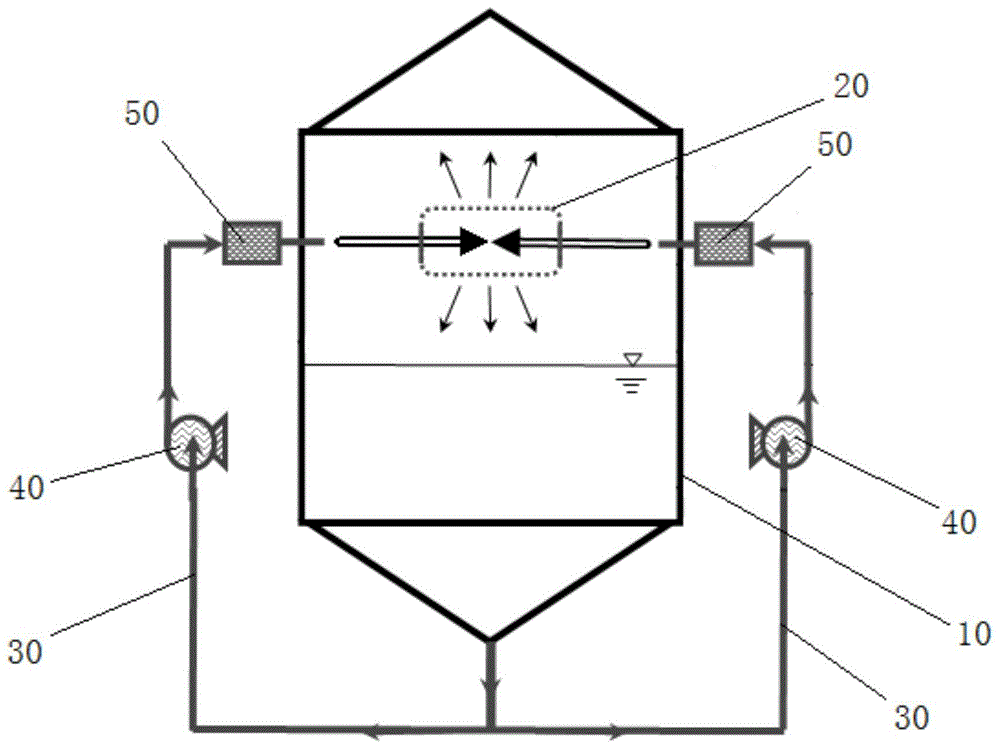
本实用新型涉及有机化学领域,具体而言,涉及一种液体非淹没式撞击流反应装置。
背景技术:
:两股连续运动的液体或两股连续运动的气体(均被称为连续相工作流体)反向运动相互撞击,被定义为撞击流。实验证明,在两股连续相撞击流的撞击点上加装一块固体隔板不改变撞击流性质,因此,单股连续相工作流体(气体或液体)撞击固体隔板或不同的固体构件,同样具有撞击流的所有特征,因此也可以定义为撞击流。连续相的液体中也可以掺有少量的气体、固体或气体加固体(被称为稀疏相);连续相的气体中也可以掺有少量的液体、固体或液体加固体(也被称为稀疏相)。撞击流的概念首先由elperin在elperinitheatandmasstransferinopposingcurrents[j].jeng.physics,1961,(6):62-68.一文中提出用于气固相的相间传递,后经以色列ben-curion大学tamir所领导的研究团队研究将撞击流原理用于气-气、液-液、气固混合、气体吸收或解吸,大大地扩展了人们对撞击流原理的认识和撞击流在工业上的应用。2000年我国学者伍沅提出了淹没式连续液体撞击流反应器(cn00230326),设计了全混流-无混流连续转换的反应过程并在工业上获得了应用,开创了我国对撞击流的研究和应用。根据环境相态和连续相工作流体的关系,撞击流可以分为淹没式撞击流和非淹没式撞击流。在撞击过程中,运动连续相工作流体边界外(环境)的相态与工作流体的相态相同,称该工作流体为淹没式撞击流,其撞击过程为淹没式撞击。例如在水下(环境)用高速水流(工作流体)冲砂,边界及边界外的环境是液相,工作流体也是液相;再如用空调给室内降温,工作流体(冷风)和环境都是气相。非淹没式撞击流的工作流体如果是液相,则边界外(环境)的相态可以是气相或固相,但不能是液相;非淹没式撞击流的工作流体如果是气相,则边界外(环境)的相态可以是液相或固相。且该流体撞击过程被称为非淹没式撞击。大多数有关撞击流的文章和专利都是讨论淹没式撞击流。例如伍沅的scirs专利cn00230326、计建炳等的专利zl201420224919.4、郑莹等的专利zl201710627354.2。然而,淹没式撞击流由于受到边界环境相同相态流体粘滞的影响,工作流体的运动速度难以提高,一般<10m/s。因此,淹没式撞击流的强化作用主要用以提高工作流体(反应物质)传热、传质效率,促进反应物的混合效率,增加化学反应的反应速率等。然而,淹没式撞击流因流体动能不足,在破坏分子结构的内能、促进新物质的产生方面的强化作用有限,相应限制了液体化学反应的反应效率。技术实现要素:本实用新型的主要目的在于提供一种液体非淹没式撞击流反应装置及反应方法,以解决现有技术中淹没式撞击流在破坏分子结构的内能、促进新物质的产生方面的强化作用不足的问题。为了实现上述目的,根据本实用新型的一个方面,提供了一种液体非淹没式撞击流反应装置,其包括:反应壳体,具有腔体;非淹没式撞击流反应组件,设置在腔体中,非淹没式撞击流反应组件用于使液体原料的喷射流体在非淹没式撞击、空化、剪切作用中完成反应。进一步地,非淹没式撞击流反应组件包括:第一筒体,第一筒体具有液体原料的进口,第一筒体的内腔用于提供非淹没式撞击场所,第一筒体的筒壁上设置有多个第一孔结构,且第一孔结构的轴向与第一筒体的液体原料的进口方向具有夹角。进一步地,第一筒体具有相对的两个侧端,且侧端设置有一个或多个液体原料的进口。