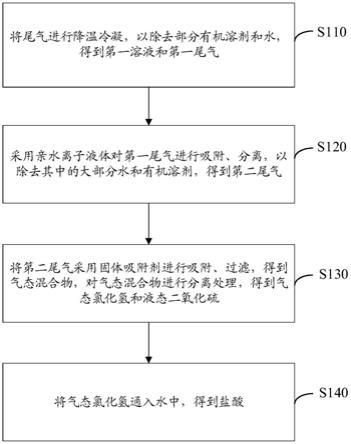
1.本发明属于化工尾气分离回收工业技术领域,具体涉及一种尾气处理方法。
背景技术:2.三氯蔗糖
‑6‑
酯是制备三氯蔗糖中重要的中间体之一,蔗糖
‑6‑
酯可由蔗糖经酯化,然后经氯代试剂氯化得来,目前,工业化的氯化试剂主要有维尔斯迈尔(vilsmeier)氯代试剂及光气类产品,由于光气的高风险,高污染性,使用的企业较少。而vilsmeier氯代试剂主要由dmf,二甲基亚砜制备而来,使用时较为安全。然而在氯化过程中,会产生大量尾气,其中包含hcl、so2、水、dmf及三氯乙烷等。
3.传统的对上述尾气的处理通常采用降温冷凝、硫酸脱水、活性炭吸附等操作,但是这不足以去除尾气中的全部有机物及水,一方面导致在后续加压精馏过程中,会产生大量的有机/无机固体附着在管壁、输送泵等过流材质表面,造成严重的设备腐蚀及堵塞,极大地限制了hcl和so2的回收;另一方面hcl和so2得不到彻底的分离,如采用直接水吸附hcl得到的盐酸中含有大量so2气体,so2气体在水中会形成h2so3,由于h2so3受热易分解,产生大量so2气体,导致回收的盐酸产品在使用过程中与碱接触会产生气体乳化现象,严重影响盐酸产品的品质。
4.目前也有一些区别于传统技术的关于含有hcl和so2混合气体的尾气处理的报道,如中国专利cn103113197报道了一种以氯化尾气为原料,与醇、乙腈反应制备原乙酸三甲酯的方法,该法虽解决了hcl的处理问题,并为蔗糖酯化提供了原料;但原乙酸三甲酯酯化工艺目前已很少采用,且该工艺容易产生大量废盐、废水,因此该方法不具有很大的实用价值。
5.中国专利cn208511908采用低温冷凝的方式分离hcl和so2混合气体,其方法是利用两者沸点不同,且在so2产品中鼓入空气,带出hcl,从而提高so2产品纯度。该法单纯以两种气体的沸点不同,进行分离,但在能耗上较其他方法高很多,且得到的产品纯度不佳;此外,对于三氯蔗糖工艺中产生的氯化尾气在含水、含溶剂的情况下,该工艺并不适用。
6.中国专利cn108373139在针对三氯蔗糖氯化尾气除水、除溶剂的基础上,同样采用了冷却分离的方法分离hcl和so2。该方法使用了浓硫酸除水,除水效果较佳,但后续废酸再生或处理较为麻烦;有机物分离过程中单纯以冷凝的方式收集,无法实现为其中有机物的完全去除,因此得到的hcl及so2产品纯度不高。
7.又如中国专利cn103466550报道了一种阿莫西林生产工艺中d
‑
酸酯化尾气回收系统,尾气系统中主要为hcl及so2气体。该法采用加压精馏的方式分离两种气体,并采用三联加压精馏塔分离气体及有机物;然而该体系中不含水分,因此对于系统设备的要求相对不高;但蔗糖氯化反应中会产生较多的水分,对系统的分离方法及设备具有极大的考验,该方法不适宜用于对蔗糖氯化反应产生的废气中。
技术实现要素:8.鉴于目前蔗糖采用vilsmeier氯代试剂氯化生成三氯蔗糖
‑6‑
酯工艺产生的尾气的处理现状,存在着分离效果差、后处理困难、容易造成严重的设备腐蚀,以及压缩气体形成固体附着物导致管路堵塞等问题,提出了一种尾气处理方法,可克服上述问题或者至少部分地解决上述问题。
9.根据本技术的第一方面,提供了一种尾气处理方法,该尾气为蔗糖
‑6‑
酯经氯化反应生成三氯蔗糖
‑6‑
酯的过程中产生的,该方法包括:
10.冷凝步骤:将尾气进行降温冷凝,以除去部分有机溶剂和部分水,得到第一溶液和第一尾气;
11.脱除步骤:采用亲水离子液体对第一尾气进行吸附、分离,以除去其中的大部分水和部分有机溶剂,得到第二尾气;
12.分离步骤:将第二尾气采用固体吸附剂进行吸附、过滤,得到气态混合物,对气态混合物进行分离处理,得到气态氯化氢和液态二氧化硫;和
13.相转化步骤:将气态氯化氢通入水中,得到盐酸。
14.可选的,该方法还包括:
15.在所述脱除步骤内包括的第一再生步骤:将脱除步骤中使用后的亲水离子液体进行再生处理,得到再生亲水离子液体和第一再生尾气;以及
16.将再生亲水离子液体回收,以供脱除步骤使用。
17.可选的,在上述方法中,亲水离子液体的再生温度为80~120℃,再生真空度为
‑
0.1至
‑
0.05mpa。
18.可选的,该方法还包括:
19.在所述第一再生步骤后的回收步骤:采用亲油离子液体对第一再生尾气进行吸附,以脱除有机组分,得到第三尾气;
20.采用饱和氯化钠水溶液对第三尾气进行吸附,以吸收氯化氢,得到第四尾气;
21.将第四尾气回收至要进入脱除步骤的第一尾气中;
22.对得到的吸附了氯化氢的饱和氯化钠水溶液进行氯化氢再生处理,得到再生氯化氢,将再生氯化氢回收至要进入相转化步骤的氯化氢中;将释放了氯化氢的饱和氯化钠水溶液回收至饱和氯化钠水溶液中。
23.可选的,该方法还包括:
24.在所述回收步骤后的第二再生步骤:将回收步骤中使用后的亲油离子液体进行再生处理,得到再生亲油离子液体和第五尾气;
25.将再生亲油离子液体回收,以供回收步骤使用;
26.对第五尾气进行溶剂回收处理。
27.可选的,在上述方法中,亲油离子液体的再生温度为80~120℃,再生真空度为
‑
0.1至
‑
0.05mpa。
28.可选的,在上述方法中,在回收步骤中,亲油离子液体为1
‑
乙基
‑3‑
甲基咪唑磷酸二丁酯和/或1
‑
丁基
‑3‑
甲基咪唑磷酸二丁酯;
29.采用亲油离子液体对第一再生尾气进行吸附包括:
30.在温度为20~40℃,采用亲油离子液体对第一再生尾气进行吸附。
31.可选的,在上述方法中,在冷凝步骤中,降温冷凝的温度设为0~30℃。
32.可选的,在上述方法中,亲水离子液体为吡啶硫酸氢盐、甲基咪唑硫酸氢盐和乙基咪唑硫酸氢盐中的一种或几种。
33.可选的,在上述方法中,采用亲水离子液体对第一尾气进行吸附包括:
34.在温度为20~50℃,采用亲水离子液体对第一尾气进行吸附。
35.本技术的有益效果在于,利用离子液体吸附氯化尾气中的杂质,在加压精馏前,有效解决了水及有机物对hcl和so2两种气体分离的影响,解决了因加压分离过程中产生的有机/无机固体附着在管壁及输送泵造成的严重腐蚀及堵塞问题,且可获得高纯度的液体so2产品;离子液体的腐蚀性极低,采用离子液体代替浓硫酸,可有效克服传统技术中浓硫酸脱水带来的设备腐蚀及后续处理问题;此外,离子液体具有高度可再生性,且再生工艺简单,极大程度上降低了尾气处理的成本。本技术以离子液体吸附为主,并且与冷凝、精馏等手段有机结合,能够有效处理三氯蔗糖生产工艺中的氯化尾气,实现hcl和so2两种气体的有效分离,获得高品质的盐酸和液态so2产品,且整体处理工艺简单、成本低、具有极大的经济和应用价值。
