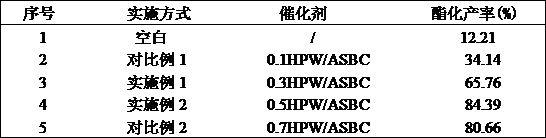
[0001]
本发明涉及复合材料技术领域,特别是涉及一种基于磷钨酸的硅氧烷嵌段共聚物复合材料的制备。
背景技术:[0002]
生物柴油通常是由游离脂肪酸和短链醇在酸催化剂作用下发生酯化反应获得的。游离脂肪酸中油酸的获得途径广泛,一般是从各种植物类油料作物、动物油脂和餐饮废油中获得。常用的短链醇为甲醇、乙醇等,其中甲醇因为其价格低廉、极性较强、能较快速发生酯化反应而被广泛利用。生物柴油不仅可替代化石柴油,还可替代燃料石油化工产品。
[0003]
传统催化反应通常使用硫酸、盐酸等液体酸作为酸催化剂,但反应所需时间较长,副产物多,且对设备有腐蚀性,产生的大量含酸废水处理困难,且不能回收循环使用,不符合绿色化学的要求。
[0004]
近年来,keggin型杂多酸钨磷酸被广泛使用,利用其优异的酸催化性能来达到很好的催化效果。又因为其价格昂贵、易溶于极性溶剂导致难以分离和回收利用,限制了纯的hpw的使用。
[0005]
将具有较高催化活性的hpw负载到适宜的载体上是目前科研工作者的工作重点,其中高分子负载催化剂得到了极大的重视。这类催化剂有着稳定性高、溶剂适用性广、易于产物分离纯化、对环境影响小、易从反应体系中分离回收和重复使用等优点。
[0006]
研究结果表明,通过使用自合成的硅氧烷嵌段共聚物作为载体,采用后合成嫁接法利用分子间的酸碱、配位和氢键等作用负载hpw,制得的复合材料在催化油酸和甲醇的酯化反应中起到很好的催化作用。asbc载体制备的操作较简单,对实验设备的要求不高;复合材料催化剂的活性位点确定,酸催化效果好;复合材料中多酸负载牢固不易脱落,且复合材料可以重复使用。因此,我们提出一种基于磷钨酸的硅氧烷嵌段共聚物复合材料的制备方法,合成hpw/asbc复合材料。
技术实现要素:[0007]
本发明要解决的技术问题是提供一种基于磷钨酸的硅氧烷嵌段共聚物复合材料的制备方法。
[0008]
本发明产品以自合成的硅氧烷嵌段共聚物asbc为载体,采用keggin结构的hpw作为布朗斯特酸活性中心,制备了一系列复合材料。
[0009]
本发明的基于磷钨酸的硅氧烷嵌段共聚物复合材料,其结构为hpw/asbc,所述复合材料是以asbc为反应载体,所述反应载体是自合成的硅氧烷嵌段共聚物,所述载体asbc通过酸碱、配位和氢键等作用负载酸催化活性成分,所述酸催化活性组分为磷钨酸。
[0010]
优选的,所述硅氧烷嵌段共聚物载体asbc是由d4、apdes和mm在tmah的催化条件下制成。
[0011]
优选的,所述hpw为磷和钨缩合比为1:12的keggin型结构。
[0012]
本发明一种基于磷钨酸的硅氧烷嵌段共聚物复合材料的制备方法,包括以下步骤:(1)在装有回流冷凝管、n2导管、温度计的100 ml三口烧瓶中,依次向体系中加入质量比为50:1的d4和tmah,向体系通入20 min高纯n2;(2)设置反应温度90 ℃、搅拌速率700 rpm的条件下反应2 h,然后打开真空泵减压反应1 h,三口烧瓶内的液体变粘稠,收集瓶内液体;(3)使用步骤(1)装置,依次向三口烧瓶中加入物质的量比为3:1的d4和apdes,和d4质量1/20的步骤(2)合成的液体,向体系中通入20 min高纯n2;(4)设置反应温度90 ℃,同时以700 rpm的转速搅拌,反应10 h,然后加入apdes物质的量的1/50的mm封端剂反应2 h;(5)步骤(4)反应结束后,再次通入20 