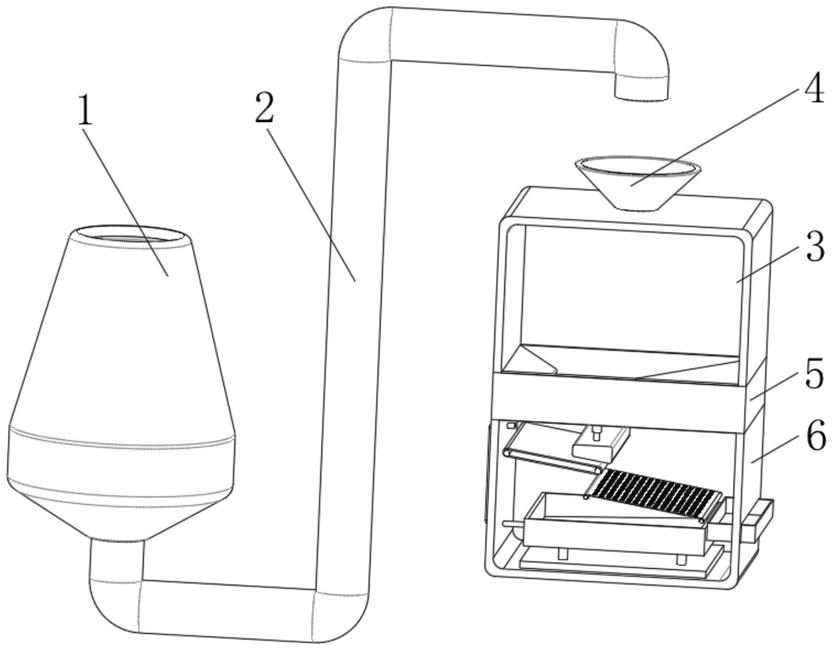
1.本发明涉及颗粒剂形成技术领域,具体为一种颗粒剂形成装置、形成方法。
背景技术:2.医药制粒方法可以分为三大类:湿法制粒、干法制粒、喷雾制粒,其中湿法制粒应用最为广泛,湿法制粒是在药物粉末中加入粘合剂,靠粘合剂的桥架或粘结作用使粉末聚结在一起而制备颗粒的方法,其优点在于,湿法制成的颗粒表面润湿,具有颗粒质量好、压缩成型性好的作用。
3.而湿法制粒发缺点在于精度低、颗粒大小不均,因此我们提出一种颗粒剂形成装置、形成方法来解决这些问题。
技术实现要素:4.为了克服精度低、颗粒大小不均的问题,本发明的目的在于提供一种颗粒剂形成装置、形成方法,具有精度高,颗粒大小均匀的作用。
5.本发明为实现技术目的采用如下技术方案:一种颗粒剂形成装置,包括粉碎机、送料管、造粒机、料斗和连接台,所述连接台的底部设置检查机;
6.所述检查机的内部固定安装传动带和晃动筛网,所述传动带的上方设置摩擦板,所述检查机的右侧插接接料盒,所述检查机的内底壁固定连接晃动机,所述晃动机的顶部固定连接返工盒,所述返工盒的左侧连接返工管。
7.作为优化,所述传动带和晃动筛网均采用左高右低设计,传动带的右端位于晃动筛网的左端上方,传动带上表面与摩擦板下表面平行。
8.作为优化,所述传动带与摩擦板之间的距离为药粒允许的最大直径,所述晃动筛网表面孔的直径为药粒允许的最小直径。
9.作为优化,所述晃动筛网位于返工盒的上方,所述返工管另一端延伸到传动带左端的上方。
10.作为优化,所述返工盒内设置粘合剂喷洒设备,返工盒内底壁采用右高左低设计,所述返工管位于返工盒的一端连接吸气机。
11.一种颗粒剂形成方法,步骤包括:
12.s1、粉碎:将物料分别加入粉碎设备内,将其制成目数500-800的粉料;
13.s2、称量:按配比分别称量对应重量的物料粉;
14.s3、总混:将称量后的物料粉加入混合机中,再将混合机预热到30-50℃,以100-130r/min的速度搅拌5-10min;
15.s4、制粒:2-4min内向混合的物料粉中加入其自身配比65-75%的粘合剂,以100-130r/min的速度搅拌10-15min,直至变成粉团,利用造粒机将粉团分切成直径1-10mm的颗粒;
16.按每分钟1℃的速度升温至30-50℃,停止升温后再烘干30-40min,制成成品药粒;
17.s5、检测:将大小误差超过0.1-0.5mm的药粒挑出,返工;
18.s6、分装:将药粒按每份8-60粒进行分装,封于容器中;
19.s6、外包装:对容器进行封口和外部包装;
20.s7、抽样质检:将包装好的药品按1000:(1-10)的比例抽样检测;
21.s8、入库:抽样质检合格后,将药品入库储存。
22.作为优化,所述物料称量的误差在自身重量的1%内。
23.作为优化,所述粉碎、称量、总混、制粒、分装工艺要在洁净区内进行。
24.本发明具备以下有益效果:
25.1、该颗粒剂形成装置、形成方法,粉碎机将物料粉碎,造粒机将物料粉制成颗粒,这些颗粒通过连接台落到传动带上并向下滚动,大小适当和偏小的颗粒滑落到晃动筛网上,而偏大的颗粒则被摩擦板阻挡,而传递带不断向左传动,使这些大颗粒在传动带和摩擦板之间摩擦,直至大小适当后落下;
26.颗粒落到晃动筛网上并向下滚动,偏小的颗粒落到返工盒内,而大小合适的进入接料盒内;
27.偏小的颗粒和摩擦产生的粉末落入返工盒内,向返工盒内喷入粘合剂,晃动机带动返工盒晃动,使小颗粒粘附粉末,体积变大;
28.如此使所以加工出的颗粒大小均匀,良品率高,可以提高生产质量。
29.2、该颗粒剂形成装置、形成方法,通过改进的生产工艺,使生产的颗粒大小更加均匀,有利用提高生产质量。
附图说明
30.图1为本发明颗粒剂形成装置示意图。
31.图2为本发明颗粒剂形成装置部分示意图。
32.图3为本发明颗粒剂形成方法流程图。
33.图中:1、粉碎机;2、送料管;3、造粒机;4、料斗;5、连接台;6、检查机;61、传动带;62、摩擦板;63、晃动筛网;64、接料盒;65、晃动机;66、返工盒;67、返工管。
具体实施方式
34.下面将结合本发明实施例中的附图,对本发明实施例中的技术方案进行清楚、完整地描述,显然,所描述的实施例仅仅是本发明一部分实施例,而不是全部的实施例。基于本发明中的实施例,本领域普通技术人员在没有做出创造性劳动前提下所获得的所有其他实施例,都属于本发明保护的范围。
