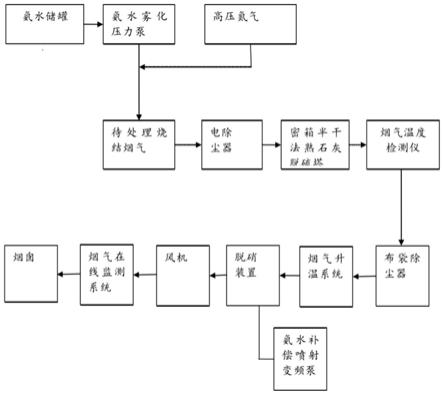
[0001]
本发明属于烧结烟气超低排放技术领域,特别涉及一种烧结烟气的处理方法。
背景技术:[0002]
烧结烟气是烧结混合料在燃烧烧结过程中产生的含有二氧化硫、氮的氧化物和粉尘的混合气体,烧结烟气中的二氧化硫、氮的氧化物和粉尘含量超标,污染大气,必须进行脱硫脱硝处理才能排放。
[0003]
目前,烧结烟气脱硫、脱硝、除尘处理时,一般采用以下几种方法:a、湿法:石灰石-石膏法、石灰-石膏法等脱硫,scr法脱硝,但脱硫时产生的废水含大量的重金属、及高含盐、高cod的废水很难处理,并且颗粒物达不到超低排放的要求,投资较大。b、活性炭法脱硫脱硝制酸:活性炭法脱硫脱硝制酸法工艺复杂,运行中活性炭模块易发生板结,活性炭再生制酸时,产生含大量的重金属、高氨氮、高氟及高含盐、高cod的废水很难处理。c、半干法:密箱熟石灰循环脱硫、熟石灰流化床烟气循环脱硫、nid法烟气循环熟石灰法脱硫、喷雾干燥法烟气法等脱硫,scr法脱硝,但半干法脱硫效率较低,很难达到so2超低排放的要求。d、氨法:用氨水在吸收塔和so2反应,对氨水进行循环使用,形成硫酸铵产品,然后再进行脱硝处理,但由于形成的硫酸铵产品含重金属较高,无法使用,并且产生含高氨氮、高重金属、高cod的废水难于处理。
[0004]
上述的处理方法都存在问题,因此亟需一种脱硫效果好,且脱硫后的产物易于处理的烧结烟气处理方法。
技术实现要素:[0005]
本发明实施例提供了一种烧结烟气的处理方法,以解决现有技术中,不能同时兼备良好的脱硫效果且脱硫产物易于处理的技术问题。
[0006]
本发明实施例提供了一种烧结烟气的处理方法,所述方法包括,
[0007]
用雾化氨水与待处理烧结烟气混合进行一级脱硫,获得一级脱硫烧结烟气;
[0008]
将所述一级脱硫烧结烟气和含水熟石灰接触进行二级脱硫,获得二级脱硫烧结烟气;
[0009]
所述二级脱硫烧结烟气进入第一除尘装置进行第一除尘;
[0010]
所述第一除尘后的二级脱硫烧结烟气进入脱硝装置进行脱硝处理,然后达标排放。
[0011]
进一步地,所述雾化氨水的雾滴直径≤150μm。
[0012]
进一步地,所述雾化氨水的运动方向与所述待处理烧结烟气的运动方向相同。
[0013]
进一步地,所述氨水的质量浓度为5~20%。
[0014]
进一步地,所述二级脱硫温度为90~110℃。
[0015]
进一步地,所述含水熟石灰中,水的质量分数为66~72%。
[0016]
进一步地,所述含水熟石灰的摩尔质量为所述一级脱硫烧结烟气中二氧化硫的摩
尔质量的2~4倍。
[0017]
进一步地,所述用雾化氨水与待处理烧结烟气混合进行一级脱硫,获得一级脱硫烧结烟气,包括,
[0018]
用雾化氨水与待处理烧结烟气混合进行一级脱硫;
[0019]
所述一级脱硫后的待处理烧结烟气进行第二除尘装置进行第二除尘,获得一级脱硫烧结烟气。
[0020]
进一步地,所述雾化氨水由雾化氨水制备装置获得,所述待处理烧结烟气在烟道中运动,所述雾化氨水制备装置设置于所述烟道上,所述氨水制备装置与所述第二除尘装置之间的烟道长度为30~100m。
[0021]
进一步地,所述第一除尘装置为布袋除尘器,所述第二除尘装置为电除尘器。
[0022]
本发明实施例中的一个或多个技术方案,至少具有如下技术效果或优点:
[0023]
