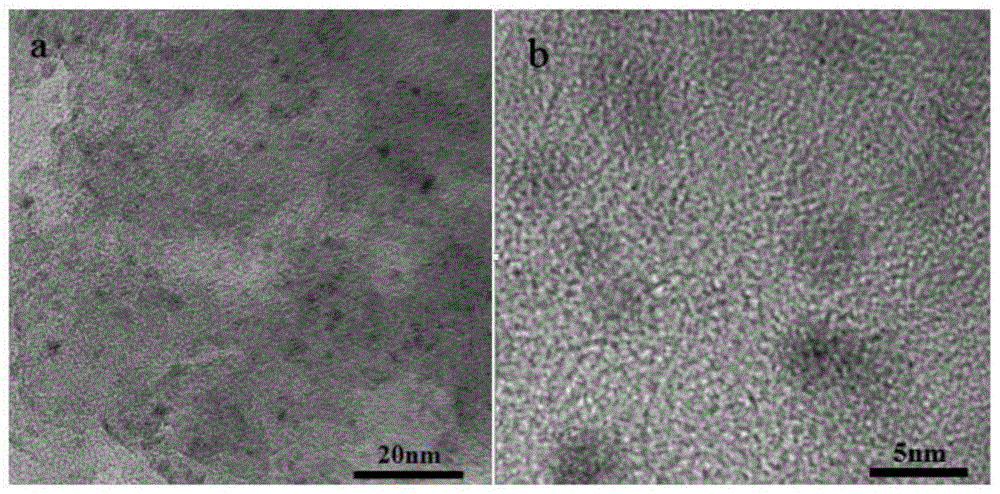
本发明属于催化剂的制备领域,具体涉及一种碳氮掺杂二氧化硅负载pt催化剂及其制备方法和应用。
背景技术:
:根据iupac(国际纯粹与应用化学联合会)定义,多孔材料可以分为微孔材料、介孔材料和大孔材料。微孔材料是指孔径小于2nm的材料,介孔材料是指孔径介于2~50nm的材料,大孔材料是指孔径大于50nm的材料。介孔氧化硅材料由于具有较大的比表面积和合适的孔径,因此在吸附、分离、催化等领域拥有广阔的应用前景。为了进一步改善介孔氧化硅材料在这些方面的应用,通常将杂原子(如b、c、n、al等)或含杂原子的基团(氨基、环氧烷基、咪唑基等)掺杂到介孔氧化硅中加入,使介孔氧化硅材料的各项性能大大提高。梁等人(“梁继芬,张晓明,景铃胭,etal.氮掺杂有序介孔碳负载超小尺寸铂纳米颗粒催化硝基苯类化合物选择加氢(英文)[j].催化学报,2017(07):163-171.”),利用软模板(嵌段共聚物f127为模板),以间氨基苯酚为碳源和氮前体,制备出较高含氮量和比表面积,以及规则孔径分布的介孔碳材料。但该负载型贵金属催化剂存在成本昂贵、结构稳定性差的缺点。技术实现要素:鉴于此,本发明提供了一种碳氮掺杂二氧化硅负载pt催化剂及其制备方法和应用。本发明提供的碳氮掺杂二氧化硅负载pt催化剂原料易得,成本低廉,结构稳定好。为了实现上述发明目的,本发明提供了以下技术方案:本发明提供了一种碳氮掺杂二氧化硅负载pt催化剂,包括以碳氮掺杂的二氧化硅为载体和负载在所述载体表面的pt,由包括以下组分的原料制备得到:二氧化硅、碳源、氮源、可溶性pt盐、乙醇溶液和水。优选地,所述碳源为氨基葡萄糖盐酸盐;所述氮源为三聚氰胺或尿素。优选地,所述二氧化硅、碳源和氮源的质量比为(1~10):(1~6):(1~9)。优选地,所述可溶性pt盐以水溶液的形式加入,所述水溶液中pt的浓度为0.0085g/ml~0.085g/ml。本发明还提供了上述技术方案所述碳氮掺杂二氧化硅负载pt催化剂的制备方法,包括以下步骤:将二氧化硅、碳源、氮源和乙醇水溶液混合后,在保护气氛下煅烧,得到碳氮掺杂的二氧化硅载体;将所述碳氮掺杂的二氧化硅载体、可溶性pt盐和水混合后,在氢气条件下焙烧,得到所述碳氮掺杂二氧化硅负载pt催化剂。优选地,所述煅烧依次包括第一煅烧和第二煅烧,所述第一煅烧的温度为500~650℃,保温时间为1~3h,所述第二煅烧的温度为800~900℃,保温时间为1~3h。优选地,升温至所述第一煅烧的温度和第二煅烧的温度的升温速率独立地为2~4℃/min。优选地,所述焙烧的温度为200~300℃,保温时间为3~4h。优选地,升温至所述焙烧的温度的升温速率为2~3℃/min。本发明还提供了上述技术方案所述碳氮掺杂二氧化硅负载pt催化剂或由上述技术方案所述制备方法制得的碳氮掺杂二氧化硅负载pt催化剂在芳香类硝基化合物的催化反应中的应用。本发明提供了一种碳氮掺杂二氧化硅负载pt催化剂,包括以碳氮掺杂的二氧化硅为载体和负载在所述载体表面的pt,由包括以下组分的原料制备得到:二氧化硅、碳源、氮源、可溶性pt盐、乙醇溶液和水。本发明通过掺杂碳源有效地提高了二氧化硅载体的热稳定性,进而提高碳氮掺杂二氧化硅负载pt催化剂(pt/sio2-cn)的结构稳定性,使pt/sio2-cn能多次循环利用;通过掺杂氮元素来抑制pt/sio2-cn中pt颗粒的长大,使pt在催化剂中分散更均匀,从而极大提高pt/sio2-cn的催化反应活性。