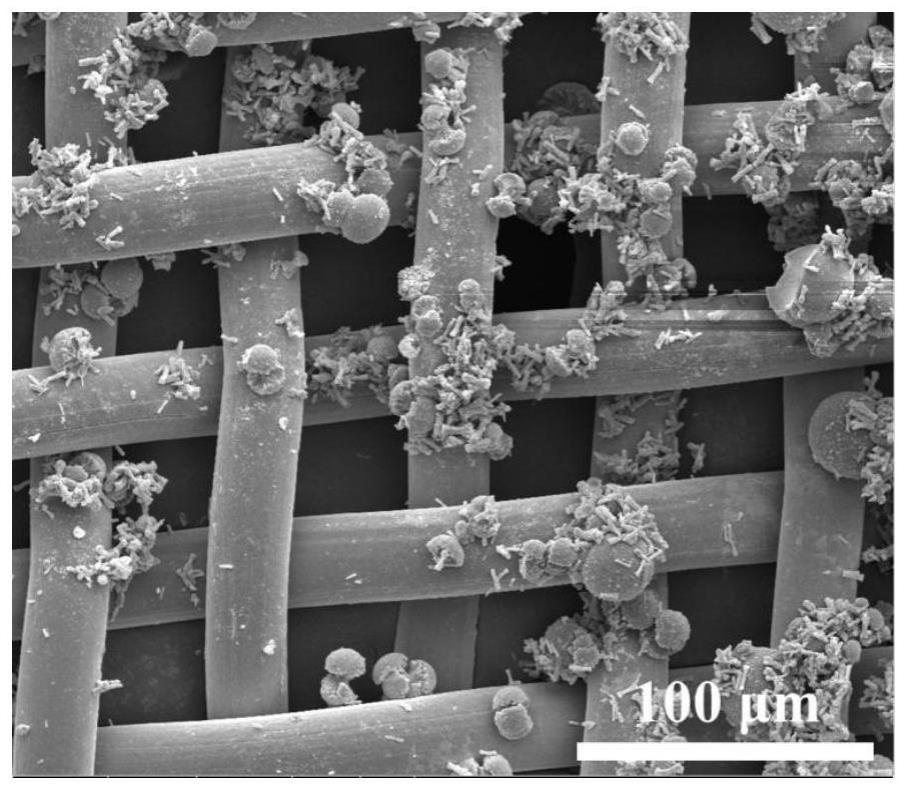
1.本发明属于油水分离材料及其制备技术领域,具体涉及一种水下疏油/油下疏水可切换的油水分离材料及其制备方法。
背景技术:2.随着社会的快速发展,人们对于化学制品的需求量日益增加,这极大地促进了化工及材料行业的快速发展。然而,化工及材料行业的快速发展也使得化工原料的泄漏事故也日益增多,尤其是含卤素有机溶剂进入水体后因其密度大于水而位于在水体下层,使得其无法通过传统的吸附法或自然挥发的方式进行去除。这些位于水体下层的有机试剂会造成严重的水体和土壤污染。与此同时,在海上原油运输过程中频发的泄漏事故也不仅造成了水体和土壤污染,还带来了巨大的能源浪费。目前,过油阻水和过水阻油是用于含油废水处理的两大类材料之一。过油阻水材料主要被用于含重油(密度大于水)废水处理,而过水阻油主要应用于含轻油(密度小于水)废水处理。
3.过油阻水和过水阻油材料均是利用材料表面对油或水的相反润湿性,即亲水疏油性、亲油疏水性、水下疏油和油下疏水等性能。其中实现亲水疏油通常需要具有低表面能的长链含氟硅氧烷改性,亲油疏水性则需要含氟磺酸钠等物质的改性,这些物质不仅价格昂贵且具有一定生物毒性,对环境存在潜在威胁。而水下疏油和油下疏水性是通过水或油润湿来提供相异的润湿性,也是实现过水阻油和过油阻水的有效手段。
4.在一个给定的油水体系中,水下油接触角和油下水接触角之和理论上等于180
°
,即水下疏油和油下疏水性是热力学不稳定状态,因此无法通过常规方法同时获得油下疏水且可水下疏油的材料。但是同时具备水下疏油性和油下疏水性可使得材料能够应用于各种类型的含油废水的处理,即可过水阻油亦可过油阻水从而实现含油废水的可切换分离。目前已经报道的在同一油水体系中能同时实现水下疏油和油下疏水性的材料通常在空气中通常表现为亲水性且制备过程繁琐。如tian等(tianx,jokinenv,li j,sainio j,rasrh.unusual dual superlyophobic surfaces in oil-water systems:the designprinciples[j].advancedmaterials,2016,28(48):10652-10658.)通过等离子刻蚀,制备了水下疏油和油下疏水阵列的材料,并从理论上证明了该阵列材料需要满足在空气中水接触角在56~74
°
之间就可实现水下疏油和油下疏水性。然而该材料仅适用于一个特定的油水体系,当油水体系更换后需要重新修饰才可再次实现水下疏油和油下疏水性。kang及其合作者(kangl,wangb,zengj s,chengz,li jp,xuj,gaowh,chenkf.degradable dual superlyophobic lignocellulosic fibers for high-efficiency oil/water separation[j].green chemistry,2020,22(2):504-512.)采用三聚氰胺甲醛树脂改性木质素制备了同时具有水下疏油和油下疏水性材料,其在空气中具有超亲水性(水接触角近似等于0
°
)。wu等(wu m,shi g,liu w,long y,mu p,li j.a universal strategy for the preparation of dual superlyophobic surfaces in oil
–
water systems[j].acs applied materials&interfaces,2021,13(12):14759-14767.)采用山软木、黄土、二氧化
钛和十八烷基三氯硅烷为原料制备了油下疏水和水下疏油的材料,并用于含油废水净化,然而,其使用循环性较差,且仍然无法避免使用昂贵且具有强腐蚀性的硅氧烷。综上所述,目前已经报道的在同一油水体系中同时具有水下疏油和油下疏水性的材料,通常需要在空气中满足亲水性,且存在制备过程复杂、产物循环使用性差、需使用昂贵剧毒或腐蚀性试剂、通常不能适应多种油水体系以及不能将方法拓展于更多基材等问题。因此,亟需找到一种经济成本低、绿色环保、可适用于多种基材以用于过水阻油和过油阻水可切换分离油水的水下疏油和油下疏水材料的制备方法且制备的材料在空气中具有宽的亲疏水性,以满足不同类型含油废水净化处理。
技术实现要素:[0005]
本发明的目的是针对上述现有技术存在的缺陷或问题,提供一种水下疏油/油下疏水可切换的油水分离材料,该材料具有高通量、高分离效率、高循环耐久使用性的特点。
[0006]
本发明的另一目的是提供一种水下疏油/油下疏水可切换的油水分离材料的制备方法,该方法制备工艺简单环保、成本低,且适用基材广泛。
[0007]
本发明提供的一种水下疏油/油下疏水可切换的油水分离材料,其特征在于该材料是由酚类化合物改性并由有机配体和金属离子生成的化合物自组装形成的微纳米结构附着于多孔网状基底材料表面组成,该材料在空气中水接触角为0~155
°
,在水下油接触角大于90
°
且在油下水接触角大于90
°
,其既能用于过油阻水又能用于过水阻油来分离油水混合物。
[0008]
以上油水分离材料在空气中水接触角为90~155
°
,在水下油接触角大于90
°
且在油下水接触角大于90
°
。
[0009]
当以上油水分离材料在空气中接触角大于90
