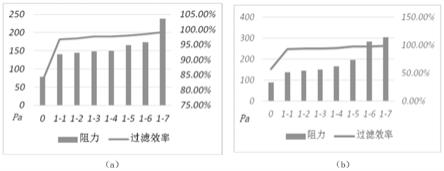
1.本发明属于过滤材料领域,具体涉及一种具有梯度结构的复合过滤材料及其制备方法。
背景技术:2.空气污染已经成为全球人们共同关注的问题。新型冠状病毒的蔓延更是让大家意识到过滤材料的重要性,疫情的出现再一次让一次性口罩等相关产品处于焦点位置。现代口罩通常由“3层或3层以上”非织造织物构成。采用阻隔能力强、高效低阻的纤维过滤材料加强对于空气中微细颗粒物的过滤,是解决上述问题的有效途径。普通非织造布材料例如口罩、防护服等目前已具备比较优异的过滤性能。但当处于颗粒浓度大以及颗粒尺寸较小时的环境下,过滤性则达不到较好的程度,即便达到相关标准,但材料的过滤阻力也会变的很大。根据标准,医用口罩的吸气阻力不得超过343.2pa,但是佩戴者长期佩戴口罩会感觉到呼吸困难,供氧不足的问题,需降低口罩的气体阻力。
3.颗粒、飞沫和气溶胶是新冠病毒主要的载体,其中气溶胶尺寸最小,不携带病毒的气溶胶尺寸最低为0.01μm,携带病毒的气溶胶尺寸最小只有0.07μm,飞沫及飞沫核尺寸最小为1.0μm。利用静电纺丝方法制备的纳米纤维空气过滤材料具有纤维直径小、纤维膜孔径小、孔隙率高的结构特点,在可以有效拦截pm2.5及0.3μm以下雾霾颗粒的同时,对含有新冠病毒颗粒、飞沫、气溶胶也具有极好的阻隔作用,对小颗粒物的过滤效率高达99.99%。普通静电纺材料的气体阻力高达1600pa,应用于口罩滤材将会使人窒息。静电纺过滤材料存在难以满足超精密过滤的要求,并且难以同时满足低阻、高效的过滤要求,在使用过程中具有能耗较高的问题,这是阻碍静电纺过滤膜产业化的重要原因。因此制备出梯度孔隙的高效低阻过滤材料,为气流提供丰富的输运孔道,赋予材料高过滤效率、低空气阻力的特性,并研究其梯度孔隙的构建机制以指导产业化生产就显得尤为重要了。
技术实现要素:4.为了解决现有技术问题,本发明目的在于提供一种具有梯度结构的复合过滤材料制备方法。
5.本发明的技术思路如下:虽然静电纺丝纳米纤维膜具有纤维直径小、吸附能力强、比表面积大、孔隙率高和孔径小等特点,对微纳米颗粒的捕获能力较强,在空气过滤领域有着广阔的应用前景,但由于静电纺纳米纤维膜的强度相对较差,同时由于其寿命短,性能易失效的特有属性使其很难单独使用,因此需要与非织造过滤材料复合使用,将熔喷布等材料作为底布,为静电纺纳米纤维膜提供支撑,增加其力学性能和使用寿命。此外,现有的静电纺纳米纤维空气过滤材料大都采用单一的纤维直径,而对于不同滤膜间的梯度复合研究还相对较少。按纤网阶梯排列方式,可分为从粗到细、从细到粗、从细到粗再到细等方式。对于每层梯度滤膜的纺丝工艺不同,会对静电纺微观上纤维直径产生不同程度的影响,通过改变纤维直径以影响滤膜的孔隙率,孔隙率会影响材料整体通道,而通道则影响梯度复合
纤维膜的整体过滤性能。采用梯度过滤的原理使得不同直径的纤维膜相互复合有利于提高过滤效率的同时降低过滤阻力。
6.因此,本发明采用如下技术方案:具有梯度结构的复合过滤材料的制备方法,其特征在于:以聚丙烯腈(pan)为原料,n-n二甲基甲酰胺(dmf)为纺丝液,制备pan静电纺丝膜,将聚丙烯(pp)熔喷无纺布作为基底织物,将pan静电纺丝膜直接收集在聚丙烯熔喷无纺布上,所收集的pan静电纺丝膜的层数为2-4层,得到具有梯度结构的复合过滤材料。