进一步地,液体原料的进口均设置在一个侧端,第一筒体的另一个侧端设置有撞击底板;或者,液体原料的进口均设置在一个侧端,第一筒体的径向截面积沿远离液体原料的进口方向逐渐减小,且第一筒体的另一侧端封闭;或者,部分液体原料的进口设置在一个侧端,另一部分液体原料的进口设置在另一侧端,其中一个侧端的液体原料的进口中的至少一个与另一侧端的液体原料的进口中的至少一个的物料进入方向重叠。进一步地,第一筒体为锥形筒体、圆筒、方筒或不规则筒体,并且,不规则筒体的径向截面积沿第一筒体的两端向中间逐渐减小;或者,不规则筒体的径向截面积沿远离液体原料的进口方向逐渐减小或逐渐增大。进一步地,非淹没式撞击流反应组件还包括第二筒体,第二筒体套设在第一筒体的外围,且第二筒体的筒壁上设置有多个第二孔结构,且第二孔结构的轴向与第一孔结构的轴向具有夹角。进一步地,非淹没式撞击流反应组件还包括至少一个第三筒体,第三筒体套设在第二筒体的外围,第三筒体的筒壁上设置有多个第三孔结构,且第三孔结构的轴向与第二孔结构的轴向具有夹角。进一步地,第一孔结构、第二孔结构及第三孔结构的孔径分别独立地选自1~3mm。进一步地,非淹没式撞击流反应组件还包括撞击部,撞击部设置在第一筒体的内部。进一步地,撞击部包括实心固体组件,具有尖状端部,尖状端部与液体原料的进口方向相对。进一步地,撞击部还包括外壳,外壳设置在实心固体组件外部,且尖状端部穿过外壳延伸至外壳的外部,外壳的壳壁上设置有多个第四孔结构,第四孔结构的轴向方向分别与液体原料的进口方向及第一孔结构的轴向方向均具有夹角。进一步地,第四孔结构的孔径为1~3mm。进一步地,反应装置为重油加氢反应装置。进一步地,反应壳体底部设置有液相出口,反应装置还包括:循环管路,循环管路的进口与液相出口相连,出口与液体原料的进口相连;驱动设备,设置在循环管路上。进一步地,反应装置还包括混料单元,其设置在循环管路上,且混料单元设置有重油入口、氢气入口及加氢催化剂入口。进一步地,非淹没式撞击流反应组件设置在反应壳体的内部靠近顶端的位置。进一步地,反应装置还包括加氢产物收集单元,加氢产物收集单元设置在反应壳体的内部,并位于非淹没式撞击流反应组件的上方。本实用新型提供了一种液体非淹没式撞击流反应装置,其包括反应壳体和非淹没式撞击流反应组件,反应壳体具有腔体,非淹没式撞击流反应组件设置在腔体中,用于使液体原料的喷射流体在非淹没式撞击、空化、剪切作用中完成反应。与传统淹没式撞击流反应器不同的是,本实用新型利用非淹没式撞击流反应组件使液体原料在非淹没式撞击、空化、剪切过程中完成化学反应。通过非淹没式撞击不仅可以提高液体原料的化学反应速率和传热、传质或混合速率,使具有高动能的流体通过以撞击为主的强化方式,再伴随着空化、剪切等一系列的强化手段,最终达到破坏液体原料分子结构、断开分子键从而获得新的化学产物的目的。总之,将本实用新型提供的液体非淹没式撞击流反应装置应用于液体化学反应,能够显著提高对液体原料流体的强化效果,使其在较温和的反应条件下能够高效反应。需说明的是,本实用新型中所指的液体原料是指在反应环境及反应温度下呈液相的化学物质,它可以是单纯的液相,也可以是密相为液相,稀相为气相、固相或气固两相的多相流体。附图说明构成本申请的一部分的说明书附图用来提供对本实用新型的进一步理解,本实用新型的示意性实施例及其说明用于解释本实用新型,并不构成对本实用新型的不当限定。