°
时,在同一油水体系中水下油接触角大于90
°
,油下水接触角大于90
°
。
[0010]
以上油水分离材料中所述的酚类化合物为苯酚、邻苯二酚、间苯二酚、对苯二酚、单宁酸、没食子酸、多巴胺、多巴和新绿原酸中的至少一种。
[0011]
以上油水分离材料中所述的有机配体为咪唑、1-甲基咪唑、2-甲基咪唑、4-甲基咪唑、咪唑-2-甲醛、苯并咪唑、咪唑-4,5-二羧酸、4-羟甲基咪唑盐酸盐、咪唑-4-甲酸乙酯、咪唑-4-甲酸甲酯和1h-咪唑-4-甲酸中的至少一种。
[0012]
以上油水分离材料中所述的金属离子为zn
2+
、co
2+
、cu
2+
、fe
2+
、fe
3+
、in
2+
、ni
2+
、mg
2+
或ba
2+
中的任一种。
[0013]
以上油水分离材料中所述的多孔网状基底材料为不锈钢金属筛网、聚合物泡沫、铜泡沫、滤布、棉织物或砂芯滤板中的任一种。
[0014]
以上油水分离材料中可用于过油阻水是指用于重油-水混合物的分离,又能用于过水阻油是指用于轻油-水混合物的分离。
[0015]
本发明提供的上述水下疏油/油下疏水可切换的油水分离材料的制备方法,该方法工艺步骤和条件如下:
[0016]
(1)先将多孔网状基底材料置于配制的浓度为0.1mmol/l~10mol/l的酚类化合物水溶液中于5~50℃浸泡反应0.5~48h后取出,干燥;
[0017]
(2)先分别配制浓度为1mmol/l~15mol/l的金属离子前驱体水溶液和浓度为
1mmol/l~15mol/l的有机配体水溶液,再按水溶液中有机配体与金属离子的摩尔比为20:1~1:20配制混合溶液,然后将第(1)步骤中干燥后所得的多孔网状基底材料浸泡于该混合溶液中,于5~50℃反应0.5~48h后用去离子水冲洗、干燥即可。
[0018]
以上方法中所用的酚类化合物溶液为苯酚、邻苯二酚、间苯二酚、对苯二酚、单宁酸、没食子酸、多巴胺、多巴和新绿原酸中的至少一种配制而成。
[0019]
以上方法中所用的有机配体溶液为咪唑、1-甲基咪唑、2-甲基咪唑、4-甲基咪唑、咪唑-2-甲醛、苯并咪唑、咪唑-4,5-二羧酸、4-羟甲基咪唑盐酸盐、咪唑-4-甲酸乙酯、咪唑-4-甲酸甲酯和1h-咪唑-4-甲酸中的至少一种配制而成。
[0020]
以上方法中所用的金属离子前驱体溶液为含zn
2+
的前驱体溶液、含co
2+
的前驱体溶液、含cu
2+
的前驱体溶液、含fe
2+
的前驱体溶液、含fe
3+
的前驱体溶液、含in
2+
的前驱体溶液、含ni
2+
的前驱体溶液、含mg
2+
的前驱体溶液或含ba
2+
的前驱体溶液中的任一种,其中含zn
2+
的前驱体溶液为由硫酸锌、卤化锌、硝酸锌、醋酸锌或磷酸二氢锌中的任一种配制而成;含co
2+
的前驱体溶液为硫酸钴、卤化钴、硝酸钴、醋酸钴或磷酸二氢钴中的任一种配制而成;含cu
2+
的前驱体溶液为硫酸铜、卤化铜、硝酸铜、醋酸铜或磷酸二氢铜中的任一种配制而成;含fe
2+
的前驱体溶液为硫酸亚铁、卤化亚铁、硝酸亚铁或醋酸亚铁中的任一种配制而成;含fe
3+
的前驱体溶液为硫酸铁、卤化铁、硝酸铁或醋酸铁中的任一种配制而成;含in
2+
的前驱体溶液为硫酸铟、卤化铟、硝酸铟或醋酸铟中的任一种配制而成;含ni
2+
的前驱体溶液为硫酸镍、卤化镍、硝酸镍或醋酸镍中的任一种配制而成;含mg
2+
的前驱体溶液为硫酸镁、卤化镁硝酸镁或醋酸镁中的任一种配制而成;含ba
2+
的前驱体溶液卤化钡、硝酸钡或醋酸钡中的任一种配制而成。
[0021]
以上方法中所用的多孔网状基底材料为不锈钢金属筛网、聚合物泡沫、铜泡沫、滤布、棉织物或砂芯滤板中的任一种。
[0022]
以上方法中所用的有机配体与金属离子前驱体溶液中金属离子的摩尔比优选4:1~1:4。
[0023]
以上方法第(1)步中酚类化合物浸泡反应时间优选1~24h。
[0024]
以上方法第(1)步中酚类化合物浓度优选0.2~2mol/l。
[0025]
以上方法第(2)步中反应时间优选1~24h。
[0026]
以上方法第(1)步中配制的酚类化合物水溶液的浓度为0.1mmol/l~3mol/l;第(2)步配制的金属离子前驱体水溶液的浓度为1mmol/l~5mol/l,配制的有机配体水溶液的浓度为1mmol/l~5mol/l,且配制的混合溶液中按水溶液中有机配体与金属离子的摩尔比为5:1~1:5。
[0027]
本发明与现有技术相比,具有以下有益效果:
[0028]
1、由于本发明所提供的水下疏油/油下疏水可切换的油水分离材料由酚类物质改性多孔网状基底材料后再附着有由有机配体和金属离子生成的化合物自组装形成的微纳米结构,使该材料在空气中对水润湿性更广,即该材料在空气中表现为亲水或疏水,均可实现同时实现水下疏油和油下疏水,因而能满足在不同类型油水体系中的水下疏油和油下疏水的切换。
[0029]
2、由于本发明所提供的水下疏油/油下疏水可切换的油水分离材料由酚类物质改性多孔网状基底材料随后附着有由有机配体和金属离子生成的化合物自组装形成的微纳
米结构,因而该材料不仅能够满足在不同类型油水体系中的水下疏油和油下疏水的切换分离,且分离油水50个循环后,分离效率还可以高于98.55%。
[0030]
3、由于本发明提供的制备方法所采用的原料均为来源广泛、价格低廉的酚类物质、有机配体和含金属离子化合物,因而不仅可以降低所得油水分离材料的成本,且更易于扩大生产。