实施例结果表明,本发明制得的pt/sio2-cn具有良好的结构稳定性,对芳香类硝基化合物的催化反应具有超高的催化活性和选择性,9次循环使用后,转化率>95.2%,选择性>99%。进一步地,本发明提供的制备方法工艺简单,原料易得,成本低廉,环保。附图说明下面结合附图和具体实施方式对本发明作进一步详细的说明。图1为实施例1~2制得的pt/sio2-cn的sem图,其中,a为实施例1制得的pt/sio2-cn的sem图,b为实施例2制得的pt/sio2-cn的sem图。具体实施方式本发明提供了一种碳氮掺杂二氧化硅负载pt催化剂,包括以碳氮掺杂的二氧化硅为载体和负载在所述载体表面的pt,由包括以下组分的原料制备得到:二氧化硅、碳源、氮源、可溶性pt盐、乙醇溶液和水。在本发明中,所述碳源优选为氨基葡萄糖盐酸盐;所述氮源优选为三聚氰胺或尿素。在本发明中,所述二氧化硅优选包括mcm-41,sba-15,mcm-48或kit-6,所述二氧化硅的孔径优选为2nm~50nm,进一步优选为8~10nm。在本发明中,所述二氧化硅、碳源和氮源的质量比为(1~10):(1~6):(1~9),进一步优选为(3~8):(1~4):(2~7),更优选为5:1:3。在本发明中,所述二氧化硅和可溶性pt盐中pt的质量比为1:0.005~0.08,进一步优选为1:0.01~0.06,更优选为1:0.02~0.04。本发明采用特定用量的氨基葡萄糖盐酸盐作为碳源,不仅可以使后续氮源更易引入,还可以有效地提高二氧化硅载体的热稳定性,进而提高pt/sio2-cn的结构稳定性,使pt/sio2-cn能多次循环利用。本发明采用特定用量的三聚氰胺或尿素作为氮源,能够有效地抑制pt/sio2-cn中pt颗粒的长大,使pt在催化剂中分散更均匀,从而极大提高pt/sio2-cn的催化反应活性。且本发明采用的碳源和氮源易得,成本低廉,环保。在本发明中,所述pt/sio2-cn中碳含量优选为2.5wt%~10wt%,进一步优选为4wt%~8wt%,更优选为5wt%,氮含量优选为1.8wt%~5.6wt%,进一步优选为2wt%~5wt%,更优选为2.5wt%。在本发明中,所述可溶性pt盐优选为氯铂酸,所述可溶性pt盐优选以水溶液的形式加入,所述水溶液中pt的浓度为0.0085g/ml~0.085g/ml,进一步优选为0.02~0.06g/ml,更优选为0.03~0.04g/ml。在本发明中,所述pt/sio2-cn中pt的含量优选为0.1wt%~10wt%,进一步优选为1wt%~6wt%,更优选为2wt%。在本发明中,所述乙醇溶液中乙醇的质量百分含量优选为40~60%,进一步优选为45~55%,更优选为50%。在本发明中,所述水优选为去离子水。在本发明中,若无特殊说明,所采用的原料均为本领域常规市售产品。本发明还提供了上述技术方案所述碳氮掺杂二氧化硅负载pt催化剂的制备方法,包括以下步骤:将二氧化硅、碳源、氮源和乙醇水溶液混合后,在保护气氛下煅烧,得到碳氮掺杂的二氧化硅载体;将所述碳氮掺杂的二氧化硅载体、可溶性pt盐和水混合后,在氢气条件下焙烧,得到所述碳氮掺杂二氧化硅负载pt催化剂。本发明将所述二氧化硅、碳源、氮源和乙醇水溶液混合后,在保护气氛下煅烧,得到碳氮掺杂的二氧化硅载体。在本发明中,所述混合优选在水浴条件下进行,所述水浴的温度优选为40~80℃,时间优选为50℃。在本发明中,所述混合的方式优选为搅拌。本发明对所述搅拌的条件没有特殊的限定,能够满足将混合后的物料蒸干即可。