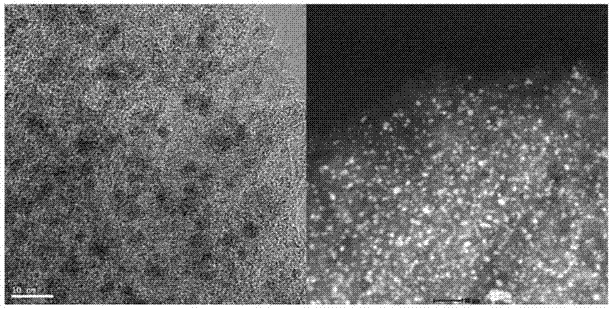
本发明属于化工催化剂
技术领域:
,具体涉及一种氮掺杂炭负载金属催化剂及其制备方法和在苯环加氢反应中的应用。
背景技术:
:苯、甲苯的苯环加氢产物环己烷、环己基甲烷已被广泛用于各种有机原料和医药化工中间体的制备中。环己基甲酸是一种重要的有机合成中间体,可用于合成抗孕392药物和治疗吸虫新药吡喹酮,其衍生物如反式-4-异丙基环己甲酸是生产治疗糖尿病新药那格列奈的中间体。对苯二甲酸二甲酯(dmt)苯环加氢生成的1,4-环己基二甲酸二甲酯(dmcd),是很有价值的化学中间体,不仅可单独作为聚合物的改性材料,而且在涂料方面也有很大的用途,可以进一步加氢制备作为多种高性能聚酯材料单体的1,4-环己烷二甲醇(chdm),用于生产具有良好热稳定性和热塑性的聚酯树脂;此外在化妆品包装、医用容器、食品容器、显示器、文具和日用品反面均有广泛应用。目前苯环加氢反应主要通过贵金属催化剂催化,由于贵金属价格昂贵,一般采用载体负载少量贵金属的方式制备催化剂。而炭材料因高比表面积、孔隙结构发达、价格低廉等优势而成为贵金属催化剂最常用的载体,但是,炭材料由于本身一些稳定的化学性质,导致其表面活性低,所以需要进行改性,而氮掺杂是一种普遍有效的炭改性手段,制备氮掺杂炭负载金属催化剂以提高催化活性是目前研究的热点。掺杂氮原子可以改变载体表面的酸碱性质,增强金属与载体之间的相互作用,加速催化体系中的电子转移,从而实现对炭负载金属纳米结构及性能的调控。公布号为cn107413331a的专利文献公开了一种氮掺杂活性炭负载贵金属催化剂,所述催化剂由载体氮掺杂的活性炭和活性组分组成,其制备方法包括:先将活性炭预处理,再将配制好的氮源溶液与预处理后的活性炭混合打浆,得到活性炭浆液,水热处理后得到氮掺杂活性炭;将氮掺杂活性炭负载活性组分金属盐溶液,得到氮掺杂活性炭负载贵金属催化剂。所述的传统氮掺杂炭负载金属催化剂的制备方法需要添加额外的氮源,以及相应的混合工序,其制备方法复杂,会浪费大量资源,不适合大量生产。刘杰等[chinesejournalofcatalysis,2018,39,1664-1671.]研究了以小麦粉为原料,先通过直接炭化法制备了氮掺杂中孔成型炭,再制备haucl4水溶液,将haucl4水溶液滴加到载体中孔成型炭中,混合均匀后老化12h并在120℃下干燥12h,制备了小麦粉衍生中孔氮掺杂颗粒炭负载金催化剂。所述的制备方法复杂,炭化处理后还需要进行后续还原处理,同时金粒子经过后续处理负载在载体上,会使得金粒子易流失,影响催化剂的催化活性。技术实现要素:本发明的目的在于提供一种直接将小麦粉与金属盐混合后炭化制备氮掺杂炭负载金属催化剂的方法,其简化了制备步骤,提高了催化剂的催化活性,将制得的催化剂应用于苯环加氢领域,表现出了极好的催化活性和选择性。本发明的具体技术方案如下:一种氮掺杂炭负载金属催化剂的制备方法,包括以下步骤:步骤1:将小麦粉和金属盐混合后进行研磨,再以和面的方式加水捏成团状,在室温下放置10~14h,得到样品;或将小麦粉进行研磨,再以和面的方式加入金属盐的水溶液捏成团状,在室温下放置10~14h,得到样品;步骤2:将步骤1得到的样品在100~120℃条件下进行预炭化;步骤3:将步骤2得到的预炭化样品放入管式炉中,在流动的惰性气氛下,升温至500~900℃,再保温2~4h进行深度炭化处理,最后在惰性气氛下吹扫,自然冷却至室温,即得氮掺杂炭负载金属催化剂。