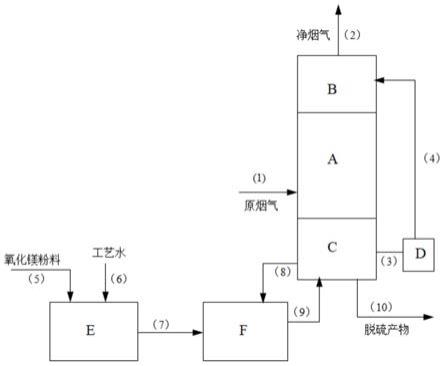
1.本发明涉及烟气脱硫,尤其涉及对现有镁法烟气脱硫工艺的改进。
背景技术:2.传统镁法烟气脱硫的脱硫塔包括吸收、中和、喷淋三个单元,吸收液在位于脱硫塔中部的吸收单元与烟气进行气液传质吸收烟气中二氧化硫,完成脱硫吸收的吸收液进入中和单元(塔底储液段)与(氢)氧化镁脱硫剂进行中和反应,并由循环单元的喷淋泵引入位于脱硫塔上部的喷淋层循环用于对烟气的脱硫吸收。基于将一次脱硫产物亚硫酸镁氧化为硫酸镁的目的,通常在塔底储液段设置氧化曝气单元来氧化一次脱硫产物。
3.传统镁法烟气脱硫工艺,其脱硫剂配置是采用外部工艺水与氧化镁粉料混合,并通入蒸气消化生成氢氧化镁浆液以提高其吸收反应活性。由于脱硫系统的烟气蒸发量小于外部工艺水的补充量,基于降低废水排放量、降低消化反应能耗的目的,脱硫剂浆液的配制浓度通常控制在10
‑
20%(以氧化镁计)。上述脱硫剂浆液的投加方式是直接投加到脱硫塔底储液段(中和单元)与脱硫吸收液进行中和反应,虽然脱硫剂的投加当量大于二氧化硫吸收当量(镁硫比1.03),但离开中和单元进入喷淋单元的吸收液中仍含有大量未反应的脱硫剂,吸收液的ph仍只有5.5
‑
5.8,造成吸收单元的气液传质效率低,需要通过提高气液传质面积来满足脱硫效率的需要,为此,其喷淋液气比(喷淋量与烟气量的比)较大,通常在7
‑
10升(吸收液)/标立方米(烟气),脱硫系统的喷淋能耗高。同时,为维持脱硫系统的物料平衡,脱硫系统需要通过排放塔内吸收液来排出脱硫产物,由于塔内吸收液中含有大量的未反应脱硫剂,为此,排出液量越大,脱硫剂损耗越大。为了最大限度地降低脱硫剂的损失,传统镁法采用的是将塔内吸收液的固形物积累到5%
‑
10%后外排,实现废水及废渣的同时外排,此举虽然最大限度地降低了脱硫系统的排液量,降低了脱硫剂的损耗,但其不利后果是塔内吸收液的固含量高,设备的磨损、堵塞严重,影响脱硫系统的运行可靠性。
4.我们研究认为:传统镁法并未有效利用亚硫酸镁的微溶性及弱碱性优势,表现在塔底中和反应未完成前即将吸收液用于喷淋吸收,吸收过程实际进行的是气—液—固三相传质的(氢)氧化镁吸收反应,而非传质效率更高的亚硫酸镁吸收反应(气—液两相)。提高塔底中和反应的转化率可以有效提高吸收传质效率,而制约塔底中和反应转化率提高的根本原因在于:1)塔底吸收液与脱硫剂浆液在脱硫塔底储液段(中和单元)的混合比大;2)塔底中和反应停留时间短。常规烟气脱硫的烟气量通常在30
‑
240万标立方米/小时的水平,其对应的脱硫塔径达6
‑
18米,而对应的喷淋量为2000
‑
16000吨/小时,其喷淋量是脱硫剂浆液投加量的1000倍左右,脱硫剂需在脱硫塔底储液段完成1000倍的稀释,才能实现中和反应的目的。但是,同样是由于其庞大的喷淋量,即使在脱硫塔底储液段达到7
‑
8米的极限高度,脱硫剂浆液与塔内吸收液的混合以及中和反应的停留时间也只能达到5分钟左右,加之塔径巨大以及侧向搅拌所形成的层流均不利于脱硫剂浆液与塔内吸收液的混合,为此,大量的脱硫剂与吸收液未完全混合、中和即进入喷淋单元,其结果是:虽然吸收液中的脱硫剂当量远高于亚硫酸氢镁的当量,但吸收液ph低,需通过较大的喷淋量来满足脱硫效率的要求。