混合完成后,本发明优选将混合得到的物料进行干燥后,再在保护气氛下煅烧。在本发明中,所述干燥的温度优选为100~120℃,时间优选为8~12h。本发明对所述干燥的具体操作方式没有特殊的限定,采用本领域技术人员熟知的干燥方式即可。本发明通过将原料依次进行混合和干燥,使碳源和氮源均匀分散在二氧化硅孔道中,经过后续煅烧过程后,将碳氮掺杂在二氧化硅上。在本发明中,所述煅烧依次优选包括第一煅烧和第二煅烧,所述第一煅烧的温度优选为500~650℃,进一步优选为600℃,保温时间优选为1~3h;所述第二煅烧的温度优选为800~900℃,进一步优选为850℃,保温时间优选为1~3h;至所述第一煅烧的温度和第二煅烧的温度的升温速率独立地优选为2~4℃/min。在本发明中,所述保护气氛优选为氮气。本发明通过分段煅烧使碳源和氮源均匀地掺杂在二氧化硅上。得到碳氮掺杂的二氧化硅载体后,本发明将所述碳氮掺杂的二氧化硅载体、可溶性pt盐和水混合后,在氢气条件下焙烧,得到所述碳氮掺杂二氧化硅负载pt催化剂。在本发明中,所述混合优选在水浴条件下进行,所述水浴的温度优选为40~80℃,时间优选为40℃。在本发明中,所述混合的方式优选为搅拌。本发明对所述搅拌的条件没有特殊的限定,能够满足将混合后的物料蒸干即可。在本发明中,所述焙烧的温度优选为200~300℃,进一步优选为200℃,保温时间优选为3~4h;升温至所述焙烧的温度的升温速率优选为2~3℃/min。本发明通过焙烧,将可溶性pt盐还原为pt负载在碳氮掺杂二氧化硅上。本发明还提供了上述技术方案所述碳氮掺杂二氧化硅负载pt催化剂或上述技术方案所述制备方法制得的碳氮掺杂二氧化硅负载pt催化剂在芳香类硝基化合物的催化反应中的应用。在本发明中,所述催化反应优选在h2气氛中进行,所述h2的压力优选为2~4mpa;所述催化反应的温度优选为70~85℃,时间优选为0.5~1h。下面结合实施例对本发明提供的碳氮掺杂二氧化硅负载pt催化剂及其制备方法和应用进行详细的说明,但是不能把它们理解为对本发明保护范围的限定。实施例1(1)将1g二氧化硅、0.3g氨基葡萄糖盐酸盐和0.6g三聚氰胺,置于50ml质量百分含量为50%的乙醇水溶液中,在60℃条件下水浴搅拌蒸干,之后在100℃条件下干燥12小时,得到固体粉末;(2)将上述步骤中的固体粉末在氮气条件下煅烧,得到碳氮掺杂的二氧化硅载体;(3)将2.4ml(0.0085g/ml)氯铂酸溶液和1g碳氮掺杂的二氧化硅在水溶液中混合均匀,于50℃条件下水浴搅拌蒸干,得到的固体在氢气气氛下焙烧,即得到目标催化剂pt/sio2-cn,其中pt在pt/sio2-cn中的含量为2%。步骤(2)中的煅烧温度为先升温到550℃,保温2h,然后升温到900℃,保温1h,升温速率为3℃/min。步骤(3)中的焙烧温度为200℃,焙烧时间为3h,升温速率为2℃/min。对pt/sio2-cn的结构稳定性能进行测试(1)称取20mg催化剂,2g4-氯硝基苯,20ml乙醇,置于高压反应釜中,在h2压力为2mpa,反应温度为70℃条件下,反应0.5h。(2)收集步骤(1)中的催化剂,用于第2次循环,对于损耗的少量催化剂则进行补加新的催化剂。(3)重复步骤(2),直至循环到第9次,每次补加新的催化剂的用量为损失多少补多少,保证每次都是20mg催化剂即可。(4)计算每次循环过程中pt/sio2-cn对芳香类硝基化合物的催化反应转化率和选择性,结果参见表1。