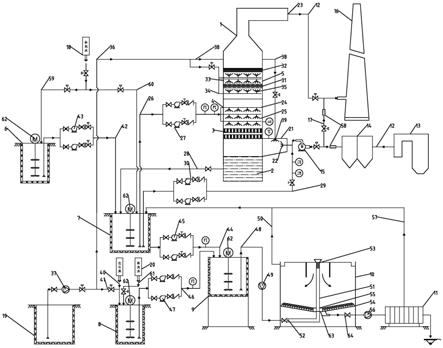
[0001]
本发明涉及一种脱硫装置,尤其是涉及一种钠碱法脱硫装置及其脱硫工艺,属于尾气处理技术领域。
背景技术:[0002]
锅炉是一种能量转换设备,向锅炉输入的能量有燃料中的化学能、电能,锅炉输出具有一定热能的蒸汽、高温水或有机热载体。锅的原义指在火上加热的盛水容器,炉指燃烧燃料的场所,锅炉包括锅和炉两大部分。锅炉中产生的热水或蒸汽可直接为工业生产和人民生活提供所需热能,也可通过蒸汽动力装置转换为机械能,或再通过发电机将机械能转换为电能。由于煤炭的燃烧成本较低,我国大多数企业仍然采用传统的煤炭作为锅炉燃料。但是煤炭在燃烧过程中会产生较多的硫化物,直接排放势必会对环境造成不可估量的污染。
[0003]
所以,目前国家对锅炉烟气的排放均设定有排放标准。而so2是大气污染当中最主要的有害成分,严重影响着生态环境与人类的身体健康,因此,脱除烟气中的so2是控制其污染环境的最有效的方法。目前,世界各国研发、使用的脱除so2的技术已经超过200多种,根据脱硫剂和脱硫方式的不同,大致可以分为干法脱硫、湿法脱硫和半干法脱硫,其中湿法烟气脱硫技术始于20世纪30年代,因其具有处理量大、脱除效率高、工艺成熟等特点而得到广泛应用,已经成为应用规模最大、商业化生产最多的脱硫方式,相比较这几种脱硫的方法,在全国乃至世界应用的比例最大是湿法脱硫技术,约占85%左右,主要有石灰石/石膏法、氧化镁法、海水法等。
[0004]
目前,工业生产当中应用最为广泛、技术最为成熟的脱硫工艺是石灰石/石膏法,该法主要的优点是吸收剂资源丰富、廉价易得、设备运行状况稳定等,但同时也存在一些不足,如占地面积大、极易结垢堵塞管道喷嘴、脱硫效率低等问题,无法满足企业需求。
技术实现要素:[0005]
本发明主要是针对现有脱硫装置存在占地面积大、极易结垢堵塞管道喷嘴、脱硫效率低的问题,提供一种钠碱法脱硫装置及其脱硫工艺,该装置利用钠盐易溶于水,在吸收塔内部采用钠碱吸收 so2,吸收后的脱硫液在再生池内利用廉价的石灰进行再生,从而使得钠离子循环吸收利用,设备占地面积小,循环过程中对泵和管道均无腐蚀与堵塞现象, 便于设备运行与保养,脱硫效率高。
[0006]
本发明的目的主要是通过下述方案得以实现的:一种钠碱法脱硫装置,包括so2吸收系统、吸收液供给系统、副产物处理系统、烟气系统和工艺水系统;所述so2吸收系统包括吸收塔本体,所述吸收塔本体内部从下至上依次设有储液层、文丘里棒层、雾化喷淋层和除雾层;所述吸收液供给系统包括吸收液制备系统、吸收液循环系统和吸收液再生系统,所述吸收液制备系统包括钠碱溶解槽,所述吸收液循环系统包括循环池,所述循环池与吸收塔本体对应连通,所述吸收液再生系统包括石灰浆池、
再生池和沉淀池,所述钠碱溶解槽、循环池和再生池依次连通,所述石灰浆池、再生池和沉淀池依次连通,且沉淀池与循环池对应连通;所述副产物处理系统包括压滤机,所述压滤机与循环池对应连通;所述烟气系统包括依次设置在烟气主管上的锅炉、除尘器、引风机和烟囱,且所述吸收塔本体位于引风机和烟囱之间,所述烟囱通过烟气旁管与烟气主管连接;所述工艺水系统包括第一工艺水装置、第二工艺水装置和水池,所述第一工艺水装置包括第一水源,所述第一水源分别与钠碱溶解槽和循环池连通,所述第二工艺水装置包括第二水源,所述第二水源与石灰浆池连通;所述钠碱溶解槽、循环池、石灰浆池和再生池内均设有搅拌装置。
[0007]