7.进一步地,纺丝电压设定为14-20kv,纺丝距离设定为12-21cm,纺丝液的浓度为10%-20%,单层pan静电纺丝膜纺丝时间为1h,纺丝速率为1ml/h。
8.进一步地,每一层pan静电纺丝膜的制备工程中,纺丝电压均为18kv,纺丝液的浓度均为15%,纺丝距离逐层递增。
9.进一步地,每一层pan静电纺丝膜的制备工程中,纺丝距离均为18cm,纺丝液的浓度均为15%,纺丝电压逐层递减。
10.进一步地,每一层pan静电纺丝膜的制备工程中,纺丝电压均为18kv,纺丝距离均为18cm,纺丝液的浓度逐层递增。例如,每一层pan静电纺丝膜的制备工程中,纺丝电压均为18kv,纺丝距离均为18cm,纺丝液的浓度逐层递增,分别为10%,13%,所收集的pan静电纺丝膜的层数为2层;或者,每一层pan静电纺丝膜的制备工程中,纺丝电压均为18kv,纺丝距离均为18cm,纺丝液的浓度逐层递增,分别为10%,13%,15%,所收集的pan静电纺丝膜的层数为3层;或者,每一层pan静电纺丝膜的制备工程中,纺丝电压均为18kv,纺丝距离均为18cm,纺丝液的浓度逐层递增,分别为10%,13%,15%,20%,所收集的pan静电纺丝膜的层数为4层。
11.本发明考虑到现有的非织造过滤材料虽然具有较高的过滤效率,但在使用过程中空气阻力会随着容尘量的增大而急剧上升,增大能量的消耗。因此,在本发明中,采用聚丙烯腈为原料,n-n二甲基甲酰胺为有机溶剂,将聚丙烯熔喷无纺布用作基底织物,直接在熔喷布上收集静电纺纤维膜,并通过改变若干个材料变量和环境变量来尝试改变电纺纳米纤维膜结构,同时将多层不同结构的纤维膜进行复合操作,制备梯度复合结构的纤维膜,对其外观,纤维结构和过滤性能等进行了研究。结果表明,通过改变纺丝距离,纺丝浓度,纺丝电压,向纺丝液中添加不同浓度的电解质这四种变量,通过梯度复合的方式制备聚丙烯腈(pan)/聚丙烯(pp)熔喷布梯度复合膜,适当增加纺丝距离将使纤维直径更小,纺丝液浓度越大纤维直径越粗,纺丝电压越大纤维越细,电解质含量越高纤维直径具有先减小后增大的趋势,经过梯度复合后的静电纺纤维膜显著地改善了普通非织造材料的空气过滤效率,但是也增加了通气阻力,可根据具体需要改变工艺,以便在合理的通气阻力下,提高过滤效率。本发明对制备高效低阻口罩滤芯材料具有重要的参考价值。
附图说明
12.图1为实施例1不同纺丝距离制备的复合滤材的过滤性能图,其中,(a)为盐性(nacl)过滤性能图,(b)为油性(dop)过滤性能图。
13.图2为实施例2不同纺丝液浓度制备的复合滤材的过滤性能图,其中,(a)为盐性(nacl)过滤性能图,(b)为油性(dop)过滤性能图。
14.图3为实施例3不同纺丝电压离制备的复合滤材的过滤性能图,其中,(a)为盐性
(nacl)过滤性能图,(b)为油性(dop)过滤性能图。
15.图4为实施例4不同纺丝电解质制备的复合滤材的过滤性能图,其中,(a)为盐性(nacl)过滤性能图,(b)为油性(dop)过滤性能图。
具体实施方式
16.为了进一步解释本发明的技术方案,下面通过具体实施例来对本发明进行详细阐述。
17.本发明涉及的材料与设备如下:聚丙烯腈(pan),相对分子质量150000;n-n二甲基甲酰胺(dmf),分析纯;氯化钠(nacl)分析纯;自制静电纺丝设备;口罩滤材颗粒物过滤效率测试仪fe/r-2626-11。