本发明方法选用天然含高氮含量的小麦粉作为载体的前驱体,无需添加额外的氮源,炭化后氮元素可以均匀地分布在催化剂中;此外,一般负载型催化剂采用后负载金属前驱体再经还原的方法,而本发明方法直接将小麦粉与金属盐混合后,采用原位炭化法使得金属在炭化过程中便得到还原,省去了后续还原的步骤,简化了制备步骤,同时还产生了一种金属纳米粒子镶嵌在炭载体上的结构,使得金属不易流失并增强了相互作用,进一步提高了催化剂的催化活性。本发明先采用固相研磨的方式将金属盐与其他前驱体混合,其混合均匀程度受一些因素影响较大,如不同金属盐的性状(硬度、易受潮程度等),研磨手法差异等,而混合不均匀会导致影响金属在催化剂中的分散度,造成部分金属离子的聚集,影响催化剂性能。因此,本发明还采用了液相浸渍的混合方式,将金属盐加入到原本所需的水中配制成溶液,以和面的方式完成混合,固液混合的方式可以有效提高混合的均匀程度,间接有益于催化剂性能。步骤1中,所述的金属盐为氯化钌、醋酸钌、硝酸钌、羰基钌、氯化钯、氯铂酸、硝酸钴、氯金酸中的任意一种或多种。步骤1中,以小麦粉的吸水量和所需的金属负载量为依据,小麦粉、金属盐和水的质量比为1:0.007~0.08:0.4~0.6。步骤3中,以1~5℃/min的升温速率升温。步骤3中,惰性气氛为n2,he,ar中的任意一种。优选地,所述步骤1中加入模板剂一起进行研磨,还包括步骤4:将步骤3得到的炭化后样品用氢氧化钠-乙醇-水混合溶液浸泡除去模板剂,洗涤干燥后即得氮掺杂炭负载金属催化剂。苯环加氢反应的反应底物分子尺寸较大,中孔结构有利于底物在催化剂表面的扩散从而加快催化速率,因此使用模板剂制备具有中孔结构的催化剂;此外,模板剂为纳米球状,与前驱体小麦粉混合后经炭化处理,其表面被炭材料所包覆,经步骤4将模板剂清除后,炭材料产生中孔结构。所述的模板剂为纳米球状的二氧化硅。模板剂量过多在除模板后会造成炭材料坍塌,为确保模板剂不影响炭材料骨架结构而同时尽可能多造中孔,所述的模板剂与小麦粉的质量比为1:3~7,进一步优选为1:5~6。综合除模板效果和成本的考虑,所述浸泡时间为20~240min,进一步优选为60~120min,浸泡温度为40~90℃,进一步优选为60~80℃。所述氢氧化钠-乙醇-水混合溶液中氢氧化钠、乙醇和水的质量比为1:15~35:10~30。本发明还公开了一种由上述方法制备得到的氮掺杂炭负载金属催化剂,所述的氮掺杂炭负载金属催化剂的金属负载量为0.5%~5%,其中,金属负载量为金属占催化剂的质量比。本发明还公开了一种上述氮掺杂炭负载金属催化剂在苯环加氢反应中的应用。苯环加氢反应主要涉及苯及其简单衍生物,如苯、甲苯、苯甲酸和对苯二甲酸二甲酯(dmt)等芳香族化合物,其中,苯、甲苯的苯环加氢产物环己烷、环己基甲烷已被广泛用于各种有机原料和医药化工中间体的制备中。本发明与现有技术相比,具有以下有益效果:(1)本发明方法采用天然含高氮含量的小麦粉作为炭源和氮源,原料价廉易得,在合成过程中避免了复杂的氮元素引入步骤,操作简单,容易大量生产;(2)本发明方法直接将小麦粉与金属盐进行混合,再通过原位炭化法得到氮掺杂炭负载金属催化剂,催化剂后续无需进行还原活化处理,省去了后续还原操作,简化了制备步骤,有效节约了成本,提高了催化剂的催化活性;(3)本发明方法制备得到的催化剂可应用于苯环加氢反应领域,所得到的催化剂具有很好的催化活性和选择性。附图说明图1为实施例2所制备的氮掺杂钌炭催化剂的tem图。具体实施方式以下实施例是为了使本行业人员更详细地理解本发明的内容做出一些非本质的改进和调整,但是本发明的范围不受这些实施例的限制。实施例1称取15g小麦粉和0.24g三氯化钌作为钌源,一并加入研钵中,研磨2h,之后采用和面的手法加水7.8g将其捏成团,室温放置12h;再将样品放入110℃的鼓风干燥箱内预炭化12h,之后将样品置于管式炉中,惰性气氛下进行850℃深度炭化3h(240min从30℃升温到850℃,保持3h),得到钌负载量为2wt%的氮掺杂钌炭催化剂。