通过采用上述技术方案,锅炉的烟气从烟气主管进入除尘器,在除尘器中去除烟气中99.9%的粉尘,烟尘含量低于20mg/nm3,然后经引风机送入吸收塔本体;烟气进入吸收塔本体后,首先经过一层文丘里棒层,即烟气与脱硫吸收液混合反应层,烟气由下而上与喷淋浆液逆流接触,两者充分混合,在文丘里棒层上部设置雾化喷淋层,在该区段空间充满着粒径为100-300μm的雾化液滴,烟气中so2与吸收液再次反应,脱除90%以上的so2,从而达到脱硫的目的;脱硫后的烟气继续上升经除雾层进行气液分离,利用其导向作用产生强大的离心力,将烟气中的液滴分离出来,达到同时除尘除雾的效果,净烟气经除雾后进入吸收塔本体顶部的烟气主管排放至烟囱内;脱硫后的液体落入吸收塔本体底部的储液层,定时定期排入吸收液再生系统中的循环池内,适当补充一定量的吸收液后再次送入雾化喷淋层中进行再次利用,脱硫吸收液始终处于循环状态;循环池内部分循环吸收液流入到再生池,再生池内加入来自石灰浆池的石灰乳浆液,使吸收液再生并流至沉淀池,钙盐在沉淀池快速沉淀,经过初次浓缩的渣浆液泵入压滤机进行二次浓缩脱水,经脱水后的渣浆外运,沉淀池内的过滤液和压滤机产生的压滤液返回吸收液再生系统中的循环池;钠碱溶解槽和石灰浆池内的搅拌装置能够加快钠碱和生石灰的溶解,循环池内的搅拌装置能够加快溶液的混合,再生池内的搅拌装置能够加快吸收液的再生。
[0008]
作为优选,所述储液层位于吸收塔本体的底部,且吸收塔本体位于储液层和文丘里棒层之间的侧壁上安装有冷却箱,所述烟气主管伸入到冷却箱内,且伸入冷却箱的烟气主管端部安装有进气喷嘴;所述吸收塔本体顶部设有出气口,所述出气口与烟气主管连接。
[0009]
通过采用上述技术方案,设置有冷却箱,烟气进入吸收塔本体之前先进行冷却降温,避免进入吸收塔本体时温度过高,影响气液传质,导致脱硫效率下降。
[0010]
作为优选,所述雾化喷淋层设有三层,每层所述雾化喷淋层均由雾化喷淋支管和安装于所述雾化喷淋支管上的若干雾化喷嘴,所述雾化喷淋支管与雾化喷淋总管的一端连通,雾化喷淋总管的另一端与循环池连通,且雾化喷淋总管上设有至少一个第一循环泵;所述储液层内的液体通过排液管排至循环池内,循环池与烟气主管之间连接有进液管,所述进液管位于引风机和冷却箱之间,且进液管上设有至少一个第二循环泵。
[0011]
通过采用上述技术方案,雾化喷淋层的设计使其达到所要求的喷淋浆液覆盖率,使吸收液与烟气充分接触,从而保证在适当的液/气比下可靠地实现所要求的脱硫效率,雾化喷淋支管及雾化喷嘴的布置设计成均匀覆盖吸收塔本体的横截面,使喷出的喷淋浆液充分布满整个雾化喷淋层,从而保证对烟气的脱硫效果;为了能够充分吸收含硫烟气,进液管内的吸收液与烟气主管内的烟气汇流后一同经进气喷嘴进入冷却箱;从雾化喷淋层和冷却箱脱硫后的液体均落入吸收塔本体底部的储液层,定时定期通过排液管将吸收液排出至再
生系统中的循环池内,适当补充一定量的吸收液后再次送入雾化喷淋层和冷却箱中进行再次利用,脱硫吸收液始终处于循环状态。
[0012]
作为优选,所述除雾层包括位于下面的一级除雾器和位于上面的二级除雾器,且一级除雾器的上下方和二级除雾器的下方均设有冲洗层,每层所述冲洗层均包括冲洗支管和安装于所述冲洗支管上的若干冲洗喷嘴,所述冲洗支管与高压水总管的一端连通,所述高压水总管的另一端与水池连通,且高压水总管上设有高压水泵;所述高压水总管上还连接有冷却管,所述冷却管伸入到冷却箱内,且伸入到冷却箱内的冷却管端部设有冷却喷嘴。
[0013]