18.具有梯度结构的复合过滤材料的制备方法,具体如下:以聚丙烯腈为原料,n-n二甲基甲酰胺为纺丝液,制备pan静电纺丝膜,将聚丙烯熔喷无纺布作为基底织物,将pan静电纺丝膜直接收集在聚丙烯熔喷无纺布上,所收集的pan静电纺丝膜的层数为至少2层,得到具有梯度结构的复合过滤材料。
19.实施例1改变纺丝距离制备聚丙烯腈(pan)纤维膜纺丝电压设定为18kv,pan纺丝液质量分数为15%,单层pan静电纺丝纺丝时间为1h,纺丝速率为1ml/h。改变一次性注射针管同滚筒式接收器之间的距离,将聚丙烯(pp)熔喷布卷绕在滚筒式接收器上,静电纺丝纤维膜收集在pp熔喷布上。纺丝距离设定为12cm,15cm,18cm,21cm。对每次纺丝结果进行编号1-1,1-2,1-3,1-4。依次进行2层(12cm,15cm),3层(12cm,15cm,18cm),4层(12cm,15cm,18cm,21cm)的多层次梯度复合操作,纺丝时间分别为2h,3h,4h,并对实验结果进行编号1-5,1-6,1-7。将单层的聚丙烯(pp)熔喷布将其数据编号设为0。
20.实施例2改变纺丝浓度制备聚丙烯腈(pan)纤维膜纺丝电压设定为18kv,纺丝距离设定为18cm,单层滤膜纺丝时间为1h,纺丝速率为1ml/h。改变纺丝液浓度。纺丝浓度分别设定为10%,13%,15%,20%,将聚丙烯(pp)熔喷布卷绕在滚筒式接收器上,静电纺丝纤维膜收集在pp熔喷布上。对每次纺丝结果进行编号2-1,2-2,2-3,2-4。依次进行2层(10%,13%),3层(10%,13%,15%),4层(10%,13%,15%,20%)的多层次梯度复合操作,纺丝时间分别为2h,3h,4h。并对实验结果进行编号2-5,2-6,2-7。将单层的聚丙烯(pp)熔喷布将其数据编号设为0。
21.实施例3改变纺丝电压制备聚丙烯腈(pan)纤维膜纺丝距离设定为18cm,pan纺丝液质量分数为15%,单层滤膜纺丝时间为1h,纺丝速率为1ml/h。改变纺丝电压。纺丝电压分别设定为20kv,18kv,16kv,14kv,将聚丙烯(pp)熔喷布卷绕在滚筒式接收器上,静电纺丝纤维膜收集在pp熔喷布上。对每次纺丝结果进行编号3-1,3-2,3-3,3-4。依次进行2层(20kv,18kv),3层(20kv,18kv,16kv),4层(20kv,18kv,16kv,14kv)的多层次梯度复合操作,纺丝时间分别为2h,3h,4h。并对实验结果进行编号3-5,3-6,3-7。将单层的聚丙烯(pp)熔喷布将其数据编号设为0。
22.实施例4改变纺丝电解质制备聚丙烯腈(pan)纤维膜纺丝电压设定为18kv,纺丝距离设定为18cm,pan纺丝液质量分数为15%,单层滤膜纺丝时间为1h,纺丝速率为1ml/h。向纺丝液中添加氯化钠电解质。添加电解质浓度分别为0.025%,0.050%,0.075%,0.100%,将聚丙烯(pp)熔喷布卷绕在滚筒式接收器上,静电纺丝纤维膜收集在pp熔喷布上。对每次纺丝结果进行编号4-1,4-2,4-3,4-4。依次进行2层(0.025%,0.050%),3层(0.025%,0.050%,0.075%),4层(0.025%,0.050%,0.075%,0.100%)的多层次梯度复合操作,并对实验结果进行编号4-5,4-6,4-7。将单层的聚丙烯(pp)熔喷布将其数据编号设为0。