min高纯n2,快速升温至140 ℃,打开真空泵减压蒸馏1 h,收集三口瓶内的微黄色粘稠透明状液体,即为目标产物asbc;(6)在4个50 ml圆底双口烧瓶内分别加入0.5 g步骤(5)制得的asbc和15 ml无水乙醇,在60 ℃、700 rpm磁性搅拌冷凝回流的条件下,反应2 h,使asbc充分溶解于无水乙醇;(7)称量0.1、0.3、0.5和0.7 g hpw,分别溶于5、10、15和20 ml无水乙醇中,并使用25 ml恒压漏斗,分别在约20、40、60和80 min内向反应烧瓶内滴加完毕,反应10 h;(8)将步骤(7)的混合液分别旋蒸除去乙醇,取出固体,真空箱60 ℃干燥24 h,取出干燥后的块状固体研磨20-30 min,得到均匀的粉末,即为复合材料0.1hpw/asbc、0.3hpw/asbc、0.5hpw/asbc和0.7hpw/asbc。
[0013]
与现有技术相比,本发明具有以下有益效果:本发明的复合材料的催化活性成分为磷钨酸;本发明使用自合成的硅氧烷嵌段共聚物asbc为载体,二者通过酸碱、配位和氢键等作用紧密结合,便于催化剂的回收和循环使用,降低了成本;本发明的复合材料可对油酸和甲醇的酯化反应起催化作用,提高其催化产率。
附图说明
[0014]
为了更清楚地说明本发明实施例或现有技术中的技术方案,下面将对实施例中所需要使用的附图做简单介绍,显而易见地,下面描述中的附图仅仅是本发明的个别实施例,对于本领域普通技术人员来讲,依据本发明的思想,可以根据这些附图获得其他的附图。
[0015]
图1是纯的hpw、自制的asbc、本发明实施例1-2和对比例1-2测得的傅里叶变换红外光谱图。
具体实施方式
[0016]
下面结合具体实施例和附图对本发明做进一步说明。
[0017]
实施例1一种基于磷钨酸的硅氧烷嵌段共聚物复合材料,包括以下步骤制备而成:(1)在装有回流冷凝管、n2导管、温度计的100 ml三口烧瓶中,依次向体系中加入质量比为50:1的d4和tmah,向体系通入20 min高纯n2;(2)设置反应温度90 ℃、搅拌速率700 rpm的条件下反应2 h,然后打开真空泵减压反应1 h,三口烧瓶内的液体变粘稠,收集瓶内液体,即为制成的tmah硅醇盐,用作之后合成
asbc的催化剂;(3)使用步骤(1)装置,依次向三口烧瓶中加入物质的量比为3:1的d4和apdes,和d4质量1/20的步骤(2)合成的液体,向体系中通入20 min高纯n2;(4)设置反应温度90 ℃,同时以700 rpm的转速搅拌,反应10 h,然后加入apdes物质的量的1/50的mm封端剂反应2 h;(5)步骤(4)反应结束后,再次通入20 min高纯n2,快速升温至140 ℃,使tmah硅醇盐失活,打开真空泵减压蒸馏1 h,除去失活的tmah硅醇盐和低聚物,收集三口瓶内的微黄色粘稠透明状液体,即为目标产物asbc;(6)在1个50 ml圆底双口烧瓶内分别加入0.5 g步骤(5)制得的asbc和15 ml无水乙醇,在60 ℃、700 rpm磁性搅拌冷凝回流的条件下,反应2 h,使asbc充分溶解于无水乙醇;(7)称量0.3 g hpw,溶于10 ml无水乙醇中,并使用25 ml恒压漏斗,在约40 min时间内向反应烧瓶内滴加完毕,反应10 h;(8)将步骤(7)的混合液旋蒸除去乙醇,取出固体物,真空箱60 ℃干燥24 h,取出干燥后的块状固体研磨20-30 min,得到均匀的粉末,即为复合材料0.3hpw/asbc。
[0018]