称取15mgpt/sio2-cn,2g4-氯硝基苯和20ml乙醇,置于高压反应釜中,在h2压力为2mpa,反应温度为85℃条件下,反应0.5h后,计算对芳香类硝基化合物的催化反应转化率和选择性,结果参见表2。表1实施例1制得的pt/sio2-cn对芳香类硝基化合物的催化反应转化率和选择性结果循环次数转化率(%)选择性(%)195.399.98295.399.95395.299.96495.399.93595.399.94695.299.95795.399.96895.299.97995.299.96上述实验结果表明,本发明制得的pt/sio2-cn使用9次后仍有高催化性能,说明本发明制得的pt/sio2-cn具有稳定的结构,可多次循环利用。实施例2(1)将1gsba-15、2g氨基葡萄糖盐酸盐和6g尿素,置于50ml质量百分含量为50%的乙醇水溶液中,在80℃条件下水浴搅拌蒸干,之后在100℃条件下干燥12小时,得到固体粉末;(2)将上述步骤中的固体粉末,在氮气条件下煅烧,得到碳氮掺杂的二氧化硅载体;(3)将2.4ml(0.0085g/ml)氯铂酸溶液和1g碳氮掺杂的二氧化硅在水溶液中混合均匀,于50℃条件下水浴搅拌蒸干,得到的固体在氢气气氛下焙烧,即得到目标催化剂pt/sio2-cn,其中pt在pt/sio2-cn中的含量为1%。步骤(2)中的煅烧温度先升温到600℃,保温1h,然后升温到800℃,保温5h,升温速率为3℃/min。步骤(3)中的焙烧温度为200℃,焙烧时间为3h,升温速率为2℃/min。称取15mgpt/sio2-cn,2g4-氯硝基苯和20ml乙醇,置于高压反应釜中,在h2压力为2mpa,反应温度为85℃条件下,反应0.5h后,计算对芳香类硝基化合物的催化反应转化率和选择性,结果参见表2。图1为实施例1~2制得的pt/sio2-cn的sem图,其中a为实施例1制得的pt/sio2-cn的sem图,b为实施例2制得的pt/sio2-cn的sem图。从图中可以看出,pt在pt/sio2-cn中分散均匀。实施例3(1)将1gmcm-41、1g氨基葡萄糖盐酸盐和3g尿素,置于50ml质量百分含量为50%的乙醇水溶液中,在80℃条件下水浴搅拌蒸干,之后在100℃条件下干燥12小时,得到固体粉末;(2)将上述步骤中的固体粉末,在氮气条件下煅烧,得到碳氮掺杂的二氧化硅载体;(3)将2.4ml(0.0085g/ml)氯铂酸溶液和1g碳氮掺杂的二氧化硅在水溶液中混合均匀,于50℃条件下水浴搅拌蒸干,得到的固体在氢气气氛下焙烧,即得到目标催化剂pt/sio2-cn。步骤(2)中的煅烧温度先升温到600℃,保温1h,然后升温到900℃,保温1h,升温速率为3℃/min。步骤(3)中的焙烧温度为200℃,焙烧时间为3h,升温速率为2℃/min。称取15mgpt/sio2-cn,2g4-氯硝基苯和20ml乙醇,置于高压反应釜中,在h2压力为2mpa,反应温度为85℃条件下,反应0.5h后,计算对芳香类硝基化合物的催化反应转化率和选择性,结果参见表2。实施例4(1)将1g二氧化硅、0.3g氨基葡萄糖盐酸盐和0.6g三聚氰胺,置于50ml质量百分含量为50%的乙醇水溶液中,在60℃条件下水浴搅拌蒸干,之后在100℃条件下干燥12小时,得到固体粉末;(2)将上述步骤中的固体粉末在氮气条件下煅烧,得到碳氮掺杂的二氧化硅载体;(3)将2.4ml(0.0085g/ml)氯铂酸溶液和1g碳氮掺杂的二氧化硅在水溶液中混合均匀,于50℃条件下水浴搅拌蒸干,得到的固体在氢气气氛下焙烧,即得到目标催化剂pt/sio2-cn。