡墙6及多个感应线圈7。具体来说,多个不透气隔板3相互错开设置,以形成一气体流动路径f。多个透气载板4设置于气体流动路径f上,且多个透气载板4各承载一触媒载体5。触媒载体5为一体式结构,且为金属丝(如铂或铂合金丝)所构成,触媒载体5具有特定废有机溶剂进行热裂解反应所需的触媒。挡墙6围绕不透气隔板3、透气载板4与触媒载体5,多个感应线圈7设置于挡墙6的外侧,用于快速加热至反应所需的温度。或者,如图9及图10所示,在此等设计中,触媒载体5为堆栈式结构,也就是说,触媒载体5为多个触媒载体单元5a堆栈而成。多个触媒载体单元5a可以靠透气载板4支撑(如图9所示),或在气体流动路径f上相互支撑(如图10所示)。或者,如图11所示,触媒载体5可进一步区分为第一触媒载体51及第二触媒载体52,第一触媒载体51与第二触媒载体52均为一体式结构,其中第一触媒载体51的密度高于第二触媒载体52的密度,也就是说,第一触媒载体51在每单位面积上有更多的金属丝。实施例的有益效果本发明的其中一有益效果在于,本发明所提供的模块化反应器,其能通过“进气接头与进液接头均连接于输送管的第一端部,其中进气接头的延伸方向与第一端部的延伸方向相同,进液接头的延伸方向与第一端部的延伸方向不同”的技术方案,以利用输送气体所产生的吸引力将废有机溶剂导入输送管,且随着输送气体进入反应腔体,进而反应生成气体燃料。如下表一所示,在进料组件以180ml/min的进料流率将异丙醇(60wt%)导入反应腔体的条件下,使用傅立叶变换红外线光谱仪(ftir)检测热裂解反应,在最低检测下限(l.d.l)2950ppm下未测出异丙醇成分(n.d.)。由此可知,利用模块化反应器将废有机溶剂转化成气体燃料,其转化率可以达到99%以上。表一成分浓度(重量%)最低检测下限(ppm)ipan.d.2950ch434.9286co21.13423本发明所提供的废有机溶剂的燃料化装置,其将多个模块化反应器串联在一起(即使用模块化反应器),可以一次处理更大量的废有机溶剂,且可以实现气体燃料的大规模连续化生产。本发明所提供的废有机溶剂的燃料化方法,其能通过“将输送气体导入反应腔体,并通过输送气体所产生的吸引力将废有机溶剂导入反应腔体”的技术方案,以解决废有机溶剂的处理问题,同时产生再生能源。以上所公开的内容仅为本发明的优选可行实施例,并非因此局限本发明的权利要求书的保护范围,因此凡运用本发明说明书及附图内容所做的等效技术变化,均包含于本发明的权利要求书的保护范围内。当前第1页12