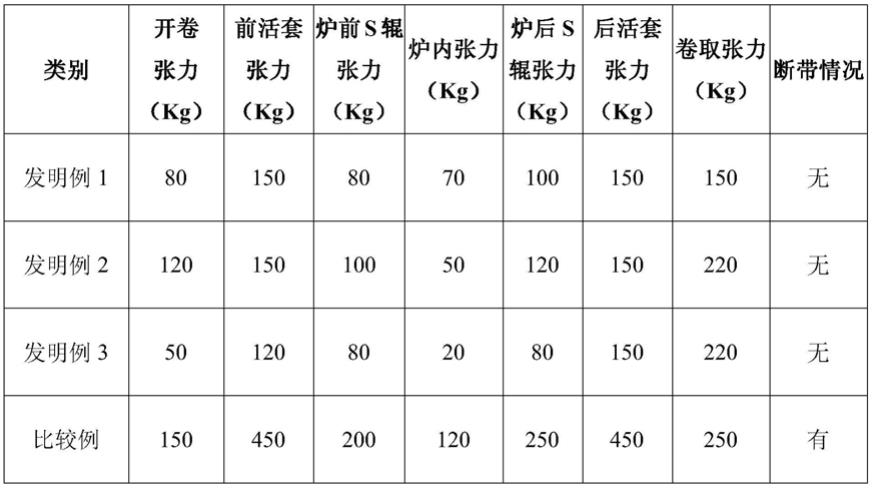
1.本发明涉及一种硅钢热处理方法,尤其涉及一种取向硅钢极薄带绝缘层涂覆方法。
背景技术:2.随着国防军工、机电、电子、家电、汽车等产品小型化、极薄化、环保化、节能化、高效化的发展,以及国家新能源发展规划的推进,硅钢极薄带将呈指数曲线上升。取向硅钢极薄带以其更低的损耗、更高的磁通密度和更低的磁滞伸缩正在迅速得到广泛应用。极薄取向硅钢是电力工业、电子工业和军工等领域重要的软磁材料,广泛应用于航空航天、高铁动车、电抗器、精密机械、智能硬件、智能汽车连接器、船舶配件、医疗器械等产品的制造。
3.我国1959年开始研制极薄取向硅钢带,厚度为0.08mm、0.12mm、0.15 mm,近年来宝钢、武钢及几家民企也相继开始取向硅钢极薄带的生产,但由于受原料、技术、装备等因素制约,产品质量与国外相比还有一些差距,无法实现量产,且由于硅钢极薄带厚度范围为0.03~0.15mm,厚度极薄,制备工艺异常复杂,生产过程中很容易出现断带,涂层厚度不均等问题,生产效率低下,生产成本较高。
技术实现要素:4.本发明的目的是克服现有技术存在的缺陷,提供一种低成本、涂覆层均匀的取向硅钢极薄带绝缘层涂覆方法。
5.实现本发明目的的技术方案是:一种取向硅钢极薄带绝缘层涂覆方法,包括以下步骤:
6.(1)准备工作:接入普碳钢引带,并在焊缝处加垫2~3道碳钢带进行夹紧点焊;
7.(2)设定张力:分别设定涂覆线中的开卷张力、前活套张力,炉前s 辊张力,炉内张力,炉后s辊张力,及卷曲张力;
8.(3)调节炉内气氛及温度:取向硅钢极薄带绝缘涂层涂覆后的烘干在卧式退火炉进行,所述卧式退火炉包括干燥炉,干燥炉温度设定为 100~400℃,加热段温度设定450~650℃,炉内充有保护气氛4%h2+n2;
9.(4)涂覆绝缘层及厚度检测:待炉内温度稳定后,压下涂层辊,打开涂液泵对普碳钢带表面进行绝缘层涂覆,经干燥炉烘干,加热炉退火后检测涂层厚度,并根据检测结果调整涂层厚度;
10.(5)极薄带涂层涂覆及烘干:涂层厚度检测合格后接入取向硅钢极薄带,采用上述工艺进行涂覆及烘干;
11.(6)取向硅钢极薄带表面绝缘涂层指标及磁性能检测:检测钢带表面绝缘涂层的厚度,及附着性、绝缘电阻及铁损检测。
12.上述技术方案,所述步骤(3)中干燥炉包括预干燥段和干燥段,加热段包括预加热炉和加热炉;所述预干燥段炉长1~2m,所述干燥炉炉长8~12 米,预加热炉炉长1~2米,加
热炉炉长2~8米,钢带运行速度12~20m/min。
13.上述技术方案,所述步骤(2)中,开卷张力为50~80kg,前活套张力 100~150kg,炉前s辊张力60~90kg,炉内张力20~70kg,炉后s辊张力 80~100kg,后活套张力150kg,卷曲张力150~220kg。