本发明实施例提供了一种烧结烟气的处理方法,采用雾化氨水与烧结烟气混合,氨水与烟气中的大部分二氧化硫发生化学反应,生成亚硫酸铵和亚硫酸氢铵;烟气中剩余的二氧化硫与含水熟石灰发生化学反应,进行二级脱硫,生成亚硫酸钙、亚硫酸氢钙、硫酸钙和硫酸氢钙的混合颗粒;含有混合颗粒的二级脱硫烟气依次经过除尘和脱硝处理后,然后排入大气。这种雾化氨水一级脱硫与含水熟石灰的半干法脱硫相结合,排入大气中的二氧化硫含量为10~20mg/nm3,nox含量为20~30mg/nm3,粉尘的含量为2~3mg/nm3,实现了超低排放,对环境友好。整个处理过程不存在循环使用,因此,不会出现采用氨水和喷淋塔处理烧结烟气所造成的重金属富集的问题,除尘获得的铵盐可以作为化肥使用。
附图说明
[0024]
为了更清楚地说明本发明实施例中的技术方案,下面将对实施例描述中所需要使用的附图作一简单地介绍,显而易见地,下面描述中的附图是本发明的一些实施例,对于本领域普通技术人员来讲,在不付出创造性劳动的前提下,还可以根据这些附图获得其它的附图。
[0025]
图1是本发明实施例烧结烟气处理过程示意图。
具体实施方式
[0026]
下文将结合具体实施方式和实施例,具体阐述本发明,本发明的优点和各种效果将由此更加清楚地呈现。本领域技术人员应理解,这些具体实施方式和实施例是用于说明本发明,而非限制本发明。
[0027]
在整个说明书中,除非另有特别说明,本文使用的术语应理解为如本领域中通常所使用的含义。因此,除非另有定义,本文使用的所有技术和科学术语具有与本发明所属领域技术人员的一般理解相同的含义。若存在矛盾,本说明书优先。
[0028]
除非另有特别说明,本发明中用到的各种原材料、试剂、仪器和设备等,均可通过市场购买得到或者可通过现有方法制备得到。
[0029]
本申请中“第一”、“第二”、“一级”和“二级”不代表顺序,可以理解为名词。
[0030]
本发明实施例提供的技术方案为解决上述技术问题,总体思路如下:
[0031]
本发明实施例提供了一种烧结烟气的处理方法,所述方法包括,
[0032]
s1,用雾化氨水与待处理烧结烟气混合进行一级脱硫,获得一级脱硫烧结烟气;
[0033]
s2,将所述一级脱硫烧结烟气和含水熟石灰接触进行二级脱硫,获得二级脱硫烧结烟气;
[0034]
s3,所述二级脱硫烧结烟气进入第一除尘装置进行第一除尘;
[0035]
s4,所述第一除尘后的二级脱硫烧结烟气进入脱硝装置进行脱硝处理,然后达标排放。
[0036]
采用雾化氨水与烧结烟气混合,氨水与烟气中的大部分二氧化硫发生化学反应,生成亚硫酸铵和亚硫酸氢铵;烟气中剩余的二氧化硫与含水熟石灰发生化学反应,生成亚硫酸钙、亚硫酸氢钙、硫酸钙和硫酸氢钙的混合颗粒,该过程可以在密箱半干法熟石灰脱硫塔中进行;含有混合颗粒的二级脱硫烟气依次经布袋除尘和脱硝处理后,排入大气。采用雾化氨水与烧结烟气反应,可以更充分的脱除烧结烟气中的二氧化硫气体;由于烧结烟气中二氧化硫含量高,仅通过雾化氨水一级脱硫,不能达标排放,因此再配合含水熟石灰对烟气进行二级脱硫处理,排入大气中的二氧化硫含量为10~20mg/nm3,实现了超低排放,对环境友好。整个处理过程不存在循环使用,因此,不会出现采用氨水和喷淋塔处理烧结烟气所造成的重金属富集的问题。且氨水和喷淋塔处理烧结烟气由于含水量高,除尘效果差,处理后的烟气中粉尘含量高达50mg/nm3。
[0037]
本申请中脱硝装置为以scr法为原理的脱硝装置,是一种现有技术。scr(selective catalytic reduction)是指选择性催化还原技术,在催化剂的作用下,向280~420℃的烟气中喷入氨,将no