在附图中:图1示出了根据本实用新型一种实施例的液体非淹没式撞击流反应装置的结构示意图;图2示出了根据本实用新型一种实施例的液体非淹没式撞击流反应装置中非淹没式撞击流反应组件的结构示意图;图3示出了根据本实用新型另一种实施例的液体非淹没式撞击流反应装置中非淹没式撞击流反应组件的结构示意图;图4示出了图3中非淹没式撞击流反应组件的第一筒体处的流体撞击原理图;图5示出了根据本实用新型又一种实施例的液体非淹没式撞击流反应装置中非淹没式撞击流反应组件的结构示意图;图6示出了根据本实用新型又一种实施例的液体非淹没式撞击流反应装置中非淹没式撞击流反应组件的结构示意图;图7示出了图6中非淹没式撞击流反应组件的液体原料进口端a-a截面结构示意图;图8示出了根据本实用新型又一种实施例的液体非淹没式撞击流反应装置中非淹没式撞击流反应组件的结构示意图。其中,上述附图包括以下附图标记:10、反应壳体;20、非淹没式撞击流反应组件;21、第一筒体;22、第二筒体;23、撞击部;231、实心固体组件;232、外壳;24、撞击底板;30、循环管路;40、驱动设备;50、混料单元。具体实施方式需要说明的是,在不冲突的情况下,本申请中的实施例及实施例中的特征可以相互组合。下面将参考附图并结合实施例来详细说明本实用新型。正如
背景技术:
部分所描述的,现有技术中淹没式撞击流在破坏分子结构的内能、促进新物质的产生方面的强化作用不足。为了解决上述问题,本实用新型提供了一种液体非淹没式撞击流反应装置,如图1所示,该装置包括反应壳体10和非淹没式撞击流反应组件20,反应壳体10具有腔体,非淹没式撞击流反应组件20设置在腔体中,非淹没式撞击流反应组件20用于使液体原料的喷射流体在非淹没式撞击、空化、剪切作用中完成反应。与传统淹没式撞击流反应器不同的是,本实用新型利用非淹没式撞击流反应组件使液体原料在非淹没式撞击、空化、剪切过程中完成化学反应。通过非淹没式撞击不仅可以提高液体原料的化学反应速率和传热、传质或混合速率,使具有高动能的流体通过以撞击为主的强化方式,再伴随着空化、剪切等一系列的强化手段,最终达到破坏液体原料分子结构、断开分子键从而获得新的化学产物的目的。总之,将本实用新型提供的液体非淹没式撞击流反应装置应用于液体化学反应,能够显著提高对液体原料流体的强化效果,使其在较温和的反应条件下能够高效反应。需说明的是,本实用新型中所指的液体原料是指在反应环境及反应温度下呈液相的化学物质,它可以是单纯的液相,也可以是密相为液相,稀相为气相、固相或气固两相的多相流体。需要指出的是,任一种流体,例如液相流体,其运动雷诺数大于一定值(≥4000)时,流体运动呈紊流状态。呈紊流状态的液体内部都会发生撞击、空化和剪切等效应。但这些强化效应与高速流体直接进行非淹没式撞击产生的强化效应比较,其效率的差别是106~109数量级。在郑莹等专利号为zl201710627354.2的专利中提出了在反应器中使用不同强化功能模块的组合。本实用新型与之最大区别就是:该专利中所有串联的模块(也含有撞击、空化、剪切等功能)无论如何的设计,也只能使流体工作在淹没式状态,因而在相同的外力推动下,工作流体难以获得超高速运动的动能。该专利中仅模块i出口的流体才处于非淹没式状态,但此时的工作流体即便获得高速度和高动能,也仅仅是一个带有初速的自由落体,并未发生非淹没式撞击,流体的动能无法转变为导致分子键断裂的内能。而本实用新型提供的上述反应装置中,原料液体的喷射流体能够通过非淹没式撞击、空化、剪切作用,将高速的流体动能转变为导致分子键断裂的内能,达到更显著的强化的工艺目的。在一种优选的实施方式中,如图2、3、5、6、8,非淹没式撞击流反应组件20包括第一筒体21,第一筒体21具有液体原料的进口,第一筒体21的内腔用于提供非淹没式撞击场所,第一筒体21的筒壁上设置有多个第一孔结构,且第一孔结构的轴向与第一筒体21的液体原料的进口方向具有夹角。