实施例2称取3.33g纳米二氧化硅作为模板,称取15g小麦粉,0.24g三氯化钌作为钌源,一并加入研钵中,研磨2h,之后采用和面的手法加水7.8g将其捏成团,室温放置12h;再将样品放入110℃的鼓风干燥箱内预炭化12h,之后将样品置于管式炉中,惰性气氛下进行850℃深度炭化3h(240min从30℃升温到850℃,保持3h),炭化后取部分样品研磨成细颗粒,使用氢氧化钠的醇溶液(质量比naoh:c2h5oh:h2o=1:25:20)进行除模板两次,处理条件为70℃水浴2h。抽滤,洗涤,干燥后得到钌负载量为2wt%的氮掺杂钌炭催化剂。制备得到的氮掺杂钌炭催化剂的tem图如图1所示。实施例3称取3.33g纳米二氧化硅作为模板,与15g小麦粉一并加入研钵中,研磨2h;将0.24g三氯化钌溶于7.8g水中,采用和面的手法将氯化钌溶液加入上述混合物中并捏成团,室温放置12h;再将样品放入110℃的鼓风干燥箱内预炭化12h,之后将样品置于管式炉中,惰性气氛下进行850℃深度炭化3h(240min从30℃升温到850℃,保持3h),炭化后取部分样品研磨成细颗粒,使用氢氧化钠的醇溶液(质量比naoh:c2h5oh:h2o=1:25:20)进行除模板两次,处理条件为70℃水浴2h。抽滤,洗涤,干燥后得到钌负载量为2wt%的氮掺杂钌炭催化剂。实施例4称取3.33g纳米二氧化硅作为模板,与15g小麦粉一并加入研钵中,研磨2h;将1.17g硝酸钴溶于7.8g水中,采用和面的手法将氯化钌溶液加入上述混合物中并捏成团,室温放置12h;再将样品放入110℃的鼓风干燥箱内预炭化12h,之后将样品置于管式炉中,惰性气氛下进行850℃深度炭化3h(240min从30℃升温到850℃,保持3h),炭化后取部分样品研磨成细颗粒,使用氢氧化钠的醇溶液(质量比naoh:c2h5oh:h2o=1:25:20)进行除模板两次,处理条件为70℃水浴2h。抽滤,洗涤,干燥后得到钴负载量为5wt%的氮掺杂钴炭催化剂。对比例称取市售椰壳活性炭hy-12g作为载体,将1.08g三氯化钌溶于2.4ml水中,逐滴浸渍到上述载体中,室温放置12h;再放入120℃的鼓风干燥箱中处理12h,之后将样品在流量为30ml/min的h2气氛下,400℃还原2h,即可得到钌负载量为2wt%的ru/ac催化剂。应用例将实施例1~4和对比例中得到的催化剂用于催化苯环加氢反应,并利用反应物转化率和对目标产物选择性对催化剂的催化效率进行评价。应用的具体步骤为:先分别将0.4g苯甲酸、20mg催化剂和25ml去离子水投料到配有磁转子的50ml反应釜中;再将反应釜在120℃的油浴条件下用恒温磁力搅拌器进行搅拌,并将釜内的气体用纯氢气置换3次,待温度恒定在120℃后,转速调到1000rpm,通入氢气,反应1h后结束,最后取出反应原料和各产物,采用气相色谱进行检测,按照面积归一化法计算混合物各物质的百分含量。实施例1~4和对比例中得到的催化剂的评价结果见下表1,由表1可知,与未掺氮的对比例相比,实施例的反应物转化率均有所提高;而与实施例1相比,添加模板剂的实施例2和3在转化率和选择性上均有明显提高,同时采用固液浸渍混合的实施例3转化率要优于以固相研磨混合的实施例2;实施例4的转化率最高,这主要与其钴负载量为5wt%,其他实施例钌负载量只有2wt%有关。表1反应物转化率/%目标产物选择性/%实施例136.6687.17实施例257.1597.13实施例365.9397.93实施例482.7297.46对比例28.1490.31当前第1页12