[0031]
4、由于本发明提供的方法在制备过程中只采用水作为溶剂,不仅摒弃了现有技术采用的价格昂贵的含氟含硅试剂,还省去了购置庞大且昂贵的制备设施的费用,因而既绿色环保,又可以进一步降低成本。
[0032]
5、由于本发明提供的方法的制备过程简单、能耗低,因而便于推广应用。
附图说明
[0033]
图1为本发明实施例5所制得的水下疏油/油下疏水可切换的不锈钢金属筛网的扫描电镜照片。从照片中可见金属离子与有机配体反应生成的化合物自组装形成的微纳米结构并均匀地附着在筛网表面。
[0034]
图2为本发明实施例5所制得的水下疏油/油下疏水可切换的不锈钢金属筛网的能量色散x射线光谱仪谱图及数据结果。通过各元素原子摩尔比进行计算对比可知金属离子与有机配体反应形成的化合物已成功改性到了网膜表面。
[0035]
图3为本发明实施例5所制得的水下疏油/油下疏水可切换的不锈钢金属筛网用于原油抗污染测试照片。从第一张照片可见,所制得的筛网在原油中浸泡后,其表面覆盖了一层原油;从第二张照片可见,将上述覆盖有原油的筛网浸入清水中后,其表面的原油被去除。
[0036]
图4为本发明实施例5所制得的水下疏油/油下疏水可切换的不锈钢金属筛网过油阻水测试图。从图中可见,重油成功滤过,而水相被阻隔,实现了重油/水混合物的分离。
[0037]
图5为本发明实施例5所制得的水下疏油/油下疏水可切换的不锈钢金属筛网过水阻油测试图。从图中可见,水成功通过,而油相被阻隔,实现了轻油/水混合物的分离。
[0038]
图6为本发明应用例1中采用所制备的水下疏油/油下疏水可切换的不锈钢金属筛网应用于正己烷/水、石油醚/水和二氯甲烷/水等混合物的过水阻油以及过油阻水可切换的油水分离图。从图可知,该材料能成功实现过水阻油和过油阻水的分离。
[0039]
图7为本发明应用例1中采用所制备的水下疏油/油下疏水可切换的不锈钢金属筛网应用于正己烷/水和石油醚/水等混合物的过水阻油以及应用于二氯甲烷/水混合物的过油阻水分离的分离效率与循环分离次数的图谱。由图可知,循环分离50次后,分离效率仍大于98.55%。
[0040]
图8为本发明应用例2中采用所制备的水下疏油/油下疏水可切换的不锈钢金属筛网应用于正己烷/水和二氯甲烷/水等混合物的过水阻油以及过油阻水可切换的油水分离图。从图可知,该材料能成功实现过水阻油和过油阻水的分离。且对于同一种油水体系既可实现过水阻油亦可实现过油阻水。
[0041]
图9为本发明应用例2中采用所制备的水下疏油/油下疏水可切换的不锈钢金属筛网应用于正己烷/水混合物的过水阻油以及应用于二氯甲烷/水混合物的过油阻水分离的分离效率与循环分离次数的图谱。由图可知,循环分离50次后,分离效率仍大于98.55%。
具体实施方式
[0042]
下面给出实施例,以对本发明的技术方案进行清楚、完整地描述,但是,所给出的实施例仅仅是本发明技术方案的一部分实施例,而不是其全部的实施例。基于本发明中的技术方案,本领域普通技术人员在没有作出创造性劳动的前提下所获得的其他实施例,都属于本发明的保护范围。
[0043]
另外,值得说明的是,1)材料表面水接触角大于90
°
时,该材料为疏水性,而当材料表面水接触角小于90
°
时,该材料为亲水性;与之类似,材料表面油接触角大于90
°
时,该材料为疏油性,而当材料表面油接触角小于90
°
时,该材料为亲油性;材料水下疏油即指材料在水中的油接触角大于90
°
,而材料油下疏水即指材料在油中的水接触角大于90
°
;2)材料在空气中水接触角由下述方法测得:将材料水平置放于水接触角测试仪平台,在其表面滴放约5μl水滴,5s后拍摄水滴形态,用自带软件计算其水接触角数值;3)材料在水下油接触角由下述方法测得:将材料浸泡于盛有水的透明容器中,将容器置放于水接触角测试仪样品平台,保持样品水平,在其表面滴落约5μl油滴,5s后拍摄油滴形态,用自带软件计算其水下油接触角数值;材料在油下水接触角由下述方法测得:将材料浸泡于盛有油的透明容器中,将容器置放于水接触角测试仪样品平台,保持样品水平,在其表面滴落约5μl水滴,5s后拍摄水滴形态,用自带软件计算其油下水接触角数值;4)材料过水阻油分离按下述方法进行,将材料置于分离器中央并固定,用水润湿材料表面,随后将油水混合物倒入分离器中,水相通过材料而油相被阻隔;材料过油阻水分离按下述方法进行,将材料置于分离器中央并固定,用油润湿材料表面,随后将油水混合物倒入分离器中,油相通过材料而水相被阻隔;5)油水混合物循环分离是指每进行一次分离后将材料洗净烘干,按上述4)中的方法再次进行分离;6)油水混合物分离效率效率按下述公式计算获得:η=(m1/m0)
×
100%,其中η为分离效率,m0和m1分别为油水混合物中水在分离前后的质量;分离效率大于95%时证明该材料的油水分离效率优异。
[0044]
实施例1
[0045]
将不锈钢金属筛网置于配制的浓度为0.1mmol/l苯酚水溶液中,然后于50℃浸泡反应48h,反应结束后干燥;先分别配制含有浓度为1mol/l1-甲基咪唑水溶液和1mol/l硝酸锌前驱体水溶液,再按有机配体与金属离子前驱体水溶液中金属离子的摩尔比为10:1配制混合溶液,然后将干燥后所得的不锈钢金属筛网浸泡于该混合溶液中,于50℃反应0.5h后用去离子水冲洗,并于45℃烘箱中干燥即可。