此处“第一孔结构的轴向”是指第一孔结构的通孔方向,也即孔的延伸方向。“液体原料的进口方向”指示液体原料喷射流体的喷入方向。因第一筒体21上设置有多个第一孔结构,使得原料液体的喷射流体进入其内腔进行撞击后,流体经第一孔结构排出,这就是第一筒体21内腔的环境一直是气体环境,从而使原料的喷射流体一直处于非淹没撞击过程。喷射流体的撞击时间非常短暂,为毫秒级。撞击瞬间发生后,流体流向被迫改变为与原喷射流体进入方向接近正交的方向,形成二次流体。被迫改变方向的“二次流体”仍然有很高的初速,其撞向带有多个第一孔结构的第一筒体21后,由于第一孔结构的轴向与第一筒体21的液体原料的进口方向具有夹角,二次流体被筒壁和第一孔结构阻拦,发生空化、剪切和再撞击作用下,大大提高了撞击流的转化效应,从而在高效状态下完成流体动能向分子内能的转换,完成了液体原料的化学反应。上述第一孔结构的轴向与第一筒体21的液体原料的进口方向具有夹角,其夹角优选为165~195°。优选地,第一筒体21具有相对的两个侧端,且侧端设置有一个或多个液体原料的进口。这样,多组喷射流体在第一筒体21内腔中完成非淹没式撞击、空化和剪切,有利于进一步提高反应效率。因第一筒体21的多个第一孔结构维持了内腔中的气相环境,因此上述非淹没式撞击可以是“液-液对撞”,也可以是“液-固相撞”。在一种典型的实施方式中,如图8所示,液体原料的进口均设置在一个侧端,第一筒体21的另一个侧端设置有撞击底板24。这样,原料液体的喷射流体通过与撞击底板24发生液固相撞,流体改变方向,形成的二次流体在第一筒体21和其第一孔结构作用下发生空化、剪切和再撞击,实现动能和分子内能转化,完成反应。在另一种典型的实施方式中,如图6所示,液体原料的进口均设置在一个侧端,第一筒体21的径向截面积沿远离液体原料的进口方向逐渐减小,且第一筒体21的另一侧端封闭。这样,进入的喷射流体可以直接撞击第一筒体21的内壁,完成液固非淹没式撞击,并在第一孔结构的作用下发生空化和剪切。更优选地,如图6所示,液体原料的进口均设置在一个侧端,第一筒体21的径向截面积沿远离液体原料的进口方向逐渐减小,第一筒体21的另一侧端封闭,且封闭一段设置有撞击底板24。这样,从第一孔结构出来的流体可以与撞击底板24发生二次非淹没式撞击,完成最后的转化。更优选地,如图6和8所示,撞击底板24的面积大于第一筒体21的径向截面积,这样,从第一孔结构出来的流体能够更充分地与其进行二次撞击,进一步提高动能向分子内能的转化程度。在另一种典型的实施方式中,如图2、3、5所示,部分液体原料的进口设置在一个侧端,另一部分液体原料的进口设置在另一侧端,其中一个侧端的液体原料的进口中的至少一个与另一侧端的液体原料的进口中的至少一个的物料进入方向重叠。这样,从第一筒体21两侧端进入的喷射流体相互完成液液撞击后,改变方向的二次流体继续在第一筒体21作用下完成空化、剪切和再撞击。为了更有效地进行流体撞击,更优选位于第一筒体21两侧端的进口数目相同,且形成一一相对的多组。上述第一筒体的形状不限,只要能够阻拦撞击后的二次流体即可。在一种优选的实施方式中,第一筒体21为锥形筒体(图6)、圆筒(图2)、方筒(图中未示出)或不规则筒体,并且,不规则筒体的径向截面积沿第一筒体21的两端向中间逐渐减小(图3、图5);或者,不规则筒体的径向截面积沿远离液体原料的进口方向逐渐减小(图8)或逐渐增大(图中未示出)。