实施例2一种基于磷钨酸的硅氧烷嵌段共聚物复合材料,包括以下步骤制备而成:(1)在装有回流冷凝管、n2导管、温度计的100 ml三口烧瓶中,依次向体系中加入质量比为50:1的d4和tmah,向体系通入20 min高纯n2;(2)设置反应温度90 ℃、搅拌速率700 rpm的条件下反应2 h,然后打开真空泵减压反应1 h,三口烧瓶内的液体变粘稠,收集瓶内液体,即为制成的tmah硅醇盐,用作之后合成asbc的催化剂;(3)使用步骤(1)装置,依次向三口烧瓶中加入物质的量比为3:1的d4和apdes,和d4质量1/20的步骤(2)合成的液体,向体系中通入20 min高纯n2;(4)设置反应温度90 ℃,同时以700 rpm的转速搅拌,反应10 h,然后加入apdes物质的量的1/50的mm封端剂反应2 h;(5)步骤(4)反应结束后,再次通入20 min高纯n2,快速升温至140 ℃,使tmah硅醇盐失活,打开真空泵减压蒸馏1 h,除去失活的tmah硅醇盐和低聚物,收集三口瓶内的微黄色粘稠透明状液体,即为目标产物asbc;(6)在1个50 ml圆底双口烧瓶内分别加入0.5 g步骤(5)制得的asbc和15 ml无水乙醇,在60 ℃、700 rpm磁性搅拌冷凝回流的条件下,反应2 h,使asbc充分溶解于无水乙醇;(7)称量0.5 g hpw,溶于15 ml无水乙醇中,并使用25 ml恒压漏斗,在约60 min时间内向反应烧瓶内滴加完毕,反应10 h;(8)将步骤(7)的混合液旋蒸除去乙醇,取出固体物,真空箱60 ℃干燥24 h,取出干燥后的块状固体研磨20-30 min,得到均匀的粉末,即为复合材料0.5hpw/asbc。
[0019]
对比例1一种基于磷钨酸的硅氧烷嵌段共聚物复合材料,包括以下步骤制备而成:(1)在装有回流冷凝管、n2导管、温度计的100 ml三口烧瓶中,依次向体系中加入质量比为50:1的d4和tmah,向体系通入20 min高纯n2;(2)设置反应温度90 ℃、搅拌速率700 rpm的条件下反应2 h,然后打开真空泵减压反
应1 h,三口烧瓶内的液体变粘稠,收集瓶内液体,即为制成的tmah硅醇盐,用作之后合成asbc的催化剂;(3)使用步骤(1)装置,依次向三口烧瓶中加入物质的量比为3:1的d4和apdes,和d4质量1/20的步骤(2)合成的液体,向体系中通入20 min高纯n2;(4)设置反应温度90 ℃,同时以700 rpm的转速搅拌,反应10 h,然后加入apdes物质的量的1/50的mm封端剂反应2 h;(5)步骤(4)反应结束后,再次通入20 min高纯n2,快速升温至140 ℃,使tmah硅醇盐失活,打开真空泵减压蒸馏1 h,除去失活的tmah硅醇盐和低聚物,收集三口瓶内的微黄色粘稠透明状液体,即为目标产物asbc;(6)在1个50 ml圆底双口烧瓶内分别加入0.5 g步骤(5)制得的asbc和15 ml无水乙醇,在60 ℃、700 rpm磁性搅拌冷凝回流的条件下,反应2 h,使asbc充分溶解于无水乙醇;(7)称量0.1 g hpw,溶于5 ml无水乙醇中,并使用25 ml恒压漏斗,在约20 min时间内向反应烧瓶内滴加完毕,反应10 h;(8)将步骤(7)的混合液旋蒸除去乙醇,取出固体物,真空箱60 ℃干燥24 h,取出干燥后的块状固体研磨20-30 min,得到均匀的粉末,即为复合材料0.1hpw/asbc。
[0020]