[0046]
所制得的材料在空气中水接触角为100
±5°
,同一油水体系中水下油接触角和油下水接触角均大于90
°
。
[0047]
实施例2
[0048]
将不锈钢金属筛网置于配制的浓度为10mol/l邻苯二酚水溶液中,然后于5℃浸泡反应48h,反应结束后干燥;先分别配制含有浓度为20mmol/l2-甲基咪唑水溶液和1mmol/l硫酸铜前驱体水溶液,再按有机配体与金属离子前驱体水溶液中金属离子的摩尔比为20:1配制混合溶液,然后将干燥后所得的不锈钢金属筛网浸泡于该混合溶液中,于5℃反应48h后用去离子水冲洗,并于45℃烘箱中干燥即可。
[0049]
所制得的材料在空气中水接触角为95
±3°
,同一油水体系中水下油接触角和油下水接触角均大于90
°
。
[0050]
实施例3
[0051]
将不锈钢金属筛网置于配制的浓度为0.2mmol/l间苯二酚水溶液中,然后于25℃浸泡反应24h,反应结束后干燥;先分别配制含有浓度为1mmol/l4-甲基咪唑水溶液和20mmol/l氯化钴前驱体水溶液,再按有机配体与金属离子前驱体水溶液中金属离子的摩尔比为1:20配制混合溶液,然后将干燥后所得的不锈钢金属筛网浸泡于该混合溶液中,于25℃反应24h后用去离子水冲洗,并于45℃烘箱中干燥即可。
[0052]
所制得的材料在空气中水接触角为110
±6°
,同一油水体系中水下油接触角和油下水接触角均大于90
°
。
[0053]
实施例4
[0054]
将不锈钢金属筛网置于配制的浓度为3mol/l对苯二酚水溶液中,然后于30℃浸泡反应1h,反应结束后干燥;先分别配制含有浓度为1mol/l咪唑-2-甲醛水溶液和4mol/l磷酸二氢铜前驱体水溶液,再按有机配体与金属离子前驱体水溶液中金属离子的摩尔比为1:4配制混合溶液,然后将干燥后所得的不锈钢金属筛网浸泡于该混合溶液中,于20℃反应24h后用去离子水冲洗,并于45℃烘箱中干燥即可。
[0055]
所制得的材料在空气中水接触角为107
±5°
,同一油水体系中水下油接触角和油下水接触角均大于90
°
。
[0056]
实施例5
[0057]
将不锈钢金属筛网置于配制的浓度为0.35mol/l单宁酸水溶液中,然后于25℃浸泡反应6h,反应结束后干燥;先分别配制含有浓度为96mmol/l咪唑水溶液和48mmol/l氯化锌前驱体水溶液,再按有机配体与金属离子前驱体水溶液中金属离子的摩尔比为2:1配制混合溶液,然后将干燥后所得的不锈钢金属筛网浸泡于该混合溶液中,于25℃反应24h后用去离子水冲洗,并于45℃烘箱中干燥即可。
[0058]
所制得的材料在空气中水接触角为130
±5°
,同一油水体系中水下油接触角和油下水接触角均大于90
°
。
[0059]
实施例6
[0060]
将不锈钢金属筛网置于配制的浓度为2mol/l单宁酸水溶液中,然后于35℃浸泡反应24h,反应结束后干燥;先分别配制含有浓度为15mol/l苯并咪唑水溶液和1.5mol/l醋酸铁前驱体水溶液,再按有机配体与金属离子前驱体水溶液中金属离子的摩尔比为10:1配制混合溶液,然后将干燥后所得的不锈钢金属筛网浸泡于该混合溶液中,于40℃反应1h后用去离子水冲洗,并于45℃烘箱中干燥即可。
[0061]
所制得的材料在空气中水接触角为105
±5°
,同一油水体系中水下油接触角和油下水接触角均大于90
°
。
[0062]
实施例7
[0063]
将不锈钢金属筛网置于配制的浓度为3mol/l没食子酸水溶液中,然后于28℃浸泡反应18h,反应结束后干燥;先分别配制含有浓度为5mol/l咪唑水溶液和1mol/l醋酸铁前驱体水溶液,再按有机配体与金属离子前驱体水溶液中金属离子的摩尔比为5:1配制混合溶液,然后将干燥后所得的不锈钢金属筛网浸泡于该混合溶液中,于30℃反应2h后用去离子水冲洗,并于45℃烘箱中干燥即可。
[0064]
所制得的材料在空气中水接触角为102
±3°
,同一油水体系中水下油接触角和油
下水接触角均大于90
°
。
[0065]
实施例8
[0066]
将聚合物泡沫置于配制的浓度为8mol/l没食子酸水溶液中,然后于10℃浸泡反应20h,反应结束后干燥;先分别配制含有浓度为4mol/l咪唑-4,5-二羧酸水溶液和1mol/l氯化亚铁前驱体水溶液,再按有机配体与金属离子前驱体水溶液中金属离子的摩尔比为4:1配制混合溶液,然后将干燥后所得的聚合物泡沫浸泡于该混合溶液中,于45℃反应1h后用去离子水冲洗,并于45℃烘箱中干燥即可。
[0067]
所制得的材料在空气中水接触角为150
±5°
,同一油水体系中水下油接触角和油下水接触角均大于90
°
。
[0068]
实施例9
[0069]
将聚合物泡沫置于配制的浓度为10mol/l多巴胺水溶液中,然后于35℃浸泡反应1h,反应结束后干燥;先分别配制含有浓度为1mmol/l4-羟甲基咪唑盐酸盐水溶液和10mmol/l硝酸镍前驱体水溶液,再按有机配体与金属离子前驱体水溶液中金属离子的摩尔比为1:10配制混合溶液,然后将干燥后所得的聚合物泡沫浸泡于该混合溶液中,于15℃反应24h后用去离子水冲洗,并于45℃烘箱中干燥即可。
[0070]
所制得的材料在空气中水接触角为10
±2°
,同一油水体系中水下油接触角和油下水接触角均大于90
°
。
[0071]
实施例10
[0072]