36.上述说明仅是本技术技术方案的概述,为了能够更清楚了解本技术的技术手段,而可依照说明书的内容予以实施,并且为了让本技术的上述和其它目的、特征和优点能够更明显易懂,以下特举本技术的具体实施方式。
附图说明
37.此处所说明的附图用来提供对本技术的进一步理解,构成本技术的一部分,本技术的示意性实施例及其说明用于解释本技术,并不构成对本技术的不当限定。在附图中:
38.图1示出了根据本技术的一个实施例的尾气处理方法的流程示意图;
39.图2示出了根据本技术的一个实施例的尾气处理装置的结构示意图。
具体实施方式
40.下面将更详细地描述本技术的示例性实施例。虽然显示了本技术的示例性实施例,然而应当理解,可以以各种形式实现本技术而不应被这里阐述的实施例所限制。相反,提供这些实施例是为了能够更透彻地理解本技术,并且能够将本技术的范围完整地传达给本领域的技术人员。
41.离子液体又称室温离子液体(room temperature ionic liquids,简称rtils),是一种备受关注的绿色溶剂和催化剂。它是一种熔点低于100℃的液态有机熔融盐,由于其完全由阴阳离子组成,因此具有许多不同于常规有机溶剂的性质,如“零”蒸汽压、热稳定性高,溶解能力强及结构与功能可设计等,在有机反应、液相分离、气体吸收、电化学等领域具有极大的应用潜力。
42.现有技术中,对蔗糖采用vilsmeier氯代试剂氯化生成三氯蔗糖
‑6‑
酯工艺产生的尾气,简称氯化尾气的处理,存在着分离效果差、容易造成严重的设备腐蚀,以及压缩气体形成固体附着物导致管路堵塞等问题。
43.本技术将离子液体引入至氯化尾气的处理中,通过离子液体吸附尾气中的水分和有机杂质,并结合冷凝和加压精馏等技术,有效克服了现有技术的不足。
44.图1示出了根据本技术的一个实施例的尾气处理方法的流程示意图,从图1可以看出,本技术至少包括步骤s110~步骤s140:
45.冷凝步骤s110:将尾气进行降温冷凝,以除去部分有机溶剂和水,得到第一溶液和第一尾气。
46.本技术的尾气指的是蔗糖
‑
6酯与氯代试剂,如vilsmeier试剂等,进行氯化反应,生成三氯蔗糖
‑6‑
酯的氯化工艺中产生的,主要含有气态水、hcl、so2、以及dmf和三氯乙烷等有机溶剂。目前对上述尾气的处理,主流技术通常采用降温冷凝
‑
浓硫酸脱水
‑
活性炭脱溶
‑
加压精馏分离的传统工艺,这种工艺存在着如下的技术缺陷:采用浓硫酸脱水的方式容易导致严重的设备腐蚀,且容易使溶剂碳化,浓硫酸吸水后不易再生;传统的冷凝加活性炭吸附,无法对气体中含有的较高浓度有机物完全去除,这会导致后续压缩过程中有机物富集,在hcl及so2存在的情况下与固体微颗粒一起附着在管壁或阀门处,堵塞管路等。
47.在本技术中,首先,将上述尾气进行降温冷凝,在这个过程中,大部分气态水会转化为液态水、气态dmf和气态三氯乙烷等气态有机溶剂会转化为液态,记为第一溶液,与气态混合物分流,气态混合物记为第一尾气。
48.在降温冷凝后,第一溶液中主要包含液态的水、dmf和三氯乙烷,第一溶液可做溶剂回收处理。第一尾气包含气态氯化氢、so2、以及部分气态水、少量的气态dmf和气态三氯乙烷。
49.在本技术的一些实施例中,在冷凝步骤中,对降温冷凝降至的温度不作限定,低于蔗糖
‑
6酯与氯代试剂的氯代反应的温度即可;在另一些实施例中,出于经济和效果的综合考虑,可将降温冷凝的温度设为0~30℃。
50.脱除步骤s120:采用亲水离子液体对第一尾气进行吸附,以除去其中的大部分水和有机溶剂,得到第二尾气;
51.在冷凝步骤中,有机溶剂的含量已经被降至很低,含量是非常少的,水分含量相对较多,该步骤选择亲水离子液体对第一尾气进行吸附,这是由于亲水离子液体对水分有很强的吸附作用,同时对有机溶剂也有一定的吸附效果,在采用亲水离子液体对第一尾气进行吸附后,水分基本被消除殆尽,且有机溶剂的含量也是非常低的。
52.气态hcl和气态so2在离子液体中的溶解度是很低的,因此,采用离子液体对尾气进行吸附,可有效分离水、有机溶剂和hcl、so2。
53.分离步骤s130:将第二尾气采用固体吸附剂进行吸附、过滤,得到第一气态混合物,对第一气态混合物进行分离处理,得到气态氯化氢和液态二氧化硫。
54.为了进一步除去尾气中的有机溶剂,可以采用固体吸附剂,如活性炭等,吸附第二尾气中的残余溶剂,然后过滤掉固体吸附剂,得到了气态混合物,这时的气态混合物主要包括气态hcl和气态so2,还包括极其微量的水蒸气和气态有机溶剂。
55.然后对第一气态混合物进行分离,即可得到分离后的气态hcl和液态so2,具体的分离过程可参考现有技术,也可以采用加压、吸附、过滤和加压精馏的方法,首先对第一气态混合物进行加压,然后再次采用固体吸附剂再次对残余有机溶剂进行吸附,最后利用气态hcl和气态so2在挥发度的差异,采用加压精馏技术对气态混合物进行分离处理,在加压的过程中,气态so2转化为液态so2,从而使得气态hcl和气态so2互相分离,在分离后,获得气态hcl和液态so2。
56.和相转化步骤s140:将气态氯化氢通入水中,得到盐酸。
57.气态氯化氢不容易存储,且在实际应用中,盐酸是比较常用的化学试剂,因此,出于经济的考虑,将气态氯化氢转化为液态产物,即盐酸,具体地,将气态氯化氢通入水中,即可得到盐酸。
58.从图1所示的方法中,可以看出,本技术利用离子液体吸附氯化尾气中的杂质,在加压精馏前,有效解决了水及有机物对hcl和so2两种气体分离的影响,解决了因加压分离过程中产生的有机/无机固体附着在管壁及输送泵造成的严重腐蚀及堵塞问题,且可获得高纯度的液体so2产品;离子液体的腐蚀性极低,采用离子液体代替浓硫酸,可有效克服传统技术中浓硫酸脱水带来的设备腐蚀及后续处理问题;此外,离子液体具有可高再生性,且再生工艺简单,极大程度上降低了尾气处理的成本。本技术以离子液体为主,并且与冷凝、精馏等手段有机结合,能够有效处理三氯蔗糖生产工艺中的氯化尾气,实现hcl和so2两种气体的有效分离,获得高品质的盐酸和液态so2产品,且整体处理工艺简单、成本低、具有极大的经济和应用价值。
59.在本技术的一些实施例中,上述方法还包括:在所述脱除步骤内包括的第一再生步骤:将脱除步骤中使用后的亲水离子液体进行再生处理,得到再生亲水离子液体和第一再生尾气;以及将再生亲水离子液体回收至脱除步骤中。
60.在脱除步骤中,采用亲水离子液体对第一尾气进行吸附后并分离后,得到第二尾气,以及吸附了杂质的亲水离子液体,即使用后的亲水离子液体,由于亲水离子液体再生能力强、再生工艺简单、再生成本低,因此可将亲水离子液体进行再生处理,循环利用,这能够极大程度节约氯化尾气的处理成本。