相比于圆筒而言,图3示出的不规则筒体更有利于提高第一孔结构的剪切作用,如图4所示,二次流体a以一定角度撞向第一筒体21的筒壁,在第一孔结构的剪切、再撞击作用下分成平行于筒壁方向的第一类三次流体b及平行于第一孔结构轴向的第二拨三次流体c,第一孔结构的外缘处即为撞击、剪切效应点,第一孔结构内部空腔处即为空化效应点。图2和图3所示的非淹没式撞击流反应组件20更适用于液-液撞击中撞击速度较小的撞击流,一般喷射流体速度=10~100m/s。如图6和7所示,多股喷射流体沿锥形筒体底端垂直喷入,直接与锥形筒体筒壁相撞并在瞬间同时产生空化、剪切和撞击效应,高速度流体所承载的动能被构件的阻拦而转化为破坏自身结构的内能,从而达到截断连续相物料分子键的目的。且从第一孔结构出来的流体继续运动,并与设置在锥形筒体顶部的撞击底板在此相撞,完成最后的动能吸收。为了更大程度地对喷射流体的动能进行吸收,在一种优选的实施方式中,如图5所示,非淹没式撞击流反应组件20还包括第二筒体22,第二筒体22套设在第一筒体21的外围,且第二筒体22的筒壁上设置有多个第二孔结构,且第二孔结构的轴向与第一孔结构的轴向具有夹角。这样,从第一孔结构出来的三次流体经第二筒体22的阻拦,在第二孔结构的二次剪切和空化作用下进一步被吸收动能。类似地,非淹没式撞击流反应组件20还包括至少一个第三筒体,第三筒体套设在第二筒体22的外围,第三筒体的筒壁上设置有多个第三孔结构,且第三孔结构的轴向与第二孔结构的轴向具有夹角。这样的非淹没式撞击流反应组件20更适宜处理初速更高的喷射流体,比如速度≥100m/s的流体。且,该非淹没式撞击流反应组件20更适宜处理所需分子内能更高、化学反应分子内能转变更大的液体原料,这样可以利用多层筒体和孔结构将高速动能的喷射流体的动能尽量转化为分子内能,从而完成反应。事实上,当撞击流初速u0≥340m/s,流体动能已经进入水力切割速度范围。因此当撞击流初速u0≥340m/s时,一般而言,只能通过直接地液-液撞击,将工作流体动能降低到金属构件能够承受的范围。通常情况下,优选非淹没式撞击流反应组件20包括由内之外设置的1至5层筒体,各层筒体上设置有多个孔结构,且相邻两层筒体的孔结构的轴向具有夹角。为了进一步提高孔结构的剪切、空化效应,在一种优选的实施方式中,第一孔结构、第二孔结构及第三孔结构的孔径分别独立地选自1~3mm。为了进一步加强非淹没式撞击的效果,在一种优选的实施方式中,如图8所示,非淹没式撞击流反应组件20还包括撞击部23,撞击部23设置在第一筒体21的内部。该类非淹没式撞击流反应组件20更适用于超高流速状况,当撞击流速接近340m/s时,液相连续流体已经具有足以将固体切割的动能,此时最好通过液-液撞击将连续相流体动能减低,再与金属构件接触,可以保护构件不至于迅速损坏。但如果液-液对撞的条件不能满足喷射流体的流速u0≤340m/s甚至更高时,设置撞击部23更有利于超高速喷射流体的非淹没式撞击。更优选地,如图8所示,撞击部23包括实心固体组件231,具有尖状端部,尖状端部与液体原料的进口方向相对。设置实心固体组件231,有利于维持构建自身的稳定和寿命,而利用其尖状端部与喷射流体相撞,流体会沿尖状端部周围360°分散开来,有利于更充分的吸收其动能。更优选地,如图8所示,撞击部23还包括外壳232,外壳232设置在实心固体组件231外部,且尖状端部穿过外壳232延伸至外壳232的外部,外壳232的壳壁上设置有多个第四孔结构,第四孔结构的轴向方向分别与液体原料的进口方向及第一孔结构的轴向方向均具有夹角。