通过采用上述技术方案,位于下面的一级除雾器是一个大液滴分离器,叶片间隙稍大,用来分离上升烟气所携带的较大液滴,上方的二级除雾器是一个细液滴分离器,叶片距离较小,用来分离上升烟气中的微小浆液液滴和除雾层的冲洗水滴。烟气流经除雾层时,液滴由于惯性作用,留在除雾器的挡板,由于被滞留的液滴也含有固态物,因此存在挡板上结垢的危险,同时为保证烟气通过除雾层时产生的压降不超过设定值,需定期进行在线清洗,因此一级除雾器的上下方和二级除雾器的下方均设有冲洗层,正常运行时一级除雾器的上方和下方,二级除雾器的下方自动按程序轮流清洗各区域,冲洗层冲洗可根据烟气负荷、一级除雾器和二级除雾器两端的压差自动调节冲洗的频率。冲洗水由水池内工艺水提供,并通过高压水泵泵入,冲洗水还用于补充吸收塔本体中的水分蒸发损失;另外高压水总管上还连接有冷却管,用于实现冷却箱内烟气的冷却降温。
[0014]
作为优选,所述石灰浆池上连通有生石灰给料管,且所述生石灰给料管和高压水总管之间连接有高压水旁管。
[0015]
通过采用上述技术方案,生石灰通过生石灰给料管送入石灰浆池进行石灰浆液的制作,并通过高压水加快生石灰的加入。
[0016]
作为优选,所述钠碱溶解槽与循环池之间通过第一加药管连通,且第一加药管上设有至少一个第一加药泵;所述循环池与再生池之间通过再生管连通,且再生管上设有至少一个第三循环泵;所述石灰浆池与再生池之间通过第二加药管连通,且第二加药管上设有至少一个第二加药泵;所述再生池与沉淀池之间通过提升管连通,且提升管上设有提升泵;所述沉淀池与循环池之间通过第一回流管连通。
[0017]
通过采用上述技术方案,钠碱溶解槽内的吸收液通过第一加药管流入循环池,并通过第一加药管上的第一加药泵泵入;循环池内的部分吸收液通过再生管进入再生池进行再生,并通过再生管上的第三循环泵泵入;石灰浆池内的石灰浆液通过第二加药管进入再生池,并通过第二加药管上的第二加药泵泵入;再生池内的再生液通过提升管流入沉淀池,并通过提升管上的提升泵泵入。
[0018]
作为优选,所述沉淀池内设有滤浆筒,所述提升管与所述滤浆筒底部的进浆口连接,滤浆筒的顶部设有若干出浆口;所述沉淀池的下面还设有漏斗状的排浆板,所述且排浆板与滤浆筒之间设有排浆口,所述排浆口下方设有排浆漏斗,所述排浆漏斗与压滤机通过排浆管连通,所述排浆管上设有排浆泵,且压滤机通过第二回流管与循环池连通。
[0019]
通过采用上述技术方案,再生液通过进浆口流经滤浆筒并从出浆口流出进入沉淀池内槽内部,沉淀池内槽底部设有漏斗状的排浆板,排浆板上部沉淀堆积的淤泥从排浆口流入排浆漏斗再流出至排浆管,沉淀池内槽上部相对清澈的水从溢水台流出,并通过第一回流管回流至循环池;经过初次浓缩的渣浆液通过排浆管上的排浆泵泵入压滤机进行二次
浓缩脱水,经脱水后的渣浆外运,压滤机产生的压滤液通过第二回流管返回吸收液再生系统中的循环池。
[0020]
作为优选,所述除尘器与引风机之间的烟气主管上设有膨胀节,所述烟气旁管上设有膨胀节。
[0021]
通过采用上述技术方案,膨胀节的设置增强烟气旁路和烟气主路的伸缩、膨胀性能,膨胀节用于补偿烟气主路和烟气旁路的热膨胀引起的位移,膨胀节在所有运行和事故条件下都能吸收全部连接设备和烟道的轴向和径向位移。
[0022]
作为优选,所述第一水源通过第一补水管与钠碱溶解槽连通,第一水源通过第二补水管与循环池连通,所述第二水源通过第三补水管与石灰浆池连通。
[0023]
通过采用上述技术方案,第一水源用于补充钠碱溶解槽和循环池内的水,第二水源用于补充石灰浆池内的水。
[0024]