61.对于亲水离子液体的再生可采用下述方法:将亲水离子液体送入离子液体再生釜进行再生,再生后的亲水离子液体从再生釜的釜底采出,经冷凝器冷凝后、在经过过滤器过滤,然后就能够回流反复使用。
62.对于离子液体的再生,就是使得离子液体释放出已经吸附的气态物质。本技术对亲水离子液体的再生条件不做限制,凡是能够使得离子液体脱除吸附的气态物质即可,如通过搅拌、加热等手段实现上述目的;在本技术的另一些实施例中,出于经济的考虑,亲水离子液体的再生温度为80~120℃,再生真空度为
‑
0.1至
‑
0.05mpa,在上述条件下,亲水离子液体能够迅速脱除吸附的气态物质。
63.需要说明的是,亲水离子液体在对第一尾气进行吸附的过程中,不仅会吸附尾气中的水分、有机溶剂,一部分目标产物hcl和so2两种气体也会随着亲水离子液体一起被带出第一尾气,因此在亲水离子液体进行再生时,产生的第一再生尾气中,除了包含杂质水分、dmf和三氯乙烷等有机溶剂,还会包含一些目标产物hcl和so2。为了进一步提高hcl和so2的产率,可对第一再生尾气进行回收再处理,以便分离出其中的hcl和so2。
64.在本技术的一些实施例中,上述方法还包括:在所述第一再生步骤后的回收步骤:采用亲油离子液体对第一再生尾气进行吸附,以脱除有机组分,得到第三尾气;采用饱和氯化钠水溶液对第三尾气进行吸附,以吸收氯化氢,得到第四尾气;将第四尾气回收至要进入脱除步骤的第一尾气中。对得到的吸附了氯化氢的饱和氯化钠水溶液进行氯化氢再生处理,得到再生氯化氢,将再生氯化氢回收至要进入相转化步骤的氯化氢中;将释放了氯化氢的饱和氯化钠水溶液回收至饱和氯化钠水溶液中。
65.在第一再生尾气中,水分的含量是微乎其微的,几乎没有,而有机组分的含量相对较多,因此在对第一再生尾气进行回收时,选择了亲油性的离子液体,亲油离子液体对于有机组分的吸附效果强于亲水离子液体,这里选择亲油离子液体能够更好地纯化第一再生尾气,在采用亲油离子液体对第一再生尾气进行吸附、分离后,得到吸附了杂质的亲油离子液体,以及第三尾气。
66.在第三尾气中主要包含hcl和so2,对于第三尾气可以同对第二尾气的处理方法一致,直接进行分离处理,如将第三尾气采用固体吸附剂进行吸附、过滤,得到气态混合物,对气态混合物进行分离处理,包括但不限于加压、吸附、过滤以及加压精馏,即可得到气态氯化氢和液态二氧化硫;进一步的,将气态氯化氢通入水中,得到盐酸。
67.也可以采用下述推荐的方法进行分离处理,首先采用饱和氯化钠水溶液对第三尾气进行吸附,吸收第三尾气中的氯化氢,由于so2不溶于饱和氯化钠水溶液,以此hcl和so2得以分离,得到吸附了氯化氢的饱和氯化钠水溶液和第四尾气,第四尾气主要包含so2,由于so2从饱和氯化钠水溶液中析出,会带上水分,因此可将第四尾气回收至要进入脱除步骤的第一尾气中,循环处理,以脱除水分。对得到的吸附了氯化氢的饱和氯化钠水溶液进行氯化氢再生处理,即使得吸附了氯化氢的饱和氯化钠水溶液释放出氯化氢气体,如可通过加热使得氯化氢气体释放,将再生得到的氯化氢的纯度是非常高的,可直接回收至要进入相转化步骤的氯化氢中。而对于将释放了氯化氢的饱和氯化钠水溶液可以重复利用,即回收至饱和氯化钠水溶液中。
68.在本实施例中,利用了具有亲水与疏水性的两类离子液体配合处理氯化尾气中的水及有机物,能够达到更加显著的分离效果,在得到的hcl和so2的纯度较单纯使用亲水离子液体效果更好。
69.同亲水离子液体一样,在本技术的一些实施例中,也可以对回收步骤中,使用后的亲油离子液体进行再生处理,以循环使用,具体的,同亲水离子液体,将亲油离子液体送入离子液体再生釜进行再生,再生后的亲油离子液体从再生釜的釜底采出,经冷凝器冷凝后、在经过过滤器过滤,然后就能够回流反复使用。
70.对于亲油离子液体的再生,就是使得亲油离子液体释放出已经吸附的气态物质。本技术对亲油离子液体的再生条件不做限制,凡是能够使得亲油离子液体脱除吸附的气态物质即可,如通过搅拌、加热等手段实现上述目;在本技术的另一些实施例中,出于经济的考虑,亲水离子液体的再生温度为80~120℃,再生真空度为
‑
0.1至
‑
0.05mpa,在上述条件下,离子液体能够迅速脱除吸附的气态物质。
71.对于亲油离子液体再生过程中,产生的少量尾气,记为第五尾气,含量较少,已经没有回收价值,可直接做溶剂回收处理。
72.亲水液体离子的种类
73.在本技术的一些实施例中,对亲水离子液体的种类不作限制,对水有较好亲和性的离子液体均可;在另一些实施例中,亲水离子液体为吡啶硫酸氢盐、甲基咪唑硫酸氢盐和乙基咪唑硫酸氢盐中的一种和几种。
74.亲水液体离子作用条件
75.在本技术的一些实施例中,对于亲水离子液体对第一尾气进行吸附条件,即亲水离子液体的作用条件不作限制,但需要保持亲水离子液体为离子液体状态,而不会转化为
溶液状态;由于离子液体的阴阳离子之间的力为库伦作用力,升高温度会使得阴阳离子之间的作用力减弱,过高温度容易使得离子液体转化为溶液,因此,在本技术的另一些实施例中,在采用亲水离子液体在对第一尾气进行吸附时,温度可设为20~50℃。
76.亲油液体离子的种类
77.在本技术的一些实施例中,对亲油离子液体的种类不作限制,对有机物有较好亲和性的离子液体均可;在另一些实施例中,亲油离子液体为1
‑
乙基
‑3‑
甲基咪唑磷酸二丁酯和/或1
‑
丁基
‑3‑
甲基咪唑磷酸二丁酯。
78.亲油液体离子作用条件
79.在本技术的一些实施例中,对于亲油离子液体对第一再生尾气进行吸附条件,即亲油离子液体的作用条件不作限制,但需要保持亲油离子液体为离子液体状态;在本技术的另一些实施例中,在采用亲油离子液体在对第一再生尾气进行吸附时,温度可设为20~40℃。
80.本技术针对上述方法,设计了尾气处理装置,如图2所示,图2示出了根据本技术的一个实施例的尾气处理装置的结构示意图,从图2可以看出,该尾气处理装置200主要包括:
81.冷却塔r
‑
1、吸附塔r
‑
2、脱水脱溶塔r
‑
3、加压精馏塔r
‑
4、吸附塔r
‑
5、过滤器(e
‑
1,e
‑
2,e
‑
3,e
‑
4)、离子液体再生釜v
‑
1、离子液体再生釜v
‑
2、hcl吸收釜v
‑
3、hcl再生釜v
‑
4、过滤罐t
‑
1、压缩机t
‑
2、以及冷凝器(c
‑
1,c
‑
2,c
‑
3)。
82.其中,冷却塔r
‑
1的出口连接吸附塔r
‑
2的入口,吸附塔r
‑
2的气态物质出口连接过滤罐t