将聚合物泡沫置于配制的浓度为20mmol/l多巴水溶液中,然后于5℃浸泡反应48h,反应结束后干燥;先分别配制含有浓度为6mol/咪唑-4-甲酸乙酯水溶液和1mol/l溴化镁前驱体水溶液,再按有机配体与金属离子前驱体水溶液中金属离子的摩尔比为6:1配制混合溶液,然后将干燥后所得的聚合物泡沫浸泡于该混合溶液中,于5℃反应1h后用去离子水冲洗,并于45℃烘箱中干燥即可。
[0073]
所制得的材料在空气中水接触角为70
±5°
,同一油水体系中水下油接触角和油下水接触角均大于90
°
。
[0074]
实施例11
[0075]
将聚合物泡沫置于配制的浓度为200mmol/l新绿原酸水溶液中,然后于30℃浸泡反应0.5h,反应结束后干燥;先分别配制含有浓度为10mmol/l咪唑-4-甲酸甲酯水溶液和50mmol/l硝酸钡前驱体水溶液,再按有机配体与金属离子前驱体水溶液中金属离子的摩尔比为1:5配制混合溶液,然后将干燥后所得的聚合物泡沫浸泡于该混合溶液中,于15℃反应48h后用去离子水冲洗,并于45℃烘箱中干燥即可。
[0076]
所制得的材料在空气中水接触角为50
±4°
,同一油水体系中水下油接触角和油下水接触角均大于90
°
。
[0077]
实施例12
[0078]
将聚合物泡沫置于配制的浓度为80mmol/l苯酚水溶液中,然后于50℃浸泡反应0.5h,反应结束后干燥;先分别配制含有浓度为15mol/l 1h-咪唑-4-甲酸水溶液和1.5mol/l醋酸铟前驱体水溶液,再按有机配体与金属离子前驱体水溶液中金属离子的摩尔比为10:1配制混合溶液,然后将干燥后所得的聚合物泡沫浸泡于该混合溶液中,于50℃反应0.5h后用去离子水冲洗,并于45℃烘箱中干燥即可。
[0079]
所制得的材料在空气中水接触角为90
±5°
,同一油水体系中水下油接触角和油下水接触角均大于90
°
。
[0080]
实施例13
[0081]
将聚合物泡沫置于配制的浓度为0.1mol/l邻苯二酚水溶液中,然后于5℃浸泡反应36h,反应结束后干燥;先分别配制含有浓度为0.5mol/l1h-咪唑-4-甲酸水溶液和5mol/l硫酸锌前驱体水溶液,再按有机配体与金属离子前驱体水溶液中金属离子的摩尔比为1:10配制混合溶液,然后将干燥后所得的聚合物泡沫浸泡于该混合溶液中,于5℃反应48h后用去离子水冲洗,并于45℃烘箱中干燥即可。
[0082]
所制得的材料在空气中水接触角为20
±5°
,同一油水体系中水下油接触角和油下水接触角均大于90
°
。
[0083]
实施例14
[0084]
将聚合物泡沫置于配制的浓度为2mol/l苯酚水溶液中,然后于5℃浸泡反应18h,反应结束后干燥;先分别配制含有浓度为4mmol/l1-甲基咪唑水溶液和1mmol/l硝酸锌前驱体水溶液,再按有机配体与金属离子前驱体水溶液中金属离子的摩尔比为4:1配制混合溶液,然后将干燥后所得的聚合物泡沫浸泡于该混合溶液中,于10℃反应5h后用去离子水冲洗,并于45℃烘箱中干燥即可。
[0085]
所制得的材料在空气中水接触角为100
±6°
,同一油水体系中水下油接触角和油下水接触角均大于90
°
。
[0086]
实施例15
[0087]
将铜泡沫置于配制的浓度为0.1mmol/l间苯二酚水溶液中,然后于50℃浸泡反应0.5h,反应结束后干燥;先分别配制含有浓度为6mol/l咪唑-4-甲酸甲酯水溶液和1mol/l氯化钴前驱体水溶液,再按有机配体与金属离子前驱体水溶液中金属离子的摩尔比为6:1配制混合溶液,然后将干燥后所得的铜泡沫浸泡于该混合溶液中,于35℃反应24h后用去离子水冲洗,并于45℃烘箱中干燥即可。
[0088]
所制得的材料在空气中水接触角为95
±5°
,同一油水体系中水下油接触角和油下水接触角均大于90
°
。
[0089]
实施例16
[0090]
将铜泡沫置于配制的浓度为15mmol/l对苯二酚水溶液中,然后于5℃浸泡反应48h,反应结束后干燥;先分别配制含有浓度为100mmol/l咪唑-4-甲酸乙酯水溶液和1.5mol/l硝酸铜前驱体水溶液,再按有机配体与金属离子前驱体水溶液中金属离子的摩尔比为1:15配制混合溶液,然后将干燥后所得的铜泡沫浸泡于该混合溶液中,于5℃反应40h后用去离子水冲洗,并于45℃烘箱中干燥即可。
[0091]
所制得的材料在空气中水接触角为0
°
,同一油水体系中水下油接触角和油下水接触角均大于90
°
。
[0092]
实施例17
[0093]
将铜泡沫置于配制的浓度为200mmol/l单宁酸水溶液中,然后于25℃浸泡反应24h,反应结束后干燥;先分别配制含有浓度为3mol/l4-羟甲基咪唑盐酸盐水溶液和150mmol/l醋酸亚铁前驱体水溶液,再按有机配体与金属离子前驱体水溶液中金属离子的摩尔比为15:2配制混合溶液,然后将干燥后所得的铜泡沫浸泡于该混合溶液中,于25℃反
应1h后用去离子水冲洗,并于45℃烘箱中干燥即可。
[0094]
所制得的材料在空气中水接触角为155
±5°
,同一油水体系中水下油接触角和油下水接触角均大于90
°
。
[0095]
实施例18
[0096]
将铜泡沫置于配制的浓度为1mol/l没食子酸水溶液中,然后于20℃浸泡反应18h,反应结束后干燥;先分别配制含有浓度为10mol/l咪唑-4,5-二羧酸水溶液和1mmol/l硫酸铁前驱体水溶液,再按有机配体与金属离子前驱体水溶液中金属离子的摩尔比为10:1配制混合溶液,然后将干燥后所得的铜泡沫浸泡于该混合溶液中,于25℃反应36h后用去离子水冲洗,并于45℃烘箱中干燥即可。