步骤(2)中的煅烧温度先升温到500℃,保温2h,升温速率为3℃/min。步骤(3)中的焙烧温度为200℃,焙烧时间为3h,升温速率为2℃/min。称取15mgpt/sio2-cn,2g4-氯硝基苯和20ml乙醇,置于高压反应釜中,在h2压力为2mpa,反应温度为85℃条件下,反应0.5h后,计算对芳香类硝基化合物的催化反应转化率和选择性,结果参见表2。实施例5(1)将1g二氧化硅、0.3g氨基葡萄糖盐酸盐和0.6g三聚氰胺,置于50ml质量百分含量为50%的乙醇水溶液中,在60℃条件下水浴搅拌蒸干,之后在100℃条件下干燥12小时,得到固体粉末;(2)将上述步骤中的固体粉末在氮气条件下煅烧,得到碳氮掺杂的二氧化硅载体;(3)将2.4ml(0.0085g/ml)氯铂酸溶液和1g碳氮掺杂的二氧化硅在水溶液中混合均匀,于50℃条件下水浴搅拌蒸干,得到的固体在氢气气氛下焙烧,即得到目标催化剂pt/sio2-cn。步骤(2)中的煅烧温度先升温到550℃,保温2h,然后升温到900℃,保温1h,升温速率为3℃/min。步骤(3)中的焙烧温度为100℃,焙烧时间为3h,升温速率为2℃/min。称取15mgpt/sio2-cn,2g4-氯硝基苯和20ml乙醇,置于高压反应釜中,在h2压力为2mpa,反应温度为85℃条件下,反应0.5h后,计算对芳香类硝基化合物的催化反应转化率和选择性,结果参见表2。实施例6(1)5g二氧化硅、1g氨基葡萄糖盐酸盐和3g三聚氰胺,置于50ml质量百分含量为50%的乙醇水溶液中,在60℃条件下水浴搅拌蒸干,之后在100℃条件下干燥12小时,得到固体粉末;(2)将上述步骤中的固体粉末在氮气条件下煅烧,得到碳氮掺杂的二氧化硅载体;(3)将2.4ml(0.03g/ml)氯铂酸溶液和1g碳氮掺杂的二氧化硅在水溶液中混合均匀,于50℃条件下水浴搅拌蒸干,得到的固体在氢气气氛下焙烧,即得到目标催化剂pt/sio2-cn。步骤(2)中的煅烧温度先升温到500℃,保温2h,然后升温到900℃,保温1h,升温速率为4℃/min。步骤(3)中的焙烧温度为300℃,焙烧时间为3h,升温速率为2℃/min。称取15mgpt/sio2-cn,2g4-氯硝基苯和20ml乙醇,置于高压反应釜中,在h2压力为2mpa,反应温度为85℃条件下,反应0.5h后,计算对芳香类硝基化合物的催化反应转化率和选择性,结果参见表2。实施例7(1)10g二氧化硅、6g氨基葡萄糖盐酸盐和9g三聚氰胺,置于50ml质量百分含量为50%的乙醇水溶液中,在60℃条件下水浴搅拌蒸干,之后在100℃条件下干燥12小时,得到固体粉末;(2)将上述步骤中的固体粉末在氮气条件下煅烧,得到碳氮掺杂的二氧化硅载体;(3)将2.4ml(0.02g/ml)氯铂酸溶液和1g碳氮掺杂的二氧化硅在水溶液中混合均匀,于50℃条件下水浴搅拌蒸干,得到的固体在氢气气氛下焙烧,即得到目标催化剂pt/sio2-cn。步骤(2)中的煅烧温度先升温到500℃,保温2h,然后升温到800℃,保温1h,升温速率为4℃/min。步骤(3)中的焙烧温度为300℃,焙烧时间为3h,升温速率为2℃/min。称取15mgpt/sio2-cn,2g4-氯硝基苯和20ml乙醇,置于高压反应釜中,在h2压力为2mpa,反应温度为85℃条件下,反应0.5h后,计算对芳香类硝基化合物的催化反应转化率和选择性,结果参见表2。