35.实施例1
36.请参阅图1-2,一种颗粒剂形成装置,包括粉碎机1、送料管2、造粒机3、料斗4和连接台5,连接台5的底部设置检查机6;
37.检查机6的内部固定安装传动带61和晃动筛网63,传动带61的上方设置摩擦板62,检查机6的右侧插接接料盒64,检查机6的内底壁固定连接晃动机65,晃动机65的顶部固定连接返工盒66,返工盒66的左侧连接返工管67。
38.传动带61和晃动筛网63均采用左高右低设计,传动带61的右端位于晃动筛网63的
左端上方,传动带61上表面与摩擦板62下表面平行。
39.传动带61与摩擦板62之间的距离为药粒允许的最大直径,晃动筛网63表面孔的直径为药粒允许的最小直径。
40.晃动筛网63位于返工盒66的上方,返工管67另一端延伸到传动带61左端的上方,返工盒66内底璧设置条纹凹槽。
41.返工盒66内设置粘合剂喷洒设备,返工盒66内底壁采用右高左低设计,返工管67位于返工盒66的一端连接吸气机。
42.粉碎机1将物料粉碎,造粒机3将物料粉制成颗粒,这些颗粒通过连接台5落到传动带61上并向下滚动,大小适当和偏小的颗粒滑落到晃动筛网63上,而偏大的颗粒则被摩擦板62阻挡,而传递带61不断向左传动,使这些大颗粒在传动带和摩擦板62之间摩擦,直至大小适当后落下;
43.颗粒落到晃动筛网63上并向下滚动,偏小的颗粒落到返工盒66内,而大小合适的进入接料盒64内;
44.偏小的颗粒和摩擦产生的粉末落入返工盒66内,向返工盒66内喷入粘合剂,晃动机65带动返工盒66晃动,使小颗粒粘附粉末,体积变大;
45.如此使所以加工出的颗粒大小均匀,良品率高,可以提高生产质量。
46.实施例2
47.请参阅图3,一种颗粒剂形成方法,步骤包括:
48.s1、粉碎:将物料分别加入粉碎设备内,将其制成目数500的粉料;
49.s2、称量:按配比分别称量对应重量的物料粉;
50.s3、总混:将称量后的物料粉加入混合机中,再将混合机预热到30℃,以100r/min的速度搅拌5min;
51.s4、制粒:2min内向混合的物料粉中加入其自身配比65%的粘合剂,以100r/min的速度搅拌10min,直至变成粉团,利用造粒机将粉团分切成直径1mm的颗粒;
52.按每分钟1℃的速度升温至30℃,停止升温后再烘干30min,制成成品药粒;
53.s5、检测:将大小误差超过0.1mm的药粒挑出,返工;
54.s6、分装:将药粒按每份8粒进行分装,封于容器中;
55.s6、外包装:对容器进行封口和外部包装;
56.s7、抽样质检:将包装好的药品按1000:1的比例抽样检测;
57.s8、入库:抽样质检合格后,将药品入库储存。
58.物料称量的误差在自身重量的1%内。
59.粉碎、称量、总混、制粒、分装工艺要在洁净区内进行。
60.实施例3
61.请参阅图3,一种颗粒剂形成方法,步骤包括:
62.s1、粉碎:将物料分别加入粉碎设备内,将其制成目数800的粉料;
63.s2、称量:按配比分别称量对应重量的物料粉;
64.s3、总混:将称量后的物料粉加入混合机中,再将混合机预热到50℃,以130r/min的速度搅拌10min;
65.s4、制粒:4min内向混合的物料粉中加入其自身配比75%的粘合剂,以130r/min的
速度搅拌15min,直至变成粉团,利用造粒机将粉团分切成直径10mm的颗粒;
66.按每分钟1℃的速度升温至50℃,停止升温后再烘干40min,制成成品药粒;
67.s5、检测:将大小误差超过0.5mm的药粒挑出,返工;
68.s6、分装:将药粒按每份60粒进行分装,封于容器中;
69.s6、外包装:对容器进行封口和外部包装;
70.s7、抽样质检:将包装好的药品按1000:10的比例抽样检测;
71.s8、入库:抽样质检合格后,将药品入库储存。
72.物料称量的误差在自身重量的1%内。
73.粉碎、称量、总混、制粒、分装工艺要在洁净区内进行。
74.尽管已经示出和描述了本发明的实施例,对于本领域的普通技术人员而言,可以理解在不脱离本发明的原理和精神的情况下可以对这些实施例进行多种变化、修改、替换和变型,本发明的范围由所附权利要求及其等同物限定。