[0097]
所制得的材料在空气中水接触角为108
±4°
,同一油水体系中水下油接触角和油下水接触角均大于90
°
。
[0098]
实施例19
[0099]
将铜泡沫置于配制的浓度为5mol/l多巴胺水溶液中,然后于50℃浸泡反应1h,反应结束后干燥;先分别配制含有浓度为15mol/l苯并咪唑水溶液和1mol/l醋酸镍前驱体水溶液,再按有机配体与金属离子前驱体水溶液中金属离子的摩尔比为15:1配制混合溶液,然后将干燥后所得的铜泡沫浸泡于该混合溶液中,于35℃反应36h后用去离子水冲洗,并于45℃烘箱中干燥即可。
[0100]
所制得的材料在空气中水接触角为125
±5°
,同一油水体系中水下油接触角和油下水接触角均大于90
°
。
[0101]
实施例20
[0102]
将铜泡沫置于配制的浓度为6mol/l多巴水溶液中,然后于25℃浸泡反应10h,反应结束后干燥;先分别配制含有浓度为200mol/l咪唑-2-甲醛水溶液和1.8mol/l硫酸铟前驱体水溶液,再按有机配体与金属离子前驱体水溶液中金属离子的摩尔比为2:9配制混合溶液,然后将干燥后所得的铜泡沫浸泡于该混合溶液中,于30℃反应6h后用去离子水冲洗,并于45℃烘箱中干燥即可。
[0103]
所制得的材料在空气中水接触角为78
±5°
,同一油水体系中水下油接触角和油下水接触角均大于90
°
。
[0104]
实施例21
[0105]
将铜泡沫置于配制的浓度为0.1mmol/l多巴胺水溶液中,然后于15℃浸泡反应15h,反应结束后干燥;先分别配制含有浓度为1mmol/l1-甲基咪唑水溶液和5mmol/l醋酸铁前驱体水溶液,再按有机配体与金属离子前驱体水溶液中金属离子的摩尔比为1:5配制混合溶液,然后将干燥后所得的铜泡沫浸泡于该混合溶液中,于20℃反应8h后用去离子水冲洗,并于45℃烘箱中干燥即可。
[0106]
所制得的材料在空气中水接触角为118
±5°
,同一油水体系中水下油接触角和油下水接触角均大于90
°
。
[0107]
实施例22
[0108]
将滤布置于配制的浓度为800mmol/l新绿原酸水溶液中,然后于45℃浸泡反应1h,反应结束后干燥;先分别配制含有浓度为12mol/l4-甲基咪唑水溶液和1.5mol/l醋酸镁前驱体水溶液,再按有机配体与金属离子前驱体水溶液中金属离子的摩尔比为8:1配制混合
溶液,然后将干燥后所得的滤布浸泡于该混合溶液中,于20℃反应24h后用去离子水冲洗,并于45℃烘箱中干燥即可。
[0109]
所制得的材料在空气中水接触角为85
±4°
,同一油水体系中水下油接触角和油下水接触角均大于90
°
。
[0110]
实施例23
[0111]
将滤布置于配制的浓度为3mol/l苯酚水溶液中,然后于18℃浸泡反应36h,反应结束后干燥;先分别配制含有浓度为50mmol/l2-甲基咪唑水溶液和450mmol/l磷酸二氢钡前驱体水溶液,再按有机配体与金属离子前驱体水溶液中金属离子的摩尔比为1:9配制混合溶液,然后将干燥后所得的滤布浸泡于该混合溶液中,于20℃反应40h后用去离子水冲洗,并于45℃烘箱中干燥即可。
[0112]
所制得的材料在空气中水接触角为45
±3°
,同一油水体系中水下油接触角和油下水接触角均大于90
°
。
[0113]
实施例24
[0114]
将滤布置于配制的浓度为9mol/l邻苯二酚水溶液中,然后于5℃浸泡反应42h,反应结束后干燥;先分别配制含有浓度为3mol/l1-甲基咪唑水溶液和5mol/l磷酸二氢锌前驱体水溶液,再按有机配体与金属离子前驱体水溶液中金属离子的摩尔比为3:5配制混合溶液,然后将干燥后所得的滤布浸泡于该混合溶液中,于40℃反应1h后用去离子水冲洗,并于45℃烘箱中干燥即可。
[0115]
所制得的材料在空气中水接触角为65
±3°
,同一油水体系中水下油接触角和油下水接触角均大于90
°
。
[0116]
实施例25
[0117]
将滤布置于配制的浓度为400mmol/l间苯二酚水溶液中,然后于15℃浸泡反应24h,反应结束后干燥;先分别配制含有浓度为6mol/l咪唑水溶液和5mol/l氯化亚铁前驱体水溶液,再按有机配体与金属离子前驱体水溶液中金属离子的摩尔比为6:5配制混合溶液,然后将干燥后所得的滤布浸泡于该混合溶液中,于45℃反应32h后用去离子水冲洗,并于45℃烘箱中干燥即可。
[0118]
所制得的材料在空气中水接触角为75
±5°
,同一油水体系中水下油接触角和油下水接触角均大于90
°
。
[0119]
实施例26
[0120]
将滤布置于配制的浓度为90mmol/l对苯二酚水溶液中,然后于50℃浸泡反应40h,反应结束后干燥;先分别配制含有浓度为700mmol/l2-甲基咪唑水溶液和100mmol/l硫酸钴前驱体水溶液,再按有机配体与金属离子前驱体水溶液中金属离子的摩尔比为7:1配制混合溶液,然后将干燥后所得的滤布浸泡于该混合溶液中,于35℃反应28h后用去离子水冲洗,并于45℃烘箱中干燥即可。
[0121]
所制得的材料在空气中水接触角为135
±5°
,同一油水体系中水下油接触角和油下水接触角均大于90
°
。