‑
1、过滤罐t
‑
1依次连接过滤器e
‑
3、压缩机t
‑
2、过滤器e
‑
4和加压精馏塔r
‑
4。吸附塔r
‑
2的液态物质出口连接离子液体再生釜v
‑
1的入口,离子液体再生釜v
‑
1的液体物质出口连接冷凝器c
‑
1、过滤器e
‑
1和吸附塔r
‑
2的离子液体入口。离子液体再生釜v
‑
1的气态物质的出口连接脱水脱溶塔r
‑
3的入口。脱水脱溶塔r
‑
3的液态物质出口连接离子液体再生釜v
‑
2的入口,离子液体再生釜v
‑
2的液态物质出口依次连接冷凝器c
‑
2、过滤器e
‑
2、以及吸附塔r
‑
2的离子液体入口。脱水脱溶塔r
‑
3的气态物质出口连接hcl吸收釜v
‑
3、hcl再生釜v
‑
4、以及吸附塔r
‑
5。加压精馏塔r
‑
4的气态物质出口连接吸附塔r
‑
5的入口。
83.需要说明的是,上述描述仅是尾气处理装置200的主要连接关系,各个釜或者过滤器等的连接关系可以根据需要进行适应性调整,且各个釜的类型可以根据各自的功能需要进行选择,本技术不作限制,如脱溶釜可以选择蒸发型的反应釜,必要时可以设置真空泵;另外,也可以根据需要对上述装置中的各个釜或者过滤器等根据需要进行增加或删减。
84.采用上述尾气处理装置200实施尾气处理方法的过程可简述如下:
85.氯化尾气经冷却塔r
‑
1降温冷凝,去除大部分dmf、三氯乙烷和水,此时冷却塔r
‑
1的塔底水溶液送去溶剂回收,冷却塔r
‑
1的塔顶得到第一尾气,第一尾气进入脱水脱溶塔r
‑
2继续处理。
86.脱水脱溶塔r
‑
2中预置有亲水离子液体,可基本完全脱除尾气中剩余的水分,以及大部分溶剂,经脱水脱溶后,得到第二尾气,第二尾气进入下一步固体吸附剂吸附处理。而吸附水分和有机溶剂的亲水离子液体进入离子液体再生釜v
‑
1脱水脱溶再生,再生后的亲水离子液体经冷凝器e
‑
1冷却后,返回脱水脱溶塔r
‑
2继续使用,脱出的水、hcl、so2及有机溶剂形成的混合蒸气进入脱水脱溶塔r
‑
3继续处理。
87.过滤罐t
‑
1可选用活性炭罐t
‑
1,采用活性炭罐t
‑
1吸附脱水脱溶塔r
‑
2塔顶采出的
第二尾气中的残余溶剂,再经过滤器e
‑
3、压缩机t
‑
2、过滤器e
‑
4处理后,进入加压精馏塔r
‑
4分离处理,得到加压精馏塔r
‑
4的塔底高纯液体so2产品,加压精馏塔r
‑
4的塔顶得到的hcl气体去水吸附塔r
‑
5吸附处理,生成盐酸。
88.脱水脱溶塔r
‑
3可基本完全脱除再生釜v
‑
1蒸发出的第三尾气中的有机物,脱水脱溶塔r
‑
3的塔底采出的亲油离子液体经再生釜v
‑
2再生后,再经冷凝器e
‑
2冷凝,即可返回脱水脱溶塔r
‑
3继续使用;再生釜v
‑
2蒸出的有机物去溶剂回收。
89.脱水脱溶塔r
‑
3塔顶采出的水、hcl和so2形成的混合蒸气进入含有饱和食盐水的hcl吸收釜v
‑
3吸收hcl,含有so2和水的第四尾气返回脱水脱溶塔r
‑
2循环处理。
90.hcl吸收釜v
‑
3的吸附了hcl的饱和食盐水进入hcl再生釜v
‑
4,再生出的hcl水蒸气与加压精馏塔r
‑
4塔顶采出的hcl气体一同进入吸附塔r
‑
5吸附,即可从吸附塔r
‑
5的塔底获得品质较高的盐酸产品,塔顶微量尾气去做尾气处理。可根据经济和效果的综合需求,需要对上述步骤进行增加或删减,以达到预期效果。
91.氯化尾气的来源
92.在本技术的下述各实施例和对比例中,氯化尾气是采用单基团保护法制备三氯蔗糖时,蔗糖经过酯化得到的蔗糖
‑6‑
酯,与氯代试剂发生氯化反应,生成三氯蔗糖
‑6‑
酯产的尾气,下称氯化尾气。
93.实施例1
94.氯化尾气经冷却塔r
‑
1降温冷凝,冷凝至0℃,冷凝后,冷却塔r
‑
1的塔底水溶液送去溶剂回收,冷却塔r
‑
1的塔顶尾气,即第一尾气进入脱水脱溶塔r
‑
2继续处理。第一尾气进入预置有亲水离子液体的脱水脱溶塔r
‑
2,吸附温度设为40℃,其中,亲水离子液体为50wt%吡啶硫酸氢盐和50wt%甲基咪唑硫酸氢盐的混合物。脱水脱溶塔r
‑
2塔顶采出的第二尾气经活性炭罐t
‑
1吸附残余的有机气体,然后经过滤器e
‑
3、压缩机t
‑
2、过滤器e
‑
4处理后,进入加压精馏塔r
‑
4,加压精馏塔压力为2mpa,塔底温度0℃,塔顶温度10℃,从压精馏塔r
‑
4的塔底得到高纯液体so2,纯度99.9%;从加压精馏塔r
‑
4的塔顶得到的hcl气体进入水吸附塔r
‑
5吸附。
95.亲水离子液体的再生釜v
‑
1的釜顶蒸发出的水、有机溶剂及少量hcl、so2形成的第三尾气进入预置有亲油离子液体的脱水脱溶塔r
‑
3,其中,亲油离子液体为1
‑
乙基
‑3‑
甲基咪唑磷酸二丁酯,吸附温度为25℃。脱除有机组分后,脱水脱溶塔r
‑
3的塔底采出的亲油离子液体进入亲油离子液体的再生釜v
‑
2再生,再生温度为85℃,真空度
‑
0.09mpa,再经冷凝器e
‑
2冷却至25℃,然后返回脱水脱溶塔r
‑
3继续使用。脱水脱溶塔r
‑
3塔顶采出的水、hcl和so2形成的混合气体,记为第四尾气,第四尾气进入含有饱和氯化钠水溶液的hcl吸收釜v
‑
3吸附hcl气体,常温吸附。釜顶采出的含有so2和水的混合气体,记为第五尾气,第五尾气返回脱水脱溶塔r
‑
2继续处理,吸收釜v
‑
3的釜底采出的含有hcl的饱和食盐水进入hcl再生釜v
‑
4,再生出的hcl水蒸气与加压精馏塔r
‑
4塔顶采出的hcl气体一同进入水吸附塔r
‑
5吸附,即可从塔底获得品质较高的盐酸产品,纯度34.5%,塔顶微量尾气去做尾气处理。再生釜v
‑
4产生的饱和食盐水,补加部分纯水后返回hcl吸收釜v
‑
3继续使用。
96.实施例2
97.氯化尾气经冷却塔r
‑
1降温冷凝,冷凝至30℃,冷凝后,冷却塔r
‑
1的塔底水溶液送去溶剂回收,冷却塔r
‑
1的塔顶尾气,即第一尾气进入脱水脱溶塔r
‑
2继续处理。第一尾气进
入预置有亲水离子液体的脱水脱溶塔r
‑
2,吸附温度设为30℃,其中,亲水离子液体为40wt%吡啶硫酸氢盐和60wt%乙基咪唑硫酸氢盐的混合物。脱水脱溶塔r
‑
2的塔底使用后的亲水离子液体进入离子液体再生釜v
‑
1进行再生处理,再生温度为100℃,真空度
‑
0.07mpa,再生后的亲水离子液体从再生釜v
‑
1的釜底采出,经冷凝器e
‑
1冷却至30℃后,并经过过滤器e
‑
1过滤后,返回脱水脱溶塔r
‑
2继续使用。脱水脱溶塔r
‑
2塔顶采出的第二尾气经活性炭罐t
‑
1吸附残余的有机气体,然后经过滤器e
‑
3、压缩机t
‑
2、过滤器e
‑
4处理后,进入加压精馏塔r