一种钠碱法脱硫工艺,包括下述步骤:1)吸收液的制备与补充:将钠碱投入到钠碱溶解槽中进行溶解,并通过搅拌装置加快钠碱的溶解,制备完成的钠碱吸收液泵入循环池内;吸收液经多次循环后,吸收液ph值降低,从钠碱溶解槽中向循环池内补入新鲜的钠碱吸收液,来调节吸收液的ph值;2)含硫烟气的送气:通过引风机将含硫烟气送入吸收塔本体中参与脱硫反应;3)烟气的脱硫:含硫烟气从吸收塔本体下部进入,依次通过文丘里棒层和雾化喷淋层与来自于循环池中的吸收液进行雾化喷淋脱硫反应,再经除雾层除雾后排入烟囱;脱硫产物流入储液层存储,储存在储液层的脱硫产物流入循环池进行吸收液再生和吸收液循环;4)吸收液的再生:将循环池中的吸收液送入再生池中与来自于石灰浆池中的石灰浆液和通入的大量空气中的氧发生置换反应;5)吸收液的循环:将再生池中的溶液泵入沉淀池,沉淀池内的过滤液回流至循环池中参与并重复步骤烟气的脱硫和步骤吸收液的再生;6)渣浆液的脱水回收:沉淀池内的渣浆液泵入压滤机,压滤液回流至循环池中参与并重复步骤烟气的脱硫和步骤吸收液的再生;同时将获得的滤饼外运。
[0025]
因此,本发明具备下述优点:(1)本发明利用钠碱脱硫,循环液基本上是钠离子的水溶液,在循环过程中对泵、管道、设备均无腐蚀与堵塞现象,便于设备运行与保养;(2)本发明吸收液的再生和脱硫渣的沉淀均发生在吸收塔本体外,避免了吸收塔本体内堵塞和磨损,提高了运行的可靠性,降低了操作费用;(3)本发明的吸收液吸收so2速度快,可用较小的液气比,达到较高的脱硫效率,脱硫效率在98%以上;(4)本发明损耗相对较少、运行成本低,占地面积小、建设投资少,操作简便、运行稳定高效。
附图说明
[0026]
图1是本发明的一种结构示意图。
[0027]
图示说明:1-吸收塔本体,2-储液层,3-文丘里棒层,4-雾化喷淋层,5-除雾层,6-钠碱溶解槽,7-循环池,8-石灰浆池,9-再生池,10-沉淀池,11-压滤机,12-烟气主管,13-锅
炉,14-除尘器,15-引风机,16-烟囱,17-烟气旁管,18-第一水源,19-水池,20-第二水源,21-冷却箱,22-进气喷嘴,23-出气口,24-雾化喷淋支管,25-雾化喷嘴,26-雾化喷淋总管,27-第一循环泵,28-排液管,29-进液管,30-第二循环泵,31-一级除雾器,32-二级除雾器,33-冲洗层,34-冲洗支管,35-冲洗喷嘴,36-高压水总管,37-高压水泵,38-冷却管,39-冷却喷嘴,40-生石灰给料管,41-高压水旁管,42-第一加药管,43-第一加药泵,44-再生管,45-第三循环泵,46-第二加药管,47-第二加药泵,48-提升管,49-提升泵,50-第一回流管,51-滤浆筒,52-进浆口,53-出浆口,54-排浆板,55-排浆口,56-排浆泵,57-第二回流管,58-膨胀节,59-第一补水管,60-第二补水管,61-第三补水管,62-搅拌装置,63-排浆漏斗,64-排浆管。
具体实施方式
[0028]
下面通过具体实施例,并结合附图,对本发明的技术方案作进一步的具体说明。应当理解,本发明的实施并不局限于下面的实施例,对本发明所做的任何形式上的变通和/或改变都将落入本发明保护范围。
[0029]
在本发明中,若非特指,所有的份、百分比均为重量单位,所采用的设备和原料等均可从市场购得或是本领域常用的。下述实施例中的方法,如无特别说明,均为本领域的常规方法。下述实施例中的部件或设备如无特别说明,均为通用标准件或本领域技术人员知晓的部件,其结构和原理都为本技术人员均可通过技术手册得知或通过常规实验方法获知。
[0030]
实施例1:如图1所示,本发明提供一种技术方案,一种钠碱法脱硫装置,由so2吸收系统、吸收液供给系统、副产物处理系统、烟气系统和工艺水系统组成。
[0031]