x
还原成n2和h2o。本申请中脱硝所用催化剂包括但不限于v2o5或v2o
5-wo3。
[0038]
进一步地,所述雾化氨水的雾滴直径≤150μm。
[0039]
雾滴越细小,与待处理烧结烟气的接触面积越大,那么可以促进一级脱硫反应快速充分的进行。雾滴过大,脱硫效果差,脱硫率低。
[0040]
进一步地,所述雾化氨水通过氨水压力雾化与高压氮气雾化共同作用获得,所述氨水压力为0.1~0.6mpa,所述高压氮气的压力为0.4~0.7mpa,所述雾化氨水的运动方向与所述待处理烧结烟气的运动方向相同。
[0041]
本申请中通过高压氮气雾化与氨水压力雾化共同作用,可以改善氨水的雾化效果,使雾滴粒径小。在实际操作中,雾滴的喷出方向与待处理烧结烟气的运行方向一致,可以使雾滴随着待处理烧结烟气向前运动,同时进行脱硫反应,延长接触时间,改善一级脱硫率。且反应后获得的亚硫酸铵、亚硫酸氢铵、硫酸铵和硫酸氢铵的混合颗粒也具有与烟气同时向前的速度,在后续的第一除尘装置中被部分截留。受雾化压力设备的影响,氨水压力和高压氮气压力不可能过大,脱氨水压力和高压氮气压力过小,雾化氨水雾滴大,且速率小,影响脱硫效率。当二氧化硫脱除后,剩余的雾化氨水还可以随着处理烟气进入scr脱硝装置,作为脱硝原料进行二次利用。本申请雾化氨水可通过以下方式获得:在储存氨水的氨水储罐上连接氨水雾化压力泵,在氨水雾化压力泵上设置一个两相喷头,两相喷头包括互相连通的第一相入口、第二相入口和出口,两相喷头中的第一相入口和氨水雾化压力泵连通,两相喷头中的第二相入口与高压氮气连通,从两相喷头的出口喷出的雾化氨水受到雾化压力泵和高压氮气的共同作用,雾化效果极好,雾滴小,速率高。
[0042]
进一步地,所述氨水的质量浓度为5~20%。
[0043]
氨水质量浓度过小,为了提高脱硫效果,必须增加氨水的雾化量,第一方面,这会使烟气的温降过大,第二方面,会使烟尘沾水形成块状物,粘结在电除尘器中,难以去除。
[0044]
氨水质量浓度过大,会造成浪费。
[0045]
进一步地,所述二级脱硫温度为90~110℃。二级脱硫温度不可过低,否则进入布袋除尘会析出水,使烟尘粘结在布袋除尘器上,影响除尘的进行;二级脱硫温度不可过高,这样烟尘中饱和蒸气压高,析出水少,会影响脱硫效率。
[0046]
进一步地,所述含水熟石灰中,水的质量分数为66~72%。
[0047]
熟石灰中含有一定量的水分,有利于与烟气中的二氧化硫进行化学反应,提高脱硫率。水的含量过高,烟尘易结块,造成反应器及布袋除尘器故障,水的含量过低,会降低脱硫效率。
[0048]
进一步地,所述含水熟石灰的摩尔质量为所述一级脱硫烧结烟气中二氧化硫的摩尔质量的2~4倍。为了使一级脱硫烧结烟气中的二氧化硫被充分脱除,因此要使含水熟石灰过量。
[0049]
进一步地,所述用雾化氨水与烧结烟气混合进行一级脱硫反应,获得一级脱硫烧结烟气,包括,
[0050]
用雾化氨水与待处理烧结烟气混合进行一级脱硫;
[0051]
所述一次脱硫后的待处理烧结烟气进行第二除尘装置进行第二除尘,获得一级脱硫烧结烟气。
[0052]
待处理烧结烟气中携带大量的粉尘,且经过一级脱硫,产生了亚硫酸铵、亚硫酸氢铵、硫酸铵和硫酸氢铵的混合颗粒,大部分去除。第二除尘装置可选用电除尘器。
[0053]