‑
4,加压精馏塔压力为2.5mpa,塔底温度5℃,塔顶温度15℃,从压精馏塔r
‑
4的塔底得到高纯液体so2,纯度99.8%;从加压精馏塔r
‑
4的塔顶得到的采出的hcl气体进入水吸附塔r
‑
5吸附。
98.亲水离子液体的再生釜v
‑
1的釜顶蒸发出的水、有机溶剂及少量hcl、so2形成的第三尾气进入预置有亲油离子液体的脱水脱溶塔r
‑
3,其中,亲油离子液体为1
‑
丁基
‑3‑
甲基咪唑磷酸二丁酯,吸附温度为30℃。脱除有机组分后,脱水脱溶塔r
‑
3的塔底采出的亲油离子液体进入亲油离子液体的再生釜v
‑
2再生,再生温度为95℃,真空度
‑
0.07mpa,再经冷凝器e
‑
2冷却至30℃,然后返回脱水脱溶塔r
‑
3继续使用。脱水脱溶塔r
‑
3塔顶采出的水、hcl和so2形成的混合气体,记为第四尾气,第四尾气进入含有饱和氯化钠水溶液的hcl吸收釜v
‑
3吸附hcl气体,常温吸附。釜顶采出的含有so2和水的混合气体,记为第五尾气,第五尾气返回脱水脱溶塔r
‑
2继续处理,吸收釜v
‑
3的釜底采出的含有hcl的饱和食盐水进入hcl再生釜v
‑
4,再生出的hcl水蒸气与加压精馏塔r
‑
4塔顶采出的hcl气体一同进入水吸附塔r
‑
5吸附,即可从塔底获得品质较高的盐酸产品,纯度35.8%,塔顶微量尾气去做尾气处理。再生釜v
‑
4产生的饱和食盐水,补加部分纯水后返回hcl吸收釜v
‑
3继续使用。
99.实施例3
100.氯化尾气经冷却塔r
‑
1降温冷凝,冷凝至10℃,冷凝后,冷却塔r
‑
1的塔底水溶液送去溶剂回收,冷却塔r
‑
1的塔顶尾气,即第一尾气进入脱水脱溶塔r
‑
2继续处理。第一尾气进入预置有亲水离子液体的脱水脱溶塔r
‑
2,吸附温度设为40℃,其中,亲水离子液体为20wt%吡啶硫酸氢盐、30wt%甲基咪唑硫酸氢盐和50wt%乙基咪唑硫酸氢盐的混合物。脱水脱溶塔r
‑
2的塔底使用后的亲水离子液体进入离子液体再生釜v
‑
1进行再生处理,再生温度为120℃,真空度
‑
0.05mpa,再生后的亲水离子液体从再生釜v
‑
1的釜底采出,经冷凝器e
‑
1冷却至20℃后,并经过过滤器e
‑
1过滤后,返回脱水脱溶塔r
‑
2继续使用。脱水脱溶塔r
‑
2塔顶采出的第二尾气经活性炭罐t
‑
1吸附残余的有机气体,然后经过滤器e
‑
3、压缩机t
‑
2、过滤器e
‑
4处理后,进入加压精馏塔r
‑
4,加压精馏塔压力为1.5mpa,塔底温度
‑
5℃,塔顶温度5℃,从压精馏塔r
‑
4的塔底得到高纯液体so2,纯度99.7%;从加压精馏塔r
‑
4的塔顶得到的采出的hcl气体进入水吸附塔r
‑
5吸附。
101.亲水离子液体的再生釜v
‑
1的釜顶蒸发出的水、有机溶剂及少量hcl和so2形成的第三尾气进入预置有亲油离子液体的脱水脱溶塔r
‑
3,其中,亲油离子液体为1
‑
乙基
‑3‑
甲基咪唑磷酸二丁酯,吸附温度为35℃。脱除有机组分后,脱水脱溶塔r
‑
3的塔底采出的亲油离子液体进入亲油离子液体的再生釜v
‑
2再生,再生温度为80℃,真空度
‑
0.10mpa,再经冷凝器e
‑
2冷却至25℃,然后返回脱水脱溶塔r
‑
3继续使用。脱水脱溶塔r
‑
3塔顶采出的水、hcl和so2形成的混合气体,记为第四尾气,第四尾气进入含有饱和氯化钠水溶液的hcl吸收釜v
‑
3吸附hcl气体,常温吸附。釜顶采出的含有so2、水的混合气体,记为第五尾气,第五尾气
返回脱水脱溶塔r
‑
2继续处理,吸收釜v
‑
3的釜底采出的含有hcl的饱和食盐水进入hcl再生釜v
‑
4,再生出的hcl水蒸气与加压精馏塔r
‑
4塔顶采出的hcl气体一同进入水吸附塔r
‑
5吸附,即可从塔底获得品质较高的盐酸产品,纯度35.6%,塔顶微量尾气去做尾气处理。再生釜v
‑
4产生的饱和食盐水,补加部分纯水后返回hcl吸收釜v
‑
3继续使用。
102.实施例4
103.氯化尾气经冷却塔r
‑
1降温冷凝,冷凝至0℃,冷凝后,冷却塔r
‑
1的塔底水溶液送去溶剂回收,冷却塔r
‑
1的塔顶尾气,即第一尾气进入脱水脱溶塔r
‑
2继续处理。第一尾气进入预置有亲水离子液体的脱水脱溶塔r
‑
2,吸附温度设为40℃,其中,亲水离子液体为50wt%吡啶硫酸氢盐和50wt%甲基咪唑硫酸氢盐的混合物。脱水脱溶塔r
‑
2的塔底使用后的亲水离子液体进入离子液体再生釜v
‑
1进行再生处理,再生温度为80℃,真空度
‑
0.10mpa,再生后的亲水离子液体从再生釜v
‑
1的釜底采出,经冷凝器e
‑
1冷却至40℃后,并经过过滤器e
‑
1过滤后,返回脱水脱溶塔r
‑
2继续使用。脱水脱溶塔r
‑
2塔顶采出的第二尾气经活性炭罐t
‑
1吸附残余的有机气体,然后经过滤器e
‑
3、压缩机t
‑
2、过滤器e
‑
4处理后,进入加压精馏塔r
‑
4,加压精馏塔压力为2mpa,塔底温度0℃,塔顶温度10℃,从压精馏塔r
‑
4的塔底得到高纯液体so2,纯度99.9%;从加压精馏塔r
‑
4的塔顶得到的采出的hcl气体进入水吸附塔r
‑
5吸附处理。
104.亲水离子液体的再生釜v
‑
1的釜顶蒸发出的水、有机溶剂及少量hcl和so2形成的第三尾气进入预置有亲油离子液体的脱水脱溶塔r
‑
3,其中,亲油离子液体为1
‑
乙基
‑3‑
甲基咪唑磷酸二丁酯,吸附温度为20℃。脱除有机组分后,脱水脱溶塔r
‑
3的塔底采出的亲油离子液体进入亲油离子液体的再生釜v
‑
2再生,再生温度为90℃,真空度
‑
0.08mpa,再经冷凝器e
‑
2冷却至20℃,然后返回脱水脱溶塔r
‑
3继续使用。脱水脱溶塔r
‑
3塔顶采出的水、hcl和so2形成的混合气体,记为第四尾气,第四尾气进入含有饱和氯化钠水溶液的hcl吸收釜v
‑
3吸附hcl气体,常温吸附。釜顶采出的含有so2和水的混合气体,记为第五尾气,第五尾气返回脱水脱溶塔r
‑
2继续处理,吸收釜v
‑
3的釜底采出的含有hcl的饱和食盐水进入hcl再生釜v
‑
4,再生出的hcl水蒸气与加压精馏塔r
‑
4塔顶采出的hcl气体一同进入水吸附塔r
‑
5吸附,即可从塔底获得品质较高的盐酸产品,纯度35.1%,塔顶微量尾气去做尾气处理。再生釜v
‑
4产生的饱和食盐水,补加部分纯水后返回hcl吸收釜v
‑
3继续使用。
105.实施例5
106.氯化尾气经冷却塔r
‑
1降温冷凝,冷凝至30℃,冷凝后,冷却塔r
‑
1的塔底水溶液送去溶剂回收,冷却塔r
‑
1的塔顶尾气,即第一尾气进入脱水脱溶塔r
‑
2继续处理。第一尾气进入预置有亲水离子液体的脱水脱溶塔r