14.上述技术方案,所述步骤(4)中涂层辊槽型为半圆形,槽深0.1~0.3mm,槽间隙为32~38槽/英寸;
15.上述技术方案,所述步骤(4)中涂层辊为光滑辊面,辊上无刻槽。
16.上述技术方案,所述(4)绝缘层涂液比重为1.2-1.24。
17.上述技术方案,所述步骤(5)中硅钢极薄带接入时采用2~3道普碳钢薄带夹紧点焊的方式进行焊接。
18.上述技术方案,所述绝缘涂层厚度为0.6-1.2μm,附着性为a级,绝缘电阻30~40ω/cm2。
19.上述技术方案,所述步骤(1)中普碳钢带厚度为0.08~0.15mm,所述硅钢极薄带厚度为0.03~0.15mm。
20.采用上述技术方案后,本发明具有以下积极的效果:
21.(1)本发明前期采用与极薄带厚度相当的普碳钢薄带作为引带,通过普碳钢引带测试产线张力和涂覆绝缘层的厚度,待温度和张力调试合格后再接入硅钢极薄带,一方面可通过普碳钢薄带的运行加速炉内温度和气氛的稳定,节约炉内气氛和温度稳定的时间;另一方面可以通过采用成本较低的普碳钢检测炉内张力和温度的设定,及绝缘涂层的涂覆效果,避免开始采用硅钢带出现断带,及涂覆不合格后造成产品报废带来的成本升高;
22.(2)本干燥炉设置预干燥段和干燥段,预干燥段温度为100-200℃,干燥段温度为350-400℃。极薄带在经过涂层辊后,表面涂覆一层湿润的绝缘层,这层绝缘层内还含有大量的水分。通过低温干燥,可以使水分缓慢蒸发,避免绝缘层内的水分快速气化,在绝缘层表面形成气泡,导致点状漏涂。通过预干燥段烘干后的板带,再进过干燥段烘干,表面水分彻底去除;
23.(3)本加热段设置预加热段和加热段,预加热段温度为450-500℃,加热段温度为500-650℃。由于极薄带厚度较薄,带钢在经过干燥炉后,如果加热速度过快,带钢内部将产生热应力,导致带钢板形发生变化。预加热段的存在起到缓冲带钢温度的作用,避免快速加热导致的热应力。加热炉内通入4%h2+n2的保护气氛可以防止硅钢带表面出现氧化,改善带钢表面质量;
24.(3)本发明采用三道碳钢带夹紧点焊的方式进行焊接,与传统的搭接焊接相比更牢固,避免运行过程中出现开裂断带造成的生产效率下降和产量质量的异常;
25.(4)本发明通过各段张力的合理设置即可保证硅钢带的正常运行,避免断带的发生,又可保证极薄带有较好的磁性;
26.(5)本发明要求绝缘层厚度为0.6-1.2μm,同时要求绝缘涂层均匀平整。涂层辊采用半圆形槽型,并采用较浅的槽深和较密的槽间隙,比目前常用的三角槽涂覆的表面更均匀,不易出现厚涂。
具体实施方式
27.本发明取向硅钢极薄带绝缘层涂覆方法,包括以下步骤:
28.(1)准备工作:接入普碳钢引带,并在焊缝处加垫2~3道碳钢带进行夹紧点焊;