进一步地,所述雾化氨水由雾化氨水制备装置获得,所述待处理烧结烟气在烟道中运动,所述雾化氨水制备装置设置于所述烟道上,所述氨水制备装置与所述第二除尘装置之间的烟道长度为30~100m。
[0054]
雾化氨水的制备装置包括氨水储罐、氨水雾化压力泵和两相喷头,氨水雾化压力泵的入口与氨水储罐连通;两相喷头包括互相连通的第一相入口、第二相入口和出口,两相喷头中的第一相入口和氨水雾化压力泵的出口连通,两相喷头中的第二相入口与外界高压氮气连通,从两相喷头的出口喷出的雾化氨水由氨水雾化压力泵对氨水进行压力雾化以及高压氮气雾化的共同作用获得,这种方法雾化效果极好,雾滴小,速率高。处理待处理烧结烟气的设备之间是通过烟道连通的,待烧结烟气通过烟道从雾化氨水的制备装置运动至第二除尘装置,第二除尘装置与雾化氨水的制备装置之间烟道距离过小,会使大量的雾滴到达电除尘设备处,使粉尘受潮结垢,影响电除尘效果;第二除尘装置与雾化氨水的制备装置之间的烟道距离过大,会增加处理场地,提高烟道成本。
[0055]
进一步地,所述第一除尘装置为布袋除尘器,所述第二除尘装置为电除尘器。
[0056]
由于布袋除尘器的除尘效率比电除尘器效率高,因此先采用电除尘器除尘,对烧结烟气进行预除尘,再采用布袋除尘器精除尘是。电除尘器的工作原理是,烟气通过电除尘器主体结构前的烟道时,使其烟尘带正电荷,然后烟气进入设置多层阴极板的电除尘器通道。由于带正电荷烟尘与阴极电板的相互吸附作用,使烟气中的颗粒烟尘吸附在阴极上,定时打击阴极板,使具有一定厚度的烟尘在自重和振动的双重作用下跌落在电除尘器结构下方的灰斗中,从而达到清除烟气中的烟尘的目的。布袋除尘器的工作原理是:含尘气体由除
尘器下部进气管道,经导流板进入灰斗时,由于导流板的碰撞和气体速度的降低等作用,粗粒粉尘将落入灰斗中,其余细小颗粒粉尘随气体进入滤袋室,由于滤料纤维及织物的惯性、扩散、阻隔、钩挂、静电等作用,粉尘被阻留在滤袋内,净化后的气体逸出袋外,经排气管排出。滤袋上的积灰用气体逆洗法去除,清除下来的粉尘下到灰斗,经双层卸灰阀排到输灰装置。滤袋上的积灰也可以采用喷吹脉冲气流的方法去除,从而达到清灰的目的,清除下来的粉尘由排灰装置排走。电除尘器和布袋除尘器为冶金废物处理领域的现有技术,在此不做具体限定。
[0057]
图1为本发明实施例烧结烟气处理过程示意图,结合图1,本申请实际运行时如下:待处理烧结烟气在烟道内与雾化氨水制备装置制备的雾化氨水发生脱硫反应,进行一级脱硫,因雾化氨水有一定向前的速率,因此二者向前运动的过程中也持续进行脱硫反应,经过电除尘器除尘后进入密箱半干法熟石灰脱硫塔,与含水熟石灰接触进行二级脱硫,获得二级脱硫烧结烟气;布袋除尘器前设置有烟气温度检测仪,二级脱硫烧结烟气经烟气温度检测仪检测后,经布袋除尘器除尘;布袋除尘器后面设置有烟气升温系统,经布袋除尘器除尘后的烟气经过烟气升温系统升温至280~420℃温度条件后,进入脱硝装置,脱硝装置内设置有氨水补偿喷射变频泵,可以提供氨水,在脱硝装置中,烟气与催化剂和氨水发生反应进行脱硝,脱硝后的烟气经风机加压,经烟气在线监测系统检测so2、no
x
、颗粒物符合排放要求后,从烟囱排放。
[0058]
下面将结合实施例、对照例及实验数据对本申请的一种烧结烟气处理方法进行详细说明。
[0059]
实施例1
[0060]