[0122]
实施例27
[0123]
将棉织物置于配制的浓度为600mmol/l单宁酸水溶液中,然后于24℃浸泡反应1h,反应结束后干燥;先分别配制含有浓度为300mmol/l咪唑水溶液和700mmol/l氯化铜前驱体
水溶液,再按有机配体与金属离子前驱体水溶液中金属离子的摩尔比为3:7配制混合溶液,然后将干燥后所得的棉织物浸泡于该混合溶液中,于15℃反应30h后用去离子水冲洗,并于45℃烘箱中干燥即可。
[0124]
所制得的材料在空气中水接触角为130
±5°
,同一油水体系中水下油接触角和油下水接触角均大于90
°
。
[0125]
实施例28
[0126]
将棉织物置于配制的浓度为880mmol/l没食子酸水溶液中,然后于10℃浸泡反应0.5h,反应结束后干燥;先分别配制含有浓度为1mol/l4-羟甲基咪唑盐酸盐水溶液和900mmol/l氯化铁前驱体水溶液,再按有机配体与金属离子前驱体水溶液中金属离子的摩尔比为10:9配制混合溶液,然后将干燥后所得的棉织物浸泡于该混合溶液中,于28℃反应35h后用去离子水冲洗,并于45℃烘箱中干燥即可。
[0127]
所制得的材料在空气中水接触角为80
±5°
,同一油水体系中水下油接触角和油下水接触角均大于90
°
。
[0128]
实施例29
[0129]
将棉织物置于配制的浓度为7mol/l多巴胺水溶液中,然后于15℃浸泡反应24h,反应结束后干燥;先分别配制含有浓度为4mol/l咪唑-4-甲酸甲酯水溶液和7mol/l氯化铟前驱体水溶液,再按有机配体与金属离子前驱体水溶液中金属离子的摩尔比为4:7配制混合溶液,然后将干燥后所得的棉织物浸泡于该混合溶液中,于30℃反应48h后用去离子水冲洗,并于45℃烘箱中干燥即可。
[0130]
所制得的材料在空气中水接触角为55
±4°
,同一油水体系中水下油接触角和油下水接触角均大于90
°
。
[0131]
实施例30
[0132]
将棉织物置于配制的浓度为1.5mol/l多巴水溶液中,然后于20℃浸泡反应12h,反应结束后干燥;先分别配制含有浓度为9mol/l苯并咪唑水溶液和7mol/l硫酸镍前驱体水溶液,再按有机配体与金属离子前驱体水溶液中金属离子的摩尔比为9:7配制混合溶液,然后将干燥后所得的棉织物浸泡于该混合溶液中,于25℃反应28h后用去离子水冲洗,并于45℃烘箱中干燥即可。
[0133]
所制得的材料在空气中水接触角为85
±5°
,同一油水体系中水下油接触角和油下水接触角均大于90
°
。
[0134]
实施例31
[0135]
将砂芯滤板置于配制的浓度为10mol/l新绿原酸水溶液中,然后于5℃浸泡反应0.5h,反应结束后干燥;先分别配制含有浓度为200mmol/l咪唑-4-甲酸乙酯水溶液和800mmol/l硫酸镁前驱体水溶液,再按有机配体与金属离子前驱体水溶液中金属离子的摩尔比为1:4配制混合溶液,然后将干燥后所得的砂芯滤板浸泡于该混合溶液中,于50℃反应0.5h后用去离子水冲洗,并于45℃烘箱中干燥即可。
[0136]
所制得的材料在空气中水接触角为55
±3°
,同一油水体系中水下油接触角和油下水接触角均大于90
°
。
[0137]
实施例32
[0138]
将砂芯滤板置于配制的浓度为0.1mmol/l多巴胺水溶液中,然后于50℃浸泡反应
48h,反应结束后干燥;先分别配制含有浓度为320mmol/l 1h-咪唑-4-甲酸水溶液和80mmol/l硝酸钡前驱体水溶液,再按有机配体与金属离子前驱体水溶液中金属离子的摩尔比为4:1配制混合溶液,然后将干燥后所得的砂芯滤板浸泡于该混合溶液中,于5℃反应48h后用去离子水冲洗,并于45℃烘箱中干燥即可。
[0139]
所制得的材料在空气中水接触角为95
±5°
,同一油水体系中水下油接触角和油下水接触角均大于90
°
。
[0140]
实施例33
[0141]
将砂芯滤板置于配制的浓度为0.1mmol/l苯酚900mmol/l没食子酸水溶液中,然后于22℃浸泡反应26h,反应结束后干燥;先分别配制含有浓度为2mol/l咪唑-4-甲酸甲酯水溶液和600mmol/l醋酸锌前驱体水溶液,再按有机配体与金属离子前驱体水溶液中金属离子的摩尔比为10:3配制混合溶液,然后将干燥后所得的砂芯滤板浸泡于该混合溶液中,于30℃反应24h后用去离子水冲洗,并于45℃烘箱中干燥即可。
[0142]
所制得的材料在空气中水接触角为110
±4°
,同一油水体系中水下油接触角和油下水接触角均大于90
°
。
[0143]
实施例34
[0144]
将砂芯滤板置于配制的浓度为6mol/l单宁酸水溶液中,然后于20℃浸泡反应24h,反应结束后干燥;先分别配制含有浓度为8mol/l咪唑水溶液和1mol/l硝酸钴前驱体水溶液,再按有机配体与金属离子前驱体水溶液中金属离子的摩尔比为8:1配制混合溶液,然后将干燥后所得的砂芯滤板浸泡于该混合溶液中,于25℃反应48h后用去离子水冲洗,并于45℃烘箱中干燥即可。
[0145]
所制得的材料在空气中水接触角为118
±5°
,同一油水体系中水下油接触角和油下水接触角均大于90
°
。
[0146]
实施例35
[0147]