这样,尖状端部与喷射流体相撞后,流体沿尖状端部周围360°分散开来,并通过外壳232壳壁上的第四孔结构对分散后的流体进行剪切和空化,从而更有利于加强对流体动能的吸收。最优选地,如图8所示,外壳232的锥形外壳,其顶部即为实心固体组件231的尖状端部,第一筒体21的与液体原料进口相对的另一端设置有撞击底板24,撞击部23以焊接方式固定在撞击底板24上,第一筒体21与外壳232之间不接触,第一筒体21的径向截面积沿液体原料进口向撞击底板24的方向逐渐减小。这样,当高速的连续相流体接触到金属构件的椎体时,流体被迫向四面360°分散并在椎体孔板上以液膜形式高速流动。锥型的金属孔板对液膜造成了剪切和空化效应。进入空化小孔的液体以剩余的动能撞击构件最后的板面,被迫改变方向穿出锥型构件小孔,产生二次剪切、空化和撞击,几乎将所有的动能都转换为破坏自身结构的内能。外层的空化构件将对连续相液流进行最后的拦截和最后的动能-内能转换。需要说明的是,当处理流速接近340m/s甚至更高的液体原料喷射流体时,高速流体的喷嘴口附近是水力切割区,因此喷射流体与撞击部23的对撞距离应当避开液体动能最高的切割区,用牺牲部分动能来换取构件的稳定和寿命。同理,为了进一步加强剪切、空化效应,优选第四孔结构的孔径为1~3mm。本实用新型提供的液体非淹没式撞击流反应装置适用于各种液相原料的化学反应,比如重油加氢反应。在一种典型的实施方式中,上述反应装置为重油加氢反应装置。现有减压渣油加氢反应器多采用悬浮床(浆态床),采用420~470℃高温、15~40mpa高压及高氢油比(1000立方氢气压入1立方渣油中),可以获得良好的加氢效果,但也成为炼厂中高投资、高成本和高风险的典型工艺。采用本实用新型提供的液体非淹没式撞击流反应装置,利用了机械原理中关于局部应力集中导致断裂和破坏的概念,用局部的、微观产生的高温高压应力集中,切断重油的分子键。而反复地、不断循环地重复该过程,同样能够达到减压渣油轻质化效果,且本工艺的投资、成本大大地小于悬浮床工艺,仅为该工艺的十分之一到几十分之一。反应器的整体压力≤0.1mpa,是悬浮床的1/150~1/400,免除了悬浮床高温高压高氢导致高风险的危险。在一种优选的实施方式中,如图1所示,反应壳体10底部设置有液相出口,反应装置还包括循环管路30和驱动设备40,循环管路30的进口与液相出口相连,出口与液体原料的进口相连;驱动设备40设置在循环管路30上。在实际的反应过程中,重油原料夹带着氢气和加氢催化剂在非淹没式撞击流反应组件20中通过非淹没式撞击、空化、剪切作用完成反应后,反应轻质化产物为气态,向上排出反应壳体10之外,未反应的重油下落至反应壳体10底部,然后利用驱动设备40和循环管路30将未反应的物料返回并循环反应。优选地,循环管路30的出口处设置有喷射嘴,用以喷射液体原料,将其转化为喷射流体。在一种优选的实施方式中,反应装置还包括混料单元50,其设置在循环管路30上,且混料单元50设置有重油入口、氢气入口及加氢催化剂入口。通过重油入口、氢气入口及加氢催化剂入口可以补充原料。在一种优选的实施方式中,非淹没式撞击流反应组件20设置在反应壳体10的内部靠近顶端的位置。这样有利于保持非淹没式撞击流反应组件20高于反应壳体10的内部液面,使非淹没式撞击流反应组件20内腔保持气体环境,以维持喷射流体的非淹没式撞击。优选地,反应装置还包括加氢产物收集单元,加氢产物收集单元设置在反应壳体10的内部,并位于非淹没式撞击流反应组件20的上方。轻质化产物以气态形式朝上排出非淹没式撞击流反应组件20后,通过加氢产物收集单元可以将其收集。