23.实施例1-4的结果如下:一般情况下,静电纺纤维过滤材料的过滤性能取决于纤维直径、纤维毡厚度、填充密度、荷电情况及操作条件。纤维过滤材料的透气率与纤维的直径、纤维集合体的孔隙结构以及面密度等因素密切相关,且面密度越大,透气性越差。
24.为了排除基布对于过滤性能的影响,更清楚直观地表现电纺纤维膜对过滤性能的影响。因此,在测试各种样品的过滤性能之前,先分别测试复合滤膜和底布的过滤性能,然后再测试各种实施例样品。
25.通过使用口罩过滤颗粒物过滤效率测试仪对滤膜样本的逐一测量,得出每个样本在盐性(nacl)和油性(dop)条件下的过滤性能以及空气阻力的数值,将每种变量下多个样品的测量数据记录下来,并与基布测量数据进行对比,通过编排和处理多个变量的数据,绘制折线图。经过梯度复合后的静电纺纤维膜显著地改善了普通非织造材料的空气过滤效率,但是也增加了通气阻力。
26.实施例1,即在纺丝距离的变量样本中,图1(a)、(b)为复合过滤材料的的盐性(nacl)和油性(dop)过滤性能图。可见滤膜过滤效率和空气阻力随着纺丝距离的的增加而数值会增大。分析其原因在于由于距离的增大使得纺丝液可以得到有效的拉伸,进而使纤维滤膜的平均直径降低。接收距离的增大,对电场的场强有一定的降低,但高压静电下,并不足以引起较大的变化。因此,纤维平均直径的降低使纤维丝之间的孔隙率降低,最终使滤膜的整体过滤效率提高,空气阻力也随之增大。随着滤膜的多层复合,过滤效率和空气阻力也随之增大。
27.实施例2,即在纺丝液浓度的变量样本中,图2(a)、(b)为滤膜的盐性(nacl)和油性(dop)过滤性能图。可见复合滤膜过滤性效率和空气阻力随着纺丝液浓度的增大而减小,分析其原因在于纺丝液浓度的增大,纺丝液粘稠度和张力也逐渐增大,进而使丝平均直径增大,使纤维丝之间的孔隙率增大,进而导致滤膜的整体过滤效率以及空气阻力降低。随着滤膜的多层复合,过滤效率和空气阻力也随之增大。
28.实施例3,即在纺丝电压的变量样本中,图3(a)、(b)为滤膜的盐性(nacl)和油性(dop)过滤性能图。可见单层滤膜过滤效率和空气阻力随着电压的降低而数值变小。在较小的电压下,纺丝液体容易在喷丝口形成液滴,更不易将聚合物拉伸成纤维。电压的提高有利于纤维细度的降低。电压的降低,使纺丝液受到的静电力的作用减弱,喷射时的拉伸效果减弱,进而导致收集到的纤维直径偏大。从而使滤膜整体的过滤性能降低,空气阻力也逐渐减小。随着滤膜的多层复合,过滤效率和空气阻力也随之增大。
29.实施例4,在纺丝电解质的变量样本中,图4(a)、(b)为滤膜的盐性(nacl)和油性(dop)过滤性能图。可见过滤效率和空气阻力变化有先减小后增加的趋势,均维持在一定的区间内,但电解质相较于普通纺丝液来说,纺丝液更易纺,可以提高纺丝液的可纺性能。随着滤膜的多层复合,过滤效率和空气阻力也随之增大。
30.由实施例1-4可知,根据改变参数变量后的纤维滤膜可知,纤维直径和滤膜层数将直接影响滤膜的过滤性能,分析其原因在于:通过降低纤维直径,增大纤维滤膜的密度,减少了纤维膜的孔隙率,而通过梯度复合将不同直径的纤维滤膜复合在一起,互相弥补之间孔隙率的差别,进而影响到纤维滤膜的整体通道,使其过滤性能远高于单层膜的过滤性能,要显著高于单层梯度复合膜。且随着复合层数的增多,其过滤性能越好,当增大到一定厚度时,过滤性能提升不大,但空气阻力会持续上升。各种变量对于单层复合膜的过滤性能不会产生显著的改变,而梯度复合下复合膜的过滤性能要显著高于单层复合膜。