5.本发明人发明专利《外部再生循环亚硫酸镁法烟气或废气脱硫工艺》(授权专利cn200810124177),通过在脱硫塔外部设置再生单元,将部分或全部的吸收液引出脱硫塔后与氧化镁脱硫剂进行中和反应,将吸收液中的亚硫酸氢镁再生为亚硫酸镁,固液分离去除中和反应生成的亚硫酸镁结晶物及其它固态杂质,固液分离后的吸收液回流到脱硫塔用于吸收烟气中的二氧化硫。上述专利通过外部再生(中和)反应,提高了中和反应效率,解决了塔内中和反应不完全问题,提高了吸收液的ph,将脱硫系统的空塔喷淋液气比将低近一半。同时,由于中和反应完全在塔外进行,而固液分离环节将固态物完全去除,使塔内吸收液的固含量趋近于零,有效解决了吸收液高固含量所导致的设备堵塞、磨损等问题。基于该发明良好的应用效果,上述技术被环保部命名为“亚硫酸镁清液法”烟气脱硫技术,并被列入“国家重大环保实用技术”。
6.但是,“亚硫酸镁清液法”技术也存在三个方面的技术缺陷:1)基于亚硫酸镁的微溶特性,进行外部再生的吸收液量需达到塔内喷淋量的25%
‑
100%,外部再生量大所导致的装置规模大、场地要求高这一技术缺陷制约了该项技术的推广应用。2)由于中和反应生成物中含有烟尘、氧化镁杂质等微小颗粒物,为了防止小颗粒物在循环系统内的积累,必须在固液分离过程中将其从吸收液中彻底分离,而粒径更大的亚硫酸镁结晶物以及过量的氧化镁脱硫剂也随之从吸收液中完全去除,为此,实际回流脱硫塔的回流液的固含量接近于零,其有效吸收介质亚硫酸镁完全是以饱和溶液的形式回到脱硫塔。而在引出25%吸收液再生的情况下,再生液与循环系统内的吸收液混合后的亚硫酸镁浓度,只能达到饱和浓度的55%左右,塔内吸收液有效吸收介质浓度低、ph低,仍需较高的喷淋液气比。虽然通过进一步提高再生量可提高脱硫效率,但再生系统规模进一步扩大。3)受进入塔内的亚硫酸镁量的限制,不可能在塔内将亚硫酸镁氧化为硫酸镁,脱硫产物最终只能以亚硫酸镁结晶物的形式从固液分离环节脱离脱硫系统,而亚硫酸镁结晶物脱离脱硫循环系统后极难氧化的特点,使脱硫产物的综合利用难以实现。4)为了最大限度地降低外部再生量,通常采用过量投加脱硫剂的方式,来提高中和反应速率和中和反应完成度,虽然其再生液的ph能达到7.2
‑
7.8的弱碱性水平,但脱硫系统的镁硫比达1.05以上,脱硫剂损耗大。
技术实现要素::
7.为了克服上述现有技术的不足,本发明提供了一种二次混合镁法烟气脱硫工艺,其技术方案如下:
8.一种二次混合镁法烟气脱硫工艺,其脱硫剂与吸收液的中和反应包括以下步骤:
9.步骤1:从脱硫塔引出部分吸收液与氧化镁脱硫剂一次混合:
10.一次混合会出现三种可能性,1)在混合过程无停留时间的情况下,一次混合液中只有氧化镁无亚硫酸镁结晶物;2)在混合过程有停留时间且引出吸收液相对于氧化镁过量的情况下,一次混合液中只有亚硫酸镁结晶物,无氧化镁;3)在混合过程有停留时间但引出吸收液相对于氧化镁不过量的情况下,则一次混合液中既有氧化镁,也有亚硫酸镁结晶物。