对比例2一种基于磷钨酸的硅氧烷嵌段共聚物复合材料,包括以下步骤制备而成:(1)在装有回流冷凝管、n2导管、温度计的100 ml三口烧瓶中,依次向体系中加入质量比为50:1的d4和tmah,向体系通入20 min高纯n2;(2)设置反应温度90 ℃、搅拌速率700 rpm的条件下反应2 h,然后打开真空泵减压反应1 h,三口烧瓶内的液体变粘稠,收集瓶内液体,即为制成的tmah硅醇盐,用作之后合成asbc的催化剂;(3)使用步骤(1)装置,依次向三口烧瓶中加入物质的量比为3:1的d4和apdes,和d4质量1/20的步骤(2)合成的液体,向体系中通入20 min高纯n2;(4)设置反应温度90 ℃,同时以700 rpm的转速搅拌,反应10 h,然后加入apdes物质的量的1/50的mm封端剂反应2 h;(5)步骤(4)反应结束后,再次通入20 min高纯n2,快速升温至140 ℃,使tmah硅醇盐失活,打开真空泵减压蒸馏1 h,除去失活的tmah硅醇盐和低聚物,收集三口瓶内的微黄色粘稠透明状液体,即为目标产物asbc;(6)在1个50 ml圆底双口烧瓶内分别加入0.5 g步骤(5)制得的asbc和15 ml无水乙醇,在60 ℃、700 rpm磁性搅拌冷凝回流的条件下,反应2 h,使asbc充分溶解于无水乙醇;(7)称量0.7 g hpw,溶于20 ml无水乙醇中,并使用25 ml恒压漏斗,在约80 min内向反应烧瓶内滴加完毕,反应10 h;(8)将步骤(7)的混合液旋蒸除去乙醇,取出固体物,真空箱60 ℃干燥24 h,取出干燥后的块状固体研磨20-30 min,得到均匀的粉末,即为复合材料0.7hpw/asbc。
[0021]
对本发明实施例1-2以及对比例1-2制备的复合材料的催化性能进行检测,其以油酸和甲醇的酯化反应为探针实验。
[0022]
实验所用基本原料:油酸、甲醇和正己烷。实验所用的催化剂为实施例1-2以及对比例1-2制备的复合材料,同时结合空白对比组。催化测试前,将实施例1-2以及对比例1-2
的复合材料在真空干燥箱中60 ℃干燥12 h。
[0023]
催化反应均在带有聚四氟乙烯内衬的反应釜中进行。反应条件为100 ℃,催化剂用量150 mg,酸醇比为1:30。将反应物和催化剂置于反应器中在上述条件下反应12 h,搅拌速率700 rpm。反应结束后,将反应釜置于冰水中快速降温,之后通过离心使固液分离,固体用正己烷洗涤后干燥;液体部分旋蒸除去甲醇和少量水。以催化酯化反应来考察不同种类催化剂的催化性能,结果如表1所示。
[0024]
获得的目标产物,用1h-nmr分析。并通过公式:油酸甲酯产率(%) = 100
ꢀ×ꢀ
(2ame/3 aα-ch2)计算油酸甲酯的产率。其中ame=甲氧基氢(ch3o-)信号的积分面积,出现在3.69 ppm处,aα-ch
2 = α-亚甲基氢的积分面积(在羰基的α-位)在2.26-2.39 ppm范围内,因子2和3来源于亚甲基碳具有两个氢原子、甲醇衍生的甲基碳具有三个连接的氢原子。
[0025]
本发明制备的复合材料,利用其作为油酸和甲醇的酯化反应的催化剂,其催化效果较理想,且本发明的复合材料可以回收使用。催化产物油酸甲酯是生物柴油的主要原料,是新型的生物能源燃料,并且反应中过量的甲醇可通过旋转蒸发回收,反应过程清洁绿色,适于工业化推广。
[0026]
本文中应用了具体示例对本发明的原理及实施方式进行了阐述,以上实施例的说明只是用于帮助理解本发明的方法及其核心思想;同时,对于本领域的一般技术人员,依据本发明的思想,在具体实施方式及应用范围上均会有改变之处。综上所述,本说明书内容不应理解为对本发明的限制。