所述so2吸收系统包括吸收塔本体1,吸收塔本体1内部从下至上依次设有储液层2、文丘里棒层3、雾化喷淋层4和除雾层5;所述吸收液供给系统由吸收液制备系统、吸收液循环系统和吸收液再生系统组成,吸收液制备系统包括钠碱溶解槽6,吸收液循环系统包括循环池7,循环池7与吸收塔本体1对应连通,吸收液再生系统由石灰浆池8、再生池9和沉淀池10组成,钠碱溶解槽6、循环池7和再生池9依次连通,石灰浆池8、再生池9和沉淀池10依次连通,且沉淀池10与循环池7对应连通;所述副产物处理系统包括压滤机11,压滤机11与循环池7对应连通;所述烟气系统由依次设置在烟气主管12上的锅炉13、除尘器14、引风机15和烟囱16组成,且吸收塔本体1位于引风机15和烟囱16之间,烟囱16通过烟气旁管17与烟气主管12连接;所述工艺水系统由第一工艺水装置、第二工艺水装置和水池19组成,第一工艺水装置包括第一水源18,第一水源18分别与钠碱溶解槽6和循环池7连通,第二工艺水装置包括第二水源20,第二水源20与石灰浆池8连通。
[0032]
锅炉13的烟气从烟气主管12进入除尘器14,在除尘器14中去除烟气中99.9%的粉尘,烟尘含量低于20mg/nm3,然后经引风机15送入吸收塔本体1;烟气进入吸收塔本体1后,首先经过一层文丘里棒层3,即烟气与脱硫吸收液混合反应层,烟气由下而上与喷淋浆液逆流接触,两者充分混合,在文丘里棒层3上部设置雾化喷淋层4,在该区段空间充满着粒径为100-300μm的雾化液滴,烟气中so2与吸收液再次反应,脱除90%以上的so2,从而达到脱硫的目的;脱硫后的烟气继续上升经除雾层5进行气液分离,利用其导向作用产生强大的离心
力,将烟气中的液滴分离出来,达到同时除尘除雾的效果,净烟气经除雾后进入吸收塔本体1顶部的烟气主管12排放至烟囱16内;脱硫后的液体落入吸收塔本体1底部的储液层2,定时定期排入吸收液再生系统中的循环池7内,适当补充一定量的吸收液后再次送入雾化喷淋层4中进行再次利用,脱硫吸收液始终处于循环状态;循环池7内部分循环吸收液流入到再生池9,再生池9内加入来自石灰浆池8的石灰乳浆液,使吸收液再生并流至沉淀池10,钙盐在沉淀池10快速沉淀,经过初次浓缩的渣浆液泵入压滤机11进行二次浓缩脱水,经脱水后的渣浆外运,沉淀池10内的过滤液和压滤机11产生的压滤液返回吸收液再生系统中的循环池7。
[0033]
实施例2:如图1所示,本发明提供另一种技术方案,一种钠碱法脱硫装置,由so2吸收系统、吸收液供给系统、副产物处理系统、烟气系统和工艺水系统组成。
[0034]
所述so2吸收系统包括吸收塔本体1,吸收塔本体1内部从下至上依次设有储液层2、文丘里棒层3、雾化喷淋层4和除雾层5;储液层2位于吸收塔本体1的底部,储液层2内的液体通过排液管28排至循环池7内,循环池7与烟气主管12之间连接有进液管29,进液管29位于引风机15和冷却箱21之间,且进液管29上设有至少一个第二循环泵30;吸收塔本体1位于储液层2和文丘里棒层3之间的侧壁上安装有冷却箱21,烟气主管12伸入到冷却箱21内,且伸入冷却箱21的烟气主管12端部安装有进气喷嘴22;吸收塔本体1顶部设有出气口23,出气口23与烟气主管12连接;雾化喷淋层4设有三层,每层雾化喷淋层4均由雾化喷淋支管24和安装于雾化喷淋支管24上的若干雾化喷嘴25组成,雾化喷淋支管24与雾化喷淋总管26的一端连通,雾化喷淋总管26的另一端与循环池7连通,且雾化喷淋总管26上设有至少一个第一循环泵27;除雾层5由位于下面的一级除雾器31和位于上面的二级除雾器32组成,且一级除雾器31的上下方和二级除雾器32的下方均设有冲洗层33,每层冲洗层33均由冲洗支管34和安装于冲洗支管34上的若干冲洗喷嘴35组成,冲洗支管34与高压水总管36的一端连通,高压水总管36的另一端与水池19连通,且高压水总管36上设有高压水泵37;高压水总管36上还连接有冷却管38,冷却管38伸入到冷却箱21内,且伸入到冷却箱21内的冷却管38端部设有冷却喷嘴39,冷却喷嘴39不仅能实现冷却箱21内烟气的冷却降温,还能通过高压水冲洗冷却箱21,避免结垢。