11.步骤2:将上述一次混合液不经固液分离回流到脱硫塔,与塔内吸收液进行二次混合;
12.一次混合吸收液量越大,二次混合比越小,越有利于中和反应在塔底储液段进行。
13.步骤3:二次混合后,一次混合未反应的氧化镁与塔内吸收液中的亚硫酸氢镁进行
中和反应,或/和一次混合生成的亚硫酸镁结晶物溶于脱硫塔内吸收液;
14.步骤4:将步骤3中和或/和溶解后的二次混合液用于吸收烟气中的二氧化硫。
15.上述二次混合镁法烟气脱硫工艺,其脱硫塔包括将亚硫酸镁氧化成硫酸镁的氧化单元;
16.由于一次混合生成的亚硫酸镁结晶物和过量的氧化镁脱硫剂进入塔内吸收液,只要控制亚硫酸镁氧化量不超过脱硫吸收最终生成的亚硫酸镁量,吸收液中的液相亚硫酸镁浓度可维持在接近饱和的状态,此举解决了亚硫酸镁结晶物脱离循环体系后难以氧化的问题,也有利于降低脱硫循环系统吸收液的固含量。
17.上述二次混合镁法烟气脱硫工艺,其脱硫塔的空塔喷淋液气比不大于4升(吸收液)/标立方米(烟气);
18.由于吸收液具备了高ph优势,喷淋液气比较传统镁法降低50%以上,相应地,中和反应的停留时间增加一倍,而脱硫剂与吸收液的二次混合比再降低1倍。
19.上述二次混合镁法烟气脱硫工艺,从脱硫循环系统引出的吸收液,先经过固液分离除去固形物后再与氧化镁脱硫剂进行一次混合;
20.由于中和反应转化率的提高,甚至接近于完全反应,从脱硫塔引出的吸收液脱硫剂的含量大幅度降低,为此,结合其引出过程去除其中固形物,其造成脱硫剂的损失极其有限,而引出吸收液进行固液分离的量越大,脱硫循环系统内的固含量也越低。
21.上述固液分离方法,从脱硫塔引出的吸收液其固液分离后的ph不大于7;由于中和反应转化率提高,造成固液分离后吸收液ph小于7,即:引出脱硫塔的吸收液其携带的氧化镁在固液分离过程中完全反应后仍不足以将吸收液中的亚硫酸氢镁中和,可认为在固液分离过程中氧化镁的损失量为零。
22.上述固液分离方法,脱硫塔吸收液的固含量不大于0.15%。
23.脱硫塔内吸收液的固含量,与引出吸收液进行固液分离的量相关,固液分离量越大,吸收液固含量越低。而采用引出吸收液固液分离后回流脱硫塔的方法,在降低塔内吸收液固含量的同时并不排放废水。
24.上述二次混合镁法烟气脱硫工艺,氧化镁脱硫剂是氧化镁粉料或未经消化的氧化镁浆液;
25.由于中和反应的条件大为改善,已经无需通过将氧化镁消化为反应活性更高的氢氧化镁来提高中和反应速率,甚至可以直接采用氧化镁粉料与吸收液进行一次混合,上述举措有利于节约蒸气和外部工艺水,降低废水排放量。
26.上述二次混合镁法烟气脱硫工艺,所述的从脱硫塔引出的吸收液量占脱硫塔喷淋量的体积比不小于0.8%;
27.理论上只要采用吸收液与脱硫剂进行一次混合,就能降低二次混合的稀释比,提高二次混合中和反应的转化率,而在引出吸收液量占喷淋量的比不小于0.8%的条件下,脱硫系统的吸收液ph将提高到6.0以上。
28.上述二次混合镁法烟气脱硫工艺,所述的从脱硫塔引出的吸收液量占脱硫塔喷淋量的体积比不小于4.0%。