‑
2,吸附温度设为30℃,其中,亲水离子液体为40wt%吡啶硫酸氢盐和60wt%乙基咪唑硫酸氢盐的混合物。脱水脱溶塔r
‑
2的塔底使用后的亲水离子液体进入离子液体再生釜v
‑
1进行再生处理,再生温度为100℃,真空度
‑
0.07mpa,再生后的亲水离子液体从再生釜v
‑
1的釜底采出,经冷凝器e
‑
1冷却至30℃后,并经过过滤器e
‑
1过滤后,返回脱水脱溶塔r
‑
2继续使用。脱水脱溶塔r
‑
2塔顶采出的第二尾气经活性炭罐t
‑
1吸附残余的有机气体,然后经过滤器e
‑
3、压缩机t
‑
2、过滤器e
‑
4处理后,进入加压精馏塔r
‑
4,加压精馏塔压力为2.5mpa,塔底温度5℃,塔顶温度15℃,从压精馏塔r
‑
4的塔底得到高纯液体so2,纯度99.8%;从加压精馏塔r
‑
4的塔顶得到的采出的hcl气体进入水吸附塔r
‑
5吸附处理。
107.亲水离子液体的再生釜v
‑
1的釜顶蒸发出的水、有机溶剂及少量hcl和so2形成的第三尾气进入预置有亲油离子液体的脱水脱溶塔r
‑
3,其中,亲油离子液体为1
‑
丁基
‑3‑
甲基咪唑磷酸二丁酯,吸附温度为40℃。脱除有机组分后,脱水脱溶塔r
‑
3的塔底采出的亲油离子液体进入亲油离子液体的再生釜v
‑
2再生,再生温度为80℃,真空度
‑
0.10mpa,再经冷凝器e
‑
2冷却至40℃,然后返回脱水脱溶塔r
‑
3继续使用。脱水脱溶塔r
‑
3塔顶采出的水、hcl和so2形成的混合气体,记为第四尾气,第四尾气进入含有饱和氯化钠水溶液的hcl吸收釜v
‑
3吸附hcl气体,常温吸附。釜顶采出的含有so2和水的混合气体,记为第五尾气,第五尾气返回脱水脱溶塔r
‑
2继续处理,吸收釜v
‑
3的釜底采出的含有hcl的饱和食盐水进入hcl再生釜v
‑
4,再生出的hcl水蒸气与加压精馏塔r
‑
4塔顶采出的hcl气体一同进入水吸附塔r
‑
5吸附,即可从塔底获得品质较高的盐酸产品,纯度37.0%,塔顶微量尾气去做尾气处理。再生釜v
‑
4产生的饱和食盐水,补加部分纯水后返回hcl吸收釜v
‑
3继续使用。
108.实施例6
109.氯化尾气经冷却塔r
‑
1降温冷凝,冷凝至10℃,冷凝后,冷却塔r
‑
1的塔底水溶液送去溶剂回收,冷却塔r
‑
1的塔顶尾气,即第一尾气进入脱水脱溶塔r
‑
2继续处理。第一尾气进入预置有亲水离子液体的脱水脱溶塔r
‑
2,吸附温度设为20℃,其中,亲水离子液体为20wt%吡啶硫酸氢盐、30wt%甲基咪唑硫酸氢盐和50wt%乙基咪唑硫酸氢盐的混合物。脱水脱溶塔r
‑
2的塔底使用后的亲水离子液体进入离子液体再生釜v
‑
1进行再生处理,再生温度为120℃,真空度
‑
0.05mpa,再生后的亲水离子液体从再生釜v
‑
1的釜底采出,经冷凝器e
‑
1冷却至20℃后,并经过过滤器e
‑
1过滤后,返回脱水脱溶塔r
‑
2继续使用。脱水脱溶塔r
‑
2塔顶采出的第二尾气经活性炭罐t
‑
1吸附残余的有机气体,然后经过滤器e
‑
3、压缩机t
‑
2、过滤器e
‑
4处理后,进入加压精馏塔r
‑
4,加压精馏塔压力为1.5mpa,塔底温度
‑
5℃,塔顶温度5℃,从压精馏塔r
‑
4的塔底得到高纯液体so2,纯度99.9%;从加压精馏塔r
‑
4的塔顶得到的采出的hcl气体进入水吸附塔r
‑
5吸附处理。
110.亲水离子液体的再生釜v
‑
1的釜顶蒸发出的水、有机溶剂及少量hcl和so2形成的第三尾气进入预置有亲油离子液体的脱水脱溶塔r
‑
3,其中,亲油离子液体为50wt%1
‑
乙基
‑3‑
甲基咪唑磷酸二丁酯和50wt%1
‑
丁基
‑3‑
甲基咪唑磷酸二丁酯的混合物,吸附温度为30℃。脱除有机组分后,脱水脱溶塔r
‑
3的塔底采出的亲油离子液体进入亲油离子液体的再生釜v
‑
2再生,再生温度为110℃,真空度
‑
0.07mpa,再经冷凝器e
‑
2冷却至30℃,然后返回脱水脱溶塔r
‑
3继续使用。脱水脱溶塔r
‑
3塔顶采出的水、hcl和so2形成的混合气体,记为第四尾气,第四尾气进入含有饱和氯化钠水溶液的hcl吸收釜v
‑
3吸附hcl气体,常温吸附。釜顶采出的含有so2和水的混合气体,记为第五尾气,第五尾气返回脱水脱溶塔r
‑
2继续处理,吸收釜v
‑
3的釜底采出的含有hcl的饱和食盐水进入hcl再生釜v
‑
4,再生出的hcl水蒸气与加压精馏塔r
‑
4塔顶采出的hcl气体一同进入水吸附塔r
‑
5吸附,即可从塔底获得品质较高的盐酸产品,纯度34.9%,塔顶微量尾气去做尾气处理。再生釜v
‑
4产生的饱和食盐水,补加部分纯水后返回hcl吸收釜v
‑
3继续使用。
111.实施例7
112.氯化尾气经冷却塔r
‑
1降温冷凝,冷凝至20℃,冷凝后,冷却塔r
‑
1的塔底水溶液送去溶剂回收,冷却塔r
‑
1的塔顶尾气,即第一尾气进入脱水脱溶塔r
‑
2继续处理。第一尾气进入预置有亲水离子液体的脱水脱溶塔r
‑
2,吸附温度设为50℃,其中,亲水离子液体为
75wt%甲基咪唑硫酸氢盐和25wt%乙基咪唑硫酸氢盐的混合物。脱水脱溶塔r
‑
2的塔底使用后的亲水离子液体进入离子液体再生釜v
‑
1进行再生处理,再生温度为110℃,真空度
‑
0.06mpa,再生后的亲水离子液体从再生釜v
‑
1的釜底采出,经冷凝器e
‑
1冷却至50℃后,并经过过滤器e
‑
1过滤后,返回脱水脱溶塔r
‑
2继续使用。脱水脱溶塔r
‑
2塔顶采出的第二尾气经活性炭罐t
‑
1吸附残余的有机气体,然后经过滤器e
‑
3、压缩机t
‑
2、过滤器e
‑
4处理后,进入加压精馏塔r
‑
4,加压精馏塔压力为1.0mpa,塔底温度
‑
10℃,塔顶温度0℃,从压精馏塔r
‑
4的塔底得到高纯液体so2,纯度99.8%;从加压精馏塔r
‑
4的塔顶得到的采出的hcl气体进入水吸附塔r
‑
5吸附处理。
113.亲水离子液体的再生釜v
‑
1的釜顶蒸发出的水、有机溶剂及少量hcl和so2形成的第三尾气进入预置有亲油离子液体的脱水脱溶塔r
‑
3,其中,亲油离子液体为85wt%1
‑
乙基
‑3‑
甲基咪唑磷酸二丁酯和15wt%1
‑
丁基
‑3‑
甲基咪唑磷酸二丁酯的混合物,吸附温度为35℃。脱除有机组分后,脱水脱溶塔r
‑
3的塔底采出的亲油离子液体进入亲油离子液体的再生釜v
‑
2再生,再生温度为110℃,真空度
‑
0.07mpa,再经冷凝器e
‑
2冷却至30℃,然后返回脱水脱溶塔r
‑
3继续使用。脱水脱溶塔r
‑