[0035]
吸收塔本体1内所有部件能够承受最大入口气流及最高进口烟气温度的冲击,高温烟气不会对任何系统和设备造成损害;吸收塔本体1选用的材料适合工艺过程的特性,并且能承受烟气飞灰和脱硫工艺固体悬浮物的磨损,当然所有部件包括塔体和内部结构设计考虑腐蚀余度。本实施例中吸收塔本体1材质为10mm厚的优质q235-a钢板卷制圆柱形塔,塔体内壁衬35mm花岗岩,中间用耐酸胶泥粘结,能适应-20~180℃的温度,耐酸碱腐蚀、耐磨损、抗剥离强度高,使用寿命在30年以上。
[0036]
本实施例中吸收塔本体1可配备有足够数量和大小合适的人孔,人孔不能有泄漏,而且在附近还设有与人孔对应的爬梯和平台,方便吸收塔本体1检修、维护和调试。吸收塔本体1还包括所有必需的测量装置,如吸收塔本体1液位、ph值、温度、压力、除雾层5冲洗水压等测点。
[0037]
吸收塔本体1设置有文丘里棒层3,由于文丘里结构,使之烟气流速在通过文丘里棒层3时,大大提高了烟气流速,由于浆液的附壁效应,也即在文丘里棒上粘附了吸收液,当
烟气以高速相向接触时,剥离了原来的浆液表面,形成了新的气液接触面,打破了原来的二相传质表面,因而使气液二相传质速率加快,也即提高了so2的吸收,提高了脱硫效率。烟气脱硫时文丘里棒层3上部形成了一个气液湍流层,在这一湍流层中,气液的传质反应非常激烈,与常规的吸收塔相比,文丘里湍流层以液体包围气体的形式而大大提高了so2的吸收效果;另外文丘里棒层3改善了吸收塔本体1内部的气体分布状态,进入吸收塔本体1的烟气由于文丘里棒层3的分割作用,把原烟气充分打破,形成多股分流烟气与液体接触,增加了脱硫率;文丘里棒层3的应用,使整个吸收塔本体1相比常规吸收塔具有更紧凑的效果,尽管文丘里棒层3会增加部分的压力损失,但在同等脱硫效率情况下,液气比(l/g)比常规吸收塔减少20-25%,整个脱硫能耗可节省10-15%,同时烟气所带粉尘由于被润湿,经过文丘里棒层3时被黏附在棒表面,而上部喷淋落入层面又把粉尘给剥离而落入塔底部排出。
[0038]
雾化喷淋层4的雾化喷嘴25采用材质为不锈钢或陶瓷材料组成,实心球形喷雾,雾径为50-150μm,雾化效果好,雾化角度120
°
;具有耐腐蚀、不堵塞、全面雾化、不滴流的优点,雾化喷嘴25、雾化喷淋支管24及雾化喷淋总管26均设置有花岗岩保护套。
[0039]
除雾层5用于分离烟气携带的液滴,位于下面的一级除雾器31是一个大液滴分离器,叶片间隙稍大,用来分离上升烟气所携带的较大液滴,上方的二级除雾器32是一个细液滴分离器,叶片距离较小,用来分离上升烟气中的微小浆液液滴和除雾层的冲洗水滴。烟气流经除雾层时,液滴由于惯性作用,留在除雾器的挡板,由于被滞留的液滴也含有固态物,因此存在挡板上结垢的危险,同时为保证烟气通过除雾层时产生的压降不超过设定值,需定期进行在线清洗,因此一级除雾器31的上下方和二级除雾器32的下方均设有冲洗层33,正常运行时一级除雾器31的上方和下方,二级除雾器32的下方自动按程序轮流清洗各区域,冲洗层33冲洗可根据烟气负荷、一级除雾器31和二级除雾器32两端的压差自动调节冲洗的频率。冲洗水由水池19内工艺水提供,并通过高压水泵37泵入,冲洗水还用于补充吸收塔本体1中的水分蒸发损失。