将砂芯滤板置于配制的浓度为60mmol/l对苯二酚水溶液中,然后于45℃浸泡反应18h,反应结束后干燥;先分别配制含有浓度为6mol/l 1h-咪唑-4-甲酸水溶液和15mol/l硝酸铜前驱体水溶液,再按有机配体与金属离子前驱体水溶液中金属离子的摩尔比为2:5配制混合溶液,然后将干燥后所得的砂芯滤板浸泡于该混合溶液中,于35℃反应20h后用去离子水冲洗,并于45℃烘箱中干燥即可。
[0148]
所制得的材料在空气中水接触角为68
±4°
,同一油水体系中水下油接触角和油下水接触角均大于90
°
。
[0149]
实施例36
[0150]
将砂芯滤板置于配制的浓度为60mmol/l对苯二酚和60mmol/l单宁酸混合水溶液中,然后于25℃浸泡反应30h,反应结束后干燥;先分别配制含有浓度为1mol/l 1h-咪唑-4-甲酸及1mol/l咪唑-4,5-二羧酸水溶液和2mol/l硝酸铜及4mmol/l硫酸亚铁前驱体水溶液,再按有机配体与金属离子前驱体水溶液中金属离子的摩尔比为1:3配制混合溶液,然后将干燥后所得的砂芯滤板浸泡于该混合溶液中,于35℃反应20h后用去离子水冲洗,并于45℃烘箱中干燥即可。
[0151]
所制得的材料在空气中水接触角为30
±3°
,同一油水体系中水下油接触角和油下水接触角均大于90
°
。
[0152]
实施例37
[0153]
将不锈钢金属筛网置于配制的浓度为1mol/l多巴胺和1mmol/l没食子酸混合水溶液中,然后于35℃浸泡反应12h,反应结束后干燥;先分别配制含有浓度为2mol/l4-羟甲基咪唑盐酸盐及7mol/l咪唑水溶液和2mol/l硝酸钴及1mol/l氯化钡前驱体水溶液,再按有机配体与金属离子前驱体水溶液中金属离子的摩尔比为3:1配制混合溶液,然后将干燥后所得的不锈钢金属筛网浸泡于该混合溶液中,于35℃反应18h后用去离子水冲洗,并于45℃烘箱中干燥即可。
[0154]
所制得的材料在空气中水接触角为94
±6°
,同一油水体系中水下油接触角和油下水接触角均大于90
°
。
[0155]
实施例38
[0156]
将不锈钢金属筛网置于配制的浓度为1mol/l单宁酸水溶液中,然后于25℃浸泡反应24h,反应结束后干燥;先分别配制含有浓度为48mmol/l咪唑及32mol/l2-甲基咪唑水溶液和20mmol/l硝酸锌及20mmol/l氯化锌前驱体水溶液,再按有机配体与金属离子前驱体水溶液中金属离子的摩尔比为2:1配制混合溶液,然后将干燥后所得的不锈钢金属筛网浸泡于该混合溶液中,于25℃反应24h后用去离子水冲洗,并于45℃烘箱中干燥即可。
[0157]
所制得的材料在空气中水接触角为127
±6°
,同一油水体系中水下油接触角和油下水接触角均大于90
°
。
[0158]
实施例39
[0159]
将滤布置于配制的浓度为100mmol/l对苯二酚、100mmol/l苯酚和50mmol/l单宁酸混合水溶液中,然后于30℃浸泡反应24h,反应结束后干燥;先分别配制含有浓度为6mol/l 1h-咪唑-4-甲酸、和1mol/l咪唑及1mol/l苯并咪唑水溶液和0.5mol/l硫酸铜、1mol/l硝酸钴、0.5mol/l氯化铟前驱体水溶液,再按有机配体与金属离子前驱体水溶液中金属离子的摩尔比为4:1配制混合溶液,然后将干燥后所得的滤布浸泡于该混合溶液中,于25℃反应36h后用去离子水冲洗,并于45℃烘箱中干燥即可。
[0160]
所制得的材料在空气中水接触角为106
±6°
,同一油水体系中水下油接触角和油下水接触角均大于90
°
。
[0161]
实施例40
[0162]
将棉织物置于配制的浓度为120mmol/l咪唑水溶液中,然后于45℃浸泡反应25h,反应结束后干燥;先分别配制含有浓度为100mmol/l 2-甲基咪唑水溶液和10mmol/l硝酸锌、10mmol/l硫酸锌、10mmol/l氯化锌及10mmol/l醋酸锌前驱体水溶液,再按有机配体与金属离子前驱体水溶液中金属离子的摩尔比为5:2配制混合溶液,然后将干燥后所得的棉织物浸泡于该混合溶液中,于45℃反应16h后用去离子水冲洗,并于45℃烘箱中干燥即可。
[0163]
所制得的材料在空气中水接触角为112
±3°
,同一油水体系中水下油接触角和油下水接触角均大于90
°
。
[0164]
下面给出应用例,以对本发明所制备的水下疏油/油下疏水可切换油水分离材料的实际应用,但是,所给出的应用例仅仅是本发明技术方案的一部分实施例所制备获得的材料的应用例。
[0165]
应用例1
[0166]
选用实施例5所制备获得的不锈钢金属筛网材料,该材料在正己烷/水、石油醚/水
和二氯甲烷/水等油水体系中均呈现水下疏油和油下疏水性。将其置放在分离器中央,用水润湿后采用过水阻油的方式分离油水混合物;同时也将采用油润湿后采取过油阻水方式分离油水混合物。效果如图6所示,可见该材料既能采用过水阻油亦能采用过油阻水方式成功分离油水混合物。循环分离50次后,分离效率仍大于98.55%。
[0167]
应用例2
[0168]
选用实施例38所制备获得的不锈钢金属筛网材料,该材料在正己烷/水、石油醚/水和二氯甲烷/水等油水体系中均呈现水下疏油和油下疏水性。将其置放在分离器中央,用水润湿后采用过水阻油的方式分离油水混合物;同时也将采用油润湿后采取过油阻水方式分离油水混合物。效果如图7所示,可见该材料既能采用过水阻油亦能采用过油阻水方式成功分离油水混合物。且对于同一油水体系亦可实现过水阻油亦可实现过油阻水。循环分离50次后,分离效率仍大于98.55%。