实施例8(1)3g二氧化硅、1g氨基葡萄糖盐酸盐和2g三聚氰胺,置于50ml质量百分含量为50%的乙醇水溶液中,在60℃条件下水浴搅拌蒸干,之后在100℃条件下干燥12小时,得到固体粉末;(2)将上述步骤中的固体粉末在氮气条件下煅烧,得到碳氮掺杂的二氧化硅载体;(3)将2.4ml(0.06g/ml)氯铂酸溶液和1g碳氮掺杂的二氧化硅在水溶液中混合均匀,于50℃条件下水浴搅拌蒸干,得到的固体在氢气气氛下焙烧,即得到目标催化剂pt/sio2-cn。步骤(2)中的煅烧温度先升温到500℃,保温2h,然后升温到800℃,保温1h,升温速率为2℃/min。步骤(3)中的焙烧温度为300℃,焙烧时间为3h,升温速率为2℃/min。称取15mgpt/sio2-cn,2g4-氯硝基苯和20ml乙醇,置于高压反应釜中,在h2压力为2mpa,反应温度为85℃条件下,反应0.5h后,计算对芳香类硝基化合物的催化反应转化率和选择性,结果参见表2。实施例9(1)8g二氧化硅、4g氨基葡萄糖盐酸盐和7g尿素,置于50ml质量百分含量为50%的乙醇水溶液中,在60℃条件下水浴搅拌蒸干,之后在100℃条件下干燥12小时,得到固体粉末;(2)将上述步骤中的固体粉末在氮气条件下煅烧,得到碳氮掺杂的二氧化硅载体;(3)将2.4ml(0.03g/ml)氯铂酸溶液和1g碳氮掺杂的二氧化硅在水溶液中混合均匀,于50℃条件下水浴搅拌蒸干,得到的固体在氢气气氛下焙烧,即得到目标催化剂pt/sio2-cn。步骤(2)中的煅烧温度先升温到500℃,保温2h,然后升温到800℃,保温1h,升温速率为2℃/min。步骤(3)中的焙烧温度为300℃,焙烧时间为3h,升温速率为2℃/min。称取15mgpt/sio2-cn,2g4-氯硝基苯和20ml乙醇,置于高压反应釜中,在h2压力为2mpa,反应温度为85℃条件下,反应0.5h后,计算对芳香类硝基化合物的催化反应转化率和选择性,结果参见表2。实施例10(1)1g二氧化硅、1g氨基葡萄糖盐酸盐和1g三聚氰胺,置于50ml质量百分含量为50%的乙醇水溶液中,在60℃条件下水浴搅拌蒸干,之后在100℃条件下干燥12小时,得到固体粉末;(2)将上述步骤中的固体粉末在氮气条件下煅烧,得到碳氮掺杂的二氧化硅载体;(3)将2.4ml(0.085g/ml)氯铂酸溶液和1g碳氮掺杂的二氧化硅在水溶液中混合均匀,于50℃条件下水浴搅拌蒸干,得到的固体在氢气气氛下焙烧,即得到目标催化剂pt/sio2-cn。步骤(2)中的煅烧温度先升温到650℃,保温2h,然后升温到850℃,保温1h,升温速率为2℃/min。步骤(3)中的焙烧温度为300℃,焙烧时间为3h,升温速率为3℃/min。称取15mgpt/sio2-cn,2g4-氯硝基苯和20ml乙醇,置于高压反应釜中,在h2压力为2mpa,反应温度为85℃条件下,反应0.5h后,计算对芳香类硝基化合物的催化反应转化率和选择性,结果参见表2。实施例11(1)11g二氧化硅、7g氨基葡萄糖盐酸盐和10g三聚氰胺,置于50ml质量百分含量为50%的乙醇水溶液中,在60℃条件下水浴搅拌蒸干,之后在100℃条件下干燥12小时,得到固体粉末;(2)将上述步骤中的固体粉末在氮气条件下煅烧,得到碳氮掺杂的二氧化硅载体;(3)将2.4ml(0.085g/ml)氯铂酸溶液和1g碳氮掺杂的二氧化硅在水溶液中混合均匀,于50℃条件下水浴搅拌蒸干,得到的固体在氢气气氛下焙烧,即得到目标催化剂pt/sio2-cn。步骤(2)中的煅烧温度先升温到650℃,保温2h,然后升温到850℃,保温1h,升温速率为2℃/min。