[0040]
所述吸收液供给系统由吸收液制备系统、吸收液循环系统和吸收液再生系统组成,吸收液制备系统包括钠碱溶解槽6,吸收液循环系统包括循环池7,循环池7与吸收塔本体1对应连通,吸收液再生系统由石灰浆池8、再生池9和沉淀池10组成,钠碱溶解槽6、循环池7和再生池9依次连通,石灰浆池8、再生池9和沉淀池10依次连通,且沉淀池10与循环池7对应连通;钠碱溶解槽6与循环池7之间通过第一加药管42连通,且第一加药管42上设有至少一个第一加药泵43;循环池7与再生池9之间通过再生管44连通,且再生管44上设有至少一个第三循环泵45;石灰浆池8与再生池9之间通过第二加药管46连通,且第二加药管46上设有至少一个第二加药泵47,石灰浆池8上还连通有生石灰给料管40,且生石灰给料管40和高压水总管36之间连接有高压水旁管41;再生池9与沉淀池10之间通过提升管48连通,且提升管48上设有提升泵49;沉淀池10与循环池7之间通过第一回流管50连通,沉淀池10内设有滤浆筒51,提升管48与滤浆筒51底部的进浆口52连接,滤浆筒51的顶部设有若干出浆口53;沉淀池10的下面还设有漏斗状的排浆板54,排浆板54与沉淀池10的内壁紧密贴合,且排浆板54与滤浆筒51之间设有排浆口55,排浆口55下方设有排浆漏斗63,排浆漏斗63与压滤机11通过排浆管64连通,排浆管64上设有排浆泵56;上述钠碱溶解槽6、循环池7、石灰浆池8和再生池9内均设有搅拌装置62。
[0041]
上述第一加药泵43、第二加药泵47、第一循环泵27、第二循环泵30和第三循环泵45
均按照一主一备设置,各管道采用增强塑料管。
[0042]
上述钠碱溶解槽6、循环池7、石灰浆池8和再生池9内均设有搅拌装置62,搅拌装置62可采用旋桨结构,能够加快溶液的制备以及避免溶液的沉淀、结垢或堵塞。
[0043]
所述副产物处理系统包括压滤机11,钙盐经过压滤机二次浓缩脱水后,压滤液通过第二回流管57回流至循环池7,脱水后的渣浆外运。
[0044]
所述烟气系统由依次设置在烟气主管12上的锅炉13、除尘器14、引风机15和烟囱16组成,且吸收塔本体1位于引风机15和烟囱16之间,烟囱16通过烟气旁管17与烟气主管12连接;除尘器14与引风机15之间的烟气主管12上设有膨胀节58,烟气旁管17上亦设有膨胀节58。
[0045]
烟气主管12上增设引风机15,属于正压操作,可以避免引风机15的腐蚀问题,烟气主管12及烟气旁管17根据可能发生的最差运行条件进行设计;吸收塔本体1出气口23至烟气主管12的净烟道采用内衬玻璃鳞片;烟气主管12和烟气旁管17最小壁厚至少位5mm,能够承压为
±
5000pa,烟气主管12和烟气旁管17外侧设有保护层,其材料为彩色压型钢板,厚度为0.6mm;另外烟气主管12和烟气旁管17的布置能确保冷凝液的排放,不允许有水或冷凝液的聚积,需要有低位点的排水和预防冷凝液的聚积措施,任何情况下膨胀节58都不能布置在低位点;整个脱硫装置短暂检修时,烟气从烟气旁路17短暂流向到烟囱16,检修完毕后,烟气再从烟气主路12流入吸收塔本体1。
[0046]
所述工艺水系统由第一工艺水装置、第二工艺水装置和水池19组成,第一工艺水装置包括第一水源18,第一水源18分别与钠碱溶解槽6和循环池7连通,第二工艺水装置包括第二水源20,第二水源20与石灰浆池8连通;第一水源18通过第一补水管59与钠碱溶解槽6连通,第一水源18通过第二补水管60与循环池7连通,第二水源20通过第三补水管61与石灰浆池8连通。