29.在从脱硫塔引出的吸收液占脱硫塔喷淋量的比不小于4%的条件下,脱硫系统的空塔喷淋液气比可降至不大于4升(吸收液)/标立方米(烟气)。
30.上述二次混合镁法烟气脱硫工艺,中和或/和溶解后的二次混合液其ph大于6.0,
31.基于中和反应转化率的提高,吸收液的ph得到大幅提升,即使在引出的吸收液量只占喷淋量0.8%的清况下,吸收液ph由传统镁法的5.8提高到6.0以上。
32.上述二次混合镁法烟气脱硫工艺,在引出吸收液与脱硫剂一次混合之前存在脱硫塔的启动步骤:将含有二氧化硫的烟气或废气连续地引进脱硫塔,用固含量低于0.5%的氧化镁浆液对烟气进行循环吸收,除去烟气或废气中的二氧化硫,至吸收液ph≤6后完成启动过程。
33.上述二次混合镁法烟气脱硫装置,该装置包括脱硫塔吸收单元a,脱硫塔喷淋单元b,脱硫塔中和单元c,喷淋泵d,一次混合罐f。其中脱硫塔喷淋单元b、脱硫塔吸收单元a、脱硫塔中和单元c在脱硫塔内自上往下依次设置;脱硫塔吸收单元a有原烟气进口,脱硫塔喷淋单元b顶部有净烟气出口;脱硫塔中和单元c的吸收液出口与喷淋泵d的进口相连,喷淋泵d的出口与脱硫塔喷淋单元b的进口相连;脱硫塔中和单元c的吸收液出口与一次混合罐f的进口相连,一次混合罐f的出口与脱硫塔中和单元c的进口相连,一次混合罐f有脱硫剂的进口。
34.有益效果:
35.本发明基于“脱硫剂浆液与塔内吸收液的混合比大、以及中和反应停留时间短是造成传统镁法烟气脱硫中和反应转化率低的根本原因”的研究结论,通过采用从脱硫塔内引出吸收液与脱硫剂一次混合后再与塔内吸收液进行二次混合的方式,大幅度降低了脱硫剂与塔内吸收液的混合比,提高了中和反应的转化率和吸收液的ph。更为有益的是,由于吸收液ph的提高,对喷淋量的要求显著降低,而喷淋量的降低,不但进一步降低了吸收液与脱硫剂的混合比,而且提高了中和反应的停留时间,进一步提高了中和反应的转化率及吸收液的ph,,进一步降低喷淋量,实现了有益的循环。其积极意义具体表现在:
36.相对于传统镁法烟气脱硫,本发明采用吸收液与脱硫剂一次混合后再与塔内吸收液进行二次混合的技术手段,有效提高了塔内中和反应的转化率,将吸收液的ph由5.5
‑
5.8提高至6.0—6.5,而喷淋液气比由8
‑
10升/标立方米降至不大于4升/标立方米,大幅度节约了喷淋能耗。结合在一次混合前将吸收液固液分离去除固形物的技术手段,使脱硫循环系统吸收液的固含量降低80%以上,有效降低了脱硫系统的腐蚀、磨损、堵塞的风险。
37.相对于“亚硫酸镁清液法”脱硫技术,本发明采用将一次混合液不经固液分离(去除亚硫酸镁结晶)直接进入脱硫循环系统的技术手段,使中和反应生成的有效吸收介质亚硫酸镁结晶物及过量的氧化镁脱硫剂也进入塔内吸收液中,有效提高了塔内吸收液的有效吸收介质浓度,提高了脱硫吸收效率,进一步降低了脱硫喷淋量和喷淋能耗,降低了脱硫剂的损耗。同时,基于脱硫塔内吸收液的有效吸收介质浓度的提高,在脱硫塔内氧化亚硫酸镁具备了充分的可行性,制约“亚硫酸镁清液法”技术应用的脱硫废渣处理问题得以解决。而尤为重要的是,本发明吸收液的引出量较“亚硫酸酸镁清液法”降低50%以上,有效解决了由于外部再生系统庞大而制约“亚硫酸酸镁法”应用的难题。而通过在一次混合前将引出脱硫系统的吸收液进行固液分离,结合脱硫塔内氧化亚硫酸镁的技术手段,同样可以将塔内吸收液的固含量控制在“清液”的水平。