根据本实用新型的另一方面,还提供了一种液体非淹没式撞击流反应方法,其是将液体原料以喷射流体形态通入上述反应装置中,使其在非淹没式撞击流反应组件20中通过非淹没式撞击、空化、剪切作用完成反应。如前文所述,本实用新型利用非淹没式撞击流反应组件使液体原料在非淹没式撞击、空化、剪切过程中完成化学反应。通过非淹没式撞击不仅可以提高液体原料的化学反应速率和传热、传质或混合速率,使具有高动能的流体通过以撞击为主的强化方式,再伴随着空化、剪切等一系列的强化手段,最终达到破坏液体原料分子结构、断开分子键从而获得新的化学产物的目的。总之,将本实用新型提供的液体非淹没式撞击流反应装置应用于液体化学反应,能够显著提高对液体原料流体的强化效果,使其在较温和的反应条件下具有高流体动能,并能够高效反应。在一种优选的实施方式中,非淹没式撞击流反应组件20包括第一筒体21,第一筒体21具有液体原料的进口,且第一孔结构的轴向与第一筒体21的液体原料的进口方向具有夹角;反应方法包括以下步骤:将液体原料以喷射流体的形态通入第一筒体21的内腔,并在内腔中进行非淹没式撞击,撞击后的物料在位于筒壁的第一孔结构的空化、剪切作用下完成反应。在一种优选的实施方式中,第一筒体21具有相对的两个侧端,且侧端设置有一个或多个液体原料的进口,其中,当液体原料的进口均设置在一个侧端时,将液体原料通入内腔后,使液体原料的喷射流体撞击位于第一筒体21的另一个侧端的撞击底板24,完成非淹没式撞击;或者,第一筒体21的径向截面积沿远离液体原料的进口方向逐渐减小,将液体原料通入内腔后,使液体原料的喷射流体直接撞击第一筒体21的筒壁完成非淹没式撞击;当部分液体原料的进口设置在一个侧端,另一部分液体原料的进口设置在另一侧端时,使液体原料分别通过位于两侧的进口进入内腔,使通过两侧进入的液体原料的喷射流体在内腔中完成非淹没式撞击。在一种优选的实施方式中,非淹没式撞击流反应组件20还包括第二筒体22,当液体原料在内腔中进行非淹没式撞击后,撞击后的物料先在第一孔结构的作用下完成第一次空化、剪切,然后在位于第二筒体22筒壁的第二孔结构的第二次空化、剪切作用下,完成反应。在一种优选的实施方式中,非淹没式撞击流反应组件20还包括至少一个第三筒体,当撞击后的物料进行第二次空化、剪切后,在位于第三筒体筒壁的第三孔结构的进一步空化、剪切作用下,完成反应。在一种优选的实施方式中,非淹没式撞击流反应组件20还包括撞击部23,撞击部23设置在第一筒体21的内部;当液体原料进入内腔之后,液体原料的喷射流体在撞击部23的作用下进行非淹没式撞击。在一种优选的实施方式中,撞击部23包括实心固体组件231,具有尖状端部,尖状端部与液体原料的进口方向相对;当液体原料进入内腔之后,液体原料的喷射流体通过与尖状端部发生作用完成非淹没式撞击。在一种优选的实施方式中,撞击部23还包括外壳232,外壳232设置在实心固体组件231外部,且尖状端部穿过外壳232延伸至外壳232的外部;当液体原料的喷射流体通过与尖状端部发生非淹没式撞击之后,撞击后的物料在外壳232上的第四孔结构的作用下进行第一次空化、剪切,进入第四孔结构的物料经二次撞击后,再次通过第四孔结构进行第二次空化、剪切,最后通过第一孔结构进一步空化、剪切,完成反应。在一种优选的实施方式中,在将液体原料通入非淹没式撞击流反应组件20时,液体原料的流体速度为小于等于340m/s。在一种优选的实施方式中,反应方法用于重油的加氢反应;重油的加氢反应包括以下步骤:将重油、氢气及加氢催化剂组成的液体原料通过非淹没式撞击流反应组件20中,通过非淹没式撞击、空化、剪切作用完成反应,形成加氢产物。