29.(2)设定张力:分别设定涂覆线中的开卷张力、前活套张力,炉前s 辊张力,炉内张力,炉后s辊张力,及卷曲张力;其中开卷张力为50~80kg,前活套张力100~150kg,炉前s辊张力60~90kg,炉内张力20~70kg,炉后s辊张力80~100kg,后活套张力150kg,卷曲张力150~220kg;
30.(3)调节炉内气氛及温度:取向硅钢极薄带绝缘涂层在卧式退火炉进行,所述卧式退火炉包括干燥炉,干燥炉温度设定为100~400℃,加热段温度设定450~650℃,炉内充有保护气氛4%h2+n2;
31.(4)涂覆绝缘层及厚度检测:待炉内温度稳定后,压下涂层辊,打开涂液泵对普碳钢带表面进行绝缘层涂覆,绝缘层涂液比重为1.2-1.24;经干燥炉烘干,加热炉退火后检测涂层厚度,并根据检测结果调整涂层厚度;
32.(5)极薄带涂层涂覆、烘干及退火:涂层厚度检测合格后接入取向硅钢极薄带,极薄带厚度为0.03~0.15mm。接入时采用2~3道普碳钢薄板夹紧点焊的方式进行焊接,普碳钢带厚度为0.08~0.15mm;随后采用上述工艺进行涂覆及烘干、退火;
33.(6)取向硅钢极薄带表面绝缘涂层指标及磁性能检测:检测钢带表面绝缘涂层的厚度,及附着性、绝缘电阻及铁损检测。
34.优选地,本发明中涂覆线干燥炉包括预干燥段和干燥段,加热段包括预加热炉和加热炉;所述预干燥段炉长1~2m,所述干燥炉炉长8~12米,预加热炉炉长1~2米,加热炉炉长2~8米,钢带运行速度12~20m/min。
35.本发明涂层辊槽型优选半圆形,槽深0.1~0.3mm,槽间隙为32~38槽/ 英寸。针对0.03mm规格取向硅钢极薄带也可选择辊面无刻槽,即光滑辊面的涂层辊,可防止厚涂,及由于刻槽辊磨损程度不一致带来的涂覆不均匀缺陷。
36.硅钢极薄带由于厚度较薄,生产中张力设定不合适,经常会出现断带的情况,本发明针对0.08mm取向硅钢极薄带分别采取表1中各张力值进行涂覆、烘干、退火,并观察断带情况,从下表可知,采用发明例1、发明例 2和发明例3中的张力值均不会发生断带,比较例中的张力值则会发生断带情况。
37.表1涂覆线中不同区域张力设定与断带情况对照表
[0038][0039]
表2为不同极薄带厚度,涂层辊刻槽深度,刻槽间隙对应的涂层厚度、绝缘电阻、附着性和铁损情况,0.05~0.15mm厚度取向硅钢极薄带选用刻槽辊,涂层厚度和绝缘电阻及附着性均符合标准要求,0.03mm取向硅钢极薄带由于本身厚度较薄,涂层厚度不能大范围涂覆不均匀情况,因此选用辊面不刻槽的光滑辊面,各项指标均在正常范围内。
[0040]
表2不同极薄带厚度与涂层线涂层参数及性能对应关系
[0041][0042][0043]
以上所述的具体实施例,对本发明的目的、技术方案和有益效果进行了进一步详细说明,所应理解的是,以上所述仅为本发明的具体实施例而已,并不用于限制本发明,凡在本发明的精神和原则之内,所做的任何修改、等同替换、改进等,均应包含在本发明的保护范围之内。