步骤(3)中的焙烧温度为300℃,焙烧时间为3h,升温速率为3℃/min。称取15mgpt/sio2-cn,2g4-氯硝基苯和20ml乙醇,置于高压反应釜中,在h2压力为2mpa,反应温度为85℃条件下,反应0.5h后,计算对芳香类硝基化合物的催化反应转化率和选择性,结果参见表2。对比例1以本领域常规市售商业pt/c催化剂(湖北得力新材料有限公司)作为对比例。称取15mg商业pt/c催化剂,2g4-氯硝基苯和20ml乙醇,置于高压反应釜中,在h2压力为2mpa,反应温度为85℃条件下,反应0.5h后,计算对芳香类硝基化合物的催化反应转化率和选择性,结果参见表2。对比例2为比较不同碳源对催化剂性能的影响,以蔗糖为碳源,按照实例1的方法制备了pt/sio2-cn催化剂。称取15mgpt/sio2-cn催化剂(以蔗糖为碳源),2g4-氯硝基苯和20ml乙醇,置于高压反应釜中,在h2压力为2mpa,反应温度为85℃条件下,反应0.5h后,计算对芳香类硝基化合物的催化反应转化率和选择性,结果参见表2。对比例3为比较不同碳源对催化剂性能的影响,以葡萄糖为碳源,按照实例1的方法制备了pt/sio2-cn催化剂。称取15mgpt/sio2-cn催化剂(以葡萄糖为碳源),2g4-氯硝基苯和20ml乙醇,置于高压反应釜中,在h2压力为2mpa,反应温度为85℃条件下,反应0.5h后,计算对芳香类硝基化合物的催化反应转化率和选择性,结果参见表2。对比例4为比较不同氮源对催化剂性能的影响,以单氰胺为氮源,按照实例1的方法制备了pt/sio2-cn催化剂。称取15mgpt/sio2-cn催化剂(以单氰胺为氮源),2g4-氯硝基苯和20ml乙醇,置于高压反应釜中,在h2压力为2mpa,反应温度为85℃条件下,反应0.5h后,计算对芳香类硝基化合物的催化反应转化率和选择性,结果参见表2。对比例5为比较不同氮源对催化剂性能的影响,以双氰胺为氮源,按照实例1的方法制备了pt/sio2-cn催化剂。称取15mgpt/sio2-cn催化剂(以双氰胺为氮源),2g4-氯硝基苯和20ml乙醇,置于高压反应釜中,在h2压力为2mpa,反应温度为85℃条件下,反应0.5h后,计算对芳香类硝基化合物的催化反应转化率和选择性,结果参见表2。对比例6为比较不同氮源对催化剂性能的影响,以二氰二胺为氮源,按照实例1的方法制备了pt/sio2-cn催化剂。称取15mgpt/sio2-cn催化剂(以二氰二胺为氮源),2g4-氯硝基苯和20ml乙醇,置于高压反应釜中,在h2压力为2mpa,反应温度为85℃条件下,反应0.5h后,计算对芳香类硝基化合物的催化反应转化率和选择性,结果参见表2。对比例7(1)11g二氧化硅和7g氨基葡萄糖盐酸盐,置于50ml质量百分含量为50%的乙醇水溶液中,在60℃条件下水浴搅拌蒸干,之后在100℃条件下干燥12小时,得到固体粉末;(2)将上述步骤中的固体粉末在氮气条件下煅烧,得到碳氮掺杂的二氧化硅载体;(3)将2.4ml(0.085g/ml)氯铂酸溶液和1g碳氮掺杂的二氧化硅在水溶液中混合均匀,于50℃条件下水浴搅拌蒸干,得到的固体在氢气气氛下焙烧,即得到目标催化剂pt/sio2-cn。步骤(2)中的煅烧温度先升温到650℃,保温2h,然后升温到850℃,保温1h,升温速率为2℃/min。步骤(3)中的焙烧温度为300℃,焙烧时间为3h,升温速率为3℃/min。