在一种优选的实施方式中,反应过程中还产生了未反应原料,重油的加氢反应还包括:将未反应原料从反应壳体10底部排出,并在驱动设备40的驱动作用下通过循环管路30返回至非淹没式撞击流反应组件20中进行循环反应。在一种优选的实施方式中,在加氢反应过程中,控制非淹没式撞击流反应组件20位于反应壳体10中的液面上方。在一种优选的实施方式中,在加氢反应过程中,利用设置在非淹没式撞击流反应组件20上方的加氢产物收集单元收集反应生成的加氢产物。为了能够断开分子键,喷射流体的流速优选在10m/s~1000m/s的高速或超速范围;流体温度一般在50℃~450℃。当应用于重油催化加氢时,为了提高流体强化效果,并尽量避免能源浪费,在一种优选的实施方式中,加氢反应的温度为350~410℃;加氢反应的压力小于等于0.1mpa。以下结合具体实施例对本申请作进一步详细描述,这些实施例不能理解为限制本申请所要求保护的范围。实施例1采用图1所示的反应装置,其中非淹没式撞击流反应组件采用图2所示,进行减压渣油的催化加氢制备轻质化油(汽柴油),工艺条件如下:减压渣油、氢气和催化剂的液态混合原料经喷嘴喷入非淹没式撞击流反应组件两侧入口,两侧均为单股喷射流体,方向相反并重叠,在组件内腔中完成非淹没式撞击后,二次流体与原物料运动方向呈90°扩散,并与筒体及其上设置的多个孔结构发生二次撞击,并发生空化、剪切效应破坏分子键后得到的气相轻质化产物,从反应壳体上方被收集。经过强化后仍然未反应或反应后仍然属于重质部分的物料呈液相落入反应壳体底部,经驱动装置和循环管路在此返回发生反应。其中,减压渣油的反应温度为350~410℃(减压渣油在室温为固态,200~250℃为液态,300℃以上才有较好的流动性),反应器整体压力≤0.1mpa,氢油比为(20~100):1。反应结果如下:表1油样饱和分/%芳香分/%胶质/%沥青质/%减压渣油(原料)1.658.623.714.1轻质化油(产品)72.521.84.61.1表1中,饱和烃(烷烃、环烷烃)是汽柴油的基本组分,而原料油中饱和烃基本为零,带环的芳烃占有最大比例。由此可知,该减压渣油是低价值的废料。轻质化后产品饱和烃达到72.5%,占据产品油的绝大多数,是以汽柴油为主的高价值油品;由测试结果可知,撞击流多功能强化反应器利用撞击、空化和剪切效应,破坏了原料油中芳烃、胶质和沥青质结构,切断了环烃上的碳键,使结构稳固的环烃经过分子键断裂后变成了饱和烃。馏程分析:通过加热蒸馏分离出原料和产品中不同饱和蒸气压组分,由馏程分析可以考查物料中轻重组分的含量,具体见表2。表2由表2可知,原料减压渣油是低价值重质油,其中汽柴油含量百分数为零,350-500℃仅能作为锅炉燃料的组分占8.5%,剩余的91.5%仅能通过调和做道路沥青。从表2的产品馏程可以看出,汽柴油馏分占约60%,锅炉燃料32.3%,沥青质仅为7.5%。其轻质化效果明显。以上的检验是一次反应结果,如果二次反应并与炼厂其它工序结合,其整体效益更是突出,可达到:73%的汽柴油,总汽柴油收率达到86.8%,仅有8.1%产出产品为固体的石油焦。近代炼油规模日趋增大,100万吨级炼厂比比皆是,1%的增量就是万吨规模,因此上述检验足以表明本实用新型能够得到的效益是异常显著的。以上所述仅为本实用新型的优选实施例而已,并不用于限制本实用新型,对于本领域的技术人员来说,本实用新型可以有各种更改和变化。凡在本实用新型的精神和原则之内,所作的任何修改、等同替换、改进等,均应包含在本实用新型的保护范围之内。当前第1页12