3塔顶采出的水、hcl和so2形成的混合气体,记为第四尾气,第四尾气进入含有饱和氯化钠水溶液的hcl吸收釜v
‑
3吸附hcl气体,常温吸附。釜顶采出的含有so2和水的混合气体,记为第五尾气,第五尾气返回脱水脱溶塔r
‑
2继续处理,吸收釜v
‑
3的釜底采出的含有hcl的饱和食盐水进入hcl再生釜v
‑
4,再生出的hcl水蒸气与加压精馏塔r
‑
4塔顶采出的hcl气体一同进入水吸附塔r
‑
5吸附,即可从塔底获得品质较高的盐酸产品,纯度36.1%,塔顶微量尾气去做尾气处理。再生釜v
‑
4产生的饱和食盐水,补加部分纯水后返回hcl吸收釜v
‑
3继续使用。
114.实施例8
115.氯化尾气经冷却塔r
‑
1降温冷凝,冷凝至15℃,冷凝后,冷却塔r
‑
1的塔底水溶液送去溶剂回收,冷却塔r
‑
1的塔顶尾气,即第一尾气进入脱水脱溶塔r
‑
2继续处理。第一尾气进入预置有亲水离子液体的脱水脱溶塔r
‑
2,吸附温度设为25℃,其中,亲水离子液体为15wt%甲基咪唑硫酸氢盐和85wt%乙基咪唑硫酸氢盐的混合物。脱水脱溶塔r
‑
2的塔底使用后的亲水离子液体进入离子液体再生釜v
‑
1进行再生处理,再生温度为100℃,真空度
‑
0.07mpa,再生后的亲水离子液体从再生釜v
‑
1的釜底采出,经冷凝器e
‑
1冷却至25℃后,并经过过滤器e
‑
1过滤后,返回脱水脱溶塔r
‑
2继续使用。脱水脱溶塔r
‑
2塔顶采出的第二尾气经活性炭罐t
‑
1吸附残余的有机气体,然后经过滤器e
‑
3、压缩机t
‑
2、过滤器e
‑
4处理后,进入加压精馏塔r
‑
4,加压精馏塔压力为3.0mpa,塔底温度10℃,塔顶温度20℃,从压精馏塔r
‑
4的塔底得到高纯液体so2,纯度99.7%;从加压精馏塔r
‑
4的塔顶得到的采出的hcl气体进入水吸附塔r
‑
5吸附处理。
116.亲水离子液体的再生釜v
‑
1的釜顶蒸发出的水、有机溶剂及少量hcl和so2形成的第三尾气进入预置有亲油离子液体的脱水脱溶塔r
‑
3,其中,亲油离子液体为25wt%1
‑
乙基
‑3‑
甲基咪唑磷酸二丁酯和75wt%1
‑
丁基
‑3‑
甲基咪唑磷酸二丁酯的混合物,吸附温度为25℃。脱除有机组分后,脱水脱溶塔r
‑
3的塔底采出的亲油离子液体进入亲油离子液体的再生釜v
‑
2再生,再生温度为95℃,真空度
‑
0.08mpa,再经冷凝器e
‑
2冷却至25℃,然后返回脱水脱溶塔r
‑
3继续使用。脱水脱溶塔r
‑
3塔顶采出的水、hcl和so2形成的混合气体,记为第四尾气,第四尾气进入含有饱和氯化钠水溶液的hcl吸收釜v
‑
3吸附hcl气体,常温吸附。釜顶
采出的含有so2和水的混合气体,记为第五尾气,第五尾气返回脱水脱溶塔r
‑
2继续处理,吸收釜v
‑
3的釜底采出的含有hcl的饱和食盐水进入hcl再生釜v
‑
4,再生出的hcl水蒸气与加压精馏塔r
‑
4塔顶采出的hcl气体一同进入水吸附塔r
‑
5吸附,即可从塔底获得品质较高的盐酸产品,纯度35.5%,塔顶微量尾气去做尾气处理。再生釜v
‑
4产生的饱和食盐水,补加部分纯水后返回hcl吸收釜v
‑
3继续使用。
117.实施例9
118.氯化尾气经冷却塔r
‑
1降温冷凝,冷凝至5℃,冷凝后,冷却塔r
‑
1的塔底水溶液送去溶剂回收,冷却塔r
‑
1的塔顶尾气,即第一尾气进入脱水脱溶塔r
‑
2继续处理。第一尾气进入预置有亲水离子液体的脱水脱溶塔r
‑
2,吸附温度设为35℃,其中,亲水离子液体为15wt%吡啶硫酸氢盐和85wt%乙基咪唑硫酸氢盐的混合物。脱水脱溶塔r
‑
2的塔底使用后的亲水离子液体进入离子液体再生釜v
‑
1进行再生处理,再生温度为105℃,真空度
‑
0.07mpa,再生后的亲水离子液体从再生釜v
‑
1的釜底采出,经冷凝器e
‑
1冷却至35℃后,并经过过滤器e
‑
1过滤后,返回脱水脱溶塔r
‑
2继续使用。脱水脱溶塔r
‑
2塔顶采出的第二尾气经活性炭罐t
‑
1吸附残余的有机气体,然后经过滤器e
‑
3、压缩机t
‑
2、过滤器e
‑
4处理后,进入加压精馏塔r
‑
4,加压精馏塔压力为2.5mpa,塔底温度5℃,塔顶温度15℃,从压精馏塔r
‑
4的塔底得到高纯液体so2,纯度99.9%;从加压精馏塔r
‑
4的塔顶得到的采出的hcl气体进入水吸附塔r
‑
5吸附处理。
119.亲水离子液体的再生釜v
‑
1的釜顶蒸发出的水、有机溶剂及少量hcl和so2形成的第三尾气进入预置有亲油离子液体的脱水脱溶塔r
‑
3,其中,亲油离子液体为1
‑
乙基
‑3‑
甲基咪唑磷酸二丁酯,吸附温度为35℃。脱除有机组分后,脱水脱溶塔r
‑
3的塔底采出的亲油离子液体进入亲油离子液体的再生釜v
‑
2再生,再生温度为85℃,真空度
‑
0.09mpa,再经冷凝器e
‑
2冷却至35℃,然后返回脱水脱溶塔r
‑
3继续使用。脱水脱溶塔r
‑
3塔顶采出的水、hcl和so2形成的混合气体,记为第四尾气,第四尾气进入含有饱和氯化钠水溶液的hcl吸收釜v
‑
3吸附hcl气体,常温吸附。釜顶采出的含有so2和水的混合气体,记为第五尾气,第五尾气返回脱水脱溶塔r
‑
2继续处理,吸收釜v
‑
3的釜底采出的含有hcl的饱和食盐水进入hcl再生釜v
‑
4,再生出的hcl水蒸气与加压精馏塔r
‑
4塔顶采出的hcl气体一同进入水吸附塔r
‑
5吸附,即可从塔底获得品质较高的盐酸产品,纯度36.5%,塔顶微量尾气去做尾气处理。再生釜v
‑
4产生的饱和食盐水,补加部分纯水后返回hcl吸收釜v
‑
3继续使用。
120.实施例10
121.氯化尾气经冷却塔r
‑
1降温冷凝,冷凝至25℃,冷凝后,冷却塔r
‑
1的塔底水溶液送去溶剂回收,冷却塔r
‑
1的塔顶尾气,即第一尾气进入脱水脱溶塔r
‑
2继续处理。第一尾气进入预置有亲水离子液体的脱水脱溶塔r
‑
2,吸附温度设为45℃,其中,亲水离子液体为35wt%吡啶酸氢盐和65wt%甲基咪唑硫酸氢盐的混合物。脱水脱溶塔r
‑
2的塔底使用后的亲水离子液体进入离子液体再生釜v
‑
1进行再生处理,再生温度为115℃,真空度
‑
0.06mpa,再生后的亲水离子液体从再生釜v
‑
1的釜底采出,经冷凝器e
‑
1冷却至45℃后,并经过过滤器e
‑
1过滤后,返回脱水脱溶塔r
‑
2继续使用。脱水脱溶塔r
‑
2塔顶采出的第二尾气经活性炭罐t
‑
1吸附残余的有机气体,然后经过滤器e
‑
3、压缩机t
‑
2、过滤器e
‑
4处理后,进入加压精馏塔r
‑
4,加压精馏塔压力为1.5mpa,塔底温度
‑
5℃,塔顶温度5℃,从压精馏塔r