附图说明:
38.图1为本发明实施例1、实施例2、实施例3工艺流程图
39.图2为本发明实施例4、实施例5、实施例6工艺流程图。
40.其中:a为脱硫塔吸收单元,b为脱硫塔喷淋单元,c为脱硫塔中和单元,d为喷淋泵,e为氧化镁配料罐,f为一次混合罐,g为固液分离器,h为氧化风机
具体实施方式:
41.实施例1
‑
3:如说明书附图1所示:原烟气由管线(1)进入脱硫塔吸收单元a,在用于脱硫塔吸收单元a与从脱硫塔喷淋单元b喷出的吸收液进行气液传质后的净烟气经管线(2)外排,吸收液由塔内吸收单元a进入脱硫塔中和单元c。脱硫剂氧化镁由管线(5)进入氧化镁配料罐e与由管线(6)进入氧化镁配料罐e的工艺水配置成氧化镁浆液,氧化镁浆液由管线(7)进入一次混合罐f与由管线8从脱硫塔中和单元c引入一次混合罐f的吸收液一次混合,一次混合液由管线(9)回流到脱硫塔中和单元c与塔内吸收液进行二次混合,二次混合液经管线(3)由喷淋泵d经管线(4)泵入喷淋单元b。从脱硫塔中和单元c经管线(10)外排吸收液(脱硫产物)。
42.按照上述图1工艺流程,对某工业窑炉进行烟气脱硫,窑炉烟气量600000标立方米/小时,烟气二氧化硫浓度1800毫克/立方米,脱硫塔直径9米,脱硫塔中和单元高7米,塔中和单元容积397立方米,一次混合罐有效容积按表1设计一次混合停留时间设置。采用外排吸收液的方式外排脱硫产物,外排吸收液量20吨/小时。通过调节从脱硫塔引出的吸收液量占喷淋量的比,进行实施例1
‑
3以及传统镁法(对比技术)的运行,脱硫系统启动方法是:将含有二氧化硫的烟气或废气连续地引进脱硫塔,用固含量低于0.5%的氧化镁浆液对烟气进行循环吸收,除去烟气或废气中的二氧化硫,至吸收液ph≤6后完成启动过程。脱硫系统运行参数如表1:
43.表1:实施例1—3运行参数表
[0044][0045]
由实施例1与对传统镁法脱硫运行参数对比可知,在喷淋液气比相同(对应塔底中和反应停留时间相同)的情况下,即使在引出液量占喷淋量比仅为0.8%、一次混合停留时间接近于零(氧化镁未与吸收液发生中和反应,未生成亚硫酸镁结晶物)的条件下,二次混合的稀释比由传统镁法1067倍降至111倍,吸收液的ph由5.80提高到6.02,相应的脱硫系统二氧化硫浓度由86.2毫克/立方米降至66.6毫克/立方米。即:只要引出吸收液进行一次混
合即能有效提高塔底中和反应的转化率,提高吸收液的ph,有效提高脱硫效率,降低二氧化硫的排放浓度。
[0046]
由实施例2与实施例1对比可知,在吸收液引出量相同的情况下,通过降低喷淋液气,可以提高塔底中和反应停留时间、降低二次混合稀释比,从而进一步提高吸收液的ph,而二氧化硫的排放浓度基本不变。此举的积极意义在于降低喷淋电耗。
[0047]