称取15mgpt/sio2-cn,2g4-氯硝基苯和20ml乙醇,置于高压反应釜中,在h2压力为2mpa,反应温度为85℃条件下,反应0.5h后,计算对芳香类硝基化合物的催化反应转化率和选择性,结果参见表2。对比例8(1)11g二氧化硅和10g三聚氰胺,置于50ml质量百分含量为50%的乙醇水溶液中,在60℃条件下水浴搅拌蒸干,之后在100℃条件下干燥12小时,得到固体粉末;(2)将上述步骤中的固体粉末在氮气条件下煅烧,得到碳氮掺杂的二氧化硅载体;(3)将2.4ml(0.085g/ml)氯铂酸溶液和1g碳氮掺杂的二氧化硅在水溶液中混合均匀,于50℃条件下水浴搅拌蒸干,得到的固体在氢气气氛下焙烧,即得到目标催化剂pt/sio2-cn。步骤(2)中的煅烧温度先升温到650℃,保温2h,然后升温到850℃,保温1h,升温速率为2℃/min。步骤(3)中的焙烧温度为300℃,焙烧时间为3h,升温速率为3℃/min。称取15mgpt/sio2-cn,2g4-氯硝基苯和20ml乙醇,置于高压反应釜中,在h2压力为2mpa,反应温度为85℃条件下,反应0.5h后,计算对芳香类硝基化合物的催化反应转化率和选择性,结果参见表2。对比例9(1)11g二氧化硅,置于50ml质量百分含量为50%的乙醇水溶液中,在60℃条件下水浴搅拌蒸干,之后在100℃条件下干燥12小时,得到固体粉末;(2)将上述步骤中的固体粉末在氮气条件下煅烧,得到碳氮掺杂的二氧化硅载体;(3)将2.4ml(0.085g/ml)氯铂酸溶液和1g碳氮掺杂的二氧化硅在水溶液中混合均匀,于50℃条件下水浴搅拌蒸干,得到的固体在氢气气氛下焙烧,即得到目标催化剂pt/sio2-cn。步骤(2)中的煅烧温度先升温到650℃,保温2h,然后升温到850℃,保温1h,升温速率为2℃/min。步骤(3)中的焙烧温度为300℃,焙烧时间为3h,升温速率为3℃/min。称取15mgpt/sio2-cn,2g4-氯硝基苯和20ml乙醇,置于高压反应釜中,在h2压力为2mpa,反应温度为85℃条件下,反应0.5h后,计算对芳香类硝基化合物的催化反应转化率和选择性,结果参见表2。表2实施例1~11制得的pt/sio2-cn及对比例1~9的催化剂对芳香类硝基化合物的催化反应转化率和选择性结果催化剂转化率(%)选择性(%)实施例195.399.88实施例293.699.95实施例391.799.93实施例41746.36实施例55590.69实施例610099.99实施例794.499.65实施例895.699.75实施例994.799.86实施例1092.699.78实施例1185.295.57对比例16285.43对比例26487.62对比例37890.59对比例47881.20对比例57682.37对比例68076.49对比例767.485.6对比例865.883.7对比例952.682.6表2实施例1中的转化率和选择性结果为实施例1制得pt/sio2-cn催化剂循环一次后的实验结果。上述实验结果表明,本发明采用的二氧化硅、碳源、氮源之间的用量比对于本发明制得的催化剂的催化性能有重要的影响。本发明制得的pt/sio2-cn相较于商业pt/c催化剂、以其他碳源和氮源制得的pt/sio2-cn催化剂对芳香类硝基化合物的催化反应,具有超高的催化活性和选择性。以上所述仅是本发明的优选实施方式,应当指出,对于本
技术领域:
的普通技术人员来说,在不脱离本发明原理的前提下,还可以做出若干改进和润饰,这些改进和润饰也应视为本发明的保护范围。当前第1页12