[0047]
该钠碱法脱硫装置还设有控制系统,控制系统由plc及上位机组成;控制系统由现场控制站传入dcs系统监控,现场控制站主要完成现场工艺数据采集、数据处理和控制输出,dcs系统通过与现场控制站之间的数据通讯,完成人机对话功能,实现操作控制、数据管理,与现场控制站通过实时控制冗余网络互联,完成实时数据交换,实现工艺数据的采集,实时控制,工艺流程的动态监测,各个过程量的趋势记录,并可挂接局域网;当整个脱硫装置出现故障或发生其他事故需要紧急停运时,烟气旁路17短暂流向到烟囱16,不会影响锅炉13运行,检修完毕后,烟气再从烟气主路12流入吸收塔本体1。
[0048]
本发明还提供一种通过上述钠碱法脱硫装置进行脱硫工艺:s1:吸收液的制备与补充:将na2co3或naoh投入到钠碱溶解槽6中进行溶解,并通过搅拌装置62加快na2co3或naoh的溶解,制备完成的吸收液泵入循环池7内;吸收液经多次循环后,吸收液ph值降低,从钠碱溶解槽6中向循环池7内补入新鲜的氢氧化钠吸收液,来调节吸收液的ph值;s2:含硫烟气的送气:通过引风机15将含硫烟气送入吸收塔本体1中参与脱硫反应;s3:烟气的脱硫:含硫烟气从吸收塔本体1下部进入,依次通过文丘里棒层3和雾化喷淋层4与来自于循环池7中的吸收液进行雾化喷淋脱硫反应,再经除雾层5除雾后排入烟囱16;脱硫产物流入储液层2存储,储存在储液层2的脱硫产物流入循环池7进行吸收液再生和吸收液循环;
脱硫反应中产生的化学反应方程式如下:na2co3+so2→
na2so3+co2↑ꢀ①
2naoh+so2→
na2so3+h2o
ꢀ②
na2so3+so2+h2o
→
2nahso3ꢀ③
其中:式
①
为启动阶段na2co3溶液吸收so2的反应;式
②
为再生液ph值较高时(高于9时),溶液吸收so2的主反应;式
③
为溶液ph值较低(5-9)时的主反应;s4:吸收液的再生:将循环池7中的吸收液送入再生池9中与来自于石灰浆池8中的ca(oh)2溶液和通入的大量空气中的氧发生置换反应;置换反应中产生的化学反应方程式如下:ca(oh)2+na2so3→
2naoh+caso3ꢀ④
ca(oh)2+2nahso3→
na2so3+caso3·
1/2h2o+3/2h2o
ꢀ⑤
caso3+1/2o2→
caso4ꢀ⑥
caso3·
1/2h2o+1/2o2→
caso4+1/2h2o
ꢀ⑦
如式
④
、
⑤
,在石灰浆液(石灰达到饱和状况)中,中性(两性)的nahso3很快跟石灰反应从而释放出[na
+
],随后生成的[so
32-]又继续跟石灰反应,反应生成的亚硫酸钙以半水化合物形式慢慢沉淀下来,从而使[na
+
]得到再生,吸收液恢复对so2的吸收能力,循环使用;如式
⑥
、
⑦
,再生池9内通入氧气的情况下,亚硫酸钙还会与氧气发生反应,生成硫酸钙;s5:吸收液的循环:将再生池9中含有亚硫酸钙和硫酸钙的溶液泵入沉淀池10,沉淀池10内上端的过滤液回流至循环池7中参与并重复步骤s3烟气的脱硫和步骤s4吸收液的再生;s6:渣浆液的脱水回收:沉淀池10内含有亚硫酸钙和硫酸钙的渣浆液泵入压滤机11,压滤液回流至循环池7中参与并重复步骤s3烟气的脱硫和步骤s4吸收液的再生,同时将获得的滤饼外运。
[0049]
应理解,该实施例仅用于说明本发明而不用于限制本发明的范围。此外应理解,在阅读了本发明讲授的内容之后,本领域技术人员可以对本发明作各种改动或修改,这些等价形式同样落于本申请所附权利要求书所限定的范围。