由实施例3与实施例1对比可知,将引出吸收液占喷淋量的比由0.8%提高到4%,二次混合的稀释比进一步降低,吸收液ph提高、喷淋液气比降低,而随着喷淋液气比由8升/立方米降至4升立方米,中和反应稀释比降低50%,而中和单元停留时间也增加1倍,吸收液的ph由6.02提高到6.28,二氧化硫排放浓度随之由66.6毫克/立方米降至32.8毫克/立方米的超低排放水平。
[0048]
需要说明的是:虽然通过提高中和反应的转化率,降低了传统镁法外排脱硫产物方式所造成的脱硫剂损耗问题,但受排放废水量的限制,塔内吸收液的固含量仍达7.93%,设备磨损、堵塞的风险大,同时造成过量的废水排放。
[0049]
实施例4
‑
6:如说明书附图2所示:原烟气由管线(11)进入脱硫塔吸收单元a,在吸收单元a与从脱硫塔喷淋单元b喷出的吸收液进行气液传质,完成气液传质后的净烟气经管线(12)外排,完成气液传质后的吸收液由脱硫塔吸收单元a进入脱硫塔中和单元c。从脱硫塔中和单元c引出部分吸收液由管线(15)进入固液分离器g进行固液分离,固液分离产生的废渣经管线(19)外排,去除固相杂质的吸收液由管线(16)进入一次混合罐f与由管线(17)投加到一次混合罐f的氧化镁粉料进行一次混合,完成一次混合的一次混合液由管线(18)回流到脱硫塔中和单元c与塔内吸收液进行二次混合,脱硫塔中和单元c的二次混合液经管线(13)由喷淋泵d经管线(14)泵入脱硫塔喷淋单元b。氧化风机h将氧化空气由管线(20)送入脱硫塔中和单元c。
[0050]
按照上述图2工艺流程,对某工业窑炉进行烟气脱硫,窑炉烟气量600000标立方米/小时,烟气二氧化硫浓度1800毫克/立方米,脱硫塔直径9米,脱硫塔底储液段高7米,塔底储液段容积397立方米,一次混合罐容积80立方米。设置氧化风机对脱硫塔中和单元内的吸收液进行氧化,氧化风机风量1500立方米/小时。在一次混合前,采用沉淀池对引出的塔内吸收液进行固液分离,沉淀池表面积72平方米。通过调节从脱硫塔引出吸收液量占喷淋量的比,以及氧化风机的开闭,进行实施例4
‑
6的运行,脱硫系统运行参数如表2:
[0051]
表2:实施例4—6运行参数表
[0052][0053]
由实施例4与实施例3对比可知,采用将引出脱硫系统的吸收液先经固液分离去除固形物后再进行一次混合的方式,可将循环吸收液的固含量由7.93%降至1.38%,降低80%以上。
[0054]
由实施例5与实施例4对比可知,通过对中和单元内吸收液进行氧化的方式,既解决了脱硫产物的氧化问题,又进一步降低循环吸收液的固含量至0.15%以下,达到与“亚硫酸镁法”同样的清液水平。
[0055]
由实施例6与实施例5对比可知,通过加大塔内吸收液的引出量,保证一次混合的停留时间,可使中和反应在塔外全部完成,塔内二次混合只有亚硫酸镁结晶的溶解过程,而无中和反应过程,此举进一步提高了吸收液的ph和脱硫效率,降低了喷淋液气比和吸收液的固含量。同时,此举也创造了固液分离后吸收液的ph小于7.0的有益效果,即无脱硫剂在固液分离过程中的损耗,脱硫剂利用率接近100%。