‑
4的塔底得到高纯液体so2,纯度99.7%;从加压精馏塔r
‑
4的塔顶得到的采出的hcl气体进入水吸附塔
r
‑
5吸附处理。
122.亲水离子液体的再生釜v
‑
1的釜顶蒸发出的水、有机溶剂及少量hcl和so2形成的第三尾气进入预置有亲油离子液体的脱水脱溶塔r
‑
3,其中,亲油离子液体为1
‑
丁基
‑3‑
甲基咪唑磷酸二丁酯,吸附温度为20℃。脱除有机组分后,脱水脱溶塔r
‑
3的塔底采出的亲油离子液体进入亲油离子液体的再生釜v
‑
2再生,再生温度为115℃,真空度
‑
0.06mpa,再经冷凝器e
‑
2冷却至20℃,然后返回脱水脱溶塔r
‑
3继续使用。脱水脱溶塔r
‑
3塔顶采出的水、hcl和so2形成的混合气体,记为第四尾气,第四尾气进入含有饱和氯化钠水溶液的hcl吸收釜v
‑
3吸附hcl气体,常温吸附。釜顶采出的含有so2和水的混合气体,记为第五尾气,第五尾气返回脱水脱溶塔r
‑
2继续处理,吸收釜v
‑
3的釜底采出的含有hcl的饱和食盐水进入hcl再生釜v
‑
4,再生出的hcl水蒸气与加压精馏塔r
‑
4塔顶采出的hcl气体一同进入水吸附塔r
‑
5吸附,即可从塔底获得品质较高的盐酸产品,纯度35.5%,塔顶微量尾气去做尾气处理。再生釜v
‑
4产生的饱和食盐水,补加部分纯水后返回hcl吸收釜v
‑
3继续使用。
123.实施例11
124.氯化尾气经冷却塔r
‑
1降温冷凝,冷凝至35℃,冷凝后,冷却塔r
‑
1的塔底水溶液送去溶剂回收,冷却塔r
‑
1的塔顶尾气,即第一尾气进入脱水脱溶塔r
‑
2继续处理。第一尾气进入预置有亲水离子液体的脱水脱溶塔r
‑
2,吸附温度设为35℃,其中,亲水离子液体为75wt%吡啶酸氢盐和25wt%乙基咪唑硫酸氢盐的混合物。脱水脱溶塔r
‑
2的塔底使用后的亲水离子液体进入离子液体再生釜v
‑
1进行再生处理,再生温度为85℃,真空度
‑
0.09mpa,再生后的亲水离子液体从再生釜v
‑
1的釜底采出,经冷凝器e
‑
1冷却至35℃后,并经过过滤器e
‑
1过滤后,返回脱水脱溶塔r
‑
2继续使用。脱水脱溶塔r
‑
2塔顶采出的第二尾气经活性炭罐t
‑
1吸附残余的有机气体,然后经过滤器e
‑
3、压缩机t
‑
2、过滤器e
‑
4处理后,进入加压精馏塔r
‑
4,加压精馏塔压力为1.0mpa,塔底温度
‑
10℃,塔顶温度0℃,从压精馏塔r
‑
4的塔底得到高纯液体so2,纯度99.9%;从加压精馏塔r
‑
4的塔顶得到的采出的hcl气体进入水吸附塔r
‑
5吸附处理。
125.亲水离子液体的再生釜v
‑
1的釜顶蒸发出的水、有机溶剂及少量hcl和so2形成的第三尾气进入预置有亲油离子液体的脱水脱溶塔r
‑
3,其中,亲油离子液体为1
‑
乙基
‑3‑
甲基咪唑磷酸二丁酯,吸附温度为25℃。脱除有机组分后,脱水脱溶塔r
‑
3的塔底采出的亲油离子液体进入亲油离子液体的再生釜v
‑
2再生,再生温度为105℃,真空度
‑
0.07mpa,再经冷凝器e
‑
2冷却至25℃,然后返回脱水脱溶塔r
‑
3继续使用。脱水脱溶塔r
‑
3塔顶采出的水、hcl和so2形成的混合气体,记为第四尾气,第四尾气进入含有饱和氯化钠水溶液的hcl吸收釜v
‑
3吸附hcl气体,常温吸附。釜顶采出的含有so2和水的混合气体,记为第五尾气,第五尾气返回脱水脱溶塔r
‑
2继续处理,吸收釜v
‑
3的釜底采出的含有hcl的饱和食盐水进入hcl再生釜v
‑
4,再生出的hcl水蒸气与加压精馏塔r
‑
4塔顶采出的hcl气体一同进入水吸附塔r
‑
5吸附,即可从塔底获得品质较高的盐酸产品,纯度36.5%,塔顶微量尾气去做尾气处理。再生釜v
‑
4产生的饱和食盐水,补加部分纯水后返回hcl吸收釜v
‑
3继续使用。
126.对比例1
127.氯化尾气经冷凝塔冷凝,冷凝温度为20℃,除去大部分有机溶剂,然后经浓硫酸脱水,水含量低于0.01%,然后将气体经活性炭吸附处理,气体经压缩机压缩后再进入加压精馏塔分离,加压精馏塔压力为1.0mpa,塔底温度
‑
10℃,塔顶温度0℃,从压精馏塔r
‑
4的塔底
得到液体so2,纯度98.5%,其中有机物含量1.3%;塔顶hcl气体进入水吸附塔吸附,塔底得到盐酸产品,纯度35.1%,塔顶微量气体去做尾气处理。
128.综上所述,本技术利用离子液体吸附氯化尾气中的杂质,在加压精馏前,有效解决了水及有机物对hcl和so2两种气体分离的影响,解决了因加压分离过程中产生的有机/无机固体附着在管壁及输送泵造成的严重腐蚀及堵塞问题,且可获得高纯度的液体so2产品;离子液体的腐蚀性极低,采用离子液体代替浓硫酸,可有效克服传统技术中浓硫酸脱水带来的设备腐蚀及后续处理问题;此外,离子液体具有可高再生性,且再生工艺简单,极大程度上降低了尾气处理的成本。本技术以离子液体为主,并且与冷凝、精馏等手段有机结合,能够有效处理三氯蔗糖生产工艺中的氯化尾气,实现hcl和so2两种气体的有效分离,获得高品质的盐酸和液态so2产品,且整体处理工艺简单、成本低、具有极大的经济和应用价值。
129.在本技术的描述中,需要说明的是,术语“中心”、“上”、“下”、“左”、“右”、“竖直”、“水平”、“内”、“外”等指示的方位或位置关系为基于附图所示的方位或位置关系,仅是为了便于描述本技术和简化描述,而不是指示或暗示所指的装置或元件必须具有特定的方位、以特定的方位构造和操作,因此不能理解为对本技术的限制。此外,术语“第一”、“第二”、“第三”等仅用于描述目的,而不能理解为指示或暗示相对重要性。
130.在本技术的描述中,需要说明的是,除非另有明确的规定和限定,术语“安装”、“相连”、“连接”应做广义理解,例如,可以是固定连接,也可以是可拆卸连接,或一体地连接;可以是机械连接,也可以是电连接;可以是直接相连,也可以通过中间媒介间接相连,可以是两个元件内部的连通。对于本领域的普通技术人员而言,可以具体情况理解上述术语在本技术中的具体含义。
131.以上所述,仅为本技术的具体实施方式,在本技术的上述教导下,本领域技术人员可以在上述实施例的基础上进行其他的改进或变形。本领域技术人员应该明白,上述的具体描述只是更好的解释本技术的目的,本技术的保护范围应以权利要求的保护范围为准。
132.此外,本领域的技术人员能够理解,尽管在此所述的一些实施例包括其它实施例中所包括的某些特征而不是其它特征,但是不同实施例的特征的组合意味着处于本技术的范围之内并且形成不同的实施例。例如,在下面的权利要求书中,所要求保护的实施例的任意之一都可以以任意的组合方式来使用。