待处理烧结烟气在烟道内与质量浓度为8%雾化氨水发生脱硫反应,进行一级脱硫,其中雾化氨水的雾滴直径≤150μm,待处理烧结气与雾化氨水的运动方向相同,雾化氨水通过氨水压力雾化与高压氮气雾化共同作用获得,其中,氨水压力为0.5mpa,高压氮气的压力为0.5mpa。一级脱硫后的待处理烧结烟气进入电除尘器除尘,获得一级脱硫烧结烟气,其中雾化氨水制备装置与电除尘器之间的烟道长度为50m。一级脱硫烧结烟气温度为108℃,进入密箱半干法熟石灰脱硫塔中,与含水量为68%的含水熟石灰接触进行二级脱硫,获得二级脱硫烧结烟气;二级脱硫烧结烟气经烟气温度测量仪检测后,经布袋除尘器除尘;布袋除尘器后面设置有烟气升温系统,经布袋除尘器除尘后的烟气经过烟气升温系统升温至280~420℃温度条件后,进入脱硝装置,在脱硝装置中,烟气与催化剂和氨水发生反应进行脱硝,脱硝后的烟气经风机加压,经烟气so2、no
x
、颗粒物在线监测后排放至大气中,在线监测结果如表1所示。
[0061]
实施例2
[0062]
待处理烧结烟气在烟道内与质量浓度为18%雾化氨水发生脱硫反应,进行一级脱硫,其中雾化氨水的雾滴直径≤130μm,待处理烧结气与雾化氨水的运动方向相同,雾化氨水通过氨水压力雾化与高压氮气雾化共同作用获得,其中,氨水压力为0.6mpa,高压氮气的压力为0.7mpa。一级脱硫后的待处理烧结烟气进入电除尘器除尘,获得一级脱硫烧结烟气,其中雾化氨水制备装置与电除尘器之间的烟道长度为80m。一级脱硫烧结烟气温度为105℃,进入密箱半干法熟石灰脱硫塔中,与含水量为70%的含水熟石灰接触进行二级脱硫,获得二级脱硫烧结烟气;二级脱硫烧结烟气经烟气温度测量仪检测后,经布袋除尘器除尘;布
袋除尘器后面设置有烟气升温系统,经布袋除尘器除尘后的烟气经过烟气升温系统升温至280~420℃温度条件后,进入脱硝装置,在脱硝装置中,烟气与催化剂和氨水发生反应进行脱硝,脱硝后的烟气经风机加压,经烟气so2、no
x
、颗粒物在线监测后排放至大气中,在线监测结果如表1所示。
[0063]
实施例3
[0064]
待处理烧结烟气在烟道内与质量浓度为15%雾化氨水发生脱硫反应,进行一级脱硫,其中雾化氨水的雾滴直径≤125μm,待处理烧结气与雾化氨水的运动方向相同,雾化氨水通过氨水压力雾化与高压氮气雾化共同作用获得,其中,氨水压力为0.3mpa,高压氮气的压力为0.7mpa。一级脱硫后的待处理烧结烟气进入电除尘器除尘,获得一级脱硫烧结烟气,其中雾化氨水制备装置与电除尘器之间的烟道长度为60m。一级脱硫烧结烟气温度为110℃,进入密箱半干法熟石灰脱硫塔中,与含水量为66%的含水熟石灰接触进行二级脱硫,获得二级脱硫烧结烟气;二级脱硫烧结烟气经烟气温度测量仪检测后,经布袋除尘器除尘;布袋除尘器后面设置有烟气升温系统,经布袋除尘器除尘后的烟气经过烟气升温系统升温至280~420℃温度条件后,进入脱硝装置,在脱硝装置中,烟气与催化剂和氨水发生反应进行脱硝,脱硝后的烟气经风机加压,经烟气so2、no
x
、颗粒物在线监测后排放至大气中,在线监测结果如表1所示。
[0065]
实施例4
[0066]
待处理烧结烟气在烟道内与质量浓度为15%雾化氨水发生脱硫反应,进行一级脱硫,其中雾化氨水的雾滴直径≤135μm,待处理烧结气与雾化氨水的运动方向相同,雾化氨水通过氨水压力雾化与高压氮气雾化共同作用获得,其中,氨水压力为0.3mpa,高压氮气的压力为0.7mpa。一级脱硫后的待处理烧结烟气进入电除尘器除尘,获得一级脱硫烧结烟气,其中雾化氨水制备装置与电除尘器之间的烟道长度为60m。一级脱硫烧结烟气温度为100℃,进入密箱半干法熟石灰脱硫塔中,与含水量为72%的含水熟石灰接触进行二级脱硫,获得二级脱硫烧结烟气;二级脱硫烧结烟气经烟气温度测量仪检测后,经布袋除尘器除尘;布袋除尘器后面设置有烟气升温系统,经布袋除尘器除尘后的烟气经过烟气升温系统升温至280~420℃温度条件后,进入脱硝装置,在脱硝装置中,烟气与催化剂和氨水发生反应进行脱硝,脱硝后的烟气经风机加压,经烟气so2、no
x
、颗粒物在线监测后排放至大气中,在线监测结果如表1所示。
[0067]
对比例1
[0068]
对比例1提供了一种烧结烟气的处理方法,待处理烧结烟气经过电除尘后,进入密箱熟石灰半干法脱硫塔进行脱硫,然后进入布袋除尘器进行布袋除尘,随后升温进入scr法脱硝装置脱硝处理后,烟气经风机加压,经烟气so2、no
x
、颗粒物在线监测后排放至大气中,在线监测结果如表1所示。
[0069]
表1
[0070]
编号so2/mg/nm3no
x
/mg/nm3粉尘/mg/nm3实施例115222.0实施例216202.7实施例320303.0实施例410262.5
对比例185462.5
[0071]
根据表1中的数据可知,
[0072]
本申请实施例1~4处理后的烧结烟气,so2为10~20mg/nm3,nox含量为20~30mg/nm3,粉尘的含量为2~3mg/nm3,实现了超低排放,对环境友好。
[0073]
对比例1处理后的烧结烟气so2为85mg/nm3,nox含量为46mg/nm3,粉尘的含量为2.5mg/nm3。
[0074]
本申请实施例经济效益测算:
[0075]
将本发明应用于烧结烟气处理,其产生效益具体如下:
[0076]
(1)直接经济效益:
[0077]
在使用本发明的技术方案之前,烧结过程采用含硫量较低的脱硫矿作为烧结的原料,以保证烧结烟气经过处理后可以达标排放;采用本发明的技术方案,烧结过程可以采用含硫量较高的铁矿石作为烧结原料,这种情况下的烧结烟气采用本发明的技术方案处理后,可以达标排放。而含硫量较高的铁矿石比含硫量较低的脱硫矿便宜约200元/t,烧结每天需要消耗600t的铁矿石,据此计算可以产生效益为:
[0078]
200元/t
×
600t
×
365天=4380万/年
[0079]
(2)间接经济效益:360m2烧结脱硫脱硝系统稳定运行,环保稳定达标。
[0080]
本发明实施例提供了一种烧结烟气的处理方法,采用雾化氨水对待处理烧结烟气进行一级脱硫,同时配合电除尘,再采用含水熟石灰进行二级脱硫,同时配合电除尘、布袋除尘和scr法脱硝,排入大气中的二氧化硫含量为10~20mg/nm3,no
x
含量为20~30mg/nm3,粉尘的含量为2~3mg/nm3,实现了超低排放,对环境友好。且设备投资小,工艺简单,故障率低,脱硫效率高,运行费用低。
[0081]
最后,还需要说明的是,术语“包括”、“包含”或者其任何其他变体意在涵盖非排他性的包含,从而使得包括一系列要素的过程、方法、物品或者设备不仅包括那些要素,而且还包括没有明确列出的其他要素,或者是还包括为这种过程、方法、物品或者设备所固有的要素。
[0082]
尽管已描述了本发明的优选实施例,但本领域内的技术人员一旦得知了基本创造性概念,则可对这些实施例作出另外的变更和修改。所以,所附权利要求意欲解释为包括优选实施例以及落入本发明范围的所有变更和修改。
[0083]
显然,本领域的技术人员可以对本发明进行各种改动和变型而不脱离本发明的精神和范围。这样,倘若本发明的这些修改和变型属于本发明权利要求及其等同技术的范围之内,则本发明也意图包含这些改动和变型在内。